Работа карьерных экскаваторов и самосвалов на открытых месторождениях
Мировой рынок твёрдых полезных ископаемых на протяжении нескольких десятилетий испытывает постоянный рост: за последние 4 десятилетия объёмы потребления минерального сырья значительно увеличились, что обусловлено ростом населения и развитием промышленности. Добыча основных сырьевых ресурсов в период с 1970 по 2010 показывает следующий рост: угля – в 2 раза, железной руды – в 3 раза, медной руды – в 2,5 раза, бокситов – в 7 раз, никеля — в 2 раза. Эти факторы влекут за собой закономерное увеличение потребности в тяжелой технике для разработки открытых месторождений.
К 2011 году мировой машиностроительный комплекс, производящий карьерную технику, сконцентрировался в четырёх крупнейших корпорациях: Caterpillar, Komatsu, Hitachi, Volvo. Эти производители и по сей день являются лидерами по количеству спецтехники, поставляемой на карьеры России.
Технологические процессы разработки месторождений
Вскрыша пустых пород производится бульдозерами и скреперами, вскрыша тяжелых грунтов — экскаваторами или драглайнами.
Разработка наиболее твердых каменных пород производится взрывом «на разрыхление» (применяется заряд такой силы, которая может только разрушить и разрыхлить материал, не разбрасывая его в стороны от места взрыва). Разработка менее твердых пород производится одноковшовыми экскаваторами с непосредственной погрузкой в автотранспорт. Разработка наиболее слабых грунтов (легких супесей и песков) производится одноковшовыми и многоковшовыми погрузчиками.
Для погрузки дробленой взрывом скалы целесообразно использовать экскаваторы на гусеничном ходу с рабочим оборудованием прямой лопаты и вместимостью ковша от 3 м3. Погрузка некрупных каменных материалов и грунтов в транспортные средства производится экскаваторами с ковшами емкостью до 2 м3. Погрузка песка, галечника часто осуществляется фронтальными погрузчиками.
Для вывоза горной массы идеально подходят карьерные самосвалы. Выбор модели карьерного самосвала в основном зависит от того, какая техника используется для загрузки горной массы.
Карьерные экскаваторы
Гусеничные карьерные экскаваторы широко используются на открытых горных работах: для разработки ископаемых пород и вскрыши и их погрузки в транспортные средства, а также для перемещения породы по площадке.
Гидравлические экскаваторы обладают очевидными технологическими преимуществами. С их помощью возможно осуществлять выемку пород верхним и нижним черпанием, выполнять загрузку автотранспорта, который может находиться как на горизонте установки экскаватора, так и выше или ниже его. Данные машины очень мобильны и многофункциональны, обеспечивают высокую эффективность селективной разработки сложных месторождений, разработку обводнённых залежей, безвзрывную выемку пород. Кроме того, современные гидравлические экскаваторы экологичны: они оснащены дизельными двигателями с минимальным выхлопом, а также надежными системами по недопущению утечек рабочих жидкостей в окружающую среду.
Основные элементы конструкции карьерного экскаватора — это кузов, поворотная платформа, стрела с рукоятью и ковшом, нижняя рама и гусеничная ходовая часть, двуногая стойка. Все составляющие изготовлены из высокопрочной стали, что обеспечивает высокую надежность, а также возможность работы машины в любых погодных условиях, в диапазоне температур от –40 до +45 градусов. Длина стрелы определяет показатели выработки вертикальных стен карьера: высота копания может достигать 20 м, радиус– 24 м. Главный определяющий фактор производительности машины — это размер ковша (до 50 м3): чем больше его объем, тем эффективнее выработка и загрузка породой кузова транспортного средства. Для всех современных моделей экскаваторов доступен большой ассортимент ковшей, с помощью которых осуществляется загрузка самосвалов с разной грузоподъемностью при сохранении оптимального количества циклов (обычно до 4-6). Различают два основных вида используемых ковшей: скальный (разгрузка через днище) и сменный (разгрузка опрокидыванием). Стоит заметить, что гидравлические экскаваторы обладают значительным преимуществом перед мехлопатами: они способны выполнять плавную, почти безударную выгрузку породы в кузов, что способствует значительному снижению динамической нагрузки на днище кузова и подвеску самосвала, значительно уменьшает пылеобразование и помогает избежать просыпей породы за пределы кузова.
Карьерные самосвалы
Карьерный самосвал – это грузовой автомобиль с самостоятельной разгрузкой, которая осуществляется с помощью наклона кузова или всего автомобиля телескопическими подъемниками. Данные машины широко применяются на открытых карьерах, показывая наибольшую эффективность в работе с гидравлическими экскаваторами.
Благодаря совершенству конструкции, современные самосвалы отличаются высокой проходимостью и надежностью в условиях бездорожья, трудных климатических условиях, а также имеют очень высокую грузоподъемность.
Карьерные самосвалы с жесткой рамой массово применяются на карьерах по всему миру, что свидетельствует об их исключительных технико-экономических показателях. Данные машины прекрасно зарекомендовали себя при работе в сложных условиях. Карьерный самосвал – это мощная маневренная машина большой грузоподъемности, предназначенная для перевозки сыпучих грузов и горных пород по дорогам с прочным основанием.
Разработка карьерных самосвалов производится с учетом их работы в связке с экскаваторами, поэтому при проектировании большое внимание уделяется соответствию параметров самосвала характеристикам экскаватора: в первую очередь, это оптимальное соотношение объема ковша и вместимости кузова самосвала. Размер и форма кузова должны обеспечивать эффективную разгрузку ковша экскаватора, минимизировать просыпи и способствовать оптимизированию укладки породы. Также большое значение имеет число разгрузочных циклов (оптимальным считается количество от 3 до 6). В зависимости от условий, продолжительность разгрузки должна составлять от 9 до 30 секунд.
Карьерные экскаваторы от 100т + карьерные самосвалы с жесткой рамой:
Caterpillar 6015 Hitachi ZX1200 Komatsu 1250, Komatsu 2000 |
Komatsu 785 |
Шарнирно-сочлененные самосвалы — относительно новый класс горно-транспортных машин, разработанных для работы с гидравлическими экскаваторами в течение последних двух десятилетий. Важно, что в России нет производства такого вида техники. Наибольший опыт в проектировании и производстве шарнирно-сочлененных самосвалов имеют такие производители как Volvo и Caterpillar.
Особенности конструкции и показываемые рабочие характеристики обеспечивают сочлененным самосвалам большие перспективы для работы в условиях российских карьеров. Благодаря сочленению, проектировщикам данных машин удалось добиться высокой степени независимости кабины и кузова, что обеспечивает машине плавный ход в условиях бездорожья. Беспроблемное передвижение самосвала по карьерным дорогам также обеспечивается работой высокотехнологичной гидравлической системы и оснащенностью каждого колеса отдельным приводом. Еще одно важное отличие от жесткорамных самосвалов заключается в значительно меньшем радиусе поворота и ширине машины, что обеспечивает исключительную маневренность.
Карьерные экскаваторы от 70т + шарнирно-сочлененные самосвалы
Volvo EC700, Hitachi 850, Hitachi 860, Hitachi 870 Komatsu PC600, PC650, PC800 Caterpillar 374, Caterpillar 385, Caterpillar 390 |
Volvo A35, Volvo A40 Caterpillar 735, Caterpillar 740 |
torion.pro
Экскаваторы в щебеночных карьерах — Дорожно-строительные материалы и машины
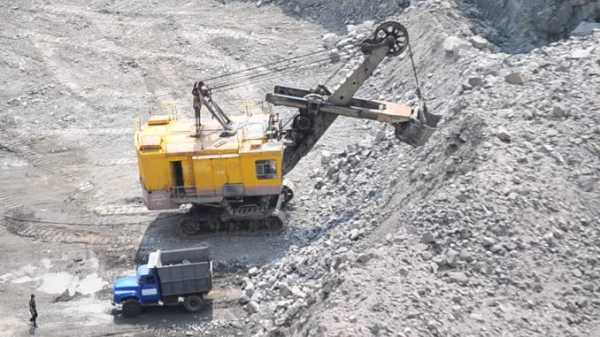
Карьерные экскаваторы представляют собой гусеничную технику, предназначенную для выполнения для разработки и погрузки горной породы. Помимо этого карьерные экскаваторы занимаются вскрытием месторождений.
Современный карьерный экскаватор состоит из следующих узлов и агрегатов:
- рама с крепящимися на нее гусеницами или шагающим механизмом;
- стойка двуногая;
- нижняя рама;
- кузов;
- кабина оператора – машиниста;
- силовая установка;
- пневматические и гидравлические системы;
- поворотная платформа;
- ковш, закрепленный на стреле.
Классификация карьерных экскаваторов может происходить по нескольким признакам:
- по типу ходовой части: гусеницы, шагающий механизм;
- по типу привода рабочих агрегатов: гидравлический или пневматический, электрический, механический, гидромеханический;
- по типу силовой установки: дизельная, электрическая, одно- или многомоторная;
- по типу работы: непрерывного действия (роторные) или циклического действия (одноковшовые).
Гусеничные экскаваторы в зависимости от размеров могут быть двух, четырех и восьми гусеничными. Гусеницы крепятся к платформе. Гусеничные экскаваторы могут оборудоваться, как ковшом (прямым или обратным) так и роторным механизмом.
Шагающий экскаватор, это экскаватор фактически опирающийся рамой-платформой на грунт. При необходимости с помощью устройств похожих на «лыжи-башмаки», закрепленных на гидравлических опорах, он может передвинуться на один шаг вперед и снова опереться на раму-платформу. Количество шагов определяется необходимостью и дальностью расстояние, на которую перемещают карьерную машину. Обычно шагающий экскаваторы являются очень громоздкими механизмами, вес которых гусеничные механизмы просто не выдержат. Благодаря опоре на раму вес конструкции распределяется равномерно по большой площади опирания. Габариты ковшей и длина вылета стрелы у таких экскаваторов намного больше, чем у экскаваторов на гусеничном ходу. Хотя есть и исключения.
Самый большой карьерный экскаватор, когда-либо созданный человеком – это Bagger 293. Этот гигантский экскаватор был построен в 1995 году компанией из Лейпцига и передвигается он на гусеницах. Экскаватор является роторным, его длина 226 метров, а высота 96 метров. В настоящий момент эта машина эксплуатируется в Германии.
Самый большой шагающий карьерный экскаватор – это Big Muskie. Этот драглайн был создан американской компанией Bucyrus International в 1969 году. Длина гигантского механизма составила 128 метров, а высота 67,8 метров. Экскаватор работал на постоянном токе, получаемом от дизельного генератора. В 1999 году эксплуатация самого большого в мире шагающего экскаватора завершилась.
Экскаваторы по типу привода могут подразделяться на гидравлические, механические, гидромеханические, электрические.
У экскаваторов с механическим приводом, рабочие органы (стрела, ковш) приводятся в движение с помощью цепей или канатов. Механический канатный или цепной привод по надежности уступает моделям с гидравлическим приводом. Детали таких экскаваторов быстро изнашиваются и требуют замены.
В конструкциях экскаваторов с гидравлическим приводом, усилие на рабочие элементы прикладывается через гидроцилиндры или гидродвигатели. Гидравлический насос, приводимы в движение двигателем экскаватора, обеспечивает необходимы напор жидкости в гидравлической систему.
Самыми распространенными экскаваторами в условиях щебеночных карьеров являются гусеничные одноковшовые экскаваторы с гидравлическим приводом, оснащенные дизельными двигателями внутреннего сгорания. Объем ковшей таких экскаваторов от 8 куб.м. до 40 куб.м.
Самые известные и надежные марки карьерных экскаваторов: Caterpillar, Уралмаш, HITACHI, Komatsu. Все большую известность приобретают китайские карьерные экскаваторы BONNY. Оснащаются такие экскаваторы, в зависимости от задач, прямой или обратной лопатой.
Еще один тип экскаваторов, применяемых на карьерных работах – это драглайны. Основной принцип работы экскаватора-драглайна является способ наборы породы в ковш. Зацеп породы осуществляется за счет волочения ковша по поверхности. Драглайн оснащен тяговым и подъемным канатами. Один канат поднимает ковш, а другой подтягивает его к машине. Одним из минусов драглайна является трудность погрузки породы с помощью него в транспортные средства. Чаще всего драглайн помещает породу в отвал. Еще один недостаток – это требования к исходному материалу. Разрабатываемая поверхность должна быть достаточно мягкой и рыхлой, ведь , фактически, забор породы в ковш осуществляется за счет веса самого ковша. Производители наиболее популярных моделей грейферов: HITACHI, Komatsu, TEREX, Эксмаш.
pro-scheben.ru
Опыт эксплуатации канатных и гидравлических экскаваторов в условиях карьера Мурунтау
П.А.Шеметов, к.т.н., начальник карьера Мурунтау (Навоийский ГМК)
С.К.Рубцов, к.т.н., начальник лаборатории А.Г.Шлыков, к.т.н., старший научный сотрудник (ВНИПИпромтехнологии)
Карьер Мурунтау Навоийского ГМК — высокопроизводительное золоторудное предприятие, глубина которого достигает 450 м и постоянно увеличивается, что приводит к сокращению рабочих зон и, соответственно, к повышенной концентрации на ограниченной площади горнотранспортного оборудования. В условиях ограничения рабочих зон и увеличения насыщения в них выемочно-погрузочного и другого оборудования происходит снижение производительности экскаваторов за счет организационно-технических причин, вызванных несвоевременной подачей автосамосвалов и скоростью их движения, а также необходимостью частого переноса ЛЭП. Поэтому в данных условиях применение мобильной и автономной, не зависящей от энергоснабжения, выемочно-погрузочной техники с большой единичной мощностью, в частности, гидравлических экскаваторов (ЭГ), вполне оправдано. Преимущества ЭГ в части автономности и маневренности позволяют наиболее эффективно их использовать в сочетании с большегрузными автосамосвалами в стесненных условиях отработки забоев, при широком диапазоне изменения свойств горных пород, сложном строе нии рудных тел и неравномерности распределения полезного ископаемого в горном массиве.
На карьере эксплуатируются 16 канатных экскаваторов шести типоразмеров (ЭКГ4У, ЭКГ8УС, ЭКГ8И, ЭКГ10, ЭКГ12.5, ЭКГ15), которые используются на вскрышных и добычных работах, для заоткоски бортов карьера, на перегрузочных пунктах карьера (ППК). Начиная с 1995 г. введены в эксплуатацию гидравлические экскаваторы: САТ5230 (2 шт.), Rh270 (2 шт.) и ЕХ3500 (1 шт.) фирм Caterpillar (США), Orenstein & Koppel (Германия) и Hitachi (Япония) с емкостью ковша до 15 м3, а с августа 2003 г. — два электрогидравлических экскаватора Rh300 с емкостью ковша 20 м3. При этом у 15 экскаваторов ЭКГ и 4-х экскаваторов ЭГ (кроме RH-170 №5) превышен срок амортизации.
Анализ конструктивных и технологических данных гидравлических экскаваторов показывает, что они практичес ки сопоставимы друг с другом по геометрическим и энергосиловым параметрам. Основными отличиями ЭГ по сравнению с канатными ЭКГ являются автономность в работе и шарнирное сочленение рукояти ковша со стрелой.
Шарнирное сочленение рукояти ковша со стрелой уменьшает радиус черпания, поэтому гидравлические экскаваторы в процессе работы располагаются ближе к откосу уступа по сравнению с электрическими канат ными. Так, например, если у экскава тора ЭКГ15 максимальная высота черпания (16.4 м) в 1.4 раза меньше радиуса черпания (22.6 м), то у гидравлических экскаваторов эти параметры сопоставимы и составляют 15-17 м. В результате, безопасность работы ЭГ (в частности, исключение образования козырьков, нависей и т.п.) обуславливает более высокую степень дробления в забоях, отрабатываемых ЭГ.
Результаты совместной эксплуатации канатных и гидравлических экскаваторов за последние годы в условиях карьера Мурунтау позволили провести оценку эффективности их работы с целью выявления наиболее перспективной модели, сокращения номенклатуры применяемого выемочно-погрузочного оборудования и определения его наиболее эффективного сочетания с транспортным оборудованием для обеспечения оптимальной производительности экскаваторно-автомобильного комплекса. Для сравнения с ЭГ принят наиболее близкий по емкости ковша канатный экскаватор ЭКГ15 (табл. 1).
За время эксплуатации ЭГ ими отгружено 115.3 млн. м3 горной массы, из них — 12.3 млн. м3 — экскаваторами Rh300.
Обеспечение экскаваторов автосамосвалами при выемке горной массы осуществляется с учетом текущих потребностей в руде заданного качества, поскольку управление содержанием в товарной руде начинается с экскаваторных забоев, в связи с чем в зависимости от конкретной ситуации экскаваторы обслуживаются автосамосвалами на 30-100%. Потери рабочего времени на аварийные простои составили 20-25% (рис. 1), причем, как показывает динамика их изменения, при увеличении срока службы они возрастают. Наименьшие простои у САТ5230 (в среднем 7950 час), наибольшие — у экскаватора ЕХ3500 (9300 час), у Rh270 9020 час. Наибольшие простои ЕХ3500 обусловлены более сложным по сравнению с другими ЭГ конструктивным исполнением и, соответственно, сложностью проведения ремонтных работ. За тот же период простои канатного экскаватора ЭКГ15 составили 5640 час, что на 40% меньше, чем у ЕХ3500 и на 29% меньше, чем у САТ5230.
Табл. 1 Основные показатели работы экскаваторов за 1999-2003 гг.
Показатели |
САТ-5230 |
ЕХ-3500 |
RH-170 |
RH-200* |
ЭКГ-15 |
Количество экскаваторов |
2 |
1 |
2 |
2 |
1 |
Геометрическая емкость ковша, м3 |
15.1 |
13.7 |
14.8 |
20.6 |
15.0 |
Объем отгруженной горной массы, тыс. м3 |
21760 |
13370 |
22310 |
3330 |
12460 |
Аварийные простои, час |
15900 |
9300 |
18040 |
340 |
5640 |
Производительность, м3/ч |
510 |
585 |
560 |
577 |
480 |
Удельный расход топлива, кг/м3 |
0.29 |
0.35 |
0.28 |
||
Коэффициент использования |
0.47 |
0.59 |
0.46 |
0.79 |
0.59 |
* RH-200 введены в эксплуатацию в августе 2003 г.
Экскаваторы
Рис. 1 Аварийные простои экскаваторов за период 1999-2003 гг.
Основные характерные причины аварийных простоев ЭГ — это отказы гидроцилиндров ковша, рукояти, стрелы, разрыв шлангов высокого давления, выход из строя двигателей и др. Общими неисправностями для всех экскаваторов являются:
— разрыв шлангов высокого давления, трещины в гидробаках, выход из строя насосов, обрыв шпилек головок цилиндров двигателя;
— экскаваторы САТ5230 и Rh270 имеют нетехнологичную конструкцию упоров на рукояти для ограничения действия ковша и даже из-за небольшой неточности их установки на заводе неравномерно распределяются нагрузки на каждый из упоров, в результате чего возникают трещины в металлоконструкциях.
Анализ работы ЭГ и характерных простоев позволил выявить наиболее слабые детали и узлы с малой наработкой и наладить их производство непосредственно в условиях Навоийского машиностроительного завода (НМЗ), в частности, наиболее подверженных износу сменных элементов ковшей, зубьев, режущих кромок, протекторов. В результате этого предприятие отказалось от закупок за рубежом сменных элементов ковшей, так как стоимость аналогичных изделий собственного производства значительно ниже и не уступает зарубежным по стойкости. Освоен выпуск практически всех сменных элементов ковша САТ5230, а также унифицированного зуба для Rh270 и ЕХ3500.
Динамика изменения коэффициента использования гидравлических экскаваторов (Ки) показывает, что их работа не отличается стабильностью. Разброс показателей Ки для одного типа экскаватора в различные годы достигал 15-20%. Наибольшая стабильность в работе отмечается у экскаваторов ЕХ3500 и Rh270 №4. Значительные аварийные простои, вызванные выходом из строя главного двигателя САТ5230 №2 в 1999 г., практически привели к остановке экскаватора (Ки = 0.06). Аналогичная ситуация наблюдалась в 2003г. с экскаватором Rh270 №5 (Ки = 0.04), который отработал в забое всего один месяц (228 час).
Рис. 2 Среднее значение коэффициента использования за период 1999-2003 гг.
По результатам эксплуатации ЭГ за 1999-2003 гг. величина Кине превышает 0.59-0.47 (рис. 2). Значения Ки для экскаваторов САТ5230 и Rh270 практически одинаковы — 0.47 и 0.46, соответственно, у ЕХ3500 — 0.59, что в среднем на 27% выше. Следует заметить, что Киэлектрогидравлических экскаваторов Rh300, введенных в эксплуатацию в 2003г., достаточно высок и составил 0.79. Работа канатного экскаватора ЭКГ15 отличается достаточной надежностью. За последние 5 лет изменение Ки составило всего 10% (Ки = 0.6 в 1999 г. до 0.54 в 2003 г.), а среднее значение Ки за данный период 0.59, что выше, чем у экскаваторов САТ5230 и Rh270.
Применение на карьере Мурунтау гидравлических экскаваторов с большой единичной мощностью и вместимостью ковша в сочетании с большегрузными самосвалами позволило в первые годы их эксплуатации обеспечить высокие темпы добычи и рост производительности при сокращении общего парка выемочно-погрузочного оборудования при увеличивающейся глубине карьера.
Рис. 3 Приведенные затраты на содержание экскаваторов за период 2000-2004 гг.
Анализ основных показателей работы ЭГ, их достоинств и недостатков не позволяет дать однозначную оценку о преимуществе одного какого-либо типа экскаватора. Однако, по большинству рассматриваемых параметров (объемам горной массы, производительности, коэффициенту использования и др.) лучшие показатели имеют экскаваторы ЕХ3500 фирмы Hitachi и САТ5230 фирмы Caterpillar. В настоящее время оборудование фирмы Caterpillar широко используется в условиях карьера (грейдеры, бульдозеры, погрузчики), которые имеют много унифицированных и взаимозаменяемых с экскаваторами узлов и деталей, что позволяет более оперативно решать вопросы по их обслуживанию и ремонту.
Оценивая работу канатных экскаваторов ЭКГ15, можно заключить, что по многим параметрам отличие в показателях незначительно, а по некоторым показателям ЭКГ15 да же превосходят характеристики гидравлических экскаваторов. Канатные экскаваторы этого типа проще в изготовлении и обслуживании, они дешевле гидравлических и не требуют сложной ремонтной базы. Соответственно дешевле запасные части, которые более доступны по стоимости при отсутствии на них дефицита.
Согласно действующим Единым правилам безопасности при разработке взорванных пород канатными экскаваторами, высота уступа Ну не должна превышать полуторную максимальную высоту копания экскаватора hon™* или Нч1Ш1, так как hon™* = для канатных экскаваторов.
По конструктивной схеме гидравлические экскаваторы при отработке забоя не могут реализовать максимальную кинематическую высоту копания = Нчт_ указанную в технической характеристике экскаватора. Как видно из рис. 3, на котором приведена сопоставительная оценка зон копания на примере канатного (ЭКГ 20) и гидравлического (ЭГ20) экскаваторов, непосредственно в контакте с забоем ковш гидравлического экскаватора может находиться до высоты, равной (0.65-0.75) houm,*, которая на 25-35% меньше паспортной величины г^^. Эту фактическую высоту контакта ковша ЭГ с откосом забоя называют приведенной высотой копания экскаватора h’^^, т.е. h’,,,,,,^^0.7-0.75 • ho,,™ [1, 2]. В связи с этим при отработке ЭГ уступов без применения взрывных работ максимальная высота забоя и уступа составляет Ну = h’,,,,,,^ или Ну = 0.7-0.75 •Н,,^.
В случае разработки взорванных пород с различными значениями коэффициента разрыхления (Кр) и среднего размера взорванного куска (d,,) превышение возможной высоты отрабатываемого забоя (Hmax) над приведенной высотой приведено в табл. 2 [2].
Экспериментальными работами по оценке качества дробления пород карьера Мурунтау установлено, что величина среднего размера куска взорванных пород находится в пределах 14.5-28 см. В связи с этим из данных табл. 3 пред ставляется возможным в случае использования в карьере гидравлических экскаваторов принять относительное значение высоты забоя для ЭГ равным Hmax/1.6 • h’,^^ = 1.6. Тогда максимальная высота взорванного забоя для ЭГ равна Ну = Hmax = 1.6 • h’^^ = 1.6 • 0.7 • Н,^ = 1.12 Н,^.
С учетом изложенного и на основе паспортных технических параметров экскаваторов выполнено сравнение возможных высот взорванных забоев для канатных и гидравлических экскаваторов, используемых на карьере (табл. 3).
Из анализа данных, приведенных в табл. 3, видно, что при взрывании 15 м уступа и Кр = 1.3 (Ну = 19.0 м) только ЕХ3500 в состоянии отработать взорванный уступ, для остальных типов ЭГ необходимо разделение взорванного уступа на подуступы. В случае применения канатных экскаваторов такой проблемы не существует. Из изложенного видно, что шарнирное сочленение рукояти ковша со стрелой у гидравлических экскаваторов ограничивает высоту разрабатываемого забоя.
Рассматривая работу выемочно-погрузочного комплекса, в т.ч. ЭГ, за все время их эксплуатации, можно отметить, что в начальный период производительность экскаваторов
была достаточной для обеспечения запланированных объемов работ. В дальнейшем, по мере окончания гарантийного срока обслуживания и износа оборудования, материальные и трудовые затраты на поддержание экскаваторов в работоспособном состоянии возрастают за счет закупки запасных частей и увеличения затрат времени на выполнение ремонтных работ.
Проведенная технико-экономическая оценка показывает, что после 6-7 лет работы ЭГ существенно падает экономическая целесообразность дальнейшей их эксплуатации, т.к. снижается производительность и увеличиваются затраты на текущие и капитальные ремонты, которые перекрывают средства амортизационных отчислений.
Экскаватор ЭКГ15 — более ремонтопригоден чем ЭГ, т.к. не требует при производстве ремонтных работ (изготовлении новых деталей) такого класса чистоты обработки поверхностей, как для гидравлических систем. По этой причине нет возможности ремонта (восстановления) деталей ЭГ на имеющемся станочном оборудовании в ремонтной службе предприятия. Кроме того, для ремонта ЭГ необходимо содержание отдельного специализированного участка со специальным оборудованием, инструментом и приспособлениями.
За последние годы объем экскавации ЭКГ находится практически на одном уровне (17-18 млн. м3/год). Значительные аварийные простои ЭГ привели к падению объемов выемки горной массы в 2003 г. по сравнению с другими периодами времени. Производительность ЭГ на протяжении последних трех лет остается невысокой и если бы не ввод в эксплуатацию двух Rh300, то производительность карьера в 2004 г. не превысила бы 25-26 млн. м3 (объем выемки горной массы в 2004 г. составил 34.7 млн. м3).
Данное обстоятельство подтверждает вывод о том, что потенциал повышения производительности имеющегося экскаваторного парка полностью исчерпан. Необходимо его обновление, причем не за счет увеличения количества, а за счет ввода в эксплуатацию наиболее производительной техники.
Табл. 3 Возможная высота разрабатываемых забоев для ЭКГ и ЭГ
Модель |
Коэффициент |
Кусковатость взорванной горной массы ()ср, см |
Высота черпания Нч.тах, м |
Выс ота забоя (уступа) , м |
|
экскаватора |
разрыхления Кр |
без БВР, м |
с БВР, м |
||
Кан атные экскаваторы |
|||||
Ну — Нч.тах |
Ну — 1,5-Нч.тах |
||||
ЭКГ-10 |
13.5 |
13.0 |
20.0 |
||
ЭКГ-12,5 |
1.25- 1.35 |
20-10 |
15.5 |
15.0 |
22.0 |
ЭКГ-15 |
16.4 |
16.0 |
24.0 |
||
ЭКГ-20 |
17.8 |
17.5 |
26.0 |
||
Ну — 0,7-Нч.тах |
Ну — 1,12Нч.тах |
||||
RH-170 |
16.0 |
11.0 |
18.0 |
||
EX-3500 |
1.25-1.35 |
20-70 |
17.2 |
12.0 |
19.0 |
CAT-5230 |
14.8 |
10.5 |
16.5 |
||
RH-200 |
15.2 |
10.6 |
17.0 |
Табл. 2 Рекомендуемые относительные значения высоты забоев для ЭГ при различных свойствах взорванной горной массы
Взорванная горная масса, Кр |
Угол взорванного забоя, град. |
||||
При кусковатости ()ср, см |
Выход негабаритных |
||||
5-12 |
20-Ю |
40-60 |
кусков (5-8%) |
||
Связная Кр — 1.02-1.15 |
75-87 |
1.1 5 |
1. 1 |
1.05 |
1. 0 |
Связносыпучая Кр — 1.2-1.35 |
60-80 |
1. 9 |
1. 6 |
1.35 |
1.05 |
Связносыпучая Кр — 1.3-1.4 |
50-70 |
2.7 |
2.1 |
1. 7 |
1. 1 |
Сыпучая Кр — 1.4-1.5 |
32-50 |
3.8 |
3.5 |
3.2 |
— |
Рис. 4 Изменение аварийных простоев экскаваторов за период 1996-2004 гг.
Рис. 5 Изменение приведенной производительности
экскаватора в зависимости от срока его службы
Приведенные затраты на содержание экскаваторов с увеличением срока использования возрастают, причем эти затраты для ЭГ более чем в три раза превышают затраты на ЭКГ15 (рис. 4). Из-за изношенности оборудования за период эксплуатации возросли аварийные простои экскаваторов (рис. 5), причем наибольшее увеличение характерно для ЭГ; для ЭКГ15 за рассматриваемый период аварийные простои в среднем остаются на одном уровне, что свидетельствует о более надежной их работе. Аварийные простои являются одной из основных причин снижения производительности, особенно это наблюдается у ЭГ (рис. 6), где интенсивность уменьшения производительности по сравнению с ЭКГ15 более значительная. Если в первые годы эксплуатации производительность ЭГ была выше на 30-35%, чем у ЭКГ15, то при увеличении срока службы это отличие составляет всего 10-15%.
Несмотря на большие валютные затраты для ремонта и поддержания ЭГ в работоспособном состоянии (до 800 тыс. долл.), тенденция снижения их производительности не уменьшается, что в конечном итоге увеличивает себестоимость экскавации 1 м3 горной массы, почти в два раза превышая себестоимость погрузки ЭКГ15, которая остается прак тически неизменной на протяжении последних лет (рис. 7). При этом значительную долю в увеличении себестоимости экскавации ЭГ составляет расход дизтоплива (рис. 8), объем которого возрастает из-за физического износа дизельных двигателей, причем увеличение расхода особенно наблюдается после проведения ремонтных работ двигателей.
Невысокая надежность физически изношенных ЭГ не позволяет их использовать в настоящее время на ответ ственных направлениях и участках работ, т.к. возрастают риски срыва плановой выемки и погрузки горной массы, что влечет за собой необходимость в дополнительных пе регонах экскаваторов в карьере.
Оценивая результаты эксплуатации ЭГ на карьере Мурунтау в течение 1996-2004 гг., можно заключить, что на сегодняшний день дизельные гидравлические экскаваторы фактически утратили те преимущества (высокую мобиль ность и автономность; возможность лучшей селективной выемки горной массы из массива; производительность) пе ред канатными, ради которых они приобретались и использовались, несмотря на более высокие эксплуатационные затраты.
Рис. 6 Изменение себестоимости экскавации горной массы
Рис. 7 Изменение удельного расхода дизельного топлива
гидравлическим экскаватором с начала эксплуатации
Принимая во внимание окончание срока амортизации ЭГ, представляется целесообразным с целью унификации экска ваторного парка сократить типажный ряд ЭГ, используя при этом наиболее эффективное сочетание комплексов выемоч но-погрузочного и транспортного оборудования. В перспективе целесообразно выемочно-погрузочное оборудование карьера Мурунтау ориентировать на экскаваторы: ЭКГ15 в карьере и складах; ЭКГ8У — для выполнения работ в приконтурных зонах при постановке бортов карьера в предельное положение; ЭКГ10 на ППК, как наиболее соответствующих по своим параметрам железнодорожным думпкарам В105. На участках, требующих высокой концентрации и интенсивного ведения горных работ в значительных объемах (верхние горизонты юго-западной и восточной части карьера), предусматривается использование электрогидравличес ких экскаваторов большой единичной мощности Rh300.
Таким образом, эффективность использования экскаваторного парка определяется комплексом взаимосвязанных факторов, основными из которых являются технические возможности экскаватора, технологические параметры взорванной горной массы, соотношение высоты забоя и паспортной характеристики оборудования, обеспеченность забоев автотранспортом, а также стоимостные показатели работы экскаваторов.
ЛИТЕРАТУРА:
1. Беляков Ю.И. Выемочно-погрузочныеработы на карьерах. М., Недра, 1987,208 с.
2. Беляков Ю.И. Проектирование экскаваторных работ. М., Недра, 1983, 350 с.
Журнал «Горная Промышленность» №5 2005
mining-media.ru
экскаватор в карьере — Лучшее видео смотреть онлайн
Опубликовано: 11 часов назад
2 774 просмотра
Опубликовано: 18 часов назад
12 117 просмотров
Опубликовано: 12 часов назад
56 823 просмотра
Опубликовано: 50 лет назад
373 121 просмотр
Опубликовано: 1 час назад
28 194 просмотра
Опубликовано: 12 часов назад
3 843 просмотра
Опубликовано: 5 часов назад
16 378 просмотров
Опубликовано: 10 часов назад
21 988 просмотров
Опубликовано: 16 часов назад
4 901 просмотр
Опубликовано: 16 часов назад
2 235 749 просмотров
Опубликовано: 15 часов назад
15 437 просмотров
Опубликовано: 15 часов назад
52 568 просмотров
Опубликовано: 15 часов назад
1 526 326 просмотров
Опубликовано: 16 часов назад
129 324 просмотра
Опубликовано: меньше минуты назад
39 828 просмотров
Опубликовано: 17 часов назад
55 529 просмотров
Опубликовано: 17 часов назад
25 324 просмотра
Опубликовано: 50 лет назад
601 061 просмотр
Опубликовано: 12 часов назад
15 831 просмотр
Опубликовано: 16 часов назад
44 680 просмотров
luchshee-video.ru
Как правильно работать в карьере на экскаваторе
Как добывают известняк в Липецкой области
Как-то упоминал Пудлинговый карьер известняка в Свердловской области, но ЭТО.. нечто.
Оригинал взят у chistoprudov в Как добывают известняк.Подробный производственный репортаж из карьера Сокольско-Ситовского месторождения флюсовых известняков, расположенного в паре километров к северо-востоку от Липецка. Под катом большие экскаваторы, БелАЗы, фабрика, конвейеры, взрыв и многое другое…
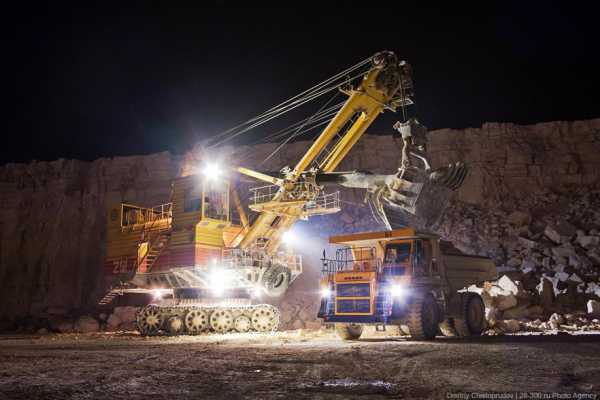
1. Немного официальных данных: Карьер разрабатывает ОАО «Студеновская акционерная горнодобывающая компания», в настоящее время предприятие входит в Группу НЛМК и является одним из российских лидеров по производству флюсовых известняков, применяемых главным образом в металлургической промышленности и строительстве.
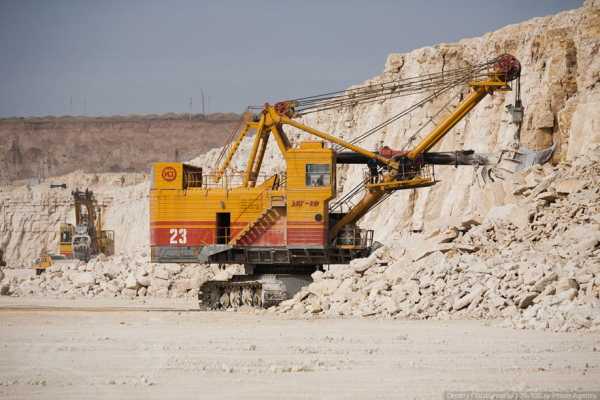
2. Объемы добычи составляют более 15% добываемого флюсового известняка в России.
3. Размеры карьера внушительные: 1500х500 метров, и глубина — 50 метров. Здесь спокойно можно построить больше 10 футбольных полей или проложить трассу для Формулы 1…
Увеличить изображение
4. По оценкам геологов, запасов сырья в карьере при нынешних мощностях хватит, как минимум, на 30 лет работы.
Увеличить изображение
5. Известняк — широко распространённая осадочная порода, образующаяся при участии живых организмов в морских бассейнах. Когда-то, примерно 350-370 миллионов лет назад до нашей эры, в Девонском периоде Палеозойской эры, Липецкая область, как и многие регионы центральной части России, была морем. Часто в осколках породы можно найти ископаемые остатки древней жизни тех лет…
6. Месторождение разрабатывается открытым способом. Технологический процесс добычи полезного ископаемого можно разделить на следующие основные виды работ:
Вскрышные работы
Добычные работы
Отвалообразование и горнотехническая рекультивация
Транспортные работы
Переработка полезного ископаемого
Увеличить изображение
7. Вскрышные работы.
Сначала с помощью бульдозера или погрузчика снимают верхний плодородный слой почвы — чернозем, и складируют его для последующей рекультивации земель, нарушенных горными работами. Далее следует глинистый слой толщиной около 20 метров, который отрабатывается электрическими экскаваторами с емкостью ковша 8 – 10 кубометров. К вскрышным работам относится также частичная выборка некондиционного (некачественного) известняка, который располагается непосредственно под слоем глины.
8. На этой фотографии хорошо виден срез «карьерного пирога»: слой глины, слой некондиционного известняка и ровный уступ полезного ископаемого. Осыпавшаяся горка известняка под уступом — последствие взрыва. Вот именно эти «последствия взыва» загружают в БелАЗы и отвозят на фабрику. А все вскрышные породы отвозят во внутренний отвал.
Увеличить изображение
9. Добычные работы.
У горняков принято говорить до́быча, с ударением на первый слог. Непосредственно добыче известняка, предшествуют буровзрывные работы — самая зрелищная часть всего процесса.
10. Твердый слой известняка, который невозможно зачерпнуть ковшом экскаватора, приходится бурить, закладывать в него взрывчатые материалы и взрывать. Для бурения используются буровые станки типа СБР, работающие от электричества.
11. Буровые станки серьезные, бурят на глубину до 24 метров (в 7 этажей) скважины диаметром 16 см. На бурение одной скважины уходит 50 минут. Вереницу скважин, вытянутых в линию, одну за одной бурят в 5 метрах от края обрыва.
12. Отважный бурильщик!
13. Для взрыва используют промышленные и конверсионные взрывчатые вещества, для приобретения которых нужна целая куча различных разрешительных документов и лицензий, а также специальный транспорт для перевозки и вооруженная охрана. Просто так порох на базаре не купить…
14. Тротиловые шашки служат детонатором.
15. В среднем, для осуществления одного взрыва бурят около 30 скважин, куда в общей сложности закладывается 5-6 тонн взрывчатки.
16. Для связи всех скважин с взрывчаткой в единую цепь используется детонирующий шнур.
17. Взрыв — дело очень ответственное! Карьер полностью оцепляют, в районе будущего взрыва выставляют охрану. Вся техника отводится на безопасное расстояние, а БелАЗы вообще уезжают из карьера. Перед взрывом происходит опрос всех постов оцепления по рации и выясняется обстановка. Если все нормально, дается разрешение на проведение взрывных работ. (Пост охраны и трансформаторную будку тоже увозят).
18. Скважины взрывают не одновременно, а с задержкой в несколько сотых долей секунды, иначе будет землетрясение, и у большей части зданий Липецка повылетают стекла.
19. Для ощущения масштаба — в правой части кадра стоит экскаватор размером с 4-этажный дом… Мелкие куски породы могут улетать на расстояние, сравнимое с высотой главного здания МГУ — на 250 метров.
20. Видно, как тяжелые куски твердой породы ровными рядами отделяются от уступа и падают вниз.
21. Весь взрыв проходит за несколько секунд и его хорошо слышно в городе. Так выглядит обвалившаяся порода. После того, как дым рассеется и осядет пыль, взрывники проверят наличие не сработавших зарядов, после чего экскаваторы и БелАЗы займутся своей работой.
22. Породу загружают в БелАзы с помощью механической лопаты (то есть экскаватора), а точнее — с помощью самоходной полноповоротной выемочно-погрузочной машины. Этот монстр работает на электричестве напряжением 6000 вольт, на фотографии видно высоковольтный кабель, который питает двигатели экскаватора. За сутки работы машина кушает энергии столько же, сколько обычный девятиэтажный жилой дом за неделю.
23. За один раз экскаватор может загрузить 10 обычных фотографов, или 20 фотографов-китайцев.
24.
25. Вес такого ковша — 16 тонн.
26. В каждом экскаваторе работает по два человека, для обеспечения непрерывности производственного процесса.
27. Всего в карьере работает 6 больших экскаваторов (ковш объемом 8 и 10 кубометров) и 2 поменьше, объемом ковша около 5-ти кубометров.
28. Иногда техника ломается. Например у этого экскаватора вышла из строя главная шестерня и его чинят прямо в карьере. Диаметр безвольно свисающих стальных канатов — 4 см.
29. А это — ныне списанный ветеран, честно отдавший предприятию около 40 лет. Несмотря на солидный возраст и потрепанный вид, дедушка, в случае крайней необходимости, может быть выведен на работу в карьер.
30. Отвалообразование и горнотехническая рекультивация.
При неизменной глубине чаша карьера постоянно движется в направлении, по которому залегает известняк. На одной стороне карьера происходит снятие вскрыши и добыча известняка, на другой — выработанное пространство заполняется вскрышными породами, отсевом дробления известняка и черноземом.
Увеличить изображение
31.
32. С дробильно-обогатительной фабрики в думпкарах привозят отсев, образующийся после дробления известняка и не пригодный для использования. Экскаватор переваливает все на отвал, заполняя выработанное пространство карьера. Потом отвалы засыпят ранее вскрытым грунтом и сверху черноземом.
33. Эта механическая лопата поменьше — с ковшом на 5 кубов.
34. Далее осуществляется вспашка земель и проводится биологическая рекультивация – засевание земель полезными растениями. Через несколько лет рекультивированные земли можно будет вновь использовать в сельскохозяйственных целях. Раньше карьер начинался прямо от посадок (справа в кадре) и за 20 лет сместился на 600 метров. Теперь там поле. В будущем карьер может продвинуться еще на 2,7 километра.
35. Транспортные работы.
Ежедневно на линии в карьере работает 12 БелАЗов, которые обеспечивают транспортировку вскрышной породы на отвалы, а добытый известняк на ДОФ — дробильно-обогатительную фабрику.
36. Белазисты работают круглосуточно в три смены, по восемь часов каждая. За сутки БелАЗ совершает до 100 ходок, и перевозит добытого известняка до 16 тысяч тонн. За три месяца машина пробегает расстояние от Москвы до Владивостока.
37. Грузоподъемность такого БелАЗа составляет 55 тонн, больше, чем его собственный вес. БелАЗы с большей грузоподъемностью в данном карьере использовать нецелесообразно по нескольким причинам: глубина карьера, расстояние транспортировки, объем добычи и так далее. Приводит в движение этого мамонтенка дизельный двигатель в 700 л/с.
38. Если при транспортировке из БелАЗов что-то вывалится на дорогу, например большой камень, специальный колесный бульдозер уберет его обратно в забой, к экскаватору.
39. В карьере активно борются с пылью, дороги постоянно обливаются специальной поливалкой. А зимой полив сменяется посыпкой песчано-соляной смесью.
40. Чтобы сделать этот кадр, пришлось попросить по рации водителя (каждая единица техники в карьере оснащена радиостанцией), чтобы тот проехал вне политой дороги. Допустимая скорость движения в карьере составляет 20 км/ч.
41. В карьере проложено 14 км технологических дорог, возведенных насыпным способом, также есть электрификация и подстанции, чтобы питать экскаваторы. Дороги отличные, по ним спокойно можно перемещаться на легковом автомобиле.
42. Цех по ремонту и обслуживанию БелАЗов.
43.
44. У этого БелАЗа сняли кузов и двигатель.
45. Добытое полезное ископаемое привозят на ДОФ и сгружают в приемный бункер, перед этим самосвал взвешивают и простым вычитанием веса пустого БелАЗа получают вес груза.
46. Приемный бункер.
47. Переработка полезного ископаемого.
Это первый корпус фабрики — корпус крупного дробления. Здесь на щековой дробилке происходит грубое дробление больших кусков породы. Получаются фракции величиной куска до 10 см.
48. Дальше по конвейеру материал поступает в корпус среднего дробления.
49. По конвейерной ленте за сутки транспортируется примерно 15 000 тонн породы.
50. Конусная дробилка осуществляет среднее дробление.
51. Хитрая система вибрационных грохотов. В закрытых устройствах продукция разделяется на фракции (по размерам камней) и распределяется по конвейерам.
52. В цехе легко поместится обычный пятиэтажный дом…
53. Совсем мелкий известняк — отсев до 1 см отправляют на выгрузку в думпкары для последующей перевозки его в отвал карьера.
54. Корпус сортировки и погрузки. Сюда поставляется готовый продукт, где происходит загрузка в ж/д вагоны. Основной потребитель продукции — Новолипецкий металлургический комбинат.
55.
56. В один вагон входит 69 тонн дробленого камня.
57.
58. Рядом происходит погрузка в автотранспорт.
59. Работа в карьере не останавливается и ночью. Для этого на экскаваторах работает подсветка.
60.
61. НЛО.
62. 55-тонные БелАЗы, применяемые на работах в карьере сравнительно невелики, а по горняцким меркам так и просто малыши. Когда-нибудь я обязательно посмотрю на работу 320-тонников!
63. Ночной карьер и фабрика прекрасны!
Отдельно хочется сказать про людей, с которыми я работал два съемочных дня. Открытые, добрые, веселые горняки, с удовольствием рассказывающие о своей работе и технике. Настоящие мужики!
Спасибо всем сотрудникам ОАО «Стагдок», кто участвовал в организации съемки!
Другие съемки карьеров:
Рассвет на карьере Михайловского ГОКа
Лебединский ГОК. Часть 1
Лебединский ГОК. Часть 2
Как доывают известняк
Каталог всех моих записей.
Все фотографии, представленные в этом репортаже, принадлежат фотоагентству «28-300», по вопросам использования снимков, а также проведения фотосессий пишите на электронную почту [email protected]
Tags: Работа
Tags: Как правильно работать в карьере на экскаваторе
Работа CAT-D8 & CAT-349D в Туапсинском карьере Адрес: Туапсинский район, с.Кривенковское, ул. Майкопская, 2 …
Как правильно называется человек управляющий экскаватором? | Автор топика: Федор
Артём машинист экскаватора
Геннадий Экскаваторщик
Владимир Экскаваторы они тоже разные бывают, общее название -экскаваторщик, а еще грейдерист, управляющий грейдером, машинист и т. д.
Роман Поднимите ЕТКС Ярослав Там даются определения профессий и характер выполняемой работы.
Леонид как хочешь так и называй. ему от этого зарплаты не прибавится
Василий экскаватор бульдозер
Как правильно работать на экскаваторе-Поставщик строительных …
Просмотр и скачка видео Как правильно работать на экскаваторе в хорошем качестве. … экскаватор в карьере. Просмотров: 2546 tow truck ltd …
Как правильно работать в карьере на экскаваторе | новое, 2017 год
Как правильно работать на экскаваторе подробнее по ссылке …. Гусеничный экскаватор Daewoo работает в карьере… Что нужно уметь экскаваторщику …
uvlechenie.info
Какой экскаватор нужен для песчаного карьера? | ООО «СПЕЦТРАНС»
22.02.2015
Для землеройных работ применяется тяжелая техника – экскаваторы, оснащенные ковшом. С их помощью производится погрузка сыпучих материалов. Чтобы добывать песок в Долгопрудном , нужно решить, какой тип экскаватора выбрать для работы в карьере – гусеничный или колесный.
Экскаваторы российского производства имеют маркировку, указывающую на все основные характеристики. Общая для всех марок первая буква – Э (экскаватор), вторая буква указывает на количество ковшей – О (1) и Д (2). Затем следуют три цифры, указывающие на емкость ковша, тип ходового устройства и тип подвески. И последние две буквы в маркировке указывают на тип климата и модернизацию агрегата. Прежде чем выбрать тип экскаватора, нужно определиться с предстоящим объемом работ и типом грунтов.
Теперь разберемся с особенностями экскаваторов.
Гусеничный экскаватор
При проведении работ в песчаном карьере есть вероятность, что колесные машины будут буксовать. В то же время конструктивные особенности гусеничного экскаватора позволяют с легкостью справляться с любым бездорожьем. К тому же он обладает высокой проходимостью, максимальной грузоподъемностью и устойчивостью.
Экскаваторы гусеничного типа отличаются высокой производительностью погрузочно-разгрузочных работ и отличной маневренностью. К тому же площадь гусеничной поверхности позволяет равномерно распределить давление груза на поверхность грунта.
Единственным недостатком гусеничной техники можно считать низкую скорость передвижения (5-10 км/ч). Но в условиях песчаного карьера этот недостаток несущественен. Когда требуется длительная работа на одном объекте, гусеничный экскаватор незаменим.
Колесная техника
Преимуществом техники на колесах является ее мобильность и вполне приемлемая скорость (25 км/ч). Когда возникает необходимость погрузочных работ сразу на нескольких участках, то выбор падает на колесные экскаваторы. Они гораздо быстрее могут быть перемещены с одного объекта на другой своим ходом по дорогам общего пользования.
Экономически целесообразно использовать колесные экскаваторы на площадках с твердым покрытием, поскольку на песчаных грунтах они буксуют. По сравнению со своими гусеничными собратьями они менее устойчивы, поэтому запрещена работа колесных экскаваторов на площадках со значительным уклоном или сложным рельефом.
tsptrans.com
Горные экскаваторы для эффективной работы в карьерах
Различная спецтехника используется в самых разных отраслях промышленности, в том числе и на ниве добычи полезных ископаемых. Горные экскаваторы относятся к спецтехнике активно используемой на всех этапах разработки, а именно: погрузка грунта и ископаемых в транспорт, разработка месторождений, организация отвалов, кроме того существует возможность применения данной техники и внутри зданий (складские работы). Существует возможность оснащения таких экскаваторов удлиненной оснасткой, при помощи такого оборудования можно разрабатывать пионерские траншей, а так же осуществлять погрузку в транспорт расположенный выше уровня экскаватора.
Основные отличия горных экскаваторов
Горные экскаваторы имеют множество преимуществ, они: производительны, имеют превосходную управляемость и маневренность, просты и неприхотливы в обслуживании. За счет современной и надёжной конструкции, а так же использования материалов повышенной прочности экскаваторы этого класса получили возможность работать практически в любых погодных и климатических условиях. Кабина оператора находится выше кузова экскаватора, что гарантирует великолепный обзор.
Электронные системы управления, которыми оснащён горный экскаватор, работают по принципу тиристорных преобразователей, что гарантирует плавное и бесступенчатое переключение всех основных приводов. Кроме того данный тип систем управления позволяет получать оптимальные рабочие показатели по схеме «генератор-двигатель». Системы управления такого рода экскаваторов полностью отвечают всем современным стандартам безопасности и оснащены необходимыми блокировками. Тиристорные преобразователи размещены блоками, что максимально облегчает их ремонт и диагностику.
Электрический экскаватор ЭКГ-8И является полноповоротной техникой и активно используется как при разработке полезных ископаемых, так и при масштабных строительных работах (например, возведение крупных промышленных комплексов). Основным источником питания такого рода экскаватора является высоковольтный переключательный пункт. Однако источник питания должен соответствовать всем нормативным и качественным документам, что должно контролироваться потребителем.
При получасовой непрерывной работе потребляемая мощность не превысит 250-275 кВт (коэффициент мощности при этом составляет 0,6). Стоит отметить, что кабель для передачи энергии от источника к потребителю следует выбирать исходя из погодных условий. Так для умеренного климата прекрасно подойдёт кабель КШВГ-Зх16+1х6, а в случае высокой температуры и влажности (тропики, субтропики) необходимо использовать кабель КШВГ-Т-Зх25+1хЮ.
Ходовая часть полноповоротного экскаватора состоит из: гусеничного хода, рамы, зубчатого венца, редуктор, гидравлический привод систем торможения, муфт обеспечивающих переключение хода. Источником питания для всей ходовой части служит электромотор, установленный в передней части рамы.
Работу вспомогательных систем (продувка, торможение поворотных и подъёмных систем и др.) обеспечивает пневматический привод. Источником питания пневматической системы служит достаточно производительный компрессор с рабочей мощностью 580 л/мин и давлением 0,7 МПа. Гидравлика обеспечивает работу систем торможения ходового агрегата, а так же механизма переключения гусениц экскаватора. Расположены основные элементы гидросистемы в задней части рамы.
Высокопроизводительные многоковшовые экскаваторы
Экскаваторы непрерывного действия предназначены для выполнения широкого спектра работ. К этому классу чаще всего относятся многоковшовые экскаваторы, однако существуют случаи, когда к ним относят бесковшовую (скребковую, фрезерную, шнековую) и комбинированную технику.
Многоковшовые экскаваторы работают по тому же принципу, что и простые (одноковшовые) и предназначены для тех же целей, а именно разработка грунта как выше уровня расположения техники, так и ниже.
Грузоподъёмность экскаватора зависит от следующих факторов: расположения центра тяжести, местом установки крюка, мощностью гидравлических систем, а также веса экскаватора. Чем массивнее общая конструкция техники, тем больший тоннаж можно обрабатывать.
Все рабочие показатели экскаваторов, а именно устойчивость и номинальная грузоподъемность экскаватора полностью продиктованы нормами SAE. Корпус конструкции техники и все механические соединения выполнены из стальных материалов самого высокого качества. Конструкция технического устройства, методы управления, размещение рабочих механизмов разработаны так, чтобы обеспечить максимальную производительность агрегата, с минимальными энергетическими затратами. Также, большое внимание уделяется безопасности и комфорту рабочего персонала, при управлении данным копательным приспособлением.
promplace.ru