Шпалы деревянные. Характеристики, технические требования.
Шпалы — это опоры для рельсов. Их назначение – принимать, упруго перерабатывать и передавать напряжение от рельсов непосредственно на балластную призму. В данной статье мы рассмотрим подробно деревянные шпалы.
Материал изготовления – породы хвойных деревьев. Это могут быть сосна, лиственница, ель, пихта, кедр. Для подъездных путей допускается применение берёзы.
Срок службы деревянных шпал варьируется от 7 до 40 лет, в зависимости от того, какая древесина была применена, а также насколько интенсивно они использовались; от внешних условий. Средний срок службы – около 16 лет.
По ГОСТу разделение происходит на 3 вида:
- обрезные (отёсанные со всех четырёх сторон)
- полуобрезные (отёсанные только с трёх сторон)
- необрезные (отёсанные только сверху и снизу)
По типу шпалы подразделяют на 1-й и 2-й тип.
Пропитка.
По обработке защитными средствами деревянные шпалы могут быть как пропитанные, так и непропитанные. Способы и материал пропитки также имеют подвиды.
Приоритетным способом пропитки является метод «вакуум-давление-вакуум», который нормирован ГОСТ в России.
· Пропитка древесины методом «вакуум-давление-вакуум» обеспечивает наиболее глубокое проникновение защитного средства и применяется для пропитки древесины, эксплуатируемых в тяжёлых условиях: шпал, опор ЛЭП связи, свай, мостов и др. Древесина должна быть сухой или подсушенной непосредственно перед пропиткой в том же автоклаве.
Пропитка шпал осуществляется каменноугольными маслами, креозотом, либо антисептиками ЖТК для пропитки железнодорожных шпал.
Для пропитки шпал производители используют комплекс оборудования: автоклавы, сушильные камеры, котлы-парообразователи и пр.
На деревянные шпалы расходуется очень много леса, но они, в отличие от железобетонных, лучше смягчают тряску.
Применяются деревянные шпалы чаще для трамвайных путей.
Характеристики.
1. Длина шпал зависит от ширины колеи. В России применяют деревянные шпалы длиной 275, 280 или 300 сантиметров.
2. Эпюра укладки шпал – этим термином называется количество шпал на один километр железнодорожного пути. В разных странах данный параметр колеблется от 1000 до 2200 шпал. В России по стандарту идут 3 варианта: 2000, 1840, 1600 либо 1440 шпал/километр. Зачастую применяется эпюра 1840 шт/км (46 шпал на 25 метров) на прямых участках и 2000 шт/км – на кривых.
Основные типы и размеры (согласно ГОСТ 78-2004).
1. Форма поперечного сечения шпал приведена на рисунках 1-3.
|
|
|
Рисунок 1 |
Рисунок 2 |
Рисунок 3 |
2. По размерам поперечного сечения шпалы изготовляют трех типов в зависимости от назначения:
I — для главных путей 1-го и 2-го классов, а также для путей 3-го класса при грузонапряженности более 50 млн. т км брутто/км в год при скоростях движения поездов более 100 км/ч;
II — для главных путей 3-го и 4-го классов, подъездных путей с интенсивной работой, приемоотправочных и сортировочных путей на станциях;
III — для любых путей 5-го класса, в том числе станционных, малодеятельных подъездных и прочих путей с маневрово — вывозным характером движения.
3. Размеры шпал в зависимости от типов должны соответствовать указанным в таблице 1 (см. ГОСТ 78-2004).
верхняя пласть шпалы: Пропиленная продольная поверхность шпалы, имеющая меньшую ширину.
нижняя пласть шпалы: Пропиленная продольная поверхность шпалы, имеющая большую ширину.
боковая сторона шпалы: Пропиленная продольная боковая поверхность шпалы.
обзольная часть шпалы: Непропиленные участки поверхности шпалы по верхней пласти и боковой стороне.
глубоконаколотая шпала: Шпала, подвергнутая специальной обработке путем глубокой наколки с целью увеличения глубины пропитки защитными средствами.
8. После сушки перед пропиткой шпалы должны быть укреплены от растрескивания одним из способов в соответствии с требованиями технологических процессов пропитки шпал на шпалопропиточных заводах и инструкции по содержанию деревянных шпал, переводных и мостовых брусьев железных дорог колеи 1520 мм. По согласованию с потребителем шпалы могут быть без укрепителей.
9. Шпалы следует изготовлять из древесины сосны, ели, пихты, лиственницы и березы.
10. Влажность древесины шпал при изготовлении не нормируется.
11. Качество древесины шпал должно соответствовать требованиям, указанным в таблице 2 (см. ГОСТ 78-2004).
12. Непропитанные шпалы должны быть рассортированы по каждому типу отдельно и по породам:
— сосновые;
— еловые и пихтовые;
— лиственничные;
— березовые.
13. Глубоконаколотые и укрепленные от растрескивания шпалы рассортировывают отдельно. Пропитанные шпалы рассортировывают по типам.
14. Непропитанные шпалы должны быть маркированы в соответствии с таблицей 3 (см. ГОСТ 78-2004).
15. Маркировка должна позволять идентифицировать предприятие-изготовитель. Маркировка должна быть четкой и нанесена клеймением или стойкой краской на один из торцов шпалы. Маркировка шпал после пропитки не возобновляется.
ООО «УралВнешТоргЭкспорт» поставляет деревянную шпалу 1 и 2 типов, как пропитанную, так и непропитанную. Пропитка осуществляется антисептиком «Элемсепт», либо «Креозот». Если Ваше предприятие заинтересовано в поставках шпалы на постоянной основе, мы готовы к долгосрочному и взаимовыгодному сотрудничеству. Работая на рынке железнодорожных материалов более 10-ти лет, ООО «УралВнешТоргЭкспорт» заявило о себе как надежная и устойчивая компания, которая не подводит своих партнеров.
Стать нашим клиентом Вы можете, оставив нам заявку.
Наши контакты:
Email:: [email protected]
Конт./тел.: 8 (343) 301-03-33.
Наша работа – залог Вашего успеха!
Железобетонные шпалы. История и современность
- Главная /
- Железобетонные шпалы. История и современность
Железобетонные шпалы. История и современность
В поисках антисептика для железнодорожной шпалы
06 декабря 2013 г.
В концессионный период железнодорожного строительства в России (вторая половина XIX века) размеры деревянных шпал стали задавать техническими условиями, которые разрабатывали отдельно для каждой магистрали. Применяемая в России длина шпал при этом колебалась от 2,34 до 3,2 м.
Распиловку заготовок вели вручную. Стоимость конечного продукта сильно зависела от числа резов. Самыми дешевыми, простыми в изготовлении и популярными были пластинные шпалы. Круглую заготовку просто продольно распиливали пополам.
В 1886 году был издан циркуляр, установивший шесть типоразмеров шпал, в котором основными признали брусковые. Пластинные разрешалось изготавливать только из дуба и лишь в крайнем случае – из древесины других пород.
Однако слабое развитие лесопильного производства мешало выполнять рекомендации Министерства путей сообщения. На деле частные дороги продолжали применять главным образом полулегальные пластины из сосны.
В 1900-м ведомство снова попыталось навести порядок в шпальном хозяйстве, отчасти узаконив сложившееся положение. При этом резко сокращалось количество годных для заготовки лесных пород: только сосна и дуб. Но на состоянии пути применение нового циркуляра особенно не сказалось. Пластинные шпалы гораздо быстрее брусковых повреждались и выходили из строя. Позже размеры шпал и требования к материалу неоднократно корректировались. В итоге пластинные, кроме дубовых, были-таки окончательно исключены из нормативов.
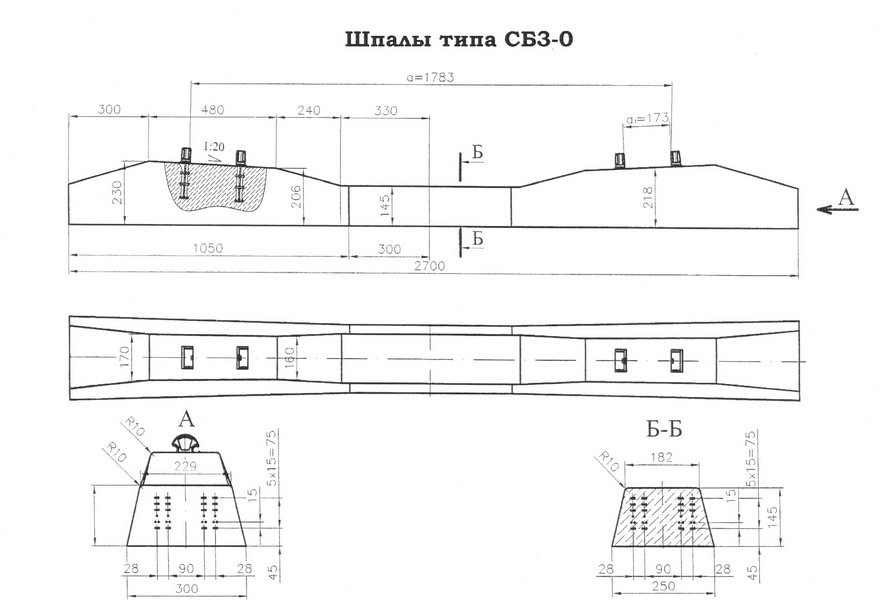
В начале ХХ века на железных дорогах России применяли деревянные шпалы 12 типоразмеров. Четырехгранные бруски заготавливались в основном для укладки на мостах и стрелочных переводах. Число шпал на километр пути было относительно невелико (от 1218 до 1500), но зато к ним предъявляли высокие требования. К примеру, до 1912 года еловые шпалы к укладке не допускали вообще, а позднее их разрешали применять только на станционных и подъездных путях.
Но из какого бы дерева ни производились эти элементы верхнего строения пути, у всех был недостаток – недолговечность. Пока дорог было мало, с этим еще как-то мирились. Но с 1880-х годов вырубка лесов в европейской части России стала массовой, что резко подняло цены на сырую древесину. Железно
дорожникам пришлось всерьез заняться решением проблемы продления срока службы шпал. Пионером в этой сфере стала Московско-Нижегородская магистраль, где впервые в России был создан специализированный шпалопропиточный завод.
Но далеко не везде применялся именно этот метод.
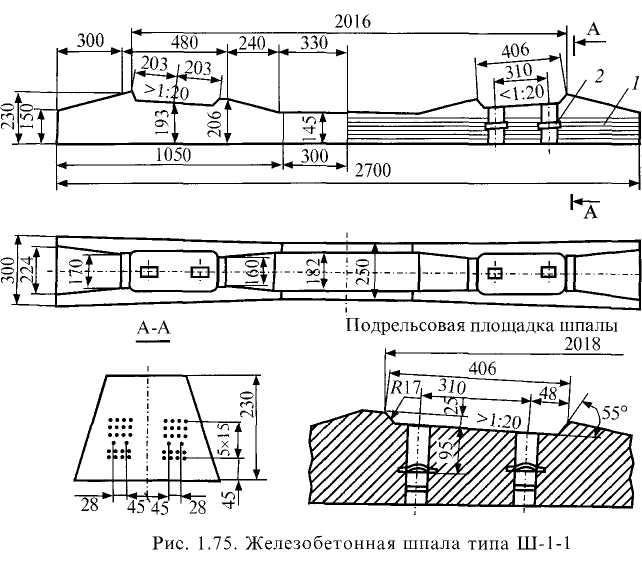
Интересно, что сейчас этот залив на западе Азовского моря, отделяющий Крым от материка, – курортная зона. А соли, использовавшиеся когда-то для пропит ки шпал, теперь считаются целебными.
С растрескиванием шпал боролись путем их обвязки и забивки различных скоб в торцы. А в 1910 году на XXVII Совещательном съезде инженеров службы пути была продемонстрирована деревянная шпала со сквозным металлическим нашпальником – полосой, к которой были присоединены фасонные упоры для рельсов.
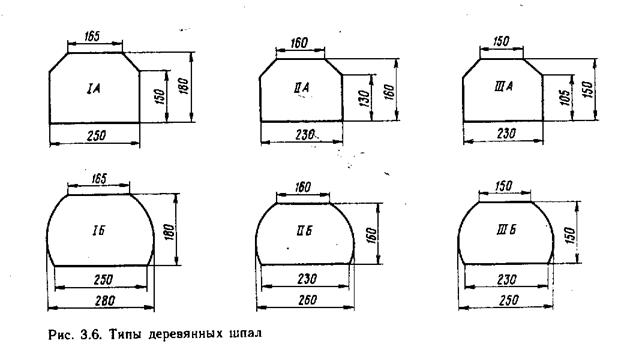
Во время Первой мировой, а потом и Гражданской войны шпальное хозяйство оказалось в плачевном состоянии. Меняться ситуация стала только в 1920‑е годы, когда был утвержден новый ведомственный стандарт. За пять лет в путь было уложено около 80 млн новых шпал. При этом пропитка применялась гораздо чаще, чем до революции. К 1940 году именно обработанные шпалы составляли уже 74 % от общего количества на сети.
Чаще всего старые шпалы уничтожались, однако некоторые из них получали вторую жизнь. Например, журнал «Путеец» в 1936 году рассказывал: «На Никопольской дистанции пути Сталинской железной дороги по инициативе бывшего начальника дистанции тов. Фиалковского создана замечательная столовая для путейцев. Особенность ее в том, что построена она из старых шпал при дружном участии всего коллектива. На каждой дороге в нынешнем году идет большая смена шпал.

Во время Первой мировой и Великой Отечественной войн деревянные шпалы также оказались весьма полезны родине. Их можно было относительно легко вывести из строя, что было весьма актуально при отступлении армий под натиском врага. Была создана даже специальная машина – путевой разрушитель, получивший название «Червяк», по фамилии военнослужащего, придумавшего это устройство. Путеразрушитель представлял собой огромную металлическую петлю из согнутых швеллеров, которая цеплялась к паровозу. Во время движения металлический крюк переламывал шпалы и деформировал рельсы, избавляя военных от необходимости взрывать полотно и тратить на это боеприпасы.
Там, где было возможно, путь старались сохранить. Рельсы, скрепления, стрелочные переводы и шпалы снимали, вывозили и использовали при строительстве новых линий, усилении и ремонте действующих магистралей.

Восстановление железных дорог началось задолго до завершения войны.
Масштабы работ были беспрецедентны. Так, только в 1943 году на освобожденной территории СССР было восстановлено 17,8 тыс. км главных путей, 2,1 тыс. км вторых путей и 1,7 тыс. км станционных путей. То есть всего – 21,6 тыс. км дорог.
Это больше, чем половина экватора.
Материалов катастрофически не хватало. Шпалы заготавливали не только специализированные предприятия, но и просто работники дороги, а также члены их семей. Так, в книге «Железнодорожники в Великой Отечественной войне» под редакцией Николая Конарева, возглавлявшего в 1980-х МПС СССР, расска зывается история о путеобходчике Петрозаводской дистанции пути Забайкальской дороги тов. Бянкине, который вместе с супругой лишь за одну военную зиму заготовил более 700 шпал.
К списку новостей
Краткий обзор: Материалы для железнодорожных шпал
Железнодорожные шпалы, или шпалы, как их называют в США, представляют собой довольно негламурный компонент железнодорожной отрасли. Но эти блоки, которые укладываются горизонтально под рельсы, чтобы удерживать рельсовые пути на нужной ширине колеи, составляют основу железнодорожного движения. Миллионы этих жизненно важных блоков производятся и распространяются каждый год, чтобы удовлетворить потребности в расширении сети и обновлении линейки.
Если не считать некоторых экспериментов со шпалами из каменных блоков на самых ранних этапах развития железнодорожного транспорта, древесина исторически была доминирующим материалом, используемым для железнодорожных шпал. В течение 20-го века появились новые материалы, отвечающие необходимости выдерживать более высокие нагрузки на ось и более высокие скорости. Здесь мы взвешиваем преимущества и недостатки предлагаемых материалов.
Деревянные шпалы
Учитывая, что древесина использовалась для изготовления железнодорожных шпал на протяжении большей части двух столетий, удивительно, что деревянные шпалы по-прежнему составляют большую часть рынка железнодорожных шпал. Это особенно характерно для США, где на древесину приходится 93% рынка — ежегодно укладывается 16 миллионов деревянных шпал.
Неслучайно господство на рынке древесины никогда не ослабевало. Естественные свойства древесины (обычно твердая древесина, такая как дуб, но более дешевая хвойная древесина используется на более легких и менее загруженных линиях) подходят для обеспечения упругой гусеницы с отличным динамическим ослаблением ударных нагрузок, а также снижением шума и вибрации.
«Железнодорожные шпалы прокладываются горизонтально под путями, чтобы удерживать рельсовые пути на нужной ширине колеи».
Деревянные шпалы также сравнительно дешевы, легки и просты в транспортировке, установке и обслуживании. Средняя деревянная шпала весит около 160-250 фунтов, тогда как эквивалентная шпала из бетона может весить до 800 фунтов. Это означает, что деревянные шпалы быстрее и проще устанавливаются на начальном этапе и практически не требуют специального оборудования или транспортных средств для обслуживания, что означает экономию средств для железнодорожных операторов.
Сторонники лесоматериалов для железнодорожных шпал также указали на сильный второй рынок бывших в употреблении деревянных железнодорожных шпал.
Существует быстро развивающийся бизнес по переработке бывших в употреблении железнодорожных шпал в качестве прочного материала для садоводства и ландшафтного дизайна или для использования в качестве топлива из биомассы для когенерационных электростанций. Однако большинство деревянных шпал пропитывают креозотом каменноугольной смолы, чтобы защитить их от износа под воздействием окружающей среды и заражения насекомыми. Креозот продлевает срок службы деревянных шпал (необработанные деревянные шпалы обычно необходимо заменять каждые 7–12 лет), но представляет собой токсическую опасность, которая создает дополнительные затраты на утилизацию и подрывает экологическую надежность традиционного материала для шпал в отрасли.
Древесина также гораздо более подвержена износу, чем более современные материалы для шпал. Операторы все чаще заменяют древесину бетоном или композитными материалами в районах, где солнце и сырость могут деформировать или сгнить древесину.
Бетонные шпалы
Хотя бетонные шпалы захватили лишь небольшую часть рынка в США, Европе и Японии, где железнодорожный транспорт, возможно, имеет более высокий приоритет, бетонные шпалы с конца Второй мировой войны. В Австралии бетон используется для большинства железнодорожных шпал, а в Великобритании железнодорожный оператор Network Rail ежегодно заменяет 200 000 деревянных шпал бетонными.
Бетонные шпалы обычно изготавливаются из литых бетонных плит, армированных изнутри стальной проволокой. Ранние прототипы, сделанные из обычного железобетона, часто оказывались слишком хрупкими, чтобы выдерживать высокие уровни динамической нагрузки. Современные бетонные шпалы в основном изготавливаются с использованием предварительно напряженного бетона — метод, при котором внутреннее напряжение прикладывается к шпале (обычно к каркасу из высокопрочной стальной проволоки) до того, как она будет отлита, чтобы противодействовать внешнему давлению, которому блоки подвергаются во время эксплуатации.
Производители бетона, такие как Abetong Teknik, INFRASET и Stanton Bonna, убедительно доказали эффективность бетона на рынке железнодорожных шпал. Этот материал требует меньшего ухода и имеет более длительный срок службы, чем деревянные шпалы, поскольку он не подвержен деградации окружающей среды, деформации или заражению насекомыми, а его негорючий характер означает, что он снижает вероятность возгорания путей.
«Древесина исторически была доминирующим материалом, используемым для железнодорожных шпал».
Шпалы из предварительно напряженного бетона также могут похвастаться более высокой грузоподъемностью и более плавным ходом благодаря большему весу и вертикальной/поперечной устойчивости. Для самых современных высокоскоростных линий бетон (или композитный пластик) становится необходимостью, чтобы выдерживать более высокие скорости
Но критики поспешили указать, что вес и объем бетонных шпал является существенным недостатком, когда речь идет о стоимости. – как по времени, так и по деньгам – первоначальной установки и последующего ремонта.
В то время как деревянные шпалы можно установить довольно быстро и с небольшим количеством специального оборудования, для установки бетонных шпал требуется тяжелая техника.
Поскольку для производства предварительно напряженного бетона требуется квалифицированная рабочая сила и специальное оборудование, этот высококачественный материал, безусловно, не является дешевым вариантом, хотя производители бетона утверждают, что долговечность материала означает более высокую ценность бетонных шпал в течение всего срока службы.
Ограниченное использование стальных шпал
Стальные железнодорожные шпалы часто считаются промежуточным звеном между деревом и бетоном. Более прочная, чем древесина, и менее дорогая, чем предварительно напряженный бетон, казалось логичным, что сталь может оказаться благом для компаний, стремящихся провести экономичную модернизацию гусениц. Действительно, в некоторых областях стальные шпалы по-прежнему работают должным образом после 50 лет службы. Меньшая зависимость от балласта (примерно на 60% меньше, чем требуется для бетона; на 45% меньше, чем для дерева) также, по-видимому, склоняет чашу весов в пользу стали, особенно в районах, где не хватает древесины.
Однако ряд уникальных проблем ограничил использование стали для изготовления шпал, особенно в США с обилием природных ресурсов древесины. Стальные шпалы подвержены коррозии, и в прошлом железнодорожные операторы сообщали, что стальные шпалы снимались с путей после того, как посадочные места рельсов быстро утомлялись, особенно на линиях с большим количеством поворотов.
«Бетонные шпалы обычно изготавливаются из литых бетонных плит, армированных изнутри стальной проволокой».
Capital Metro, транспортная служба города Остин, штат Техас, представляет собой хороший пример другой распространенной проблемы, связанной со стальными стяжками, — отсутствия изоляции. Неопреновая композитная изоляция отделяет стальные шпалы от электрифицированных рельсов, но любая ошибка может нанести ущерб железнодорожной сети. В отчете Austin American-Statesman в марте 2010 г. отмечалось, что из-за проблем с проводимостью и сбоев сигнала Capital Metro была вынуждена заменить длинные секции стальных шпал деревянными за дополнительную плату в размере 9 долларов.0,000. «Жаль, что я никогда этого не делал», — сказал газете менеджер железной дороги Capital Metro Билл Ле Жен.
Пластиковые композиты: материал будущего?
Самый современный материал, используемый для железнодорожных шпал, композитный пластик, представляет собой последнюю попытку производителей найти материал, отвечающий необходимым критериям и не имеющий существенных недостатков. Композитные шпалы изготавливаются из различных смесей сырья (пластика, резины из использованных шин, отходов стекловолокна) для создания синтетического материала, обладающего гибкостью и доступностью дерева в сочетании с долговечностью бетона.
Япония была лидером в производстве композитов. Японский производитель Sekisui Chemical поставил шпалы из вспененного уретана (FFU), армированного волокном, для высокоскоростного поезда Синкансэн. Ежегодно в стране укладывается 90 000 шпал FFU, из которых в настоящее время эксплуатируется около 1,5 миллиона.
Композитные шпалы Sekisui дебютировали в Европе в 2004 году, когда они были установлены на пути моста Цолламт в Вене, Австрия. Материал для моста был выбран потому, что он соответствовал характеристикам дерева, но при этом оставался устойчивым к перепадам температуры и постоянной влажности воздуха.
Преимущества композитов очевидны – материал можно обрабатывать и распиливать так же, как дерево, без каких-либо встроенных недостатков его полностью натурального аналога. Обладает прочностью бетона (срок службы композитов 50 и более лет), без веса бетона и громоздкости монтажа. В отличие от железобетонных шпал, для которых требуется капитальный ремонт пути, композитные шпалы можно устанавливать по частям вместе со старыми деревянными моделями.
«Композитные шпалы изготавливаются из различных смесей сырья».
Композитные шпалы имеют дополнительное преимущество, заключающееся в том, что они изготавливаются в основном из переработанного материала и полностью пригодны для вторичной переработки (их можно перерабатывать в новые шпалы). В отчете Программы действий по отходам и ресурсам (WRAP) за 2006 год отмечается, что на милю деревянных шпал требуется 810 взрослых дубов, в то время как эквивалентная длина составных шпал требует двух миллионов пластиковых бутылок, 8,9 миллионов пластиковых пакетов и 10 800 бывших в употреблении шин, которые иначе может оказаться на свалке.
Очевидно, что композитный материал (или производная от него технология) является ключом к созданию широко распространенного, экологически чистого и эффективного в эксплуатации материала для производства железнодорожных шпал. Из соображений стоимости, как правило, его использование ограничивается линиями, где древесина и бетон непригодны, но по мере того, как производственный процесс становится более совершенным и доступным для рынка шпал, кажется, что композиты не смогут догнать и перегнать древесину в качестве шпал. материал на выбор.
Железнодорожные шпалы Норвич и Ипсвич | Купить у поставщика № 1 в Восточной Англии
железнодорожных шпал Norwich & Ipswich | Покупайте у поставщика №1 в Восточной Англии | www.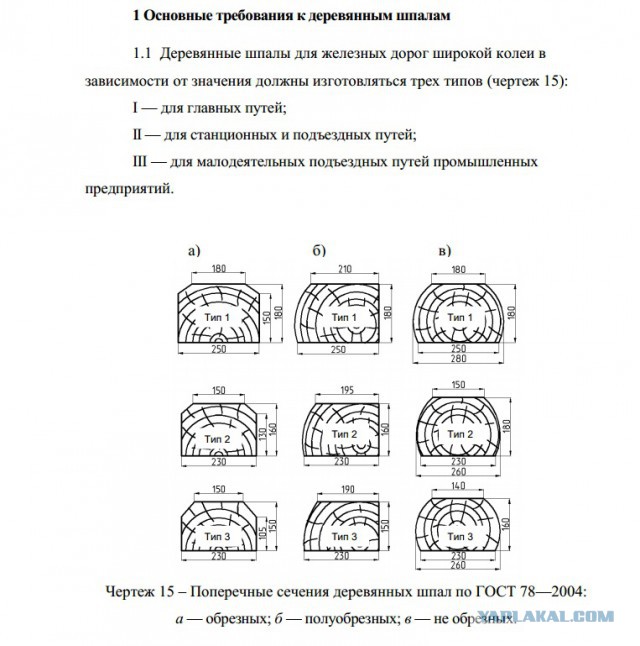