Способы и режимы закалки и отпуска стали
Термическая обработка сталей – одна из самых важных операций в машиностроении, от правильного проведения которой зависит качество выпускаемой продукции. Закалка и отпуск сталей являются одними из разнообразных видов термообработки металлов.
Тепловое воздействие на металл меняет его свойства и структуру. Это позволяет повысить механические свойства материала, долговечность и надежность изделий, а также уменьшить размеры и массу механизмов и машин. Кроме того, благодаря термообработке, для изготовления различных деталей можно применять более дешевые сплавы.
Также вам не помешает знать, как правильно варить полуавтоматом. Как закалялась сталь
Термообработка стали заключается в тепловом воздействии на металл по определенным режимам ля изменения его структуры и свойств.
К операциям термообработки относятся:
- отжиг;
- нормализация;
- старение;
- закалка стали и отпуск стали (и пр.).
Термообработка стали: закалка отпуск – зависит от следующих факторов:
- температуры нагрева;
- времени (скорости) нагрева;
- продолжительности выдержки при заданной температуре;
- скорости охлаждения.
Закалка
Закалка стали – это процесс термообработки, суть которого заключается в нагреве стали до температуры выше критической с последующим быстрым охлаждением. В результате этой операции повышаются твердость и прочность стали, а пластичность снижается.
При нагреве и охлаждении сталей происходит перестройка атомной решетки. Критические значения температур у разных марок сталей неодинаковы: они зависят от содержания углерода и легирующих примесей, а также от скорости нагрева и охлаждения.
После закалки сталь становится хрупкой и твердой. Поверхностный слой изделий при нагреве в термических печах покрывается окалиной и обезуглероживается тем более, чем выше температура нагрева и время выдержки в печи. Если детали имеют малый припуск для дальнейшей обработки, то брак этот является неисправимым. Режимы закалки закалки стали зависят от ее состава и технических требований к изделию.
Охлаждать детали при закалке следует быстро, чтобы аустенит не успел превратиться в структуры промежуточные (сорбит или троостит). Необходимая скорость охлаждения обеспечивается посредством выбора охлаждающей среды. При этом чрезмерно быстрое охлаждение приводит к появлению трещин или короблению изделия. Чтобы этого избежать, в интервале температур от 300 до 200 градусов скорость охлаждения надо замедлять, применяя для этого комбинированные методы закалки. Большое значение для уменьшения коробления изделия имеет способ погружения детали в охлаждающую среду.
Нагрев металла
Все способы закалки стали состоят из:
- нагрева стали;
- последующей выдержки для достижения сквозного прогрева изделия и завершения структурных превращений;
- охлаждения с определенной скоростью.
Изделия из углеродистой стали нагревают в камерных печах. Предварительный подогрев в этом случае не требуется, так как эти марки сталей не подвергаются растрескиванию или короблению.
Сложные изделия (например, инструмент, имеющий выступающие тонкие грани или резкие переходы) предварительно подогревают:
- в соляных ваннах путем двух-или трехкратного погружения на 2 – 4 секунды;
- в отдельных печах до температуры 400 – 500 градусов по Цельсию.
Нагрев всех частей изделия должен протекать равномерно. Если это невозможно обеспечить за один прием (крупные поковки), то делаются две выдержки для сквозного прогрева.
Если в печь помещается только одна деталь, то время нагрева сокращается. Так, например, одна дисковая фреза толщиной 24 мм нагревается в течение 13 минут, а десять таких изделий – в течение 18 минут.
Защита изделия от окалины и обезуглероживания
Для изделий, поверхности которых после термообработки не шлифуются, выгорание углерода и образование окалины недопустимо. Защищают поверхности от подобного брака применением защитных газов, подаваемых в полость электропечи. Разумеется, такой прием возможен только в специальных герметизированных печах. Источником подаваемого в зону нагрева газа служат генераторы защитного газа. Они могут работать на метане, аммиаке и других углеводородных газах.Если защитная атмосфера отсутствует, то изделия перед нагревом упаковывают в тару и засыпают отработанным карбюризатором, чугунной стружкой (термисту следует знать, что древесный уголь не защищает инструментальные стали от обезуглероживания). Чтобы в тару не попадал воздух, ее обмазывают глиной.
Соляные ванны при нагреве не дают металлу окисляться, но от обезуглероживания не защищают. Поэтому на производстве их раскисляют не менее двух раз в смену бурой, кровяной солью или борной кислотой. Соляные ванны, работающие на температурах 760 – 1000 градусов Цельсия, весьма эффективно раскисляются древесным углем. Для этого стакан, имеющий множество отверстий по всей поверхности, наполняют просушенным углем древесным, закрывают крышкой (чтобы уголь не всплыл) и после подогрева опускают на дно соляной ванны. Сначала появляется значительное количество языков пламени, затем оно уменьшается. Если в течение смены таким способом трижды раскислять ванну, то нагреваемые изделия будут полностью защищены от обезуглероживания.
Степень раскисления соляных ванн проверяется очень просто: обычное лезвие, нагретое в ванне в течение 5 – 7 минут в качественно раскисленной ванне и закаленное в воде, будет ломаться, а не гнуться.
Охлаждающие жидкости
Основной охлаждающей жидкостью для стали является вода. Если в воду добавить небольшое количество солей или мыла, то скорость охлаждения изменится. Поэтому ни в коем случае нельзя использовать закалочный бак для посторонних целей (например, для мытья рук). Для достижения одинаковой твердости на закаленной поверхности необходимо поддерживать температуру охлаждающей жидкости 20 – 30 градусов. Не следует часто менять воду в баке. Совершенно недопустимо охлаждать изделие в проточной воде.
Недостатком водяной закалки является образование трещин и коробления. Поэтому таким методом закаливают изделия только несложной формы или цементированные.
- При закалке изделий сложной конфигурации из конструкционной стали применяется пятидесятипроцентный раствор соды каустической (холодный или подогретый до 50 – 60 градусов). Детали, нагретые в соляной ванне и закаленные в этом растворе, получаются светлыми. Нельзя допускать, чтобы температура раствора превышала 60 градусов.
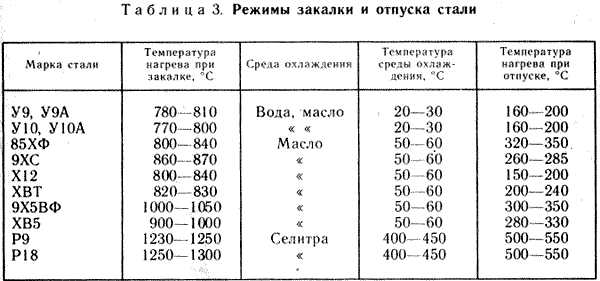
Пары, образующиеся при закалке в растворе каустика, вредны для человека, поэтому закалочную ванну обязательно оборудуют вытяжной вентиляцией.
- Закалку легированной стали производят в минеральных маслах. Кстати, тонкие изделия из углеродистой стали также проводят в масле. Главное преимущество масляных ванн заключается в том, что скорость охлаждения не зависит от температуры масла: при температуре 20 градусов и 150 градусов изделие будет охлаждаться с одинаковой скоростью.
Следует остерегаться попадания воды в масляную ванну, так как это может привести к растрескиванию изделия. Что интересно: в масле, разогретом до температуры выше 100 градусов, попадание воды не приводит к появлению трещин в металле.
Недостатком масляной ванны является:
- выделение вредных газов при закалке;
- образование налета на изделии;
- склонность масла к воспламеняемости;
- постепенное ухудшение закаливающей способности.
- Стали с устойчивым аустенитом (например, Х12М) можно охлаждать воздухом, который подают компрессором или вентилятором. При этом важно не допускать попадания в воздухопровод воды: это может привести к образованию трещин на изделии.
- Ступенчатая закалка выполняется в горячем масле, расплавленных щелочах, солях легкоплавких.
- Прерывистая закалка сталей в двух охлаждающих средах применяется для обработки сложных деталей, изготовленных из углеродистых сталей. Сначала их охлаждают в воде до температуры 250 – 200 градусов, а затем в масле. Изделие выдерживается в воде не более 1 – 2 секунд на каждые 5 – 6 мм толщины. Если время выдержки в воде увеличить, то на изделии неизбежно появятся трещины. Перенос детали из воды в масло следует выполнять очень быстро.
Процесс отпуска
Отпуску подвергаются все закаленные детали. Это делается для снятия внутренних напряжений. В результате отпуска несколько снижается твердость и повышается пластичность стали.
В зависимости от требуемой температуры отпуск производится :
- в масляных ваннах;
- в печах с принудительной воздушной циркуляцией;
- в ваннах с расплавленной щелочью.
Температура отпуска зависит от марки стали и требуемой твердости изделия, например, инструмент, для которого необходима твердость HRC 59 – 60, следует отпускать при температуре 150 – 200 градусов. В этом случае внутренние напряжения уменьшаются, а твердость снижается незначительно.
Быстрорежущая сталь отпускается при температуре 540 – 580 градусов. Такой отпуск называют вторичным отвердением, так как в результате твердость изделия повышается.
Изделия можно отпускать на цвет побежалости, нагревая их на электроплитах, в печах, даже в горячем песке. Окисная пленка, которая появляется в результате нагрева, приобретает различные цвета побежалости, зависящие от температуры. Прежде чем приступать к отпуску на один из цветов побежалости, надо очистить поверхность изделия от окалины, нагара масла и т. д.
Обычно после отпуска металл охлаждают на воздухе. Но хромоникелевые стали следует охлаждать в воде или масле, так как медленное охлаждение этих марок приводит к отпускной хрупкости.
elsvarkin.ru
Закалка стали – способы, температура, правила
Одним из наиболее распространенных способов термообработки металлов является закалка стали. Именно при помощи закаливания формируются требуемые характеристики готового изделия, а ее неправильное выполнение может привести к излишней мягкости металла (непрокаливание) или к его чрезмерной хрупкости (перекаливание). В нашей статье речь пойдет о том, что такое правильная закалка и что нужно сделать, чтобы ее выполнить.
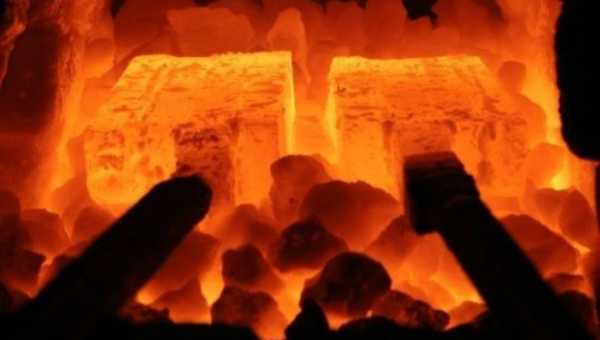
Закалка стали
Какой бывает закалка металла
О том, что воздействие высокой температуры на металл может изменить его структуру и свойства, знали еще древние кузнецы и активно использовали это на практике. В дальнейшем уже научно было установлено, что закалка изделий, изготовленных из стали, предполагающая нагрев и последующее охлаждение металла, позволяет значительно улучшать механические характеристики готовых изделий, значительно увеличивать срок их службы и даже в итоге уменьшать их вес за счет увеличения прочности детали. Что примечательно, закалка деталей из недорогих сортов стали позволяет придать им требуемые характеристики и успешно использовать вместо более дорогостоящих сплавов.
Смысл процесса, который называется закалка изделий из стальных сплавов, заключается в нагреве металла до критической температуры и его последующем охлаждении. Основная цель, которая преследуется такой технологией термообработки, заключается в повышении твердости и прочности металла с одновременным уменьшением его пластичности.
Существуют различные виды закалки и последующего отпуска, отличающиеся режимами проведения, которые и определяют конечный результат. К режимам закалки относятся температура нагрева, время и скорость его выполнения, время выдержки детали в нагретом до заданной температуры состоянии, скорость, с которой осуществляется охлаждение.
Наиболее важным параметром при закалке металлов является температура нагрева, при достижении которой происходит перестройка атомной решетки. Естественно, что для сталей разных сортов значение критической температуры отличается, что зависит, в первую очередь, от уровня содержания в их составе углерода и различных примесей.
После выполнения закалки повышается как твердость, так и хрупкость стали, а на ее поверхности, потерявшей значительное количество углерода, появляется слой окалины. Толщину этого слоя обязательно следует учитывать для расчета припуска на дальнейшую обработку детали.
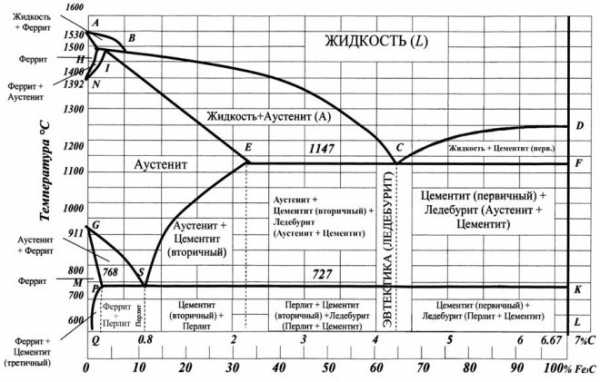
Диаграмма состояний железо-углерод
При выполнении закалки изделий из стальных сплавов, очень важно обеспечить заданную скорость охлаждения детали, в противном случае, уже перестроенная атомная структура металла может перейти в промежуточное состояние. Между тем, слишком быстрое охлаждение тоже нежелательно, так как оно может привести к появлению на детали трещин или к ее деформации. Для того, чтобы избежать образования таких дефектов, скорость охлаждения после падения температуры нагретого металла до 200 градусов Цельсия, несколько замедляют.
Для нагрева деталей, изготовленных из углеродистых сталей, используют камерные печи, которые могут прогреваться до 800 градусов Цельсия. Для закалки отдельных марок стали критическая температура может составлять 1250–1300 градусов Цельсия, поэтому детали из них нагреваются в печах другого типа. Удобство закалки сталей таких марок заключается в том, что изделия из них не подвержены растрескиванию при охлаждении, что исключает необходимость в их предварительном прогреве.
Очень ответственно следует подходить к закалке деталей сложной конфигурации, имеющих тонкие грани и резкие переходы. Чтобы исключить растрескивание и коробление таких деталей в процессе нагрева, его следует проводить в два этапа. На первом этапе такую деталь предварительно прогревают до 500 градусов Цельсия и лишь затем доводят температуру до критического значения.
Нагрев стали при закалке токами высокой частоты
Для качественной закалки сталей важно обеспечить не только уровень нагрева, но и его равномерность. Если деталь отличается массивностью или сложной конфигурацией, обеспечить равномерность ее нагрева можно только в несколько подходов. В таких случаях нагревание производится с двумя выдержками, которые необходимы для того, чтобы достигнутая температура равномерно распределилась по всему объему детали. Увеличивается суммарное время нагревания и в том случае, если в печь одновременно помещаются сразу несколько деталей.
Как избежать образования окалины и обезуглероживания при закалке
Многие детали из стали проходят закалку уже после того, как была выполнена их финишная обработка. В таких случаях недопустимо, чтобы поверхность деталей была обезуглерожена или на ней образовалась окалина. Существуют способы закалки изделий из стали, которые позволяют избежать таких проблем. Закалка, выполняемая в среде защитного газа, который нагнетается в полость нагревательной печи, может быть отнесена к наиболее передовому из таких способов. Следует иметь в виду, что используют такой метод лишь в том случае, если печь для нагрева полностью герметична.
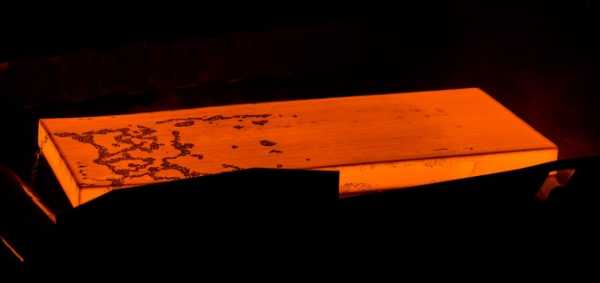
На фото виден момент гидросбива на стане горячей прокатки — удаление окалины
Более простым способом, позволяющим избежать обезуглероживания поверхности металла при закалке, является применение чугунной стружки и отработанного карбюризатора. Для того чтобы защитить поверхность детали при нагревании, ее помещают в специальную емкость, в которую предварительно засыпаны эти компоненты. Для предотвращения попадания в такую емкость окружающего воздуха, который может вызвать процессы окисления, снаружи ее тщательно обмазывают глиной.
Если после закалки металла его охлаждают не в масле, а в соляной ванне, ее следует регулярно раскислять (не менее двух раз за смену), чтобы избежать обезуглероживания поверхности детали и появления на ней окисла. Для раскисления соляных ванн могут быть использованы борная кислота, бурая соль или древесный уголь. Последний обычно помещают в специальный стакан с крышкой, в стенках которого имеется множество отверстий. Опускать такой стакан в соляную ванну следует очень осторожно, так как в этот момент на ее поверхности вспыхивает пламя, которое затухает через некоторое время.
Существует простой способ, позволяющий проверить качество раскисления соляной ванны. Для этого в такой ванне нескольких минут (3–5) нагревают обычное лезвие из нержавеющей стали. После соляной ванны лезвие помещают в воду для охлаждения. Если после такой процедуры лезвие не гнется, а ломается, то раскисление ванны прошло успешно.
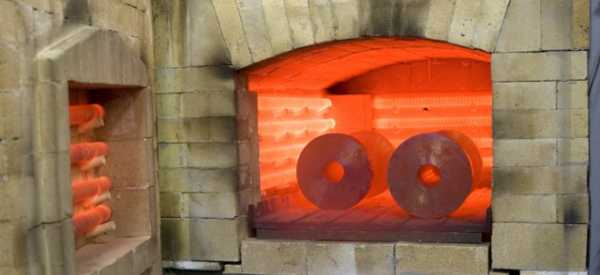
Объемная закалка толстостенных заготовок
Охлаждение стали при закалке
Основу большинства охлаждающих жидкостей, используемых при закалке изделий из сталей, составляет вода. При этом важно, чтобы такая вода не содержала в своем составе примесей солей и моющих средств, которые могут значительно повлиять на скорость охлаждения. Емкость, в которой содержится вода для закалки изделий из металла, не рекомендуется использовать в других целях. Важно также учитывать и то, что для охлаждения металла в процессе закалки, нельзя использовать проточную воду. Оптимальной для охлаждающей жидкости считается температура в 30 градусов Цельсия.
Закалка изделий из стали с использованием для их охлаждения обычной воды, имеет ряд существенных недостатков. Самый главный из них — это растрескивание и коробление деталей после их охлаждения. Как правило, таким способом охлаждения пользуются, когда выполняется цементирование металла, поверхностная закалка стали или термическая обработка деталей простой конфигурации, которые в дальнейшем будут подвергаться финишной обработке.
Для изделий сложной формы, изготовленных из конструкционных сталей, применяют другой тип охлаждающей жидкости – 50%-й раствор каустической соды, нагретый до температуры 60 градусов Цельсия. После охлаждения в таком растворе закаленная сталь приобретает светлый оттенок.
Очень важно при работе с каустической содой соблюдать технику безопасности, обязательно использовать вытяжку, размещаемую над ванной. При опускании раскаленной детали в раствор образуются пары, очень вредные для здоровья человека.
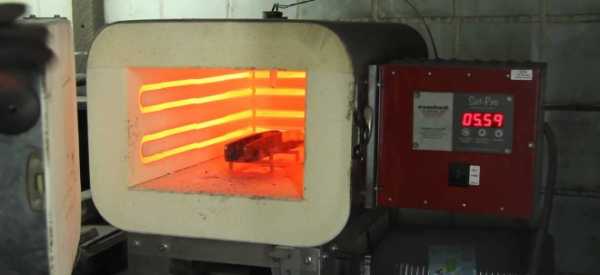
Закалка стали в муфельной печи
Лучшей охлаждающей жидкостью для тонкостенных деталей из углеродистых сталей и изделий, выполненных из легированных сплавов, являются минеральные масла, которые обеспечивают постоянную (изотермическую) температуру охлаждения, вне зависимости от условий окружающей среды. Главное, чего следует избегать при использовании такой технической жидкости, — это попадания в нее воды, что может привести к растрескиванию деталей в процессе их охлаждения. Однако, если в такую охлаждающую жидкость все же попала вода, ее можно легко удалить из нее, нагрев масло до температуры, превышающей температуру кипения воды.
У закалки стали с использованием масла в качестве охлаждающей жидкости есть ряд существенных недостатков, о которых обязательно стоит знать. При контакте масла с раскаленной деталью выделяются пары, вредные для человеческого здоровья, кроме того, масло в этот момент может загореться. У масляной ванны есть и такое свойство: после ее использования на детали остается налет, а сама охлаждающая жидкость со временем теряет свою эффективность.
Все эти факторы следует учитывать при выполнении закалки металлов в масляной среде и принимать следующие меры безопасности:
- погружать детали в масляную ванну при помощи щипцов с длинными ручками;
- все работы выполнять в специальной маске из закаленного стекла и в перчатках, изготовленных из толстой ткани с огнеупорными свойствами или из грубой кожи;
- надежно защищать плечи, шею, грудь рабочей одеждой, изготовленной из толстой огнеупорной ткани.
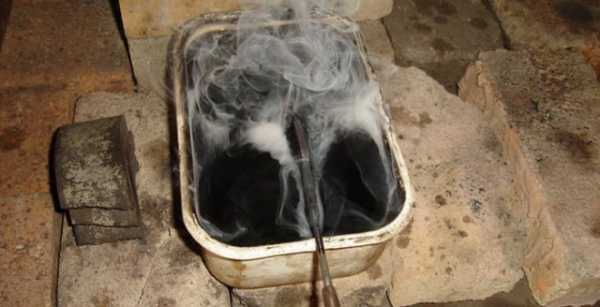
Охлаждение в масляной ванне
Для закалки сталей отдельных марок охлаждение осуществляют при помощи потока воздуха, создаваемого специальным компрессором. Очень важно, чтобы охлаждающий воздух был совершенно сухим, так как содержащаяся в нем влага может вызвать растрескивание поверхности металла.
Существуют способы закалки стали, при которых используют комбинированное охлаждение. К ним обращаются для охлаждения деталей из углеродистых сталей, имеющих сложный химический состав. Суть таких способов закалки заключается в том, что сначала нагретую деталь помещают в воду, где за короткое время (несколько секунд) ее температура снижается до 200 градусов, дальнейшее охлаждение детали проводят уже в масляной ванне, куда ее следует переместить очень оперативно.
Выполнение закалки и отпуска стальных деталей в домашних условиях
Термическая обработка металлических изделий, в том числе поверхностная закалка стали, не только увеличивает твердость и прочность сплава, но и значительно повышает внутренние напряжения в его структуре. Чтобы снять эти напряжения, способные в процессе эксплуатации детали привести к ее поломке, необходимо отпустить изделие из стали.
Следует иметь в виду, что такая технологическая операция приводит к некоторому снижению твердости стали, но увеличивает ее пластичность. Для выполнения отпуска, суть которого состоит в постепенном уменьшении температуры нагретой детали и ее выдерживании при определенном температурном режиме, используются печи, соляные и масляные ванны.
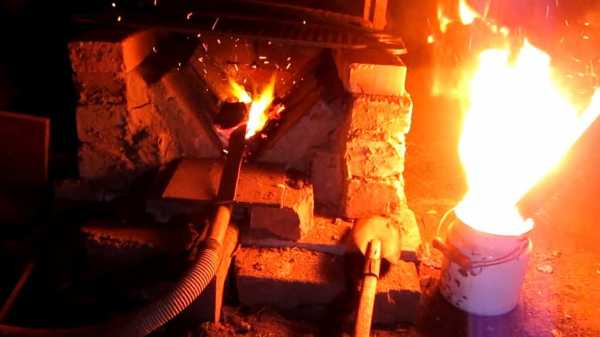
Закалка и отпуск стали в домашних условиях
Температуры, при которых выполняется отпуск, отличаются для различных сортов стали. Так, отпуск быстрорежущих сплавов проводится при температуре 540 градусов Цельсия, а для сталей с твердостью на уровне HRC 59-60 достаточно и 150 градусов. Что характерно, при отпуске быстрорежущих сплавов их твердость даже возрастает, а во втором случае ее уровень понижается, но значительно повышается показатель пластичности.
Закалка и отпуск изделий из стали, в том числе и нержавеющих сортов, вполне допустима (и, более того, часто практикуется) и в домашних условиях, если в этом возникла необходимость. В таких случаях для нагрева изделий из стали можно использовать электроплиты, духовки и даже раскаленный песок. Температуры, до которых следует нагревать стальные изделия в таких случаях, можно подобрать по специальным таблицам. Перед закалкой или отпуском стальных изделий, их необходимо тщательно очистить, на их поверхности не должно содержаться грязи, следов масла и ржавчины.
После очистки изделие из стали следует нагреть так, чтобы оно равномерно раскалилось докрасна. Для того чтобы раскалить его до такого состояния, необходимо выполнять нагрев в несколько подходов. После того, как требуемое состояние достигнуто, нагреваемое изделие следует охладить в масле, а затем сразу поместить в духовку, предварительно разогретую до 200 градусов Цельсия. Затем необходимо постепенно снизить температуру в духовке, доведя ее до отметки в 80 градусов Цельсия.
Данный процесс занимает обычно час. Дальнейшее охлаждение следует проводить на открытом воздухе, исключение составляют лишь изделия из хромоникелевых сталей, для снижения температуры которых используются масляные ванны. Обусловлено это тем, что стали таких марок при медленном охлаждении могут приобрести так называемую отпускную хрупкость.
Оценка статьи:
Загрузка…Поделиться с друзьями:
met-all.org
Закалка стали
Закалка сталиЗакалкой называется операция термической обработки, состоя¬щая из нагрева до температур выше верхней критической точки AC3 для доэвтектоидной стали и выше нижней критической точки АС1 для заэвтектоидной стали и выдержки при данной температуре с последующим быстрым охлаждением (в воде, масле, водных раство¬рах солей и пр.).
В результате закалки сталь получает структуру мартенсита и благодаря этому становится твердой.
Закалка повышает прочность конструкционных сталей, придает твердость и износостойкость инструментальным сталям.
Режимы закалки определяются скоростью и температурой на¬грева, длительностью выдержки при этой температуре и особенно скоростью охлаждения.
Выбор температуры закалки.
Температура нагрева стали для закалки зависит в основном от химического состава стали. При за¬калке доэвтектоидных сталей нагрев следует вести до температуры на 30 — 50° выше точки АС3. В этом случае сталь имеет структуру однородного аустенита, который при последующем охлаж¬дении со скоростью, превышающей критическую скорость закалки, превращается в мартенсит. Такая закалка называется полной. При нагреве доэвтектоидной стали до температур AC1 — АC3 в структуре мартенсита сохраняется некоторое количество оставше¬гося после закалки феррита, снижающего твердость закаленной ста¬ли. Такая закалка называется неполной.
Для заэвтектоидной ста¬ли наилучшая температура закалки — на 20—30° выше АС1 , т. е. неполная закалка. В этом случае сохранение цементита при нагреве и охлаждении будет способствовать повышению твердости, так как твердость цементита больше твердости мартенсита. Нагревать заэвтектоидную сталь до температуры выше Аст не следует, так как твердость получается меньшей, чем при закалке с температуры выше АС1,за счет растворения цементита и увеличения количества остаточного аустенита. Кроме того, при охлаждении с более высоких температур могут возникнуть большие внутренние напря-жения.
Скорость охлаждения.
Для получения структуры мартенсита требуется переохладить аустенит путем быстрого охлаждения ста¬ли,находящейся при температуре наименьшей устойчивости аусте¬нита, т. е.при 650—550° С.
В зоне температур мартенситного превращения, т. е,ниже 240°С, наоборот, выгоднее применять замедленное охлаждение, так как образующиеся структурные напряжения успевают выравняться, а твердость образовавшегося мартенсита практически не снижается.
Правильный выбор закалочной среды имеет большое значение для успешного проведения термической обработки.
Наиболее распространенные закалочные среды —вода, 5—10%-ный водный раствор едкого натра или поваренной соли и минераль¬ное масло. Для закалки углеродистых сталей можно рекомендовать воду с температурой 18° С; а для закалки большинства легирован¬ных сталей — масло.
Закаливаемость и прокаливаемость стали.
При закалке стали важно знать ее закаливаемость и прокаливаемость. Эти характерис-тики не следует смешивать.
Закаливаемость показывает способность стали к повы¬шению твердости при закалке. Некоторые стали обладают плохой закаливаемостью, т.е. имеют недостаточную твердость после за¬калки. О таких сталях говорят, что они «не принимают» закалку.
Закаливаемость стали зависит в основном от содержания в ней углерода. Это объясняется тем, что твердость мартенсита зависит от степени искажения его кристаллической решетки. Чем меньше в мартенсите углерода, тем меньше будет искажена его кристалли-ческая решетка и, следовательно, тем ниже будет твердость стали.
Стали, содержащие менее 0,3% углерода, имеют низкую зака¬ливаемость и поэтому, как правило, закалке не подвергаются.
Прокаливаемость стали характеризуется ее способ¬ностью закаливаться на определенную глубину. При закалке по¬верхность детали охлаждается быстрее, так как она непосредствен¬но соприкасается с охлаждающей жидкостью, отнимающей тепло. Сердцевина детали охлаждается гораздо медленнее, тепло из цент¬ральной части детали передается через массу металла к поверх¬ности и только на поверхности поглощается охлаждающей жидкостью.
Прокаливаемость стали зависит от критической скорости за¬калки: чем ниже критическая скорость, тем на большую глубину прокаливаются стальные детали. Например, сталь с крупным при¬родным зерном аустенита (крупнозернистая), которая имеет низ¬кую критическую скорость закалки, прокаливается на большую глу¬бину, чем сталь с мелким природным зерном аустенита (мелкозернистая), имеющая высокую критическую скорость закалки. Поэто¬му крупнозернистую сталь применяют для изготовления деталей, которые должны иметь глубокую или сквозную прокаливаемость, а мелкозернистую — для деталей с твердой поверхностной закален¬ной коркой и вязкой незакаленной сердцевиной. На глубину прокаливаемости влияют также исходная структура закаливаемой стали, температура нагрева под закалку и закалочная среда.
Прокаливаемость стали можно определить по излому, по микроструктуре и по твер-дости.
Виды закалки стали.
Су¬ществует несколько способов закалки, применяемых в за¬висимости от состава стали, характера обрабатываемой де¬тали, твердости, которую не¬обходимо получить, и усло¬вий охлаждения.
Закалка в одной среде схематично показана на рис. 1 в виде кривой 1. Такую закалку проще выполнять, но ее можно применять не для каждой стали и не для любых деталей, так как быстрое охлаждение деталей переменного сечения в боль¬шом интервале температур способствует возникновению температур¬ной неравномерности и больших внутренних напряжений, что может вызвать коробление детали, а иногда и растрескивание (если вели¬чина внутренних напряжений превзойдет предел прочности).
Чем больше углерода в стали, тем больше объемные изменения и структурные напряжения, тем больше опасность возникновения трещин.
Рис. 1. Кривые охлаждения для различных способов закалки
Заэвтектоидные стали закаливают в одной среде, если детали имеют простую форму (шарики, ролики и т. д.). Если детали слож¬ной формы, применяют либо закалку в двух средах, либо ступенча¬тую закалку.
Закалку в двух средах (кривая 2)применяют для инструмента из высокоуглеродистой стали (метчики, плашки, фре¬зы). Сущность способа состоит в том, что деталь вначале замачива¬ют в воде, быстро охлаждая ее до 300—400° С, а затем переносят в масло, где оставляют до полного охлаждения.
Ступенчатую закалку (кривая 3) выполняют путем быстрого охлаждения деталей в соляной ванне, температура кото¬рой намного выше температуры начала мартенситного превращения (240—250° С). Выдержка при этой температуре должна обеспечить выравнивание температур по всему сечению детали. Затем детали охлаждают до комнатной температуры в масле или на спокойном воздухе, устраняя тем самым термические внутренние напряжения.
Ступенчатая закалка уменьшает внутренние напряжения, ко¬робление и возможность образования трещин.
Недостаток этого вида закалки в том, что горячие следы не мо¬гут обеспечить большую скорость охлаждения при температуре 400—600° С. В связи с этим ступенчатую закалку можно применять для деталей из углеродистой стали небольшого сечения (до 8—10 мм). Для легированных сталей, имеющих небольшую критическую ско¬рость закалки, ступенчатая закалка применима к деталям большого сечения (до 30 мм).
Изотермическую закалку (кривая 4)проводят так же, как ступенчатую, но с более длительной выдержкой при темпера¬туре горячей ванны (250—300° С), чтобы обеспечить полный распад аустенита. Выдержка, необходимая для полного распада аустенита, определяется по точкам а и b и по S-образной кривой (см. рис. 1). В результате такой закалки сталь приобретает структуру игольча¬того троостита с твердостью HRC45 55 и с сохранением необхо¬димой пластичности. После изотермической закалки охлаждать сталь можно с любой скоростью. В качестве охлаждающей среды ис¬пользуют расплавленные соли: 55% KNO3 + 45% NaNO2 (темпе¬ратура плавления 137° С) и 55% KNO3 + 45% NaNO3 (температура плавления 218° С), допускающие перегрев до необходимой темпера¬туры.
Изотермическая закалка имеет следующие преимущества перед обычной:
минимальное коробление стали и отсутствие трещин; большая вязкость стали.
В настоящее время широко используют ступенчатую и изотерми¬ческую светлую закалки.
Светлую закалку стальных деталей проводят в специ¬ально оборудованных печах с защитной средой. На некоторых инст¬рументальных заводах для получения чистой и светлой поверхности закаленного инструмента применяют ступенчатую закалку с ох-лаждением в расплавленной едкой щелочи. Перед закалкой инстру¬мент нагревают в соляной ванне из хлористого натрия при темпера¬туре на 30—50° С выше точки АС1 и охлаждают при 180—200° С в ванне, состоящей из смеси 75% едкого калия и 25% едкого натра сдобавлением 6—8% воды (от веса всей соли). Смесь имеет тем¬пературу плавления около 145° С и, благодаря тому что в ней находится вода, обладает очень высокой закаливающей способ¬ностью.
При ступенчатой закалке стали с переохлажде¬нием аустенита в расплавленной едкой щелочи с последующим окон¬чательным охлаждением на воздухе детали приобретают чистую светлую поверхность серебристо-белого цвета; в этом случае отпа¬дает необходимость в пескоструйной очистке деталей и достаточна промывка их в горячей воде.
Закалка с самоотпуском широко применяется в инструментальном производстве. Сущность ее состоит в том, что детали не выдерживают в охлаждающей среде до полного охлажде¬ния, а в определенный момент извлекают из нее, чтобы сохранить в сердцевине изделия некоторое количество тепла, за счет которого производится последующий отпуск. После достижения требуемой температуры отпуска за счет внутреннего тепла деталь окончатель¬но охлаждают в закалочной жидкости.
Проконтролировать отпуск можно по цветам побежалости (см. рис. 2), появляющимся на зачищенной поверхности стали при 220—330° С.
Рис. 2. Цвета побежалости при отпуске
Закалку ссамоотпуском применяют для зубил, кувалд, слесарных молотков, кернеров и другого инструмента, требующего высокой твердости на поверхности и сохранения вязкой сердцевины.
Способы охлаждения при закалке.
Быстрое охлаждение стальных деталей при закалке является причиной возникновения в них боль¬ших внутренних напряжений. Эти напряжения иногда приводят к короблению деталей, а в наиболее тяжелых случаях — к трещинам. Особенно большие и опасные внутренние напряжения возни¬кают при охлаждении в воде. Поэтому там, где можно, следует ох¬лаждать детали в масле. Однако в большинстве случаев для деталей из углеродистой стали это невозможно, так как скорость охлаждения в масле значительно меньше критической скорости, необходи¬мой для превращения аустенита в мартенсит. Следовательно, мно¬гие детали из углеродистых сталей рекомендуется закаливать с ох-лаждением в воде, но при этом уменьшать неизбежно возникающие внутренние напряжения. Для этого пользуются некоторыми из описанных способов закалки, в частности, закалкой в двух средах, закалкой с самоотпуском и т. д.
Внутренние напряжения зависят также от способа погружения деталей в закалочную среду. Необходимо придерживаться следую¬щих основных правил:
детали, имеющие толстую и тонкую части, погружать в закалоч¬ную среду сначала толстой частью;
детали, имеющие длинную вытянутую форму (метчики, сверла развертки), погружать в строго вертикальном положении, иначе они покоробятся (рис. 3).
Рис. 3. Правильное погружение деталей и инструментов в за¬каливающую среду
Иногда по условиям работы должна быть закалена не вся деталь, а лишь часть ее. В этом случае применяют местную закалку: деталь нагревают не полностью, а в закалочную среду погружают целиком. В этом случае закаливается только нагретая часть детали.
Местный нагрев мелких деталей производят в соляной ванне, погружая в нее только ту часть детали, которую требуется закалить; так закаливают, например, центры токарных станков. Можно по¬ступать и так: нагреть деталь полностью, а охладить в закалочной среде только ту часть, которая должна быть закалена.
Дефекты, возникающие при закалке стали.
Недостаточная твердость закаленной детали — следствие низкой темепературы нагрева, малой выдержки при рабочей температуре или недостаточной скорости охлаждения.
Исправление дефекта: нормализация или отжиг с последующей закалкой; при¬менение более энергичной закалочной среды.
Перегрев связан с нагревом изделия до температуры, значительно превышающей необходимую температуру нагрева под закалку. Перегрев сопровождается образованием крупнозернистой структуры, в результате чего повышается хрупкость стали.
И справление дефекта: отжиг (нормализация) и последущая закалка с необходимой температуры.
Пережог возникает при нагреве стали до весьма высоких температур, близких к температуре плавления (1200—1300° С) в окислительной атмосфере. Кислород проникает внутрь стали, и по границам зерен образуются окислы. Такая сталь хрупка и исправить ее невозможно.
Окисление и обезуглероживание стали ха¬рактеризуются образованием окалины (окислов) на поверхности дета¬лей и выгоранием углерода в поверхностных слоях. Этот вид брака термической обработкой неисправим. Если позволяет припуск на механическую обработку, окисленный и обезуглероженный слой нужно удалить шлифованием. Чтобы предупредить этот вид брака, детали рекомендуется нагревать в печах с защитной атмосфе¬рой.
Коробление и трещины — следствия внутренних напряжений. Во время нагрева и охлаждения стали наблюдаются объемные изменения, зависящие от температуры и структурных пре¬вращений (переход аустенита в мартенсит сопровождается увеличе¬нием объема до 3%). Разновременность превращения по объему за¬каливаемой детали вследствие различных ее размеров и скоростей охлаждения по сечению ведет к развитию сильных внутренних нап¬ряжений, которые служат причиной трещин и коробления деталей в процессе закалки.
Образование трещин обычно наблюдается при температурах ниже 75—100° С, когда мартенситное превращение охватывает значительную часть объема стали. Чтобы предупредить образова¬ние трещин, при конструировании деталей необходимо избегать резких выступов, заостренных углов, резких переходов от тонких сечений к толстым; следует также медленно охлаждать сталь в зоне образования мартенсита (закалка в масле, в двух средах, ступенча¬тая закалка). Трещины являются неисправимым браком, коробле-ние же можно устранить последующей рихтовкой или правкой.
Основные превращения в железоуглеродистых сплавах при медленном нагревании и охлаждении
Линия на диаграмме Температура превращения, °С Описание превращения Обозначение критических точек
PSK 723 Превращение перлита в аустенит. Превращение аустенита в перлит Ac1, Ar1
MO 768 Потери магнитных свойств для сталей с содержанием углерода до 0,5%. Возникновение магнитных свойств для тех же сталей. Ac2, Ar2
GS 723-910 Окончание растворения феррита в аустените в доэвтектоидных сталях. Начало выделения феррита из аустенита в доэвтектоидных сталях. Ac3, Ar3
SE 723-1130 Окончание растворения цементита в аустените в заэвтектоидных сталях. Начало выделения цементита из аустенита в заэвтектоидных сталях. Acm, Arm
IE — Начало плавления стали при нагреве. Окончание затвердевания стали при охлаждении —
ECF — Начало плавления чугуна при нагреве. Окончание затвердевания чугуна при охлаждении —
Источник:
Остапенко Н.Н.,Крапивницкий Н.Н. Технология металлов. М. Высшая школа,1970г.
prominductor.ru
Закалка (металлов) — это… Что такое Закалка (металлов)?
Зака́лка — вид термической обработки изделий из металлов и сплавов, заключающийся в их нагреве выше критической температуры (температуры изменения типа кристаллической решетки, т.е. полиморфного превращения), с последующим быстрым охлаждением, как правило, в жидкости (воде или масле).
Различают закалку с полиморфным превращением, для сталей, и закалку без полиморфного превращения, для большинства цветных металлов.
Материал, подвергшийся закалке приобретает бо́льшую твердость, но становится хрупким, менее пластичным и вязким. Для снижения хрупкости и увеличения пластичности и вязкости, после закалки с полиморфным превращением применяют отпуск. После закалки без полиморфного превращения применяют старение. При отпуске имеет место некоторое снижение твердости и прочности материала.
В зависимости от температуры нагрева, закалку подразделяют на полную и неполную. В случае полной закалки материал нагревают выше линии GSE (см. диаграмму железоуглеродистых сплавов), в этом случае сталь приобретает структуру аустенит. При неполной закалке производят нагрев выше линии PSK диаграммы, что приводит к образованию избыточных фаз по окончанию закалки. Неполная закалка, как правило, применяется для инструментальных сталей
Закалка снимается отжигом материала.
В некоторых изделиях закалка выполняется частично, например при изготовлении японских катан, закалке подвергается только режущаяя кромка меча. Такая обработка оставляет на металле хамон — видимую границу между закаленным и незакаленным металлом.
Закалочные среды
При закалке для переохлаждения аустенита до температуры мартенситного превращения требуется быстрое охлаждение, но не во всём интервале температур, а только в пределах 650-400° С, то есть в том интервале температур в котором аустенит менее всего устойчив, быстрее всего превращается в феритно-цементитную смесь. Выше 650° С скорость превращения аустенита мала, и поэтому смесь при закалке можно охлаждать в этом интервале температур медленно, но, конечно, не настолько, чтобы началось выпадение феррита или превращение аустенита в перлит.
Механизм действия закалочных сред (вода, масло, водополимерная закалочная среда(Термат), а также охлаждение деталей в растворах солей) следующий. В момент погружения изделия в закалочную среду вокруг него образуется плёнка перегретого пара, охлаждение происходит через слой этой паровой рубашки, то есть относительно медленно. Когда температура поверхности достигает некоторого значения (определяемого составом закаливающей жидкости), при котором паровая рубашка разрывается, то жидкость начинает кипеть на поверхности детали, и охлаждение происходит быстро.
Первый этап относительно медленного кипения называется стадией плёночного кипения, второй этап быстрого охлаждения — стадией пузырчатого кипения. Когда температура поверхности металла ниже температуры кипения жидкости, жидкость кипеть уже не может, и охлаждение замедлится. Этот этап носит название конвективного теплообмена.
Способы закалки
- Закалка в одном охладителе — нагретую до определённых температур деталь погружают в закалочную жидкость, где она остаётся до полного охлаждения. Этот способ применяется при закалке несложных деталей из углеродистых и легированных сталей.
- Прерывистая закалка в двух средах — этот способ применяют при закалке высокоуглеродистых сталей. деталь сначала быстро охлаждают в быстро охлаждающей среде (например воде), а затем в медленно охлаждающей (масло).
- Струйчатая закалка заключается в обрызгивании детали интенсивной струёй воды и обычно её применяют тогда, когда нужно закалить часть детали. При этом способе не образуется паровая рубашка, что обеспечивает более глубокую прокаливаемость, чем простая закалка в воде. Такая закалка обычно производится в индукторах на установках ТВЧ.
- Ступенчатая закалка — закалка, при которой деталь охлаждается в закалочной среде, имеющей температуру выше мартенситной точки для данной стали. При охлаждении и выдержке в этой среде закаливаемая деталь должна приобрести во всех точках сечения температуру закалочной ванны. Затем следует окончательное, обычно медленное, охлаждение, во время которого и происходит закалка, т.е. превращение аустенита в мартенсит.
- Изотермическая закалка. В отличии от ступенчатой при изотермической закалке необходимо выдерживать сталь в закалочной среде столько времени, чтобы успело закончиться изотермическое превращение аустенита.
Источники
- БСЭ
- А.П. Гуляев «Металловедение» Москва Издательство «Металлургия» 1977
Wikimedia Foundation. 2010.
dic.academic.ru
Что такое закалка стали, виды закалки металла и применяемая температура
Для придания металлам определённых качеств, например, прочности, их подвергают специальной термической обработке, которая называется закалка. Во время этого процесса металл подвергают нагреву при очень высоких температурах, при этом доводят сталь до критической точки, а затем быстро охлаждают. Для быстрого охлаждения стали могут применяться в качестве охладителя сжатый воздух, водяной туман, жидкая полимерная закалочная среда.
Это сложный вид обработки металла, так как при этом металл становится не только прочным, но и не таким вязким и эластичным, как до обработки. Чтобы металлическое изделие после закалки получило необходимые качества, применяют различные виды закалки. Каким бы способом ни производилась закаливание, необходимо соблюдать определённые меры безопасности.
- Если деталь нужно опустить в масляную ванну, делать это только с помощью щипцов с длинными ручками.
- Маски для лица использовать только с закалёнными стёклами.
- Перчатки для работы должны иметь огнеупорные свойства.
- Для изготовления одежды должна применяться огнеупорная ткань.
Способы закалки стали
Есть несколько видов закалки, выбор которых зависит от того, какой состав имеет металл, какой характер у обрабатываемой детали, насколько необходимо увеличить прочность материала и при каких условиях будет происходить охлаждение. Способы, при которых происходит обработка металла, также можно разделить на несколько подвидов.
Использование одной среды
Способ достаточно прост, но он подходит не для каждой марки стали и не для всех деталей. В данном случае используется быстрое охлаждение с большим интервалом температур. В процессе обработки возникает температурная неравномерность и большое внутреннее напряжение в материале, что может привести к деформации изделия и даже к его разрушению. Материал, который имеет большое содержание углерода в своём составе, не подходит для такой обработки.
Закалка металла в несколько ступеней
При этом методе сталь после нагрева до нужной температуры погружают в соляную ванну. Это помогает выровнять ее температуру. После этого деталь охлаждают до обычной температуры с использованием масла или воздуха. При этом способе снимается внутреннее напряжение и повышаются механические качества изделия. Такой способ подходит для обработки небольших деталей.
Изотермическая
Такой вид обработки производится почти так же, как и ступенчатая закалка, но при этом изделие выдерживают в соляной ванне более длительное время. При применении изотермической закалки на качества детали скорость охлаждения не влияет. Преимущества такого вида закаливания в том, что сталь практически не коробится и полностью отсутствуют трещины. Металл становится более вязким.
Светлая
Для этой процедуры используют специальные печи, которые имеют защитную среду. Перед тем как заложить инструмент в такую печь, его подвергают нагреву в соляной ванне, которая содержит хлористый натрий, а затем охлаждают в ванне, содержащей смесь едкого калия и едкого натрия с небольшим добавлением воды.
Закаливание с самоотпуском
Такой способ подходит для инструментального производства. Суть такого метода в том, что нагретые детали извлекают из среды для охлаждения до того, как они полностью остынут. Таким образом удаётся сохранить немного тепла в сердцевине детали. Именно это тепло даёт возможность производить отпуск изделия. Только когда он произведён, изделие полностью охлаждают при помощи специальной жидкости. Такая термическая обработка применяется для стали, которая идёт на изготовление инструментов, требующих высокой прочности при эксплуатации.
Способы, применяемые для охлаждения
При быстром охлаждении закалённая сталь приобретает внутреннее напряжение, которое со временем приводит к тому, что детали, изготовленные из нее, начинают коробиться, и в них могут появиться трещины. Эти отрицательные качества сталь может получить, если её охлаждать в воде. Лучше для охлаждения использовать масло. Однако для некоторых деталей, при изготовлении которых применялась углеродистая сталь, использование масла не подходит, так как процесс охлаждения недостаточно быстр. В этом случае лучше использовать закаливание в двух средах, с самоотпуском или иной способ.
От того, каким способом деталь погружают в среду для закаливания, зависит внутреннее напряжение в металле. Основные правила, которых необходимо придерживаться при охлаждении, следующие:
- если по своей конфигурации деталь имеет тонкую и толстую части, то тогда охлаждают сначала толстую часть;
- чтобы детали длинной и вытянутой формы не покоробились, опускать их в закалочную среду необходимо вертикально;
- если нужно закалить только часть изделия, применяется местная закалка, но в среду для охлаждения погружают всю деталь.
Дефекты, возникающие при закалке металла
Если во время термообработки стали были нарушены технологические нормы, изделия могу иметь недостаточную твёрдость. Это происходит при недостаточно высокой температуре при нагреве и малой выдержке, а также если скорость охлаждения была недостаточной. Это можно исправить отжигом и повторной закалкой или применить более энергичную закалочную среду.
Иногда закалённая сталь получается с крупнозернистой структурой, что влечёт за собой повышенную хрупкость. Это является следствием перегрева изделия. Необходимо произвести отжиг и провести новую закалку при необходимой температуре. Если хрупкость появилась после пережога, исправить такой дефект невозможно.
Если после закалки деталь покоробило и появились трещины, значит, металл имеет высокое внутреннее напряжение. Такие дефекты появляются из-за неравномерного изменения объёма закаливаемой детали, если она имеет неодинаковые размеры и при этом нарушается режим охлаждения. Трещины исправить невозможно, а коробление можно устранить правкой или рихтовкой. Иногда на обрабатываемом изделии после закалки появляется окалина. Исправить такой брак невозможно. Этого можно избежать, если нагревать детали в печах, которые имеют защитную атмосферу.
tokar.guru
9. Назначение и сущность закалки стали. Способы закалки
Закалка — самый распространенный вид термической обработки. Закаливаются валы, шестерни, пружины, штампы, зубила, резцы, фрезы и другие изделия и инструменты. Столь широкое распространение этого вида термической обработки объясняется тем, что при помощи закалки и последующего отпуска можно изменить свойства стали в очень широком диапазоне. Были рассмотрены превращения, которые протекают в стали, имеющей структуру аустенита, при ее охлаждении с различной скоростью.
Закалка стали основана именно на этих превращениях. Операция закалки состоит в том, что стальные изделия нагревают немного выше критических температур Aci, Асз а иногда и Аст и затем быстро охлаждают. В качестве охлаждающей среды применяют воду, масло и растворы солей. Целью закалки чаще всего является повышение твердости и прочности стальных изделий. При закалке имеют место понижение пластичности и вязкости стали, однако эти качества можно восстановить при последующем отпуске.
Как известно из предыдущего, при увеличении скорости охлаждения аустенита можно получить структуры сорбита, троостита или мартенсита. При закалке, как правило, стремятся получить структуру мартенсита, которая обеспечивает максимальную твердость стали.
Структуру сорбита или троостита более целесообразно получать путем отпуска закаленной стали. Закалка является наиболее сложным видом термической обработки, так как она протекает при очень больших скоростях охлаждения, что связано с образованием значительных внутренних напряжений в металле. Поэтому даже небольшие отклонения от установленных режимов обработки приводят к браку в изделии. Существенное влияние на результаты закалки оказывают температура нагрева и скорость охлаждения изделия.
Способы закалки стали:
1. Закалка в одном охладителе (v1).
Нагретую до нужной температуры деталь переносят в охладитель и полностью охлаждают. В качестве охлаждающей среды используют:
воду – для крупных изделий из углеродистых сталей;
масло – для небольших деталей простой формы из углеродистых сталей и изделий из легированных сталей.
Основной недостаток – значительные закалочные напряжения.
2. Закалка в двух сферах или прерывистая (v2).
Нагретое изделие предварительно охлаждают в более резком охладителе (вода) до температуры ~ 3000C и затем переносят в более мягкий охладитель (масло).
Прерывистая закалка обеспечивает максимальное приближение к оптимальному режиму охлаждения. Применяется в основном для закалки инструментов (см. Подкладной инструмент).
Недостаток: сложность определения момента переноса изделия из одной среды в другую.
3. Ступенчатая закалка (v3).
Нагретое до требуемой температуры изделие помещают в охлаждающую среду, температура которой на 30 – 50oС выше точки МН и выдерживают в течении времени, необходимого для выравнивания температуры по всему сечению. Время изотермической выдержки не превышает периода устойчивости аустенита при заданной температуре.
В качестве охлаждающей среды используют расплавленные соли или металлы. После изотермической выдержки деталь охлаждают с невысокой скоростью.
Способ используется для мелких и средних изделий.
studfiles.net
Закалка и отпуск стали.
Целью закалки и отпуска стали является повышение твердости и прочности. Закалка и отпуск стали необходимы для очень многих деталей и изделий. Закалка основана на перекристаллизации при нагреве и предотвращении перехода аустенита в перлит путем быстрого охлаждения. Закаленная сталь имеет неравновесную структуру мартенсита, троостита или сорбита.
Чаще всего сталь резко охлаждают на мартенсит. Для смягчения действия закалки сталь отпускают, нагревая до температуры ниже точки А1. При отпуске структура стали из мартенсита закалки переходит мартенсит отпуска, троостит отпуска, сорбит отпуска.
Закалка стали. Температура нагрева стали при закалке та же, что и при полном отжиге: для доэвтектоидной стали на 30—50 °С выше точки Ас3, для заэвтектоидной — на 30—50° выше точки Aс1. При нагреве доэвтектоидной стали до температуры между точками Ас1 и Ac3 (неполная закалка) в структуре быстро охлажденной стали наряду с закаленными участками будет присутствовать нерастворенный при нагреве (в аустените) феррит, резко снижающий твердость и прочность. Поэтому для доэвтектоидной стали обязательна полная закалка с нагревом выше точки Ас3.
В заэвтектоидной стали избыточной фазой является цементит, который по твердости не уступает мартенситу и даже превосходит его, поэтому сталь достаточно нагреть на 30—50 °С выше точки Ас1.
Нагревать заготовки, особенно крупные, нужно постепенно во избежание местных напряжений и трещин, а время выдержки нагретых заготовок должно быть достаточным, чтобы переход в структуру аустенита полностью завершился.
Скорость охлаждения заготовок при закалке должна быть такой, чтобы получить заданную структуру. Критическая скорость закалки изменяется в широких пределах в зависимости от наличия легирующих компонентов в стали. Для простых сплавов железо—углерод эта скорость очень высока. Присутствие в стали кремния и марганца облегчает закалку на мартенсит, так как для такой стали С-образные кривые на диаграмме изотермического превращения аустенита будут сдвинуты вправо и критическая скорость закалки понижается.
Наиболее распространено охлаждение заготовок погружением их в воду, в щелочные растворы воды, в масло, расплавленные соли и т. д. При этом сталь закаливается на мартенсит или на бейнит.
При закалке применяют различные способы охлаждения в зависимости от марки стали, формы и размеров заготовки.
Простую закалку в одном охладителе (чаще всего в воде или водных растворах) выполняют, погружая в него заготовки до полного охлаждения. На рис. 2 режим охлаждения при такой закалке характеризует кривая 1.
Для получения наибольшей глубины закаленного слоя применяют охлаждение при интенсивном обрызгивании.
Прерывистой закалкой называют такую, при которой заготовку охлаждают последовательно в двух средах: первая среда — охлаждающая жидкость (обычно вода), вторая — воздух или масло (см. кривую 2 на рис. 2). Резкость такой закалки меньше, чем предыдущей. Рис. 2.
При ступенчатой закалке заготовку быстро погружают в соляной расплав и охлаждают до температуры несколько выше Мн. Выдержка обеспечивает выравнивание температуры от поверхности к сердцевине заготовки, что уменьшает напряжения, возникающие при мартенситном превращении; затем заготовку охлаждают на воздухе (кривая 3 на рис. 2).
Изотермическая закалка (закалка в горячих средах) основана на изотермическом распадении аустенита. Охлаждение ведется до температуры несколько выше начала мартенситного превращения (200—300 °С) в зависимости от марки стали. В качестве охладителя используют соленые расплавы или масло, нагретое до 200—250 °С. При температуре горячей ванны заготовка выдерживается продолжительное время, пока пройдет инкубационный период и период превращения аустенита (кривая 4 на рис. 2). В результате получается структура бейнита, по твердости близкая к мартенситу, но более вязкая и пластичная. Последующее охлаждение производится на воздухе.
При изотермической закалке вначале требуется быстрое охлаждение со скоростью не менее критической, чтобы избежать распадения аустенита. Следовательно, по этому методу можно закаливать лишь небольшие (диаметром примерно до 8 мм) заготовки из углеродистой стали, так как массивные заготовки не удается быстро охладить. Это не относится однако к легированным сталям, большинство марок которых имеют значительно меньшие критические скорости закалки. Большим преимуществом изотермической закалки является возможность рихтовки (выправления искривлений) заготовок во время инкубационного периода превращения аустенита (который длится несколько минут), когда сталь еще пластична.
Закалка при помощи газовой горелки. Кислородно-ацетиленовое пламя газовой горелки с температурой около 3200 °С направляется на поверхность закаливаемой заготовки и быстро нагревает ее поверхностный слой до температуры выше критической. Вслед за горелкой перемещается трубка, из которой на поверхность заготовки направляется струя воды, закаливая нагретый слой. Этот способ применяется для изделий с большой поверхностью (например, для прокатных валков, зубьев больших шестерен и т. д.).
Закалка токами высокой частоты по методу В. П. Вологдина нашла очень широкое применение в промышленности, так как отличается высокой производительностью, легко поддается автоматизации.
Обработка холодом. Этот метод применяется для повышения твердости стали путем перевода остаточного аустенита закаленной стали в мартенсит. Холодом обрабатывают углеродистую сталь, содержащую больше 0,5 % С, у которой температура конца мартен-ситного превращения находится ниже 00 С, а также легированную сталь (например, быстрорежущую).
Отпуск стали. Отпуск смягчает действие закалки, снимает или уменьшает остаточные напряжения, повышает вязкость, уменьшает твердость и хрупкость стали. Отпуск производится путем нагрева заготовок до температуры ниже критической; при этом в зависимости от температуры могут быть получены структуры мартенсита, троостита или сорбита отпуска.
При низком отпуске (нагрев до температуры 150—200 °С) в структуре стали в основном остается мартенсит, который однако имеет другую решетку, как сказано выше. Кроме того, начинается выделение карбидов железа из пересыщенного твердого раствора углерода в -железе и начальное скопление их небольшими группами. Это влечет за собой некоторое уменьшение твердости и увеличение вязкости стали, а также уменьшение внутренних напряжений в заготовках. Для низкого отпуска, заготовки выдерживают в течение определенного времени обычно в масляных или солевых ваннах. Если для низкого отпуска заготовки нагревают в атмосфере воздуха, то для контроля температуры часто пользуются цветами побежалости, появляющимися на зачищенной поверхности заготовки. Появление этих цветов связано с интерференцией белого цвета в пленках оксида железа, возникающих на поверхности заготовки при ее нагреве. Для углеродистой стали в интервале температур от 220 до 330 °С в зависимости от толщины пленки цвет изменяется от светло-желтого до серого. Для легированной стали соответствующие температуры выше. Низкий отпуск применяют для режущего инструмента из углеродистых и легированных сталей, измерительного инструмента, цементированных заготовок, а также других изделий, работающих в условиях трения на износ.
При среднем (нагрев в пределах 300—500 °С) и высоком (500—700 °С) отпуске структура мартенсита переходит соответственно в структуру троостита или сорбита. Чем выше температура отпуска, тем меньше твердость отпущенной стали и тем больше ее вязкость. При высоком отпуске сталь получает наилучшее сочетание механических свойств: повышенные прочность, вязкость и пластичность; поэтому закалку на мартенсит с последующим высоким отпуском называют улучшением стали. Средний отпуск применяют при производстве кузнечных штампов, пружин, рессор, а высокий—для многих деталей, подверженных действию высоких напряжений (например, осей автомобилей, шатунов двигателей).
studfiles.net