Что такое полимерное покрытие металла. Статьи Виды сварки Полимерное покрытие металла
Металлоконструкции в Череповце.
Порошковая окраска металлоизделий. Изготовление сварных металлоконструкций с полимерным покрытием.
« НазадЧто такое полимерное покрытие металла. 25.12.2015 06:30 Полимерное покрытие популярно благодаря своей чрезвычайной устойчивости ко всем видам воздействия со стороны внешних факторов, а также высокого эстетического уровня. Полимерное покрытие или, другими словами, порошковое окрашивание представляет собой процесс нанесения на металлические поверхности порошка с последующим образованием в печах полимеризации полимерного слоя. Затем изделие с нанесенной порошковой краской переносится в камеру полимеризации. Под действием высокой температуры (150° — 220°С) частицы порошковой краски плавятся, образуя равномерное полимерное покрытие. ![]() Оплавление порошковых красок происходит в три стадии: 1. порошок оплавляется и переходит в вязко-текучее состояние; 2. образуется непрерывный слой из оплавленных частиц порошка; 3. окрашиваемая поверхность смачивается расплавленным полимером, вследствие чего и формируется покрытие. Следует заметить, что твердая пленка при обработке образуется в зависимости от материала двумя способами: — для термореактивных материалов в результате отвердения или — для термопластичных материалов в результате охлаждения. Чаще всего слой полимерного покрытия порошковыми красками на металлических изделиях составляет 0,3мм. Данный метод ![]() Например, литые; автомобильные диски при окраске порошковыми красками надежно предохраняются от воздействия кислоты, солей и других дорожных реагентов. Кроме того,порошковое покрытие является ударопрочным и выдерживает значительные удары твердых тел: камней, песка и прочего дорожного мусора. Таким образом, при формировании полимерного покрытия из нанесенного порошкового слоя создается монолитное качественное покрытие на поверхности металлического изделия, а сама технология полимерной окраски порошковыми красками позволяет получить долговечное декоративно-защитное покрытие металла с отличными характеристиками и является экологически чистым способом. Достоинства порошковой окраски o Прочность и долговечность Помимо всего, этот тип окрашивания металла признан самым экологичным, а также отличается увеличенной адгезией к поверхности. ![]() |
Полимерное покрытие: виды, свойства, нанесение
Применение полимерных покрытий позволяет защитить металлические поверхности от коррозии, механических повреждений, внешних, химических и других воздействий. Они представляют собой порошкообразные вещества на основе различных смол и полимеров.
Для создания полимерных покрытий применяются следующие материалы:
-
Пластизоль
-
Полиэстер
-
Пурал
-
ПВДФ
Рассмотрим их подробнее.
Пластизоль
В состав данного покрытия входит поливинлхлорид (ПВХ) и вещества-пластификаторы. Слой нанесенного материала составляет 200 мкм, благодаря чему обеспечивается очень высокая степень защиты от механических воздействий. Помимо этого, ПВХ устойчив к агрессивным погодным условиям и химическим веществам.
Существует ограничение на применение пластизола в жарком климате, что обусловлено низкой термостойкостью покрытия – да +80 °C. Такое покрытие также склонно к быстрому выцветанию, поэтому для него используются только светлые тона, которые обладают высокими светоотражающими свойствами, меньше нагреваются и выгорают.
Покрытия на основе пластизола применяются для создания тисненых, фактурных оснований и штампованных рисунков. Благодаря таким декоративным свойствам они могут образовывать древесную, кожаную и другие виды текстур.
Полиэстер
Полиэстеровые покрытия – самая дешевая и распространенная разновидность материалов. Они медленно выгорают, что позволяет им длительное время сохранять свой цвет, и устойчивы к воздействию ультрафиолета. Такие покрытия обладают высокими антикоррозионными свойствами и не разрушаются от перепадов температур.
Отрицательной чертой полиэстера является невысокая прочность, которая является побочным эффектом тонкого слоя материала на поверхностях. Материал очень легко царапается и повреждается. Решить это возможно посредством обработки кварцевым песком. Но такая дополнительная процедура сделает процедуру нанесения дороже.
Существует две разновидности полиэстеровых покрытий: глянцевая и матовая. Они различаются только по свойствам. Матовое покрытие имеет шероховатую поверхность, может применяться для имитации текстуры и рельефа древесины, кирпича или камня, наносится толстым слоем, поэтому, в отличие от глянцевого, срок службы такого материала может достигать до 40 лет.
Пурал
Для изготовления пурала используется полиуретан и модифицированный полиамид. Данное покрытие имеет шелковисто-матовую поверхность и отличается невосприимчивостью к резким температурным передам и высокой термостойкостью.
Это очень долговечный материал – он может прослужить до 50 лет. Не смотря на тонкий слой (до 50 мкм), пурал очень трудно повредить. Помимо этого, данный вид покрытий не выцветает и выдерживает длительное воздействие агрессивных веществ.
Из минусов пурала можно выделить высокую стоимость и меньшую, чем у пластизоля, стойкость к пластическим деформациям. Но, несмотря на это, данный материал более оптимален по соотношению характеристик и стоимости.
Покрытия на основе пурала применяются на производствах кровельных элементов из оцинкованного металла. Они имеют красивый внешний вид, устойчивы к воздействию ультрафиолета и прекрасно защищают от коррозии.
ПВДФ
ПВДФ (полвинилденфторид) – одно из популярных видов полимерных покрытий. В его состав входит поливинилхлорид (80 %) и акрил (20 %). Благодаря стойкости к выцветанию и блестящей поверхности ПВДФ используется в декоративных целях: для придачи основаниям эффекта «металлик, глянцевого блеска, серебристых или медных металлических оттенков.
Покрытие обладает очень высокой стойкостью к механическим повреждениям и имеет наибольший срок службы. Оно также подходит для обработки изделий, работающих в агрессивных условиях.
Особый вид полимерных покрытий – антифрикционные твердосмазочные покрытия (АТСП). Они похожи на краски, но краситель в них заменен на мельчайшие истицы твердых смазок, распределенных по объему связующего вещества и растворителя.
Для производства полимерных АТСП используется политетрафторэтилен (тефлон, ПТФЭ), дисульфид молибдена, графит и другие твердосмазочные вещества. В качестве связующего могут выступать как органические, так и неорганические материалы: титанат, эпоксидная смола, акриловые, полиамид-имидные, фенольные и т.п. компоненты.
В России разработкой и изготовлением таких материалов занимается компания «Моделирование и инжиниринг». В линейку продукции входят антифрикционные твердосмазочные покрытия, предназначенные для решения различных задач, очистители и специальные растворители.
Полимерные покрытия MODENGY – MODENGY 1010, MODENGY 1011, MODENGY 1014 и другие – отлично зарекомендовали себя в подшипниках скольжения, направляющих скольжения, зубчатых передачах, других средне- и тяжелонагруженных узлах трения скольжения, крепеже и резьбовых соединениях, деталях двигателей транспортных средств (штоки клапанов, юбки поршней, дроссельные заслонки, коренные вкладыши, шлицевые соединения), трубопроводной арматуре, металлических и пластиковых элементах автомобильной техники (скобы, пружины, петли, замки, механизмы регулировки и т.п.), а также других парах трения металл-полимер, металл-резина, металл-металл, полимер-полимер.
Преимущества полимерных покрытий MODENGY:
-
Работоспособность в запыленной среде, вакууме и радиации
-
Низкий коэффициент трения
-
Высокие противоизносные, антикоррозионные и противозадирные свойства
-
Широкий диапазон рабочих температур
-
Устойчивость к кислотам, органическим растворителям, щелочам и прочим химикатам
-
Способность создавать на деталях тонкий защитный слой, практически не меняющий их исходный размер
Полимерные покрытия MODENGY позволяют эффективно управлять трением, повысить ресурс и эффективность оборудования, обеспечить поверхностям деталей необходимый набор защитных и триботехнических свойств.
Благодаря применению АТСП MODENGY можно полностью отказаться от пластичных масел и смазок. Технология твердой смазки позволяет создать узел трения, которому не требуется обслуживания. Антифрикционные покрытия наносятся однократно и обеспечивают смазывание и защиту различных деталей в течение всего срока их службы.
К полимерным покрытиям предъявляют достаточно серьезные требования. Во-первых, они должны обладать очень высоким сцеплением с поверхностью, так как они связываются с металлическим основанием на молекулярном уровне, а не просто его покрывают. Второе – устойчивость к различным деформациям, которая не позволяет покрытию разрушиться при механических воздействиях.
В-третьих, такие материалы не должны терять своих свойств при длительном воздействии воды, щелочей, растворителей, различных химикатов, высоких температур, УФ-излучения. Если покрытие отвечает всем этим запросам, область его применения существенно расширяется.
Преимущества:
-
Возможность выбрать практически любой цвет
-
Высокая адгезия
-
Экологичность
-
Высокая прочность
-
Термостойкость
-
Устойчивость к агрессивным веществам и воде
-
Непроницаемость
-
Диэлектрические свойства
-
Эстетичность
Поговорим о минусах полимерных покрытий. Главный из них – высокая стоимость, которая складывается из количества материала и применения специального оборудования. Но, наряду с этим, полимерный слой наносится на весь срок эксплуатации, а также не требует обновления или подкрашивания слоя. Поэтому окупаемость такого покрытия происходит очень быстро.
Сложное удаление с поверхности, в то же время, является и минусом. От них очень сложно очистить основания деталей, так как полимерные составы слабовосприимчивы к механическому воздействию и химикатам. Ввиду того, что специальных очистителей для удаления подобных материалов не существует, просто так стереть такой слой не получится. Это также обусловлено связью полимерного покрытия с поверхностью на молекулярном уровне. Чтобы его удалить, потребуется специальный инструмент.
Полимерные покрытия не получится нанести самостоятельно. Технологический процесс включает в себя применение определенного оборудования, которое можно найти только на предприятиях или специалистов, занимающихся выполнением подобных работ. При попытке нанесения с использованием подручных средств ничего не получится, а израсходованные средства будут потрачены впустую.
Ну и последний минус – нанесение полимерных покрытий, кроме антифрикционных, возможно только на металлы, которые хорошо проводят электричество. Это обусловлено применением технологии магнитной индукции для создания слоя покрытия.
Оборудование играет главную роль при нанесении, особенно краскопульт. Его особенность состоит в том, что кроме распыления материала, он заряжает его электричеством. На окрашиваемую деталь подается отрицательный заряд, а на бак краскопульта – положительный. Магнитная индукция возникает при контакте краски и поверхности покрываемого элемента. По своей природе она схожа с дуговой сваркой при замыкании электрода.
Нанесение состоит из нескольких этапов. Их качество напрямую зависит от умений маляра. Даже малейшие отклонения от технологии могут привести к порче изделий, а также полностью лишить полимерное покрытие рабочих характеристик.
В первую очередь производится подготовка окрашиваемых поверхностей. С них нужно удалить все возможные загрязнения и окислы, а затем обезжирить. Участки деталей, которым не требуется окраска, закрываются.
Следующий этап – нанесение. Сюда входит грунтование, окрашивание и лакирование. Все эти действия выполняются в специальных камерах, которые изолированы от проникновения пыли и других частиц. Сама камера должна иметь хорошее освещение, так как мастеру в процессе работы нужно видеть поверхность детали при любом ракурсе, чтобы правильно нанести покрытие. Сами детали подвешиваются на специальных крюках и на них подается отрицательный заряд. После этого следует нанесение. Вследствие того, что по технологии покрытие следует нанести одним слоем за один раз, этот процесс занимает очень много времени. При каких-либо паузах при нанесении полимерный слой будет неравномерным.
Далее следует отверждение покрытия. Детали медленно нагреваются в специальной камере с максимальной температурой +200 °C в течение 60 минут. Время и температура зависят от слоя. Так, например, для грунта нужно меньше времени и невысокие температуры, чем для отверждения лака. Правильность полимеризации также зависит от скорости повышения температуры в печи. Все дело в том, что при нагреве краска растекается по поверхности изделий и заполняет все труднодоступные места, а для этого нужно медленное и равномерное нагревание.
На следующем этапе детали охлаждаются. Для этого температура постепенно снижается до +100 °C. Для этого не требуется специальных приспособлений, так как печь остывает без постороннего вмешательства. При резком падении температуры до 100 °C покрытие на поверхности деталей может растрескаться. По этой же причине запрещается открывать печь.
После охлаждения изделий они извлекается из печи и доставляются в камеру покраски для напыления следующего слоя покрытия. Последний слой – декоративный, и его нанесение необязательно. Он лишь усиливает эстетичные свойства краски, а для обеспечения оптимальных защитных параметров достаточно двух слоев покрытия.
Возврат к списку
Полимерные покрытия металла и их особенности
Для изготовления металлочерепицы, сайдинга, профнастила, строительных конструкций, бытовой техники все чаще используется сталь с полимерным покрытием, так называемая «полимерка», «металлопласт». Полимерные покрытия для металла используются в Европе уже более 40 лет для придания строительным конструкциям декоративных свойств и защиты от коррозии. Металлы с полимерным покрытием объединяют в себе прочность стали с коррозийной стойкостью полимерного покрытия.
Цветовая палитра металла с полимерным покрытием весьма разнообразна, поэтому при выборе цвета обычно используют каталоги цветов либо образцы цвета. Покрытие может быть матовым и блестящим, иметь различную фактуру (в том числе имитировать дерево, камень и пр.).
Содержание
Структура стального листа с полимерным покрытиемНанесение полимерных покрытий на оцинкованную сталь — сложнейший процесс, так как стальной лист с полимерным покрытием имеет многослойную структуру: стальной лист, слой цинка, пассивирующий слой, слой грунта, с лицевой стороны — слой цветного полимера, а с нижней стороны листа «многослойный пирог» завершает защитная краска.
В качестве основы при изготовлении берется стальной прокат толщиной 0,4-2,0мм. На него может наноситься слой цинка (или алюмоцинка) как гальваническим методом, так и методом погружения в расплав. Иногда полимерное покрытие наносят сразу на черный металл (однако такие металлопласты очень недолговечны). Затем металл пассивируется, грунтуется и покрывается защитным слоем различных полимеров.
Полимерное покрытие получают различными методами:
- путём нанесения на полосу заранее изготовленной плёнки,
- погружением полосы в расплав полимера,
- валковым методом нанесения жидкого полимера(Coil Coating),
- напылением полимера в порошкообразном состоянии электростатическим методом.
Покрытие может быть как одностороннее, так и двустороннее. Прокат с односторонним полимерным покрытием – это прокат с двухслойным полимерным покрытием на лицевой стороне и однослойным полимерным покрытием на обратной стороне.
Двухслойное полимерное покрытие – покрытие, состоящее из слоя грунта и слоя отделочного полимера.
Однослойное покрытие – это, как правило, покрытие обратной стороны проката, состоящее из слоя защитной эмали без регламентирующих требований к внешнему виду, толщине, коррозионной стойкости и т.д.
Нанесение полимерного покрытия является заключительным этапом производства металлопроката. По желанию заказчика может наноситься защитная пленка из полиэтилена.
Таким образом, чаще всего сталь с полимерным покрытием имеет нижеприведенную структуру.
1 — стальной лист
2 — слой цинка
3 — пассивирующий слой (антикоррозионный слой)
4 — слой грунта
5 — полимерное покрытие
6 — защитная краска с обратной стороны
Грунтовочный слой предназначен для обеспечения прочного сцепления и высокой коррозионной стойкости всей системы, т.е. от качества грунтовки зависит, насколько будет крепко держаться полимерное покрытие.
Виды полимерных покрытий для стального листаВ качестве полимерных покрытий используют:
- полиэстер (полиэфир), обозначается PE.
SP;
- пищевой ламинат;
- полиэстер матовый, модифицированный тефлоном, PEMA;
- пурал — полиуретан, модифицированный полиамидом, PURAL;
- пластизоль поливинилхлоридный, PVS;
- поливинилиденфторид, PVDF, состоит из 80% поливинилхлорида и 20% акрила;
- акрил, AY.
Полиэстер является самым популярным покрытием из-за оптимального соотношения «цена-качество» и имеет удовлетворительную устойчивость к УФ-излучению и коррозии. Однако стойкость к механическим повреждениям выше у покрытий Пурал и PVDF.
Пурал дороже полиэстера, но он имеет и более высокую химическую стойкость, а также к механическому воздействию и перепадам температур.
Самым устойчивым к механическим повреждениям из-за толщины, но вместе с тем и наименее стойким к перепадам температур и к УФ-излучениям является пластизоль.
Самое долговечное и наиболее дорогостоящее покрытие – это поливинилиденфторид (PVDF).
Наименее долговечное и нестойкое к механическому и атмосферному воздействию-это акриловое покрытие.
Все эти покрытия могут иметь различную фактуру, блеск, цвета. Таким образом, полимерные покрытия имеют разную стойкость к ультрафиолетовому излучению, к высоким и низким температурам, атмосферному воздействию, к механическим повреждениям и другим
Вышеприведенные покрытия являются изначально жидкими и наносятся валковым методом, который является наиболее распространенным и востребованным как в России, так и в других странах.
Важнейшие требования к покрытиям – прочное сцепление (адгезия) отдельных слоев друг с другом, нижнего слоя с подложкой, твердость, прочность при изгибе и ударе, износосотойкость, влагонепроницаемость, атмосферостойкость, комплекс декоративных свойств (прозрачность или укрывистость, цвет, степень блеска, узор и др.).
Антикоррозионные защитные свойства покрытий для внутреннего использования классифицируются в соответствии со стандартом EU 10169:2008. Процесс испытаний во влажной камере регламентируется стандартом EN 13523-26.
- Возможность штамповки, профилирования, гибки металла в готовые изделия (металлочерепица, профилированный настил, детали бытовых приборов и пр.)
- Однородные и стабильные свойства по всей поверхности
- Прекрасные защитные свойства
- Атмосферостойкость
- Сохранение защитных и декоративных свойств более 10 лет
- Разнообразие цветов и фактур
Изготовлением металла с полимерным покрытием занимаются чаще всего металлургические заводы, производящие тонколистовую сталь. Наиболее известные из них: Новолипецкий металлургический комбинат, Череповецкий металлургический комбинат, международные концерны Arcelor Mittal, RАUТАRUUККI OY (Финляндия), ЕСО STAНL (Германия), ISPAT KARMET (Караганда, Казахстан), HOGOVENS (Голландия), BRITISH STEEL (Великобритания), MIRIAD (Франция ) SSAB TUNNPLAT AB ( Швеция ). Однако, сейчас появляется все больше и больше производителей, оказывающих услуги по нанесению полимерных покрытий на любой необходимый заказчику типоразмер листа металлургических гигантов.
Металл с полимерным покрытием применяется в основном для изготовления профиля. Пример линий от китайских партнеров.
Автор Ирина Химич.
Как выполняется полимерная покраска металла
- СОДЕРЖАНИЕ:
- • Как выполняется операция
- • Способ обработки металлических рулонов
- • Обработка металлоконструкций
- • Виды полимерных красок
- • Преимущества полимерных красок
- • Как выбрать краску
- • Область применения окрашивания
- • Подготовка поверхности
Полимерная покраска металла пришла на смену более традиционным способам.
Технология заключается в нанесении на поверхность спекаемого порошкообразного красителя из полимеров. В обиходе его называют
«сухой покраской», по причине отсутствия растворителя. Порошковый состав краски состоит из эпоксидных и полиэфирных смол.
Термическое воздействие образует плотный слой, сроки службы не менее 20 лет.
Как выполняется операция
- 1 этап – предварительно металл обезжиривают, удаляют с него всю грязь, обрабатывают специальным составом – фосфатирование, который повышает адгезию и антикоррозийные свойства;
- 2 этап – наносится слой краски;
- 3 этап – спекание покрытия и полимеризация в сушильной печи, для формирования пленочного покрытия. К примеру, оцинкованные листы с полимерным покрытием используются в фасадных и кровельных работах.
Способ обработки металлических рулонов
Окрашенный прокат получают путем нанесения полимерной покраски толщиной до 200 мкм, покрытие может быть
одно- и двуслойным. Изделия из оцинкованной стали, покрытые специальным составом полимерного слоя, эффективнее
справляются с коррозией и обладают широкой сферой применения. Распространенные полимерные краски – полиэстер матовый, алюцинк, пурал и пластизол.
Обработка металлоконструкций
Преимущества обработки металлоконструкций с точки зрения нанесения – отсутствует неприятный запах, после нанесения не оставляет потеков, пузырей и трещин. Полезные свойства порошковой краски:
- • антикоррозионная защита;
- • электроизолирующие свойства;
- • невосприимчивость к ультрафиолету;
- • устойчивость к механическим нагрузкам;
- • широкий диапазон температурной эксплуатации;
- • декоративные свойства.
Виды полимерных красок
Полимерные краски бывают всех цветов и оттенков радуги. Но кроме цвета, есть и другие классификации. Например,
в зависимости от материала, который образует полимерную гладкую плёнку при покраске, порошки могут быть: эпоксидными,
полиамидными, полиэфирными, полиэфирно-эпоксидными и сделанными на основе эпоксидных смол.
Фактура полимерной краски может быть матовой, глянцевой или текстурной, а также различают оттенки «муар» и «металлик».
Красители бывают для наружных работ и для внутренней отделки металлоизделий.
В зависимости от способа застывания полимеры тоже бывают разные: есть такие, которые «схватываются» на поверхности
изделия методом простого нагревания, а есть краски, застывающие только под воздействием ультрафиолетового излучения.
Если покрытие формируется в следствие химической реакции – это термоактивная краска, а если методом плавления и
нагревания в камере полимеризации, то это – термпластичнае покрытие.
Преимущества полимерных красок
Порошковые красители имеют ряд преимуществ, за счёт которых ими можно обрабатывать наружные и внутренние изделия из разных видов металла.
К достоинствам полимеров относятся:
— им не страшны механические повреждения: если металлоизделие повредится или деформируется, то окраска просто примет новую форму, оставшись на поверхности;
— водо- и влагозащищённость: полимерное покрытие не утрачивает свои качества, даже если изделие длительное время находится в воде или под водой;
— стойкость к воздействию УФ-лучей: в то время, как другие виды красок от солнечного света могут выцвести, разрушиться и потерять все свои свойства,
полимерное покрытие останется такими же прочным и ярким, с ним ничего не случится даже в самый солнечный день;
— могут выдерживать огонь и высокую температуру: так как полимерное окрашивание производится под сильным тепловым воздействием, то в дальнейшем высокий
температурный режим покрытию не страшен; порошковой краской можно даже покрасить мангал и котёл отопления.
— не разрушается от химических веществ.
Как выбрать краску
Полимерную краску выбирают в зависимости от вида работы, изделия и места его дальнейшего использования. Для отделки элементов в помещении выбирают экологически чистые красители, без резкого запаха. Для окрашивания поверхностей, которые будет использовать снаружи, полимерные краски должны обладать устойчивостью к влаге, солнцу, пыли. Рекомендуют выбирать быстросохнущие типы порошковых красителей. Кроме того, для металлоизделий необходимы краски, обладающие защитой от коррозии. Также необходимо определиться, какая поверхность вам подходит – глянцевая или матовая. Глянцевую легче мыть, она более практична. Но матовой можно замаскировать мелкие дефекты на поверхности металла. Обязательно нужно смотреть на срок годности – чем он ближе к дате изготовления – тем лучше.
Область применения окрашивания
Полимерные красители используют, чтобы обрабатывать металлические изделия для наружного и внутреннего пользования.
Красками на основе полимеров покрывают трубопроводы, металлические полы, элементы складских помещений и кораблей. Краску
используют не только как декоративное украшение поверхности, но и в качестве защитного покрытия – например,
красят конструкции из металла в бассейнах, которые постоянно контактируют с водой.
Полимерной краской окрашивают автомобили, бытовую технику (ванные, котлы, бойлеры, холодильники), обрабатывают элементы
мостов и виадуков, зданий и других металлических конструкций.
Подготовка поверхности
Перед тем, как наносить полимерное покрытие на поверхность металлического изделия, его нужно подготовить.
Это нужно, чтобы краска легла ровно, не создавала комок и быстро застыла.
Подготавливая изделие для полимерной окраски, мастер должен очистить поверхность, убрать все дефекты, устранить
жировые загрязнения, масляные пятна. Если изделие старое, то сперва нужно избавиться от остатков прошлого окрашивания и удалить продукты коррозии.
Очистку и подготовку металлоизделий осуществляют механическими, термическими и химическими способами.
Цель подготовки: готовая поверхность должна стать максимально совместимой с полимерным покрытием, не терять при
этом свои свойства и качества и не снижать защитное качество окрашивания.
Окрашивание и полимерное покрытие — услуги обработки металла в Москве
ООО «Металлмос» производит окраску металла различными типами краски или полимерных покрытий. Гарантируем эстетичность и долговечность покраски, а также отличную защиту от коррозионного разрушения. Мы выполняем окрашивание поверхностей со сложной геометрией, которые впоследствии будут подвергаться динамическим и вибрационным нагрузкам, а также воздействию химически агрессивных веществ.
Технология проведения окраски
Окрашивание металла начинается с очистки от загрязнений и остатков застарелой краски, а также обезжиривания. Для этого используют специализированные химические вещества, либо механические средства. При крайних степенях загрязнения применяют пескоструйную обработку поверхностей, как вручную, так и с применением механических приспособлений.
Металлические поверхности окрашивают порошковыми лакокрасочными смесями. Процедура окраски порошковой краской выполняется в два этапа:
1. Нанесение красящего вещества на металлическую поверхность в покрасочной камере.
Предварительно порошковой краске и металлической поверхности придают противоположные электрические заряды. Поскольку последние взаимно притягиваются друг к другу, то порошок плотно и равномерно прилипает ко всей окрашиваемой поверхности.
Частички, которые остались в воздухе, втягиваются вентиляционной системой и оседают в накопительных ёмкостях. Их можно повторно использовать для покраски. Поэтому окраска металла м2 на 1 тонну порошками дешевле, чем аэрозолями или жидкостями.
2. Термическая обработка напылённой поверхности.
Под воздействием повышенной температуры частички порошка спекаются друг с другом и с металлической поверхностью, образуя монолитный и прочный слой лакокрасочного покрытия.
В процессе спекания расплавленное красящее вещество проникает в кристаллическую структуру металла, поэтому красящими веществами выполняется окраска оцинкованного металла. Причем не только для придания эстетичного внешнего вида изделию, но и для защиты от механических повреждений защитного слоя цинка.
Упаковка рулонов
- Разматыватель;
- Сшивка лент;
- Накопитель ленты;
- Химическая подготовка поверхности;
- Окрасочные камеры;
- Сушка в печи;
- Водяное охлаждение;
- Нанесение эмали;
- Сушка в печи;
- Водяное охлаждение;
- Накопитель ленты;
- Резка;
- Наматыватель рулонов.
Производство рулонной оцинкованной стали с защитно-декоративным лакокрасочным покрытием осуществляется по ГОСТ 30246-94, Р 52146-2003.
В качестве красителей используются следующие виды эмалей:
- Полиэфирные (полиэстер)
- Полиуретановое покрытие
- Поливинилхлоридные (ПВХ) и поливинилдендифторидные (ПВДФ)
Полиэфирные (полиэстер) — материал в котором идеально сбалансированы цена и хорошие эксплуатационные характеристики. Подходит для любой климатической зоны и имеет достаточно хорошие механические свойства. Покрытие матовое. Толщина покрытия — 50 мкм. Теплостойкость — 120°С.
Полиуретановое покрытие — покрытие на основе полиуретана, обладающий шелковисто-матовой поверхностью. Материал выдерживает большие перепады температур (до 120°С), стойкий к солнечному излучению, обладает хорошей химической устойчивостью и цветостойкостью. При толщине 50 мкм — обладает отличными антикоррозийными свойствами.
Поливинилидендифторидные (ПВДФ) — покрытие на основе смеси поливинилдендифторида и акриловой смолы. Материал устойчив к механическим повреждениям и имеет высокие прочностные и антикоррозийные свойства. Сохраняет свои свойства при температурах от -60°С до +120°С. Устойчив к УФ-излучению, обладает высокой стойкостью к агрессивным средам и механическим воздействиям. Толщина покрытия — 27 мкм.
Покрытия PVDF и полиуретановое покрытие могут быть использованы в случае особых эксплуатационных требований, имеют высокие прочностные и антикоррозийные свойства. Эти покрытия ценны тем, что обладают устойчивостью к УФ-излучению и цветостойкостью. Использование полиуретанового покрытия особенно эффективно в условиях российского климата, этот материал не боится как низких, так и высоких температур, способен выдерживать большие перепады температур. В отличие от PVDF и полиуретанового покрытия, полиэстер гораздо менее устойчив к механическим повреждениям, но обладает гораздо большей гибкостью и более привлекательной ценой.
Printech — это покрытие с множеством видом рисунков, нанесенными на оцинкованный стальной лист офсетным способом. Сочетает в себе элегантный внешний вид и превосходные защитные свойства покрытия. Данная технология уже завоевала популярность во многих странах, выпускается на основе полиэфирного (полиэстер) и поливинилдендифторидного (ПВДФ) покрытий.
Структура покрытия Printech
Каталог палитры цветов покрытия Printech
Структура стали с полимерным покрытием:
- Полимерное покрытие
- Грунт под эмаль
- Пассивированный слой
- Слой цинка
- Стальной лист
- Слой цинка
- Пассивированный слой
- Грунт под эмаль
- Краска для обратной стороны
Характеристика металла
ГОСТ 52246-2004, ЦИНК Zn 80-275 | |
Металл: ММК, Северсталь, НЛМК | |
Толщина: 0,2-0,9 мм | |
Ширина: 900-1250 мм | |
Виды покрытия: ПВДФ, полулеретан, полиэстер | |
Вся палитра RAL: более 200 цветов | |
Вес рулона: от 1,5 тонн |
Стеновые и кровельные сэндвич-панели, профилированный настил, сталь оцинкованная окрашенная в рулонах с покрытием ПВДФ (поливинилдентфторидное покрытие), полиуретановое покрытие, полиэстер от стандартных до редких и эксклюзивных цветов.
Стандартные цвета RAL:
Вся палитра цветов RAL:
Преимущества окраски металла от Металлмос
Главное преимущество сотрудничества с нами — качественная порошковая окраска металла, цена которой одна из самых выгодных в Москве.
В работе мы используем порошковые краски и полимерные покрытия от ведущих мировых производителей. Если вы хотите получить качественную и долговечную покраску металлических поверхностей — следует обратиться в компанию «Металлмос». Ждем вашего звонка по номеру телефона 8-495-118-36-88!
Что такое полимерное покрытие? Полимерное покрытие металла
Полимерное покрытие – это уникальная возможность защитить металлические поверхности. Это самый эффективный и современный способ борьбы с коррозией, которая рано или поздно все равно появляется на металлических изделиях.
В чем суть?
Для улучшения эксплуатационных свойств металла используются полимеры, которые могут вступать в реакцию в определенных условиях. Подобные покрытия представляют собой сухие составы на основе порошка мелкой дисперсии, куда дополнительно добавляются отвердители, наполнители и пигменты. Полимерное покрытие было выбрано для повышения защитных средств металла не случайно: металлы проводят электрический ток, как следствие, заряд передается изделию, в результате чего образуется электростатическое поле. Оно притягивает частицы порошка, удерживая их на поверхности обрабатываемого изделия. Особенность полимерного покрытия – в высокой степени устойчивости к любым видам воздействия. Кроме того, оно эстетично.
Как проходит полимеризация
Цех порошковой окраски состоит из нескольких участков:
- Участка подготовки изделий: чтобы полимерное покрытие было нанесено правильно и равномерно, металлическое изделие сначала тщательно очищается от пыли, ржавчины, грязи. Целесообразно использовать эффективную пескоструйную обработку и фосфатирование. Обязательный этап – обезжиривание металлической поверхности.
- Камеры напыления: в окрасочной камере выполняется непосредственно покраска.
Камера термическая, она способна нагреться до температуры в 200 градусов и прогревается равномерно. Порошок начинает плавиться, за счет чего образуется ровное и гладкое покрытие по всей поверхности металла, заполняются и его поры.
- Полимеризация изделия выполняется в камере охлаждения: здесь температура постепенно падает, а полимерная пленка становится тверже. Спустя 24 часа полимерное покрытие уже готово к эксплуатации.
Технология окраски: в чем суть
Нанесение порошкового покрытия выполняется в несколько этапов. На первом обрабатываются поверхности. Очень важно, чтобы металлические изделия были тщательно очищены от загрязнений, окислов, а обезжиривание поверхности будет способствовать улучшенной сцепляемости. После подготовки выполняется этап маскировки, то есть скрываются те элементы металлического изделия, на которые не должен попасть порошковый состав.
Детали, которые должны быть обработаны, завешиваются на транспортную систему, затем отправляются в камеру покраски. После напыления на металле образуется порошковый слой. На этапе полимеризации формируется покрытие, которое представляет собой оплавление слоя краски.
В чем особенности?
Металл, обработанный полимерным покрытием, отличается надежностью и повышенной прочностью. Объясняется это тем, что образуется герметичная монолитная пленка, полностью покрывающая поверхность изделия и прочно держащаяся на нем. Благодаря полимерному покрытию металл обладает:
- высокой адгезией к поверхности;
- высокой прочностью и износоустойчивостью;
- длительным сроком эксплуатации при сохранении первоначальных свойств;
- богатой цветовой гаммой;
- быстрым производственным циклом.
Полимерное покрытие металла выполняется на основе различных материалов и красящих порошков. Выбор конкретного вещества зависит от того, для каких целей наносится покрытие, насколько важны декоративные свойства.
Полиэстер
Для полимерного покрытия металла чаще всего используется именно полиэстер. Это недорогой материал, обладающий высоким уровнем гибкости, формуемости, к тому же он может эксплуатироваться в любых климатических условиях. Лист с полимерным покрытием на основе полиэстера отличается стойкостью к ультрафиолетовому излучению и коррозии. Материал образует качественную и прочную пленку на поверхности, благодаря чему при любых условиях транспортировки стальные листы доставляются в целости.
Широко используется и матовый полиэстер: покрытие имеет совсем маленькую толщину, а поверхность металла получается матовой. Особенность данного материала – в высокой цветостойкости, хорошей стойкости к коррозии и механическому воздействию.
Пластизоль
Еще одно популярное полимерное покрытие металла – пластизоль. В составе этого декоративного материала — поливинилхлорид, пластификаторы; внешне он привлекает внимание тисненой поверхностью. Это самое дорогое покрытие, и в то же время самое стойкое к механическим повреждениям благодаря большой толщине покрытия. С другой стороны, материал не обладает высокой температурной стойкостью, а потому под воздействием солнечных лучей при высокой температуре покрытие будет портиться. За счет большой толщины стойкость к коррозии пластизоля высокая.
Популярна сталь с полимерным покрытием на основе пурала, которая отличается шелковисто-матовой структурной поверхностью. Стойкость к перепадам температуры и воздействию химических веществ делает данный состав популярным для обработки металлов.
Характеристики стали с полимерным покрытием
Особенности материалов с полимерным покрытием – в прочности, формуемости, высокой коррозийной стойкости. После обработки сталь обретает прекрасный внешний вид, которому можно придать любые цвета и оттенки. Прокат выполняется по ГОСТ, полимерное покрытие получается качественным. Окрашенный прокат может иметь одно- или двухслойное покрытие, возможны варианты, когда вещество наносится с одной или с обеих сторон. Благодаря полимерному покрытию улучшаются эксплуатационные свойства стали:
- металл с полимерным покрытием может быть переработан в готовые изделия;
- покрытие распределяется по поверхности равномерно, поэтому и степень защиты равномерная;
- отсутствие пор служит залогом хорошего уровня защитных свойств;
- сталь отличается хорошей адгезией;
- металл может сохранять защитные и декоративные свойства больше 10 лет.
С экономической точки зрения сталь оцинкованная с полимерным покрытием более выгодна: во-первых, она способствует высокой производительности и качеству, так как снижается себестоимость нанесения покрытий. Во-вторых, покупателю не нужно самому вкладывать средства в дополнительную обработку стали для защиты ее поверхности. Отметим, что антикоррозионные свойства оцинкованной стали, которая обработана полимерным покрытием, зависит от толщины слоя. Чтобы повысить срок эксплуатации стальных изделий, они дополнительно покрываются двумя слоями полимера, что делает защиту металла еще выше.
Особенности покрытия
Полимерное покрытие – это пленка, которая обладает целым комплексом уникальных эксплуатационных характеристик. Предварительно окрашенный прокат создается на основе нескольких типов полимеров. Любой материал, обработанный на основе такого метода – стальной лист или сетка с полимерным покрытием – отличается ударопрочностью, стойкостью к воздействию коррозии и высокой адгезией. Немаловажно и то, что порошковое окрашивание позволяет сделать поверхность металла любой с точки зрения цвета, в том числе и искусственно состаренной, например, под стиль антик.
Сегодня популярен такой способ окраски стального проката, как Coil Coating. Суть метода в том, что покрытие наносится на автоматизированной линии, то есть листы рулонного проката обрабатываются на линии, после чего на них валиковыми машинами наносится покрытие. Данная технология получила распространение благодаря тому, что нет потерь материалов, а сама линия более производительна, а потому и выгодна.
Как и при любых других отделочных работах, сначала требуется подготовить поверхность, после чего выполняется ее окраска. Данная технология позволяет вести качественную обработку стали, алюминия и белой жести. Таким образом, полимерное покрытие – это возможность улучшить эксплуатационные свойства металла, повысить его защитные свойства и обеспечить длительность эксплуатации.
Что такое полимерное покрытие? (Руководство по его технологии и применению)
Что такое полимерное покрытие?
Полимерное покрытие представляет собой тонкослойное покрытие или краску, изготовленную из полимеров, обеспечивающих превосходную адгезию и защиту от коррозии. Полимер — это молекула, образованная путем соединения множества небольших молекул, называемых мономерами, которые состоят из большого количества подобных единиц. Это могут быть синтетические органические материалы, такие как смолы и пластмассы.
Будучи ведущим поставщиком решений для покрытий, наша приверженность побуждает нас оставаться в курсе последних достижений в области покрытий. В этой статье представлена краткая история того, с чего все началось, роста отрасли и преимуществ оптимальной производительности при использовании правильного полимерного покрытия.
Главы- 1Краткая история технологии полимеров в лакокрасочной промышленности
- 2Что такое полимерное покрытие, новости отрасли и развитие
- 3 Использование полимера и полимерного покрытия
- 4 Преимущества полимерного покрытия для оптимальной работы (пример из реальной жизни)
- 5 Меры безопасности при обращении с полимерным покрытием
Глава 1
Краткая история полимерных технологий в лакокрасочной промышленности на работах Германа Марка, основавшего Институт исследований полимеров в 1946, который стал центром исследования полимеров в США.
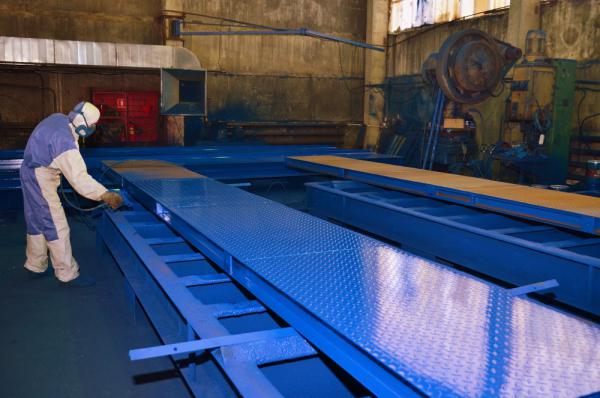
Работа Штаудингера заложила основу для расширения индустрии пластмасс. Химический состав и структура этих гигантских молекул сделали их пригодными для промышленного применения .
Дверь для полимеров открылась, когда Aerospace 9Композитные требования 0013 требовали высокой прочности, легкости, коррозионной стойкости и экономичных материалов . Считалось, что различные полимеры удовлетворяют этим требованиям к характеристикам. Несколько полимеров, которые были изучены, включают:
Фенольные смолы – очень хрупкие, с низкой ударной вязкостью, с высоким содержанием растворителя и с трудом наносятся (требуется три термических отверждения во время нанесения)
Полиэфир – низкие физические свойства, плохая адгезия
Винилэфир – высокая содержание стирола (неприятно для дыхания) — чрезвычайно легко воспламеняется и токсично во время нанесения и отверждения, чувствителен к атмосферной влаге и температуре, короткий срок хранения (3 месяца), высокая усадка при отверждении — делает его очень хрупким, составляет одну треть прочности эпоксидной смолы смолы, плохое сцепление
Эпоксидные смолы — высокая прочность, высокое сцепление, низкая поверхностная энергия, химическая стойкость
Эпоксидные полимеры, класс термореактивных полимеров, стали лучшим выбором. Они стабильны, прочны и устойчивы к агрессивным химическим веществам. Эпоксидные смолы представляют собой высокоэффективные клеи и полезные промышленные покрытия для поверхностей.
Большинство поверхностных покрытий основано на синтетических полимерах промышленного производства и при нанесении на поверхность образует прочную, долговечную пленку.
Глава 2
Что такое полимерное покрытие, новости отрасли и развитие
Полимерное покрытие — это покрытие или краска, изготовленные из полимеров, которые обеспечивают превосходную адгезию и защиту от коррозии, согласно Corrosionpedia. Чтобы полностью понять полимерное покрытие, необходимо понять действия полимера. Глядя на определение полимера, приведенное в Википедии, полимер — это молекула, состоящая из соединения множества небольших молекул, называемых мономерами.
Этот тип химической реакции (связывание в более крупную молекулу) определяет функциональное поведение покрытий. В APC химические покрытия представляют собой высокоэффективные специальные покрытия , которые могут противостоять агрессивным кислотам, щелочам и растворителям при различных температурах.
Новости отрасли промышленных покрытий
«Глобальный спрос на промышленные покрытия, по прогнозам, достигнет 105,5 миллиардов долларов к 2022 году, ежегодный рост составит 6,1% в период с 2016 по 2022 год». [источник]
За последние десять лет исследования приблизили нас к функциональным покрытиям , которые просты в использовании, самоочищаются, обладают антибактериальными свойствами или обладают противообрастающими свойствами. Одним из наиболее существенных преимуществ полимерного покрытия является то, что оно практически не влияет на другие свойства при использовании. Например, когда покрытия наносятся в целях защиты при транспортировке и хранении химикатов, безопасность и механическая прочность не ухудшаются.
Покрытия стойкие и долговечные. Поскольку они в основном используются для защиты от элементов (например, воды, коррозии, окружающей среды), они должны соответствовать требованиям высокой производительности.
Глава 3
Использование полимера и полимерного покрытияПолимеры обладают уникальными свойствами, которые можно использовать для различных целей. Полимеры могут быть искусственными (синтетическими) и/или природными (например, каучук, шеллак, целлюлоза). В зависимости от их желаемого использования, они могут быть использованы для устойчивости к царапинам и истиранию, эластичности или хрупкости.
Полимерные покрытия повсюду. Они используются в вашем доме для защиты столов и мебели, а также для автомобилей, больниц и медицинских учреждений, и это лишь некоторые из них.
Machine Design поделился примером полимера, достаточно прочного, чтобы выдерживать многократные циклы стерилизации, а также легко подвергаться механической обработке. «Термическая и размерная стабильность полимера, а также его устойчивость к химическим веществам и отсутствие впитывания воды делают его хорошим выбором для деталей, требующих повторной дезинфекции и стерилизации паром».
Являясь лидером в области промышленных покрытий, наши полимеры настроены так, чтобы влиять на защитных свойств .
Использование полимерного покрытия зависит от:
- рабочей температуры
- износ окружающей среды
- тип коррозии
Качественная подготовка поверхности и методы нанесения играют центральную роль между покрытием и основанием и обеспечивают устойчивость к атмосферным воздействиям.
Глава 4
Преимущества полимерного покрытия для оптимальной работы (пример из реальной жизни)
Химическое покрытие — это покрытие наносится на поверхность объекта, также известную как подложка . Например, такие покрытия, как полимерные краски и лаки, выполняют двоякую функцию: защищают подложку и служат украшением.
Функциональные покрытия изменяют поверхностные свойства нижнего слоя. Его можно применять для обеспечения адгезии, смачиваемости, коррозионной стойкости и износостойкости.
1. Адгезия – связывает разнородные поверхности
2. Смачиваемость — это способность жидкости поддерживать контакт с твердой поверхностью
3. Коррозионная стойкость — некоторые металлы более устойчивы к коррозии ( превращение рафинированного металла в химически устойчивую форму ), чем другие. Защитить металлы от окисления (коррозии) можно нанесением полимерных красок или покрытий.
4. Износостойкость — скорость износа зависит от его стадии (ранняя, средняя или старая). Основной причиной износостойкости являются химические реакции между изнашиваемым материалом и коррозионной средой. [источник: Стачвайк, Гвидон В.; Бэтчелор, Эндрю В. (2005). Инженерная трибология (3-е изд. ). Elsevier Inc]
Усовершенствованные покрытия для оптимальной работы (пример из реальной жизни)
Hutchison Ports TNG предлагает комплексные решения для судоремонтных услуг в Мексиканском заливе. Одна из их специализированных ремонтных работ включает в себя очистку и покраску корпусов, палуб, цистерн, грузовых отсеков, интерьеров судов и цепей.
Посмотрите видео ниже, как они наносят усовершенствованные покрытия для улучшения характеристик корабля.
Их проекты включают:
- покрытия, армированные стекловолокном — для защиты от кавитации и коррозии
- противообрастающие покрытия — для оптимизации расхода топлива катера
- химически стойкие полимерные покрытия — для хранения химических продуктов
Эти покрытия повышают эффективность работы, сокращают время портирования и увеличивают чистую прибыль.
Глава 5
Меры безопасности при обращении с полимерным покрытием
Нанесение полимерного покрытия на различные поверхности требует специальных процедур. Крайне важно защитить себя или сотрудников, которые наносят покрытия, следуя этим пошаговым инструкциям:
Шаг 1: Используйте опытных людей для нанесения промышленных покрытий
Шаг 2: Обеспечьте надлежащую вентиляцию рабочих мест
Этап 3: Нанесите лосьон для кожи (защитный крем), содержащий ланолин, на руки, предплечья и лицо перед работой с покрытием
Этап 4: Обеспечьте надлежащее защитное оборудование и одежду для каждого работника при использовании этих продуктов
Шаг 5: Носите защитную одежду
- При смешивании, приготовлении или ремонте: надевайте резиновые перчатки, защитный комбинезон, химические очки и респираторы для очистки газов/паров.
- При распылении: надевайте резиновые перчатки, защитный комбинезон, пластиковые сапоги, защитный капюшон и полнолицевую маску с положительным давлением воздуха. Лента закрыла все отверстия.
Шаг 6: Используйте мыло и воду только , чтобы удалить любое покрытие
Шаг 7: Повторно нанесите лосьон для кожи после мытья
Шаг 8: Используйте крем с кортизоном, если кожа покраснела Заключение
Полимерные покрытия и технологии развиваются экспоненциально. Химические покрытия используются для различных целей и требований к производительности.
В APC мы понимаем проблемы, с которыми вы сталкиваетесь каждый день, и продолжаем разрабатывать и улучшать наши покрытия и технологии.
Являясь поставщиком высококачественных покрытий премиум-класса, мы предлагаем инновационные покрытия с добавленной стоимостью для защиты ваших активов.
Полимерные покрытия для стальных фасадов и крыш
Фасады и кровли из оцинкованной стали с полимерным покрытием являются лучшим решением для строительства зданий благодаря долговечности, превосходному внешнему виду и экономичности. Правильный выбор полимерного покрытия обеспечивает высокую долговечность и надежность изделий.
Стали с полимерным покрытием для крыш и фасадов Ruukki-SSAB разработаны с учетом возможности применения в любых условиях эксплуатации. На кровлю и фасады воздействуют солнце, мороз, содержащиеся в воздухе загрязняющие вещества, грязь, дожди, снегопады, сильный ветер, а иногда и ураганы. При этом качественное покрытие надолго сохраняет первоначальный вид и свойства изделий. Кровельная и фасадная сталь Ruukki обладает отличной деформируемостью и может обрабатываться даже при низких температурах.
При выборе полимерного покрытия для строительных материалов важно учитывать срок эксплуатации здания, климатические и эксплуатационные условия окружающей среды, а также другие возможные особые требования. Из широкого спектра покрытий, предлагаемых Ruukki, можно выбрать наиболее подходящий вариант, позволяющий добиться необходимого срока службы и превосходного внешнего вида здания.
Условия окружающей среды
Условия окружающей среды оказывают существенное влияние на выбор стали с полимерным покрытием. Солнечное УФ-облучение, воздействуя на покрытие, постепенно изменяет химический состав краски, что может привести к ослаблению эффекта глянца, выцветанию цвета, а также ухудшению антикоррозионной защиты.
Кроме того, на коррозионную стойкость стали влияют влага, тепло, атмосферные загрязнения и другие соединения. Для различных условий эксплуатации рекомендуется подбирать соответствующие полимерные покрытия. Оцинкованная сталь с покрытием может использоваться в категориях коррозионной активности С1-С4, а использование в категории С5 рассматривается индивидуально для конкретных условий эксплуатации. Атмосферная нагрузка определяется по ДСТУ ISO 12944-2:2019.
Corrosivity category means atmospheric conditions as per DSTU ISO 12944-2:2019
Corrosivity category | Environment | |
Exterior | Interior | |
C1 очень низкая | – | Отапливаемые помещения с чистой атмосферой (например, офисы, магазины, школы, гостиницы).![]() |
C2 низкий | Атмосферы с низким уровнем загрязнения. В основном сельские районы. | Неотапливаемые помещения, в которых может образовываться конденсат (например, склады, спортивные залы). |
C3 средний | Городская или промышленная атмосфера, умеренное загрязнение двуокисью серы. Прибрежные районы с низкой соленостью. | Промышленные помещения с повышенной влажностью и некоторым загрязнением воздуха (например, предприятия пищевой промышленности, прачечные, пивоваренные и молочные заводы). |
C4 высокая | Промышленные и прибрежные районы с умеренным засолением. | Химические заводы, плавательные бассейны, верфи и верфи. |
C5-I | Промышленные зоны с повышенной влажностью и агрессивной атмосферой. | Здания или зоны с почти постоянной конденсацией и высоким уровнем загрязнения. |
С5-М | Прибрежные и морские районы с повышенной соленостью.![]() | Помещения и зоны с практически постоянной влажностью и высоким уровнем загрязнения. |
Срок службы зданий
Полимерное покрытие должно обладать устойчивыми техническими свойствами и внешним видом, которые должны сохраняться на протяжении всего периода эксплуатации объекта с минимальными затратами на обслуживание. Справочные сроки полезного использования для различных типов зданий определены в ДБН В.1.2-14:2018.
Планируемый срок полезного использования здания в большинстве случаев составляет более 50 лет. Такая долговечность кровельных и фасадных решений достигается за счет применения самых стойких покрытий – Hiarc, Hiarc Max, Pural. Срок эксплуатации сельскохозяйственных и других зданий с коротким периодом эксплуатации составляет от 15 до 50 лет, поэтому для них подходит более широкий спектр покрытий.
Справочные плановые сроки полезного использования зданий приняты согласно ДБН В. 1.2-14:2018
Building type | Indicative useful life, years |
Residential and public | 100 |
Industrial and ancillary | 60 |
Warehouses | 60 |
Сельскохозяйственная | 50 |
Мобильные сборно-разборные (включая промышленные, жилые и т.п.) | 20 |
Мобильные контейнерные здания | 15 |
Специальные требования к покрытию стальных строительных материалов
Крыши
Крыши подвергаются сильному оказанию ЕС — Снег, стоячая вода и скопившийся мусор создают нагрузку на крышу, что требует нанесения высококоррозионностойких покрытий.
Поверхность испорчена снегом, льдом и перемещением людей по крыше. Это обусловливает повышенные требования к износостойким покрытиям. Кроме того, покрытие крыш, соединенных с фальцами, должно выдерживать формовку, осуществляемую ручным инструментом.
Фасады
Вентилируемые фасады и сэндвич-панели должны сохранять привлекательный внешний вид, поэтому важно, чтобы полимерное покрытие обеспечивало устойчивость к УФ-излучению, легко чистилось или самоочищалось. В некоторых случаях требуется хорошая износостойкость.
Водосточные системы
Водосточные желоба должны иметь хорошую коррозионную стойкость, так как в них скапливается застойная вода и мусор, а трубы ливневой канализации – хорошую стойкость к царапанью. В таком случае стальной лист должен быть окрашен с обеих сторон и подходить для формовки.
Потолки и стены
Чистота и возможность очистки – важнейшие параметры внутренних поверхностей зданий.
Свойства и критерии выбора полимерных покрытий
На применимость и стойкость покрытий в различных атмосферных условиях влияет ряд факторов, таких как толщина покрытия, тип краски, использование добавок (пигментов, стабилизаторов) . Толщина покрытия влияет в основном на механические свойства: формуемость, износостойкость и коррозионную стойкость, стойкость к царапанью.
Hiarc и Hiarc Max обладают наилучшей температурной и химической стойкостью, а также высокой стойкостью к УФ-излучению. Применение таких покрытий позволяет фасаду сохранять насыщенный цвет и блеск на протяжении длительного времени под воздействием солнечного излучения. Отличные свойства таких покрытий основаны на молекулярном наращивании, а неорганическая пигментация придает прекрасную устойчивость цветовому оттенку. Покрытие Hiarc Max имеет более толстый грунтовочный слой по сравнению со стандартным покрытием Hiarc (20 мкм/7 мкм) с антикоррозионным пигментом, поэтому подходит для более ответственных условий применения. Hiarc – лучший выбор для фасадов.
Pural и Pural Matt – покрытия на основе полиуретана, специально разработанные для крыш. Их неорганическая пигментация и химический состав гарантируют высочайшую коррозионную стойкость при воздействии неорганических загрязнителей (соли, кислоты, щелочи), очень хорошую стойкость к УФ-облучению, а также термостойкость и стабильность цвета. Толстое покрытие Plural обладает отличной способностью к формованию. В таком покрытии используется полиамид, обеспечивающий устойчивость к царапинам и улучшенную гибкость. Покрытия Pural – лучший вариант для крыш и фасадов промышленных зданий.
Pural farm (Csafe) — толстое покрытие на основе полиуретана, сочетающее в себе высокую прочность, коррозионную стойкость и устойчивость к царапинам. Пураловая ферма легко обрабатывается и может гнуться без каких-либо ограничений по радиусу изгиба. Химический состав покрытия обеспечивает наилучшую коррозионную стойкость к органическим агрессивным загрязнителям, в том числе животноводческой отрасли (соли фосфорной кислоты и дезактиваторы). Изделие с таким покрытием обладает высокой стойкостью к значительным механическим нагрузкам на крышу. Пурал ферма обладает высокой способностью к самоочищению и предназначена для объектов с повышенной влажностью, которые подлежат частой уборке.
Полиэфирные и полиэфирно-матовые покрытия обладают средней устойчивостью к атмосферным воздействиям и механической стойкостью. Помимо механической и коррозионной стойкости, полиэстер матовый имеет более толстый слой, чем стандартное полиэфирное покрытие. При этом матовое покрытие не содержит матирующих веществ, как гладкое полиэфирное покрытие. Благодаря невысокой цене такие покрытия рекомендуются для крыш и стен зданий с коротким сроком эксплуатации, а также во внутренних сухих помещениях.
Пленочный ламинат FoodSafe обладает высокой формуемостью и стойкостью к органическим веществам. Как правило, это покрытие имеет гладкую белую поверхность. FoodSafe не токсичен, устойчив к моющим и чистящим средствам, легко моется, не впитывает воду. Это покрытие было тщательно протестировано на соответствие строгим требованиям стандарта безопасности пищевых продуктов HACCP. С ламинатом FoodSafe может даже находиться непосредственный контакт продуктов питания – это лучшее решение для внутреннего использования на предприятиях пищевой (в холодильных и морозильных камерах) и фармацевтической промышленности, а также в помещениях с повышенной влажностью.
Coating Property | Coating | |||||||||||||||
Hiarc | Hiarc Max | Pural | Pural Matt | Pural farm (Csafe) | Полиэстер | Полиэстер матовый | Ламинат FoodSafe | |||||||||
Толщина покрытия, мкм | 27 | 40 | 50 | 50 | 200 | 25 | 35 | 120 | ||||||||
Surface texture | smooth | smooth | slightly granular | matt | slightly granular | smooth | granular | Гладкий | ||||||||
Класс глянец, Gardner 60 °, EN 10169-1 | 30-40 | 30-40 | 34-46 | <5 | 40296 | <5 | 4096 | <5 | 4096 | <5 | 4096 | <5 | 4096 | .![]() | <5 | 7-13 |
Shaping (bending) capacity | good | good | good | good | good | satisfactory | satisfactory | good | ||||||||
Мин. bending radius (placticity) | 1t* | 1t | 1t | 1t | 1t | 3t | 2t | 1t | ||||||||
Min. температура формовки, °С | -10 | -10 | -15 | -15 | +15 | 0 | 0 | +10 30 Макс. ambient temperature, °C | 110 | 110 | 100 | 100 | 100 | 90 | 90 | 60 |
Class of reaction to fire, DSTU EN 13501-1:2016 | A1 s1 , d0 | A1 s1, d0 | A2 s2, d0 | A2 s2, d0 | C-s2, d1 | A1 | A2 s1, d0 | – | ||||||||
Class of UV irradiation resistance | Ruv4 | Ruv4 | Ruv4 | Ruv4 | Ruv4 | Ruv2 | Ruv3 | – | ||||||||
Class of corrosion resistance | RC4 | RC5 | RC5 | RC5 | RC4 | RC3 | RC4 | RC5 | ||||||||
Scratch resistance | 30N | 35N | 40N | 40N | 35N | 20N | 25N | 55N | ||||||||
Pollution resistance | excellent | excellent | very good | very good | excellent | satisfactory | хорошее | отличное |
* толщина листа
Стойкость покрытия к естественному УФ-излучению указана в категориях Ruv1-Ruv4 в соответствии с EN10169. Стойкость к УФ-излучению показывает, насколько хорошо покрытие может сохранять свой первоначальный цвет и степень блеска при наружном использовании. Покрытия категории Рув1 обладают очень слабой стойкостью к УФ-излучению и предназначены для использования только внутри помещений. Покрытия Ruv4 обладают высокой устойчивостью к ультрафиолетовому излучению и поэтому рекомендуются для наружного применения.
Рекомендации по применению покрытий
Практически для любого строительного объекта можно подобрать подходящее покрытие с учетом окружающих условий, планируемого срока эксплуатации и особых требований.
Использование полимерных покрытий Ruukki для крыш (R) и фасадов (F)
Гарантия для эстетических свойств продуктов | Corrosion isperties of Products | Corrosion Risties of Products | Corrosion Riesties Dersiot of Producties | -orsionsavies | .Hiarc | Hiarc Max | Pural | Pural Matt | Pural farm (Csafe) | Polyester | Polyester Matt | |||||||
R | F | R | F | R | F | R | F | R | F | R | F | R | F | |||||
Standard warranty, years | С2 | 20 | 20 | 20 | 20 | 20 | 15 | 15 | 10 | 10 | 10 | |||||||
С3 | 20 | 20 | 20 | 20 | 20 | 15 | 15 | 10 | 10 | 10 | ||||||||
Special warranty, years | С4 | 10* | 10* | 10* | 10* | |||||||||||||
С5 -I/M | 1-5* | 1-5* | 1-5* | 1-5* |
Usage of Ruukki polymer coatings for interior premises (ceilings and partitions)
Load category | Hiarc | Hiarc Max | Pural | Pural Matt | Pural farm (Csafe) | Polyester | Polyester Matt | Laminate FoodSafe |
C1 | ✔ | ✔ | ✔ | ✔ | ✔ | ✔ | ✔ | ✔ |
C2 | ✔ | ✔ | ✔ | ✔ | ✔ | ✔ | ✔ | ✔ |
C3 | ✔ | ✔ | ✔ | ✔ | ✔ | ✔ | ✔ | ✔ |
C4 | ✔* | ✔* | ✔ | ✔* | ||||
С5-I/M | ✔* |
* Условия категорий воздействия C4 и C5-I/M очень тяжелые, поэтому для конкретного проекта может быть предоставлена только ограниченная гарантия.
Неокрашенные оцинкованные стальные листы рекомендуются для условий не выше С2.
Рекомендации в таблицах представлены для сталей со степенью оцинковки 275 г/м 2 .
Защита сталей от коррозии с помощью проводящего полимерного покрытия
На этой странице
РезюмеВведениеСсылкиАвторское правоСтатьи по теме
Рассмотрена защита сталей от коррозии с помощью проводящего полимерного покрытия. Проводящий полимер, такой как полианилин, полипиррол и политиофен, действует как сильный окислитель для стали, вызывая сдвиг потенциала в благородном направлении. Полимер с сильной окислительной проводимостью облегчает пассивацию стали. Двухслойная полипропиленовая пленка была разработана для эффективной защиты от коррозии. Он состоял из внутреннего слоя, в который был легирован фосфомолибдат-ион (PMo), и внешнего слоя, в который был легирован додецилсульфат-ион (DoS). Внутренний слой стабилизировал пассивный оксид, а внешний слой обладал анионной селективностью проницаемости для предотвращения проникновения агрессивных анионов, таких как хлорид, через пленку полипропилена в стальную основу. С помощью двухслойной пленки PPy сталь выдерживалась пассивно около 200 ч в 3,5% растворе хлорида натрия без образования продуктов коррозии.
1. Введение
После исследования Shirakawa et al. о проводящем полиацетилене сообщалось о различных применениях проводящего полимера [1]. Использование проводящего полимера для антикоррозионного покрытия является одним из таких применений, и за последнее десятилетие было представлено множество работ. Получение полиацетилена производили окислением в газовой фазе; однако в настоящее время проводящие полимеры, такие как полианилин (PAni), полипиррол (PPy) и политиофен (Pthio) на рисунке 1, для защиты от коррозии получают электрохимическим окислением в жидкой фазе.
О применении проводящего полимера для защиты от коррозии впервые сообщил ДеБерри в 1985 году, который представил, что нержавеющая сталь, покрытая ПАни, сохраняется в пассивном состоянии в течение относительно длительного периода в растворе серной кислоты [2]. Затем Весслинг указал, что проводящее полимерное покрытие из полианилина и полипиррола, возможно, обладает свойствами самовосстановления, при которых пассивный оксид между металлом подложки и проводящим полимером может спонтанно преобразоваться в поврежденном месте за счет окислительной способности проводящего полимера [3]. ].
Когда к электродам, покрытым проводящими полимерами, показанными на рисунке 1, после полимеризации прикладывают анодные потенциалы, в дополнение к проводимости обеспечивается окислительное свойство. Способность проводящего полимера окислять стали подложки позволяет сместить потенциал сталей в пассивное состояние, в котором стали защищены пассивным оксидом, образующимся под проводящим полимером. Применение проводящего полимерного покрытия для защиты стали от коррозии было рассмотрено Tallman et al. [4]. В данной статье рассматривается применение двухслойного проводящего полипропилена для защиты сталей.
2. Проводящий полимер
Окислительная полимеризация и введение анионов в полимер для обеспечения электронной проводимости рассматривались многими авторами, и здесь мы кратко опишем процесс PPy. При анодной поляризации электрода в растворе электролита, содержащем мономер пиррола (Py), на электроде может образовываться черная полимерная пленка. Процедура полимеризации проводится без каких-либо затруднений, за исключением тщательной обработки электролита, при которой следует избегать окисления мономера Py воздухом. Таким образом, электролит должен быть деоксигенирован барботированием инертного газа.
Рисунок 2 иллюстрирует модель процесса анодной полимеризации полипропилена, предложенную Genies et al. [5]. Мономер Py, растворенный в электролите, отдает электрон электроду, что приводит к образованию пары катион-радикал (стадия (1)). Радикалы в Py реагируют друг с другом, и два протона удаляются из прореагировавшей пары Py (этап (2)), образуя димер Py (этап (3)). После образования пары катион-радикал и повторения реакции между радикалами на электроде образуется черная пленка полипропилена (стадия (4)).
Нейтральный PPy, образованный таким образом с сопряженной цепью, не обладает проводимостью. Чтобы добавить проводимость нейтральному PPy, требуется дальнейшее окисление, как показано на рисунке 3. Когда к электроду прикладывается анодный потенциал, электрон удаляется из π электронов в сопряженной связи, давая пару радикала и положительный заряд (или катион) в основной цепи PPy. Эта ситуация называется состоянием катион-радикала или состоянием полярона. Когда два радикала в PPy объединяются, сайты одинарной и двойной связи замещаются друг другом, и в PPy остаются два катиона, положение которых называется бикатионным состоянием или биполяронным состоянием. Катион, образующийся таким образом в PPy, может пройти через π электронных облаков, обеспечивающих электронную проводимость в основной цепи PPy.
При удалении электронов из основной цепи PPy происходит внедрение анионов из раствора электролита окружающей среды для поддержания нейтральности слоя PPy; то есть, когда нейтральное состояние PPy изменяется на окислительное, одновременно происходит отщепление электронов и легирование анионов. Предполагается, что один положительный заряд (или катион) может быть вставлен максимум в три или четыре единицы Py. Когда добавляется больше положительного заряда, PPy переходит в состояние переокисления и теряет проводимость.
3. Защита сталей от коррозии проводящим полимером PPy
3.

Для защиты от коррозии были предложены два механизма; один из них — эффект физического барьера, а другой — анодная защита. По барьерному эффекту полимерное покрытие работает как барьер от проникновения окислителей и агрессивных анионов, защищая металлы подложки. Этот эффект аналогичен лакокрасочному покрытию, которое препятствует проникновению веществ в стальную основу. При анодной защите проводящий полимер с сильным окислительным свойством работает как окислитель для стали-основы, потенциал которой смещен в сторону такового в пассивном состоянии. В растворе с нейтральным pH потенциал коррозии (или потенциал разомкнутой цепи при коррозии) голой стали находится в области активного потенциала, и скорость коррозии стали обычно относительно высока. Благодаря покрытию из проводящего полимера максимальный ток в активно-пассивной переходной области был ограничен барьерным эффектом, а затем потенциал может быть легко сдвинут к более высокому потенциалу в пассивном состоянии за счет сильного окислительного свойства проводящего полимера. (Рисунок 4). В пассивном состоянии скорость коррозии стали значительно ниже. Предполагается, что как барьерный эффект, так и окислительные свойства вызывают анодную защиту. Наконец, потенциал стали подложки может соответствовать окислительно-восстановительному потенциалу слоя полипропилена в последующей реакции и, таким образом, зависит от степени окисления слоя полипропилена.
Проводимость слоя PPy влияет на окислительную способность, которая приводит к пассивному состоянию. Если слой покрытия имеет небольшую проводимость, роль покрытия как окислителя ограничена рядом с пассивным оксидом. Если слой имеет достаточно высокую проводимость; однако окислительная способность всего слоя доступна, и мощность увеличивается с увеличением толщины слоя.
Предполагается, что степень окисления и электропроводность снижаются при более длительном воздействии окружающей среды. Если окислители в окружающей среде повторно окисляют разрушенный слой полипропилена, степень окисления и проводимость могут быть восстановлены. Когда окислитель в окружающей среде, обычно газообразный кислород в воздухе, может восстанавливать слой PPy, продолжительность сохранения окислительной способности слоя PPy может быть увеличена, а пассивное состояние стали под слоем PPy может сохраняться дольше. период. Процесс восстановления показан на рисунке 5.9.0005
3.2. Ионный обмен в проводящем полимере и его влияние на защиту от коррозии
В анодной защите самой большой проблемой является разрушение пассивного оксида из-за воздействия агрессивных анионов, таких как ионы хлорида и брома в растворе, и разрушение сопровождается большим повреждения локализованной коррозии точечной и щелевой коррозии. В отличие от катодной защиты, при анодной защите существует большой риск локальной коррозии. Когда мы контролируем легирующие ионы в слое PPy, мы, возможно, предотвращаем проникновение агрессивных анионов в слой PPy. Когда стали, покрытые токопроводящим PPy, погружают в раствор хлорида натрия, анионы, легированные в PPy, могут обмениваться с анионами хлора в водном растворе. Анионы хлора проникают через PPy в стальную основу, а затем вызывают разрушение поверхностной пассивной оксидной пленки с последующей точечной коррозией.
На подвижность анионов примесей в PPy влияют их масса и объем. Когда мы приняли ионы органических кислот в качестве легирующих ионов в PPy, они обладали достаточно большой массой и объемом, чтобы быть неподвижными в PPy. В целом предполагается, что анионы органических кислот с большой массой обладают малой подвижностью и диффузией в слое PPy. Вместе с окислением и восстановлением PPy небольшие анионы добавляются в PPy и дедопируются из него, соответственно, для поддержания нейтральности, как описано в реакции (1) и показано на рисунке 6(a). Когда подвижность и диффузия легированных анионов ограничены небольшим значением, наоборот, катионы дедопируются и легируются в PPy во время окисления и восстановления соответственно. Процесс дедопирования катионов в PPy при окислении и допирование при восстановлении описываются следующей реакцией (2):
Когда проводящий PPy рассматривается как заряженная мембрана, предполагается, что неподвижные анионы с большой массой имеют фиксированные участки с отрицательным зарядом в PPy. В канале между отрицательно заряженными участками катионы могут быть подвижны, а движение анионов сильно заторможено; то есть мембрана проявляет селективность по катионной проницаемости. Как показано на рис. 6(b), в ситуации, когда количество анионов легирующей примеси достаточно велико, анионы в растворе исключаются из PPy, а стальная основа защищена от питтинговой коррозии за счет воздействия хлоридов.
3.3. Проект защиты от коррозии по PPy
Анодная защита в значительной степени зависит от пассивности и пассивного оксида стали. Для защиты пассивность и пассивный оксид должны оставаться стабильными. Кроме того, важную роль в защите играет предотвращение проникновения агрессивных анионов.
Deslouis et al. анодно приготовили пленку PPy на стали из оксалатного раствора, содержащего мономер Py, и сообщили, что слой PPy защищает сталь в растворе хлорида натрия в течение длительного периода [6–8]. Они предположили, что слой оксалата железа, который образовался под пленкой полипропилена в результате полимеризации, действует как пассивирующая пленка против коррозии. Они также показали, что верхний слой PPy, легированного анионами додецилсульфата (DoS), был эффективен для защиты от коррозии и что двухслойное покрытие PPy-оксалат/PPy-DoS может поддерживать состояние пассивации более 500 часов, в котором продуктов коррозии не наблюдалось.
Ион DoS является поверхностно-активным веществом и образует мицеллы в водном растворе при концентрациях выше критической концентрации. Мономеры Py, которые, вероятно, входят в состав мицелл DoS в водном растворе, начинают полимеризоваться, когда мицеллы коллапсируют на электроде, к которому приложен анодный потенциал. Ионы DoS имеют относительно большие массы и работают как неподвижная примесь в PPy. Таким образом, PPy, легированный DoS, рассматривается как мембрана с отрицательно заряженными фиксированными участками и, следовательно, с катионной проницаемостью. Таким образом, внешний слой PPy-DoS может исключить внедрение агрессивных анионов, таких как ионы хлора.
На рис. 7 показано изменение массы при анодном окислении и катодном восстановлении золотого электрода, покрытого слоями полипропилена [9]. Изменение массы измеряли электрохимическими микровесами на кристалле кварца (EQCM) с золотым покрытием. Золотое покрытие было покрыто PPy, легированным фосфомолибдат-ионами, PMo 12 O 40 3− (PMo) и двухслойным PPy PPy-PMo/PPy-DoS. Изменение массы пленки PPy-PMo на рисунке 7(а) указывает на поглощение массы во время окисления и, наоборот, удаление во время восстановления. Характер изменения массы при окислении отражает отщепление электронов от PPy и одновременное внедрение анионов из электролита в PPy и наоборот при восстановлении. Когда вводится внешний слой PPy-DoS, изменение массы обратно пропорционально результату, приведенному выше, как показано на рисунке 7(b). При окислении масса увеличивается, а при восстановлении уменьшается. В слое PPy-DoS, в котором зафиксированы отрицательно заряженные ионы, катионы подвижны; при окислении происходит одновременное отщепление и электронов, и катионов от PPy, а при восстановлении наоборот. Можно понять, что PPy, легированный DoS, действует как катионная проницаемо-селективная мембрана.
Ковальски и др. защитный слой PPy сталей от коррозии разрабатывали следующим образом [9–14]. Для внутреннего слоя PPy был легирован PMo. PMo действует как пассиватор, который стабилизирует пассивное состояние сталей и способствует образованию пассивного оксида. Для внешнего слоя был приготовлен PPy, легированный DoS. Внешний слой может препятствовать проникновению анионов в слой PPy. Результаты Kowalski et al. представлены на рис. 8, [13], где построен потенциал холостого хода стали, покрытой двухслойным полипропиленом, при погружении в 3,5% раствор хлорида натрия. Сталь, покрытая двухслойным полипропиленом, около 5 мкм толщиной мкм, состоящий из PPy-PMo/PPy-DoS, показал пассивацию в течение 190 ч, при которой не наблюдалось продуктов коррозии. Если сталь была покрыта одним слоем PPy-DoS такой же толщины, то пассивация сохраняется в течение 10 ч. Предполагается, что ион PMo, легированный во внутренний PPy, стабилизирует пассивный оксид и помогает поддерживать пассивное состояние стали-основы.
Конструкция, которая сочетает в себе внутренний слой, стабилизирующий пассивный оксид, с наружным, позже препятствующим проникновению анионов через PPy в сталь, может быть подходящей для защиты стали от коррозии.
3.4. Свойство самовосстановления
При защите от коррозии покрытие должно допускать небольшие дефекты, чтобы его можно было рассматривать как подходящую замену покрытиям на основе хромата. Мы ожидаем, что проводящее полимерное покрытие обладает свойством самовосстановления, при котором пассивный оксид спонтанно восстанавливается после появления в нем небольших дефектов. На хроматном покрытии ионы хромата, растворенные в покрытии, окисляют поверхность стали в поврежденных местах, восстанавливая пассивный оксид.
Модель самовосстановления, предложенная Kowalski et al. показано на рисунке 9для двухслойного PPy PPy-PMo/PPy-DoS [9]. После того, как покрытие и пассивный оксид были локально повреждены, PMo в слое PPy гидролизуется и разлагается на ионы молибдата и фосфата, а затем оба иона достигают дефектных участков. Ионы молибдата реагируют с ионами трехвалентного железа на поврежденном участке с образованием пленки молибдата трехвалентного железа. Солевая пленка может постепенно измениться на пассивный оксид на поврежденном участке
На рис. 10 показаны результаты, опубликованные Kowalski et al. в котором через 2 ч при погружении в 3,5 % раствор хлорида натрия резаком был вставлен небольшой дефект [9].]. После того, как слой PPy получил небольшой дефект, потенциал разомкнутой цепи временно упал. Когда коррозия продолжается в месте дефекта, потенциал снизится до потенциала голой стали. Однако потенциал повышался и восстанавливался в области пассивного потенциала. После этого потенциал поддерживал высокий потенциал в пассивной области. Когда дефектный локальный участок был измерен с помощью спектроскопии рамановского рассеяния в этой ситуации, была обнаружена молибдатная соль [9]. Установлено, что на участке образовался солевой слой молибдата железа.
4. Резюме
За последние 10 лет было опубликовано множество статей по защите от коррозии проводящими полимерами. В них внимание было обращено на то, как сформировать однородные и липкие слои проводящего полимера на стали и других металлах. Для защиты от коррозии мы должны учитывать конструкцию проводящего полимера. Поскольку защита от коррозии с помощью проводящего полимера основана на механизме анодной защиты, мы должны рассмотреть, как стабилизировать пассивный оксид под полимерным слоем и как предотвратить проникновение агрессивных анионов в полимерный слой.
Рассмотрены два механизма защиты от коррозии; одна модель физического барьера и другая модель анодной защиты. Мы предполагаем, что барьерный эффект подавляет активное растворение стали, способствуя смещению потенциала в пассивную область. Окислительная способность проводящего полимера способствует потенциальному смещению и длительному поддержанию пассивного состояния стали.
Наша двухслойная модель, предназначенная для защиты от коррозии, включает в себя два важных фактора: первый — стабилизация пассивирующей пленки на стали под действием ионов легирующей примеси во внутреннем слое PPy, а второй — контроль селективности ионной проницаемости с помощью органической кислоты. ионы, легированные во внешнем слое PPy.
Ссылки
C. K. Chiang, C. R. Fincher, Y. W. Park et al., «Электропроводность в легированном полиацетилене», Physical Review Letters , vol. 39, нет. 17, стр. 1098–1101, 1977.
Посмотреть по адресу:
Сайт издателя | Google Scholar
D. W. DeBerry, «Изменение электрохимического и коррозионного поведения нержавеющих сталей с электроактивным покрытием», Journal of the Electrochemical Society , vol. 132, нет. 5, стр. 1022–1026, 1985.
Просмотр по адресу:
Google Scholar
Б. Весслинг, «Пассивация металлов покрытием полианилином: сдвиг коррозионного потенциала и морфологические изменения», Advanced Materials , vol. 6, нет. 3, pp. 226–228, 1994.
Просмотр по адресу:
Google Scholar
Таллман Д.
Э., Спинкс Г., Доминис А. и Уоллес Г. Г. Электроактивные проводящие полимеры для контроля коррозии: Часть 1. Общие положения введение и обзор цветных металлов», Журнал электрохимии твердого тела , том. 6, нет. 2, pp. 73–84, 2002.
Посмотреть по адресу:
Google Scholar
Э. М. Джинис, Г. Бидан и А. Ф. Диас, «Спектроэлектрохимическое исследование полипиррольных пленок», Журнал электроаналитической химии, том 6, 901 . 149, нет. 1-2, pp. 101–113, 1983.
Просмотр по адресу:
Google Scholar
H. Nguyen Thi Le, B. Garcia, C. Deslouis и Q. Le Xuan, «Corrosion Protection and Conducting полимеры: полипиррольные пленки на железе» Электрохимика Acta , том. 46, нет. 26–27, стр. 4259–4272, 2001.
Посмотреть по адресу:
Сайт издателя | Google Scholar
NTL Hien, B.
Garcia, A. Pailleret, and C. Deslouis, «Роль легирующих ионов в защите железа от коррозии полипирроловыми пленками», Electrochimica Acta , vol. 50, нет. 7–8, стр. 1747–1755, 2005.
Посмотреть по адресу:
Сайт издателя | Google Scholar
T. Van Schaftinghen, C. Deslouis, A. Hubin, and H. Terryn, «Влияние предварительной обработки поверхности перед синтезом пленки на защиту от коррозии железа с помощью полипиррольных пленок», Электрохимика Acta , том. 51, нет. 8–9, стр. 1695–1703, 2006.
Посмотреть по адресу:
Сайт издателя | Google Scholar
Д. Ковальски, М. Уеда и Т. Оцука, «Самовосстанавливающееся ионоселективное проводящее полимерное покрытие», Journal of Materials Chemistry , vol. 20, нет. 36, стр. 7630–7633, 2010.
Посмотреть по адресу:
Сайт издателя | Google Scholar
Т.
Оцука, М. Иида и М. Уеда, «Полипирроловое покрытие, легированное анионами молибдофосфата, для предотвращения коррозии углеродистых сталей», Журнал электрохимии твердого тела , том. 10, нет. 9, стр. 714–720, 2006.
Посмотреть по адресу:
Сайт издателя | Google Scholar
Д. Ковальски, М. Уеда и Т. Оцука, «Защита стали от коррозии двухслойным полипирролом, легированным анионами молибдофосфата и нафталиндисульфоната», Corrosion Science , vol. 49, нет. 3, стр. 1635–1644, 2007.
Посмотреть по адресу:
Сайт издателя | Google Scholar
Д. Ковальски, М. Уеда и Т. Оцука, «Влияние противоанионов на коррозионную стойкость стали, покрытой двухслойной полипиррольной пленкой», Corrosion Science , vol. 49, нет. 8, стр. 3442–3452, 2007.
Посмотреть по адресу:
Сайт издателя | Google Scholar
Д.
Ковальски, М. Уеда и Т. Оцука, «Влияние ультразвукового облучения во время электрополимеризации полипиррола на предотвращение коррозии стали с покрытием», Corrosion Science , vol. 50, нет. 1, стр. 286–291, 2008 г.
Посмотреть по адресу:
Сайт издателя | Google Scholar
Д. Ковальски, М. Уеда и Т. Оцука, «Самовосстановление способности проводящего полипиррольного покрытия с искусственным дефектом», ECS Transactions , vol. 16, нет. 52, стр. 177–182, 2008 г.
Посмотреть по адресу:
Сайт издателя | Академия Google
Copyright
Copyright © 2012 Toshiaki Ohtsuka. Это статья с открытым доступом, распространяемая в соответствии с лицензией Creative Commons Attribution License, которая разрешает неограниченное использование, распространение и воспроизведение на любом носителе при условии надлежащего цитирования оригинальной работы.
Как избежать разрушения полимерного покрытия, ведущего к коррозии материалов
Мы знаем, что в наши дни пластик используется почти во всем, но мы не часто задумываемся о том, что пластик присутствует почти во всем. Полимерные покрытия так же распространены, как латексная краска, покрывающая стены вашего дома. Для промышленного использования полимерные покрытия защищают и украшают продукты в течение последних полувека или около того. До этого краска обычно была на основе свинца или масла.
В наши дни, если вы видите окрашенный продукт, скорее всего, это покрытие на основе полимера, обеспечивающее мощный барьер между основным материалом и элементами в атмосфере, которые хотят разъесть этот материал. Технология полимерных покрытий значительно продвинулась за последнее десятилетие. Покрытия более экономичны, долговечны, обладают большей коррозионной стойкостью и, кроме того, менее вредны для окружающей среды.
Независимо от того, наносится ли полимерное покрытие в виде жидкости с полимером, растворенным в растворителе или диспергированного в латексе, или в виде порошка с полимером, измельченным в мелкую сухую пыль, эти покрытия являются важнейшим компонентом практически любого производства. сектора. Наша инфраструктура (например, мосты, нефтепроводы, транспорт и т. д.) ежедневно зависит от того, что эти покрытия выполняют свою работу и защищают находящиеся под ними металлы от коррозии и деградации.
Чтобы полимерные покрытия обеспечивали необходимую защиту, а также сохраняли свой внешний вид (поскольку эстетика является одинаково важным назначением красок и покрытий), само покрытие должно быть способно блокировать влагу, а целостность его связи с металлом должна точно контролироваться. во время изготовления.
Судьба каждого окрашенного автомобиля, моста, прибора, здания и предмета садовой мебели находится в руках производителей, которые могут гарантировать надежность полимерных покрытий, измеряя и контролируя чистоту поверхностей, на которые они наносятся.
Что такое полимерное покрытие
Полимерное покрытие на самом фундаментальном уровне представляет собой краску или покрытие, изготовленное с использованием полимерных связующих для обеспечения защиты от коррозии и визуальной привлекательности. Полимер представляет собой сложную молекулу, состоящую из более простых молекул, называемых мономерами, в большой цепи молекул, которая придает этим веществам их функциональные свойства в качестве слоя сопротивления всему, что может попытаться разрушить материал под ним, например, влаге, кислотам, растворители и тому подобное.
Краска в своей основной форме представляет собой просто полимер, растворенный в подходящем растворителе, таком как уайт-спирит, разбавитель лака или иногда вода, который наносится кистью, распылением или погружением. Растворитель испаряется и оставляет полимер в виде покрытия. Обычно краски содержат много функциональных добавок помимо полимера, включая пигменты, смачивающие агенты, модификаторы вязкости и многое другое. Совсем недавно были разработаны методы нанесения красок без использования растворителей и модификаторов вязкости.
Порошковые покрытия, с другой стороны, представляют собой измельченные полимеры, смешанные с пигментами и другими добавками, которые напыляются на электростатически заряженные поверхности. После покрытия деталь нагревают, чтобы расплавить и расплавить частицы порошка на поверхности. Поскольку в процессе нанесения не используются жидкости, порошковые покрытия можно наносить более толстым слоем и с меньшими затратами, чем жидкие краски.
Преимущества полимерных покрытий
Полимерные покрытия имеют значительные преимущества перед традиционными процессами окраски. Порошковые покрытия представляют собой 100% твердые покрытия, не требующие растворителей. Это делает их очень привлекательными для производителей, потому что они не включают дополнительные расходы на покупку или утилизацию растворителей и позволяют производителям в большей степени соблюдать правила летучих органических соединений (ЛОС), предназначенные для защиты окружающей среды и качества воздуха.
Чтобы узнать больше о разработке процессов нанесения полимерных покрытий, не оставляющих ничего на волю случая, загрузите нашу бесплатную электронную книгу: Predictable Adhesion in Manufacturing Through Process Verification.
Порошковые покрытия также имеют то преимущество, что в процессе нанесения образуется очень мало отходов. Традиционные процессы покраски стараются избежать чрезмерного распыления, которое приводит к потере краски, иначе называемому бракованным материалом. В отличие от традиционных процессов окраски, излишки порошкового покрытия можно собирать и использовать повторно.
Одним из наиболее существенных преимуществ полимерных покрытий является отсутствие влияния на другие свойства материалов, на которые они наносятся. Например, если полимерное покрытие используется для защиты контейнера, предназначенного для транспортировки и хранения химикатов, это покрытие никак не повлияет на безопасность и механическую прочность материала, на который оно нанесено. За последние десять лет исследования показали множество достижений в области функциональных покрытий , которые упростили использование, стали самоочищающимися, антибактериальными и обладают противообрастающими свойствами.
Как правило, в процессах нанесения полимерных покрытий могут использоваться покрытия, которые намного более твердые, более термостойкие, могут лучше прилипать к подложке и намного более долговечны, чем традиционные покрытия.
Процесс полимерного покрытия
Краски на водной основе не содержат летучих органических соединений, что позволяет решить упомянутую выше экологическую проблему, но они намного менее долговечны, чем полимерные покрытия, из-за их чувствительности к чистоте поверхности материалов, на которые они наносятся. Если поверхность не очищена до чрезвычайно высокого стандарта, краски на водной основе труднее прилипают к поверхности.
Подготовка поверхности всегда является важным этапом процесса для обеспечения прочной адгезии полимерных покрытий, но важно правильно подготовить поверхности для нанесения. Тип покрытия и свойства этого покрытия необходимо понимать при разработке процесса очистки и обработки поверхности.
Обычно в производстве термин «полимерное покрытие» является сокращением от «порошковое покрытие», хотя жидкие краски также представляют собой полимерные пленки, прилипшие к поверхности материала. Типичный процесс порошковой окраски начинается с того, что оператор загружает окрашиваемые детали на конвейер, который может быть подвешен к потолку или к полу. Это первая критическая контрольная точка (ККТ) или любая точка в производственном процессе, где поверхность материала может химически измениться (загрязнить или удалить загрязнения). Введение деталей в процесс всегда является первой ККТ, и производители должны позаботиться о измерении чистоты поверхности всех поступающих деталей перед их обработкой, чтобы получить базовое представление о том, насколько загрязнены или загрязнены материалы в самом начале. Этот шаг позволяет производителям выявлять критические проблемы с чистотой до того, как деталь будет обработана, и стоит компании времени и денег из-за переделок и брака.
Следующий этап и второй ККТ в этом процессе состоит из процедур очистки с использованием любой комбинации методов, начиная от промывки распылением, химической очистки, травления, а затем промывки и сушки. Это технологический пробел, который, если его не устранить, может привести к текстуре покрытия «апельсиновая корка», проколам, непостоянному покрытию и целому ряду других очень распространенных сбоев.
Следует понимать, что каждый раз, когда что-то вступает в контакт с деталью, даже если это мыло, руки техника, перемещающие его с одного шага на другой, или даже просто вода, загрязняющие вещества на молекулярном уровне могут переноситься на поверхности и вызвать плохое прилипание порошкового покрытия или его полное отсутствие.
Чистые поверхности очень хрупкие и могут быстро меняться. Это связано с тем, что чистые поверхности обладают тем, что ученые-поверхностники называют «высокой свободной поверхностной энергией». Когда поверхность чистая, она хочет реагировать со всем, с чем соприкасается, что отлично подходит для адгезии, но также означает, что если поверхность подвергается воздействию воздуха, загрязненных «чистящих» моющих средств или грязного оборудования, вещества, препятствующие адгезии может переноситься на поверхность материала.
Для нанесения полимерных покрытий обычно используется распылительное оборудование, которым покрывают поверхность подвесных деталей на автоматизированной сборочной линии. Эти детали состоят не только из больших плоских поверхностей, на которые легко наносить покрытие, они также включают узкие углы, края, изгибы, механические крепления и другие крошечные области, которые создают трудности для производителей, стремящихся нанести однородное и однородное покрытие. На эти области не только трудно нанести покрытие из-за явления, называемого эффектом клетки Фарадея, но и труднее гарантировать их чистоту, что может привести к отслоению полимерного покрытия от этих областей. Если в одном из этих небольших пространств присутствуют загрязняющие вещества, нарушающие адгезию полимерного покрытия, их может быть чрезвычайно трудно обнаружить и предотвратить разрушение покрытия.
Процесс порошковой окраски может быть сложным, так как есть несколько новых факторов, таких как необходимость заземления металлической детали, на которую наносится покрытие, правильность восстановления и повторного использования пластикового порошка и т. д. Но есть один аспект процесс, который является абсолютно жизненно важным и часто упускается из виду или, по крайней мере, не контролируется.
Прежде чем покрытие сможет хорошо прилипнуть к поверхности, поверхность должна быть тщательно очищена и подготовлена. Это почти само собой разумеется. Не существует процесса порошковой окраски, который не требует какой-либо очистки и подготовки поверхности; однако эти этапы обычно контролируются только визуально, если вообще контролируются, из-за отсутствия эффективных инструментов измерения чистоты, доступных для использования на производственной линии.
Независимо от того, выполняется ли процесс порошкового покрытия вручную на нескольких деталях каждый час или осуществляется с помощью автоматизации, способной покрывать десятки тысяч деталей каждый день, если нет возможности измерить, насколько чистые поверхности перед нанесением покрытие, то отказ неизбежен и затраты высоки.
Типы отказов полимерного покрытия
Разрушение полимерного покрытия является огромным экономическим ущербом для общества. Каждый крупный мост в Соединенных Штатах ржавеет, надлежащее обслуживание любой металлической пожарной лестницы требует постоянного повторного нанесения защитных покрытий, а коррозия является основной причиной утечек и разливов нефтепроводов.
В 2013 году 70 000 мостов по всей стране были квалифицированы как «дефектные». В том же году отчет Американского общества инженеров-строителей по американской инфраструктуре поставил стране оценку D+ за ее инфраструктуру, а предполагаемые инвестиции, необходимые к 2020 году, составили 3,6 триллиона долларов. По оценкам Института Ассоциации по защите материалов и характеристик (AMPP, ранее NACE — Национальная ассоциация инженеров по коррозии), «абсолютная коррозия обходится экономике США более чем в 500 миллиардов долларов США в год, или примерно 3,1 процента нашего ВВП».
Согласно исследованию стоимости коррозии в США, подготовленному AMPP, коррозия обходится разведке и добыче нефти и газа США в 1,4 миллиарда долларов в год.
Эти проблемы могут быть в значительной степени смягчены защитными полимерными покрытиями, которые предотвращают коррозию и поддерживают структурную целостность.
Долговечность полимерного покрытия и его способность защищать нижележащий объект от коррозии или деградации зависит от двух факторов:
- Способность покрытия препятствовать проникновению влаги
- Качество сцепления с подложкой
Эти две характеристики тесно связаны, поскольку надежная адгезия помогает бороться с попаданием влаги на нижележащий материал.
Все покрытия со временем разрушаются. Граница между полимерным покрытием и подложкой не является на 100% химически стабильной. Это особенно верно, когда подложка стальная. Ни один материал не сочетает в себе прочность и низкую стоимость стали, поэтому он по-прежнему является предпочтительным материалом для мостов, трубопроводов и автомобилей, но он ржавеет. В отличие от границы раздела полимер-сталь, поверхность раздела между полимерным покрытием и полимерной подложкой гораздо более химически стабильна и, следовательно, более долговечна. Это одна из причин, по которой производители автомобилей (и все чаще инженеры-строители!) ищут передовые композитные материалы для своих новейших разработок: пластик или композит с покрытием не имеют чувствительной к влаге поверхности раздела металл-полимер, которая со временем разрушается.
Когда мы говорим о химической стабильности, мы имеем в виду способность сохранять целостность в присутствии любой влаги, которая диффундирует через полимерное покрытие к границе между полимером и подложкой. Именно эта влага вызывает коррозию и потерю адгезии.
Интеллектуальный состав краски снижает скорость проникновения влаги, но никогда не может остановить ее полностью, а хорошие методы обработки поверхности снижают скорость коррозии подложки, но никогда не могут остановить ее полностью.
Однако, когда качество покрытия и поверхности контролируется, скорость деградации может быть замедлена до такой степени, что она практически незаметна, а защитное качество покрытия может сохраняться в течение многих-многих лет.
Как обеспечить прочное и долговечное полимерное покрытие
Первым шагом является обеспечение однородной чистоты покрываемой поверхности на молекулярном уровне. Прочная, надежная адгезия возникает, когда два вещества химически совместимы в верхних 2-5 молекулярных слоях их поверхностей. Любой процесс очистки, обработки или подготовки изменяет молекулярный состав поверхностей. Очень важно измерять чистоту поверхностей на протяжении всего производственного процесса с помощью метода, чувствительного к этим изменениям на молекулярном уровне.
Самый удобный и чувствительный способ проверить чистоту поверхности — использовать быстрые измерения контактного угла, оптимизированные для производства. Эти количественные измерения предлагают точный метод управления технологическим процессом, поэтому производители могут прогнозировать результаты покрытия и создавать высокопроизводительные продукты.
Технология полимерных покрытий значительно продвинулась в новейшей истории. Полимерные покрытия более экономичны, долговечны, обеспечивают лучшую коррозионную стойкость и менее вредны для окружающей среды, чем традиционные краски. Однако качество полимерного покрытия зависит от качества поверхности подложки. Надлежащая производственная практика, включающая измерение и контроль качества поверхности, имеет решающее значение для производителей, которые хотят увеличить производительность, снизить риски и отходы, а также создавать надежные продукты или здания и мосты.
Чтобы узнать больше о разработке процессов нанесения полимерных покрытий, которые не оставляют ничего на волю случая, загрузите нашу бесплатную электронную книгу: Predictable Adhesion in Manufacturing Through Process Verification.
Материалы Покрытия, гальванические покрытия и отделочные покрытия
Основная функция покрытий, будь то простые краски или сложные напыляемые пленки, заключается в защите подложек от повреждений в условиях эксплуатации.
Покрытия улучшают внешний вид, коррозионную стойкость, стойкость к истиранию и
электрические или оптические свойства. Их можно наносить мокрым или сухим способом, с помощью простого или сложного оборудования. Выбор почти безграничен, потому что почти любой материал покрытия обеспечивает некоторую степень защиты, пока он сохраняет свою целостность. Если оно обеспечивает непрерывный барьер между основанием и окружающей средой, даже тонкое декоративное покрытие может выполнять свою работу в относительно сухой и мягкой среде.
Главы по покрытиям, покрытиям и отделке:
|
Металлические покрытия
Было разработано много новых материалов, но сталь остается основной конструкцией. Материал для автомобилей, бытовой техники и промышленного оборудования. Из-за уязвимости стали к воздействию агрессивных химических сред или даже к простому атмосферному окислению для обеспечения различных степеней защиты необходимы покрытия. Они варьируются от горячеоцинкованных металлов и металлов с гальваническим покрытием до прочных полимеров и пламенной керамики.
Как правило, агрессивные среды содержат более одного активного материала, и покрытие должно противостоять проникновению комбинации окислителей, растворителей или того и другого. Таким образом, лучшим барьером является тот, который противостоит «широкополосной» коррозии.
Во многих случаях физическая целостность покрытия так же важна, как и его химические барьерные свойства. Приложения. Например, покрытия на рабочих колесах, которые смешивают абразивные суспензии, могут быстро истираться; покрытия на стыках труб будут нахлестывать от нагруженного участка, если скорость ползучести не низкая; а покрытия на фланцах и опорных кронштейнах могут быть отколоты или пробиты во время сборки, если ударная вязкость недостаточна. Выбор наилучшего покрытия для применения требует оценки всех воздействий конкретной среды, включая тепловые и механические условия.
Цинк:
Одним из самых распространенных и недорогих способов защиты стали является цинк. Оцинкованная или гальванизированная сталь производится с использованием различных методов горячего погружения, но сегодня все больше сталелитейных компаний переходят на электрогальваническое цинкование, поэтому они могут обеспечить и то, и другое.
Защита стали от окисления цинком действует двумя способами: сначала как барьерное покрытие, а затем как расходуемое покрытие. Если цинковое покрытие поцарапано или повреждено, оно продолжает обеспечивать защиту за счет гальванического воздействия до тех пор, пока слой цинка не истощится. Это жертвенное действие также предотвращает коррозию вокруг пробитых отверстий и на краях реза.
Марки оцинкованной стали, выпускаемые в продажу в последние годы, были разработаны для преодоления недостатков традиционной оцинкованной стали, которую трудно сваривать и красить до получения гладкой поверхности. Новые материалы предназначены специально для штампованных автомобильных компонентов, которые обычно соединяются точечной сваркой и требуют гладкой окраски класса А.
Среди современных улучшенных оцинкованных сталей — семейство Paint-Tite B компании Inland Steel, состоящее из трех продуктов. Эти оцинкованные (термически обработанные) стали имеют цинковое покрытие, нанесенное методом горячего погружения, с одной стороны и легкое покрытие, нанесенное газовой струей, с гладкой стороны. Они проходят термическую обработку для получения однородного, без блесток, окрашиваемого, свариваемого покрытия из цинково-железного сплава. Поскольку кристаллы цинка и железа на стороне с покрытием очень мелкие, лист можно формовать или прокатывать без «сквозной печати» на верхней поверхности.
Другой улучшенной сталью с цинковым покрытием является Ultrasmooth от Armco, которая имеет горячее цинковое покрытие с обеих сторон и поверхности, сравнимые с отделкой холоднокатаной стали класса 1. Струи азота, окружающие сталь при выходе из расплавленного цинка, контролируют толщину покрытия. Полученные поверхности не имеют волнистости и оксидных узоров, обычно встречающихся на обычных сталях с горячим цинкованием.
Новейший оцинкованный продукт Armco, Electrasmooth, имеет электрогальваническое покрытие с одной или обеих сторон. Изготовленный методом вертикальных ячеек, он имеет гладкую однородную поверхность, подходящую для окрашенных автомобильных панелей, оберток для бытовой техники и архитектурных изделий. Покрытия Electrasmooth доступны для всего ассортимента товарных сплавов и сплавов для волочения.
Еще одним новым процессом цинкования сталей является Galfan, разработанный Международной организацией по исследованию свинца и цинка (ILZRO). Кроме цинка в состав покрытия входит мишметалл (смесь церия, лантия и других редкоземельных металлов) и 5% алюминия. Утверждается, что гальфан обеспечивает улучшенную формуемость и окрашиваемость, а также обладает в два-три раза большей коррозионной стойкостью по сравнению с обычной сталью, оцинкованной горячим способом, в испытаниях на воздействие соляного тумана, диоксида серы и влажности.
Лицензии на производство материала в США были предоставлены Gregory Galvanizing & Metal Processing Inc., Кантон, Огайо, и Weirton Steel Corp., Вейртон, Западная Вирджиния. Галфан использовался в Европе и Японии в таких областях, как строительные панели. , запчасти для автомобилей и бытовой техники, а также морской трос. Применение в США включает панели для стиральных машин, столбы забора и связанные с ними компоненты, а также фурнитуру для гаражных ворот. Автомобильные приложения включают трубки для линий охлаждения трансмиссии, различные кронштейны и кожухи под капотом, а также, для 1988 Ford T-Bird, защита топливного бака.
Другим коррозионностойким продуктом из стали с покрытием, содержащим цинк, является Zincrometal (Metal Coatings International), который обрабатывается с помощью запатентованной двухслойной системы. Базовое покрытие представляет собой неорганический материал на основе хрома под названием Dacromet. После запекания покрытия на рулон наносится второй материал — Zincromet, верхнее покрытие на основе эпоксидной смолы с высоким содержанием цинка, после чего следует еще один цикл запекания.
Как и другие материалы с цинковым покрытием, Zincrometal используется в основном для наружных панелей грузовиков и автомобилей. Минимальная толщина сухой пленки для таких применений составляет 0,5 мил. При использовании соответствующих смазочных материалов и составов для волочения способность материала к формованию сравнима с холоднокатаной сталью. Утверждается, что сварочные характеристики аналогичны характеристикам стали без покрытия.
В отличие от материалов, оцинкованных горячим способом или электрооцинкованных материалов, Zincrometal обеспечивает барьерную, а не жертвенную защиту. Таким образом, он рекомендуется для использования там, где защита от коррозии является основной потребностью, где компоненты не подвергаются истиранию или механическому воздействию. Однако Zincrometal, который производится на платной основе компаниями, занимающимися нанесением рулонного покрытия, по сути, является односторонним продуктом и в некоторых автомобильных приложениях заменяется сталью с двусторонним покрытием.
Алюминий:
Производятся два типа стали с алюминиевым покрытием, каждый из которых обеспечивает различный вид защиты от коррозии. Тип 1 имеет алюминиево-кремниевое покрытие методом горячего погружения, обеспечивающее устойчивость к нагреву и коррозии. Тип 2 имеет горячее покрытие из технически чистого алюминия, что обеспечивает превосходную долговечность и защиту от атмосферной коррозии. Оба сорта, разработанные Armco, производителем этих алюминизированных сталей, обычно используются неокрашенными.
Сталь с алюминиевым покрытием типа 1 устойчива к тепловому накипи до 1250°F и имеет превосходную теплоотражающую способность до 900°F. Номинальное покрытие из алюминиевого сплава составляет около 1 мил с каждой стороны. Лист поставляется с мягкой, атласной отделкой. Типичные области применения включают отражатели и корпуса для панелей промышленных обогревателей, внутренние панели и теплообменники для бытовых печей, микроволновые печи, системы глушителей автомобилей и грузовиков, теплозащитные экраны для каталитических нейтрализаторов и оборудование для контроля загрязнения.
Алюминированная сталь типа 2 с алюминиевым покрытием толщиной около 1,5 мил с каждой стороны устойчива к атмосферная коррозия и, как утверждается, превосходит срок службы оцинкованного листа в промышленных условиях в пять раз. Типичными применениями являются промышленные и коммерческие кровли и сайдинг, сушильные шкафы, крыши силосов и корпуса для наружного освещения и кондиционеров.
Для применения при более высоких температурах покрытия типа 1 поставляются на двух новых продуктах.
Aluma-Ti представляет собой дегазированную в вакууме сталь без пор, содержащую ниобий и титан, которую можно использовать в циклическом режиме до 1400°F. Второй продукт, Aluma-Fuse, работает при максимальной температуре металла 1600°F. Его высокотемпературные свойства обусловлены сочетанием диффузионного покрытия и основного металла из низколегированной стали, содержащей хром, алюминий, кремний, ниобий и титан, а также термической обработки.
Armco также разработала процесс нанесения алюминиевого покрытия на нержавеющую сталь типа 409. Ожидается, что этот продукт, впервые испытанный на некоторых автомобилях 1987 года, продлит срок службы выхлопной системы до пяти и более лет благодаря своей превосходной устойчивости к коррозии, вызванной горячим конденсатом выхлопных газов и дорожными солями. Еще одно преимущество алюминиевого покрытия – косметическое. Предотвращает появление красной ржавчины на неопределенный срок.
Гальваническое покрытие:
Использование защитных металлов с гальваническим покрытием в последние годы изменилось, в основном из-за постановлений Агентства по охране окружающей среды. Использование растворов для покрытия цианидом, кадмия и свинца строго ограничено или полностью запрещено. Однако широко используются хромовые и никелированные покрытия, наносимые как традиционными методами гальванического покрытия, так и новыми, более эффективными методами, такими как высокоскоростное электроосаждение (FRED). Этот последний метод также успешно использовался Battelle Columbus Labs для нанесения нержавеющей стали на железные подложки.
Покрытие из функционального хрома или «твердого хрома» используется для предотвращения заедания и снижения трения. характеристики, а также для защиты от коррозии. Эти покрытия обычно наносятся без медных или никелевых подложек толщиной от 0,3 до 2 мил. Твердое хромирование рекомендуется для использования в соленых средах для защиты компонентов из черных металлов.
Никелированные покрытия толщиной от 0,12 до 3 мил используются в оборудовании для обработки пищевых продуктов, на изнашиваемых поверхностях упаковочного оборудования и для покрытия реакционных сосудов.
Химическое никелирование, в отличие от обычного гальванического покрытия, работает химически, а не использует электрический ток для осаждения металла. Химический процесс наносит однородное покрытие независимо от формы подложки, преодолевая главный недостаток гальванического покрытия — сложность равномерного нанесения покрытия на компоненты неправильной формы. В химическом процессе нет необходимости в соответствующих анодах и сложном креплении. Толщина отложения регулируется простым контролем времени погружения. Процесс осаждения является автокаталитическим с толщиной слоя от 0,1 до 5 мил.
Запатентованные системы химического покрытия содержат, помимо никеля, такие элементы, как
фосфор, бор и/или таллий. Относительно новый состав, называемый полисплавом, состоит из трех или четырех элементов в ванне. Эти продукты, такие как Nibron производства Pure Coatings Div. Pure Industries и Niklad от Allied Kelite Div. компании Witco Chemical Corp., как утверждается, обеспечивают превосходную износостойкость, твердость и другие свойства по сравнению с обычными методами химического осаждения.
Полисплав Nibron содержит никель, таллий и бор. Первоначально разработанный для авиационных газотурбинных двигателей, Nibron обладает превосходной износостойкостью. Сравнительные испытания показывают, что относительный износ детали с нибронным покрытием, измеренный с помощью альфа-теста Dow Corning LFW-1, значительно меньше, чем у твердых хромовых и никель-фосфорных покрытий.
Как правило, никель-боровые покрытия имеют узелковую структуру. По мере увеличения толщины покрытия размер узелков также увеличивается. Поскольку столбчатая структура покрытия изгибается при движении подложки, никель-бор устойчив к сколам и износу.
Качество адгезии ниброна зависит от таких факторов, как материал подложки, подготовка детали и загрязнение. Хотя он отлично подходит для инструментальных сталей, нержавеющей стали, высокоэффективных сплавов на основе никеля и кобальта и титана, некоторые металлические подложки несовместимы. К ним относятся металлы с высоким содержанием цинка или молибдена, алюминий, магний и карбид вольфрама. Однако модификации могут устранить эту несовместимость. Например, Nibron можно наносить на хромированный алюминий.
Другая тенденция в композитном покрытии химическим способом, по-видимому, связана с соосаждением твердых частиц в металлической матрице. Эти покрытия коммерчески доступны только с несколькими типами частиц — алмазом, карбидом кремния, оксидом алюминия и ПТФЭ, причем алмаз возглавляет список по популярности.
Одним из примеров запатентованного композитного покрытия, включающего ПТФЭ, является компания Nimet Industries. NiCoTef, который равномерно распределяет субмикронные частицы ПТФЭ по никелево-фосфорной матрице. ПТФЭ включается в количестве от 23 до 25% в гальванические покрытия, что обеспечивает чрезвычайно низкий коэффициент трения. Поскольку ПТФЭ наносится совместно с никель-фосфорной матрицей, а не наносится на поверхность при последующей операции, его подача осуществляется непрерывно в течение всего срока службы покрытия.
NiCoTef хорошо изнашивается в условиях скольжения, когда нагрузка незначительна и равномерно распределена. Он эффективно продлевает срок службы деталей во многих областях применения за счет снижения трения. Кроме того, высокое содержание фосфора в матрице обеспечивает отсутствие пор и высокую устойчивость к коррозии как в щелочных, так и в кислых средах.
Сочетание смазывающей способности NiCoTef, равномерной толщины покрытия и коррозионной стойкости делает его особенно подходящим для клапанов; гидравлические системы; застежки; прецизионные электронные приложения; компоненты карбюратора, тормоза, двигателя и системы впрыска топлива; насосы; опорные и погрузочно-разгрузочные поверхности; маленькие уши; цилиндры, пресс-формы и штампы; смесительные лопасти; и компьютерные компоненты.
Покрытие можно наносить на большинство металлов, включая железо, углеродистую сталь, чугун, алюминиевые сплавы, медь, латунь, бронзу, нержавеющую сталь и высоколегированные стали.
Конверсионные покрытия: Химические покрытия более точно называют конверсионными покрытиями, поскольку они создают защитный слой или пленку на поверхности металла посредством химической реакции. Другой процесс преобразования, покрытие черным оксидом, успешно применяется в самых разных областях, от крепежа до аэрокосмической промышленности. Черный оксид приобретает все большую популярность, поскольку обеспечивает коррозионную стойкость и эстетическую привлекательность без изменения размеров деталей.
На химическом уровне черное оксидирование происходит, когда железо на поверхности стали реагирует с образованием магнетита (Fe3O4). Переработчики используют неорганические растворы для чернения для проведения реакции. Окисляющие соли сначала растворяют в воде, затем кипятят и выдерживают при температуре от 280 до 285°F. Поверхность изделия очищается щелочным раствором, а затем ополаскивается перед погружением в раствор для чернения. После второго ополаскивания поверхность герметизируется средствами для предотвращения ржавчины, благодаря чему поверхность может варьироваться от слегка маслянистой до твердой и сухой.
Черное оксидирование создает микропористую поверхность, которая легко сцепляется с верхним покрытием. Например, можно добавить дополнительное масляное верхнее покрытие для повышения стойкости к солевому туману до того же уровня, что и у цинковой пластины с прозрачным хромовым покрытием (от 100 до 200 часов).
Черный оксид можно использовать с мягкой сталью, нержавеющей сталью, латунью, бронзой и медью. Если детали не содержат окалины и не требуют травления, покрытие не приведет к водородному охрупчиванию или изменению размеров деталей. Рабочие температуры варьируются от криогенных до 1000°F.
Напыление:
Ранее использовавшееся в основном для производства компонентов интегральных схем, напыление перешло на крупные производственные операции, такие как «гальваническое покрытие» деталей автомобильной отделки. Этот процесс позволяет наносить тонкие клейкие пленки, обычно из металла, в плазменной среде практически на любую подложку.
Напыление дает производителям автомобилей несколько преимуществ в качестве экономичной замены традиционному хромированию. Линии напыления дешевле в установке и эксплуатации, чем системы для нанесения покрытий. А поскольку напыляемые покрытия являются равномерными и тонкими, для получения приемлемой отделки требуется меньше материала покрытия. Кроме того, нет необходимости в контроле за загрязнением, потому что в процессе не образуются сточные воды. Наконец, напыление требует меньше энергии, чем обычные системы покрытия.
Хромирование пластмасс и металлов — это только одно из применений напыления. Метод не ограничивается нанесением металлических пленок. Исследовательский центр Льюиса НАСА успешно напылял ПТФЭ на металлические, стеклянные, бумажные и деревянные поверхности. В другом случае кость крупного рогатого скота напыляли на металлические протезы для использования в качестве замены бедренной кости. Пленка из напыленной кости способствует росту кости и прикреплению к живой кости.
Напыление — единственный метод осаждения, который не зависит от температуры плавления и давления паров тугоплавких соединений, таких как карбиды, нитриды, силициды и бориды. В результате пленки этих материалов можно напылять непосредственно на поверхности без изменения свойств подложки.
Большая часть исследований распыления в Исследовательском центре Льюиса направлена на производство твердопленочных смазочных материалов и твердых износостойких тугоплавких смесей. НАСА заинтересовано в этих трибологических приложениях, потому что покрытия можно наносить напылением без связующего, с сильным сцеплением и с контролируемой толщиной на изогнутых поверхностях и поверхностях сложной формы, таких как шестерни и держатели подшипников, кольца и шарики. Кроме того, поскольку напыление не ограничивается термодинамическими критериями (в отличие от большинства обычных процессов, в которых используется подвод тепла), свойства пленки можно настроить так, как это невозможно при использовании других методов осаждения.
Большинство исследований напыленных пленок твердых смазок было проведено с MoS2. Другие фильмы
напылением являются карбид вольфрама, нитрид титана, оксид свинца, золото, серебро, олово, свинец, индий, кадмий, ПТФЭ и полиимид. Из этих покрытий наиболее заметными являются покрытия из нитрида титана (TiN) золотистого цвета.
Покрытия TiN меняют как внешний вид, так и характеристики металлорежущих инструментов из быстрорежущей стали. Срок службы инструментов с покрытием TiN, согласно заявлениям производителей, увеличивается в десять раз, скорость съема металла может быть удвоена, и возможно большее количество переточек, прежде чем инструмент будет выброшен или восстановлен.
Ионное покрытие:
Основное различие между напылением и ионным покрытием заключается в том, что напыляемый материал образуется в результате ударного испарения и передается в процессе передачи импульса. При ионном напылении испаряющийся продукт образуется в результате термического испарения. Ионное покрытие сочетает в себе высокую рассеивающую способность гальванического покрытия, высокую скорость осаждения при термическом испарении и высокую энергию столкновения ионов и энергичных атомов процессов распыления и ионной имплантации.
Превосходная адгезия пленок с ионным покрытием объясняется формированием плавного перехода между пленкой и подложкой, даже если два материала несовместимы. Градиентный интерфейс также укрепляет поверхностные и подповерхностные зоны и увеличивает усталостную долговечность.
Высокая метательная способность и отличная адгезия позволяют наносить сложные покрытия. трехмерные конфигурации, такие как внутренние и внешние трубки, зубья шестерен, шарикоподшипники и крепежные детали. Зубчатые колеса для космического применения, например, были покрыты ионным покрытием золотом размером от 0,12 до 0,2 мкм для смазки и предотвращения холодной сварки линии шага зубчатого колеса. Ионное покрытие также использовалось в производстве для покрытия алюминия компонентами шасси самолета для защиты от коррозии.
Ионное покрытие также является одним из двух методов, используемых для нанесения алмазоподобных покрытий (DLC). Относительно новый продукт в области покрытий, DLC обычно изготавливают из углеводородов (часто метана) и водородных газов, нагретых до 2000°C. Углеродные покрытия ценятся за их износостойкость, а также электрические и оптические свойства. Хотя они представляют собой огромный потенциал, нынешние DLC находятся на самых ранних стадиях коммерциализации. Тем не менее, их широкий спектр свойств, наряду с их относительно низкой стоимостью, заставляет многих предсказывать огромный рост DLC.
В Battelle Laboratories в Колумбусе, штат Огайо; Женева, Швейцария; и Франкфурт, Западная Германия, работа над DLC продолжается. Исследователи Battelle предлагают использовать покрытия для повышения износостойкости насадок инструментов, в качестве электронных радиаторов, а также для повышения износостойкости и коррозионной стойкости оптических материалов.
Химическое осаждение из паровой фазы (CVD) — это метод, наиболее часто используемый для осаждения DLC. Регулировка условий осаждения позволяет переработчику изменить покрытие с графитового на алмазоподобное. Один процесс, используемый в Battelle, наносит DLC в газовой атмосфере при пониженном давлении без фиксированной цели. Этот плазменный метод CVD позволяет наносить покрытие на большие детали со всех сторон, не поворачивая их. Однако при использовании CVD подложки должны быть нагреты примерно до 800°C.
Снижение температуры подложки достигается за счет двойного ионно-лучевого осаждения, процесса, разработанного BeamAlloy Corp. Температура подложки достигает всего 150°F, а процесс двойного ионного луча не зависит от эпитаксиального роста для его формирования, как это делает CVD. Для эпитаксиального роста требуется кристаллическая подложка; поскольку обработка двойным ионным пучком не требует этой необходимости, она также позволяет наносить покрытия на аморфные материалы.
Материалы, совместимые с процессом Diond компании BeamAlloy, включают черные и цветные металлы, стекло, керамику, пластмассы и композиты. В дополнение к покрытию Diond, двойное ионно-лучевое осаждение позволяет наносить металлические покрытия на углерод/углеродные материалы, армированные волокном.
Основной процесс ионной имплантации посылает пучки элементарных атомов (произведенных в ускорителе частиц) на поверхность целевого компонента. При двойном усиленном ионно-лучевом осаждении используются два одновременных луча. Один луч непрерывно распыляет углерод на поверхность, обеспечивая углеродный материал, необходимый для выращивания алмазной пленки. Второй луч, состоящий из инертного газа с более высокой энергией, перемещает часть алмазного слоя в зону раздела. Затем энергия второго луча снижается, чтобы обеспечить рост алмаза. Имплантация алмазного материала в зоне контакта оптимизирует адгезию.
Термическое напыление:
Дуговое напыление, форма термического напыления металлов, выполняется на подготовленной (обычно пескоструйной) металлической поверхности с использованием проволочно-дугового пистолета. Металл покрытия представляет собой две проволоки, которые подаются со скоростью, поддерживающей постоянное расстояние между их концами. Электрическая дуга разжижает металл, а воздушная струя набрасывает его на подложку. Поскольку скорость частиц может значительно варьироваться, этот процесс может производить покрытие с различной текстурой от тонкой до грубой.
Покрытия, нанесенные электродуговым напылением, несколько пористы и состоят из множества перекрывающихся пластинок. Используемые в тех случаях, когда важен внешний вид, покрытия, нанесенные термическим напылением, могут быть герметизированы пигментированными виниловыми сополимерами или красками, которые обычно увеличивают срок службы металлического покрытия. Покрытия, нанесенные электродуговым напылением, толще, чем покрытия, наносимые горячим погружением: от 3 до 5 мил для легких условий эксплуатации при низких температурах и от 7 до 12 мил для тяжелых условий эксплуатации.
Поскольку цинк и алюминий в большинстве случаев более устойчивы к коррозии, чем сталь, они являются наиболее широко используемыми металлами для нанесения покрытий распылением. Кроме того, поскольку оба металла являются анодными по отношению к стали, они действуют гальванически для защиты железных подложек.
В целом алюминий более долговечен в кислой среде, а цинк лучше работает в щелочной среде. Для защиты стали на газовых или химических заводах, где температура может достигать 400°F, рекомендуется использовать алюминий. Цинк предпочтителен для защиты стали в пресных холодных водах; в водных растворах при температуре выше 150°F обычно выбирают алюминий.
Для эксплуатации при температурах до 1000°F термически напыленное алюминиевое покрытие должно быть покрыто силиконово-алюминиевой краской. При температуре от 1000 до 1650°F алюминиевое покрытие плавится и вступает в реакцию со стальным основным металлом, образуя покрытие, которое, не будучи герметизированным, защищает конструкцию от окисляющей среды. А для непрерывной работы до 1800 ° F используется никель-хромовый сплав, за которым иногда следует алюминий.
В Европе, где термически напыляемые металлические покрытия для защиты от коррозии используются гораздо шире, чем в США, многие конструкции, такие как мосты, по прошествии 40 лет все еще находятся в хорошем состоянии при минимальном обслуживании. Другие области применения включают дымовые трубы, корпуса лодок, мачты и многие наружные конструкции.
Термическое напыление стало намного больше, чем процесс восстановления изношенных металлических поверхностей. Благодаря сложному оборудованию и прецизионному контролю, теперь он учитывается в процессе проектирования, создавая однородные покрытия металлов и керамики. С помощью некоторых процессов можно наносить даже градуированные покрытия. Это делается путем покрытия подложки материалом, который обеспечивает хорошее сцепление и имеет совместимые характеристики расширения, с последующим постепенным переходом на второй материал для получения требуемого качества поверхности, такого как износостойкость, способность к пайке или теплоизоляционные характеристики.
Плазменное напыление:
Плазменное покрытие основано на горячем высокоскоростном плазменном пламени (азот, водород или аргон) для расплавления порошкообразного материала и распыления его на подложку. Дуга постоянного тока поддерживается для возбуждения газов в состояние плазмы.
Высокотемпературная плазма (свыше 15 000°F) позволяет этому процессу работать с различными материалами покрытия — большинством металлов, керамики, карбидов и пластмасс. Хотя большинство материалов для покрытий нагреваются намного выше их точек плавления, температура подложки обычно остается ниже 250°F.
Этот процесс нашел широкое применение в авиационной промышленности. Металлические покрытия с плазменным напылением защищают лопатки турбины от коррозии, а напыляемая керамика обеспечивает термобарьерную защиту других деталей двигателя.
Запатентованные усовершенствования в технологии плазменного напыления включают в себя износостойкий материал покрытия, который позволяет образовывать аморфные/микрокристаллические фазы при плазменном напылении. Полученное покрытие обеспечивает превосходную коррозионную стойкость с минимальным окислением при более высоких температурах. Это обещает устранить проблемы с нагартованными кристаллическими покрытиями, которые откалываются или расслаиваются в ответ на нагрузку, о которых ранее заботились дорогие легирующие элементы.
Другая разработка аморфного сплава включает кристаллический материал, который при абразивном износе превращается в аморфный сплав с твердой фазой. Верхний слой толщиной от трех до пяти микрон обеспечивает уровень твердости более 1300 по Виккерсу. Испытания на износ показали, что этот материал превосходит более дорогие покрытия из карбида вольфрама.
В покрытиях для детонационных пистолетов, разработанных Union Carbide и признанных многими отраслевыми стандартами, используется детонационная волна для нагрева и ускорения порошкообразного материала до 2400 футов в секунду. В процессе прямой видимости каждый отдельный взрыв образует круг покрытия диаметром 1 дюйм и толщиной 2 мкм. Покрытия, таким образом, состоят из нескольких слоев плотно упакованных линзовидных частиц, прочно связанных с поверхностью.
Super D-Gun, следующее поколение Union Carbide, было разработано для увеличения скорости частиц. Новые покрытия (серия UCAR 2000), наносимые вместе с пистолетом, обеспечивают повышенную износостойкость, не влияя на усталостные характеристики. Система предназначена для чувствительных к усталости компонентов самолетов.
Материалы Содержание.
Дом ЭРК.
Полимерные покрытия
Полимерные покрытия, предназначенные для защиты от коррозии, обычно более прочные и наносятся более тяжелыми пленками, чем покрытия для внешнего вида. Требования к таким покрытиям гораздо более строгие: они должны хорошо прилипать к подложке, не должны легко скалываться или разрушаться под воздействием тепла, влаги, соли или химикатов.
Факторы окружающей среды также определяют технологию полимерных покрытий, заменяющих хромовые и кадмиевые покрытия. Отчасти это связано с растущим беспокойством по поводу тяжелых металлов. Кроме того, автопроизводителям теперь приходится бороться с кислотными дождями в дополнение к соляным брызгам, а полимеры превосходят хром и кадмий по стойкости к кислотным дождям.
Акриловые и алкидные краски широко используются для сельскохозяйственного оборудования и промышленных товаров, требующих хорошей защиты от коррозии при умеренных затратах. Алкидные смолы, в частности, играют важную роль в ремонтной окраске из-за их хорошей устойчивости к атмосферным воздействиям и простоты применения с недорогими малотоксичными растворителями. Алкидные краски также имеют относительно высокое содержание твердых веществ, что позволяет наносить хороший слой краски с минимальным количеством слоев.
Силиконовая модификация органических смол улучшает общую атмосферостойкость и долговечность. Из-за того, что алкиды широко используются при ремонтной окраске, компания Dow Corning выделила эти смолы при исследовании органических покрытий, модифицированных силиконом. По сравнению с органическими покрытиями в целом силиконы обладают большей термостойкостью, более длительным сроком службы, лучшей стойкостью к износу от солнечного света и влаги, а также большей биологической и химической инертностью.
Исследования привели к коммерческой доступности алкидов, модифицированных силиконом, на водной основе. Эти материалы обладают атмосферостойкостью, блеском, простотой нанесения и другими эксплуатационными характеристиками покрытий на основе растворителей, но содержат лишь небольшое количество летучих органических соединений. Составы на основе растворителя доказали свою долговечность и стойкость к выцветанию на резервуарах для хранения химикатов и природного газа, надпалубных конструкциях нефтяных танкеров и других наружных конструкциях, подвергающихся воздействию промышленных и морских условий.
Для оптимальной устойчивости к атмосферным воздействиям содержание силикона должно составлять от 25 до 30%. Производительность составы на водной основе практически идентичны составам покрытий на основе растворителей.
Для покрытий, требующих более высокой термостойкости, силиконовые смолы могут использоваться отдельно для окраски транспортных средств или их можно смешивать с различными органическими смолами. Эти покрытия используются на обогревателях, сушилках для белья и грилях для барбекю. Подобные составы используются в дымовых трубах, мусоросжигательных печах, котлах и реактивных двигателях. Характеристики составов, содержащих керамические фритты, приближаются к характеристикам керамических материалов.
Полиуретановые эмали характеризуются отличной ударной вязкостью, долговечностью и коррозионной стойкостью. Эти термореактивные материалы, доступные как в одно-, так и в двухкомпонентном исполнении, стоят дороже, чем алкидные и акриловые.
Химия уретана достаточно универсальна, чтобы обеспечить твердую, прочную, устойчивую к воздействию окружающей среды пленку, жесткое эластомерное покрытие или поверхность где-то между ними. Уретаны традиционно были доступны в виде покрытий на основе растворителей, содержащих от 25 до 45% твердых веществ, но заботы об окружающей среде побудили производителей также поставлять их в составах с высоким содержанием твердых веществ, 100% твердых веществ и на водной основе.
Толщина покрытия полиуретанов колеблется от примерно 2 мил для средних требований до целых 30 мил для применений, требующих ударопрочности и/или стойкости к истиранию, а также коррозионной стойкости. Типичное использование — конвейерное оборудование, обтекатели самолетов, буксиры, дорожно-строительная техника и детали мотоциклов. Абразивостойкие покрытия из уретанов наносят на вагоны-хопперы, футеровку применяют в пескоструйных камерах и пульпопроводах.
Эпоксидные покрытия имеют лучшую адгезию к металлическим подложкам, чем большинство других органических материалов. Эпоксидные смолы привлекательны с экономической точки зрения, поскольку они эффективны против коррозии в более тонких слоях, чем большинство других отделочных материалов. Их часто используют в качестве грунтовки под другие материалы, обладающие хорошими барьерными свойствами, но ограниченными адгезионными характеристиками.
Толщина покрытия может варьироваться от 1 мил для легкой защиты до целых 20 мил для работы с коррозионно-активными химическими веществами или абразивными материалами. Однако характеристики эпоксидных смол ограничены при большей толщине, поскольку они более хрупкие, чем другие органические материалы.
Нейлон 11 покрытия обеспечивают привлекательный внешний вид, а также защиту от химических веществ, истирания и ударов. Наносимые электростатическим распылением толщиной от 2,5 до 8 мил, нейлоновые покрытия используются на офисной и уличной мебели, больничных койках, деталях торговых автоматов и перилах зданий. Более тяжелые покрытия — до 50 мил — наносятся методом псевдоожиженного слоя и используются для защиты корзин посудомоечных машин, оборудования для пищевой промышленности, сельскохозяйственного и погрузочно-разгрузочного оборудования, а также промышленного оборудования, такого как трубы, фитинги и клапаны.
Фторуглероды более инертны к химическим веществам и растворителям, чем все другие полимеры. Наиболее эффективными барьерами среди фторуглеродов для различных коррозионных условий являются PFA, PTFE, ECTFE, FEP и PVDF.
Для ударных нагрузок рекомендуются покрытия PVDF и ECTFE в указанном порядке. ПТФЭ, ФЭП и ПФА также подходят, но они имеют большую склонность к ползучести под нагрузкой. Среди фторуглеродов для абразивных условий лучше всего подходит ПВДФ. Для высоких рабочих температур — например, сушильных шкафов и парового оборудования — рекомендуются PFA и PVDF. Эти материалы также используются в компонентах двигателей и сварочных аппаратах. ПВДФ также имеет самую высокую прочность на сжатие среди фторуглеродов. ПТФЭ имеет самую высокую допустимую рабочую температуру (600°F) среди фторуглеродов.
Покрытия на основе ПТФЭ используются для снижения износа в автомобильной промышленности США. Фторполимерные покрытия предотвращают заедание и истирание в дисковых тормозных системах при температурах выше 100°C. ПТФЭ также используется в качестве сухой смазки. Кроме того, ПТФЭ можно использовать в качестве покрытия автомобильных крепежных деталей, а в новом процессе ПТФЭ используется для предотвращения заклинивания пружин клапанов. В ударе FluoroPlate, разработанном компанией Orion Industries, смесь неорганических и органических частиц бомбардирует поверхность пружины, снимая внутренние напряжения и уменьшая поверхностные дефекты. Покрытие также помогает пружинам отталкивать масло.
Новый класс покрытия — сплав фторполимера и других смол — имеет другие характеристики вязкости, чем у более ранних органических материалов. Вязкость смол покрытия «класса застежки» резко снижается по мере увеличения сдвига пленки (как при нанесении методом погружения/отжима). Затем, когда вращающаяся корзина останавливается, вязкость почти мгновенно возвращается к исходному значению. Таким образом, при нанесении на процесс погружения/отжима покрытие цепляется за острые края, нити и точки.
Толщина пленки обычно находится в диапазоне от 0,5 до 0,7 мил, но составы могут быть отрегулированы для получения пленки от 0,3 до 0,4 мил для деталей с тонкой резьбой или другими сложными элементами. Эти чрезвычайно прочные покрытия не только обеспечивают более равномерный барьер для коррозионных веществ, но и основаны на полимерах, которые по своей природе стабильны в присутствии широкого спектра кислот, оснований и водных растворов.
> Комбинированные покрытия сочетают в себе преимущества анодирования или твердого покрытия с контролируемым введением полимеров с низким коэффициентом трения и/или сухих смазочных материалов. Покрытия становятся составной частью верхних слоев металлических подложек, обеспечивая повышенную твердость и другие свойства поверхности.
Эти покрытия, представленные серией запатентованных покрытий, разработанных General Magnaplate Corp., различны для каждого класса металлов. Например, покрытие компании Tufram для алюминия сочетает в себе твердость оксида алюминия и защиту фторуглеродного верхнего покрытия, что придает повышенную твердость, износостойкость и коррозионную стойкость, а также постоянную смазывающую способность.
В многоступенчатом процессе поверхность сначала превращается в оксид алюминия. Затем субмикронные частицы ПТФЭ вплавляются в пористую анодированную поверхность, образуя непрерывную пластиковую/керамическую поверхность, которая не отслаивается, не отслаивается и не расслаивается. Утверждается, что покрытие обладает большей стойкостью к истиранию, чем цементируемая сталь или пластина из твердого хрома.
Другим запатентованным покрытием, которое проникает сквозь ПТФЭ при прецизионном анодировании твердого покрытия, является Nimet Industries’ Nituff. Покрытие обеспечивает самоотверждающуюся, самосмазывающуюся поверхность с низким коэффициентом трения, высокой коррозионной стойкостью и диэлектрическими свойствами, превосходящими обычное анодирование твердым покрытием. Он широко используется в аэрокосмической, текстильной, пищевой, упаковочной и других отраслях промышленности, где он позволяет производителям извлекать выгоду из легкого веса и простоты обработки алюминия, а также долговечности, чистоты и сухого смазывания поверхности Nituff.
Другие запатентованные комбинированные покрытия были разработаны для стали, нержавеющей стали, меди, магния и титана, которые обеспечивают аналогичное улучшение поверхности. Также доступны покрытия, улучшающие определенные свойства, такие как смазывающая способность, коррозионная стойкость или износостойкость.
Другой вид покрытия, порошковое покрытие, сочетает в себе свойства как пластмасс, так и красок. Покрытия изготавливаются с использованием стандартного оборудования для производства пластмасс. Сначала их пропускают через экструдер для расплава, а затем измельчают. Однако при нанесении в качестве покрытия порошок превращается в пленку покрытия, точно подобную краске.
Эти покрытия были разработаны в ответ на необходимость сократить выбросы летучих органических соединений (ЛОС), которые увеличились за последние несколько лет. Излишки жидких красок содержат растворители, которые выбрасываются в атмосферу. Даже в системах восстановления некоторые летучие компоненты улетучиваются. Порошковые покрытия, с другой стороны, полностью пригодны для повторного использования. Излишки можно легко собрать и использовать повторно. Если небольшое количество становится слишком загрязненным для переработки, доступны безопасные методы утилизации.
Порошковые покрытия также перспективны в качестве замены прозрачных покрытий в автомобильной промышленности. Существующие краски на основе растворителей могут быть заменены прозрачным порошковым покрытием, которое отверждается примерно при той же температуре, что и обычные краски. Порошковые покрытия также могут заменить обожженную фарфоровую эмаль, используемую для деталей приборов. Крышки стиральных и сушильных машин теперь покрыты порошковой краской от The Glidden Co.
Однако приложения — это еще не все новшества. Материалы изменились. Большинство порошковых покрытий основано на основе эпоксидной или полиэфирной смолы. Акриловые материалы, однако, становятся все более важными, и другие возможные основы включают нейлон, винил и различные фторполимеры.
Были усовершенствованы два процесса нанесения покрытий. При электростатическом напылении, наиболее популярном методе, порошок заряжается и распыляется на электрически заземленные детали. Их запекание завершает излечение. Непроводящие части должны быть загрунтованы или нагреты, чтобы придать им большее электростатическое притяжение.
В процессе с псевдоожиженным слоем воздух проходит через пористую мембрану на дне резервуара и аэрирует порошок, так что он циркулирует в резервуаре. Затем часть нагревают и погружают в резервуар, чтобы порошок расплавился на поверхности. Этот процесс используется для толстопленочных защитных покрытий и подходит только для металлических деталей, которые могут сохранять тепло достаточно долго для нанесения покрытия.
В Глиддене и в других местах продолжается работа по снижению температуры отверждения порошковых покрытий. Хотя эти покрытия в настоящее время сопоставимы с жидкими красками, которые отверждаются при температуре от 300 до 400°F, исследователи надеются разработать покрытия, которые можно отверждать при более низких температурах для использования на пластиковых деталях.
Материалы Содержание.
Источники:
Copyright 1995, 1996 Журнал Machine Design
Публикация Пентона
Дом ЭРК.
Видение |
англ.-информ. |
Презентации |
Организация |
Что нового
Области основных компетенций |
Тематические исследования |
Часто задаваемые вопросы и советы
Обратная связь |
Интранет |
университеты |
Обучение и развитие карьеры |
Базы данных
Область технических технических отчетов
Вопросы? Электронная почта на Веб-мастер в Центре технических ресурсов
Патент США на процесс изготовления металлополимерного композита с облученным полимерным покрытием.

ОБЛАСТЬ ИЗОБРЕТЕНИЯ
Настоящее изобретение относится к способу изготовления металлополимерного композита, подходящего для изготовления корпусов контейнеров и торцевых панелей контейнеров для пищевых продуктов и напитков. Более конкретно, изобретение относится к металлополимерному композиту, включающему полимерное покрытие, имеющее повышенную стойкость к распушиванию и образованию ангельских волосков.
ПРЕДПОСЫЛКИ ИЗОБРЕТЕНИЯ
Металлический лист, покрытый термопластичной смолой с одной или обеих сторон, уже давно используется для изготовления корпусов и торцевых панелей контейнеров для пищевых продуктов и напитков. Покрытие наносится различными способами, включая валиковое покрытие, обратное валиковое покрытие, распыление, электроосаждение, порошковое покрытие и ламинирование. Покрытия наносятся на металлический лист для улучшения коррозионной стойкости, формуемости и внешнего вида.
Электронно-лучевое излучение используется в известном уровне техники для отверждения материала покрытия после его нанесения на подложку. «Отверждение» — это общее название процесса, при котором органическое покрытие, нанесенное на подложку, полимеризуется до или почти до максимально возможной степени, и, кроме того, при отверждении удаляется весь или почти весь растворитель, если он присутствует. Отверждение покрытия может включать полимеризацию мономеров или удлинение цепи (сшивание) олигомеров или полимеров или любое их сочетание. Средняя молекулярная масса полимерных цепей увеличивается, и любые растворители, которые могут присутствовать, в значительной степени удаляются. Электронно-лучевое отверждение можно определить как описанный выше процесс отверждения, вызванный облучением электронным пучком. Растворители часто не присутствуют в рецептурах, отверждаемых электронным лучом, и поэтому часто не удаляются в процессе отверждения. При электронно-лучевом отверждении электронный луч ионизирует определенные молекулы, которые инициируют свободнорадикальную реакцию в неотвержденном покрытии и вызывают сшивку полимера (увеличивая среднюю молекулярную массу полимера). Типичный пример отверждения электронным лучом содержится в патенте США No. № 4,452,374, выданный Hitchcock et al. В этом патенте полимерное покрытие отверждается путем «сшивания (полимера) с использованием обычных методов облучения электронным пучком высокой энергии». Многие другие примеры существуют в патентной литературе и опубликованных ссылках. Однако отверждение прекращают, когда достигается или приближается полная полимеризация. Это связано с тем, что добавленная энергия, будь то тепловая, электронно-лучевая или другая, начнет разрушать полимерные связи, укорачивать длину цепи, уменьшать среднюю молекулярную массу и ухудшать свойства покрытия, если приложение энергии продолжается после точки полной полимеризации. Такое ухудшение свойств может включать охрупчивание, потерю прочности, нарушение адгезии и/или пожелтение полимерного покрытия.
При отсутствии рядом реакционноспособных материалов для продолжения процесса полимеризации приложение дополнительной энергии заставляет полимеры просто подвергаться процессу разрыва, в котором цепи укорачиваются, а средняя молекулярная масса уменьшается.
Полимерные покрытия, наносимые в виде полностью полимеризованных материалов, не подвергаются этапу отверждения после нанесения на металлическую основу. При экструзионном покрытии полимер, который уже полностью полимеризовался, расплавляется и выдавливается на поверхность металла. Небольшой дополнительный нагрев может быть использован для обеспечения того, чтобы расплавленный полимер затекал в микроскопические поры в подложке, но дальнейшая полимеризация не происходит, и не применяется дополнительный нагрев или облучение для отверждения покрытия, удаления растворителей или дальнейшей полимеризации. молекулы покрытия. При порошковом покрытии полностью полимеризованные порошкообразные полимеры наносятся на подложку, а затем нагреваются, чтобы расплавить их в связную массу и вызвать адгезию к подложке. Однако, опять же, никакой дальнейшей полимеризации не происходит, и не применяется нагревание или облучение для отверждения покрытия, удаления растворителей или дальнейшей полимеризации молекул покрытия.
Процессы нанесения покрытий, наиболее часто используемые в настоящее время в коммерческих целях, требуют систем на основе растворителей, которые генерируют пары. Чтобы обеспечить более экологически приемлемый процесс нанесения покрытия, не требующий каких-либо растворителей, было предложено экструзионное нанесение термопластичных полимеров на металлические поверхности. Некоторые патенты предшествующего уровня техники, раскрывающие нанесение покрытия методом экструзии на металл, включают Smith et al. патент США. №5,407,702; Левендуски и др. патент США. №5919517; Хичок и др. патент США. № 4,452,374; и Шмид и др. патент США. №№ 5,942 285 и 6 153 264.
Лист из алюминиевого сплава с экструзионным покрытием подходит для некоторых целей. Однако высокая пластичность термопластичных полимеров приводит к проблемам, когда из листа с полимерным покрытием формируют торцевые панели для контейнеров для пищевых продуктов и напитков. Первая проблема, называемая «расплыванием» или «мембранированием», возникает, когда термопластичное покрытие отделяется от металла при открытии язычка или фиксатора. Виден тонкий лист отделившегося покрытия, либо частично закрывающий горлышко контейнера, либо торчащий из открытой панели. Вторая проблема называется «волосы ангела», при которой полимерное покрытие, вдавливаемое в линию надреза на концевой панели, образует тонкие нити, когда конец открывается, что создает нежелательный внешний вид. Тонкие нити покрытия могут свободно попадать в контейнер через отверстие или в рот потребителя. Ангельские волосы иногда также образуются на периферийных краях металлических дисковых заготовок с полимерным покрытием для корпусов банок и на верхних краях корпусов банок с полимерным покрытием.
Соответственно, по-прежнему остается потребность в металлическом листе с полимерным покрытием, обладающем повышенной устойчивостью к распушиванию и образованию ангельских волосков, когда лист с покрытием формуется в торцевые панели контейнера.
Основная цель настоящего изобретения состоит в том, чтобы предложить способ изготовления металлополимерного композита, включающего полимерное покрытие с расщепленными полимерными цепями, для повышения устойчивости к распушиванию и образованию ангельских волос.
Некоторые преимущества изобретения заключаются в том, что способ является недорогим, может осуществляться быстро и может работать без образования загрязняющих веществ.
Дополнительные цели и преимущества нашего изобретения станут очевидными для специалистов в данной области техники из следующего подробного описания некоторых особенно предпочтительных вариантов осуществления.
СУЩНОСТЬ ИЗОБРЕТЕНИЯ
В соответствии с настоящим изобретением предлагается способ изготовления металлополимерного композита, пригодного для формования корпусов контейнеров и торцевых панелей контейнеров для пищевых продуктов и напитков. Композит включает металлический лист и полимерное покрытие. Полимерное покрытие предпочтительно включает только один слой, но может включать 2 или более слоев.
Металлический лист может состоять из алюминиевого сплава, стали, стали с покрытием из алюминиевого сплава или стали с покрытием из алюминия. Лист из алюминиевого сплава является особенно предпочтительным.
Алюминиевые сплавы, подходящие для изготовления корпусов контейнеров, включают алюминиево-марганцевые сплавы серии АА3000 и алюминиево-магниевые сплавы серии АА5000. Алюминиевые сплавы, подходящие для изготовления торцевых панелей контейнеров, включают алюминиево-магниевые сплавы серий АА3000 или АА5000 и особенно сплавы АА5182 и АА5042.
Алюминиевые сплавы, пригодные для изготовления торцевых панелей контейнеров, такие как AA5182, изготавливаются в виде слитков, заготовок или плит методом литья. Перед обработкой слиток или заготовку подвергают гомогенизации при повышенной температуре. Затем заготовку из сплава подвергают горячей прокатке для получения листа промежуточной толщины. Например, материал может подвергаться горячей прокатке при входной температуре металла около 700-950°F для получения промежуточного продукта толщиной от около 0,130 дюйма до около 0,190 дюйма. Этот материал подвергается холодной прокатке для получения листа толщиной от 0,007 до 0,014 дюйма.или закалка h49.
Алюминиевые сплавы, такие как AA5042, поставляются в виде гомогенизированных слитков. За этой процедурой следует горячая прокатка до промежуточной толщины около 0,125 дюйма. Обычно продукт промежуточной толщины отжигают с последующей холодной прокаткой до конечной толщины примерно от 0,007 до 0,014 дюйма. Мы предпочитаем лист из алюминиевого сплава AA5042 в состоянии h3E72.
Лист из алюминиевого сплава обычно очищают щелочным очистителем поверхности для удаления остаточной смазки, прилипшей к поверхности, а затем промывают водой. Очистки можно избежать, если остаточное содержание смазки незначительно.
Затем на лист наносится конверсионное покрытие для обеспечения хорошей адгезии полимерного покрытия и повышения коррозионной стойкости. Подходят как хромсодержащие, так и бесхромовые конверсионные системы. Хромовое конверсионное покрытие обычно содержит хромат и фосфат. Некоторые конверсионные покрытия, не содержащие хрома, представляют собой растворы, содержащие ионы цирконата, титаната, молибдата, вольфрамата, ванадата и силиката, обычно в сочетании с фтористым водородом или другими фторидами. Лист с конверсионным покрытием можно промыть водой и затем высушить перед нанесением полимерного покрытия.
Полимерное покрытие, наносимое на металлический лист, выбирают из полиолефинов, полиолефинов, модифицированных ангидридом, эпоксидных смол и фенокси, и предпочтительно представляет собой полиолефин, модифицированный ангидридом. Подходящие полиолефины включают полипропилен, полиэтилен, сополимеры этилена и пропилена, сополимеры пропилена и 1-гексена и их смеси. Мы предпочитаем полипропилен и сополимеры, содержащие пропилен и примерно до 50 мольных процентов сомономера. Ангидридный модификатор может представлять собой по меньшей мере один из малеинового ангидрида, цитраконового ангидрида, итаконового ангидрида, глутаконового ангидрида, 2,3-диметилмалеинового ангидрида и их смесей. Полиолефин предпочтительно модифицируют примерно 0,5-20 мас.% малеинового ангидрида, более предпочтительно примерно 0,5-2 мас.%. Мы особенно предпочитаем полиолефины, модифицированные примерно 1 массовым процентом малеинового ангидрида. Полимер в покрытии предпочтительно полностью отвержден. Менее предпочтительно полимер может быть почти полностью отвержден.
Подходящая полипропиленовая сополимерная смола, модифицированная ангидридом, коммерчески продается компанией Basell North American Inc. под торговым обозначением Pro-fax PF-711. Полимер имеет плотность около 0,90 г/см 3 .
Необязательно полимерное полотно может содержать определенные добавки, включая красители, частицы пигмента, антикоррозионные вещества, антиоксиданты, усилители адгезии, светостабилизаторы, смазывающие вещества и их смеси.
Полимерное покрытие может быть нанесено на лист любым из нескольких способов, включая экструзионное покрытие, щелевое покрытие, валиковое покрытие, порошковое покрытие, ламинирование, распыление и электростатическое покрытие. Нанесение экструзионного покрытия является особенно предпочтительным. Полимерное покрытие предпочтительно экструдируют на металлический лист в виде одного слоя. Альтернативно, два или более слоев могут быть соэкструдированы на лист, включая связующий слой, примыкающий к металлическому листу, и один или более верхних слоев, нанесенных поверх связующего слоя. Примерами подходящих полимеров в связующем слое являются полиолефины, модифицированные ангидридом; сополимеры этилена/акриловой кислоты, такие как сополимеры, продаваемые The Dow Chemical Company под торговой маркой PRIMACOR; и клеевые композиции, продаваемые Rohm & Haas под торговой маркой MORPRIME. Верхний слой предпочтительно содержит полиолефин, более предпочтительно полипропилен, полиэтилен или сополимер пропилена и этилена. Другие подходящие полимеры в верхнем слое включают полиолефины, модифицированные ангидридом, эпоксидные смолы и фенокси.
Предпочтительно обе стороны листа из алюминиевого сплава наносят методом экструзии с полимерным покрытием, оставляя толщину около 0,04-0,5 мил (1-13 микрон). Полимерное покрытие, имеющее толщину около 0,4 мил (10 микрон), является особенно предпочтительным для внутренней части корпуса банки.
Покрытие предпочтительно представляет собой полностью полимеризованный материал, наносимый методом экструзии, так что отверждения не происходит. После этого нанесения полностью полимеризованная, полностью отвержденная подложка с покрытием подвергается облучению электронным лучом, чтобы улучшить устойчивость полимерного покрытия к образованию волосков ангела. Доза облучения составляет примерно 2-20 мегарад, а предпочтительно 5-15 мегарад. Такое облучение полностью полимеризованного материала вызывает разрыв цепи или обрыв цепи, при котором длина полимерной цепи уменьшается, а средний молекулярный вес уменьшается. Одним из эффектов этого разрыва цепи является увеличение хрупкости полимера. Хотя это увеличение хрупкости было бы отрицательным признаком для многих применений, таких как потребность в пластичности листа для банок для приложений вытягивания-перетягивания, охрупчивание неожиданно обеспечивает положительное свойство в уменьшении ангельских волосков и перьев при открывании крышек банок с надрезами. . Это воздействие электронного луча, вызывающее разрыв цепи, возможно, на самом деле может быть тем же уровнем облучения, который использовался для первоначального отверждения покрытия, но при нанесении после полного отверждения покрытия оно будет действовать на разрыв полимерных цепей, а не на инициирование в них поперечных связей.
При необходимости полимерное покрытие, нанесенное на подложку, может быть неотвержденным или только частично отвержденным. Такое покрытие должно быть сначала отверждено любым из нескольких обычных способов, таких как термическая обработка, облучение электронным пучком, ультрафиолетовое излучение или подобные процессы.
Облученные композиты формируются в концевые панели контейнеров или корпуса контейнеров для пищевых продуктов и напитков. Легкие открытые торцевые панели для напитков обычно формируются путем штамповки металлических заготовок между штамповочными штампами. Корпуса контейнеров для хранения напитков формируются с помощью процесса, в котором заготовки придают форму чашечкам, стенкам придают форму, делают дно выпуклым, сужают горловину, а затем отбортовывают. Облучение электронным пучком, вызывающее разрыв полимерной цепи, предпочтительно применяется после того, как покрытые и отвержденные композиты сформированы в торцевые панели или корпуса контейнеров. Необязательно, облучение может быть применено к покрытому полимером и отвержденному алюминиевому листу перед формированием торцов или корпусов банок.
КРАТКОЕ ОПИСАНИЕ ЧЕРТЕЖЕЙРИС. 1 представляет собой блок-схему особенно предпочтительного способа по настоящему изобретению.
ПОДРОБНОЕ ОПИСАНИЕ ПРЕДПОЧТИТЕЛЬНЫХ ВАРИАНТОВ ВОПЛОЩЕНИЯ
В соответствии с настоящим изобретением предлагается лист из алюминиевого сплава АА5182 в состоянии h29. Толщина листа составляет примерно 7-14 мил (0,18-0,36 мм) и предпочтительно составляет примерно 8,6 мил (0,22 мм).
Лист очищается щелочным средством для очистки поверхностей, если необходимо удалить остатки смазки с поверхности, и ополаскивается. Затем очищенный лист покрывают конверсионным покрытием водным раствором, содержащим ионы хромата и фосфата, снова промывают и сушат.
Устройство для нанесения покрытия методом экструзии типа, показанного в Smith et al. патент США. № 5407702 и Levendusky et al. патент США. US 5919517 предназначен для покрытия обеих сторон листа из алюминиевого сплава полимерным покрытием. Описание обоих патентов включено в настоящий документ посредством ссылки в той мере, в какой это соответствует нашему изобретению. Металлический лист нагревают до температуры примерно 177°С непосредственно перед нанесением покрытия.
Устройство для экструзионного нанесения покрытия наносит на алюминиевый лист покрытие из полностью полимеризованной полипропиленовой сополимерной смолы толщиной примерно 0,4 мил (10 микрон). Особенно предпочтительный сополимер полипропилена продается компанией Basell North America под торговым наименованием Pro-fax PF-711. Сополимерная смола имеет плотность около 0,90 г/см 3 .
Алюминий-полимерный композит охлаждают (желательно водой) и сушат.
Наконец, полимерное покрытие в композите облучают электронным лучом. Подходящий генератор электронного луча коммерчески доступен от Energy Sciences, Inc. of Wilmingon, Mass. под торговым наименованием ESI «ELECTROCURE» EB SYSTEM.
Образцы композитов облучали электронным пучком так, что их сополимерные покрытия Pro-fax PF-711 получили дозы 5, 10 и 15 мегарад. Все композиты до облучения демонстрировали растушевку и образование ангельских волос. Образование ангельских волос было уменьшено у образцов 5 и 10 мегарад и практически исчезло у образцов 15 мегарад. Растушевка была практически устранена при воздействии 10 мегарад. Для сравнения образцы одного и того же композита подвергались воздействию различных доз ультрафиолетового (УФ) излучения. УФ-излучение не уменьшало образование ангельских волосков или распушивание при экспозициях, практически применимых в производственных целях.
Композиты, изготовленные из листа алюминиевого сплава AA5182, покрытого тканью из полиэтилентерефталатной (ПЭТ) смолы, также подвергались воздействию 5, 10 и 15 мегарад доз электронного луча и различных доз УФ-излучения. Излучение электронного пучка не оказало положительного влияния на образование перьев или ангельских волосков в композитах алюминий-ПЭТ при испытанных уровнях воздействия. УФ-излучение требовало более длительного времени воздействия, чем это практически применимо для производственных целей.
Вышеизложенное описание нашего изобретения было сделано со ссылкой на некоторые особенно предпочтительные варианты осуществления. Специалистам в данной области техники будет понятно, что могут быть сделаны многочисленные изменения и модификации без отклонения от сущности и объема следующей формулы изобретения.