используемые средства и способы обработки
Фанера – самый популярный материал в строительной сфере. Это обусловлено её невысокой стоимостью. Это как плюс, так и минус. Чем ниже цена, тем больше она подвержена воздействию влаги. Возникает вопрос: чем пропитать фанеру для влагостойкости и как повысить её прочность?
Строение фанеры
Фанера – это строительный материал, состоящий из нескольких шпоновых слоёв, соединённых друг с другом. Насколько она влагоустойчива, зависит от состава клея, связывающего слои. Высокоустойчивым к влаге является материал, при производстве которого используются бакелитовый лак или клей. Они способны выдержать прямое воздействие воды. Благодаря этому материал можно использовать для изготовления лодки и прочих плавательных средств, не выполняя дополнительных обработок. Существует единственное «но» – слишком высокая цена.
Другие материалы, оптимально подходящие для строительных работ и изготовления мебели, при повышенной влажности начинают расслаиваться и гнить.
На видео: какая фанера лучше.
Способы обработки
Обработка фанеры и защита её от влаги может осуществляться несколькими способами. Вот некоторые из них (самые распространённые в обиходе):
- шпатлевание клеем ПВА;
- покрытие олифой;
- обработка нитрокрасками;
- приклеивание стеклоткани.
Далее подробнее рассмотрим, чем лучше обработать фанеру и как это сделать правильно.
ПВА
Защита фанеры от воздействия влаги и гниения с помощью шпаклёвочного состава ПВА имеет много преимуществ. Он надёжно защищает материал от множества негативных факторов. Приводим пошаговую инструкцию, как выполнить процесс защиты:
- Прежде чем обработать материал для повышения влагостойкости, его располагают параллельно полу и наносят слой клея ПВА.
- Дают время хорошо впитаться первоначальному слою, после чего покрывают ещё одним слоем ПВА.
- Выполняют процесс до тех пор, пока пятна от клея не начнут проявляться на изнаночной стороне листа.
- Плита переворачивается, и процесс пропитки повторяется.
После того как работы завершены, плиту укладывают на ровную поверхность и дают ей просохнуть в естественных условиях. К минусам данного процесса относят довольно большие сроки обработки. Фанеру от влаги придётся защищать 3–4 дня.
Аналогичную пропитку можно выполнить, используя эпоксидную смолу. Но это довольно дорогое удовольствие и при этом не безвредно для здоровья человека. Листы, обработанные эпоксидной смолой, используют только для наружных работ.
Олифа
Олифа – это простейший способ пропитки фанерной плиты от воды. Реализуют обработку следующим способом:
- Предварительно раствор (масло для фанеры) следует разогреть до уровня температуры 600С, за счёт этого повышается его проникающая способность.
- Затем горизонтально расположенный лист пропитываем олифой с помощью кисточки.
- После завершения процесса пропитки одной стороны, приступаем к другой.
- Обязательно тщательно промазываем торцы фанеры.
- Когда первый слой нанесён, то начинаем принудительно её просушивать с помощью утюга или фена.
- После завершения сушки приступаем к повторному процессу нанесения олифы и принудительной просушки.
Количество слоёв может быть различно. Прекращают обработку олифой только тогда, когда раствор перестаёт впитываться материалом (полного достижения водоотталкивающего эффекта).
После такой обработки на фанеру можно нанести краску или лак. Часто возникает вопрос о том, чем покрыть фанеру на полу. Этот способ идеально подходит для этой цели.
Стеклоткань
- Шлифованную плиту красят лаком.
- Дав подсохнуть нанесённому слою лака порядка двух часов, на поверхность фанеры клеят стекловолокно.
- Повторно наносят слой лака на торцы плиты и оставляют до полного высыхания.
- Завершается обработка нанесением ещё одного слоя лака и сушкой пропитанной фанеры в естественных условиях.
Совет! При отсутствии стеклоткани можно использовать обычную марлю. После того как её покрасили лаком, она надёжно будет защищать материал.
Нитрокраска
Ещё один способ обработки фанеры от влаги – это нитрокраски. Особенно это актуально, когда материал непосредственно будет в контакте с водой, к примеру, при ремонте лодки или обустройстве сырого помещения.
Приведём инструкцию реализации работ своими руками:
- Первоначально необходимо отшлифовать поверхность и покрыть олифой.
- Дать полностью просохнуть слою олифы и нанести жидкую краску в качестве грунтования.
- На защищённые грунтовкой листы нанести слой нитрокраски.
- Покрываем поверхность фанеры тканью, которую параллельно необходимо пропитывать нитрорастворителями.
- После завершения сушки, вторично обрабатывают разведённой нитрокраской. Полученный влагостойкий материал подходит даже для изготовления лодки.
Важно! Последний слой нитрокраски делается довольно тонким. В противном случае, понижается степень прочности.
Подготовка поверхности
- Осуществляется просушка плиты. Она должна быть таковой, чтобы защита фанеры производилась качественно.
- Далее следует шлифовка поверхности. Прежде чем пропитывать фанеру для влагостойкости, необходимо хорошо её зачистить. Для этого следует использовать мелкозернистую наждачную бумагу. Для удобства работы её крепят на деревянный брусок, и таким устройством шлифуется поверхность.
- Особенное внимание уделяется торцам листа. Удаляются все сколы и заусенцы. Если сколы довольно большие, можно использовать шпаклёвочный материал по дереву.
Зачистку можно производить с помощью шлифовальной машины. Отшлифованное вручную не имеет такое качество поверхности, как с помощью специальных приспособлений.
Желательно провести акклиматизацию фанеры, как долго будет проходить этот процесс, зависит от показателей температуры. Если материал предназначен для работы в помещении, то для сушки достаточно одних суток, на улице при температуре 80С и ниже — 3 дня.
Важно! Плиты некоторое время пропитываются, а затем их необходимо сложить в стопку на ровную поверхность для полной просушки.
Теперь вам понятно, чем обработать фанеру, чтобы повысить ее влагоустойчивость и гидрофобные качества в домашних условиях, и необязательно покупать продукцию дорогих марок. Можно воспользоваться довольно эффективными способами обработки, представленными выше.
Какую пропитку лучше купить для фанеры (2 видео)
Пропитка для древесины (30 фото)
Чем пропитать фанеру для влагостойкости
На рынке строительных товаров одно из главных мест занимает фанера. Этот материал изготовлен путем склеивания и дальнейшего прессования нескольких пластин древесного шпона. Продукт ценится за универсальность в использовании и доступность в цене.
Однако при своих достоинствах у изделия есть одно уязвимое место: низкая влагостойкость. Чтобы устранить этот недостаток и защитить материал от влаги, совершают такую манипуляцию, как гидроизоляция фанеры. Поэтому всем, кто занят строительством или ремонтом дома рано или поздно придется решить задачу: чем можно пропитать фанеру для придания ей влагостойкости.

Чем отличается водостойкая фанера от обычной
Обычная фанера, как и натуральный шпон, деформируется и расслаивается под действием влаги. Повысить водостойкость материала снаружи можно покрытием фанеры определенными составами. А изнутри — применением специальных клеевых смесей для соединения пластин шпона, из которых изготовлен лист. Именно состав этих веществ и создает влагостойкость. Обработанное изделие приобретает свойства прочной и долговечной плиты, способной выдерживать непосредственное воздействие воды.
По уровню влагостойкости и составу клея фанера подразделяется на марки:
Марка | Описание и назначение |
ФБА | Для производства используется альбумино-казеиновый клей. Материал экологически безопасен. Влагостойкость низкая, поэтому используется только для внутренних работ. |
ФК | Изготавливается на основе карбамидного клея с добавками фенола. Отличается небольшим уровнем влагостойкости. Используется для внутренних работ без возможности использования в помещениях с повышенной влажностью (ванных комнатах, лоджиях). |
ФСФ | Материал создается с использованием фенолформальдегидных смол, поэтому токсичен. Изделие ценится прочностью, высоким уровнем влагостойкости. Запрещается применять в жилых помещениях. |
ФБК | В составе связывающего клея присутствует влагостойкий бакелитовый лак. Отличается высокой степенью влагостойкости. Не боится грибка. Не горит. Стоит очень дорого. Используется для наружных работ. Применяется в строительстве в качестве материала для опалубки. |
Изучив особенности фанерных панелей, выбрать материал, соответствующий определенным потребностям, не составит труда.
Способы обработки
Сделать фанеру влагостойкой можно самостоятельно. Для этого существует несколько способов. Важно помнить, что процесс обработки требует подготовки панели:
- Влажная плита высушивается.
- Поверхность шлифуется с помощью мелкозернистой наждачной бумаги. Для этой цели используют шлифовальную машинку.
- Добросовестно удаляются заусенцы с торцов листа.
- При необходимости шпаклюются все сколы.
- Изделие очищается от пыли сухой ветошью.
Часто фанеру используют как черновой пол, применяя ее в качестве основания для дорогих напольных покрытий. В этом случае пластину покрывают акриловой грунтовкой. Акрил защищает панель от плесени и грибков. После этого фанеру для пола пропитывают влагостойкими лаками или покрывают красками.
Обработка фанеры осуществляется с помощью таких пропитывающих средств, как:
- клей ПВА,
- олифа,
- стеклоткань,
- воск,
- нитрокраски.
Каждый вариант рассмотрим отдельно.
Клей ПВА
Надежно защитить пластину от влаги и грибка может клей ПВА. Лист покрывают слоем клея, тщательно промазывая всю поверхность. Для такой манипуляции изделие кладут горизонтально. Следующий слой наносят после намокания всей поверхности. Клей накладывают так долго, пока он не проступит на обратной стороне. Изнаночную сторону обрабатывают аналогично. После просушки панель готова к использованию. У такого способа пропитки есть большой недостаток: он занимает много времени (около 4 дней).
Клей ПВА можно заменить эпоксидной смолой, в которую предварительно добавляют отвердитель и ацетон. Операция нанесения смолы аналогична операции нанесения клея ПВА. Следует помнить, что смола токсична. Фанеру, обработанную этим способом, запрещается устанавливать внутри помещений.
Олифа
Вещество, созданное на основе льняного и других растительных масел, прошедших термообработку, называется олифой. Химические добавки, внесенные в ее состав, способствуют быстрому высыханию средства. Олифа применяется для создания стойких защитных покрытий, а также в качестве основы для разных красок. На приусадебных участках ее применяют для розжига костров.
Льняное масло — натуральный продукт, получаемый способом механического отжима льняного семени. Чистое масло иногда используется для покрытия вещей, находящихся в сухих помещениях: декоративной мебели, предметов быта. Но обработка дерева льняным маслом не приводит к созданию прочного водостойкого покрытия. К тому же масло на фанере долго сохнет. Такое покрытие ценят за экологичность и антисептические свойства, а также — за способность сохранить древесину от растрескивания.
Спасти фанеру от влаги — значит покрыть ее олифой, разогретой до t 50-60 °С. Отшлифованную поверхность, торцы и углы изделия тщательно промазывают. После подсушки первого слоя наносят второй. Чтобы ускорить высыхание, рекомендуется использовать фен. Олифу наносят до тех пор, пока она не перестанет впитываться. Далее пропитанный лист переворачивают и операцию повторяют. Этот вариант отделки подходит для панелей, предназначенных для пола. Высохший материал, по желанию, покрывают лаком или краской.
Стеклоткань
Стеклоткань — материал, который тоже может защитить фанеру от влаги. Подготовленную для обработки пластину покрывают водостойким лаком, в котором отсутствуют эпоксидные и полиэфирные смолы. После просушивания (около 2-х часов) на плиту накладывают кусок стеклоткани. Затем сверху наносят завершающий слой лака. При необходимости стеклоткань заменяется марлей. Покрытая лаком, она не будет отличаться от стеклоткани.
Воск
Небольшие по площади поверхности можно обработать смесью воска, скипидара и натуральной олифы в соотношении 2:1:1. Воск растапливают на водяной бане. В него добавляют олифу, скипидар. Смесь остужают и наносят на фанеру. После высыхания поверхность тщательно полируют.
Нитрокраска
Фанеру, использование которой предполагает контакт с водой, обрабатывают нитроэмалевыми и нитроглифталевыми красками. На изделие, покрытое олифой и уже высушенное, наносят грунтовку в виде краски. Далее ее покрывают нитрокраской. Ткань, пропитанную нитрорастворителем, укладывают на лист и окончательно красят. Покрасить фанеру последний раз нужно тонким слоем, иначе изделие потеряет свою прочность.
Последующая обработка фанеры для поддержания влагозащиты
Несмотря на все степени защиты со временем поверхность пропитанной фанеры стирается, растрескивается. Слои шпона, плохо соединенные клеем, со временем могут развалиться. Особенно уязвимы места крепления, а также торцы пластины. В результате снижается ее влагостойкость. Гидроизоляции таких мест уделяют особое внимание в момент монтажа изделия. Размещать фанеру, даже обработанную специальными средствами, нужно в местах, защищенных от влаги. Стены строений, выступы крыш, навесы не допустят прямого попадания воды на панель.
При появлении первых признаков нарушения покрытия немедленно принимают меры для его восстановления. Нельзя просто закрасить трещины, так как под слоем краски гниение продолжится. Поврежденные участки зачищают наждачной бумагой. Потом заново наносят защитный слой. Подобной реставрацией можно надолго сохранить влагостойкое покрытие в рабочем состоянии.
Вовсе не обязательно покупать дорогие марки влагостойкой фанеры. Можно все сделать своими руками. Но, прежде чем решиться на операцию пропитки, следует проанализировать все способы и выбрать для себя наиболее подходящий. В случае затруднения с выбором всегда можно проконсультироваться со специалистами.
пропитка для защиты от влаги
Стандартные мебельные плиты длительного воздействия влаги не выдерживают. Материал начинает расслаиваться и коробиться. Но и качество недорогой строительной ФСФ-фанеры не всегда на высоте. Фасады, отделанные такими плитами, со временем темнеют, местами вспучиваются. Расскажем, чем обработать фанеру, чтобы она стала влагостойкой и ее можно было эксплуатировать в уличных условиях.
Виды фанеры
Влагостойкость этого материала зависит от состава и способа производства. Фанерой называют древесные плиты, при изготовлении которых используются склеенный шпон (тонкие слои древесины). В производстве мебельной фанеры применяется менее влагостойкая береза. Строительные плиты (именно их чаще используют в быту), обычно состоят из 3-5 слоев лиственного, соснового и елевого шпона. Подобные виды древесины более стойки к гниению.
Но все же влагостойкость фанеры зависит в первую очередь от вида используемого клея. Его состав обязательно указывается в маркировке:
- ФБА: казеиновые клеи, легко разбухающие в воде;
- ФК: смесь карбамида и водостойких формальдегидных смол; материалы с подобной пропиткой могут использоваться лишь внутри помещений;
- ФСФ: фенолформальдегиды, клеи повышенной водостойкости; составы относятся к химически агрессивным и для внутренней отделки домов и квартир не рекомендуются;
- ФБ, БС и БВ: бакелитовые клеи и лаки: дополнительной обработки фанеры от влаги и гниения в этом случае не требуется; пропитанное ими дерево приобретает высочайшую прочность и изностостойкость; материалы имеют специальное назначение и используются в машино-, авиастроении и даже космической промышленности.
Дополнительно защитить ФБА, ФСФ- и ФК-плиты от гниения можно несколькими способами. Каждый из них имеет как достоинства, так и недостатки.
Какую пропитку лучше использовать?
Сделать фанеру влагостойкой в домашних условиях поможет покрытие специальными составами:
- клеем ПВА или эпоксидной смолой;
- олифой;
- влагоизолирующей грунтовкой с содержанием антигрибкового антисептика;
- стеклотканью;
- нитросоставами.
Какой из методов более эффективен? Расскажем о каждом из них подробно.
Клей ПВА
Подобная пропитка для фанеры используется лишь при условии, что материал будет эксплуатироваться в помещениях. Ведь клей ПВА не способен длительно выдерживать воздействие влаги. Основными его плюсами является дешевизна и невысокая токсичность. Такая отделка идеально подойдет при укладке фанеры, к примеру, под линолеум или ламинат.
Эпоксидная смола способна обеспечить неплохую защиту даже от влаги на улице. В жилых помещениях из-за высокой токсичности ее использовать нежелательно. Несмотря на то, что стоимость пропитки достаточно высока, она боится воздействия солнечных лучей.
Раствор ПВА или эпоксидки наносится с обеих сторон листа и торцов. Каждый слой клея необходимо тщательно просушить. Обработка производится многократно, пока дерево не перестанет впитывать раствор.
Олифа
Защитить фанеру от влаги помогут специальные пленкообразующие составы на основе растительных масел. Для пропитки лучше использовать натуральную, к примеру, льняную олифу. Для увеличения впитывания ее следует предварительно разогреть градусов до 50. Сделать это можно на водяной бане. Учтите, что, хотя подобный способ пропитки весьма эффективен, сушить фанеру придется достаточно долго. Ускорить процесс поможет строительный фен.
Слоев олифы должно быть несколько – столько, сколько дерево сможет в себя вобрать. Понадобится как минимум 2-3 нанесения. Если материал будет эксплуатироваться во влажном помещении или на улице, количество слоев необходимо увеличить до 3-4.
При любом способе обработки фанеры от влаги не забывайте тщательно промазывать торцы. Получить максимальную защиту можно с помощью одновременной пропитки олифой и нитролаком. Усилить влагостойкость поможет предварительное покрытие антигрибковой грунтовкой.
Нитролак
Перед его нанесением поверхность предварительно обрабатывают олифой в 1-2 слоя. Для получения максимальной защиты потребуется не менее 5-6 тонких слоев лака. В отличие от олифы, сохнет он достаточно быстро.
Чтобы фанера хорошо пропиталась, слишком густой состав использовать не стоит. Лак необходимо развести пожиже. Обрабатывать им дерево лучше с помощью пульверизатора или валика.
Стеклоткань
Основой для покрытия будет являться та же олифа. Ею необходимо тщательно, в несколько слоев обработать поверхность.
Далее наносим слой лака. Укладывать стеклоткань начинаем после того, как он чуть загустеет. Промоченный скипидаром (он увеличит схватывание с поверхностью) материал следует хорошо распрямить и максимально плотно прижать к фанере.
Для увеличения влагостойкости покрыть фанеру можно дополнительным слоем масляной краски. Подобная тройная защита будет максимально эффективной.
Подготовка поверхности
Предназначенное для обработки дерево требуется предварительно просушить, очистить от жира, грязи, пыли. Занесенную с улицы фанеру следует выдержать в помещении не менее суток в горизонтальном положении. Для лучшей вентиляции листы располагают на расстоянии друг от друга. Сделать это можно с помощью деревянных брусков, которые прокладывают между панелями.
Если фанера ранее была окрашена, слой краски придется полностью удалить. Далее поверхность обрабатывают наждачной бумагой, чтобы снять тонкий глянцевый слой. Шероховатая поверхность будет лучше впитывать клей или олифу. Использовать слишком крупную наждачную бумагу не стоит – она оставит заусеницы.
Выбор способа пропитки зависит от места монтажа фанеры и способа эксплуатации. При использовании в жилых помещениях достаточно 2-3-кратной пропитки клеем ПВА. Если же материал планируется использовать в жестких уличных условиях, лучше обеспечить максимальную степень защиты, обработать его вначале олифой, а затем покрыть лаком и стеклотканью.
Фанера – это строительные плиты небольшой толщины, состоящие из нескольких склеенных листов древесины. Большинство сортов многослойной фанерной продукции имеют чувствительность к воде, объяснимую низкой влагостойкостью клеев.
Использование таких плит в строительстве проблематично из-за склонности к набуханию, появлению плесени, гниению, разрушению.
Улучшить эксплуатационные качества позволяет обработка фанеры защитными препаратами, создающими на поверхности водонепроницаемый слой.

Содержание статьи
Особенности структуры
Основу процесса производства фанеры составляет склеивание тонких древесных листов между собой таким образом, чтобы природные волокна были направлены строго вдоль или поперек длинной стороне. Количество слоев чаще всего бывает нечетным, минимум составляет 3 листа.
Склеивание проводят различными средствами, из которых эффективную водостойкость обеспечивают определенные бакелитовые составы: лаки и спирторастворимые клеи. Применение водорастворимых модификаций бакелитов, всех остальных видов клеев приводит к тому, что продукция не выдерживает действия паров воды. Низкая водостойкость особенно заметна при эксплуатации фанеры на улице. В связи с этим ею необходимо проводить обработку материала защитными составами.
Средства для увеличения влагостойкости
Кардинально изменить потребительские свойства позволяет нанесение пропитки для фанеры от влаги и гниения. Существует несколько видов веществ, способных после обработки создать на поверхности защитную пленку и повысить влагостойкость фанеры. Обычные краски с задачей не справятся, потому что через время они образуют микротрещины, в которые сможет просачиваться вода.
Наибольшей популярностью при обработке фанеры пользуются следующие эффективные средства:
- поливинилацетатные клеи;
- вязкие концентраты олифы;
- нитроцеллюлозные эмали;
- стеклотканые материалы.
Композиции могут значительно повысить водостойкость не только фанеры, но и ДВП-продукции, создав на поверхности непроницаемое покрытие. Чем обрабатывать фанеру в конкретных домашних условиях – каждый мастер решает самостоятельно, учитывая финансовые возможности и наличие навыков работы.
ПВА
Наносить ПВА можно дома, расположив лист на опорах параллельно полу. Средство распределяют по поверхности вручную, валиком или кисточкой, не забывая при этом хорошо промазывать края и торцы листов. Следующий этап повышения влагостойкости требует терпения, нужно дождаться, пока слой полностью впитается и высохнет. Только после этого проводят повторную обработку.
Обратите внимание! Пропитывание повторяют несколько раз до тех пор, пока не начнут проступать пятна на обратной стороне фанеры.
После полного высыхания последнего слоя лист переворачивают, делают то же самое с другой стороны. Вся процедура обработки в целом может занять до 4 дней при условии невысокой влажности в помещении. В холодную погоду при плохом отоплении пропитать фанеру для достижения хорошего результата очень сложно.
Эпоксидные составы и олифа
Подобным образом можно проводить обработку водоотталкивающими эпоксидными составами, но следует учесть их токсичность и более высокую стоимость. Для обеспечения эффективной защиты от действия влаги наружных конструкций можно затратить средства на приобретение эпоксидных смол и ими пропитать фанеру.
Гораздо дешевле стоит олифа, которую наносят слегка разогретой в аналогичной последовательности. Масло для фанеры, представляющее собой концентрат олифы, тщательно распределяют на всей площади. Затем прогревают слой промышленным феном. Некоторые мастера используют для ускорения застывания утюг, но такой способ высушивания не легок в исполнении, требует навыков.
Обратите внимание! Особенно тщательно надо обрабатывать края листов, так как через них влага легко проникает внутрь.
Количество слоев олифы в разных случаях отличается, его можно определить опытным путем, капнув на верхнюю часть листа водой и понаблюдав за ее поведением. Если капля совсем не впитывается, пропитывать фанеру для повышения влагостойкости больше не нужно.
Нитроцеллюлозные лаки
Сильное водозащитное действие дает обработка нитроцеллюлозным лаком. Для увеличения адгезии сначала нужно выполнить шлифовку листов, затем покрыть их слоем масла. Низкосортную продукцию следует внимательно осмотреть, при наличии заметных неровностей, возможно, понадобится провести циклевку, покрыть верхнюю плоскость морилкой, способной создать нужный декоративный эффект.
Обычно мастеров удовлетворяет качественная шлифовка фанеры, проведенная наждачными материалами или специальной машинкой для циклевки.
На поверхности после полного застывания распределяют тонкий слой нитрокраски, который будет выполнять функции грунтовки. Эмаль перед нанесением распылителем желательно разбавить растворителем, предназначенным для этих целей. Разбавленным раствором нитрокраски легче хорошо пропитать фанеру, быстрее наступает его полное высыхание. В целом такой процесс повышения влагостойкости займет гораздо меньше времени, чем при использовании всех других способов обработки фанеры.
Стеклоткань
Часто для улучшения прочность и влагостойкости листы защищают стеклотканью, которая является эффективным армирующим полотном. На шлифованной фанере распределяют слой лака, затем после высыхания, которое обычно продолжается около 2 часов, к поверхности прикладывают слой стеклоткани. Волокна, содержащие нити силикатов стекла, хорошо фиксируют следующий слой лака, формируют влагостойкую пленку.
Для улучшения внешнего вида на фанеру распыляют последнюю порцию краски, формируя таким способом финишное покрытие. В результате получается достойное в эстетическом отношении изделие, не требующее последующей полировки. Продукция может с успехом применяться во влажных условиях, подвергаться обработке лобзиком, любыми другими режущими инструментами.
Для усиления влагостойкости в процессе монтажа плит на торцах можно закрепить накладки из пластика или металлических сплавов, способных предотвратить попадание воды в материал.
Правила проведения работ
Эффективно пропитать фанеру своими руками несложно, соблюдая определенные правила. Следует помнить об обязательности предварительной очистки материала, на котором не должно оставаться следов пыли, грязи, влаги, краски и лаков.
Для работы нужно подготовить кисточки или распылитель, защитную одежду. Если предстоит наносить состав на основе органических растворителей (нитроэмаль, эпоксиды), нужно обязательно надеть респиратор. Вдыхание токсичных паров опасно для человека, допускать этого не следует.
Руки нужно защитить перчатками даже в случае, если мастеру не очень удобно в них работать. Контакт с реагентами может вызывать обычное раздражение или аллергические реакции.
Хорошо пропитать фанеру, повысить ее влагостойкость можно, учитывая условия будущей эксплуатации, правильно выбрав средство, аккуратно выполнив работу.
Фанера представляет собой недорогой и популярный материал, который используют для внутренних и наружных строительных и отделочных работ. Ее производят путем многослойного склеивания лущеного шпона, снятого с дерева тонкой стружкой. Если не считать влияния клеевых составов, фанеру вполне можно отнести к экологически чистой продукции.
Этот материал плохо переносит воду. При длительном применении во влажных условиях фанера деформируется и расслаивается. Промышленность занимается выпуском водостойких сортов, однако такая продукция стоит дорого и поступает оптом на мебельные и строительные производства. В продаже найти материалы с особыми свойствами нелегко, но есть много способов защитить фанеру самостоятельно. О них пойдет речь в нашей статье.
Виды пропитки
В строительных торговых точках можно встретить отличные современные составы, применяемые для пропитки фанеры с целью приобретения ею водостойких характеристик. К ним относится ряд изделий.
- Олифа. Имеет маслянистый состав, который глубоко проникает в поверхность фанеры и образует водоотталкивающую пленку.
- Поливинилацетатный состав. ПВА может присутствовать в клее, красках или шпаклевке. Пропитка подходит в качестве защитного слоя для подготовки фанерных листов под ламинат или линолеум. Для наружной защиты поливинилацетат не годится, так как длительное время справляться с влагой ему не по силам.
- Нитрокраска. Она не только делает поверхность фанеры устойчивой к воде, но и декорирует ее.
- Нитролак. Имеет хорошие водоотталкивающие характеристики. Его наносят в несколько слоев после покрытия фанеры олифой.
- Воск. Если площадь фанеры небольшая, ее можно обработать воском. После полировки она приобретает привлекательный, безукоризненно гладкий вид.
Подготовка поверхности
Прежде чем приступать к работе над фанерой по приданию ей влагостойкости, нужно знать, где она будет использоваться. Подготавливая листы к применению во влажных помещениях, обработку следует производить с двух сторон. Сама фанера должна быть марки ФСФ, бюджетные ФБА или ФК в данном случае не подойдут.
Если для защитного слоя выбираются лакокрасочные материалы, им необходимо иметь водоотталкивающие свойства. Даже в этом случае они не защищают фанеру самостоятельно, а лишь используются как последние, финишные слои.
Иначе, когда краска со временем будет отслаиваться от поверхности, фанера начнет принимать влагу и деформироваться.
Материал, попавший в дом с улицы, до начала работ должен сутки находиться в тепле. Для улучшения вентиляции листы устанавливают вертикально, им следует отстоять друг от друга на определенном расстоянии.
Перед нанесением защитного слоя тонкий глянец снимают наждачной бумагой. Шероховатость поверхности позволит составам лучше впитываться. Затем следует абразивной шкуркой привести в гладкое состояние торцы листа. Если на фанере присутствуют глубокие дефекты, их убирают с помощью шпаклевки. Далее поверхности тщательно протирают от пыли, возникшей в результате зачистки.
Как пропитать своими руками?
Мы уже убедились, что сделать фанеру устойчивой к воде в домашних условиях можно разными способами, и все они индивидуальны. Поэтому рассмотрим рабочий процесс с каждой пропиткой отдельно.
Олифа
Это наиболее доступный вид пропитки, к тому же являющийся хорошим антисептиком. Обработка листа фанеры олифой происходит в определенной последовательности.
- Для работы подготавливают тару под олифу и кисти, можно валик.
- Олифу хорошо размешивают и отправляют в емкость, затем разогревают на водяной бане до температуры 50-60 градусов Цельсия.
- Составом тщательно обрабатывают все поверхности. Особое усердие требуют листовые торцы.
- Далее осуществляется принудительная просушка с помощью строительного фена или другим удобным способом.
- Только после высыхания покрытия можно приступать к нанесению следующего слоя. Их должно быть столько, сколько принимает фанера (до полного впитывания). После каждой обработки следует очередная просушка.
Обработанные олифой листы в дальнейшем будут защищены от грибка и плесени.
Они могут стать базой для следующих декоративных покрытий – лаков и красок, содержащих олифу.
Поливинилацетатный состав (ПВА)
Поливинилацетат применяют в создании клея ПВА, акриловых и водоэмульсионных красок, состав которых представляет собой так называемое масло в воде. Красящие изделия приобретаются в торговой сети в виде 2-х компонентов – краска пастообразной структуры и пластификатор. Оба продукта смешиваются непосредственно перед началом работ. Клей ПВА приобретается однородной структурой, без добавок. Для покрытия фанеры подходят все виды поливинилацетатных составов.
Пропитка ПВА гарантирует защиту листов от расслаивания и гниения. Таким способом подготавливают материал для настила полов. Поверхность промазывают с каждой стороны, добиваясь полного впитывания. Тщательно обрабатываются и торцы.
Между каждым слоем требуется самостоятельная просушка. Весь рабочий процесс довольно длительный и может занять целую неделю.
На основе поливинилацетата используется также шпаклевка, по структуре напоминающая густую сметану. Обрабатывается фанера следующим образом:
- лист слой за слоем покрывается шпаклевкой до тех пор, пока с обратной стороны на поверхности не проступят пятна;
- далее хорошо грунтуют другую сторону фанеры;
- сушат лист в вертикальном положении в течение 3-х дней;
- далее материал обрабатывают антисептиком;
- затем наносят несколько слоев акрилового лака.
Нитрокраска
Нитроглифталевые и нитроэмалевые краски отлично защищают фанеру от контакта с водой. Но, как мы уже упоминали, красящие составы наносятся на предварительно обработанную поверхность. Процесс покрытия состоит из нескольких пунктов.
- После выравнивания поверхности наждачной бумагой ее со всех сторон, включая торцы, покрывают олифой. Перед покраской изделие должно хорошо просохнуть.
- Краску разводят, превращая в жидкую грунтовку, и еще раз обрабатывают ею просохший лист. После высыхания фанера будет готова под покраску.
- Далее наносится как можно тоньше 2-3 слоя краски с промежуточным просыханием. Работать можно кистью, подойдет также валик, но более равномерное покрытие получается с помощью пульверизатора.
Для более тщательной защиты можно поверхность проклеить марлей, пропитанной нитрорастворителями.
Для этого ткань укладывают, нанеся начальный слой краски, остальные покрасочные работы производятся не только для защиты покрытия, но и для улучшения его внешнего вида. В заключение готовый фанерный лист можно покрыть еще и лаком.
Нитролак
Краска со временем начинает трескаться и приходить в негодность, поэтому фанеру обрабатывают лаком. Это происходит посредством ряда шагов.
- Поверхность шлифуется и прокрашивается олифой в несколько этапов.
- После просушки начинают работать с лаком. Для более качественного пропитывания его разводят до жидкой консистенции и наносят в 5-6 тонких слоев на поверхность. Каждому покрытию дают возможность просохнуть. Процесс не займет много времени, так как лак сохнет быстро. Работать можно с помощью валика или пульверизатора.
Стеклоткань
Для применения фанеры в условиях улицы водостойкость защитного слоя можно повысить с помощью стекловолокна. Для этого производят несколько действий.
- Для подготовительной обработки, как обычно, прибегают к олифе. Кроме поверхностей, следует не забывать о торцах, которые являются слабым звеном всего защитного слоя. Если он нарушается, с торцов начинает впитываться влага, что приводит к постепенному расслаиванию шпоночных пластов.
- После просыхания олифы фанеру покрывают слоем лака. Следует выбирать изделия без содержания эпоксидной смолы.
- Стеклоткань для улучшения схватывания с поверхностью промачивают скипидаром.
- На слегка загустевший лак аккуратно выкладывают материал и плотно прижимают его к поверхности, выравнивая со всех сторон.
- Когда изделие высохнет, его можно покрыть несколькими слоями лака или водостойкой краски.
Эпизоды просушивания во время всего рабочего процесса должны проходить естественным путем, что займет в общей сложности 2-3 недели.
Воск
Чтобы покрыть поверхность фанеры, понадобится пропитка, состоящая их 2-х частей: воска и смеси олифы со скипидаром (по одной части каждого ингредиента). Предварительно воск расплавляют на водяной бане и соединяют с остальными частями смеси. Остывший состав наносят на поверхность. После высыхания аккуратно полируют.
Фанера – удобный и прочный материал, применяемый для строительных работ. Из нее можно выполнять различные элементы мебели. Влагостойкий слой, произведенный в домашних условиях, продлит долговечность фанерных листов и расширит сферу их применения.
Как сделать влагозащитное покрытие своими руками смотрите далее.
пропитка от влаги и гниения своими руками
Плиты из клееного шпона имеют большую популярность и используются для обшивки внутри и снаружи дома. Но при выполнении работ на участках с повышенной влажностью требуется применять специальный материал. Ввиду дороговизны и отсутствия такой продукции в магазинах, можно обработать фанеру для влагостойкости самостоятельно. Существует несколько методов, обеспечивающих достижение нужного результата.
Чем отличается водостойкая фанера от обычной?
Все разновидности материала изготавливаются на основе шпона из лиственных и хвойных пород деревьев. Чтобы соединить слои между собой, используются специальные клеевые растворы, которые наносятся в соответствии с определенной технологией. Именно это придает продукции водоотталкивающие свойства.
Разновидности фанеры:
- К обычным вариантам относятся изделия с маркировкой «ФБА», производимые на основе альбумино-казеинового клея. Такие панели отличаются предельной экологичностью, но не способны выдерживать повышенную влажность, что ограничивает область применения материала.
- Более устойчивая разновидность – ФК, для склеивания которой используется карбамидный клей с фенольными добавками. Такая вариация характеризуется низким уровнем водостойкости, поэтому подходит для укладки внутри помещений и не рекомендуется для монтажа в ванной, на балконе и открытых террасах. Даже присутствие специальных добавок не способно предотвратить коробление при воздействии серьезной влажности и прямом попадании воды.
- Хорошей влагостойкостью обладают плиты ФСФ. Это объясняется использованием при производстве фенолформальдегидного клея. Хотя такой материал способен противостоять пагубному влиянию, он имеет низкие показатели безопасности из-за токсичности.
- Полностью водонепроницаемой является ФБС. Это бакелитовая фанера, которая выдерживает даже воздействие морской воды. Технология изготовления заключается в полном или частичном погружении плиты в склеивающий и защитный состав.

ФСФ не рекомендована для монтажа внутри дома и встречается не во всех строительных магазинах, а ФБС стоит очень дорого, поэтому при использовании обычных вариантов можно повысить параметры устойчивости к пагубному воздействию самостоятельно.
На заметку! За счет наличия внешней облицовки ламинированные плиты имеют улучшенные свойства.
Как сделать фанеру влагостойкой своими руками
Для придания нужных характеристик используются различные методы, предполагающие применение специальных пропиток.
Покраска нитроэмалью
Это эффективный способ, обеспечивающий получение поверхности, устойчивой даже к прямому контакту с водой.
Схема процесса:
- Проводится шлифовка всех сторон листа абразивом с крупной и средней структурой.
- Поверхность полностью покрывается олифой, особенно хорошо требуется пропитать торцы.
- Краска разводится до жидкого состояния и укладывается равномерно на высохшую плиту. Состав играет роль грунтовки, создавая надежную основу для будущих работ. Красить рекомендуется в 2–3 слоя. Учитывается, что последнее покрытие должно иметь наименьшую толщину.
- В качестве дополнительной защиты применяется стеклоткань, пропитанная нитрорастворителями. Полотно наклеивается на всю площадь панели, но только после первого слоя краски.

Технология допускает использование аналогичных составов, имеющих пометку о влагостойкости.
Пропитка олифой
Этот раствор относится к обычным и наиболее доступным. В домашних условиях масло используется в качестве антисептика и увеличивает долговечность изделия. Обработка осуществляется по следующему алгоритму:
- Подготавливается подходящая емкость, валик и кисточки. Олифа хорошо размешивается и переливается в тару. Состав разогревается до температуры 60 градусов. Требуется соблюдать осторожность, ведь материал является огнеопасным.
- Готовым раствором нужно обработать все фанерные листы. Важно тщательно пропитывать каждый участок, особое внимание уделяется краям.
- Выполняется принудительная просушка поверхности. Для этого целесообразно использовать строительный фен с регулировкой мощности.
- Олифа подогревается, повторяется весь цикл обработки. Смесь нужно наносить до тех пор, пока она не перестанет впитываться.

Получившееся покрытие не только обладает устойчивостью к сырости, но и уничтожает плесень и грибок.
Внимание! Основа подходит для лакирования и окрашивания составами, которые содержат олифу, использованную для обработки.
Покрытие клеем ПВА
Такую пропитку для фанеры рекомендуется применять при необходимости дополнительной защиты от гниения, что особенно актуально для половых покрытий.
Поливинилацетатным составом обрабатывают плиты похожим образом: нанесение осуществляется последовательно с обеих сторон, пока поверхность не перестанет впитывать раствор, торцам уделяется особое внимание.
Основное отличие от предыдущего метода в том, что нельзя выполнять принудительную просушку. К тому же весь комплекс работ потребует не менее 7 дней, поскольку пленка образуется довольно долго.

Защита фанеры от влаги на улице
Использование плит из клееного шпона снаружи требует более серьезного подхода и других методов.
Стекловолокно
Ткань применяется и при работах внутри помещений, в качестве альтернативы можно выбрать марлю.
Технология процесса:
- Поверхности предварительно шлифуются, обязательно удаляется образовавшаяся взвесь и пыль.
- Подготовленные основания нужно обработать определенной разновидностью лака. Раствор не должен содержать полиэфирные или эпоксидные смолы.
- После того как смесь подсохнет в течение 2 часов, наклеивается стекловолокно. Материал распределяется по поверхности так, чтобы исключить неровности.
- Осуществляется укладка еще двух слоев лака.

Любой принудительный прогрев поверхностей, способствующий ускорению высыхания раствора, недопустим.
Эпоксидная смола
Прежде чем покрыть фанеру от влаги таким составом, необходимо подобрать правильный материал. Для уличных работ нельзя использовать изделия с маркировкой «ФК», поэтому оптимальным вариантом является ФСФ. Смесь разводится веществом, которое указывает изготовитель, консистенция не должна быть слишком жидкой. Раствором покрывается вся поверхность, хорошо промазываются торцы. Количество слоев варьируется в зависимости от ситуации, но желательно наносить не менее двух.
Эпоксидная смола имеет существенный недостаток – дороговизна, что делает нецелесообразным ее применение для бытовых мероприятий.

Особенности обработки плит перед укладкой на пол
Для получения качественного результата при монтаже листов на горизонтальное основание необходимо учитывать некоторые нюансы нанесения защитного покрытия:
- Панели не должны иметь высокую остаточную влажность, обязательна акклиматизация материала не менее 24 часов. Требуется обеспечить вентиляцию листов, поэтому их размещают горизонтально. Для этого между панелями прокладываются деревянные бруски.
- Качественная шлифовка уменьшает расход состава и способствует образованию надежной пленки. Торцы также не должны иметь заусенец.
- Пропитка выполняется наиболее подходящим материалом согласно инструкции. Особое внимание уделяется стороне, которая будет обращена к основанию.

Учитывается, что обработка осуществляется после раскроя продукции на нужные по размеру детали.
Заключение
Чтобы защитить фанеру от пагубного воздействия влаги, необходимо использовать пропитывающие составы. Смеси выбираются в зависимости от места монтажа плит. Для достижения качественного результата обязательно соблюдается технология обработки.
Сегодня, фанера марки ФК, остаётся наиболее востребованным строительным материалом. Спектр её использования весьма широкий. Но, со временем ФК начинает темнеть, расслаиваться и загнивать. Влагостойкость листов фанеры можно увеличить путём обработки специальными пропитками. Статья раскрывает способы защиты фанеры от влаги и плесени и отвечает на вопрос, чем пропитать фанеру для влагостойкости.

Лист фанеры, обработанный водоотталкивающей пропиткой
Несколько слов о строении фанеры
Прежде чем говорить о способах защиты продукта, необходимо понимать, с чем мы имеем дело. Строительный материал, о котором идёт речь, состоящий из нескольких соединённых между собой шпоновых слоёв – это и есть фанера.
Чаще всего её используют в строительной отрасли. Она противостоит негативному воздействию влаги за счёт использования при производстве бакелитового лака и/или клея, связывающего её слоя.
Из этого материала изготавливаются лодки и другие плав/средства без специальной и дополнительной обработки. Хотя, такой материал, стоит весьма дорого.
Материалы и способы обработки фанеры от влаги
Наиболее распространёнными и доступными способами обработки считаются:
- Использование в качестве защиты от воздействия влаги клея ПВА.
- Нанесение олифы.
- Обработка продукта красками на нитро/основе.
- Использование стеклоткани.
Теперь, более подробно о каждом из способов, с учётом специфики защитного продукта
Обработка листов фанеры клеем ПВА

Материалы, необходимые для обработки
Защита продукта с использованием шпаклёвочного состава ПВА имеет ряд преимуществ. Процесс защиты состоит в последовательных действиях:
- Для обработки клеем ПВА материал располагают параллельно полу и наносят первый слой.
- Выждав время необходимое для пропитки, плиту покрывают вторым слоем клея.
- Процедура выполняется до тех пор, пока с обратной стороны, не начнут появляться пятна продукта обработки: клея.
- Следует перевернуть обрабатываемый лист и выполнить аналогичные действия с обратной стороны.
Таким образом, осуществляется качественная пропитка. Но этот способ имеет ряд недостатков. Это время проведения защитных мероприятий. На просушку уйдёт от трёх до четырёх суток, так как специальные инструменты и технологии для ускорения процесса не используются, а высыхание происходит в естественных условиях.
Обработка листов фанеры олифой
Обработка олифой считается наиболее доступным и простым решением, которая выполняется в определённой последовательности:
На заметку!
Для быстрого проникновение защитного состава в обрабатываемую поверхность необходимо предварительно разогреть олифу до t 50-600 С. В разогретом состоянии олифа обладает лучшей проникающей способностью.
- Используя кисточку, наносится защитный слой.
- Пропитав одну сторону, выполняется аналогичная процедура второй стороны.
Важно!
Необходимо уделить особое внимание торцам фанеры и тщательно пропитать их олифой.

Процесс нанесения водоотталкивающего состава
Пропитав обе стороны материала олифой можно приступать к сушке. В данном случае допускается принудительный вариант с использованием промышленного фена.
Способы защиты фанеры на улице
В обработке фанеры, находящейся с внешней стороны здания, можно использовать эпоксидную смолу или стеклоткань.
Эпоксидная смола
Изначально необходимо понимать, что эпоксидная смола отрицательно влияет на здоровье человека. Поэтому, обработка этим материалом внутри помещения, запрещена. К тому же стоимость пропитки высокая. Нанесение на материал защитного вещества выполняется по аналогии работы с клеем ПВА.
Защита фанеры стеклотканью
В данной технологии рекомендуется работа с влагостойким лаками, которые в своем составе не содержат эпоксидных или полиэфирных смол.

Строительство каркасного дома из фанерных листов
Технология защиты предусматривает обработку материала из трёх этапов:
- Шлифованная плита покрывается лаком.
- Затем материал сохнет. На это уходит примерно 2 часа. Выполняется повторная процедура нанесения лака на торцы. Даётся определённое время для полного высыхания обрабатываемой поверхности. Сушка происходит естественным путём.
- Второй слой (контрольный) лака предполагает аналогичные действия как на первоначальном этапе.
Чем обработать фанеру от влаги если отсутствует стеклоткань. Заменителем материала может стать обычная марля. После её покрытия лаком она будет надёжно защищать обработанную поверхность от влаги.
Какую пропитку лучше купить для фанеры
Вопрос одновременно простой, и в то же время сложный. Современный рынок предлагает массу вариантов. Самостоятельно разобраться и определиться с пропиткой сложно. Для этого лучше всего проконсультироваться со специалистами и/или посмотреть видеоролики на эту тематику. Как, например, этот материал:
Чем пропитать фанеру для пола и как лучше защитить фанеру от появления плесени
Среди многообразия защитных средств пропитки для пола, можно выделить наиболее распространённые, и уже знакомые нам:
- Олифу.
- Лаки.
- Краски.
- Стеклоткани.
Существует одно негласное правило, которое существенно повышает шансы на защиту листов от влаги и плесени:
- Это зачистка поверхности.
- И грунтование краёв фанеры.
В дальнейшем нанесение слоёв и технология обработки поверхности выполняется поэтапно, как описано выше.
О технике безопасности при проведении работ
Многие забывают и/или пренебрегают элементарными нормами страховки, работая без соблюдения мер собственной безопасности, зря. Часть продуктов, используемых для обработки листов и защиты от влаги, являются токсичными. Оказывают отрицательное влияние на здоровье человека.
Поэтому, работая, необходимо использовать средства индивидуальной защиты, к которым относятся: перчатки, очки и респиратор. Особенно актуально стоит вопрос использования средств защиты при обработке листов фанеры монтируемой с внешней стороны помещения. Ведь в этом случае допускается применение эпоксидной смолы.
В заключение
Чем обработать фанеру и как сделать поверхность влагостойкой, какие материалы использовать, решать вам. Предоставленная информация носит лишь ознакомительный и рекомендательный характер.
Китай Пропитанная меламином бумага
Пропитанная меламином бумага, используйте высококачественную печатную декоративную бумагу, пропитанную меламиновой смолой, а затем ламинированную на все виды древесных плит. Он играет очень хороший декоративный эффект на поверхности панелей, а также делает поверхность устойчивой к высоким температурам, износостойким и против загрязнений.
В настоящее время пропитка обычно принимает двойное насыщение.Декорирующую бумагу сначала пропитывают обычной меламиновой смолой для получения основного слоя, а затем используют высококачественную меламиновую смолу для второй пропитки. Меламиновую смолу в этих двухкратных пропитках можно регулировать в соответствии с требованиями, чтобы обеспечить конечное качество пропитанной меламином бумаги, и сделать производство экономичным. Пропитка предъявляет строгие требования к печатной декоративной бумаге и меламиновой смоле. Смола после модуляции должна приобретать гибкость, которая может предотвращать образование хрупких трещин на поверхности.В фактическом производстве к меламиновой смоле также необходимо добавлять различные добавки.
Чтобы гарантировать качество пропитанной меламином бумаги, необходимо использовать высококачественную декоративную бумагу. Декоративная бумага не имеет волокна α-целлюлозы, хорошо справляется с выцветанием и устойчива к высокой температуре 180 ° C и хорошей непрозрачности. В норме граммаж декоративной бумаги должен составлять 70-90 г / tole, с допуском ± 2 г / ㎡, влажность 2,5-4,2%, значение рН 6,5-7,5. Если значение pH слишком низкое, оно может помяться во время пропитки.Чтобы избежать разрыва во время пропитки, длина продольного мокрого разрыва составляет не менее 450 м, а бокового 300 м. Чтобы получить хорошую скорость пропитки, у декоративной бумаги должен быть очень высокий абсорбент с быстрым проникновением. Требования к высоте всасывания воды: вертикальные 25-35 мм / мин, горизонтальные 22-30 мм / мин. Гладкость декоративной бумаги должна быть умеренной, слишком низкая может повлиять на эффект ламинирования на поверхности, а слишком высокая снизит способность пропитывать смолу.
Модуляционная смола— это в основном MF и UF, а также различные добавки.Отверждающая добавка играет роль катализатора для ускорения времени отверждения во время ламинирования. Смачивающая добавка предназначена для уменьшения поверхностного натяжения смолы и повышения способности проникновения на декоративную бумагу для подтверждения однородности пропитки. Разделительная добавка используется для предотвращения пропитки бумаги из стальной пластины во время ламинирования. Вспенивающая добавка используется для предотвращения образования пузырьков в смоляной ванне, которые могут повлиять на равномерность пропитки. Растворителем является вода или этанол, разбавленный для корректировки вязкости для получения хорошей проницаемости на декоративной бумаге.Используя специальную технологию клея, чтобы сделать меламиноформальдегидную смолу и карбамидоформальдегидную смолу, а затем добавить модификатор и хранилище, наконец, добавить отвердитель, смачивающую добавку, разделительную добавку, пенообразующую добавку и другие добавки, впрыскивать в ванну со смолой. После двухкратной пропитки декоративную бумагу необходимо высушить, охладить и нарезать до определенных размеров. Размер должен быть примерно на 10-30 мм больше, чем у панелей по ширине и длине. В процессе пропитки мы должны следовать строгим требованиям технологического процесса, проверять образцы каждые 30 минут, гарантировать содержание смолы 130-150%, летучие вещества содержание 6-7%, степень предварительного отверждения ≦ 65%.С одобрения готовые бумажные листы, пропитанные меламином, могут быть упакованы в полиэтиленовую пленку. Около 200 листов на тюк, 10 тюков на каждый поддон. Чтобы обеспечить качественное ламинирование, пропитанную меламином бумагу следует хранить в хорошем состоянии. Относительная влажность на складе составляет 60 ± 5%, поэтому бумага не впитывает и не выделяет влагу. Температура должна быть 20-25 ℃. Высокая температура и высокая влажность делают пропитанные листы бумаги мягкими и липкими. Но пропитанную бумагу легко сломать, когда температура слишком низкая.Срок годности пропитанной бумаги составляет около 3 месяцев, если они хранятся хорошо. Во избежание липкости из-за поглощения влаги, пожалуйста, упакуйте и плотно закройте после открытия.
Содержание смолы (твердая смола по отношению к массе смолы) составляет 130-150%. Низкое содержание смолы приводит к низкой прочности бумаги, и ее легко димексировать. Надлежащее содержание меламина хорошо для ламинирования в производстве и качестве. Когда содержание смолы слишком высокое, его легко взломать. Содержание летучих веществ (при 160 ℃ сушки в течение 10 минут) составляло 6-7%.
Ключевые слова: Китай, пропитанная меламином бумага, Меламиновая бумага оптом, Поставщики бумаги, Производители пропитанной меламином бумаги, поставщики меламиновой бумаги,листов меламиновой бумаги,
меламиновая доска,
меламиновая бумага,
, пропитанная бумажная фольга,
Фанера | Изделия из дерева
Фанера изготавливается путем склеивания тонких листов шпона. Толщина отдельного листа составляет 0,2 — 3,2 мм. Листы составлены так, что направления зерен наложенных друг на друга листов обычно перпендикулярны друг другу. В березовой фанерной плите обычно бывает нечетное количество листов (не менее трех), поэтому направление зернистости поверхностных листов всегда одинаково. В листах фанеры хвойных пород число также может быть четным. При склеивании обычно используется атмосферостойкий фенольный клей.С точки зрения цвета, он значительно темнее, чем шпон.
По своим основным свойствам фанера сравнима с древесиной. Он также имеет следующие преимущества благодаря способу изготовления:- прочность, хорошая в обеспечении жесткости для конструкций
- плотный и ударопрочный
- многоцелевой
Некоторые фанерные изделия классифицируются по классу эмиссии поверхностных материалов M1. Классификация материалов включает в себя предельные значения для выбросов строительных материалов, предназначенных для интерьеров, а также их классификацию.Класс M1 содержит материалы, проверенные на выбросы, выбросы примесей которых соответствуют самым строгим требованиям.
Стандартные толщины фанерных плит. Максимальная толщина изготовления составляет 50 мм. | ||||||||||
---|---|---|---|---|---|---|---|---|---|---|
Вид фанеры | Номинальная толщина мм | |||||||||
Березовая и хвойная фанера | 4 | 6.5 | 9 | 12 | 15 | 18 | 21 | 24 | 27 | 30 |
Фанера смешанная | — | 6,5 | 9 | 12 | 15 | 18 | 21 | 24 | 27 | 30 |
ОСНОВНЫЕ ПЛЮСЫ
Основную фанеру можно разделить на три основные категории: березовая фанера (плотность ок.680 кг / м3), смешанной фанеры (плотность ок. 620 кг / м3) и хвойных фанер (плотность 460-520 / м3).
Березовая фанера используется в областях применения, требующих высокой прочности или высокого качества, таких как специальные полы и требовательные внутренние облицовки.
Фанера смешанная — это универсальная фанера общего назначения. Они используются, например, в качестве базовых плит и бетонных форм для продуктов по ходу производства и специальной фанеры. Поскольку поверхность из смешанной фанеры всегда березовая, они относятся к тем же классам качества, что и березовая фанера.Смешанные фанеры являются:
- Combi — две фанеры из березы на обеих поверхностях, внутренние фанеры чередуются из березы и хвойной древесины
- Зеркальное отображение комбинированных — шпон березовый, чередующийся внутренний шпон хвойный и березовый
- Двухслойный шпон березы, внутренний шпон хвойного дерева
Хвойные фанеры особенно используются в строительстве, например, в кровельных конструкциях и внутренней облицовке. В основном они сделаны из ели.
КЛАССЫ КАЧЕСТВА PLYWOOD
Выбор класса качества фанеры из березовой фанеры в зависимости от применения (в скобках — другой обычно используемый класс качества) представлен в таблице ниже.
Фанера из березовой фанеры | |
---|---|
A (E) | безупречное специальное качество (доступно только в ограниченном объеме) |
B (I) | лакированная или вощеная поверхность |
S (II) | окрашиваемых поверхностей |
BB (III) | нормального качества, например под покрытиями, самое распространенное качество в конструкциях |
WG (IV) | для менее требовательных приложений, качество, которое невозможно отремонтировать |
Выбор класса качества фанеры хвойных пород в соответствии с применением показан в таблице ниже.
Хвойные фанеры | |
---|---|
E | безупречное качество, только сосновая поверхность |
I | почти безупречное качество, только сосновая поверхность |
II | нисходящего качества с неповрежденной поверхностью |
III | безнадежное качество для строительства |
IV | безнадежное качество для строительства (фоновое качество поверхности) |
ИЗДЕЛИЯ ИЗ НЕИЗВЕСТНОГО ПОТОКА, ИЗГОТОВЛЕННЫЕ ИЗ ОСНОВНОГО ПИЩЕВА,
Примеры следующих продуктов из основной фанеры, предназначенных для строительства:
- 9 м настенная доска
- 18 мм круглая шпунтованная доска с пазом
- 15 мм доска с шипами и желобками на длинных сторонах в качестве кровельной конструкции
Стена доски (размер платы +1200 х 2750 мм, номинальная толщина 9 мм) не шпунтовую и предназначена в качестве опорной пластины, чтобы увеличить прочность и жесткость посадки на внутренних стенках, а в так называемом двойном покрытии стена где другой материал внутренней облицовки используется в качестве внутренней облицовки поверх фанеры.Размеры платы подходят для наиболее распространенных расстояний между колоннами — 400 и 600 мм.
Подпольная доска (размер доски 2400 x 1200 мм, установленный на шпунтах и канавках, номинальная толщина 18 мм) имеет круглые выступы и канавки и предназначена в качестве несущей конструкционной доски для полов, которые опираются на подиум. Его толщина и размеры подходят для расстояний между 400 и 600 мм.
Доска основания крыши (размер доски 2700 x 1200 мм, номинальная толщина 15 мм) имеет специальную конструкцию, имеет выступы и канавки на длинных сторонах и особенно предназначена в качестве несущей конструкции для войлочных и листовых кровель, когда расстояние между опорами крыши составляет 900 мм.По сравнению с традиционным шпунтованным шпунтованием, фанерная обшивка может обеспечить значительную экономию общего рабочего времени и ровную и конструктивно жесткую конструкцию. Доска также может быть использована в качестве несущей конструкции пола. Доски предназначены главным образом для защиты от влаги во время строительства.
Относительно других непокрытых нижестоящих продуктов, изготовленных из основной фанеры, рифленой и полужесткой и рифленой внутренней доски (размер доски 2500 x 1210 или 610 мм, толщина 7.5 и 10 мм) также следует упомянуть. Это предназначено для облицовки и полупанелирования внутренних стен и потолков и используется в качестве внутренних облицовочных досок. Внутренние доски изготовлены из хвойной фанеры с еловой поверхностью шпона, а их видимая поверхность имеет продольные бороздки шириной 75 мм с W-образными канавками. Длинные бока полухлотные и рифленые.
СПЕЦИАЛЬНЫЕ ПЛЮСЫ
Специальная фанера — это, в основном, основная фанера, изготовленная для определенной цели в стандартных размерах и покрытая по-разному, в зависимости от применения.Покрытие может улучшить износостойкость, ударопрочность, атмосферную и химическую стойкость фанеры, а также ее фрикционные свойства. Фанеры с покрытием обычно защищены краями краской с краями. Защита краев, осуществляемая на заводе, предназначена для защиты от влаги во время хранения, и ее всегда следует переделывать, если доска размещается в месте, где требуется защита от влаги.
ПРИМЕРЫ ЛИСТОВ С ПОКРЫТИЕМ
Пленочная фанера или формовочная фанера являются одними из самых известных и наиболее часто используемых видов фанеры с покрытием.Для основной плиты используются березовая, смешанная и хвойная фанера, которая обычно покрыта с обеих сторон гладкой и прочной фенольной пленкой, цвет которой обычно темно-коричневый. Этот вид фанеры используется в бетонных формах, транспортных средствах и в качестве внутренней облицовочной доски в сельскохозяйственных зданиях.
Толщина доски варьируется от 6,5 до 30 мм. Стандартная ширина составляет 1200, 1220, 1500 и 1525 мм, а длина варьируется от 1200 до 3660 мм. В дополнение к вышеупомянутой коричневой пленке, специальные цвета также доступны.Однако они не рекомендуются для бетонных форм.
Фанера, покрытая грунтовочной краской, — это доска, предназначенная для использования при облицовке фасадов, для которой требуется покраска, кузовные работы, дорожные знаки, рекламные щиты и т. Д. В качестве основной доски используется березовая и смешанная фанера, покрытая с обеих сторон феноловой основой. грунтовочная бумага (светло-коричневая), а фоновая поверхность может быть альтернативно покрыта фенольной пленкой. Доски также доступны в готовом грунтованном состоянии.
Толщина доски варьируется от 6.От 5 до 30 мм. Стандартная ширина составляет 1200, 1250, 1500 и 1525 мм, а длина варьируется от 2400 до 3660 мм. Доски могут быть окрашены обычными красками для наружных работ (грунтовка + 2 поверхностных слоя) или специальными красками (2 краски на эпоксидной основе и 1 полиуретановая краска на поверхности). Края досок защищены окраской как на поверхностях. Поверхность фанеры, которая была окрашена, не страдает от волосяных трещин, которые обычно постепенно образуются на окрашиваемой поверхности и поверхности шпона фанеры без покрытия.
Фанера обработанная огнезащитным составом
Фанеру можно обработать антипиреном, поэтому ее огнестойкость увеличивается. Поверхности обрабатываются на заводе. Обработанная огнезащитным составом фанера подходит для структурных применений, поскольку обработка не влияет на технические свойства фанеры.
ДРУГИЕ СПЕЦИАЛЬНЫЕ ПЛЮСЫ
Другие специальные фанерные изделия для производства или переработки включают
- строительные леса — покрыты фенольной пленкой, на которой напечатан противоскользящий рисунок или другой так называемый проволочный рисунок Балконная доска
- — покрыта, чтобы противостоять погоде и солнечному свету.
ИСПОЛЬЗОВАНИЕ PLYWOOD КАК ЧАСТЬ СТРУКТУРЫ РАМКИ
- Стеновая доска
- в двухслойных стенах — укрепляет конструкцию стены
- каркас крыши — укрепляет конструкцию крыши
- подпольная доска — укрепляет горизонтальную конструкцию
ВНУТРЕННЯЯ ПОДКЛАДКА
Примеры внутренней облицовки
- Подкладка
- полустеночные панели
- потолочная облицовка
Фанера для внутренней облицовки:
- вся основная фанера (класс качества выбирается на основе обработки поверхности, в основном классы E, I и II)
- нижестоящих фанерных изделий, предназначенных для внутренней облицовки
Вопросы, которые необходимо учитывать при внутренней облицовке:
- С точки зрения противопожарной безопасности, фанера особенно подходит для внутренней облицовки домов (для зданий класса пожарной безопасности P3).В большинстве случаев его также можно использовать для внутренней отделки жилых, офисных и общественных зданий и т. Д.
- В сухих внутренних помещениях динамика влажности фанеры незначительна. Желательно делать стыки между досками как открытые стыки (1-3 мм). При необходимости швы могут быть покрыты планками.
При установке настенных панелей рекомендуемая толщина и расстояние между опорами:
- 6,5-9 мм, при расстоянии не более 300 мм
- 9-12 мм, при расстоянии не более 600 мм
В потолочной облицовке рекомендуемое расстояние между крепежными опорами не более 400 мм.
Доски крепятся гвоздями или шурупами, длина которых в два с половиной раза превышает толщину доски.
ЗАКАЗ
При заказе фанерных плит необходимо указывать следующую информацию:
- использовать
- толщина как номинальная толщина (мм)
- размер доски с измерением поверхности шпона в направлении зерна всегда упоминается первым (мм х мм)
- тип фанеры (например, комби)
- качеств обеих поверхностей, видимая поверхность всегда упоминается первой / е.грамм. S / WG = II / IV)
Также можно заказать фанеру по индивидуальному заказу, перфорированную, с дополнительной или специальной механической обработкой и т. Д.
ХРАНЕНИЕ
Во время транспортировки и хранения доски защищены от сырости, грязи, контакта с землей, солнечного света, вмятин и царапин. Доски хранятся на плоской основе лицевой стороной вниз. При необходимости опорная древесина используется с интервалом 0,5 метра. Следует избегать хранения досок в вертикальном положении. Любая стальная лента вокруг кучи досок должна быть удалена, если фанера должна храниться во влажных условиях.Куча досок покрыта защитным листом. Условия хранения должны быть аналогичны условиям, в которых в конечном итоге будут использоваться доски. Перед установкой фанеру необходимо проветрить в течение 3-8 дней в условиях, близких к тем, в которых она в конечном итоге будет использоваться.
РАБОТА И ОБРАБОТКА
Влагостойкость фанеры 1 мм / 1 м фанеры необходимо учитывать при ее установке.
Пиление
Например, настольная или переносная циркулярная пила подходит для распиловки досок.Небольшие пильные работы также можно выполнять с помощью обычной ручной пилы. Контурная распиловка может быть выполнена лобзиком. Доска, распиленная в соответствии с направлением движения лезвия, установлена таким образом, чтобы на задней поверхности доски, которая остается скрытой, происходило изнашивание поверхностного шпона, вызванное распиливанием (особенно распиливанием по зерну шпона). Например, при использовании переносной циркулярной пилы (вращающейся пилы) целесообразно размещать видимую переднюю поверхность доски вниз.
Перфорация
При необходимости фанерные плиты, используемые для внутренней облицовки, также можно заказать готовыми перфорированными.Перфорированные доски обычно используются по причинам акустики или внешнего вида. Перфорация осуществляется механическим способом, и при заказе плит в дополнение к вышеупомянутым инструкциям следует также указать размер отверстия и зазор между отверстиями. Размер отверстия может составлять, например, 6, 8, 10, 12… мм и расстояние между отверстиями 16, 32, 64…. Мм. Некоторые поставщики могут иметь определенные стандартные размеры отверстий и расстояния, поэтому желательно проверить варианты перфорации перед заказом.
Сгибание
Изогнутые поверхности также могут быть сделаны из фанеры. Для этой цели наиболее подходят тонкие доски толщиной менее 10 мм. Ориентировочный радиус изгиба составляет чуть менее одного метра, причем изгиб происходит поперек направления зерна поверхностного шпона и толщина доски не более 9 мм. Вы должны знать, что небольшой радиус изгиба приводит к тому, что на поверхности доски легко появляются растрескивающиеся линии. Гнутая доска всегда крепится винтами.
Наименьшие радиусы изгиба фанеры. Обработка водой или паром помогает при сгибании фанеры. Смешанная фанера из березовой фанеры. | ||
---|---|---|
Номинальная толщина мм | Изгиб в направлении зерна поверхностного шпона | Изгиб поперек направления зерна поверхностного шпона |
6.5 | 850 | 650 |
9 | 1150 | 950 |
12 | 1150 | 1250 |
КРЕПЛЕНИЕ
Длина гвоздей, используемых для крепления досок, должна быть не менее чем в три раза больше толщины доски, но не менее 30 мм, а длина шурупов не менее чем в 2,5 раза больше толщины доски, но не менее 25 мм. ,При гвоздях целесообразно использовать профилированные гвозди, а при установке опорных плит для крыш — гайки с горячей оцинковкой или гвозди.
Доски крепятся с интервалом около 150 мм с каждой стороны и около 300 мм в центре. Крепежи, которые не будут видны, крепятся к фанерным доскам в среднем на расстоянии 10 мм от края доски. Застежки, которые будут оставлены видимыми, крепятся к фанерным доскам на расстоянии 10 мм от края доски, по прямой линии и обращены друг к другу с обеих сторон шва.
Когда фанера используется как часть каркасных конструкций (обычно фанеры с шипами и рифленой хвойной древесиной), смежные доски устанавливаются таким образом, чтобы стыки плит не образовывали крестообразный рисунок.
ЛЕЧЕНИЕ ПОВЕРХНОСТИ
Фанера без покрытия (облицованная деревянной поверхностью) может быть обработана обычными лакокрасочными материалами, предназначенными для облицовки древесины. Грунтовка должна выполняться с особой тщательностью, чтобы предотвратить возможные поверхностные трещины. Чтобы избежать появления волосяных трещин на поверхности, используйте фанеру, которая была предварительно обработана эпоксидной грунтовкой или покрыта грунтовочной бумагой.При покраске фанеры с покрытием рекомендуется наносить два слоя эпоксидной грунтовки и один слой полиуретановой краски на поверхность.
Поскольку продукты, предназначенные для обработки поверхности, имеют значительные различия в зависимости от производителя, пригодность продукта к фанерным поверхностям всегда следует проверять в инструкциях производителя.
Обработка поверхности внутренних облицовочных плит в основном имеет эстетическое значение. Покраска, окраска остекления, окрашивание и др.дает фанере желаемый цвет, в то время как бесцветный лак в основном дает желаемую степень глянца. Кроме того, обработка поверхности облегчает поддержание фанеры в чистоте.
Во внутренних помещениях для обработки поверхности фанерной облицовки подходят:
- вощение (бесцветное или цветное)
- лакировка (бесцветный или цветной лак)
- покраска (все наиболее распространенные продукты, предназначенные для внутренних деревянных поверхностей)
Перед обработкой рекомендуется слегка отшлифовать поверхность (особенно восковые поверхности).В сухих помещениях фанеру также можно использовать без обработки поверхности. В техническом смысле потолочная облицовка, в частности, обычно не требует обработки поверхности. Однако полезно знать, что ультрафиолетовое излучение солнечного света постепенно приводит к потемнению верхнего шпона, что в некоторой степени можно предотвратить с помощью лака, содержащего УФ-защитный агент. С другой стороны, лакирование само по себе может привести к изменению оттенка верхнего шпона (обычно более желтого). Этого можно избежать, используя лак, смешанный с небольшим количеством белого пигмента.Вышеупомянутые изменения в оттенке и их прочности варьируются в зависимости от типа древесины, из которой сделан верхний шпон.
ИСПОЛЬЗОВАНИЕ И УТИЛИЗАЦИЯ PLYWOOD
Повторное использование
Если доски не повреждены и не высохли, а клей от стыков шпона не отделился, фанерные плиты можно использовать повторно в каждом конкретном случае. Повторное использование является наиболее популярным способом утилизации фанерной продукции.
Жжение
Небольшие количества непокрытой или пленочной фанеры можно утилизировать путем сжигания с другой древесиной.Температура должна быть настолько высокой, чтобы горение происходило как можно лучше.
Компостирование
Основные фанеры и большинство специальных фанер также могут быть компостированы. Отходы фанеры, смешанные с отходами древесной щепы, облегчают процесс компостирования. Довольно большое количество отходов фанеры может быть принято на свалку.
PLYWOOD APPLICATIONS
Строительство
- крыша
- подпольная посадка
- Усиление обшивки стен и несущих конструкций
- внутренняя подкладка
- балконных этажей
- строительных лесов
- бетонные формы
- строительные заборы
Строительная промышленность
- как пластины для балок
- каркас паркетного пола
- Светильники и арматура
Транспортные средства
- контейнеров
- прицепов
- фургонов интерьеров
- железнодорожных вагонов
Судостроение
- грузовых лайнеров
- автомобильных палуб
- люков
- внутренняя отделка
Другие применения
- мебель, столярная промышленность и мелкие предметы
- оборудование для пищевой промышленности
- упаковка
- дорожных знаков и рекламных щитов
- Зрительные залы / стадионы
- выставочно-ярмарочные сооружения
- катков
- акустические системы
УРОВЕНЬ ТЕХНИКИ
1. Область техники, к которой относится изобретение
Изобретение относится к способу производства бумаги с покрытием из меламиновой смолы для формирования горячепрессованных, устойчивых к царапинам поверхностных слоев на синтетических материалах из ламината и деревянных рабочих материалах, таких как древесноволокнистые плиты, древесностружечные плиты, фанера или аналогичные материалы, посредством чего бумагу предварительно пропитывают мочевинной смолой, которая растворима в воде в ее все еще не затвердевшем состоянии, или аминопластом, богатым мочевиной, и которая растворима в воде в еще не затвердевшем состоянии, сушат и, кроме того, наносят, по меньшей мере, на одной стороне с применением меламиновая смола, которая растворима в воде в неотвержденном состоянии, которая также высушивается и которая в процессе горячего прессования, в случае которой бумага соединяется с поверхностью подложки, на которую необходимо нанести покрытие, образует отвержденную, устойчивую к царапинам химически постоянный замкнутый поверхностный слой при течении.
2. Описание предшествующего уровня техники
Бумага с покрытием из меламиновой смолы, покрытие из меламиновой смолы которой в процессе горячего прессования, в случае которой бумага соединяется с поверхностью подложки, на которую должно быть нанесено покрытие, будет образовывать затвердевший поверхностный слой при протекании. Они широко используются для производства поверхностных покрытий, в связи с чем они используются, прежде всего, в связи со слоистыми формовочными веществами, изготовленными из бумаги с фенольной смолой, а также для производства покровных слоев или древесно-волокнистых плит и древесностружечных плит при любой необходимости. декоративные слои поверхности должны быть созданы.При использовании такой бумаги с покрытием из меламиновой смолы можно получить поверхностные слои, которые легко устойчивы к царапинам по сравнению с обычными напряжениями, возникающими в домашнем хозяйстве или в офисе, а также способны легко противостоять термическим или химическим воздействиям, возникающим в этой области. , В связи с этим мы можем упомянуть, что для покрытия поверхности используются различные другие бумаги и фольги, поверхность которых будет испытывать такие напряжения и которые значительно уступают, особенно в отношении стойкости к царапинам поверхностных слоев, полученных на основе бумага с покрытием из меламиновой смолы.
Использование меламиновых смол, которые, как было упомянуто, приводит к получению поверхностей, способных выдерживать высокие нагрузки, и которые, кроме того, благодаря необычным оптическим характеристикам этих смол, имеют преимущества, действительно представляют значительный фактор стоимости в данном случае. производства мелованной бумаги. Замена меламиновых смол мочевинными смолами, которые доступны по более выгодной цене и которые также имеют хорошие оптические характеристики, сталкивается с большими трудностями в результате чувствительности к влаге отвержденных карбамидных смол.В случае использования смесей карбамидных смол и меламиновых смол для производства здесь поверхностных слоев рассматриваемого типа это приведет к значительному снижению качества по сравнению с поверхностными слоями, которые сформированы на основе чистых меламиновых смол. ,
Чтобы существенно снизить затраты на смолу в случае производства бумаги с покрытием из меламиновой смолы при сохранении покровных слоев, изготовленных из чистой меламиновой смолы, известны предложения, предусматривающие предварительную пропитку бумаги мочевиной. смолой или смолой, смешанной с мочевиной и меламином, и затем для бумаги, пропитанной таким образом, покровными слоями из меламиновой смолы.В этом случае возникает проблема, заключающаяся в том, что необходимо эффективно противодействовать диффузии мочевинной смолы в покрывающий слой из меламиновой смолы, чтобы сдерживать ухудшение качества покрывающего слоя. В результате возникли трудности как в отношении этой проблемы, так и в отношении процессов насыщения или нанесения покрытия и сушки бумаги, на которую должно быть нанесено покрытие во время практического выполнения известных процессов. Это препятствовало общему внедрению этих процессов, вследствие чего часто проявлялась сильная тенденция к смешиванию пропиточной смолы с покровным слоем из меламиновой смолы.
СУЩНОСТЬ ИЗОБРЕТЕНИЯ
Задачей настоящего изобретения является создание способа вышеупомянутого типа, в котором предварительная пропитка приведет к значительной экономии смолы покровного слоя и где также исключена опасность диффузии смолы перед пропиткой в покровный слой. В то же время, возможность проведения процессов насыщения быстро и без проблем должна быть гарантирована.
Способ в соответствии с изобретением включает предварительное пропитывание бумаги раствором мочевинной смолы или аминопласта, богатого мочевинной смолой (далее в совокупности «смола» или мочевина «смола»), со степенью конденсации смолы или аминопласта будучи выше, чем у водорастворимой меламиновой смолы, применяемой для формирования покровного слоя (слоев), при этом поглощение смолы или аминопласта сохраняется ниже, чем это требуется для образования пленки смолы или аминопласт, покрывающий поверхность бумаги, горячая сушка предварительно пропитанной бумаги до тех пор, пока предварительно пропитанная смола, нанесенная на бумагу, не затвердеет, по крайней мере, до такой степени, что смола или аминопласт практически не растворяется в растворе для нанесения меламиновой смолы до наносить с применением кроющего раствора меламиновой смолы, а затем сушить бумагу после нанесения меламиновой смолы до остаточной влажности, составляющей от 5 до 10%.
ПОДРОБНОЕ ОПИСАНИЕ ИЗОБРЕТЕНИЯ
В результате осуществления мер согласно изобретению, указанные выше объекты могут быть хорошо встречены, и с этой бумагой можно получить поверхностные слои, характеристики которых равны поверхностным слоям, которые получены с использованием бумаги, покрытой просто чистой меламиновой смолой. , В этом случае особенно примечательно, что в случае процесса горячего прессования, когда происходит поток меламиновой смолы, не происходит смещения мочевинной смолы, находящейся в бумаге, на поверхность, покрытую меламиновой смолой, и не происходит никаких диффузий. склеивания покровных слоев из меламиновой смолы на бумажной подложке, поскольку меламиновая смола проникает в волокнистую структуру бумаги и, следовательно, покрывающий слой из меламиновой смолы, который определяет характеристики поверхностных слоев, полученных в отношении устойчивости к царапинам, а также Что касается химической и термической стабильности, то она укрепляется волокнистой структурой бумаги, так что возможная хрупкость меламиновых смол не будет оказывать неблагоприятного воздействия.В результате более высокой степени конденсации полученной предварительно пропиточной смолы, быстрое предварительное отверждение этой смолы может быть достигнуто во время процесса сушки.
Что касается разницы в степени конденсации между предварительно пропиточной смолой и меламиновой смолой покровного слоя, мы понимаем в этом случае, таким образом, что вязкость раствора предварительно пропиточной смолы, которая имеет такую же концентрацию смолы и ту же температуру, что и Сравнительный раствор покровного слоя меламиновой смолы больше, чем вязкость последней.
Опасность смешивания мочевинной смолы или аминопласта, богатого мочевиной, из которого состоит предварительная пропитка бумаги, с меламиновой смолой, служащей для формирования покровных слоев, эффективно решается благодаря тому факту, что смола предварительной пропитки, состоящая из из мочевинной смолы или аминопласта, богатого мочевиной, затвердевает, по меньшей мере, до такой степени, что она практически не растворяется в покрывающем растворе применяемой меламиновой смолы.
В результате последней меры, просто в результате более высокой степени концентрации пропиточной смолы, предотвращается перемещение предварительно пропиточной смолы в покровный слой из меламиновой смолы.Кроме того, количество смолы, необходимое для покровных слоев, уменьшается, так как таким образом любое поглощение меламиновой смолы внутрь бумаги будет в значительной степени исключено в ходе процесса горячего прессования.
В случае способа в соответствии с изобретением целесообразно, чтобы в ходе горячей сушки, следующей за предварительной пропиткой и которая предпочтительно осуществлялась с помощью горячего воздуха, влажность бумаги понижалась до значение лежит ниже 7%.Предпочтительно, в то же время в случае сушки горячим воздухом бумагу, насыщенную предварительно пропиточной смолой, сушат до остаточной влажности, составляющей от 2 до 6%.
Высушивание горячим воздухом, которое, как известно само по себе, может быть проведено путем пропускания быстро движущегося бумажного полотна через сушильный канал, приводит к выгодному развитию желаемого отверждения смолы для предварительной пропитки по мере сушки, посредством чего продолжается в результате содержания воды температура регулируется автоматически, что благоприятно для предварительного отверждения смолы перед пропиткой.
Также возможно проводить сушку после предварительной пропитки с помощью радиационного тепла, в результате чего сушка может быть закончена при более высокой остаточной влажности, чем в случае сушки горячим воздухом, поскольку воздействие радиации на стороне, обращенной к радиатору дополнительно способствует отверждению смолы перед пропиткой. В этом случае предпочтительно обеспечить сушку до влажности 16% или менее; предпочтительная область находится между 10 и 13% влажности.
Кроме того, эффективно сушить бумагу во втором процессе сушки, который следует за нанесением меламиновой смолы до остаточной влажности, составляющей от 6 до 8%.
Предпочтительно, чтобы для предварительной пропитки бумаги использовался раствор смолы с по меньшей мере 45 мас.% Твердой смолы, в результате чего получается хорошее заполнение бумаги и в то же время очень экономичная сушка предварительной пропитки. Оба преимущества проявляются особенно в случае работы с раствором смолы, который содержит от 48 до 55 мас.% Твердой смолы.
Всякий раз, когда необходимо содействовать процессу насыщения предварительной пропитки, тогда особенно полезно, когда обрабатывается бумага с низкой впитывающей способностью, если концентрация раствора для предварительной пропитки в зависимости от типа подлежащей покрытию бумаги регулируется до твердой смолы. содержание составляет от 20 до 45, предпочтительно от 35 до 45 мас.%.Работа с раствором, который содержит от 35 до 45 мас.% Твердой смолы, приведет в одно и то же время простым способом к количественно хорошему поглощению смолы из бумаги.
Чтобы получить как можно более четко определенный процесс конденсации и отверждения для предварительной пропитки, следует преимущественно использовать чистый карбамидоформальдегидный конденсат для предварительной пропитки.
Однако для предварительной пропитки можно также использовать карбамидоформальдегидный конденсат, смешанный с меламиновой смолой, причем степень конденсации карбамидоформальдегидного конденсата, все еще свободного от меламиновой смолы, выше, чем у меламиновой смолы.
При желании, однако, можно также использовать для предварительной пропитки мочевинную смолу, смешанную с пластифицирующими агентами, такими как f. например, капролактам, сахароза, гликоли, полигидроксисоединения и т. д. или аминопласт, богатый мочевиной.
В случае использования раствора пропиточной смолы с содержанием твердой смолы более 45 мас.%, Особенно между 48 и 55 мас.%, Предпочтительно соотношение количества смолы, применяемой для предварительной пропитки, по отношению к количество нанесенной меламиновой смолы, предусмотренной для формирования покровного слоя, и в случае нанесения покровного слоя на обе стороны, выбирается в диапазоне от 2: 3 до 3: 1, предпочтительно от 55:45 до 65:35 ,Если, наоборот, используется раствор для предварительной пропитки смолы с содержанием твердой смолы от 20 до 45 мас.%, Особенно от 35 до 45 мас.%, То это количественное соотношение будет преимущественно выбираться в диапазоне от 1: 2 до 3: 2, предпочтительно от 5: 6 до 6: 5.
Что касается предварительного отверждения, будет выгодно всякий раз, когда отвердитель, добавленный к предварительно пропиточной смоле, имеет высокую температуру реакции. Можно также упомянуть, что количество отвердителя в случае технологии согласно изобретению не является критическим и что можно также использовать без каких-либо недостатков количества отвердителей, которые выше, чем обычно.
Нанесение смолы для предварительной пропитки и нанесение покрытия из меламиновой смолы может быть выполнено с помощью валиков аппликатора или путем погружения, и в то же время можно, после каждого процесса нанесения, выполнить отжим или вытирание избыток смолы.
Оказалось целесообразным выполнить нанесение смолы перед пропиткой путем увлажнения с помощью валиков аппликатора и последующего погружения бумажного полотна, вытирая или отжимая избыток смолы, и осуществлять нанесение меламиновой смолы на высушенную бумага, насыщенная мочевиной или аминопластом, богатым мочевиной, с помощью аппликаторов или фильтров-скребков.
Для нанесения особенно тонких слоев меламиновой смолы предпочтительно использовать ситовые ролики. В то же время, мы можем также упомянуть, что различие, возникающее в результате использования бумаги с разной сильной впитывающей способностью, намного ниже в стоимостном факторе, требуемом для смолы в случае использования технологии согласно изобретению, чем это было до сих пор. так как действительно, мочевинная смола, применяемая для предварительной пропитки бумаги, имеет значительно более выгодную цену, чем меламиновая смола, и предварительная пропитка в значительной степени компенсирует различия в впитывающей способности между различными типами бумаги, и, следовательно, применение меламиновой смолы практически только образует поверхностные слои.
В случае способа согласно изобретению можно обеспечить покровный слой меламиновой смолы с обеих сторон, и в этом случае нанесение меламиновой смолы, расположенное на одной стороне бумаги, также служит для соединения бумаги, образующей поверхность, с подложка и в этом случае затвердевает в процессе горячего прессования.
Однако можно также нанести меламиновую смолу только на одну сторону бумаги и соединить бумагу с помощью клея с подложкой.Этот адгезив может быть клеем горячего отверждения, который наносится на подложку, на которую наносится бумага. Тем не менее, также возможно нанести клей для горячего отверждения на бумагу на стороне бумаги, противоположной стороне, содержащей покрытие из меламиновой смолы.
Следующие примеры должны объяснить изобретение более подробно.
ПРИМЕР 1
Белая декоративная бумага с весом на единицу площади 100 г / м 2 , зольностью 40% по массе, воздухопроницаемостью 350 мл / мин (стандартное испытание), всасывающей головкой по Клемму из 32 мм, гладкость по Бекку, с обратной стороны 40 сек.и на верхней части в течение 60 с обеспечивали плотное прилегание к валику аппликатора, погружающемуся в ванну со смолой с нанесением смолы; это нанесение смолы впитывалось в непрерывную дорожку движения бумаги в бумагу, и затем бумага пропускалась через два отжимных валика, в результате чего количество смолы, которое присутствовало после оставления сжимающих валиков в бумаге, регулировалось регулировка взаимного давления прижимных валков и регулировка скорости движения бумаги.Таким образом, бумага была насыщена раствором коммерческого карбамидоформальдегидного конденсата, который имел содержание твердой смолы 51,5% по массе и вязкость 19 DIN сек (выпускное сопло 4 мм), имел молярное отношение 1: 2.1 и содержал хлорид аммония в качестве отвердителя. В этом случае, после прохождения пары сжимающих валков, насыщенная бумага имела вес 240 мг / м 2 и, следовательно, содержала 140 г раствора смолы на м 2 с содержанием смолы 50 мас.% следовательно, 70 мас.% твердой смолы в расчете на массу необработанной бумаги.
После выхода из сжимающих валков бумажное полотно плавно направлялось через канал горячего воздуха, в котором было расположено несколько регистров горячего воздуха, в результате чего температура горячего воздуха регулировалась примерно до 160 ° С. после этой сушки воду, содержащуюся в бумажном полотне, удаляли до остаточной влажности около 4%. Таким образом, бумага была в значительной степени заполнена мочевинной смолой, а мочевинная смола показала такое предварительное отверждение, что она практически перестала растворяться в растворе меламиновой смолы, предусмотренном для последующего нанесения покровного слоя.После этого бумажное полотно, предварительно пропитанное таким образом водорастворимой мочевинной смолой, направлялось в натянутом состоянии по двум рулонам-аппликатору и таким образом водный раствор меламиновой смолы с содержанием смолы 52,6 мас.% И вязкостью 16 DIN (выпускное сопло 4 мм) было нанесено на обе стороны бумажного полотна. В этом случае мы имели дело с водным раствором коммерческой меламиновой смолы, предназначенной для прессования бумажных ламинатов под высоким давлением, который был смешан с отвердителем на основе морфолина п-толуолсульфоновой кислоты.В этом случае 26 г раствора смолы наносили на м 2 на одну сторону бегового бумажного полотна, а на другой стороне 58 г на м 2 этого раствора смолы. После этого бумагу снова пропускали через сушильный канал, в котором удаляли влагу до остаточной влажности 7%. Таким образом, полученная бумага имела общий слой 50 г меламиновой смолы / м 2 .
ПРИМЕР 2
Однако, аналогично примеру 1, бумагу снова раскатывали после первого процесса сушки и хранили в течение более длительного периода времени до нанесения покрытия из меламиновой смолы.Никакого слипания не произошло, что могло бы нарушить последующее покрытие из меламиновой смолы.
ПРИМЕР 3
Сильно впитывающая декоративная бумага с плотностью на единицу площади 120 г / м 2 насыщалась способом, аналогичным примеру 1, раствором промышленного карбамидоформальдегидного полимерного лака с мольным отношением 1: 1,9, которое имел содержание смолы 50% по весу. Этот смоляной лак имел вязкость 17 DIN сек (выпускное сопло 4 мм) и добавление 3 мас.% Этиленгликоля и, разумеется, смешивался с гидрохлоридом этаноламина в качестве отвердителя (1% массы по отношению к твердой смоле).Пропитка была отрегулирована таким образом, чтобы бумага после выхода из сжимающих валков имела вес на единицу площади 360 г / м 2 . Следовательно, бумага после выхода из сжимающих валков содержала 100 мас.% Твердой смолы по отношению к массе необработанной бумаги. Затем бумажное полотно пропускали через устройство инфракрасных излучателей с целью сушки, и в результате подачи тепла, обеспечиваемого таким образом, и последующей проводимости по короткому каналу с горячим воздухом, бумага, таким образом, была высушена до остаточная влажность 5%.После этого бумажное полотно пропускали через пропиточный резервуар, в котором находился раствор коммерческой меламиновой смолы низкого давления, содержащей 52,5 мас.% Твердой смолы, который использовали для прессования с коротким циклом без повторного охлаждения. Этот раствор смолы имел вязкость 15,5 DIN с (выпускное сопло 4 мм). После выхода из пропиточного резервуара бумажное полотно пропускали через зачистные бруски и отжимные валики, и в то же время количество раствора меламиновой смолы, поглощенного бумагой, доводили до 103 г / м 2 .Затем бумажное полотно сушили в канале с горячим воздухом до остаточной влажности 7,5%.
ПРИМЕР 4
Белая декоративная бумага с весом на единицу площади 95 г / м 2 , зольностью 36% по массе, всасывающая головка, соответствующая Клемму, 26 мм, гладкость по Бекку на обратной стороне 40 секунд и на верхней стороне 70 секунд, а также воздухопроницаемость 260 л / мин (стандартное испытание) обеспечивалось с нижней стороны нанесением смолы, посредством чего нанесение смолы осуществлялось с помощью валика-аппликатора, погруженного в ванну со смолой и затем бумагу направляли на ванну со смолой.Затем бумажное полотно погрузили в ванну со смолой, направили путем отжимания валков и, наконец, достигли сушильного канала. Смоляная ванна состояла из раствора промышленного продукта конденсации мочевины и формальдегида с мольным отношением 1: 2,2, который был разбавлен до содержания твердой смолы 22,5 мас.% И который содержал в качестве отвердителя гидрохлорид этаноламина. Регулируемая таким образом смоляная ванна имела вязкость 12,2 DIN с (выпускное сопло 4 мм). В результате этой регулировки было гарантировано, что в случае скорости подачи бумажного полотна 26 м / мин от точки нанесения смолы через аппликатор до рулона бумаги до погружения бумаги в смолу ванна, полное проникновение в бумагу может иметь место.Регулируя давление взаимного контакта отжимающих валков, пропитанная бумага перед сушкой имела вес 255 г / м 2 , что соответствует пропитке 37,9% по массе твердой смолы, полученной при нанесении смолы, в зависимости от веса бегущей бумаги. Пропитанное бумажное полотно пропускали через канал горячего воздуха и сушили при температуре горячего воздуха около 155 ° С до остаточной влажности 3,5%. Бумага теперь была пропитана мочевинной смолой, и пропиточная смола имела степень предварительного отверждения, что делало ее практически нерастворимой в последующем растворе меламиновой смолы, предоставленном в качестве покрытия для покровного слоя.Бумажное полотно затем направлялось через другое устройство для нанесения смолы, в котором оно было снабжено с обеих сторон водным раствором коммерческого продукта конденсации меламин-формальдегид. Этот раствор доводили до содержания твердой смолы 50 мас.%, В то же время он имел вязкость 14,8 DIN с (выпускное сопло 4 мм) и содержал дополнительно отвердитель, морфолин п-толуолсульфоновой кислоты, смачивающий агент и разделительный агент. Это нанесение покрывающей смолы было отрегулировано таким образом, чтобы после прохождения через дополнительный сушильный канал было нанесено меламиновой смолы 67 г твердой смолы / м 2 .Сушка во втором сушильном канале была выполнена таким образом, что в конечном итоге остаточная влажность в готовой бумажной пленке составила 7,3%.
Пример 5
Декоративная бумага с массой на единицу площади 120 г / м 2 , всасывающей головкой по Клемму 28 мм и зольностью 28% по весу была предварительно пропитана водным раствором карбамидоформальдегидной смолы. лак с мольным отношением 1: 2,05. Раствор предварительно пропиточного лака доводили одновременно до содержания твердой смолы 41.5 мас.% И содержал хлорид аммония в качестве отвердителя. Вязкость раствора предварительной пропитки смолы составила 14,5 дин с (4 мм разгрузочная насадка). Устройство предварительной пропитки было отрегулировано таким образом, чтобы в случае подачи бумаги со скоростью 23 м / мин смола полностью проникала в бумагу и после прохождения через канал сушки горячим воздухом, в котором пропитанное бумажное полотно сушили до остаточной влажности. 4,5%, вес предварительно пропитанной и высушенной бумажной пленки составил 195 г / м 2 .Это соответствовало нанесению смолы 55% по весу твердой смолы в расчете на вес беговой бумаги. После этого на предварительно пропитанную бумажную пленку наносили с обеих сторон раствор коммерческой меламиновой смолы, содержащей 54 мас.% Твердой смолы, которая содержала, помимо отвердителя, обычно используемого для прессования с коротким циклом без повторного охлаждения, дополнительно смачивания и разделительный агент. Этот раствор смолы имел вязкость 16,5 DIN сек (выпускное сопло 4 мм).Затем бумажное полотно снова подвергали сушке горячим воздухом до остаточной влажности 7,2% и, наконец, наносили меламиновую смолу 65% по массе по отношению к массе бегущей бумаги.
ПРИМЕР 6
Декоративная бумага с весом на единицу площади 75 г / м 2 , зольностью 29% по массе, гладкостью 60 с (по Бекку), всасывающей головкой по Клемму 30 мм и воздухопроницаемость 250 мл / мин предварительно пропитывали продуктом конденсата формальдегид-мочевина-меламин с мольным отношением 2.3: 0,85: 0,15. Для этой цели пропиточный раствор смолы для предварительной пропитки доводили до содержания твердого вещества 35 мас.% И в то же время он имел вязкость 13,5 DIN сек (выпускное сопло 4 мм). Чтобы гарантировать степень предварительного отверждения смолы для предварительной пропитки, которая делает практически невозможным растворение смолы перед пропиткой в последующей меламиновой смоле, указанный раствор смолы для предварительной пропитки содержал упрочняющую добавку, составляющую 0,6 мас.% Гидрохлорида этаноламина, что связано с твердой смолы, и пропитанное бумажное полотно сушили до остаточной влажности 4.2% в канале сушки горячим воздухом. После выхода из первого сушильного канала предварительно пропитанная бумажная пленка имела нанесение смолы 57% по массе твердой смолы из предварительно пропитанной смолы. На бумагу, предварительно пропитанную таким образом, теперь наносили покрывающую смолу из водного раствора товарной меламиновой смолы с содержанием твердой смолы 50,5 мас.%, Которая содержала обычные добавки отвердителя, смачивателя и разделительного агента, в таком виде таким образом, чтобы 31 г твердой смолы / м 2 был нанесен на сторону бумаги, служащей в качестве внешнего слоя после последующего формования, и 10 г твердой смолы / м 2 на сторону бумаги, служащей в качестве клеевой слой.Этот раствор меламиновой смолы имел вязкость 15 DIN сек (выпускное сопло 4 мм). После нанесения меламиновой смолы, служащей в качестве покрывающего слоя, бумажное полотно снова высушили и одновременно довели до остаточной влажности 7,0%.
ПРИМЕР 7
Белая декоративная бумага, которая имела вес на единицу площади 100 г / м 2 , зольность 32% по весу, всасывающая головка по Клемму 30 мм и гладкость 70 с (по Бекку ), предварительно пропитывали раствором карбамидоформальдегидно-смоляного лака, содержащего 38.5% по весу твердой смолы. Раствор этой смолы для предварительной пропитки содержал отвердитель аминогидрохлорид и имел вязкость 15 DIN с (выпускное сопло 4 мм). При скорости подачи бумаги 20 м / мин схема предварительной пропитки регулировалась таким образом, чтобы смола полностью проникала в бумагу, и бумага после выхода из предварительной пропитки поглощала 40 мас.% Твердой смолы. Предварительно пропитанную бумагу теперь пропускали между двумя радиационными сушилками с тепловой мощностью 180 кВт, расположенными с обеих сторон бумажного полотна.Одновременно происходила сушка до остаточной влажности 12%. В результате этой сушки произошло предварительное отверждение смолы для предварительной пропитки, которая зашла настолько далеко, что смола для предварительной пропитки практически не растворилась в растворе меламиновой смолы, предусмотренном для последующего покрытия. Предварительно пропитанную бумагу затем пропускали через раствор коммерческой меламиновой смолы с содержанием твердой смолы 52,5% по массе, и обычные добавки отвердителей, смачивателя и разделительного агента впоследствии подвергали сушке горячим воздухом и одновременно сушат до остаточной влажности 7%.Этот раствор меламиновой смолы имел вязкость 15,5 DIN (выпускное сопло 4 мм). Бумага, наконец, имела покрытие из меламиновой смолы 70 мас.% В расчете на массу бегущей бумаги с обеих сторон.
ПРИМЕР 8
Аналогично примеру 6 после высыхания предварительной пропитки покрытие из меламиновой смолы наносили только на одну сторону бумажной пленки, а именно на ту сторону бумаги, которая служит внешним слоем после формования. В этом случае снова было обеспечено нанесение смолы 31 г твердой смолы / м 2, и затем бумажное полотно сушили до остаточной влажности 7%.Полученная таким образом бумажная пленка была отформована горячим способом на древесно-стружечную плиту, снабженную слоем клея, и в то же время и этот слой клея, а также нанесенная на бумагу меламиновая смола были отверждены в ходе этого процесса горячего формования , В этом случае на древесину наносили клей для мочевины горячего отверждения, предварительно разбавленный ржаной мукой (степень разведения 200; 100 частей смолы на основе мочевины, 100 частей ржаной муки, 100 частей воды), которая содержала хлорид аммония в качестве отвердителя. ЛДСП.
Бумаги, покрытые меламиновой смолой, полученные в соответствии с примерами 1-7, наконец, прессовали в обычной технологии горячего формования на подложку и затем подвергали обычным оценкам для определения качества поверхности формованных поверхностей из меламиновой смолы. Аналогично исследовали поверхность, полученную в соответствии с примером 8. В этом случае общепринятые испытания, особенно испытание на пар, испытание на трещину, испытание в кювете, испытание на твердение, испытание на пожелтение, испытания для определения устойчивости к царапинам, постоянства химических веществ и степени блеска, а также испытания на определение того, существует ли достаточно закрытая поверхность, было сделано.В этом случае оказалось, что характеристики поверхностей из меламиновой смолы, которые были получены с использованием бумаги, полученной, как описано в предыдущих отрывках, полностью соответствовали характеристикам, которые существуют в случае поверхностей из меламиновой смолы, которые были получены с использование бумаги, которая была пропитана только чистой меламиновой смолой. В частности, также было обнаружено, что поверхности, изготовленные из бумаги, разработанной в соответствии с изобретением, удовлетворяют требованиям DIN 53799.
,Выбор правильной фанеры для бетонной опалубки
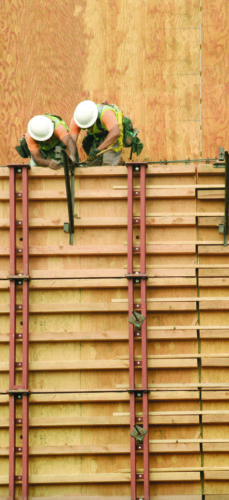
Изображения предоставлены APA
Марк Халверсон
Бетонная опалубка может составлять почти половину стоимости бетонной конструкции. Для экономически эффективного строительства, подрядчики выбирают формовочные панели, которые будут противостоять работе и многократному использованию.
Производители-члены APA — Ассоциация инженерных пиломатериалов производит различные изделия из фанерной фанеры — Plyform, предназначенные для большинства общих задач бетонирования. Обычно предварительно обработанные антиадгезивом для облегчения снятия, эти панели доступны во многих классах от базового BB до продуктов с наложениями (, т.е. наложение средней плотности [MDO]) и наложение высокой плотности [HDO]), которые добавляют стабильность, сопротивляются ссадины, и обеспечивают более гладкую и более прочную формующую поверхность.
Каждый производитель облицовочных бетоноформовочных панелей предлагает запатентованные продукты, предлагающие множество различных функций и преимуществ.
Выбор панелей
При планировании многократного повторного использования лучше всего использовать фанеру с более прочной конструкцией. Все панели Plyform имеют более прочную и прочную фанеру, чем традиционные панели обшивки, предлагаемые в диапазоне долговечности. Эти панели относятся к классу I, что означает, что они изготавливаются из самых прочных и жестких шпонов.Сорта шпона, используемого в панелях Plyform, указаны в торговой марке APA.
имеют пропитанные смолой листы целлюлозного волокна, ламинированные на их поверхности, и могут иметь либо односторонние, либо двусторонние поверхности. При бережном обращении и обслуживании любая двусторонняя формовочная панель, от B-B Plyform до накладных панелей, может быть вылита с обеих сторон.
HDO формирующие панели имеют большее количество смолы в оверлее; их поверхности тверже и более непроницаемы для воды и ударов, чем панели, образующие МДО.При использовании HDO Plyform можно ожидать большего количества применений и более гладкой поверхности бетона.
Формующие панели с гранями MDO часто накладываются только на одну сторону, но могут иметь разливные поверхности на обеих сторонах панелей. Хотя поверхности MDO не такие гладкие и долговечные, как панели HDO, подрядчик должен ожидать, что они получат больше отливов, чем панели без наложения или другой обработки поверхности. Отделка бетона от поверхности MDO будет более мягкой и не такой гладкой, как у панелей HDO.
Существует множество различных типов наложений и обработок для Plyform, которые можно использовать для увеличения срока службы. Панели B-B и B-C могут быть сделаны более прочными и устойчивыми к влаге с помощью покрытия, такого как полиуретан или другой тип обработки поверхности жидкостью. Одним из новейших высокоэффективных оверлеев является фенольная поверхностная пленка.
Важно помнить, что не все перекрывающиеся панели MDO и HDO (, например, , некоторые изделия общего и промышленного назначения, соответственно) предназначены для бетонной опалубки.Следует проявлять осторожность при определении и покупке бетонообразующих панелей; Можно посмотреть на торговые марки APA, четко идентифицирующие сорт и тип панели.
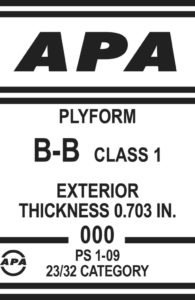
Сколько разливов можно получить из бетонной панели?
Вопрос о том, сколько заливок можно достичь с помощью одной конкретной бетонной панели, зависит не только от самого продукта, но и от его ухода и обслуживания. Почти все типы фанерных панелей могут быть использованы для формования бетона, от обычной кровли и облицовки стен до шлифованных панелей.Однако панели APA Plyform специально разработаны для того, чтобы противостоять износу при повторных заливках бетона, а также для обеспечения более гладкой и более стойкой поверхности бетона.
На число ожидаемых заливок бетонообразующей фанеры могут влиять многие факторы, в том числе:
- желаемая отделка по бетону;
- прочность поверхности панели, включая накладки;
- вида бетонной рецептуры; и
- , какие антиадгезивы используются.
Наиболее важным фактором является обработка и уход за панелями формы.
Например, поскольку панели поглощают воду, а увеличение содержания влаги обычно приводит к расширению и перемещению панелей, важно надлежащим образом прикрепить панели формы к каркасу и оставить пространство между панелями, которое обеспечивает их плоскостное движение внутри опалубка.
При разумном обслуживании можно ожидать более пяти заливок от Plyform класса B-B, в то время как панели HDO выдерживают до 20-50 повторных использований, а MDO Plyform находится где-то посередине.На самом деле, при правильном уходе, некоторые запатентованные панели для бетонирования могут достигать более 100 повторных использований.
Уход за панелями 101
Можно оптимизировать срок службы и эксплуатационные характеристики формовочных панелей, если они надлежащим образом обслуживаются. Вот некоторые общие соображения:
- применять антиадгезив перед каждой заливкой;
- используйте только цветные клинья и инструменты (, например, дерево или более мягкие пластмассы), чтобы удалить лишний бетон с поверхностей и краев панелей;
- храните панели лицом к лицу для защиты очищенных поверхностей;
- защищает уязвимые углы и края панелей при снятии и обработке;
- , если панели форм обрезаны, закройте края и кромки, чтобы защитить их от чрезмерного увлажнения; и
- учитывает примеси в бетонных составах при выборе типа формующей панели, понимая, что накладные панели обеспечивают большую устойчивость к химическим веществам.
Чтобы определить оптимальную панель для приложения, специалисты по проектированию / строительству могут посетить PerformancePanels.com, чтобы просмотреть списки производителей, ознакомиться со спецификациями продуктов и прочитать APA Руководство по проектированию / строительству бетонных конструкций .
Марк Халверсон проработал более 15 лет в сфере дистрибуции строительных изделий, прежде чем присоединиться к APA — Ассоциация инженеров по деревообработке в 1990 году. Он работал менеджером в APA с 1994 года, начиная с управления промышленными рынками и затем переходя к управление полевым персоналом группы.В этом качестве Хэлверсон курирует команду инженеров, архитекторов и технических экспертов, которые предоставляют информацию и рекомендации по инженерным лесам и системам профессионалам в области строительства и дизайна. С ним можно связаться по адресу [email protected].