Задания для олимпиады по технологии (технический труд) 7 класс
Задания школьного этапа Всероссийской олимпиады школьников по технологии.
7 класс (мальчики)
Составитель: учитель технологии МБОУ СОШ с УИОП № 7 им. А.С. Пушкина
г. Курск Даниленко В.А.
Отметьте знаком «+» правильный ответ.
Какое механическое свойство не относиться к свойствам древесины:
А) прочность;
Б) твёрдость;
В) плавкость;
Г) упругость.
Оценка выполнения данного задания:
1 балл – выбран ответ В.
0 баллов – выбран любой другой ответ.
Отметьте знаком «+» правильный ответ.
На каком станке изготавливают цилиндрические детали:
А) токарный станок;
Б) винторезный станок;
В) сверлильный станок;
Г) шлифовальный станок.
1 балл – выбран ответ А.
баллов – выбран любой другой ответ.
Отметьте знаком «+» правильный ответ.
Основной режущий инструмент при работе на токарном станке для обработки металла:
А) сверло;
Б) фреза;
В) метчик;
Г) резец.
Оценка выполнения данного задания:
1 балл – выбран ответ Г.
0 баллов – выбран любой другой ответ.
Отметьте знаком «+» правильный ответ.
С помощью, какой передачи в сверлильном станке осуществляется вращение сверла:
А) ремённой;
Б) реечной;
В) цепной;
Г) зубчатой.
Оценка выполнения данного задания:
1 балл – выбран ответ А.
0 баллов – выбран любой другой ответ.
- Отметьте знаком «+» правильный ответ.
Сведения о процессе изготовления изделий приведены на:
А) чертеже изделия;
Б) техническом рисунке;
В) сборочном чертеже;
Г) технологической карте.
Оценка выполнения данного задания:
1 балл – выбран ответ Г.
0 баллов – выбран любой другой ответ.
Отметьте знаком «+» правильный ответ.
По какому графическому документу изготавливают детали машин:
А) по чертежу;
Б) по рисункам;
В) по фотографиям.
Оценка выполнения данного задания:
1 балл – выбран ответ А.
0 баллов – выбран любой другой ответ.
Расшифруйте марку станка ТДС-120.
______________________________________________________________________________________________________________________________________________
Оценка выполнения данного задания:
1 балл – правильный ответ: токарный деревообрабатывающий станок, 120- высота центров.
0 баллов – другой ответ.
Отметьте знаком «+» правильный ответ.
Назовите одним словом: железо, медь, алюминий, олово, свинец, золото, серебро:
А) неметаллы;
Б) сплавы;
В) металлы;
Г) цветные металлы.
Оценка выполнения данного задания:
1 балл – выбран ответ В.
0 баллов – выбран любой другой ответ.
Отметьте знаком «+» правильный ответ.
Частоту вращения заготовки на токарном станке позволяет изменять:
А) задняя бабка;
Б) суппорт;
В) коробка подач;
Г) коробка передач.
Оценка выполнения данного задания:
1 балл – выбран ответ
Г.0 баллов – выбран любой другой ответ.
Определите соответствие между видом резьбы и изображением
А. Б.
В.
Г.
Контурная 2. Геометрическая 3. Прорезная 4. Скульптурная
Оценка выполнения данного задания:
1 балл – ответ А – 2, Б – 4, В – 1, Г – 3 .
0 баллов –любой другой ответ.
Определите соответствие между свойством древесины и его определением
Свойство
Определение
1. Сушка
А. Изменение формы материалов и их растрескивание
2. Усушка
Б. Процесс удаления влаги из древесины
3. Коробление
В. Количество воды, содержащееся в древесине
4. Влажность
Г. Уменьшение размеров древесины в результате сушки
5. Прочность
Д. Способность древесины сопротивляться внедрению в неё других, более твердых тел
6. Твердость
Е. Способность древесины выдерживать нагрузки
7. Ударная вязкость
Ж. Свойство древесины восстанавливать первоначальную форму и размеры
8. Упругость
З. Способность древесины поглощать работу при ударе, не разрушаясь
Оценка выполнения данного задания:
1 балл – ответ 1 – Б, 2 – Г, 3 – А , 4 – В , 5 – Е , 6 – Д, 7 – З , 8 – Ж .
0 баллов –любой другой ответ.
- Отметьте знаком «+» правильный ответ.
Какой инструмент используют для нарезания внутренней резьбы?
А) плашка;
Б) метчик;
В) клупп;
Г) плашкодержатель.
Оценка выполнения данного задания:
1 балл – выбран ответ Б.
0 баллов – выбран любой другой ответ.
Отметьте знаком «+» правильный ответ.
Коррозия металла – это…
А) разрушение металла при воздействии внешних факторов;
Б) изменение физических свойств металла;
В) изменение технологических свойств металла.
Оценка выполнения данного задания:
1 балл – выбран ответ А.
0 баллов – выбран любой другой ответ.
Определите правильную последовательность этапов при выполнение творческого проекта по технологии.
Заключительный этап.
Технологический этап.
Подготовительный этап.
Этап изготовления изделия.
Конструкторский этап.
Оценка выполнения данного задания:
балл – ответ 3, 5, 2, 4, 1.
0 баллов – любой другой ответ.
Отметьте знаком «+» правильный ответ.
При внутреннем точении древесины на токарном станке, заготовку закрепляют на:
А) трезубце;
Б) планшайбе;
В) шпинделе;
Г) подручнике.
Оценка выполнения данного задания:
1 балл – выбран ответ Б.
0 баллов – выбран любой другой ответ.
Отметьте знаком «+» правильный ответ.
Продолжите определение: источник тока и потребитель энергии, соединенные между собой проводниками, образуют:
А) электрический дисбаланс;
Б) электрическую цепь;
В) электрические колебания.
Оценка выполнения данного задания:
1 балл – выбран ответ Б.
0 баллов – выбран любой другой ответ.
Отметьте знаком «+» правильный ответ.
Что на схеме электрической цепи обозначено буквой Н:
А) электромагнит;
Б) катушка;
В) динамик;
Г) лампочка.
Оценка выполнения данного задания:
1 балл – выбран ответ Г.
0 баллов – выбран любой другой ответ.
Отметьте знаком «+» правильный ответ.
Тепловое действие электрического тока используется в:
А) генераторах;
Б) электродвигателях;
В) электроутюгах;
Г) трансформаторах;
Оценка выполнения данного задания:
1 балл – выбран ответ В.
0 баллов – выбран любой другой ответ.
Отметьте знаком «+» правильный ответ.
Электромагнитное действие электрического тока используется в:
А) лампах накаливания;
Б) нагревательных приборах;
В) плавких предохранителях;
Г) электродвигателях.
Оценка выполнения данного задания:
1 балл – выбран ответ Г.
0 баллов – выбран любой другой ответ.
Отметьте знаком «+» правильный ответ.
Для чего служит зенковка:
А) для получения фасок;
Б) для сверления отверстий;
В) для обработки отверстий полученных литьём
Оценка выполнения данного задания:
1 балл – выбран ответ А.
0 баллов – выбран любой другой ответ.
Отметьте знаком «+» правильный ответ.
Для борьбы с коррозией можно:
А) промывать изделие;
Б) протирать изделие;
В) покрыть изделие лаком или краской;
Г) просушивать изделие.
Оценка выполнения данного задания:
1 балл – выбран ответ В.
0 баллов – выбран любой другой ответ.
Отметьте знаком «+» правильный ответ.
Слесарная операция, при выполнении которой с помощью режущего инструмента и ударного инструмента с заготовки отделяется лишний слой металла, называется:
А) клёпка;
Б) зенкование;
В) рубка;
Г) сверление.
Оценка выполнения данного задания:
1 балл – выбран ответ В.
0 баллов – выбран любой другой ответ.
Отметьте знаком «+» правильный ответ.
Многолезвиный металлорежущий инструмент для снятия небольших слоёв металла – это…
А) зубило;
Б) напильник;
В) молоток;
Г) штангенциркуль.
Оценка выполнения данного задания:
1 балл – выбран ответ Б.
0 баллов – выбран любой другой ответ.
Отметьте знаком «+» правильный ответ.
К технологическим машинам относятся:
А) эскалатор;
Б) мотоцикл;
В) токарный станок;
Г) космический корабль.
Оценка выполнения данного задания:
1 балл – выбран ответ В.
баллов – выбран любой другой ответ.
Отметьте знаком «+» правильный ответ.
К энергетическим машинам относятся:
А) токарный станок;
Б) швейная машина;
В) сверлильный станок;
Г) генератор;
Оценка выполнения данного задания:
1 балл – выбран ответ Г.
0 баллов – выбран любой другой ответ.
infourok.ru
Тесты по технологии.Мальчики 7 класс
Тесты всероссийской олимпиады по технологии
для учащихся 7- х классов муниципальный тур (мальчики)
1. С помощью, какой передачи в сверлильном станке осуществляется вращение сверла:
а) ремённой;
б) реечной;
в) цепной;
г) зубчатой.
2 . Основной режущий инструмент при работе на токарном станке:
а) сверло;
б) фреза;
в) метчик;
г) резец.
3. Ровные и гладкие поверхности детали из древесины получают с помощью:
а) лучковой пилы; б) ножовки;
в) рубанка; г) шерхебеля;
4 . Для чего служат Т- образные пазы на фрезерном станке:
а) для стружки;
б) для крепления деталей;
в) для экономии металла.
5 . В предмете «Технология» изучаются:
а) технологии производства автомобилей;
б) технологии создания медицинских инструментов;
в) технологии создания самолетов;
г) технологии преобразования материалов, энергии, информации.
6. Метчик и плашка — это инструменты для:
а) разметки отверстий;
б) контроля резьбы;
в) нарезание резьбы.
7. Сведения о процессе изготовления изделий приведены на:
а) чертеже изделия;
б) техническом рисунке;
в) сборочном чертеже;
г) технологической карте.
8. К технологическим машинам относятся:
а) эскалатор;
б) мотоцикл;
в) токарный станок;
г) космический корабль.
9. К энергетическим машинам относятся:
а) токарный станок;
б) швейная машина;
в) сверлильный станок;
г) генератор;
10. Способом создания мозаики по дереву является:
а) полирование;
б) резьба;
в) выполнение инкрустации;
г) выжигание;
11. Сколько слоев древесины имеет строганный шпон:
а) три;
б) два или три;
в) один.
12. Свойства древесины выдерживать определённые нагрузки не разрушаясь:
а) твёрдость;
б) плотность;
в) прочность;
г) пластичность.
13. Для настройки рубанка с металлической колодкой применяют:
а) рулетку;
б) киянку;
в) отвертку;
г) пилу.
14.Для чего применяются накладные уголки на тисках:
а) чтобы хорошо сгибать заготовку;
б) чтобы прочно закрепить заготовку;
в) чтобы не помять заготовку.
15. По какому графическому документу изготавливают детали машин:
а) по чертежу;
б) по рисункам;
в) по фотографиям.
16. Расшифруйте марку станка ТДС-120.
17. Какие части относятся к фрезерному станку:
а) передняя бабка;
б) задняя бабка;
в) консоль.
18. Для чего служит зенковка:
а) для получения фасок;
б) для сверления отверстий;
в) для обработки отверстий полученных литьём.
19. Для изготовления молотков, зубил, напильников применяется:
а) конструкционная сталь;
б) инструментальная углеродистая сталь;
в) легированная сталь;
г) чугун.
20. Частоту вращения заготовки на токарном станке позволяет изменять:
а) задняя бабка;
б) суппорт;
в) коробка подач;
г) коробка скоростей.
в) оценкой и самооценкой проекта;
г) защитой проекта.
infourok.ru
9. Частота вращения заготовки и практическая скорость резания
9.1. Теоретическая частота вращения
,
м/мин.
где VТ — скорость резания, допускаемая режущими свойствами резца, м/мин., d — диаметр обрабатываемой (при растачивании — обработанной) поверхности, мм
9.2. Практическая частота вращения заготовки nПР выбирается по паспорту станка: берется ближайшая к nТ меньшая (или большая, если она не превышает 5%) частота вращения
9.3. Практическая скорость резания
,
м/мин.
10. Силы резания при точении
, H
где СР — коэффициент, характеризующий условия обработки; t — глубина резания, мм; s — подача, мм/об.
Радиальная составляющая силы резания
Ру = (0,4…0,5)∙ Рz
Осевая составляющая силы резания Рх = (0,25…0,3)∙Рz
Кр = Кмр*Кср*Кφр*Кzр*Кγр*Ксожр
Хр, Yр — показатели степени, учитывающие влияние t и s;
Кр — общий поправочный коэффициент, характеризующий конкретные условия обработки; является произведением ряда коэффициентов, учитывающих влияние различных факторов;
10.1. Значения СР, Хр, Yр при обтачивании, растачивании и подрезании
Обрабатываемый материал | Материал резца | ||||||||||||||||||||||||||||||||||||||||||||||
Быстрорежущая сталь | Твердый став | Режущая керамика и СТМ | |||||||||||||||||||||||||||||||||||||||||||||
СР | Хр | Yр | СР | Хр | Yр | СР | Хр | Yр | |||||||||||||||||||||||||||||||||||||||
Сталь | 225 | 1,0 | 0,75 | 214 | 1,0 | 0,75 | 208 | 1,0 | 0,75 | ||||||||||||||||||||||||||||||||||||||
Чугун серый | 98 | 1,0 | 0,75 | 95 | 1,0 | 0,75 | 92 | 1,0 | 0,75 | ||||||||||||||||||||||||||||||||||||||
Чугун ковкий и высоко прочный | 103 | 1,0 | 0,75 | 84 | 1.0 | 0,75 | 81 | 1,0 | 0,75 | ||||||||||||||||||||||||||||||||||||||
10.2. КМр — коэффициент, учитывающий влияние свойств обрабатываемого материала | |||||||||||||||||||||||||||||||||||||||||||||||
Стали незакаленные | |||||||||||||||||||||||||||||||||||||||||||||||
σв, МП а | 300-400 | 400-500 | 500-600 | 600-700 | 700-800 | 800-900 | 900-1000 | 1000-1100 | 1100-1200 | ||||||||||||||||||||||||||||||||||||||
КМр | 0,69 | 0,16 | 0,82 | 0,89 | 1,0 | 1,06 | 1,18 | 1,28 | 1,36 | ||||||||||||||||||||||||||||||||||||||
Стали закаленные и наплавленные | КМр | 1,0 | |||||||||||||||||||||||||||||||||||||||||||||
Чугуны серые | |||||||||||||||||||||||||||||||||||||||||||||||
НВ | 120-140 | 140-160 | 160-180 | 180-200 | 200-220 | 220-240 | 240-260 | 260-280 | |||||||||||||||||||||||||||||||||||||||
Кмр | 0,81 | 0,88 | 0,94 | 1,0 | 1,06 | 1,12 | 1,17 | 1,22 | |||||||||||||||||||||||||||||||||||||||
Чугуны ковкие и высокопрочные | |||||||||||||||||||||||||||||||||||||||||||||||
НВ | 100-120 | 120-140 | 140-160 | 160-180 | 180-200 | ||||||||||||||||||||||||||||||||||||||||||
КМр | 0,84 | 0,92 | 1,0 | 1,07 | 1,14 | ||||||||||||||||||||||||||||||||||||||||||
10.3. КСр — коэффициент, учитывающий влияние состояния обрабатываемого материала | |||||||||||||||||||||||||||||||||||||||||||||||
Обрабатываемый материал и его состояние | КСр | ||||||||||||||||||||||||||||||||||||||||||||||
Стали горячекатаные, улучшенные, отожженные, нормализованные | 1,0 | ||||||||||||||||||||||||||||||||||||||||||||||
Стали холоднотянутые | 0,8 | ||||||||||||||||||||||||||||||||||||||||||||||
Стали закаленные HRCЭ = 38-62 | 1,3-1,5 | ||||||||||||||||||||||||||||||||||||||||||||||
Стали наплавленные HRCЭ = 30-55 | 1,8 | ||||||||||||||||||||||||||||||||||||||||||||||
Чугуны | 1,0 | ||||||||||||||||||||||||||||||||||||||||||||||
10.4. КφР — коэффициент, учитывающий влияние главного угла резца в плане | |||||||||||||||||||||||||||||||||||||||||||||||
Обрабатываемый материал | Угол φ° | ||||||||||||||||||||||||||||||||||||||||||||||
30 | 45 | 60 | 75 | 90 | 95- 100 | ||||||||||||||||||||||||||||||||||||||||||
Сталь | КφР | 1,08 | 1,0 | 0,98 | 1,03 | 1,08 | 1,15 | ||||||||||||||||||||||||||||||||||||||||
Чугун | 1,05 | 1,0 | 0,96 | 0,94 | 0,92 | 0,9 | |||||||||||||||||||||||||||||||||||||||||
10.5. КrР — коэффициент, учитывающий влияние радиуса при вершине резца | |||||||||||||||||||||||||||||||||||||||||||||||
Обрабатываемый материал | Радиус r, мм | ||||||||||||||||||||||||||||||||||||||||||||||
0,5-0,6 | 0,8-1,0 | 1,5 | 2,0 | ||||||||||||||||||||||||||||||||||||||||||||
Сталь | Кrр | 0,87 | 0,93 | 0,97 | 1,00 | ||||||||||||||||||||||||||||||||||||||||||
Чугун | 0,91 | 0,95 | 0,98 | 1,00 | |||||||||||||||||||||||||||||||||||||||||||
10.6. КλР — коэффициент, учитывающий влияние переднего угла резца*) | |||||||||||||||||||||||||||||||||||||||||||||||
Угол λ° | -30 | -20 | -15 | -10 | -5 | 0 | 5 | 10 | 15 | 20 | |||||||||||||||||||||||||||||||||||||
КλР | 1,7 | 1,5 | 1,4 | 1,3 | 1,23 | 1,13 | 1,06 | 1,0 | 0,94 | 0,89 |
*) при наличии на передней поверхности фаски шириной f ≥ 3.s коэффициент КλР принимается по переднему углу на фаске. При ширине фаски f < 3.s — по переднему углу за фаской
10.7. КvP — коэффициент, учитывающий влияние скорости резания | |||||||||
V, м/мин, до | 50 | 100 | 150 | 200 | 250 | 300 | 400 | 500 | |
КvP | 1,00 | 0,89 | 0,83 | 0,79 | 0,76 | 0,73 | 0,70 | 0,67 | |
10.8. КсожР — коэффициент, учитывающий влияние смазывающе-охлаждающей жидкости (СОЖ) | |||||||||
Вид СОЖ | КсожР | ||||||||
Без СОЖ | 1,00 | ||||||||
Эмульсия водная | 0,95 | ||||||||
Эмульсия активированная | 0,85 |
studfiles.net
Режимы резания при токарной обработке – таблица расчета скорости
Обработка металлических и иных поверхностей с помощью токарного станка стала неотъемлемой частью повседневной жизни в индустрии. Многие технологии видоизменились, некоторые упростились, но суть осталась прежняя – правильно подобранные режимы резания при токарной обработке обеспечивают необходимый результат. Процесс включает в себя несколько составляющих:
- мощность;
- частота вращения;
- скорость;
- глубина обработки.
Ключевые моменты изготовления
Существует ряд хитростей, которых необходимо придерживаться во время работы на токарном станке:
- фиксация заготовки в шпиндель;
- точение с помощью резца необходимой формы и размера. Материалом для металлорежущих основ служит сталь или иные твердосплавные кромки;
- снятие ненужных шаров происходит за счет разных оборотов вращения резцов суппорта и непосредственно самой заготовки. Иными словами, создается дисбаланс скоростей между режущими поверхностями. Второстепенную роль играет твердость поверхности;
- применение одной из нескольких технологий: продольная, поперечная, совмещение обеих, применение одной из них.
Виды токарных станков
Под каждую конкретную деталь используется тот или иной агрегат:
- винторезно-токарные: группа станков, пользующихся наибольшей востребованностью при изготовлении цилиндрических деталей из черных и цветных металлов;
- карусельно-токарные: виды агрегатов, применяемых для вытачивания деталей. Особенно больших диаметров из металлических заготовок;
- лоботокарный станок: позволяет вытачивать детали цилиндрической и конической форм при нестандартных габаритах заготовки;
- револьверно-токарная группа: изготовление детали, заготовка которой представлена в виде калиброванного прудка;
- ЧПУ – числовое программное управление: новый вид оборудования, позволяющий с максимальной точностью обрабатывать различные материалы. Достичь подобного специалисты могут с помощью компьютерной регулировки технических параметров. Точение происходит с точностью до микронных долей миллиметра, что невозможно увидеть или проверить невооруженным глазом.
Подбор режимов резания
Режимы работы
Заготовка из каждого конкретного материала требует соответствия режима резки при токарной обработке. От правильности подборки зависит качество конечного изделия. Каждый профильный специалист в своей работе руководствуется следующими показателями:
- Скорость, с которой вращается шпиндель. Главный акцент делается на вид материала: черновой или чистовой. Скорость первого несколько меньше, нежели второго. Чем выше обороты шпинделя, тем ниже подача резца. В противном случае плавление металла неизбежно. В технической терминологии это называется «возгорание» обработанной поверхности.
- Подача – выбирается в пропорциональном соотношении со скоростью шпинделя.
Резцы подбираются исходя из вида заготовки. Выточка с помощью токарной группы самый распространенный вариант, несмотря на наличие иных видов более совершенного оборудования.
Это обосновывается невысокой стоимостью, высокой надежностью, длительным сроком эксплуатации.
Как вычисляется скорость
В инженерной среде расчет режимов резания исчисляют с помощью следующей формулы:
V = π * D * n / 1000,
где:
V – скорость резки, исчисляемая в метрах за минуту;
D – диаметру детали или заготовки. Показатели следует преобразовать в миллиметры;
n – величина оборотов за минуту времени обрабатываемого материала;
π – константе 3,141526 (табличное число).
Иными словами, скорость резания это тот отрезок пути, который проходит заготовка за минуту времени.
Например, при диаметре 30 мм скорость резки будет равна 94 метра за минуту.
При возникновении необходимости вычислить величину оборотов, при условии определенной скорости, применяется следующая формула:
N = V *1000/ π * D
Эти величины и их расшифровка уже известны по предыдущим операциям.
Дополнительные материалы
Во время изготовления, большинство специалистов руководствуются в качестве дополнительного пособия, приведенными ниже показателями. Таблица коэффициента прочности:
Материал заготовки | Граница прочности | Шкала твердости по Бринеллю | Коэффициент, МПа |
легированная и углеродистая сталь | варьируется от 400–1100 единиц | – | 1500–2600 |
чугун, а также серый | – | 1400–2200 | 1000–1200 |
бронза | – | – | 600 |
силумин | – | – | 450 |
дуралюмин | предел прочности от 250 до 350, но часто встречается и выше в зависимости от качества заготовки | – | 600–1100 |
Коэффициент прочности материала:
Сталь, кг/мм | Значение показателя |
50,1–60,1 | 1,61 |
60,1–70,3 | 1,27 |
70,3–80,1 | 1,1 |
80,3–90,1 | 0,87 |
90,3–100,1 | 0,73 |
Чугун, кг/мм | Значение показателя |
140,1–160,3 | 1,50 |
160,1–180,1 | 1,21 |
180,1–200,3 | 1,1 |
200,3–220,3 | 0,83 |
Коэффициент стойкости резца:
Значение стойкости, минуты | Показатель |
27–30 | 1,27 |
43–46 | 1,11 |
57–60 | 1,09 |
83–90 | 1,03 |
Третий способ вычисления скорости
- V фактическое = L * K*60/T резания;
- где L – длина полотна, преображенная в метры;
- K – количество оборотов за время резания, исчисляемое в секундах.
Например, длина равна 4,4 метра, 10 оборотов, время 36 секунд, итого.
Скорость равна 74 оборота в минуту.
Видео: Понятие о процессе резания
promzn.ru
Обработка заготовок на станках токарной группы
КРАТКАЯ ХАРАКТЕРИСТИКА СТАНКОВ ТОКАРНОЙ ГРУППЫ
Объединяющим признаком для станков этой группы служит то, что все они предназначаются преимущественно для обработки тел вращения. Основным инструментом для этих станков является резец. Ему сообщается движение подачи, главное движение получает заготовка.
Наиболее многочисленным типом станков рассматриваемой группы являются токарные и токарно-винторезные, позволяющие выполнять различные токарные работы, а токарно — винторезные станки, кроме того, — и нарезание резьбы.
Основными размерными характеристиками токарных станков является: высота центров и расстояние между центрами. Высота центров над станиной определяет наибольший радиус заготовки, которую можно обрабатывать на станке, а расстояние между центрами — наибольшую длину ее.
Токарные станки подразделяются на мелкие с высотой центров до 150 мм, средние с высотой центров 150 — 300 мм и крупные, у которых высота центров свыше 300 мм.
Токарно — револьверные станки предназначаются для обработки деталей, имеющих сложную геометрическую форму. Они позволяют работать различными инструментами, закрепляемыми как в суппорте, так и в поворотной головке.
Револьверные станки характеризуются наибольшим диаметром обрабатываемого прутка (на него указывают две последние цифры в обозначении модели станка) и наибольшим диаметром обработки.
Для обработки крупных деталей применяются карусельные станки, где деталь крепится на планшайбе, вращающейся вокруг вертикальной оси, а резец перемещается относительно заготовки. Диаметр планшайбы определяет наибольший размер обрабатываемой детали, а потому является для карусельных станков основным размерным параметром.
Многорезцовые станки позволяют одновременно обрабатывать ряд ступеней детали резцами, закрепленными в переднем и заднем суппортах, что значительно повышает производительность обработки.
Токарные автоматы и полуавтоматы применяются для массового изготовления разнообразных деталей. У автоматов автоматизированы все основные и вспомогательные движения. Функция рабочего состоит лишь в наблюдении за работой станка и периодической загрузке его прутками или штучными заготовками, засыпанными в бункер. Автоматы бывают одношпиндельные и многошпиндельные.
У полуавтоматов рабочий только устанавливает заготовку и снимает готовую деталь. Все остальные движения выполняет станок без его участия.
Основной размерной характеристикой для автоматов и полуавтоматов является наибольший диаметр обрабатываемого прутка или штучной заготовки.
УСТРОЙСТВО ТОКАРНО — ВИНТОРЕЗНОГО СТАНКА. МЕХАНИЗМЫ ГЛАВНОГО ДВИЖЕНИЯ
Основной несущей деталью токарно — винторезного станка (рис. 1) является станина 20. Она представляет собой массивную чугунную отливку коробчатого сечения с ребрами жесткости внутри. Верхние плоскости станины — направляющие – тщательно обрабатываются. Две наружные направляющие служат для перемещения по ним суппорта, а две внутренние — для установки и перемещения задней бабки.
Рисунок 1 – Общий вид токарно – винторезного станка модели 1К62
Станина покоится на двух тумбах : в передней Б располагается электродвигатель, в задней Д — сменные детали и привод системы охлаждения. Между тумбами под станиной располагается поддон К, куда сливается охлаждающая жидкость и собирается стружка.
С левой стороны станины прикрепляется передняя бабка I (коробка скоростей). В ее корпусе располагаются система зубчатых колес и другие механизмы для передачи вращательного движения на шпиндель и изменения числа оборотов его. Приводной шкив передней бабки получает вращение от электродвигателя через ременную передачу.
Шпиндель является наиболее ответственной деталью привода главного движения. Он изготавливается с большой точностью и располагается строго параллельно направляющим станины. Передний конец шпинделя имеет резьбу, на которую наворачивается трехкулачковый или четырехкулачковый токарный патрон 3 либо планшайба, служащие для закрепления обрабатываемых деталей. Кроме того, в передней части шпинделя имеется конусное отверстие, куда вставляется передний центр, служащий для установки деталей большой длины. Длинные заготовки устанавливаются между центрами, один из которых крепится в передней, а второй -в задней бабке.
Переключение числа оборотов шпинделя и направления его вращения выполняются с помощью рукояток управления 2, расположенных в передней части коробки скоростей.
С правой стороны станины располагается задняя бабка Д. Корпус 11 задней бабки установлен на основании, имеющем в нижней части направляющие для перемещения по направляющим станины. Корпус может смещаться по основанию в поперечном направлении, что нужно для обработки на станке конусов.
В верхней части корпуса при помощи маховичка 12, насаженного на винт, перемещается пиноль 10, имеющая коническое отверстие. Она предназначается либо для установки заднего центра при обработке в центрах, либо для закрепления и подачи инструментов для обработки отверстий — сверл, зенкеров, разверток.
МЕХАНИЗМ ДВИЖЕНИЯ ПОДАЧИ ТОКАРНО -ВИНТОРЕЗНОГО СТАНКА
Движение подачи в токарно — винторезном станке передается от шпинделя через промежуточные зубчатые колеса, дающие возможность изменять направление вращения последующих валов без изменения вращения шпинделя (реверсивный механизм), движение передается на гитару А, а с нее на коробку подач. Гитара состоит обычно из четырех сменных зубчатых колес. Подбирая любые сочетания их из имеющегося набора и устанавливая на гитару, можно в очень широких пределах получать различные подачи, что бывает необходимо обычно при нарезании разнообразных резьб.
Коробка подач Л имеет ряд механизмов с зубчатыми колесами и муфтами, переключая которые при помощи рукояток 18 можно передать вращательное движение с различным числом оборотов либо на ходовой винт, либо на ходовой валик 5.
Ходовой винт или ходовой валик передает движение фартуку И, который преобразует вращательное движение винта и валика в поступательное перемещение суппорта.
Ходовой винт используется в случае нарезания резьбы. Для этого в фартуке имеется разъемная (так называемая маточная) гайка. При включении гайки она соединяется с резьбой ходового винта и при его вращении движется вдоль винта. Так как гайка установлена в фартуке, то такое же перемещение получает и он.
При токарных работах фартук получает движение от ходового валика. Через несколько пар зубчатых колес и червячную передачу вращение передается реечному зубчатому колесу. Вращаясь, реечное зубчатое колесо катится по рейке, неподвижно укрепленной на станине, и фартук движется поступательно вдоль направляющих станины. Инструмент получает продольную подачу.
От механизмов фартука может получить вращение — также винт поперечной подачи, расположенный в суппорте, тогда инструмент будет перемещаться в поперечном направлении — перпендикулярно к направляющим станины.
Суппорт Г служит для установки и подачи резцов. Нижняя его часть — каретка 4, соединенная с фартуком, перемещается по направляющим станины. Сверху она имеет направляющие типа «ласточкин хвост» для поперечных салазок, получающих поперечную подачу. На поперечных салазках 5 укрепляется поворотная часть суппорта 6, позволяющая устанавливать инструмент под углом при обработке коротких конусов. Поворотная часть имеет сверху направляющие для продольного ручного перемещения верхних салазок 10. На них устанавливается четырехпозиционный поворотный резцедержатель 6, дающий возможность закреплять четыре различных резца и вести ими последовательно обработку детали. Откидывающийся козырек предохраняет рабочего от отлетающей стружки.
ТОКАРНО — ВИНТОРЕЗНЫЙ СТАНОК IK62 КИНЕМАТИЧЕСКАЯ СХЕМА ЦЕПЬ ГЛАВНОГО ДВИЖЕНИЯ
Токарно — винторезный станок модели 1K62 (рис. 1) является быстроходным с числом оборотов шпинделя в минуту до 2000, с набором подач — ( до 4,16 мм/об ), что позволяет более полно использовать возможности инструментов, оснащенных пластинками твердого сплава, и уменьшить машинное время.
В станке малое количество рукояток управления (коробки скоростей и подач имеют по две рукоятки, рабочие и холостые перемещения суппорта включаются одной рукояткой ), для быстрого подвода и отвода суппорта ему сообщается также ускоренное перемещение от отдельного электродвигателя, на суппорте установлен быстродействующий резцедержатель.
Для ознакомления с механизмами, станка рассмотрим его кинематическую схему (рис. 2).
Рисунок 2 – Кинематическая схема токарно – винторезного станка
Кинематической называется схема, дающая представление о передаче движения в станке или механизме. Детали и передачи показываются на ней условными обозначениями и не в масштабе. Пользуясь кинематической схемой, можно выяснить возможные варианты настройки станка на различные режимы работы. Цепь главного движения получает вращение от электродвигателя мощностью 10 кВт с числом оборотов 1450 об/мин.Через клиноременную передачу со шкивами диаметром 142 и 254 мм получает вращение вал I и сидящая на нем двусторонняя муфта M1. При включении ее влево через зубчатые колеса 56 — 34 ( цифры указывают число их зубьев) или 51 — 39 движение передается на вал II. включение одной из этих пар зубчатых колес и изменение за счет этого числа оборотов вала II осуществляется за счет передвижения вдоль зала блока Б1. В случае включения муфты вправо, передача на вал II идет через зубчатые колеса 53 — 21 — 36 — 38, и он получает вращение в противоположном направлении. Таким образом, муфта М1 изменяет направление вращения валов, а в конечном счете и шпинделя.
На валу III расположен блок из трех зубчатых колес Б2. Он может попеременно включаться с колесами 29, 21 и 38, сидящими на валу II, и передача на вал III может идти через одну из пар зубчатых колес 29 — 47, 21 — 55 или 38 — 38, что дает три различных числа оборотов. В итоге за счет переключения блоков Б1 и Б2- вал III получает шесть скоростей. С вала III при включении двойного блока Б5 влево движение через колеса 65 — 43 непосредственно передается на шпиндель VI. Когда блок Б5; включается вправо (зубчатые колеса 27 — 54 ), вращение на шпиндель передается через перебор, дающий шпинделю замедленное движение. Он включает валы IV и V с расположенными на них двойными блоками Б3 и Б4, зубчатыми колесами 27, 88, 45, а также зубчатые колеса 22 и 45 на валу III.
С учетом того, что некоторые числа оборотов повторяются, станок модели 1K62 при работе без перебора и с перебором позволяет придать шпинделю 23 различных числа оборотов.
МЕХАНИЗМ ДВИЖЕНИЯ ПОДАЧИ СТАНКА 1K62
От шпинделя зубчатыми колесами 60 — 60 при включении блока Б6 влево или колесами 45 — 45 при включении блока Б6 вправо вращение через двухскоростной реверсивный механизм, состоящий из зубчатых колес 42, 28 и 35 на валу VП, тройного блока Б7 с зубчатыми колесами 42, 56 и 35 и промежуточной шестерни 28, передается на устройство, которое называется гитарой.
Гитара имеет два сменных блока C1 и С2 и промежуточное колесо 95. Положение зубчатых колес гитары, указанное на схеме, т.е. передача движения через колеса 42 — 95 — 50, применяется для получения, механической подачи и при нарезании метрических и дюймовых резьб. Для нарезания резьб блоки поворачивают и вращение коробки подач сообщается зубчатыми колесами 64-95-97. В случае нарезания точных резьб и резьб со специальным шагом настройка гитары осуществляется подбором чисел зубьев сменных колес из имеющегося набора.
Коробка подач имеет механизм с конусным блоком зубчатых колес и четырехступенчатый множительный механизм.
Механизм с конусным блоком состоит из семи зубчатых колес 26, 28, 32, 36, 40, 44 и 46, расположенных на валу XI, и узла с накидной шестерней 36, получающей вращение от вала X через зубчатые колеса 28 и 25. Перемещая этот узел вдоль вала X и сцепляя накидную шестерню с одним из колес конусного блока, можно получить семь различных чисел оборотов.
Множительный механизм имеет два двойных блока зубчатых колес Б8 и Б9, переключая которые, можно получить четыре различных числа оборотов.
Путем переключения муфт М2, М3, М4 и М5 можно передавать, вращение по различным кинематическим цепям.
Фартук имеет также ручную продольную подачу : при вращении маховичка, сидящего на валу XX, через зубчатые колеса 14 — 66 вращение передается реечной шестерне. Ручная поперечная подача выполняется вращением вручную винта XXIII.
ОБРАБОТКА НА ТОКАРНЫХ СТАНКАХ
На токарных станках можно выполнять разнообразные работы, вести как черновую, так и чистовую обработку деталей.
При черновой обработке (обдирочные работы) снимается основной припуск с поверхности детали. Разработка ведется с большой глубиной резания и большими подачами. При обдирочных операциях получают обычно 5 -й класс точности и 2 — 3 классы чистоты поверхности.
При чистовой обработке снимается минимальный припуск. Работа ведется с малыми подачами. При этом достигается 4-й класс точности и 4 — 6 классы чистоты поверхности.
Рисунок 3 – Токарные резцы
Как известно, основным инструментом для токарных работ служит резец. Токарные резцы (рис. 3) изготавливаются из быстрорежущей стали. Они оснащаются пластинками из металлокерамических твердых сплавов и минералокерамики. Пластинки твердого сплава либо припаиваются к державке, изготовленной из конструкционной стали, либо крепятся к ней механически. Механическое крепление пластинок используется и для пластинок минералокерамики (рис. 3, м).
По форме головки резцы подразделяются на прямые (рис. 3а ) и отогнутые (рис. 3,б). У первых стержень прямолинейный, у вторых отогнут влево или вправо.
По расположению режущей кромки различает правые (рис. 3, в) и левые (рис. 3, г) резцы; правые резцы при обработке перемещаются от задней бабки к передней, левые — от передней бабки к задней.
По виду выполняемых работ токарные резцы могут быть проходными (рис. 3, а — г ), проходными упорными (рис. 3,д), подрезными (рис. 3, е), канавочными (рис. 3, д), отрезными (рис. 3, в), расточными (рис. 3, и), резьбовыми (рис. 3, к) и фасонными (рис. 3, л).
Помимо резцов, на токарных станках для обработки отверстий применяют также сверла, зенкеры, развертки для нарезания резьб — метчики и плашки.
ВИДЫ ТОКАРНЫХ РАБОТ
Обтачиванием наружных поверхностей можно получить гладкие и ступенчатые цилиндрические, конические и фасонные поверхности.
Для обработки цилиндрической поверхности заготовка крепится либо в патроне либо в центрах и получает вращательное движение.
При обработке в центрах на деталь надевается хомутик, вращаемый поводковой планшайбой. Обработка ведется проходным резцом: прямым, отогнутым или, если нужно получить уступ, (ступень ), упорным. Инструмент получает продольную подачу.
Чтобы заготовка большой длины не прогибалась, применяются специальные приспособления люнеты: подвижной, устанавливаемый на каретке суппорта и движущийся вместе с ней, и неподвижный, крепящийся на станине. При работе в центрах на заготовке закрепляется хомутик, а крутящий момент передается ему поводковой планшайбой.
Конические поверхности получаются при обтачивании в том случае, когда проходной резец получает перемещение под нужным углом к заготовке. Это можно осуществить либо наклоном инструмента по отношению к оси заготовки за счет поворота верхней части суппорта ( применяется для обработки коротких конусов ), либо поворотом заготовки посредством смещения в поперечном направлении задней бабки ( применяется при обработке длинных конусов ) , либо дав резцу одновременно продольную и поперечную подачу.
Фасонные детали получают при обтачивании заготовок фасонными резцами, заточенными по форме обрабатываемой поверхности, или при работе проходными резцами по копиру. В последнем случае салазки связываются с копиром, и резец копирует его профиль. Этим же способом, придав копиру форму плоской линейки, можно обтачивать также и конусы.
Растачиванием получают цилиндрические, конические и фасонные отверстия. Для этого, укрепив сверло в пиноли задней бабки, а заготовку в патроне, сверлят отверстие. Затем ему придают нужные форму и размеры с помощью расточных резцов. Вместо растачивания применяют также зенкерование и развертывание.
Подрезанием обрабатывают торцевые поверхности у валиков, втулок, плоскости в корпусных деталях. Оно выполняется подрезными резцами, получающими поперечную подачу.
При поперечной подаче производят также прорезание канавок и отрезание заготовок канавочными или отрезными резцами.
Резьбу можно нарезать резьбовыми резцами на токарно — винто-резных станках. Резец имеет форму впадины между витками. Для нарезания резьбы кинематическая цепь подачи настраивается так, чтобы за один оборот заготовки резец получил продольное перемещение на величину шага резьбы.
studfiles.net
Режим резания при токарной обработке: элементы и понятие резания
Одним из многофункциональных способов обработки металлов является точение. С его помощью осуществляется черновая и чистовая отделка в процессе изготовления или ремонта деталей. Оптимизация процесса и эффективная качественная работа достигается путем рационального подбора режимов резания.
Особенности процесса
Токарная отделка осуществляется на специальных станках с помощью резцов. Главные движения выполняются шпинделем, который обеспечивает вращение закрепленного на нем объекта. Движения подачи совершаются инструментом, который закреплен в суппорте.
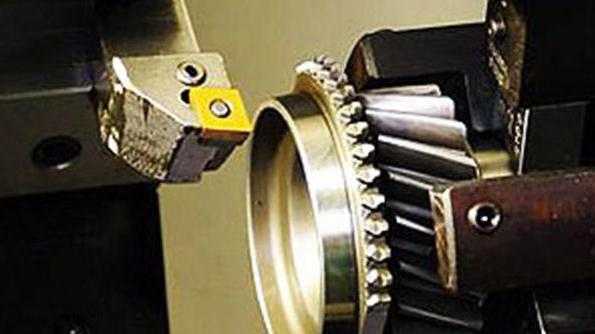
К основным видам характерных работ относятся: торцевое и фасонное обтачивание, растачивание, обработка углублений и канавок, подрезание и отрезание, оформление резьбы. Каждый из них сопровождается производительными движениями соответствующего инвентаря: проходных и упорных, фасонных, растачивающих, подрезных, отрезных и резьбовых резцов. Разнообразный типаж станков позволяет обрабатывать мелкие и очень крупные объекты, внутренние и внешние поверхности, плоские и объемные заготовки.
Основные элементы режимов
Режим резания при токарной обработке – это комплекс параметров работы металлорежущего станка, направленный на достижение оптимальных результатов. К ним относятся следующие элементы: глубина, подача, частота и скорость вращения шпинделя.
Глубина – это толщина металла, снимаемая резцом за один проход (t, мм). Зависит от заданных показателей чистоты и соответствующей шероховатости. При черновом точении t = 0,5-2 мм, при чистовом — t = 0,1-0,5 мм.
Подача – расстояние перемещения инструмента в продольном, поперечном или прямолинейном направлении относительно одного оборота обрабатываемой детали (S, мм/об). Важными параметрами для ее определения являются геометрические и качественные характеристики токарного резца.
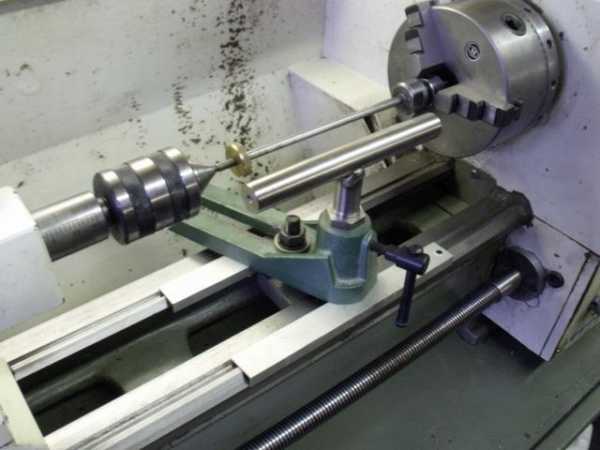
Частота вращения шпинделя – количество оборотов главной оси, к которой крепится заготовка, осуществляемое за период времени (n, об/с).
Скорость – ширина прохода за одну секунду с соответствием заданной глубины и качества, обеспеченная частотой (v, м/с).
Сила точения – показатель расходуемой мощности (P, Н).
Частота, скорость и сила – важнейшие взаимосвязанные элементы режима резания при токарной обработке, которые задают и оптимизационные показатели отделки конкретного объекта, и темп работы всего станка.
Исходные данные
С точки зрения системного подхода процесс точения можно рассматривать как слаженное функционирование элементов сложной системы. К ним относятся: токарный станок, инструмент, заготовка, человеческий фактор. Таким образом, на эффективность этой системы влияет перечень факторов. Каждый из них учитывается тогда, когда необходимо рассчитать режим резания при токарной обработке:
- Параметрические характеристики оборудования, его мощность, тип регулирования вращения шпинделя (ступенчатое или бесступенчатое).
- Способ крепления заготовки (с помощью планшайбы, планшайбы и люнета, двух люнетов).
- Физические и механические свойства обрабатываемого металла. Учитывается его теплопроводность, твердость и прочность, тип производимой стружки и характер ее поведения относительно инвентаря.
- Геометрические и механические особенности резца: размеры углов, державки, радиус при вершине, размер, тип и материал режущей кромки с соответствующей теплопроводностью и теплоемкостью, ударной вязкостью, твердостью, прочностью.
- Заданные параметры поверхности, в том числе ее шероховатость и качество.
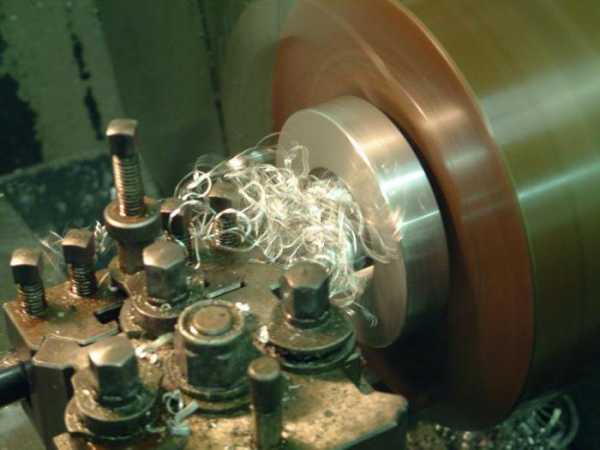
Если все характеристики системы учтены и рационально просчитаны, становится возможным достижение максимальной эффективности ее работы.
Критерии эффективности точения
Детали, изготавливаемые с помощью токарной отделки, являются чаще всего составляющими ответственных механизмов. Требования выполняются с учетом трех основных критериев. Наиболее важным является максимальное выполнение каждого из них.
- Соответствие материалов резца и обтачиваемого объекта.
- Оптимизация между собой подачи, скорости и глубины, максимальная производительность и качество отделки: минимальная шероховатость, точность форм, отсутствие дефектов.
- Минимальные затраты ресурсов.
Порядок расчета режима резания при токарной обработке осуществляется с высокой точностью. Для этого существует несколько различных систем.
Способы вычисления
Как уже было сказано, режим резания при токарной обработке требует учета большого количества разных факторов и параметров. В процессе развития технологии многочисленные ученые умы разработали несколько комплексов, направленных на вычисление оптимальных элементов режимов резания для различных условий:
- Математический. Подразумевает точный расчет по существующим эмпирическим формулам.
- Графоаналитический. Совмещение математического и графического методов.
- Табличный. Выбор значений, соответствующих заданным условиям работы, в специальных комплексных таблицах.
- Машинный. Использование программного обеспечения.
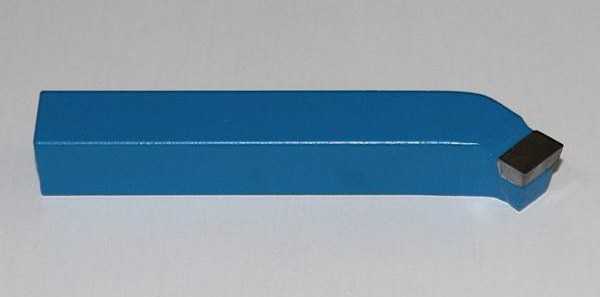
Наиболее подходящий выбирается исполнителем в зависимости от поставленных задач и массовости производственного процесса.
Математический метод
Аналитически вычисляются режимы резания при токарной обработке. Формулы существуют более и менее сложные. Выбор системы определяется особенностями и требуемой точностью результатов просчетов и самой технологии.
Глубина рассчитывается как разность толщины заготовки до (D) и после (d) обработки. Для продольных работ: t = (D — d) : 2; а для поперечных: t = D — d.
Допустимая подача определяется поэтапно:
- цифры, которые обеспечивают необходимое качество поверхности, Sшер;
- подача с учетом характеристик инструмента, Sр;
- значение параметра, учитывающее особенности закрепления детали, Sдет.
Каждое число вычисляется по соответствующим формулам. В качестве фактической подачи выбирают наименьшую из полученных S. Также существует обобщающая формула, учитывающая геометрию резца, заданные требования к глубине и качеству точения.
- S = (Cs*Ry*ru) : (tx*φz2), мм/об;
- где Cs – параметрическая характеристика материала;
- Ry – заданная шероховатость, мкм;
- ru – радиус при вершине токарного инструмента, мм;
- tx – глубина точения, мм;
- φz – угол при вершине резца.
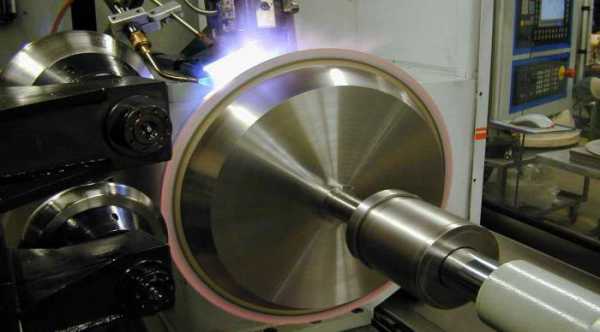
Скоростные параметры вращения шпинделя считаются по различным зависимостям. Одна из фундаментальных:
v = (Cv*Kv) : (Tm*tx*Sy), м/мин, где
- Cv – комплексный коэффициент, обобщающий материал детали, резца, условия процесса;
- Kv – дополнительный коэффициент, характеризующий особенности точения;
- Tm – стойкость инструмента, мин;
- tx – глубина резания, мм;
- Sy – подача, мм/об.
При упрощенных условиях и с целью доступности расчетов, скорость токарной обработки заготовки можно определить:
V = (π*D*n) : 1000, м/мин, где
- n – частота вращения шпинделя станка, об/мин.
Используемая мощность оборудования:
N = (P*v) : (60*100), кВт, где
- где P – сила резания, Н;
- v – скорость, м/мин.
Приведенная методика является очень трудоемкой. Существует большое разнообразие формул различной сложности. Чаще всего сложно правильно подобрать нужные, чтобы произвести расчет режимов резания при токарной обработке. Пример наиболее универсальных из них приведен тут.
Табличный метод
Суть этого варианта состоит в том, что показатели элементов находятся в нормативных таблицах в соответствии с исходными данными. Существует перечень справочников, в которых приведены значения подач в зависимости от параметрических характеристик инструмента и заготовки, геометрии резца, заданных показателей качества поверхности. Есть отдельные нормативы, вмещающие в себе предельно допустимые ограничения для различных материалов. Отправные коэффициенты, необходимые для расчета скоростей, также содержатся в специальных таблицах.
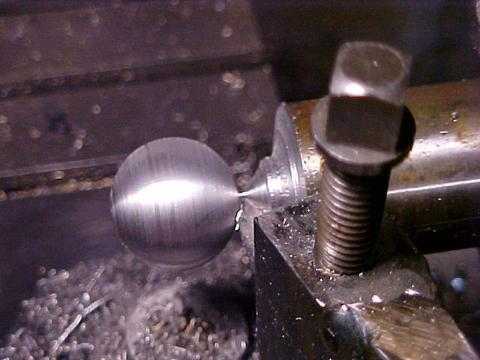
Такая методика используется обособленно или одновременно с аналитической. Она удобна и точна в применении для несложного серийного производства деталей, в индивидуальных мастерских и в домашних условиях. Она позволяет оперировать цифровыми значениями, используя минимум усилий и исходных показателей.
Графоаналитический и машинный методы
Графический способ является вспомогательным и основан на математических расчетах. Вычисленные результаты подач наносятся на график, где расчерчивают линии станка и резца и по ним определяют дополнительные элементы. Этот метод – очень сложная комплексная процедура, которая является неудобной для серийного производства.
Машинный способ – точный и доступный вариант для опытного и начинающего токаря, разработанный для того, чтобы вычислять режимы резания при токарной обработке. Программа предоставляет наиболее точные значения в соответствии с заданными исходными данными. Они обязательно должны включать:
- Коэффициенты, характеризующие материал обрабатываемой детали.
- Показатели, соответствующие особенностям инструментального металла.
- Геометрические параметры токарных резцов.
- Числовое описание станка и способов закрепления заготовки на нем.
- Параметрические свойства обрабатываемого объекта.
Сложности могут возникать на этапе числового описания исходных данных. Правильно задав их, можно быстро получить комплексный и точный расчет режимов резания при токарной обработке. Программа может содержать неточности работы, однако они менее значительны, чем при ручном математическом варианте.
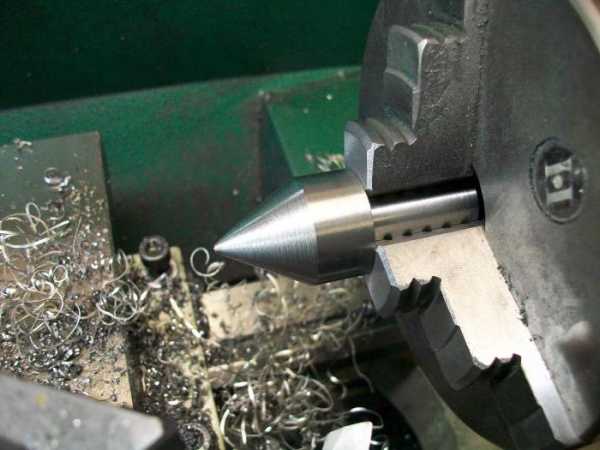
Режим резания при токарной обработке – важная расчетная характеристика, определяющая ее результаты. Одновременно с элементами выбираются инструменты и охлаждающе-смазывающие вещества. Полный рациональный подбор этого комплекса – показатель опытности специалиста или его упорности.
fb.ru
53. Элементы режима резания при точении.
К элементам режима резания при точении относят скорость резания, подачу и глубину резания. Совокупность этих величин называют режимом резания.
Скоростью резания v (м/мин) называется путь перемещения режущего лезвия инструмента относительно заготовки в направлении главного движения в единицу времени.
Если главное движение вращательное (точение), то скорость резания определяют по формуле:
v= (п·Dзаг·n)/1000,
где Dзаг — наибольший диаметр обрабатываемой заготовки, мм;n- частота вращения заготовки, об/мин.
Подачей S (мм/об) называется путь точки режущего лезвия инструмента относительно заготовки в направлении движения подачи за один оборот.
Глубиной резания t (мм) называется расстояние между обрабатываемой и обработанной поверхностями заготовки, измеренное перпендикулярно к последней, за один проход инструмента относительно обрабатываемой поверхности.
При наружном точении глубина резания определяется как полуразность диаметров до и после обработки:
t = (Dзаг –d)/2
54. Устройство токарно-винторезного станка.
Токарные станки предназначены для получения заготовок различных деталей, имеющих форму тел вращения. Их классифицируют на: специализированные, автоматы и полуавтоматы (одношпиндельные и многошпиндельные), сверлильно-отрезные, карусельные, токарные и лобовые, многорезцовые, разные токарные. На рис.23 изображен общий вид токарно – винторезного станка, указаны основные части, узлы и органы управления.
Ст а н и н а 8 – массивное чугунное
основание, на котором смонтированы все
основные части станка. Верхняя часть
станины имеет две плоские и две
призматические направляющие, по которым
могут перемещаться подвижные узлы
станка.
П е р е д н я я б а б к а 1 – чугунная коробка, внутри которой расположен главный рабочий орган станка – шпиндель, представляющий собой полый вал, на правом конце которого крепятся приспособления, зажимающие заготовку, например, патрон.
Шпиндель 2 получает вращение от расположенного в левой тумбе электродвигателя через клиноременную передачу и систему зубчатых колёс и муфт, размещенных внутри передней бабки. Механизм (т.е. система зубчатых колёс и муфт), который позволяет изменять числа оборотов шпинделя, называется коробкой скоростей.
С у п п о р т 3 — устройство для закрепления резца, обеспечения движения подачи, т. е. перемещения резца в различных направлениях. Движения подачи могут осуществляться вручную и механически. Механическое движение подачи суппорт получает от ходового винта и ходового вала . Ф а р т у к 12 — система механизмов, преобразующих вращательное движение ходового винта и ходового вала в прямолинейное движение суппорта.
К о р о б к а п о д а ч 14 — механизм, передающий вращение ходовому винту и ходовому валу и изменяющий величину подачи. Вращательное движение в коробку подач передается от шпинделя с помощью реверсивного механизма и гитары со сменными зубчатыми колесами . Г и т а р а 2 предназначается для настройки станка на требуемую подачу подбором соответствующих сменных зубчатых колес. . З а д н я я б а б к а 7 предназначена для поддерживания правого конца длинных заготовок в процессе обработки, а также закрепления свёрл, зенкеров, зенковок и разверток, метчиков и других инструментов.
studfiles.net