Стальная броня
Стальная броня
Лучшие образцы текстильной и органопластиковой брони позволяют обеспечить защиту по второму классу ГОСТ Р 50744-95 при поверхностной плотности защитной структуры 6…8 кг/м2. Для защиты от средств поражения, обладающих большей кинетической энергией (автоматные и винтовочные пули), необходимо использовать чисто металлические или комбинированные защитные структуры, включающие в себя металлические, композиционные или керамические бронеэлементы.
Металлическая броня как класс включает в себя броневые стали, высокопрочные алюминиевые и титановые сплавы. Наиболее широко используется стальная броня. С ее помощью возможно обеспечение защиты вплоть до пятого класса при толщине бронеэлемента 5,0…6,5 мм, что соответствует поверхностной плотности 39…51 кг/м~. Большие толщины стальных бронеэлементов недопустимы из-за их чрезмерно большого веса.
Броневая сталь представляет собой среднеуглеродистую, среднелегированную сталь мартенситного класса. Высокие прочностные характеристики броневых сталей для СИБ достигаются в результате термообработки, включающей в себя закалку на мартенсит и низкий отпуск. Для того чтобы получить представление о свойствах и структуре броневых сталей, коротко рассмотрим их состав и основные превращения, происходящие при термообработке [5.1].
Как известно, основой стали является сплав железа Fe с углеродом С. Железо имеет две полиморфные модификации а и у. Модификация Feα имеет ОЦК решетку и существует в двух интервалах температур: до 911 °С и 1392… 1539 °С. Модификация Feγ имеет ГЦК решетку и существует в интервале температуры от 911 °С до 1392 °С. ГЦК — решетка более компактна, чем ОЦК — решетка. В связи с этим при фазовом переходе а → γ объем железа уменьшается приблизительно на 1 %. Углерод при нормальных условиях существует в двух кристаллических модификациях (графит — стабильная модификация и алмаз — метастабильная модификация) и аморфной форме в виде сажи.
В составе стали железо и углерод присутствуют в виде растворов и химических соединений, представляющих собой следующие фазы: феррит, аустенит, цементит и графит.
Феррит (Ф, α) — твердый раствор внедрения С в Feα, имеет ОЦК — решетку. Растворимость углерода в ОЦК — решетке очень низкая: в низкотемпературном феррите — 0,02 %, в высокотемпературном — 0,1 %. Значительная часть атомов углерода вынуждена размещаться на дефектах решетки — вакансиях и дислокациях. Феррит, кроме углерода, растворяет и другие элементы. Азот образует твердый раствор внедрения, а металлы, которыми легируют стали, образуют твердые растворы замещения. Феррит — мягкая пластичная фаза, имеет следующие механические свойства: σв = 300 МПа, δ = 40 %, ψ = 70 %, НВ 80… 100.
Аустенит (А, γ) — твердый раствор внедрения С в Feγ, имеет ГЦК — решетку. Растворимость углерода в ГЦК — решетке достаточна большая и достигает 2,14 %. Аустенит пластичен, но более прочен, чем феррит. Твердость аустенита составляет НВ 160. ..200.
Цементит (Ц) — химическое соединение железа с углеродом Fe3C содержит 6,67 % углерода, имеет сложную ромбическую структуру с плотной упаковкой атомов. При нормальных условиях цементит весьма тверд (НВ 800) и хрупок. При высоких температурах цементит неустойчив и разлагается на аустенит и графит.
Графит — углерод, выделяющийся в свободном состоянии. Имеет гексагональную кристаллическую решетку, мало прочен, мягок (НВ 3).
Диаграмма состояния Fe — С имеет двойственный характер: 1) метастабильная диаграмма Fe — Fe3C; 2) стабильная диаграмма Fe — С. Для анализа состояния сталей важны обе диаграммы.
Если аустенит быстро переохладить, то вследствие превращения FeγB Feα образуется пересыщенный твердый раствор углерода в Fe a — мартенсит. Превращение является бездиффузионным (быстрым), углерод из раствора не выделяется. Мартенсит имеет особую пластинчатую структуру, его твердость очень высока и достигает HRC 65. Термообработка стали на структуру мартенсита называется закалкой. После закалки на мартенсит сталь становится хрупкой. Мартенсит является неравновесной структурой — при нагреве (отпуске) диффузионная подвижность атомов углерода возрастает и мартенсит начинает перестраиваться в смесь Ф + Ц. Задача отпуска мартенсита состоит в том, чтобы приблизить мартенсит к равновесной структуре. Чем выше температура отпуска Тотп, тем ближе структура стали к равновесной, сталь мягче, а ее хрупкость меньше. Различают низкий отпуск Тотп < 350…380 °С, в результате которого получают равновесную смесь Ф + Ц — тростит отпуска, и высокий отпуск Тотп= 400…650 °С, для которого характерно укрупнение (коагуляция) частиц цементита. Получающуюся в результате высокого отпуска структуру называют сорбитом отпуска. Для сорбита отпуска характерна достаточно высокая ударная вязкость.
Кроме термообработки, упрочнение сталей осуществляется путем их рационального легирования и с помощью термомеханической обработки (ТМО) — сочетанием термообработки с деформационным упрочнением.
Механизмы легирования сталей достаточно сложны и основываются на том, что легирующие элементы изменяют температуры полиморфных превращений железа, влияют на растворимость углерода в аустените и на химический состав сталей. При введении в состав сталей таких легирующих элементов как марганец и никель ГЦК — решетка аустенита становится устойчивой при комнатной температуре. Соответствующие стали называют аустенитными сталями. Эти стали характеризуются не только высокими значениями прочностных характеристик, но и обладают достаточно высокой ударной вязкостью и способностью к деформационному упрочнению. При введении в качестве легирующих элементов хрома, молибдена, вольфрама, ванадия, кремния и др. температурный интервал устойчивости аустенита уменьшается, и соответственно, возрастает температурный интервал устойчивости феррита. Перечисленные легирующие элементы способствуют увеличению предела текучести, предела прочности и твердости сталей.
При деформировании сталей (прокатка, штамповка, ковка и др.) происходит измельчение микроструктуры, увеличивается плотность дислокаций — структура становится более однородной. Мелкозернистый материал имеет более высокую прочность вследствие большей площади границ между зернами, являющихся естественным барьером для движения дислокаций. Связь между пределом текучести и характерным размером зерен выражается уравнением Холла-Петча [5.2]
Зависимость предела текучести на сдвигτт от плотности дислокаций описывается известным соотношением теории дислокаций
Таким образом, для увеличения прочности сталей следует стремиться к сверхмелкозернистой структуре, насыщенной дислокациями.
Влияние структурного фактора на пулестойкость броневых сталей показано на рис. 5.1 [5.3].
В средствах индивидуальной защиты применяются так называемые противопульные броневые стали высокой твердости, в которых в качестве легирующих элементов могут использоваться хром, никель, молибден, ванадий, кремний. Сложность создания таких сталей обусловлена необходимостью сочетания экстремально высоких значений твердости и прочности, обеспечивающих сопротивление прониканию пули, и достаточного уровня пластичности и вязкости для предотвращения хрупкого разрушения стального бронеэлемента. Как высокотвердые хрупкие, так и вязкие пластичные стали, обладающие невысокой твердостью, характеризуются низкой противопульной стойкостью.
В России основными серийными броневыми сталями, широко применяемыми в противопульной защите, являются среднелегированные стали марок «44», Ц-85, СПС-43, «96». Из новых разработок следует отметить стали «56», «44С» (разработчик НИИ стали) и Ф-110 (разработчик ММ3 «Серп и молот»). Прочность этих броневых сталей находится в пределах 1750…2300 МПа, твердость 50…58 HRC, относительное удлинение 8…12 % [5.4, 5.5]. Номинальная система легирования, способ получения и механические свойства некоторых высокотвердых броневых сталей, выпускаемых промышленностью, приведены в табл. 5.1 [5.5 — 5.11]. Сравнение механических характеристик броневых сталей с характеристиками среднеуглеродистых сталей показывает, что прочность броневых сталей определяется главным образом содержанием углерода.
Применяемые в СПБ бронеэлементы из стали «44» толщиной 5,5 мм обеспечивают защиту при обстреле «в упор» обычными пулями АКМ, АК74 и СВД. Для защиты от пуль с термоупрочненными сердечниками с твердостью, большей 60 HRC, требуется увеличение защищающей толщины бронеэлементов на 15.. .20 %.
Увеличить пулестойкость броневой стали можно было бы путем увеличения ее твердости. Однако при твердости преграды из гомогенной углеродистой броневой стали большей 55 HRC она становится хрупкой и при обстреле даже обычными стальными пулями поражается по типу пролома или раскола. Для того чтобы избежать этого, необходимо сохранить пластичность стали на уровне ψ = 30 %. В НИИ стали разработана сбалансированная по содержанию углерода и основных легирующих элементов сталь «44С», которая после электрошлаковой переплавки, прокатки и термообработки обладает твердостью 55… 57 HRC, прочностью σв =2250…2350 МПа, σ0,2= 2000…2100 МПа, относительным сужением ψ = 30 % [5.5]. Как показали испытания, баллистические характеристики этой стали находятся на уровне лучших зарубежных гомогенных броневых сталей марок MARS-300 (Франция), ARMOX- 600 (Швеция), 4340 TOD (США). Бронеэлементы из стали «44С» толщиной 6,5…6,6 мм в структуре бронежилета 6Б23 обеспечивают защиту от пуль 7Н22 и 7Н24 с термоупрочненными и твердосплавными сердечниками калибра 5,45 мм.
Влияние твердости стальной брони на толщину бронеэлементов, обеспечивающих защиту от пуль основного стрелкового оружия, показано на рис. 5.2 [5.5].
Одним из возможных путей повышения пулестойкости является создание биметаллической брони с внешним высокотвердым слоем 55…60 HRC и тыльным вязким слоем. Такую броню можно получить, например, сваркой взрывом, пакетной прокаткой или иными способами. В России серийного производства таких сталей пока не освоено, хотя за рубежом они используются достаточно широко.
В таблице 5.2. приведены характеристики некоторых таких сталей.
Смотрите также
Броневая сталь. Ramor
Броневая сталь. Ramor
Описание марки стали
В производстве броневой стали Ramor используется новый процесс прямой закалки. В результате использования этого метода сталь становится не только пуленепробиваемой, а также получает хорошую плоскостность, качество поверхности и точность размеров. Стали Ramor 400 разработаны для защиты от высокого давления, которое образуется при взрывахи взрывной волне.
Стали Ramor 500 — наиболее оптимальный выбор для защиты от кинетической энергии летящих объектов (противопульная защита). Цифровое обозначение в названии марки стали
говорит о средней твердости по Бринеллю 400 и 500 HBW, соответственно.
Виды продукции
Тяжелые толстые листы и листы.
Состояние поставки
В закаленном состоянии.
Размеры
Толщина листовой продукции — от 6 до 30 мм.
Листы с необрезанными кромками 2,5 – 6,5 мм
Допуски
Тяжелые толстые листы
Толщины показаны в Таблице 1.
Ширина и длина EN 10029.
Плоскостность EN 10029 класс N, тип стали H.
Листы
Толщины показаны в Таблице 1.
Ширина и длина EN 10051
Плоскостность EN 10029 класс N, тип стали H.
Качество поверхности
Соответствует стандарту EN 10 163-2 Класс В3. Не разрешается проводить ремонтную сварку толстых листов при производстве толстолистовой стали Ramor.
Основное техническое состояние поставки
Соответствует EN 10 021. При отсутствии иной договоренности сертификат на материал EN 10 204-2.2 выдается на английском языке.
Химический состав
Химический состав показан в Таблице 2.
Механические свойства
Типичные механические свойства представлены в Таблице 3
Испытания
Проведение испытания продемонстрировано в Таблице 4. Рекомендованные минимальные толщины толстых листов Ramor 500 для разных классов защиты показаны в Таблице 5.
Термическая обработка
Не рекомендуется осуществлять термическую обработку. Если необходима закалка, пожалуйста, обратитесь к техническому специалисту для получения консультации.
Сварка
Стали Ramor можно сваривать обычными способами. Рекомендуется использовать аустенитные сварочные материалы. Также можно использовать ферритные сварочные материалы, если важна прочность сварного шва. При использовании ферритных сварочных материалов необходимо определить необходимость увеличения рабочей температуры для того, чтобы сварной шов был без дефектов.
Гибка
При гибке в холодном состоянии сталей Ramor 500 минимальный радиус верхнего рабочего элемента должен быть в 8 раз больше толщины материала. Для Ramor 400 — в 5 раз больше толщины материала. Особое внимание необходимо обратить на безопасность труда. Механическая резка не подходит, как и обработка кромок для прошедших гибку компонентов.
Резка
Стали Ramor можно резать при помощи лазерной и плазменной резки. Можно использовать и механическую резку, если режущие лезвия достаточно прочные и твердые. Однако предпочтительно использовать водообразивную резку, так как этот способ позволяет сохранить баллистическую стойкость и на обрезных кромках.
Механическая обработка
Стали Ramor обрабатывают, используя надежное оборудование. Смазка должна быть обильной, особое внимание следует обращать на закрепление материала. Параметры механической обработки должны выбираться таким образом, чтобы избежать вибрации режущего инструмента и самого материала, поскольку вибрация значительно сокращает срок службы режущего инструмента.
Техника безопасности
С особой осторожностью следует обрабатывать закаленные стали. Отбортовка — сложная задача из-за высокой прочности и высокого изгибающего усилиялиста. Например, если радиус загиба слишком маленький, и трещина образовалась по линии загиба, лист может отскочить в сторону направления гибки. Осуществляющие гибку рабочие должны принять соответствующие меры предосторожности, чтобы обеспечить свою безопасность. В зоне работ не должны присутствовать посторонние. Самое безопасное место обычно находится у гибочного станка. Необходимо строго следовать инструкциям пообработке, которые составлены поставщиком стали, инструкциям по безопасности. Прежде чем новые сотрудники приступят к работе, они должны первоначально пройти соответствующее обучение.
Дополнительная информация
Дополнительную информацию можно получить из следующей технической документации: Сварка, Сварочные материалы; Термическая резка и правка газовым пламенем; Отбортовка и гибка; Механическая резка и механическая обработка.
www.gmzmetal.ru
Броневая сталь 44С-св-Ш. Военные технологии. informatik-m.ru
Как бы ни была хороша конструкция любой техники, она ничего не будет значить без соответствующих конструкционных материалов. Именно свойства материалов накладывают ограничения на конструкцию и определяют во многом характеристики изделия. Тем более это касается военной техники.
Танк «Армата» имеет настолько уникальные характеристики, что аналогов ему на сегодняшний день нет. Во многом его свойства, а именно сочетание огневой мощи, скорости и защищенности, зависят от его брони. Машина должна обладать как можно большей защищенностью от снарядов и мин, но при этом её масса не должна превышать заданных пределов. Это взаимоисключающие требования, и чаще всего единственным выходом является разработка новых конструкционных материалов. Для решения задач поставленных перед создателями «Арматы» была создана новая броневая сталь 44С-св-Ш, которая по своим показателям существенно превосходит ранее применявшиеся марки.
Чтобы понять особенности характеристик стали, достаточно воспользоваться аналогией с акустической техникой. Перед тем, как наушники beats купить, сначала знакомятся с их характеристиками. Для всех акустических систем есть универсальные показатели: диапазон частот, громкость, коэффициент искажений. Сопоставляя их со стоимостью, а также сроком эксплуатации, покупатель выбирает понравившуюся модель.
Подобным образом дела обстоят и со сталью. Важно чтобы броня обладала высокой твердостью и прочностью одновременно, сохраняла свои свойства и при высоких и при низких температурах севера. Это очень трудная задача. Твердость отражает способность материала сопротивляться изменению формы. А прочность отражает способность материала не разрушаться при определенных нагрузках. Прочность подразумевает определенную пластичность и упругость, однако при увеличении твердости эти свойства обычно снижаются за счет появления хрупкости (классический пример твердой стали - напильник). Для решения этой проблемы применяют либо многослойную структуру, как в боевых мечах, где крупные зерна одного слоя чередуются с мелкими зернами другого. Используются также определенные виды термообработки и наклеп. Однако это очень дорого и неприемлемо для материала такого изделия, как танк. Легирование (добавление в сталь дополнительных элементов) также может в определенной степени решить вопрос прочности и твердости, однако сталь не должна получиться слишком дорогой.
Создатели 44С-св-Ш, специалисты из ОАО «НИИ сталь» пошли по пути усовершенствования структуры стали. Её неоднородность во многом определяет несовершенство материала. Ученым удалось добиться прекрасного результата, создав ультрамелкозернистую структуру по всему объему. Это было достигнуто путем разработки новой технологии управления выплавкой стали.
Твердость новой броневой стали достигает значения 54HRC, при этом пластичность находится на уровне сталей марок 45-48HRC, обладающих значительно меньшей твердостью. Благодаря тому, что удалось совместить несовместимое, появилась возможность сделать новый российский танк Армата легче на 15-20%. Сталь 44С-св-Ш открыла новый этап в развитии бронетехники, переведя её на качественно новый уровень.
Комментарии: 1
informatik-m.ru
Броневая сталь — это… Что такое Броневая сталь?
В современных танках броневые листы расположены под углами к вертикали
Броня́ — защитный слой материала, обладающий достаточно большой прочностью, вязкостью и другими механическими параметрами, стоящими на высоком уровне показателей, выполняющий в том или ином случае функцию преграды от различного по силе и интенсивности воздействия на объект, окружаемый этим слоем. Понятие «броня» имеет довольно широкое толкование, но в целом основным значением является защита.
Другие значения
Броня в литейном производстве — средство защиты изнашивающихся частей модельного комплекса (стержни, ящики, опоки и др). На алюминиевых и деревянных стержневых ящиках броня выполняется из сталей (Сталь Ст3, Сталь 45 и др). Литейную броню привёртывают на борта литейных ящиков. Роль брони литейной так же выполняет наплавленный слой высокоизносостойкого сплава на вращающиеся части модельного комплекта (так называемая бронирующая вставка, ГОСТ 19367-74). Основным изготовителем брони, сталей и сплавов с высоким содержанием марганца, например 110Г13Л, является предприятие «Арсенал-Деталь» сайт http://arsenal-detal.ucoz.ru
История возникновения Брони
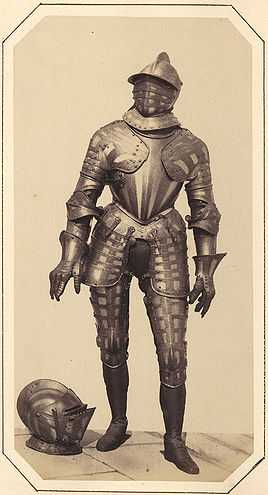
Прототипами Брони в древности были доспехи и щиты воинов. Главным назначением их была защита тела человека от воздействия на него оружия (стрел, копий, мечей и сабель). Главными материалами служили [ ], кожа, тонкие пластины металлов, кость, рог. По мере прогресса вооружений (появление арбалетов и первого огнестрельного оружия) требования к толщине и прочности материалов доспехов и щитов резко возросли. С появлением огнестрельного оружия, ростом числа военных конфликтов и интенсивности ведения боёв в прототипах брони начинают преобладать конструктивные элементы, изготовленные из железа и стали (Крестовые походы и, соответственно, культурно-технологический обмен). Одновременно снижается применение мягких и непрочных сплавов меди (латунь, бронза) и конструктивных элементов из дерева, кожи и рога. Вся совокупность прогресса в области военных технологий начинает превращаться в соревнование между оружием и защитой от него. Рост и интенсивность конфликтов огрубляют и упрощают форму доспехов и щитов к наиболее эффективной конструкции и снижения её стоимости (уменьшение количества украшений на доспехах и щитах). В дальнейшем широкое использование железа и стали увеличивается на военно-транспортных средствах (повозки, корабли, лодки) и на наземных укрепленных сооружениях. В историческом плане наблюдается увеличение толщины защитных оболочек и появление брони в современном смысле (например, танковая броня, бортовая броня кораблей и самолётов). Можно сказать, что создание брони резко ускорило прогресс в металлургии, термической и механической обработке металлов. В наши дни броня непрерывно совершенствуется и появляются её новые виды, но, как и прежде, она делится на несколько основных типов.
Виды и типы брони по назначению
Типы брони:
- Нательная: доспехи, надеваемые на тело человека (например, бронежилет).
- Транспортная: плиты из металлов и композиционных материалов, пуленепробиваемых стекол для защиты экипажа и пассажиров, активная броня.
- Корабельная: сплавы и композиты, активная броня, для защиты подводной и надводной части судов.
- Строительная: сплавы, супербетон, песок, пены и др. Защита зданий, военных сооружений (например, дот, дзот, блиндажи и др.).
- Космическая: экраны, зеркала.
Материалы для производства брони
Для производства брони используется широкий спектр конструкционных материалов, обладающих необходимыми механическими свойствами, главными из которых являются твёрдость, прочность, относительное удлинение, температура плавления, модуль упругости. В целом механические показатели материалов для производства брони должны находиться на высоком уровне. Материалы, применяемые наиболее широко для производства современной брони:
- Высокопрочные качественные стали с большой вязкостью и относительным удлинением: литые и кованые легированые стали.
- Дисперсионно упрочнённые сплавы меди: медная матрица.
- Высокопрочные титановые сплавы: титановая матрица плюс волокна.
- Высокопрочные композиты с бериллиевой матрицей.
- Композиционные материалы упрочненные волокнами металлов и нитевидными кристаллами.
- Взрывчатые вещества: для производства активной брони.
- Пластики, наполненные ориентированными волокнами углерода, оксида алюминия, волокнами бора и др.
- Пластики, упрочнённые высокопрочными волокнами и с распределёнными полостями, наполнеными водой или вязкими жидкостями («жидкая броня»).
- Высокопрочные стройматериалы: супербетон, водонаполненый бетон, специальные пены (гашение взрывных волн) и др.
Значение брони для защищаемых подвижных и неподвижных объектов
Броня имеет огромное значение для защиты объектов, техники, людей, в период ведения боевых действий (войн), учений (приближенных к боевым), испытаний новых видов вооружений. Применение брони повышает живучесть войск и армии, резко увеличивает способность к ведению боёв и обороны, так как предохраняет людей и технику от гибели, ранения, выхода из строя.
Эволюция технологии брони и новые разработки
Средства для поражения брони
Такими средствами являются мощные виды современного вооружения, обладающие значительной кинетической или тепловой энергией.
- Лёгкое переносное огнестрельное оружие с увеличенной мощностью: поражение доспехов (бронежилеты, шлемы и др.) на живой силе.
- Лёгкое переносное ракетное оружие: поражение брони летательных аппаратов, автомобилей, лёгких судов.
- Артиллерия: поражение брони спецсредств (танки, БТР, вертолёты, огневые укреплённые точки, военные суда).
- Торпеды: поражение надводной и подводной части плавательных средств, защищённых броней.
- Авиабомбы: поражение бронированных объектов (бункеры, доты, блиндажи и др.) и крупной бронированной техники.
- Лазерный луч: поражение удалённых целей из космоса или в космическом пространстве, а также поражение самолётов и наземных сооружений и техники.
- Плазма: стационарный оптический разряд в воздухе при самофокусировке или регулируемой фокусировке лазерного излучения (ещё в разработке).
- Звуковые волны: мощные импульсы звука для разрушения укреплений.
- Радиоволны: растрескивание бетона (например, наведением радиоволны с длиной волны 12 см) перед выстрелом или бомбардировкой укреплённого сооружения.
Роль и производство брони в крупнейших войнах
Литература
Wikimedia Foundation. 2010.
dic.academic.ru
Броневая сталь
Изобретение относится к составам свариваемых сталей, используемых в бронезащитных конструкциях в высокоупрочненном состоянии после закалки на мартенсит. Броневая сталь содержит, мас.%: 0,24-0,64 C; 0,4-1,9 Si; 0,3-1,6 Mn; 0,6-2,0 Cr; 0,6-1,8 Ni; 0,10-0,40 Mo; 0,01-0,15 Al; 0,001-0,020 N; 0,05-0,35 Cu; 0,01-0,15 Ti; остальное Fe. Кроме того, броневая сталь может дополнительно содержать 0,05-5,0 мас.% Co. Сталь предложенного состава обладает повышенной бронестойкостью. 1 з.п. ф-лы, 2 табл.
Изобретение относится к области металлургии, конкретнее к составам свариваемых сталей, используемых в бронезащитных конструкциях в высокоупрочненном состоянии после закалки на мартенсит.
Известна высокопрочная низколегированная сталь, закаливаемая на мартенсит, содержащая, мас.%:
Углерод | 0,05-0,62 |
Марганец | 0,42-0,82 |
Кремний | 0,80-1,80 |
Хром | 1,10-1,40 |
Молибден | 0,15-0,60 |
Алюминий | 0,02-0,15 |
Титан | 0,02-0,12 |
Железо | Остальное. |
Данная сталь может содержать до 0,24% никеля, или 1,65-2,0% никеля при содержании молибдена 0,35-0,60%, а также 1,1-1,8% кремния и дополнительно до 0,02% церия (Патент Российской Федерации №2031179, МПК C22C 38/28, C22C 38/34, C22C 38/50, 1995 г.).
Недостаток стали известного состава состоит в том, что она имеет низкую откольную стойкость при соударении с бронебойным сердечником пули. Это снижает ее бронестойкость.
Наиболее близким аналогом к предлагаемому изобретению является броневая сталь следующего состава, мас.%:
Углерод | 0,29-0,38 |
Кремний | 0,15-0,37 |
Марганец | 0,30-0,60 |
Хром | 1,2-2,0 |
Никель | 1,2-2,20 |
Молибден | 0,72-0,90 |
Ванадий | 0,06-0,20 |
Алюминий | 0,01-0,05 |
Азот | 0,005-0,020 |
Медь | не более 0,50 |
Ниобий | не более 0,05 |
Сера | не более 0,012 |
Фосфор | не более 0,015 |
Железо | Остальное |
(Патент Российской Федерации №2341583, МПК C22C 38/48, 2007 г.).
Недостатки броневой стали данного состава состоят в том, что при многократном соударении с высокопрочными бронебойными сердечниками пуль в ней возникают полосы адиабатического сдвига, интенсивно нарастают повреждения микроструктуры, которые приводят к разрушению броневой преграды. Это снижает бронестойкость стали.
Техническая задача, решаемая изобретением, состоит в повышении бронестойкости.
Для решения поставленной технической задачи броневая сталь, содержащая углерод, кремний, марганец, хром, никель, молибден, алюминий, азот, медь и железо, она дополнительно содержит титан при следующем соотношении компонентов, мас.%:
Углерод | 0,24-0,64 |
Кремний | 0,4-1,9 |
Марганец | 0,30-1,6 |
Хром | 0,6-2,0 |
Никель | 0,6-1,8 |
Молибден | 0,10-0,40 |
Алюминий | 0,01-0,15 |
Азот | 0,001-0,020 |
Медь | 0,05-0,35 |
Титан | 0,01-0,15 |
Железо | Остальное |
Кроме того, броневая сталь может дополнительно содержать кобальт в количестве 0,05-5,0%.
Сущность изобретения состоит в следующем. При соударении с высокопрочным пулевым сердечником в броневой преграде возникает и распространяется вглубь ударная волна, что сопровождается перемещением металла в направлении фронта возмущения и трансформацией его микроструктуры. После разгрузки импульса ударно-волнового воздействия происходит образование микротрещин в стали. Введение в состав предложенной стали 0,01-0,15% титана при регламентированном содержании остальных компонентов обеспечивает снижение объема металла, перемещаемого за фронтом ударной волны, вызывает искажение кристаллической решетки реечного мартенсита и появлению в ней дополнительной упрочняющей фазы — мартенсита деформации с ε-карбидной фазой титана.
Деформационное структурное упрочнение стали в результате ударно-волнового воздействия приводит к тому, что сердечник пули при соударении с броневой преградой разрушается на более мелкие фрагменты, чем обеспечивается ее непробитие.
Введение в сталь предложенного состава кобальта обеспечивает расширение температурного интервала устойчивого состояния мартенсита, за счет чего повышается живучесть бронеконструкции в целом.
Углерод упрочняет сталь. При концентрации углерода менее 0,24% не достигается требуемая прочность и твердость стали, а при его концентрации более 0,64% снижаются вязкость, пластичность и бронезащитные свойства закаленной стали. Кроме того, при концентрации углерода более 0,64% не исключается коробление и поводки при сварке деталей броневой преграды.
Кремний раскисляет сталь, повышает ее прочность и упругость. Он упрочняет сталь без образования карбидов и нитридов, повышает устойчивость мартенсита при локальном нагреве в месте соударения с пулевым сердечником. При концентрации кремния менее 0,4% прочность стали ниже допустимой, а при концентрации более 1,9% снижается ее пластичность и вязкость, а также свариваемость.
Марганец раскисляет и упрочняет сталь, связывает серу. При содержании марганца менее 0,30% прочность и твердость стали недостаточны. Увеличение содержания марганца более 1,60% приводит к снижению ударной вязкости закаленной стали.
Хром повышает прочность, вязкость и бронестойкость стали. При его концентрации менее 0,6% прочность и вязкость ниже допустимых значений. Увеличение содержания хрома более 2,0% приводит к потере пластичности.
Никель способствует повышению пластичности и вязкости закаленной стали, но при его содержании более 1,8% повышается содержание остаточного аустенита в стали и ухудшается бронестойкость. Снижение содержания никеля менее 0,6% приводит к потере пластичности и ударной вязкости.
Молибден образует мелкодисперсные карбиды, благоприятно изменяет распределение вредных примесей, уменьшая их концентрацию по границам зерен, повышает прочность и вязкость стали, обусловливает мелкозернистость микроструктуры. При содержании молибдена менее 0,10% прочность стали ниже требуемого уровня, а увеличение его содержания более 0,40% ухудшает свариваемость и пластичность закаленной стали.
Алюминий дораскисляет сталь, способствует измельчению микрострктуры, повышению работы удара и бронестойкости стали. При содержании алюминия менее 0,01% его присутствие не сказывается на повышении функциональных свойств стали. Увеличение концентрации алюминия более 0,15% ведет к графитизации стали, снижению броневой стойкости.
Влияние азота в данной стали подобно влиянию углерода, но азот, упрочняя сталь, не вызывает снижения ударной вязкости. При содержании азота менее 0,001% сталь имеет недостаточную прочность. Увеличение его концентрации более 0,020% ведет к потере пластичности и снижению откольной стойкости.
Медь повышает теплостойкость стали при локальном тепловыделении в месте соударения с бронебойным сердечником. При концентрации меди менее 0,5% имеет место локальное снижение прочностных свойств и бронестойкости стали. Увеличение концентрации меди более 0,35% снижает ударную вязкость и свариваемость закаленной стали, что недопустимо.
Титан оказывает существенное влияние на сопротивление пробитию и эволюцию микроструктуры в месте соударения. При содержании титана в стали предложенного состава менее 0,01%) циклические соударения при обстреле ведут к накоплению повреждений и разрушению броневой преграды. Увеличение концентрации титана более 0,15% нежелательно, так как уменьшает дессипацию кинетической энергии при соударении с броневым сердечником, что увеличивает вероятность пробития броневой преграды.
Введение в сталь кобальта способствует повышениют бронестойкость стали при повышенных температурах, обусловленных как прямым термическим влиянием, так и адиабатическим нагревом, возникающим при соударении сердечника пули с броневой преградой. При снижении содержания кобальта менее 0,05% ухудшается бронестойкость стали при нагреве. Увеличение концентрации кобальта более 5,0% снижает ударную вязкость, способствует разрушению стальной броневой преграды при ударно-волновом деформировании и снижению бронестойкости.
Стали различного химического состава выплавляли в электродуговой печи. Выплавленную сталь в ковше раскисляли ферромарганцем, ферросилицием, легировали феррохромом, ферромолибденом, ферротитаном, ферроазотом, вводили металлические никель, медь, алюминий, кобальт. С помощью синтетических шлаков удаляли избыток серы и фосфора. Химический состав выплавляемых сталей приведен в табл.1.
Сталь разливали в слитки и подвергали прокатке в слябы толщиной 100 мм. Затем слябы нагревали до температуры 1250°C и прокатывали на реверсивном стане кварто 2000 в листы толщиной от 5,0 до 12,0 мм.
Таблица 1 | ||||||||||||
Состав броневых сталей | ||||||||||||
№ состава | Содержание химических элементов, мас.% | |||||||||||
C | Si | Mn | Cr | Ni | Mo | Al | N | Cu | Ti | Co | Fe | |
1 | 0,23 | 0,3 | 0,2 | 0,5 | 0,5 | 0,09 | 0,009 | 0,0009 | 0,04 | 0,009 | — | Ост. |
2 | 0,24 | 0,4 | 0,3 | 0,6 | 0,6 | 0,10 | 0,010 | 0,001 | 0,05 | 0,010 | — | -:- |
3 | 0,44 | 1,2 | 0,9 | 1,3 | 1,2 | 0,25 | 0,080 | 0,010 | 0,20 | 0,050 | — | -:- |
4 | 0,64 | 1,9 | 1,6 | 2,0 | 1,8 | 0,40 | 0,150 | 0,020 | 0,35 | 0,100 | — | -:- |
5 | 0,65 | 2,0 | 1,7 | 2,1 | 1,9 | 0,50 | 0,160 | 0,022 | 0,36 | 0,110 | — | -:- |
6 | 0,23 | 0,8 | 0,5 | 0,5 | 0,8 | 0,20 | 0,050 | 0,001 | 0,10 | 0,011 | 0,04 | -:- |
7 | 0,45 | 1,1 | 0,8 | 1,2 | 1,3 | 0,24 | 0,070 | 0,011 | 0,18 | 0,060 | 0,05 | -:- |
8 | 0,50 | 1,5 | 1,5 | 1,4 | 1,5 | 0,28 | 0,090 | 0,013 | 0,28 | 0,090 | 2,25 | -:- |
9 | 0,63 | 1,8 | 1,5 | 1,9 | 1,7 | 0,38 | 0,140 | 0,019 | 0,34 | 0,095 | 5,00 | -:- |
10 | 0,66 | 2,1 | 1,7 | 2,1 | 1,9 | 0,42 | 0,170 | 0,021 | 0,37 | 0,012 | 5,20 | -:- |
11 | 0,30 | 0,3 | 0,4 | 1,6 | 1,5 | 0,80 | 0,030 | 0,014 | 0,45 | — | — | -:- |
Листовую сталь с различными составами подвергали незамедлительной закалке водой с прокатного нагрева от температуры 840°C. Закаленную сталь составов №1-5 и 11 отпускали при температуре 250°C, а составов №6-10 отпускали при температуре 450°C. Время выдержки в обоих случаях составляло 3 ч.
После охлаждения от листовой стали отбирали пробы и производили испытания механических свойств, а также бронестойкости. Бронестойкость оценивали по минимальной толщине H (мм) непробития пластин при обстреле из снайперской винтовки Драгунова бронебойными пулями типа Б-32 калибра 7,62 мм с расстояния 100 м. В таблице 2 приведены результаты испытаний свойств горячекатаной листовой стали.
Таблица 2 | ||||||
Механические свойства и бронестойкость листовых сталей | ||||||
№ состава | HRC, ед. | σв, МПа | σт, МПа | δ5, % | KCU, МДж/см2 | H, мм |
1 | 55 | 1610 | 1430 | 9,5 | 38 | 11,0 |
2 | 60 | 1800 | 1700 | 16 | 48 | 6,5 |
3 | 61 | 1820 | 1700 | 17 | 50 | 6,0 |
4 | 60 | 1830 | 1750 | 16 | 49 | 6,5 |
5 | 53 | 1730 | 1680 | 9,2 | 36 | 12,0 |
6 | 56 | 1650 | 1530 | 9,5 | 37 | 11,0 |
7 | 60 | 1820 | 1710 | 17 | 50 | 6,3 |
8 | 62 | 1830 | 1720 | 17 | 50 | 6,0 |
9 | 61 | 1830 | 1730 | 17 | 50 | 6,3 |
10 | 57 | 1680 | 1690 | 9,8 | 39 | 10,0 |
11 | 56 | 1510 | 1320 | 9,7 | 38 | 12,0 |
Из таблиц 1 и 2 следует, что предложенная сталь (составы №2-4, 7-9), имеет наиболее высокую бронестойкость: минимальная толщина листа, выдерживающая стандартные баллистикоударные испытания, составляла H=6,0-6,5 мм.
При запредельных содержаниях химических элементов в сталях (составы №1, №5, №6, №10), а также при использовании стали-прототипа (состав 11) механические и бронезащитные свойства горячекатаных закаленных листов снижаются, значение Н возрастает до 10-12 мм.
Технико-экономические преимущества предложенной броневой стали состоят в том, что введение в ее состав 0,01-0,10% титана при регламентированной концентрации всех остальных элементов обеспечивает в процессе закалки полное превращение аустенита в мартенсит, уменьшение количества включений перлитной фазы, повышение бронестойкости. Дополнительное введение в сталь кобальта в количестве 0,05-5,0% повышает температурную стабильность мартенсита, сталь сохраняет высокие функциональные свойства даже при более высоких температурах отпуска, что также способствует повышению бронестойкости стали и живучести броневой конструкции.
В качестве базового объекта принята сталь-прототип. Использование предложенной стали позволит как повысить эффективность бронезащитных конструкций в целом на 8-10%, так и снизить их толщину и массу при сохранении бронезащитных свойств.
1. Броневая сталь, содержащая углерод, кремний, марганец, хром, никель, молибден, алюминий, азот, медь и железо, отличающаяся тем, что она дополнительно содержит титан при следующем соотношении компонентов, мас.%:
Углерод | 0,24-0,64 |
Кремний | 0,4-1,9 |
Марганец | 0,30-1,6 |
Хром | 0,6-2,0 |
Никель | 0,6-1,8 |
Молибден | 0,10-0,40 |
Алюминий | 0,01-0,15 |
Азот | 0,001-0,020 |
Медь | 0,05-0,35 |
Титан | 0,01-0,15 |
Железо | Остальное |
2. Броневая сталь по п.1, отличающаяся тем, что она дополнительно содержит кобальт в количестве 0,05-5,0 мас.%.
www.findpatent.ru
Изобретение относится к составам свариваемых сталей, используемых в бронезащитных конструкциях в высокоупрочненном состоянии после закалки на мартенсит. Броневая сталь содержит, мас.%: 0,24-0,64 C; 0,4-1,9 Si; 0,3-1,6 Mn; 0,6-2,0 Cr; 0,6-1,8 Ni; 0,10-0,40 Mo; 0,01-0,15 Al; 0,001-0,020 N; 0,05-0,35 Cu; 0,01-0,15 Ti; остальное Fe. Кроме того, броневая сталь может дополнительно содержать 0,05-5,0 мас.% Co. Сталь предложенного состава обладает повышенной бронестойкостью. 1 з.п. ф-лы, 2 табл. Изобретение относится к области металлургии, конкретнее к составам свариваемых сталей, используемых в бронезащитных конструкциях в высокоупрочненном состоянии после закалки на мартенсит. Известна высокопрочная низколегированная сталь, закаливаемая на мартенсит, содержащая, мас.%:
Данная сталь может содержать до 0,24% никеля, или 1,65-2,0% никеля при содержании молибдена 0,35-0,60%, а также 1,1-1,8% кремния и дополнительно до 0,02% церия (Патент Российской Федерации № 2031179, МПК C22C 38/28, C22C 38/34, C22C 38/50, 1995 г.). Недостаток стали известного состава состоит в том, что она имеет низкую откольную стойкость при соударении с бронебойным сердечником пули. Это снижает ее бронестойкость. Наиболее близким аналогом к предлагаемому изобретению является броневая сталь следующего состава, мас.%:
(Патент Российской Федерации № 2341583, МПК C22C 38/48, 2007 г.). Недостатки броневой стали данного состава состоят в том, что при многократном соударении с высокопрочными бронебойными сердечниками пуль в ней возникают полосы адиабатического сдвига, интенсивно нарастают повреждения микроструктуры, которые приводят к разрушению броневой преграды. Это снижает бронестойкость стали. Техническая задача, решаемая изобретением, состоит в повышении бронестойкости. Для решения поставленной технической задачи броневая сталь, содержащая углерод, кремний, марганец, хром, никель, молибден, алюминий, азот, медь и железо, она дополнительно содержит титан при следующем соотношении компонентов, мас.%:
Кроме того, броневая сталь может дополнительно содержать кобальт в количестве 0,05-5,0%. Сущность изобретения состоит в следующем. При соударении с высокопрочным пулевым сердечником в броневой преграде возникает и распространяется вглубь ударная волна, что сопровождается перемещением металла в направлении фронта возмущения и трансформацией его микроструктуры. После разгрузки импульса ударно-волнового воздействия происходит образование микротрещин в стали. Введение в состав предложенной стали 0,01-0,15% титана при регламентированном содержании остальных компонентов обеспечивает снижение объема металла, перемещаемого за фронтом ударной волны, вызывает искажение кристаллической решетки реечного мартенсита и появлению в ней дополнительной упрочняющей фазы — мартенсита деформации с -карбидной фазой титана. Деформационное структурное упрочнение стали в результате ударно-волнового воздействия приводит к тому, что сердечник пули при соударении с броневой преградой разрушается на более мелкие фрагменты, чем обеспечивается ее непробитие. Введение в сталь предложенного состава кобальта обеспечивает расширение температурного интервала устойчивого состояния мартенсита, за счет чего повышается живучесть бронеконструкции в целом. Углерод упрочняет сталь. При концентрации углерода менее 0,24% не достигается требуемая прочность и твердость стали, а при его концентрации более 0,64% снижаются вязкость, пластичность и бронезащитные свойства закаленной стали. Кроме того, при концентрации углерода более 0,64% не исключается коробление и поводки при сварке деталей броневой преграды. Кремний раскисляет сталь, повышает ее прочность и упругость. Он упрочняет сталь без образования карбидов и нитридов, повышает устойчивость мартенсита при локальном нагреве в месте соударения с пулевым сердечником. При концентрации кремния менее 0,4% прочность стали ниже допустимой, а при концентрации более 1,9% снижается ее пластичность и вязкость, а также свариваемость. Марганец раскисляет и упрочняет сталь, связывает серу. При содержании марганца менее 0,30% прочность и твердость стали недостаточны. Увеличение содержания марганца более 1,60% приводит к снижению ударной вязкости закаленной стали. Хром повышает прочность, вязкость и бронестойкость стали. При его концентрации менее 0,6% прочность и вязкость ниже допустимых значений. Увеличение содержания хрома более 2,0% приводит к потере пластичности. Никель способствует повышению пластичности и вязкости закаленной стали, но при его содержании более 1,8% повышается содержание остаточного аустенита в стали и ухудшается бронестойкость. Снижение содержания никеля менее 0,6% приводит к потере пластичности и ударной вязкости. Молибден образует мелкодисперсные карбиды, благоприятно изменяет распределение вредных примесей, уменьшая их концентрацию по границам зерен, повышает прочность и вязкость стали, обусловливает мелкозернистость микроструктуры. При содержании молибдена менее 0,10% прочность стали ниже требуемого уровня, а увеличение его содержания более 0,40% ухудшает свариваемость и пластичность закаленной стали. Алюминий дораскисляет сталь, способствует измельчению микрострктуры, повышению работы удара и бронестойкости стали. При содержании алюминия менее 0,01% его присутствие не сказывается на повышении функциональных свойств стали. Увеличение концентрации алюминия более 0,15% ведет к графитизации стали, снижению броневой стойкости. Влияние азота в данной стали подобно влиянию углерода, но азот, упрочняя сталь, не вызывает снижения ударной вязкости. При содержании азота менее 0,001% сталь имеет недостаточную прочность. Увеличение его концентрации более 0,020% ведет к потере пластичности и снижению откольной стойкости. Медь повышает теплостойкость стали при локальном тепловыделении в месте соударения с бронебойным сердечником. При концентрации меди менее 0,5% имеет место локальное снижение прочностных свойств и бронестойкости стали. Увеличение концентрации меди более 0,35% снижает ударную вязкость и свариваемость закаленной стали, что недопустимо. Титан оказывает существенное влияние на сопротивление пробитию и эволюцию микроструктуры в месте соударения. При содержании титана в стали предложенного состава менее 0,01%) циклические соударения при обстреле ведут к накоплению повреждений и разрушению броневой преграды. Увеличение концентрации титана более 0,15% нежелательно, так как уменьшает дессипацию кинетической энергии при соударении с броневым сердечником, что увеличивает вероятность пробития броневой преграды. Введение в сталь кобальта способствует повышениют бронестойкость стали при повышенных температурах, обусловленных как прямым термическим влиянием, так и адиабатическим нагревом, возникающим при соударении сердечника пули с броневой преградой. При снижении содержания кобальта менее 0,05% ухудшается бронестойкость стали при нагреве. Увеличение концентрации кобальта более 5,0% снижает ударную вязкость, способствует разрушению стальной броневой преграды при ударно-волновом деформировании и снижению бронестойкости. Стали различного химического состава выплавляли в электродуговой печи. Выплавленную сталь в ковше раскисляли ферромарганцем, ферросилицием, легировали феррохромом, ферромолибденом, ферротитаном, ферроазотом, вводили металлические никель, медь, алюминий, кобальт. С помощью синтетических шлаков удаляли избыток серы и фосфора. Химический состав выплавляемых сталей приведен в табл.1. Сталь разливали в слитки и подвергали прокатке в слябы толщиной 100 мм. Затем слябы нагревали до температуры 1250°C и прокатывали на реверсивном стане кварто 2000 в листы толщиной от 5,0 до 12,0 мм.
Листовую сталь с различными составами подвергали незамедлительной закалке водой с прокатного нагрева от температуры 840°C. Закаленную сталь составов № 1-5 и 11 отпускали при температуре 250°C, а составов № 6-10 отпускали при температуре 450°C. Время выдержки в обоих случаях составляло 3 ч. После охлаждения от листовой стали отбирали пробы и производили испытания механических свойств, а также бронестойкости. Бронестойкость оценивали по минимальной толщине H (мм) непробития пластин при обстреле из снайперской винтовки Драгунова бронебойными пулями типа Б-32 калибра 7,62 мм с расстояния 100 м. В таблице 2 приведены результаты испытаний свойств горячекатаной листовой стали.
Из таблиц 1 и 2 следует, что предложенная сталь (составы № 2-4, 7-9), имеет наиболее высокую бронестойкость: минимальная толщина листа, выдерживающая стандартные баллистикоударные испытания, составляла H=6,0-6,5 мм. При запредельных содержаниях химических элементов в сталях (составы № 1, № 5, № 6, № 10), а также при использовании стали-прототипа (состав 11) механические и бронезащитные свойства горячекатаных закаленных листов снижаются, значение Н возрастает до 10-12 мм. Технико-экономические преимущества предложенной броневой стали состоят в том, что введение в ее состав 0,01-0,10% титана при регламентированной концентрации всех остальных элементов обеспечивает в процессе закалки полное превращение аустенита в мартенсит, уменьшение количества включений перлитной фазы, повышение бронестойкости. Дополнительное введение в сталь кобальта в количестве 0,05-5,0% повышает температурную стабильность мартенсита, сталь сохраняет высокие функциональные свойства даже при более высоких температурах отпуска, что также способствует повышению бронестойкости стали и живучести броневой конструкции. В качестве базового объекта принята сталь-прототип. Использование предложенной стали позволит как повысить эффективность бронезащитных конструкций в целом на 8-10%, так и снизить их толщину и массу при сохранении бронезащитных свойств. ФОРМУЛА ИЗОБРЕТЕНИЯ1. Броневая сталь, содержащая углерод, кремний, марганец, хром, никель, молибден, алюминий, азот, медь и железо, отличающаяся тем, что она дополнительно содержит титан при следующем соотношении компонентов, мас.%:
2. Броневая сталь по п.1, отличающаяся тем, что она дополнительно содержит кобальт в количестве 0,05-5,0 мас.%. | Официальная публикация патента РФ № 2447181 patent-2447181.pdf Патентный поиск по классам МПК-8: Класс C22C38/14 содержащие титан или цирконий Патенты РФ в классе C22C38/14:
Класс C22C38/50 с титаном или цирконием Патенты РФ в классе C22C38/50: |
www.freepatent.ru
Пулестойкая броня
Сравнительный анализ полезных свойств военной брони А3 и пулестойкой износостойкой стали С500 показывает,
что пулестойкая сталь С-500 превосходит бронесталь А-3 по параметрам:
Свариваемость
Живучесть
Износостойкость
При одинаковой твердости.
Что касается параметра «Пулестойкость»:
Противопульная броня С500 и А3 имеет одинаковый класс защиты Бр4, Бр2, БР3 при схожей толщине.
По классу защиты БР5 и Бр6 сертифицируется только пулестойкая сталь С-500.
Технологичность при производстве С500 намного выше, что позволяет производить толщину до 40мм! Максимальная толщина брони А3, не более 16мм.
Раскрой закаленного слоя у брони С500 имеет размеры 2000*6000мм
У брони А3, не более 1295*2500, что не удобно, когда требуется цельный лист большой площади.
Свариваемость С500 обусловлена более низким количеством углерода в диапазоне 0,19-0,26
у А3 углерода 0,4.
Военное назначение этих сталей: Броневая сталь, Пулестойкие стали для тира, баллистические плиты,
баллистические стали, баллистический лист, листы бронестали, броневые стали, Пулестойкая сталь
Гражданское применение:
Износостойкость. Работа на трение, износостойкая сталь, Износоустойчивость к трению, защита от трения и износа, стойкость на трение
Если требуется лист 110г13 смело берите С500, это лучшая защита от трения.
Есть все толщины
Отгрузка от 1 листа.
Доставка по России бесплатна. Отгружаем образцы на пробу.
Живучесть обусловлена более высокой вязкостью, что ведет к стойкости и не раскалыванию при многократном попадании пуль и осколков.
Абразивная стойкость С500: обеспечивает хром, молибден, никель, марганец, ванадий, вольфрам, бор и ниобий.
Пулестойкая броня С-500 не магнитится! Это отличное свойство для использование в корпусах военных приборов.
Гражданское применение везде где идет износ и ударная нагрузка.
В первую очередь Судостроение на ледоколы как ледоколная сталь. Дробить льдины толщиной до 4 метров под силу только танковой броне.
В цементном оборудовании, в горно-шахтном оборудовании.
Как комплектующие на дробеметное оборудование, например, пластины броневые на дробеметы;
В качестве импортозамещения для замены слабеньких иностранных износостойких сталей типа: ХАРДОКС, hardox, raex, fora, xar, марс, крусабро, которые даже при сварке требуют нагрева;
Свойства износостойких сталей дает им возможность противостоять износу, из-за трения, удара или сжимающих нагрузок от внешних факторов,
таких как цемент, песок, камни и т.д., и предназначены для использования в строительстве оборудования и для замены изношенных деталей.
Самосвальные кузова, подъемно-транспортное оборудование и дробильные машины, например, подвергаются непрерывному, абразивному и ударному износу.
В качестве замены марганцовистой стали Гадфильда, 110г13 и 110г13л.
На тяжелонагруженные ответственные конструкции;
На дробилки и мальницы как бронеплиты, футеровки, защитные пластины;
Требуется броня А3, лучшая сталь С-500 или сталь 96 (45х2мфба), обращайтесь!
Пулестойкая сталь в наличии
Ждем вас в гости!
Телефоны отдела продаж: (343) 268-24-10, 219-30-89, 361-21-18, 257-32-83
irontub.ru