Подбор болтов и шпилек для фланцевых соединений.
Главная » Техподдержка » Статьи » Подбор болтов и шпилек для фланцевых соединений.Внимание! Специально для Вас мы разработали
Чтобы правильно подобрать крепеж для фланцевых соединений необходимо учитывать следующие характеристики:
- Рабочее давление
- Рабочая температура
- Рабочая среда
- Внешняя среда
Особые замечания при выборе крепежа:
- При давлении до 25 кгс/см2 можно использовать как болт, так и шпильку. При давлении свыше 25 кгс/см2 применение болтов не допускается.
- При изготовлении крепежной пары (шпилька, гайка) твердость гайки должна быть на 20 единиц меньше чем у шпильки.
![]() |
Размеры шпилек D(диаметр мм)*L(длина мм) по ГОСТ 9066-75 для фланцевых соединений на различные давления (РУ). | |||||||||||||
Dy | Py, кгс/см2 | Dy | Py, кгс/см2 | |||||||||||
1 и 2,5 | 6 | 10 | 16 | 25 | 1 и 2,5 | 6 | 10 | 16 | 25 | 40 | 64 | 100 | ||
10 | M10x35 | M10x45 | M12x40 | M12x45 | M12x50 | 10 | M10x50 | M12x70 | M12x80 | |||||
15 | M12x45 | 15 | ||||||||||||
20 | M10x40 | M10x45 | M12x50 | M12x55 | 20 | M12x60 | M12x70 | M16x90 | M16x90 | |||||
25 | 25 | M16x100 | ||||||||||||
32 | M12x45 | M12x50 | M16x55 | M16x60 | 32 | M12x60 | M16x70 | M16x80 | M16x80 | M16x90 | M20x110 | M20x110 | ||
40 | M16x60 | M15x65 | 40 | M16x80 | ||||||||||
50 | M16x65 | M16x70 | 50 | M24x120 | ||||||||||
65 | M16x60 | 65 | M16x90 | M20x120 | M24x130 | |||||||||
80 | M16x50 | M16x55 | 80 | M16x70 | M16x90 | M16x100 | ||||||||
100 | M16x65 | M16x70 | M20x80 | 100 | M20x100 | M20x110 | M24x130 | M27x150 | ||||||
125 | M16x60 | M16x70 | M24x90 | 125 | M16x70 | M16x80 | M16x90 | M24x110 | M24x120 | M27x150 | M30x170 | |||
150 | M20x70 | M20x80 | 150 | M20x100 | M20x100 | M30x160 | M30x180 | |||||||
175 | M16x60 | M16x65 | M20x75 | 175 | M16x80 | M24x120 | M27x150 | M30x170 | ||||||
200 | M24x100 | 200 | M20x110 | |||||||||||
225 | M27x100 | 225 | M27x130 | M30x170 | M30x180 | M36x210 | ||||||||
250 | M16x65 | M16x70 | M24x90 | 250 | M24x120 | M36x210 | M42x250 | |||||||
300 | M20x70 | M20x75 | M20x80 | M27x110 | 300 | M20x90 | M27x140 | M30x180 | M36x220 | M48x270 | ||||
350 | M24x100 | M30x120 | 350 | M20x90 | M20x100 | M30x150 | M30x190 | M48x280 | ||||||
400 | M20x75 | M20x80 | M24x90 | M27x110 | M30x130 | 400 | M24x110 | M27x130 | M30x160 | M36x220 | ||||
450 | M27x120 | 450 | M20x100 | M27x140 | ||||||||||
500 | M30x130 | M36x140 | 500 | M24x120 | M30x160 | M36x180 | M42x240 | |||||||
600 | M24x80 | M24x90 | M27x110 | M36x140 | M36x150 | 600 | M24x110 | M27x130 | M36x170 | M36x190 | M48x240 | |||
700 | M42x160 | 700 | M36x180 | M42x210 | ||||||||||
800 | M27x90 | M27x100 | M30x120 | M42x170 | 800 | M27x120 | M30x150 | M48x220 | ||||||
900 | M48x180 | 900 | M27x140 | M48x230 | ||||||||||
1000 | M30x130 | M42x150 | M52x190 | 1000 | M30x160 | M42x200 | M52x240 | |||||||
1200 | M30x110 | M36x150 | M48x160 | — | 1200 | M30x140 | M36x180 | M48x210 |
© ЗАО «Башметиз» полная или частичная перепечатка текста разрешена только при указании ссылки на текущую страницу.
Шпильки, болты, гайки и шайбы
Шпилька резьбовая DIN975
Шпилька с метрической резьбой предназначена для наращивания крепежных конструкций с метрической резьбой, подвески воздуховодов, систем вентиляции на потолочных перекрытиях, соединения подвесных приспособлений, установки рекламных щитов. Для удлинения конструкций на основе резьбовой шпильки используют соединительные гайки.
Применяется длиной 1м и 2м.
Характеристики:
Размер, мм | Вес, кг/шт. | Упаковка шт. |
6х1000 | 0,1793 | 100 |
8х1000 | 0,3168 | 50 |
10х1000 | 0,5000 | 25 |
6х2000 | 0,3586 | 50 |
8х2000 | 0,6336 | 25 |
10х2000 | 1,0000 | 25 |
Болт с полной резьбой DIN933/DIN558
Головка болта шестигранная, резьба метрическая, полная. Болт изготовлен из конструкционной оцинкованной стали.
Применяется для крепления листового металла в машиностроении и при производстве мебели.
Характеристики:
Размер, мм | Вес, кг/шт. | Количество шт. в кг |
М6х20 | 0,0057 | 175 |
М6х25 | 0,0065 | 155 |
М6х30 | 0,0074 | 135 |
М6х40 | 0,0091 | 110 |
М8х20 | 0,0118 | 85 |
М8х25 | 0,0133 | 75 |
М8х30 | 0,0149 | 67 |
М8х35 | 0,0167 | 60 |
М8х40 | 0,0182 | 55 |
М10х20 | 0,0213 | 47 |
М10х25 | 0,0238 | 42 |
М10х30 | 0,0256 | 39 |
М10х35 | 0,0278 | 36 |
М10х40 | 0,0303 | 33 |
Гайка шестигранная DIN934
Гайка шестигранная представляет собой деталь с внутренней резьбой, которая вместе с винтом или болтом составляет винтовую пару. Гайки используются для крепления и соединения узлов и устройств наряду с винтами, болтами, резьбовой шпилькой.
Предназначены они, в основном, для крепежа элементов трубопровода, механизмов, строительных конструкций. Применяются в строительстве, народном хозяйстве, машиностроении.
Характеристики:
Размер, мм | Вес, кг/шт. | Количество шт. в кг |
M6 | 0,0021 | 480 |
M8 | 0,0045 | 220 |
M10 | 0,0100 | 100 |
Гайка соединительная/переходная DIN934
Гайка соединительная предназначена для конструкционных соединений резьбовых элементов (шпилек, болтов и др.). Гайку можно использовать также в комплекте с шайбой.
Соединительная гайка производится из стали, сверху покрывается цинком для повышения прочности изделия, имеет белое пассирование.
Характеристики:
Размер, мм | Вес, кг/шт. | Упаковка шт. |
М6х10х18 | 0,0090 | 100 |
М8х13х23 | 0,0190 | 100 |
М10х17х30 | 0,0410 | 100 |
Шайба плоская DIN125
Шайбу применяют для предохранения поверхности детали от повреждения гайкой при затяжке, увеличения опорной площади гайки, головки болта или винта, для устранения возможности самоотвинчивания гаек при вибрации и других случаях.
Изготавливают шайбы вырубкой из листового материала или точением из пруткового металла.
Характеристики:
Размер, мм | Вес, кг/шт. | Количество шт. в кг |
M6 | 0,0010 | 1050 |
M8 | 0,0017 | 600 |
M10 | 0,0033 | 300 |
Шайба усиленная DIN9021
Шайбу применяют для предохранения поверхности детали от повреждения гайкой при затяжке, увеличения опорной площади гайки, головки болта или винта, для устранения возможности самоотвинчивания гаек при вибрации и других случаях.
Изготавливают шайбы вырубкой из листового материала или точением из пруткового металла.
Характеристики:
Размер, мм | Вес, кг/шт. | Количество шт. в кг |
M6 | 0,0025 | 400 |
M8 | 0,0059 | 170 |
M10 | 0,0116 | 86 |
Компания «ОблВент» предлагает выгодные дилерские цены ведущих заводов России и ближнего зарубежья. Шпильки, болты, гайки и шайбы — один из самых продаваемых нами товаров. Наши специалисты помогут вам разобрать проект любой сложности, провести рассчеты и при необходимости заменить ваше оборудование на аналогичное, более дешевое и не менее качественное. Звоните нашим специалистам! Наши условия и сроки безусловно Вас заинтересуют!
Гибкая система скидок дает возможность заработать всем участникам сделки!
Тел.
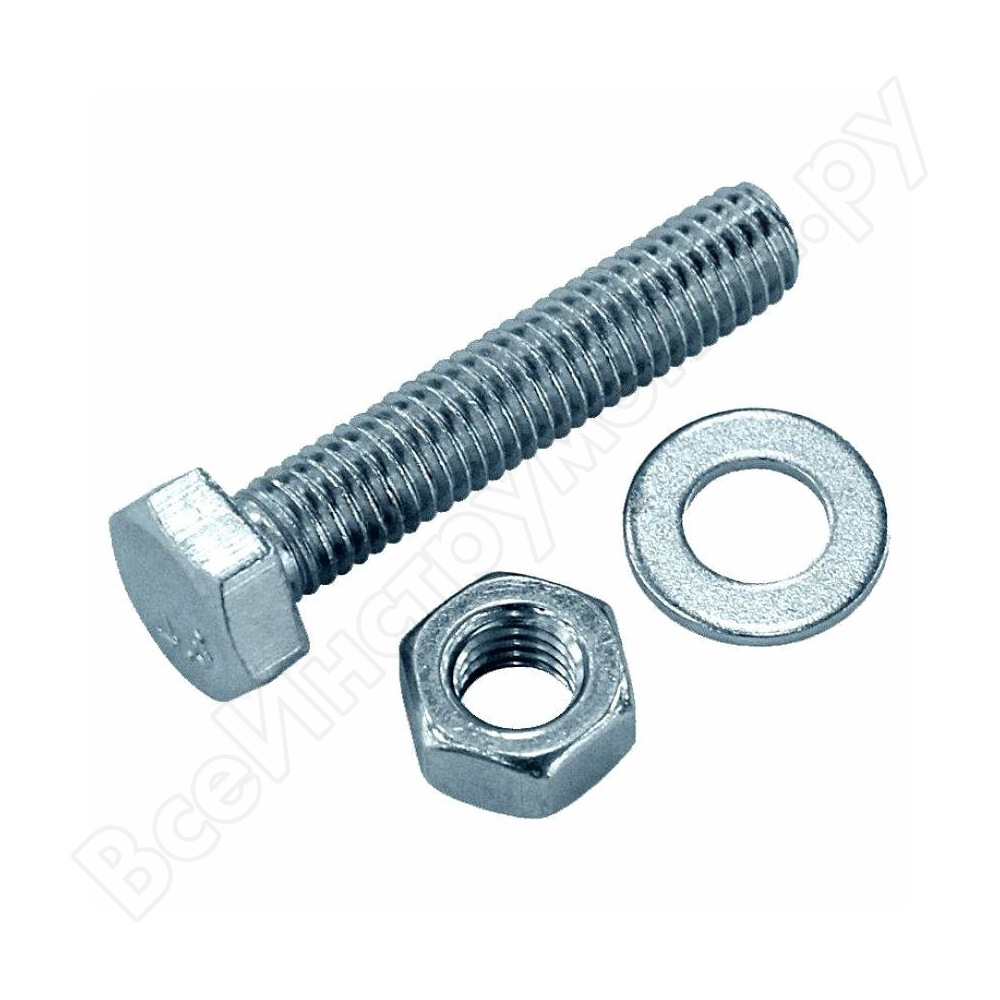
Как определить размер болта, гаек, шпилек, винтов
Определение размера крепежного изделия часто вызывает сложности. Без необходимых знаний и навыков потребуется много времени, чтобы выбрать подходящий метиз. На первый взгляд достаточно найти показатели толщины, длины и диаметра изделия. Но даже при выборе простых болтов и гаек возникают различные вопросы.
Главными параметрами, с помощью которых определяется вид и размер крепежного элемента, считаются длина, толщина и диаметр (в некоторых случаях высота).
Диаметр изделия обозначается буквой “D”, допускается написание как заглавной, так и маленькой (от сокращенного “diameter”). Соответственно, длина — это “lenght”, поэтому для обозначения используется буква “L”. Для толщины применяется понятие “stoutness” — “S”. Если понадобилось указать высоту, то указывается буква “H”, что означает “high”.
Перейдем к некоторым особенностям, которые встречаются при измерении основных видов метизов.
Определение размеров болта
Если болты имеют метрическую резьбу на стержне, то в прилагающейся документации используется формат MDxPxL. Обозначение расшифровывается следующим образом:
- M — указание метрической резьбы;
- D — показатель диаметра изделия;
- P — данные о шаге резьбы (виды отличаются, встречается мелкий, крупный, особо мелкий), при особо крупном значение не добавляется;
- L — показатель длины метиза.
Все перечисленные параметры указываются в миллиметрах.
Для того, чтобы узнать тип и размеры какого-либо болта, потребуется определить его вид. Рекомендуется руководствоваться отечественными стандартами ГОСТ или европейским ISO. Также допускается применение немецкого DIN. После того, как тип будет известен, можно определять размеры.
Диаметр крепежного элемента определяется с помощью различных инструментов — штангенциркуль, шаблонная линейка, а также микрометр. При этом точность измерений контролируется калибрами типа “ПР-НЕ”. Название приспособления расшифровывается как “проход-непроход”. Первая часть при накручивании на болт не требует прикладывания усилий, вторую деталь невозможно закрутить совсем.
Для измерения показателя длины также применяется линейка или штангенциркуль. Если потребовалось узнать шаг резьбы, то для крепежного элемента используется специальный инструмент шагомер. При отсутствии нужного приспособления допускается замер расстояния между парой витков с применением штангенциркуля.
Инструмент подойдет и предоставит точные показатели только в том случае, если измеряется крупный диаметр резьбы. Более правильные параметры получаются в результате проверки нескольких витков вместо двух. Полученный результат необходимо разделить на количество витков, используемых для измерения.
Если число, полученное в результате проверки, совпадает с каким-либо значением резьбового ряда, то это является справочным значением и искомый шаг присутствует. Если измерение не принесло необходимого результата, то вероятно перед вами дюймовый тип резьбы. В таком случае потребуется дополнительное уточнение для точного определения шага.
Болты имеют определенные разновидности, которые определяются геометрической формой метиза. Поэтому методы измерения для каждой группы отличается. Различают 2 варианта:
- с выступающей формой головки;
- потайной вид головки.
Для определения длины крепежных элементов с выступающей головкой не требуется задействовать саму головку.
- метизы с шестигранной головкой, соответствующие нормативам ГОСТ 7805-70, 7798-70, 15589-70, 10602-94;
- варианты с уменьшенными размерами головки и шестью гранями, изготовленные по стандартам ГОСТ 7808-70, 7796-70, 15591-70;
- крепежные элементы с высокой прочностью ГОСТ 22353-77;
- высокопрочные метизы с шестью гранями и увеличенным размером под ключ ГОСТ Р 52644-2006;
- болты, которые имеют шестигранную головку, а также дополнены направляющим подголовком ГОСТ 7811-70, 7795-70, 15590-70;
- головка метиза уменьшена, имеет 6 граней и применяется для монтажа в отверстия из-под развертки ГОСТ 7817-80;
- головка является увеличенной, также предусмотрен ус ГОСТ 7801-81;
- рым-болт, соответствующий отечественному стандарту ГОСТ 4751-73;
- варианты с полукруглой головкой увеличенных размеров, а также оснащенные квадратным подголовком ГОСТ 7802-81.
Если перед вами болт с потайной головкой, то потребуется измерять длину с учетом ее размеров:
- шинные метизы ГОСТ 7787-81;
- с потайной головкой, оснащенные усом и соответствующие нормативам ГОСТ 7785-81;
- стандартный вариант с квадратным подголовком и потайной разновидностью головки ГОСТ 7786-81.
Для определения вида болта и соответствующего ему стандарта применяется размер головки. Например, “под ключ” для головок с шестью гранями, если болт оснащен цилиндрической головкой, то используется диаметр.
Как правильно определить размер дюймового болта
Если рассматривать различную документацию для дюймовых болтов, то встречается аббревиатура для обозначения конструкции в виде D”-NQQQxL. Расшифровывается она следующим образом:
- D” — показатель диаметра резьбы, которая может быть указана как целое число, а также в формате дроби или номера, если метиз представлен с малым диаметром;
- N — обозначение, сколько витков находится на одном дюйме;
- QQQ — встречаются как 3, так и 4 буквы, которые означают дюймовую резьбу;
- L — показатель длины крепежного элемента, также измеряется в дюймах.
Если вам потребовалось узнать резьбовой диаметр для дюймового болта, то необходимо полученные показатели разделить на 25,4 мм. Значение в результате соответствует дюймовому. Затем цифры сопоставляются с подходящим в таблице UNC.
Для точного определения шага резьбы метиза нужно посчитать число витков, расположенных на дюйме крепежного элемента. Облегчить задачу можно с помощью дюймового резьбомера.
Показатели длины по методу измерения практически не отличаются от метрического варианта. Единственная разница в том, что полученный результат обязательно делится на 25,4 мм. Число также сравнивается, как резьбовой диаметр, с данными в таблице.
Как узнать размер винта
Винт с метрической резьбой, как и соответствующие болты, имеет аббревиатуру MDxPxL. Расшифровка тоже не отличается от стандартной:
- M — обозначается показатель метрической резьбы;
- D — показатель диаметра метиза;
- P — обозначение резьбы;
- L — данные о длине крепежного элемента.
Прежде чем начать измерения, определите, к какому стандарту относится винт, а также ознакомьтесь с разновидностью метиза. Диаметр резьбы конструкции получается соответственно методу, который применяется для измерения болтов.
Всего насчитывается 4 группы крепежных элементов:
- которые имеют выступающую головку;
- полупотайные;
- потайные;
- головка у винта отсутствует.
Для каждого варианта используются соответствующие отечественные стандарты:
- метизы, которые имеют головку в форме цилиндра и внутренний шестигранник, изготавливаются по ГОСТ 11738-84;
- для крепежных изделий, оснащенных полукруглой головкой, применим ГОСТ 17473-80;
- варианты с полупотайным типом головки соответствуют ГОСТ 17474-80;
- если перед вами винт, оснащенный потайной головкой, то для него используется ГОСТ 17475-80;
- установочная разновидность, которая отличается от других наличием прямого шлица, регулируется несколькими стандартами — ГОСТ 1476-93, 1477-93, 1478-93, 1479-93;
- метизы, относящиеся к категории установочных, для которых применяется шестигранник, соответствуют ГОСТ 8878-93, 11074-93, 11075-93;
- менее распространенные метизы с квадратным типом головки производят по стандартам ГОСТ 1482-84, 1485-84.
Технология измерения размеров шпилек
Шпильки, как и другие метизы, отличаются наличием метрической резьбы, поэтому имеют соответствующую аббревиатуру MDxPxL. Расшифровка тоже не отличается от предыдущих крепежных элементов:
- M — буквой обозначается метрическая резьба метиза;
- D — применяется для указания диаметра;
- P — разновидность шага, показатель в миллиметрах;
- L — данные о длине рабочей части конструкции.
Вид измерения выбирается в соответствии с подходящим нормативом ГОСТ, а также типом шпильки. Всего существует 2 больших группы для определения принадлежности метиза:
- конструкции, которые используются для монтажа в гладкие отверстия;
- крепежные элементы с концом, который завинчивается в отверстие.
В первом случае рабочая часть представлена по всей длине метиза, во втором случае используется только хвостовик, при этом конец для закручивания не учитывается.
Шпильки, как и другие метизы, производят по стандартам:
- метизы с резьбой DIN 975;
- размерный вариант, соответствующий DIN 976-1;
- конструкции, предназначенные для установки в гладкие участки, регулируются ГОСТ 22042-76, 22043-76;
- метизы для создания фланцевого прочного соединения ГОСТ 9066-75.
Также есть другие варианты, которые отличаются закручиваемым концом и показателем длины. Для них применяются прочие нормативы ГОСТ.
Как узнать размер заклепки
Полнотелые заклепки, оснащенные замыкающей головкой и устанавливающиеся с помощью молотка представлены в документах в виде аббревиатуры DxL. Расшифровка следующая:
- D — показатель диаметра тела;
- L — показатель длины.
В зависимости от используемых нормативов ГОСТ и конструкции полнотелой заклепки, возможна разница между способами определения длины метиза, поэтому предусмотрено 3 отдельных группы по видам:
- с выступающей головкой;
- крепежный элемент с потайной головкой;
- вариант с полупотайной головкой.
При изготовлении применяются разные ГОСТы:
- для метизов с головкой в форме цилиндра ГОСТ 10303-80;
- варианты с потайной головкой производятся согласно ГОСТ 10300-80;
- метизы с полукруглой формой головки ГОСТ 10299-80;
- полупотайной вариант ГОСТ 10301-80.
Также встречаются отрывные заклепки, монтаж которых производится за счет пистолета. Метизы в этом случае тоже обозначаются, как и предыдущие.
Если рассматривать стандарты производства, то можно выделить следующие:
- отрывные крепежные элементы с цилиндрической формой головки DIN 7337, ISO 15977, ISO 15979, ISO 15981, ISO 15983, ISO 16582;
- вариант, оснащенный потайным вариантом головки DIN 7337, ISO 15978, ISO 15980, ISO 15984.
Способы для измерения размера шплинта
Предусмотрено три варианта шплинтов, при этом для каждого применяется свой метод измерения.
У разводных шплинтов в число размеров входит условный диаметр. Значение параметра определяется показателем диаметра отверстия, предназначенного для монтажа. Примечательно, что реальный диаметр крепежного элемента имеет меньшие размеры, чем условный. Возможная разница между ними указана в ГОСТ 397-79.
Для нахождения длины разводного шплинта существует специальный способ. Метиз отличается коротким и длинным концом, поэтому требуется измерить участок от изгиба ушка крепежного элемента до окончания с короткой стороны.
Игольчатый вариант шплинтов характеризуется фиксированной длиной, регулируемой нормативом DIN 11024. Чтобы узнать размер метиза, требуется проверить показатели диаметра шплинта.
Быстросъемные метизы, оснащенные кольцом, тоже отличаются фиксированной длиной. Для конструкций применяется DIN 11024. Чтобы узнать размер крепежного элемента, воспользуйтесь полученными показателями диаметра.
Как измерять гайку
Большинство гаек имеют метрическую резьбу. Для измерения показателя диаметра резьбы потребуется чуть больше действий, чем в остальных случаях. По возможности рекомендуется проверять размер не самой гайки, а болта или винта, используемого для нее. Так можно добиться более точного результата.
Значение, которое получилось после измерения внутренней резьбы, является показателем внутреннего диаметра dвн.
Для того, чтобы точно определить диаметр метрической резьбы метиза, потребуется узнать соответствие dвн наружному диаметру используемого болта. Это производится с помощью специальной таблицы.
Точность контролируется за счет применения определенных калибров “проход-непроход”. Одна часть должна хорошо соединяться с гайкой, вторая часть наоборот, не должна.
Гайки отличаются по своему виду, и его легко определить при детальном осмотре. Чтобы узнать стандарт крепежного элемента, может потребоваться измерение высоты метиза, поскольку встречаются высокие, низкие, особо высокие и другие варианты.
Также для классификации шестигранных гаек используются габариты “под ключ”. Это объясняется тем, что метизы также различаются своими видами.
Для точного измерения шага резьбы допускается применение способа, рассматриваемого в случае с болтом. Понадобится резьбомер или придется посчитать количество витков на необходимом промежутке.
Определение размеров дюймовых гаек
Чтобы проверить размеры резьбы дюймовой гайки, необходимо рассмотреть резьбу болта или другого метиза, используемого с ней. Если подходящего нет под рукой, но есть информация о наличии дюймовой резьбы, то воспользуйтесь соответствующим резьбомером. При этом не забывайте разделять полученное значение на 25,4 мм.
Определение размеров шайбы
Для шайб используется короткое обозначение в виде D, что расшифровывается как диаметр метрической резьбы метиза, который применяется для крепежного элемента.
Чтобы точно измерять показатели, подойдет линейка или штангенциркуль. В результате получается значение, которое немного превышает показатель в обозначении. Это объясняется тем, что при монтаже требуется свободный ход, для чего выполняется небольшой зазор.
Как выполнить чертеж по инженерной графике Резьбовые изделия
Как выполнить чертеж по инженерной графике: тема 7 «Резьбовые изделия»
Часто студентам задают задание по инженерной графике из книги Фролова/Бубенникова 1990 года редакции, в теме №7 необходимо выполнить вот такой чертеж — «Резьбовые изделия».
Вот полное задание Вычертить: 1) болт, гайку, шайбу по их действительным размерам, которые следует взять из соответствующих стандартов;
2) упрощенное изображение этих же деталей в сборе;
3) гнездо под резьбу, гнездо с резьбой, шпильку отдельно и шпильку в сборе с гайкой и шайбой по их действительным размерам, которые следует взять из соответствующих стандартов.
Пошаговое выполнение на примере 2-го варианта:
1) Болт, гайка, шайба по действительным размерам
Согласно варианту, задан болт с резьбой М18 с крупным шагом резьбы ( это 2,5 мм для диаметра 18 мм, на обозначении шаг не указывается, указывается только мелкий шаг) длина болта 80 мм, исполнение 2 по ГОСТ 7796-70, находим этот ГОСТ в поисковике и открываем.
ГОСТ 7796-70 “Болты с шестигранной уменьшенной головкой класса точности В”
В нем мы найдем все необходимые размеры, по ним и будем вычерчивать вычерчивать болт в двух проекциях.
Над болтом пишем условное обозначение Болт 2 М18-6g x 80.58, что означает болт исполнения 2 с метрической резьбой М18 с крупным шагом, длиной 80 мм, с полем допуска 6g и классом прочности 5.8 без покрытия.
Поле допуска, устанавливающее величину зазоров между резьбой на стержне (болта, винта, шпильки) и в отверстии (гайки), выбирают по ГОСТ 16093-81. Установлены следующие поля допусков:
для резьбы на стержне — 4h, 6h, 6g, 6e, 6d, 8h, 8g;
для резьбы в отверстии — 4Н5Н, 5Н6Н, 6Н, 6G и 7Н, 7G
От поля допусков 4h до поля 8g для стержней и от поля допусков 4Н до 7G для отверстий зазоры увеличиваются, т. е. резьба изготовляется все с меньшей точностью. Студенты могут ограничиться этими сведениями, не обращаясь к указанному стандарту.
Класс прочности для болтов, винтов, шпилек выбирают из ряда 3.6; 4.6; 4.8; 5.6; 5.8; 6.6; 6.8; 6.9; 8.8 по ГОСТ 1759—86,
а для гаек — из ряда 4, 5, 6, 8 и т.д..
При указании класса прочности в обозначении резьбового изделия точки между цифрами не ставят, т. е. пишут 36 вместо 3.6; 46 вместо 4.6 и т. д.
Желательно, чтобы студент уяснил физическую сущность этих чисел, прочитав указанный стандарт, но основное, что надо запомнить, это то, что чем больше число, тем прочнее материал.
На учебных чертежах, выполняемых по курсу инженерной графики, допускается условно принимать, что болты, винты, шпильки изготовлены из углеродистой стали класса прочности 5.8 (в обозначении пишется 58), а гайки — из той же стали класса прочности 5, что резьба выполнена с полем допуска 6g (бывший класс точности 2) для болтов, винтов и шпилек и 6Н для гайки и что они не подвергались защитным (антикоррозионным) или декоративным покрытиям.
ГОСТ 15521-70 «Гайки шестигранные с уменьшенным размером «под ключ». класса точности В.»
Открываем ГОСТ и смотрим необходимые размеры, вычерчиваем гайку с резьбой М18 исполнения 2.
Гайка исполнения 2 отличается от гайки исполнения 1 тем, что у нее фаска сделана не с обеих, а с одной стороны.
Условное обозначение гайки исполнеия 2 с диаметром резьбы d=18 мм, с крупным шагом резьбы с полем допуска 6Н, класса прочности 5, без покрытия:
Гайка 2М18-6Н.5 ГОСТ 15521-70
ГОСТ 6402-70 “Шайбы пружинные. Технические условия.”
Вычерчиваем шайбу – Шайба 18.65Г ГОСТ 6402-70,
где 65Г — пружинная марганцовистая сталь;
2) Упрощенное изображение болта, гайки и шайбы в сборе
В методичке есть такой рисунок с конструктивными размерами и формулами.
По заданному диаметру болта (18мм) по формулам определяем все необходимые размеры и по ним вычерчиваем упрощенное изображение болтового соединения
3) Гнездо под резьбу, гнездо с резьбой, шпилька и шпильку в сборе
Таблица с заданием по вариантам
ГОСТ 22034-76.
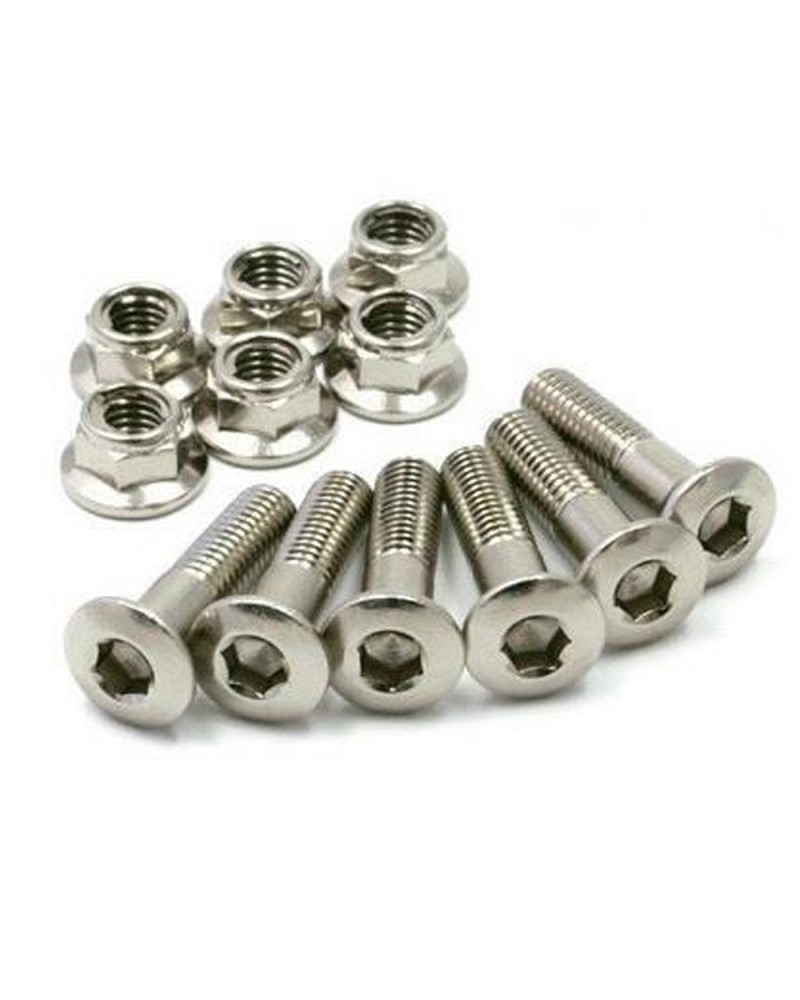
Вычерчиваем шпильку М18 длиной 55 мм ГОСТ 22034-76 согласно заданию.
Шпилька М18-6gx120.58 ГОСТ 22034-76
Расчёт резьбового гнезда под шпильку
Шпилька в сборе с гайкой ГОСТ 5915-70 и шайбой ГОСТ 11371-78
По действительным размерам, которые берем из соответствующих стандартов. ГОСТы находим их в поисковике, смотрим размеры и вычерчиваем всё в сборе.
Купить готовый чертеж по этой теме любого варианта можно ЗДЕСЬ!!!
Раздел: Инженерная графика /
- Рекомендуем
- Комментарии
- Наши товары
ГОСТ 20700-75 Болты, шпильки, гайки и шайбы для фланцевых и анкерных соединений, пробки и хомуты с температурой среды от 0 до 650 °С.

БОЛТЫ, ШПИЛЬКИ, ГАЙКИ И ШАЙБЫ
ДЛЯ ФЛАНЦЕВЫХ И АНКЕРНЫХ СОЕДИНЕНИЙ, ПРОБКИ И
ХОМУТЫ С ТЕМПЕРАТУРОЙ СРЕДЫ ОТ 0 ДО 650°С
Технические условия
ГОСТ 20700-75*
(CT СЭВ 1066-78)
ГОСУДАРСТВЕННЫЙ СТАНДАРТ СОЮЗА ССР
БОЛТЫ, ШПИЛЬКИ, ГАЙКИ И ШАЙБЫ ДЛЯ ФЛАНЦЕВЫХ И АНКЕРНЫХ СОЕДИНЕНИЙ, ПРОБКИ И ХОМУТЫ С ТЕМПЕРАТУРОЙ СРЕДЫ ОТ 0 ДО 650°С Технические условия Bolts, studs, nuts and washers for flanged and anchor connections, |
ГОСТ 20700-75* (CT СЭВ 1066-78) |
Постановлением Государственного комитета стандартов Совета Министров СССР от 28 марта 1975г. № 794 срок введения установлен
с 01. 01.76
Проверен в 1985г. Постановлением Госстандарта от 27.12.85 № 4667 срок действия продлен
до 01.01.96
Несоблюдение стандарта преследуется по закону
Настоящий стандарт распространяется на болты, шпильки, гайки и шайбы для фланцевых и анкерных соединений паровых котлов, трубопроводов и соединительных частей, паровых и газовых турбин, арматуры, приборов, аппаратов и резервуаров, пробки для турбин и трубопроводов, хомуты круглого сечения для опор и подвесок трубопроводов с температурой среды от 0 до 650°С и водогрейных котлов с температурой воды свыше 115°С.
Стандарт не распространяется на фланцевые соединения объектов, подведомственных Госгортехнадзору СССР, с условным давлением менее 0,07 МПа (0,7 кгс/см2).
Стандарт полностью соответствует CT СЭВ 1066-85.
(Измененная редакция, Изм. № 1, 2, 3).
1. ТЕХНИЧЕСКИЕ ТРЕБОВАНИЯ
1.1. Болты, шпильки, гайки, пробки, хомуты и шайбы (далее — крепежные изделия) следует изготовлять по ГОСТ 9064-75, ГОСТ 9065-75, ГОСТ 9066-75 или по рабочим чертежам из стали марок, указанных в табл. 1.
(Измененная редакция, Изм. № 2).
1.2. Условия применения марок стали, указанные в табл. 1, по температуре и давлению рабочей среды для болтов, шпилек и гаек фланцевых соединений объектов, подведомственных Госгортехнадзору СССР, должны соответствовать «Правилам устройства и безопасной эксплуатации паровых и водогрейных котлов» (утверждены 30 августа 1966г.), «Правилам устройства и безопасной эксплуатации трубопроводов тара и горячей воды» (утверждены 10 марта 1970г.), «Правилам устройства и безопасной эксплуатации сосудов, работающих под давлением» (утверждены 19 мая 1970г.).
(Измененная редакция, Изм. № 1).
1.3. Для изготовления крепежных деталей необходимо применять стали, выплавленные в мартеновских печах, электропечах, методами электрошлакового и вакуумно-дугового переплава или по другим, как минимум, равноценным технологическим процессам. Не допускается использование для крепежных изделий кипящей, полуспокойной, бессемеровской и автоматной стали.
(Новая редакция, Изм. № 3).
1.4. Материалы для изготовления крепежных деталей должны выбираться в зависимости от расчетной температуры металла и разделяются по качеству на:
категорию I — углеродистые стали с техническими требованиями к изделиям общего назначения класс точности В с номинальным диаметром резьбы до 48 мм, расчетной температурой металла изделия до 200°С;
категорию II — углеродистые стали, применяемые для болтов, шпилек, пробок, хомутов и гаек класс точности А с номинальным диаметром резьбы до 48 мм и шайб всех размеров с расчетной температурой металла изделия до 300°С. Углеродистые стали обыкновенного качества по ГОСТ 380-71, поставляемые с контролем ударной вязкости после механического старения, для изделий повышенной точности с предельными параметрами по табл. 1;
категорию III — качественные углеродистые стали в улучшенном состоянии, применяемые для болтов, шпилек, пробок, хомутов и гаек всех размеров с рабочей температурой до 400°С в случаях, если температура отпуска выше этой температуры не менее чем на 100°С. Допускается применение сталей III категории до расчетной температуры металла 425°С при наличии данных по длительной прочности при соответствующей расчетной температуре.
категорию IV — теплоустойчивые, жаропрочные легированные стали в термически обработанном состоянии, применяемые для крепежных изделий всех размеров с рабочей температурой не более температуры среды (табл. 1 и п. 1.2) в случаях, если температура отпуска выше этой температуры не менее чем на 100°С, а последняя ступень старения для сплавов выше этой температуры не менее чем на 50°С.
(Измененная редакция, Изм. № 3).
1.4.1. Заготовки болтов, шпилек, гаек, пробок и хомутов всех категорий качества после холодного и горячего деформирования должны подвергаться окончательной термообработке. После накатки резьбы термообработка не требуется.
(Введен дополнительно, Изм. № 3).
1.5. Марки стали II-IV категорий должны подвергаться сплошному визуальному и выборочному входному контролю на твердость и макроструктуру предприятием-изготовителем крепежных изделий. Объем контроля по твердости должен быть не менее 2% от партии заготовок.
Контроль макроструктуры следует производить на двух темплетах от партии только для легированных марок стали. Макроструктура стали и твердость в исходном состоянии должны соответствовать стандартам на поставку материала.
При неудовлетворительных результатах контроля на твердость сталь III и IV категорий должна быть подвергнута высокому отпуску или отжигу. Рекомендуемые режимы высокого отпуска или отжига и твердость — по приложению 5.
Допускается дополнительный химический анализ материала заготовок производить предприятием-изготовителем крепежных изделий.
Допускается дополнительный сплошной ультразвуковой контроль (УЗК) заготовок.
(Измененная редакция, Изм. № 3).
1.6. В зависимости от назначения и условий работы крепежных деталей устанавливается пять групп качества готовых изделий, указанных в табл. 2.
1.7. Для болтов, шпилек и гаек из стали I и II категорий классы прочности, механические свойства, напряжения от пробной и испытательной нагрузок по ГОСТ 1759-70.
Допускается изготовлять болты, шпильки, гайки, пробки и хомуты из стали I и II категорий с механическими свойствами или твердостью по ГОСТ 380-71, ГОСТ 1050-74, ГОСТ 1051-73, ГОСТ 10702-78.
1.8. При изготовлении гаек по 1 и 2-й группам качества нормы механических свойств устанавливаются по соглашению между изготовителем и потребителем.
Для крепежных изделий из сталей III и IV категорий режимы термической обработки заготовок, нормы механических свойств на продольных образцах при нормальной (20°С) температуре и твердость для болтов, шпилек, пробок и хомутов 1, 2, 3 и 4-й групп качества и для гаек 3 и 4-й групп качества должны соответствовать указанным в табл. 3.
Для шайб нормы твердости устанавливаются в соответствии со стандартами на марки стали, указанными в табл. 1.
Допускается термическая обработка гнутых хомутов в готовом виде при условии защиты резьбы от окисления.
1.9. Крепежные изделия с рабочей температурой до 200°С могут изготовляться с покрытием. Вид, толщина и условные обозначения покрытий — по ГОСТ 1759-70.
Для крепежных изделий с рабочей температурой металла выше 200°С следует применять покрытия, не снижающие прочность и работоспособность соединений.
1.4-1.9(Измененная редакция, Изм. № 1, 2).
1.10. Защитные покрытия должны быть однородными, пузыри и отслаивания не допускаются.
1.11. Нормы на глубину обезуглероженного слоя для крепежных изделий из стали I и II категорий с номинальными диаметрами резьбы до 48 мм — по ГОСТ 1759-70. Обезуглероженный слой для болтов, шпилек и резьбовой поверхности гаек и обработанных в готовом виде хомутов для диаметров свыше 12 мм из стали III и IV категорий не допускается.
(Измененная редакция, Изм. № 1, 2).
1.12. При выборе марок стали крепежных деталей в зависимости от категории качества при проведении расчетов на прочность крепежных изделий следует использовать следующие характеристики механических свойств:
для крепежных деталей из стали I и II категории механические свойства или твердость при 20°С по ГОСТ 1759-70 или ГОСТ 380-71, ГОСТ 1050-74, ГОСТ 1051-73 и ГОСТ 10702-78;
для крепежных деталей из стали III категории механические свойства и твердость по табл. 3. Гарантируемые значения предела текучести при 350°С — по ГОСТ 23304-78;
для крепежных деталей из стали IV категории — механические свойства и твердость по табл. 3, гарантируемые значения предела длительной прочности и предела ползучести, обеспечиваемые на уровне согласованных норм путем соблюдения режима термической обработки и уровня механических свойств по табл. 3.
Нормы длительной прочности и предел ползучести устанавливаются по соглашению сторон. Средние значения предела длительной прочности и предела ползучести сталей IV категории приведены в справочных приложениях 1 и 1.а.
1.13. Средние значения модуля нормальной упругости, коэффициентов линейного расширения, релаксационной стойкости (остаточного напряжения) сталей приведены в справочных приложениях 2-4
1.12-1.13(Новая редакция, Изм. № 3).
Таблица 1
Марка стали | Обозначение стандарта | Предельные параметры | |||||
---|---|---|---|---|---|---|---|
Болты, шпильки, пробки и хомуты | Гайки | Шайбы | |||||
Температура среды, ºС | Условное давлениеРу,МПа (кгс/см2) | Температура среды, ºС | Условное давлениеРу,МПа (кгс/см2) | Температура среды, ºС | Условное давлениеРу,МПа (кгс/см2) | ||
ВСт3сп3 | ГОСТ 380-71 | — | — | — | — | До 350 | 10(100) |
ВСт3сп5 ВСт4сп3 ВСт4сп5 ВСт5сп2 ВСт5сп5 |
До 350 | 1,6(16) | До 350 | 2,5(25) | |||
— | 2,5(25) | — | — | ||||
10 | ГОСТ 1050-74 | — | — | До 350 | 2,5(25) | До 450 | |
20 | До 400 | 1,6(16) | До 400 | 10(100) | |||
25 30, 35, 40 45 |
ГОСТ 1050-74 ГОСТ 10702-78 |
— | — | ||||
До 425 | 10(100) | До 425 | 20(200) | До 450 | Не ограничено | ||
35Х, 40Х | ГОСТ 10702-78 | 20(200) | До 450 | 20(200) | — | — | |
30ХМА, 35ХМ | ГОСТ 4543-71 | До 450 | Не ограничено | До 510 | Не ограничено | — | — |
20Х13 (2Х13) | ГОСТ 18968-73 | До 450 | Не ограничено | ||||
15ХМ | ГОСТ 4543-71 | — | — | — | — | До 545 | |
25Х1МФ (ЭИ10) | ГОСТ 20072-74 | До 510 | Не ограничено | До 540 | Не ограничено | — | — |
13Х11Н2В2МФ(ЭИ961) | ГОСТ 5949-75 | ||||||
25Х2М1Ф (ЭИ723) | ГОСТ 20072-74 | До 535 | До 565 | — | — | ||
15Х11МФ (1Х1 1МФ) 20Х12ВНМФ (ЭП428) 18Х11МНФБ (ЭП291) |
ГОСТ 18968-73 | До 560 | До 560 | До 580 | Не ограничено | ||
18Х12ВМБФР (ЭИ993) | ГОСТ 5949-75 | ||||||
12Х1МФ (12ХМФ) | ГОСТ 20072-74 | — | — | — | — | До 570 | Не ограничено |
20Х1М1Ф1ТР (ЭП182) 20Х1М1Ф1БР (ЭП44) |
До 580 | Не ограничено | До 580 | Не ограничено | — | — | |
08Х16Н131М2Б (ЭИ680) | — | До 625 | До 625 | До 650 | Не ограничено | ||
31Х19Н9МВБТ (ЭИ572) | ГОСТ 5949-75 | — | — | ||||
ХН35ВТ (ЭИ612) | — | До 650 | До 650 | — | — | ||
10Х11Н22Т3МР (ЭИ696М) | — | ||||||
12Х1.![]() 08Х18Н10Т (0Х18Н10Т) |
ГОСТ 5949-75 | — | — | — | — | До 650 | Не ограничено |
Примечания: |
Таблица 2
Группа качества готовых изделий и заготовок | Вид испытания | Количество изделий от партии | Номенклатура сдаточных характеристик |
---|---|---|---|
1 | Определение механических свойств | 100% | Значение предела текучести σ0,2, сужения поперечного сечения y, ударной вязкости KCU (aн) и твердости НВ |
Определение твердости | 100% | ||
2 | Определение механических свойств | 2%, но не менее 2 шт.![]() |
Значение предела текучести σ0,2, сужения поперечного сечения y и ударной вязкости KCU (ан) |
Определение твердости | 100% | ||
3 | Определение твердости | 100% | Значение твердости НВ |
4 | Определение твердости | 2%, но не менее 2 шт. | Значение твердости НВ |
5 | Без испытаний | — | — |
Примечания: |
1.14. Шероховатость поверхностей крепежных изделий, предназначенных для нанесения покрытий, — по ГОСТ 9. 301-78.
(Измененная редакция, Изм. № 2).
1.15. Крепежные детали должны иметь метрическую резьбу по ГОСТ 24705-81, выполненную нарезкой или накаткой. При подготовке стержня под накатку резьбы допускается гладкая конусная часть между концом сбега и безрезьбовой частью стержня длиной не более двух шагов резьбы.
В случае применения болтов, шпилек и гаек, пробок и хомутов из сталей 31Х19Н9МВБТ (ЭИ572), ХН35ВТ (ЭИ612), 08Х16Н13М2Б (ЭИ680) при рабочей температуре металла более 500°С накатка резьбы не допускается.
(Измененная редакция, Изм. № 1, 2, 3).
1.15.1. Диаметр резьбы болтов, шпилек и гаек резервуаров, работающих под давлением, должен соответствовать указанному в ГОСТ 12.2.073-82, для других крепежных изделий — не менее M12.
1.15.2. Типы шпилек для фланцевых изделий — по ГОСТ 9066-75
1.15.1; 1.15.2(Введены дополнительно, Изм. № 3).
1.16. Размеры сбегов и недорезов резьбы — по ГОСТ 10549-80, фасок для деталей с диаметром резьбы до 24 мм — по ГОСТ 12414-66, с диаметром резьбы более 24 мм — ширина фас-ми в пределах 0,7 — 2 шага резьбы.
При применении метода накатки разрешается изготовлять резьбу без концевой фаски, три этом не допускается вогнутость (лунка) опорных поверхностей значением более половины допуска на высоту головки или высоту гайки, но не более 1,5 шага резьбы.
(Измененная редакция, Изм. № 2).
1.17. Отклонения формы и расположения поверхностей и дефекты внешнего вида болтов, шпилек, гаек, пробок и хомутов диаметром резьбы до 48 мм из стали I категории должны соответствовать классу точности В, из стали II-IV категорий — классу точности А — по ГОСТ 1759-70, для болтов и гаек, пробок и хомутов диаметром резьбы свыше 48 мм — классу точности А по ГОСТ 18126-72.
Отклонение от перпендикулярности опорной плоскости и оси резьбы гаек типа А диаметром до 48 мм из стали II-IV категорий не более 30, а диаметром свыше 52 мм — по 12-й степени точности ГОСТ 24643-81.
Отклонение от перпендикулярности опорной плоскости и оси резьбы гаек типа Б диаметром до 42 мм — по 11-й степени точности, а диаметром свыше 48 мм — по 10-й степени точности ГОСТ 24643-81.
Отклонение от плоскостности шайб — не более допуска на толщину шайбы.
Отклонение от перпендикулярности боковых поверхностей шайб к опорным не свыше 3°.
Для шпилек с номинальным диаметром резьбы свыше 48 мм не допускаются:
косой срез стержня для шпилек типов А и Б в пределах 0,7-2 шага резьбы;
риски и следы от режущего инструмента, выводящие размеры изделий за предельные отклонения;
уменьшение высоты профиля резьбы с уменьшением ее наружного диаметра более чем на двух концевых витках;
закругление вершины профиля накатанной резьбы, выводящее наружный диаметр резьбы за предельные отклонения;
смещение оси резьбы относительно гладкой части стержня свыше IT12 (базовый размер для вычисления допуска — наружный диаметр резьбы).
Таблица 3
Марка стали | Термообработка, ºС | Диаметр (толщина) заготовки, мм | Категория прочности | Болты, шпильки, пробки и хомуты | Гайки | ||||||||||||||
---|---|---|---|---|---|---|---|---|---|---|---|---|---|---|---|---|---|---|---|
закалка (3) нормализация (Н) аустенизация (А) | отпуск | предела текучести σ0,2, (кгс/мм2) | предела прочности σв, МПа (кгс/мм2) | относительное удлинение δ, % | относительное сужение ψ, % | ударная вязкость KCU (ан), кДж/м2(кгс·м/см2) | число твердости НВ | диаметр отпечатка, мм | число твердости НВ, не более | диаметр отпечатка, мм | |||||||||
не менее | |||||||||||||||||||
Категория III.![]() |
|||||||||||||||||||
20 | — | — | — | — | — | — | — | — | — | — | — | По ГОСТ 1050-74 | |||||||
25 | Н. 870-890 | 620-680 | — | — | — | — | — | — | — | 143 | Св. 5,0 | ||||||||
30 | Н. 860-890 | — | — | — | — | 149 | Св.![]() |
||||||||||||
35 | Н. 850-880 | 600-680 | До 60 | 28 | 274 (28) | 530 (54) | 20 | 40 | 490 (5,0) | 156…207 | 4,8-4,2 | 149 | Св. 4,9 | ||||||
Св. 60 до 100 | 441 (4,5) | ||||||||||||||||||
Св. 100 до 300 | 17 | 38 | 343 (3,5) | ||||||||||||||||
40 | Н. 850-890 или 3. 840-860 вода или масло | До 60 | 30 | 294 (30) | 549 (56) | 18 | 40 | 490 (5,0) | 163.![]() |
4,7-4,3 | 156 | Св. 4,8 | |||||||
Св. 60 до 100 | 392 (4,0) | ||||||||||||||||||
Св. 100 до 300 | 16 | 37 | 343 (3,5) | ||||||||||||||||
45 | Н. 830-870 или 3. 830-870 вода или масло | До 60 | 32 | 314 (32) | 578 (58) | 17 | 38 | 490 (5,0) | 167…217 | 4,65-4,1 | 163 | Св. 4,7 | |||||||
Св. 60 до 100 | 392 (4,0) | ||||||||||||||||||
Св. 100 до 300 | 14 | 35 | 343 (3,5) | ||||||||||||||||
Категория IV.![]() |
|||||||||||||||||||
35Х, 40Х | З. 840-870, масло | 500-620 вода или масло | До 100 | 60 | 588-735 (60-75) | 735 (75) | 14 | 45 | 588 (6,0) | 235…285 | 3,95-3,6 | 217…187 | 4,1-4,4 | ||||||
Св. 100 до 300 | 13 | 40 | 490 (5,0) | ||||||||||||||||
30ХМА | З. 870-800 вода или масло | 540-620 | До 100 | 65 | 637 784 (65-80) | 784 (80) | 13 | 42 | 588 (6,0) | 229.![]() |
4,0 3,65 | 217…187 | 4,1-4,4 | ||||||
Св. 100 до 300 | 12 | 38 | 490 (5,0) | ||||||||||||||||
35ХМ | З. 850-880 масло | 560-650 | До 100 | 13 | 42 | 588 (6,0) | |||||||||||||
Св. 100 до 300 | 12 | 38 | 490 (5,0) | ||||||||||||||||
25Х1 МФ (ЭИ 10) | З. 930-950 вода и масло | 620-710 | До 200 | 68 | 667-784 (68-80) | 16 | 50 | 588 (6.0) | 241…277 | 3,9-3,65 | 229…197 | 4,0-4,3 | |||||||
25Х2М1Ф (ЭИ723) | Н.![]() |
680-700 | До 200 | 68 | 667-784 (68-80) | 781 (80) | 12 | 50 | 490 (5,0) | 241…277 | 3,9-3,65 | 229…197 | 4,0-4,3 | ||||||
20Х1М1Ф1ТР (ЭП182) | З. 970-990 масло | 680-720 | 15 | 588 (6,0) | |||||||||||||||
20Х1М1Ф1БР (ЭП44) | З. 970-990 масло | 680-720 | 14 | ||||||||||||||||
20Х13(2Х13) | З. 1000-1050 воздух или масло | 650-720 | — | 60 | 588-735 (60-75) | 15 | 45 | 229.![]() |
4,0-3,6 | 217…269 | 3,7-4,1 | ||||||||
55 | 539-686 (55-70) | 686 (70) | 50 | 269…217 | 3,7-4,4 | — | — | ||||||||||||
15Х11МФ (1Х11МФ) | З. 1060-1100 воздух или масло | 680-750 | — | — | — | — | — | — | — | — | 217…187 | 4,1-4,4 | |||||||
1Х12Н2ВМФ (ЭИ961) | З. 1000-1020 масло | 660-680 | До 100 | 70 | 686-833 (70-85) | 833 (85) | 15 | 55 | 882 (9,0) | 269.![]() |
3,7-3,4 | — | — | ||||||
20Х12ВНМФ (ЭП428) | З. 10140-1060 масло | 680-720 | До 200 | 68 | 667-784 (68-80) | 784 (80) | 45 | 588 (6,0) | 241…285 | 3,9-3,6 | 229…197 | 4,0-4,3 | |||||||
18Х12ВМБФР (ЭИ993) | З. 1030-1050 масло | ||||||||||||||||||
18Х11МНФБ (ЭП291) | З. 1080-1100 масло | 700-740 | — | — | |||||||||||||||
08Х16Н13М2Б (ЭИ680) | А. 1100-1130 воздух | Старение 750±10; 10ч | Не ограничивается | — | — | — | — | — | — | — | — | 187.![]() |
4,4-5,0 | ||||||
10X11h32T3MP (ЭИ696М) | — | 780±10; 16ч+650±10; 16ч | 70 | 685 (70) | 980 (100) | 12 | 14 | 490 (5,0) | 388…302 | 3,1-3,5 | — | — | |||||||
31Х19Н9МВБТ (ЭИ572) | А. 1140-1180 вода | Старение 750-800; 15ч | 32 | 314 (32) | 588 (60) | 30 | 40 | 588 (6,0) | Не менее 187 | Не более 4,4 | |||||||||
ХН35ВТ (ЭИ612) | А. 1080-1100 1-1,5 ч вода | Старение 850-900; 10ч+700±10; 10-50ч | 40 | 392 (40) | 735 (75) | 15 | 25 | ||||||||||||
Примечания: |
(Измененная, дополненная редакция, Изм. № 3).
1.18. Допускаемая кривизна стержней болтов и шпилек не должна превышать 0,2 мм, прямых участков хомутов — 0,4 мм на 100 мм длины для диаметров резьб до 24 мм; 0,1 мм и 0,2 мм соответственно на 100 мм длины для диаметров свыше 24 мм.
Для болтов и шпилек, подвергаемых химико-термической обработке в чистовых размерах, допускаемая кривизна не должна превышать норм, указанных в чертеже изделия и согласованных с потребителем.
Допуск прямолинейности прямых участков хомута не должен превышать допускаемые отклонения размера между концами хомута.
1.19. Не допускаются рванины и выкрашивания ниток резьбы крепежных изделий диаметром резьбы до 48 мм, превышающие нормы, установленные ГОСТ 1759-70, ГОСТ 1759.2-82, ГОСТ 1759.3-83, для крепежных изделий (кроме шпилек) с диаметром резьбы свыше 48 мм, превышающие нормы, установленные ГОСТ 18126-72.
Не допускаются рванины и выкрашивания ниток резьбы шпилек с диаметром резьбы свыше 48 мм, если они по глубине выходят за пределы среднего диаметра резьбы или их длина превышает 1% общей длины резьбы по винтовой линии, а в пределах одного витка — 30 мм для шпилек с диаметром резьбы до 100 мм и 40 мм для шпилек с диаметром резьбы свыше 100 мм.
Не допускаются вмятины на резьбе, препятствующие ввинчиванию проходного калибра. На резьбовой поверхности крепежных изделий II-IV категорий волосовины не допускаются.
1.20. Обработанная поверхность готовых изделий не должна иметь трещин, надрывов, закатов, рванин, плен и несмываемой ржавчины.
На нерезьбовой обработанной поверхности крепежных изделий 1-й группы качества при визуальном осмотре волосовины не допускаются.
На нерезьбовой обработанной поверхности крепежных изделий 2-5-й групп качества при визуальном осмотре не допускаются волосовины, превышающие нормы, указанные в табл. 4.
Для крепежных изделий из стали I категории и стали обыкновенного качества II категории волосовины не регламентируются.
1.17-1.20.(Измененная редакция, Изм. № 1, 2).
1.21. Уступ при сверлении центрального отверстия с двух сторон на длине стержня между резьбами (шпильки типов В, Г и Д) не допускается.
1.22. Допускается изготовление шпилек с центровым отверстием по ГОСТ 14034-74.
1.23. Отклонение от перпендикулярности оси гнезда под рым-болт в шпильках типов В, Г и Д — по ГОСТ 4751-73.
1.22, 1.23(Измененная редакция, Изм. № 1).
1.24. Уклон граней шестигранников штампованных колпачковых гаек не более 1°30‘.
1.25. Шайбы не должны иметь заусенцев и острых кромок.
1.26. В резьбовом соединении выступающая часть резьбы болта, шпильки, хомута должна составлять не менее полутора витков с каждой стороны завернутой гайки. Уменьшение наружной выступающей части резьбы болта, шпильки, хомута с номинальным диаметром резьбы до 48 мм допускается, если гайка изготавливается по ГОСТ 9064-75 и одновременно обеспечивается несущая длина резьбы по ГОСТ 1759-70.
1.26(Введен дополнительно, Изм. № 3).
2. ПРАВИЛА ПРИЕМКИ
2.1. Правила приемки крепежных деталей по внешнему виду и размерам — по ГОСТ 17769-83; для крепежных деталей, подвергаемых химико-термической обработке, — по рабочим чертежам.
2. 2. Крепежные детали предъявляются к приемке партиями. Партия должна состоять из изделий одного типоразмера, изготовленных из одной партии заготовок с покрытием одного типа.
2.2.1. Партия болтов, шпилек, гаек и шайб должна иметь массу, кг, не более, для диаметров:
до М16……………………….. 150
от М20 до М27……………. 400
от М30 до М39……………. 750
от М42 и более……………. 1000
Масса партии крепежных деталей, предназначенных для комплектования оборудования, а также масса партии пробок и хомутов не ограничивается.
2.2.2. Для деталей группы качества 2 партия заготовок должна состоять из стали одной марки, одной плавки и одной садки при термической обработке.
Для деталей групп качества 1, 3 и 4 партия заготовок должна состоять из стали одной марки, одной плавки, одной садки при термической обработке или одинакового режима термической обработки (закалка или нормализация плюс отпуск).
Для деталей группы качества 5 партия заготовок должна состоять из стали одной марки, одной садки при термической обработке или одинакового режима термической обработки.
2.1-2.2(Новая редакция, Изм. № 3).
Таблица 4
Общая площадь контролируемой безрезьбовой обработанной поверхности детали, см2 | Количество волосовин | Максимальная длина волосовин, мм, не более | Суммарная протяженность волосовин, мм, не более | ||
---|---|---|---|---|---|
Металл открытой выплавки | Металл электрошлакового и вакуумно-дугового переплава | ||||
Металл открытой выплавки | Металл электрошлакового и вакуумно-дугового переплава | ||||
До 50 | 2 | 1 | 3 | 5 | 3 |
Св. 51 до 100 | 3 | 2 | 3 | 8 | 5 |
» 101 » 200 | 4 | 2 | 4 | 10 | 6 |
» 201 » 300 | 6 | 3 | 4 | 15 | 8 |
» 301 » 400 | 8 | 4 | 5 | 20 | 10 |
» 401 » 600 | 9 | 5 | 6 | 30 | 18 |
» 601 » 800 | 10 | 5 | 6 | 40 | 24 |
» 801 » 1000 | 11 | 6 | 7 | 50 | 30 |
» 1001 » 1200 | 12 | 6 | 7 | 55 | 30 |
» 1201 » 1400 | 13 | 6 | 7 | 60 | 30 |
» 1401 » 1600 | 14 | 7 | 7 | 65 | 35 |
» 1601 » 1800 | 15 | 7 | 7 | 70 | 35 |
» 1801 » 2000 | 16 | 7 | 7 | 75 | 35 |
» 2001 » 2200 | 17 | 8 | 7 | 80 | 40 |
» 2201 » 2400 | 18 | 8 | 7 | 86 | 40 |
» 2401 » 2600 | 19 | 8 | 7 | 90 | 40 |
» 2601 » 2800 | 20 | 9 | 7 | 95 | 45 |
» 2801 » 3000 | 21 | 9 | 7 | 100 | 45 |
» 3000 » 3200 | 22 | 9 | 7 | 105 | 45 |
» 3201 » 3400 | 28 | 10 | 7 | 110 | 50 |
» 3401 » 3600 | 24 | 10 | 7 | 115 | 50 |
» 3601 » 3800 | 25 | 10 | 7 | 120 | 50 |
» 3800 » 4000 | 26 | 10 | 7 | 125 | 50 |
Примечания: |
2.3. Для каждой группы качества крепежных деталей номенклатура обязательных сдаточных характеристик, объем и виды контроля указаны в табл. 2.
(Новая редакция, Изм. № 3).
Контроль механических свойств должен проводиться на окончательно термически обработанных заготовках. Допускается оценку механических свойств проводить на образцах от припусков на готовых изделиях 1 и 2-й групп качества.
Допускается для крепежных изделий из стали I и II категорий вместо испытаний механических свойств на образцах проводить испытания самих крепежных изделий по ГОСТ 1759-70 в объеме 2% от партии, но не менее 2 шт.
Выбор метода испытаний осуществляется предприятием-изготовителем крепежных изделий.
(Измененная редакция, Изм. № 1).
2.4. Метод отбора проб для катанных заготовок — по ГОСТ 7564-73, для поковок — по ГОСТ 8479-70.
При определении механических свойств от каждой контролируемой заготовки или от припуска контролируемого изделия, или от отдельной пробы от изделия, подвергаемого химико-термической обработке, должны быть отобраны: один образец на растяжение и три на ударную вязкость.
Допускается для крепежных деталей, применяемых при рабочем давлении до 4 МПа при условии контроля твердости в объеме 2% от партии, отбирать от партии массой не более 1000 кг:
для стали I категории один образец на растяжение;
для стали II категории один образец на растяжение и два на ударную вязкость.
Допускается для крепежных деталей, применяемых при рабочем давлении до 4 МПа, для стали I и II категорий в случае массового и серийного производства, отлаженной технологии изготовления крепежных изделий объем контроля определять методами математической статистики по ГОСТ 20736-75.
2.4.(Новая редакция, Изм. № 3).
2.5. При длине изделия свыше 600 мм твердость термически обработанных (закалка или нормализация плюс отпуск) заготовок из сталей III и IV,категорий должна определяться на обоих концах; при этом разница в значениях твердости на одной заготовке не должна превышать 20 единиц по Бринеллю (НВ).
2.6. При неудовлетворительных результатах испытания хотя бы одного образца, испытания повторяют на удвоенном количестве образцов, отобранных от тех же заготовок или деталей, или от других заготовок и деталей с той же твердостью. Повторные испытания проводят по показателям, по которым получены неудовлетворительные результаты. Если при повторных испытаниях хотя бы один из образцов даст показатели ниже предусмотренных в табл. 3, то результаты испытаний считают неудовлетворительными. Определение механических свойств проводят на заготовках или деталях с последующим уровнем твердости.
2.7. Партия крепежных изделий может быть представлена к сдаче снова после ее пересортировки по показателям твердости. Повторная термическая обработка готовых изделий не допускается.
Партия заготовок, механические свойства которых проверялись непосредственно на заготовках, может быть допущена к изготовлению крепежных изделий после пересортировки по показателям твердости или после повторной термической обработки после контрольных испытаний в объеме табл. 2.
При неудовлетворительных результатах повторных испытаний партию заготовок бракуют.
Количество повторных термических обработок заготовок не должно превышать двух, при этом дополнительный отпуск заготовок и нагрев под химико-термическую обработку не считают повторной термической обработкой.
(Измененная редакция, Изм. № 1).
2. 8. Контроль обезуглероженного слоя проводят на одном шлифе от партии для крепежных изделий, изготовленных методом накатки резьбы на калиброванные заготовки из стали перлитного класса.
При выполнении резьбы способом нарезки (со снятием металла с поверхности заготовок) контроль обезуглероженного слоя не проводится.
(Измененная редакция, Изм. № 2).
2.9. По соглашению между изготовителем и потребителем производят выборочную оценку предела текучести, длительной прочности или условного предела ползучести 10-5%/ч металла болтов и шпилек при расчетной температуре.
2.9.(Новая редакция, Изм. № 3).
2.10. Готовые крепежные изделия должны подвергаться сплошному наружному осмотру, проверке размеров резьбы, проверке общих размеров изделия, шероховатости поверхности, проверке маркировки.
2.11. Нормы допустимых дефектов при УЗК — по ГОСТ 23304-78.
(Введен дополнительно, Изм. № 2).
3. МЕТОДЫ ИСПЫТАНИЯ
3. 1. Химический состав стали определяют по ГОСТ 22536.0-77 — ГОСТ 22536.13-77, ГОСТ 20560-81, ГОСТ 12344-78, ГОСТ 12345-80, ГОСТ 12346-78, ГОСТ 12347-77, ГОСТ 12348-78, ГОСТ 12349-83, ГОСТ 12350-78, ГОСТ 12351-81, ГОСТ 12352-81, ГОСТ 12353-78, ГОСТ 12354-81, ГОСТ 12355-78, ГОСТ 12356-81, ГОСТ 12357-84, ГОСТ 12358-82, ГОСТ 12359-81, ГОСТ 12360-82, ГОСТ 12361-82, ГОСТ 12362-79, ГОСТ 12363-79, ГОСТ 12364-84 или другими методами, обеспечивающими требуемую точность.
(Измененная редакция, Изм. № 2).
3.2. Определение твердости (п. 1.8) — по ГОСТ 9012-59, поверхностно-упрочненного слоя — по ГОСТ 9013-59
(Измененная редакция, Изм. № 3).
3.3. Испытания на растяжение образцов (п. 1.8) — по ГОСТ 1497-84.
3.4. Испытания на ударную вязкость (п. 1.8) — по ГОСТ 9454-78 (образец типа I).
3.5. Испытания крепежных изделий с номинальным диаметром резьбы до 48 мм из стали II категории на пробную и испытательную нагрузку (п. 1.7) — по ГОСТ 1759-70.
3. 6. Испытания на длительную прочность (п. 1.12) — по ГОСТ 10145-81, на ползучесть — по ГОСТ 3248-81.
(Измененная редакция, Изм. № 3).
3.7. Определение глубины обезуглероженного слоя (п. 1.11) проводят по микроструктуре в соответствии с ГОСТ 1763-68. Допускается производить контроль другими методами, обеспечивающими точность не ниже метода оценки по микроструктуре.
3.8. Контроль шайб — по ГОСТ 18123-82.
3.9. Наружный осмотр готовых изделий на отсутствие дефектов производят визуально без применения увеличительных приборов. Допускается использование других методов неразрушающего контроля, принятых на предприятии-изготовителе, при этом результаты не являются сдаточными.
3.10. Проверка отклонения от перпендикулярности боковой поверхности (1.17) гаек относительно опорной должна производиться шаблонами или угломерами.
3.11. Остальные методы испытаний — по ГОСТ 1759-70, ГОСТ 18126-72 и ГОСТ 18123-82.
3.12. Ультразвуковой контроль — по ГОСТ 24507-80.
(Введен дополнительно, Изм. № 2).
4. МАРКИРОВКА, УПАКОВКА, ТРАНСПОРТИРОВАНИЕ И ХРАНЕНИЕ
4.1. Общие требования к временной противокоррозионной защите, упаковке, транспортированию, хранению и маркировке тары — по ГОСТ 18160-72 и ГОСТ 9.014-78.
(Измененная редакция, Изм. № 2).
4.2. Болты, шпильки и гайки, пробки и хомуты, изготовленные из стали I и II категорий, следует маркировать по ГОСТ 1759-70.
4.3. На торце гаечного конца болтов, шпилек всех типов, гаек типа Б и на боковой поверхности гаек типа А и шайб маркируют: товарный знак предприятия-изготовителя, марку материала, условное обозначение методов выплавки для электрошлакового переплава — Ш и вакуумно-дугового переплава — ВД, номер партии (плавки).
По требованию потребителя маркируется категория стали и группа качества изделия.
Допускается на крепежных изделиях, предназначенных для оборудования, изготовляемого на том же предприятии, маркировать только номер партии.
Пробки маркируют на торце головки, хомуты — на прямом участке на расстоянии не менее 20 мм от резьбы.
4.2, 4.3.(Измененная редакция, Изм. № 1, 2).
4.4. Клеймить знак окончательной приемки.
4.5. Разрешается для болтов, шпилек и гаек, пробок и хомутов диаметром до М27 и шайб толщиной до 10 мм маркировку наносить на бирке.
(Измененная редакция, Изм. № 1, 2).
4.6. Изделие с левой резьбой маркировать по ГОСТ 2904-45.
4.7. Шрифт и размеры знаков маркировки устанавливаются изготовителем. Знаки маркировки должны быть четкими, хорошо видными невооруженным глазом.
4.8. При наличии в маркировке обозначения марки стали взамен буквенно-цифрового написания по табл. 1, например 25Х1МФ, 25Х2М1Ф, 20Х1М1Ф1ТР и др., допускается условная маркировка соответственно ЭИ10, ЭИ723, ЭП182 и др.
4.9.(Исключен, Изм. № 2).
4.10. Крепежные изделия должны храниться в закрытом помещении.
4.11. Каждая партия крепежных деталей должна сопровождаться документом, удостоверяющим их соответствие требованиям настоящего стандарта.
Для крепежных деталей из стали I и II категории и давлением до 4 МПа документ должен содержать:
наименование предприятия-изготовителя,
тип и размер деталей,
число деталей и массу партии,
марку стали,
класс прочности или результаты испытаний,
обозначение настоящего стандарта,
штамп ОТК.
Для крепежных деталей из стали I и II категории и давлением свыше 4 МПа, а также для деталей из стали III и IV категории в документе дополнительно указывают:
способ выплавки стали для электрошлакового и вакуумно-дугового переплава,
химический состав,
категорию стали и группу качества готовых изделий,
результаты проведенных испытаний,
указания о применении защитных покрытий и характеристики покрытий.
4.11.(Новая редакция, Изм. № 3).
ПРИЛОЖЕНИЕ 1
Справочное
Пределы длительной прочности
Марка стали | Пределы длительной прочности, кгс/мм2, при температуре, °С | |||||||||
---|---|---|---|---|---|---|---|---|---|---|
425 | 450 | 500 | 525 | 550 | 565 | 580 | 600 | 650 | 700 | |
30ХМА, 35ХМ | 34 29 |
30 23 |
||||||||
25Х1МФ (ЭИ10) | 55 45 |
46 37 |
26 17 |
|||||||
25Х2М1Ф (ЭИ723) | 33 25 |
27 20 |
16-22 (14) 540° |
|||||||
20Х1М1Ф1ТР (ЭП182) | 50 46 |
48 45 |
39 33 |
35 30 |
33 28 |
29 25 |
27 20 |
|||
20Х1М1Ф1БР (ЭП44) | 49 40 |
35 30 |
31 26,5 |
27,5 23,5 |
26 22 |
24 20 |
||||
20Х13 | 32 27 |
29,5 26 |
||||||||
15Х11МФ | 16-21 13-16 |
(14-16,5) | ||||||||
20Х12ВНМФ (ЭП428) | 50 48 |
39 35 |
22 | 24 19 |
||||||
18Х12ВМБФР (ЭИ993) | 48 42 |
36 31 |
560° 25 22 |
|||||||
13Х11Н2В2МФ (ЭИ961) | 35* 32,5 |
15* 10,5 |
||||||||
08Х16Н13М2Б (ЭИ680) | 26 21 |
20 15 |
13 9,5 |
|||||||
31Х19Н9МВБТ (ЭИ572) | 560° 30 26 |
23,5-27 20-24 |
18-21 15-17 |
|||||||
08Х18Н10Т (ОХ18Н10Т) | 25 20 |
21 17 |
15,5 13 |
13,5 10 |
8 6 |
5,5 | ||||
ХН35ВТ (ЭИ612) | 45 36 |
40 33 |
39 32 |
26-31 21-26 |
20 16 |
|||||
10Х11Н22ТЗМР | 50* 47,5 |
32,5* 31,0 |
15 | |||||||
*Данные за 25000 ч |
Приложение 1 (Новая редакция, Изм. № 3).
ПРИЛОЖЕНИЕ 1a
Справочное
Условный предел ползучести
Марка стали | Условный предел ползучести. кгс/мм2, при температуре ºC | ||||||||
---|---|---|---|---|---|---|---|---|---|
425 | 450 | 475 | 500 | 525 | 550 | 565 | 580 | 600 | |
30XM | 14 | 11 | |||||||
35ХМ | 13 | ||||||||
25Х1М1Ф (ЭИ10) | 23 | 14,5 | 8 | ||||||
25Х2М1Ф (ЭИ723) | 7 | ||||||||
20Х1М1Ф1ТР (ЭП182) | 12 | 9,5 | |||||||
20Х1М1Ф1БР (ЭП44) | 24 | 16 | 11 | ||||||
20Х13 | 12,8 | 7,6 | 4,8 | 3 | |||||
15Х11МФ | 9 | ||||||||
20Х12ВНМФ (ЭП428) | 28 | 17 | 10-12 | ||||||
18Х12ВМБФР (ЭИ993) | 560° 15 |
||||||||
08Х16Н13М2Б (ЭИ680) | 16-18 | 9-12 | 5-7 | ||||||
31Х19Н9МВБТ(ЭИ572) | 560° 17 |
11-13 | 8-10 | ||||||
08Х18Н10Т (ОХ18Н10Т) | 7,5 | ||||||||
ХН35ВТ (ЭИ612) | 18 | 13-14 |
Приложение 1а (Введено дополнительно, Изм. № 3).
ПРИЛОЖЕНИЕ 2
Справочное
Марка стали | Модуль упругости Е·10-4, кгс/мм2, при температуре, ºС | |||||||||
---|---|---|---|---|---|---|---|---|---|---|
20 | 100 | 200 | 300 | 400 | 450 | 500 | 550 | 600 | 650 | |
10, 20, 25, 30, 35, 40 | 2,13 | 2,10 | 1,98 | 1,90 | 1,85 | — | 1,79 | — | — | — |
35Х, 40Х, 15ХМ, 30ХМА, 35ХМ | 2,18 | 2,15 | 2,08 | 2,01 | 1,92 | — | 1,79 | — | — | — |
12Х1МФ (12ХМФ), 25Х1МФ (ЭИ10), 25Х2М1Ф (ЭИ723), 20Х1М1Ф1ТР (ЭП182), 20Х1М1Ф1БР (ЭП44) |
2,15 | 2,12 | 2,08 | 2,02 | 1,94 | — | 1,83 | 1,77 | 1,70 | — |
20Х13 (2Х13), 15Х11МФ (1Х11МФ), 20Х12ВНМФ (ЭП428), 18Х11МНФБ (ЭП291), 1Х12Н2ВМФ (ЭИ961), 18Х12ВМБФР (ЭИ903) |
2,28 | 2,22 | 2,13 | 2,05 | 1,93 | — | 1,84 | 1,75* | 1,70 | — |
12Х18Н10Т (Х18Н10Т), 08Х18Н10Т (0Х18Н10Т), 08Х16Н13М2Б (ЭИ680), 31Х19Н9МВБТ (ЭИ572), ХН35ВТ (ЭИ612) |
2,05 | 2,02 | 1,97 | 1,90 | 1,81 | 1,80 | 1,73 | 1,70 | 1,65 | 1,60 |
10Х11Н22ТЗМР (ЭИ696М) | 1,9 | 1,81 | 1,69 | 1,58 | 1,48 | 1,42 | 1,37 | 1,33 | 1,31 | 1,30 |
* При 565 ºС модуль упругости равен 1,73. |
ПРИЛОЖЕНИЕ 3
Справочное
Марка стали | Коэффициент линейного расширения α·106в интервале температур, °С | |||||||
---|---|---|---|---|---|---|---|---|
20-100 | 20-200 | 20-300 | 20-400 | 20-500 | 20-550 | 20-600 | 20-700 | |
10, 20, 25, 30, 35, 40, 45 | 11,35 | 12,36 | 12,93 | 13,44 | 14,1 | — | — | — |
35Х, 40Х, 15ХМ, 30ХМА, 35ХМ | 11,6 | 12,3 | 12,8 | 13,55 | 14,0 | — | — | — |
12Х1МФ (12ХМФ), 25Х1МФ (ЭИ10), 25Х2М1Ф (ЭИ723), 20Х1М1Ф1ТР (ЭП182), 20Х1М1Ф1БР (ЭП44) |
11,65 | 12,4 | 12,8 | 13,3 | 13,5 | 13,7 | 14,3 | — |
20Х13 (2Х13), 15Х11МФ (1Х11МФ), 20Х12ВНМФ (ЭП428), 18Х11МНФБ (ЭП291), 1Х12Н2ВМФ (ЭИ961), 18Х12ВМБФР (ЭИ903) |
10,5 | 10,8 | 11,1 | 11,5 | 11,8 | — | 12,05 | — |
12Х18Н10Т (Х18Н10Т), 08Х18Н10Т (0Х18Н10Т), 08Х16Н13М2Б (ЭИ680), 31Х19Н9МВБТ (ЭИ572), ХН35ВТ (ЭИ612), 10Х11Н22ТЗМР (ЭИ696М) |
15,3 | 15,9 | 16,5 | 16,9 | 17.![]() |
— | 17,7 | 18,2 |
ПРИЛОЖЕНИЕ 4
Справочное
Марка стали | Твердость, НВ или σ0,2 | Температура испытания, ºС | s0, кгс/мм2 | Остаточное напряжение кгс/мм1, за время, ч | |||||||||
---|---|---|---|---|---|---|---|---|---|---|---|---|---|
100 | 500 | 1000 | 2000 | 3000 | 4000 | 5000 | 8000 | 10000 | 12000 | ||||
20 | — | 200 | 10 | 9,4 | 9,2 | 9,2 | 9,0 | 9,0 | — | (8,6) | — | (8,2) | — |
15 | 11,1 | 10,5 | 10,9 | 10,7 | 10,5 | — | (10,2) | — | (9,7) | — | |||
18 | 11,7 | 11,2 | 11,2 | 11,0 | 10,8 | — | (10,5) | — | (10,0) | — | |||
300 | 10 | 8,8 | 8,7 | 8,7 | 8,6 | 8,5 | — | (8,3) | — | (8,0) | — | ||
15 | 10,6 | 10,3 | 10,3 | 10,1 | 10,1 | — | (9,8) | — | (9,6) | — | |||
400 | 10 | 7,8 | 7,3 | 7,3 | 7,0 | 7,0 | — | (6,8) | — | (6,5) | — | ||
12 | 8,5 | 8,1 | 8,0 | 7,7 | 7,6 | — | (7,0) | — | — | — | |||
450 | 7 | 4,8 | 4,5 | 4,1 | — | — | — | (3,7) | — | (2,9) | — | ||
19 | 6,6 | 6,2 | 6,0 | — | — | — | — | — | — | — | |||
40Х | НВ 269 | 300 | 27 | 25,5 | 25,0 | 24,5 | — | — | — | 23,0 | — | — | — |
НВ 207 | 26 | 23,5 | 22,5 | 22,0 | — | — | — | 20,0 | — | — | — | ||
НВ 207 | 350 | 19 | 15,5 | 14,0 | 13,5 | — | — | — | 11,5 | — | — | — | |
27 | 21,0 | 19,0 | 18,0 | — | — | — | 15,0 | — | — | — | |||
42 | 29,5 | 27,0 | 26,0 | — | — | — | 21,5 | — | — | — | |||
40Х | НВ 207 | 400 | 23 | 12,0 | 10,0 | 8,5 | — | — | 7,0 | — | — | — | — |
29 | 13,5 | 10,5 | 9,8 | — | — | 7,8 | — | — | — | — | |||
36 | 14,0 | 11,0 | 10,0 | — | — | 8,6 | — | — | — | — | |||
НВ 262 | 20 | 17,8 | 17,1 | 16,9 | — | 15,9 | — | 14,7 | — | 13,5 | — | ||
25 | 22,4 | 21,5 | 21,2 | — | 20,0 | — | 19,5 | — | 18,2 | — | |||
30ХМА 35XM | НВ 269 | 400 | 15 | 8,9 | 6,8 | 6,5 | — | — | — | (5,3) | — | (4,5) | — |
25 | 13,8 | 10,6 | 9,9 | — | — | — | (7,7) | — | (6,4) | — | |||
35 | 19,0 | 13,6 | 12,0 | — | — | — | (9,8) | — | (8,2) | — | |||
30ХМА 35XM | НВ 269 | 450 | 15 | 8,3 | 6,6 | 6,1 | — | — | — | (4,7) | — | (3,3) | — |
25 | 12,3 | 9,3 | 8,7 | — | — | — | (6,8) | — | (5,2) | — | |||
25Х1МФ (ЭИ10) | НВ 293 | 500 | 15 | 9,5 | 8,3 | 7,8 | 7,2 | 6,9 | — | (5,7) | — | (3,8) | — |
25 | 14,8 | 12,8 | 12,0 | 11,0 | 10,4 | — | (9,3) | — | (7,2) | — | |||
35 | 19,7 | 17,1 | 16,0 | 15,1 | 14,0 | — | (12,5) | — | (9,4) | — | |||
525 | 20 | — | 8,0 | — | 5,0 | — | — | — | — | — | — | ||
20Х1М1Ф1ТР (ЭП182) | σ0,2=75 кгс/мм2 | 450 | 25 | 21,5 | — | 20,7 | — | 20,3 | — | 20,1 | 19,7 | 19,4 | 19,4 |
30 | 25,8 | — | 25,0 | — | 24,3 | — | 23,8 | 23,6 | 23,2 | 23,2 | |||
35 | 29,8 | — | 28,8 | — | 28,1 | — | 27,5 | 27,2 | 27,0 | 26,9 | |||
500 | 25 | 20,2 | — | 19,3 | — | 18,6 | — | 18,2 | 17,6 | 17,4 | — | ||
30 | 24,3 | — | 22,8 | — | 22,5 | — | 21,9 | 21,3 | 20,7 | 20,3 | |||
35 | 28,2 | — | 26,2 | — | 25,2 | — | 24,9 | 24,3 | 24,2 | 22,6 | |||
565 | 20 | 14,4 | — | 13,2 | — | 11,6 | — | 11,2 | 10,5 | 10,3 | — | ||
25 | 17,5 | — | 15,0 | — | 13,5 | — | 12,4 | 11,6 | 11,1 | 9,7 | |||
30 | 19,8 | — | 17,5 | — | 15,5 | — | 14,3 | 13,3 | 13,1 | — | |||
35 | 22,4 | — | 19,1 | — | 16,8 | — | — | — | (14,5) | — | |||
580 | 25 | 16,2 | — | 14,0 | — | 12,3 | — | 11,6 | 10,2 | 8,7 | — | ||
30 | 17,7 | — | 15,1 | — | 13,8 | — | 12,9 | 11,2 | 10,5 | 10,5 | |||
35 | 20,6 | — | 17,5 | — | 15,0 | — | 13,3 | — | (11,5) | — | |||
25Х2М1Ф (ЭИ723) | σ0,2=78 кгс/мм2 | 500 | 30 | — | — | — | — | 17,5 | — | — | — | 16,5 | — |
35 | — | — | — | — | 20,0 | — | — | — | 17,0 | — | |||
525 | 25 | — | 15,0 | 14,5 | 13,6 | 13,0 | — | — | 11,5 | 10,8 | — | ||
30 | — | 19,7 | 17,0 | 16,0 | 15,5 | — | — | 13,5 | 10-13 | — | |||
35 | — | 20,2 | 19,0 | 17,0 | 16,5 | — | — | 14,5 | 12-13,5 | — | |||
550 | 25 | — | 13,0 | 11,0 | 10,5 | 10,0 | — | — | 7,3 | 4,3-6,7 | — | ||
30 | — | 16,0 | 14,5 | 12,5 | 11,0 | — | — | 8,0 | 7,0 | — | |||
35 | — | 17,7 | 16,0 | 14,0 | 12,5 | — | — | 8,5 | 7,5 | — | |||
20Х1М1Ф1БР (ЭП44) | σs0,2=68-80 кгс/мм2 | 450 | 25 | 21,5 | 21,2 | 21,0 | 20,8 | 20,6 | 20,3 | 20,0 | 19,6 | 19,5 | 19,3 |
30 | 25,5 | 25,0 | 24,8 | 24,5 | 24,2 | 24,0 | 23,7 | 23,4 | 23,2 | 23,0 | |||
25 | 30,0 | 29,5 | 28,8 | 28,5 | 28,0 | 27,8 | 27,5 | 27,2 | 27,0 | 26,7 | |||
500 | 25 | 21,0 | 19,5 | 19,2 | 18,7 | 18,5 | 18,2 | 18,0 | 17,5 | (17,0) | — | ||
30 | 24,0 | 22,5 | 22,0 | 21,8 | 21,6 | 21,0 | 20,6 | 20,3 | (20,0) | — | |||
35 | 29,0 | 27,5 | 26,5 | 26,0 | 25,5 | 24,8 | 24,2 | 23,5 | (23,0) | — | |||
565 | 25 | 16,5 | 15,5 | 14,3 | 13,2 | 12,5 | 12,0 | 11,5 | 10,8 | 10,3 | 10,0 | ||
30 | 20,0 | 18,0 | 17,3 | 15,5 | 15,0 | 14,3 | 14,0 | 13,2 | 13,0 | 12,8 | |||
35 | 22,6 | 20,0 | 19,0 | 17,6 | 17,0 | 16,5 | 16,0 | 15,0 | 14,5 | 14,0 | |||
580 | 25 | 15,7 | 13,5 | 12,7 | 11,7 | 11,0 | 10,6 | 10,4 | 10,0 | 9,8 | 9,5 | ||
30 | 15,0 | 16,3 | 15,3 | 14,0 | 13,2 | 12,5 | 12,0 | 11,0 | 10,8 | 10,5 | |||
35 | 22,0 | 19,5 | 17,5 | 16,0 | 15,0 | 14,0 | 13,5 | 12,0 | 11,5 | — | |||
20Х12ВНМФ (ЭП428) | НВ 269 | 400 | 25 | 21,7 | — | 20,8 | — | 20,5 | — | 20,5 | — | (20,5) | — |
30 | 25,7 | — | 24,6 | — | 24,3 | — | 23,9 | — | (23,5) | — | |||
35 | 29,8 | — | 28,6 | — | 28,0 | — | 27,9 | — | (27,5) | — | |||
40 | 34,0 | — | 32,5 | — | 32,2 | — | 32,0 | — | (31,5) | — | |||
450 | 25 | 19,6 | — | 18,5 | — | 18,1 | — | 17,9 | — | 17,5 | 16,4** | ||
30 | 23,3 | — | 22,1 | — | 21,5 | — | 21,0 | — | 20,5 | 19,4** | |||
35 | 27,0 | — | 25,4 | — | 24,7 | — | 24,4 | — | 24,0 | 22,5** | |||
40 | 30,6 | — | 28,4 | — | 27,4 | — | 26,8 | — | 26,5 | — | |||
500 | 25 | 16,8 | — | — | — | 13,5 | — | 13,0 | — | 11,3 | 10,3** | ||
30 | 20,0 | — | — | — | 17,0 | — | 16,0 | — | 14,0 | 12,2** | |||
35 | 23,0 | — | — | — | 18,8 | — | 18,0 | — | 16,0 | 14,4** | |||
565 | 35 | 16,0 | — | 12,5 | — | 11,0 | — | 9,5 | — | 7,0 | — | ||
30* | 23,0 | — | 18,0 | — | 15,0 | — | 14,0 | — | 12,5 | — | |||
35* | 25,0 | — | 19,5 | — | 17,0 | — | 16,0 | — | 14,0 | 19,4*** | |||
18Х12ВМБФР (ЭИ 993) | σ0,2=68-80 кгс/мм2 | 450 | 25 | 21,0 | — | 20,5 | — | — | 20,0 | — | — | — | 19,4*** |
30 | 25,0 | — | 24,5 | — | — | 23,9 | — | — | — | 23,0*** | |||
35 | 28,5 | — | 28,0 | — | — | 27,2 | — | — | — | 26,3*** | |||
500 | 25 | 19,7 | — | 18,4 | — | — | 17,2 | — | — | — | — | ||
30 | 23,0 | — | 21,5 | — | — | 20,3 | — | — | — | — | |||
35 | 26,9 | — | 24,9 | — | — | 23,2 | — | — | — | — | |||
565 | 25 | 15,0 | 14,3 | 13,4 | 12,6 | 12,3 | 11,6 | 11,2 | 10,2 | 9,8 | — | ||
30 | 17,5 | 16,8 | 15,8 | 14,8 | 14,6 | 13,9 | 13,7 | 12,1 | 11,5 | — | |||
35 | 20,4 | 19,0 | 18,3 | 17,0 | 16,4 | 16,0 | 15,5 | 13,5 | 13,0 | — | |||
580 | 30 | 22,0 | 15,0 | 13,9 | 12,0 | 11,5 | 11,0 | 10,8 | 9,8 | 9,0 | — | ||
35 | 20,5 | 17,5 | 16,0 | 14,0 | 13,2 | 13,0 | 12,5 | 11,0 | 10,5 | — | |||
08Х16Н13М2Б (ЭИ680) | НВ 143.![]() |
600 | 15 | 9,5 | 8,8 | 8,5 | — | 7,7 | — | 6,8 | — | — | — |
20 | 12,1 | 11,3 | 10,7 | — | 9,8 | — | 9,4 | — | — | — | |||
31Х19Н9МВБТ (ЭИ&7,2.) | НВ св. 207 | 560 | 20 | 15,5 | 14,7 | 14,4 | — | 13,9 | — | — | — | — | — |
20**** | 18,3 | 17,7 | 17,3 | — | 16,9 | — | — | — | — | — | |||
600 | 20 | 13,8 | 12,5 | 11,7 | — | — | 9,9 | — | — | — | — | ||
25 | 16,0 | 13,5 | 12,3 | — | — | 9,6 | — | — | — | — | |||
30 | 18,0 | 16,3 | 13,9 | — | — | 10,0 | — | — | — | — | |||
650 | 20 | 11,0 | 9,0 | 8,2 | — | — | 6,5 | — | — | — | — | ||
25 | 13,0 | 10,3 | 9,1 | — | — | 7,5 | — | — | — | — | |||
ХН35ВТ (ЭИ612) | НВ св.![]() |
500 | 45 | 35,0 | 34,4 | 34,3 | — | 33,8 | — | 32,6 | — | 32,4 | — |
600 | 15 | 13,9 | 13,8 | 13,7 | — | 13,6 | — | 13,5 | 13,5 | 13,0 | — | ||
20 | 18,2 | 18,0 | 17,9 | — | 17,6 | — | 17,3 | 17,1 | 17,0 | — | |||
25 | 22,3 | 21,9 | 21,7 | — | 21,3 | — | 20,9 | 20,4 | 20,0 | — | |||
30 | 25,3 | 24,9 | 24,6 | — | 23,9 | — | 23,4 | 22,7 | 22,5 | — | |||
650 | 15 | 13,2 | 13,0 | 12,8 | — | 12,1 | — | 11,8 | 11,5 | 11,2 | — | ||
20 | 17,5 | 16,8 | 16,4 | — | 15,6 | — | 14,9 | 14,3 | 14,0 | — | |||
25 | 21,0 | 20,5 | 19,9 | — | 18,4 | — | 18,0 | 16,6 | 16,0 | — | |||
45 | 25,0 | 24,2 | 23,2 | — | 20,3 | — | 19,0 | 17,4 | 16,5 | — | |||
10X11h32T3MP (ЭИ696М) | НВ 285.![]() |
450 | 25 | 23,7 | 23,7 | 23,7 | 23,5 | 23,5 | — | 23,2 | 23,0 | 22,8 | — |
35 | 32,8 | 32,8 | 32,7 | 32,7 | 32,6 | — | 31,5 | 30,5 | 30,0 | — | |||
45 | 42,6 | 42,6 | 42,2 | 42,2 | 42,2 | — | 41,5 | 40,8 | 40,0 | — | |||
500 | 25 | 23,3 | 23,1 | 23,0 | 22,9 | 22,9 | — | 22,8 | 22,7 | 22,6 | 22,4 | ||
35 | 32,5 | 32,4 | 32,1 | 31,9 | 31,8 | — | 31,5 | 31,4 | 31,3 | 31,2 | |||
45 | 41,8 | 41,7 | 41,2 | 41,1 | 41,0 | — | 40,7 | 40,3 | 40,1 | 40,0 | |||
650 | 15 | 13,1 | 11,4 | 10,9 | 10,0 | 9,5 | — | 9,0 | 7,1 | — | — | ||
25 | 21,4 | 17,8 | 14,5 | 12,6 | 11,7 | — | 10,3 | 8,5 | 7,8 | 7,1 | |||
35 | 28,3 | 23,4 | 18,6 | 16,2 | 14,8 | — | 12,6 | 9,1 | 8,8 | 8,2 | |||
45 | 34,9 | 28,5 | 23,1 | 19,7 | 17,8 | — | 15,7 | 12,5 | 11,5 | 10,9 | |||
В скобках экстраполированные значения: * — после повторных погружений через 50-10000 ч, ** — за 20000 ч, *** за 13000 ч, **** — повторное погружение через 25 ч. |
ПРИЛОЖЕНИЕ 5
Рекомендуемое
Марка стали | Твердость отожженной или высокоотпущенной стали | Рекомендуемые температуры отжига (высокого отпуска), ºС | |
---|---|---|---|
Диаметр отпечатка, мм, не менее | Число твердости НВ, не более | ||
35Х | 4,3 | 197 | 830-850 |
40Х | 4,1 | 217 | |
15ХМ | 4,5 | 179 | 850-870 |
30ХМА | 4,0 | 229 | |
35ХМ | 3,9 | 241 | |
12Х1МФ | 4,1 | 217 | 900-950 |
25ХИМФ (ЭИ10), 25Х2М1Ф (ЭИ72З), 20Х1М1Ф1ТР (ЭП182), 20Х1М1Ф1БР(ЭП44) |
4,0 | 229 | |
20Х13 (2Х13), 15Х11МФ(1Х11МФ) | 700-750 | ||
20Х12ВНМФ (ЭП428), 18Х11МНФБ (ЭП281), 18Х12ВМБФР (ЭИ993), 1Х12Н2ВМФ(ЭИ961) |
700-720 | ||
12Х18Н10ГГ(Х18Н10Т), 08Х18Н10Т(0Х18Н10Т), 08Х16Н13М2Б (ЭИ680), 31Х19Н9МВБТ (ЭИ572), 10Х11Н22ТЗМР (ЭИ696М), ХН35ВТ (ЭИ612) |
Сталь поставляется в горячекатаном (кованом) состоянии; твердость не ограничивается | — | |
Примечание. |
Просмотров: 11672
Дата первого показа: 21.07.2010 00:32:37
Дата публикации: 21.07.2010 00:32:07
Назад в раздел
Шпильки — Sigma Fasteners
Шпильки
Оцинкованные шпильки с гайками Используются при болтовых соединениях высокого давления для трубопроводов, бурения, нефтепереработки и нефтепереработки и в общей промышленности для уплотнения и фланцевых соединений. Все резьбовые, резьбовые и двойные шпильки составляют львиную долю отрасли. Болт-шпилька с полной резьбой представляет собой резьбовой стержень с 2 тяжелыми шестигранными гайками, в то время как конец метчика и двойной конец имеют гайку с постоянной резьбой, но имеют корпус посередине с одной гайкой.В конце метчика короткий конец шпильки разработан с посадкой UNC 3A, чтобы входить в резьбовое отверстие на корпусе более крупного механически обработанного или кованого оборудования.
Во фланцевом соединении размер, длина, диаметр и количество отверстий под болты зависят от типа фланца и класса давления фланца. Марки и размеры шпилек
определены отраслевыми стандартами ASTM A193 и ASME B16.5.
Стандартная резьба для болтов в США определяется в стандарте ASME / ANSI Unified Inch Screw Threads.Чаще всего используются унифицированные резьбы UN, UNC, UNF с шагом резьбы, соответствующим диаметру. Комбинации диаметра резьбы / шага измеряются числом резьбы на дюйм (TPI), сопровождающим каждый диаметр.
В Sigma мы производим шпильки из самых разных марок ASTM и экзотических высокопрочных сплавов. В разделе «Бронирование для Energy Book», посвященном шпилькам, содержится множество более мелких деталей о шпильках. Нравится, как закончены концы.
Концы для шпилек
По выбору производителя концы или острия могут быть скругленными (овальными), срезанными, плоскими или пропиленными и скошенными.В закругленном состоянии шип должен иметь овальную точку с радиусом, примерно равным одному диаметру основного шипа. При плоском и скошенном конце конец должен иметь фаску от диаметра, не превышающего меньший диаметр резьбы, чтобы получить длину фаски или неполной резьбы, приблизительно равную 2-кратному шагу резьбы.
Длина
Длина шпильки обычно измеряется встык или от начала до конца. Длина шпильки, измеренная параллельно оси, представляет собой расстояние от первой резьбы до первой резьбы.
Первая резьба определяется как пересечение большого диаметра резьбы с основанием острия. Шпильки обычно доступны с шагом 1/4 дюйма.
Материал
Мы можем производить болты диаметром 4 дюйма и длиной рукоятки более 4 футов на наших современных станках с ЧПУ. Мы отправляем метрическую резьбу, UN, UNC и UNF, присылаем нам длину и шаг резьбы, и мы будем работать для вас.
Таблица выбора материалов ASTM
Если вы не найдете в списке то, что вам нужно, позвоните нам или отправьте нам свой отпечаток или рисунок.Мы уверены, что сможем изготовить специальный болт по индивидуальному заказу!
Что такое шпильки? | Fastener Engineering
Шпильки, предназначенные для прикрепления (слева направо): вкручивание в дерево, приклеивание в композит и запрессовку в листовой металл.
Д-р Джоди Мюланер
Шпилька — это, по сути, кусок стержня с резьбой. Это часто напоминает крепежный винт без головки, хотя некоторые шпильки имеют головки, которые постоянно встраиваются в деталь, к которой они прикреплены.Шпильки часто предназначены для постоянного прикрепления к одной части, что является средством крепления другой части вместе с гайкой. Этот тип шпильки может быть приварен, обжат или приклеен для крепления и, следовательно, может иметь небольшую головку для этого.
Другие шпильки могут иметь резьбу на обоих концах. В некоторых случаях они оба предназначены для установки гаек — такая шпилька называется шпилькой. В качестве альтернативы, шпилька может иметь самоклеящуюся резьбу на одном конце, предназначенную для постоянного ввинчивания в деталь, и машинную резьбу на другом конце для установки гайки.Некоторые распространенные типы шпилек включают:
• Шпилька с полной резьбой: Тип шпильки, которая представляет собой всего лишь отрезок стержня с резьбой. Шпилька или шпилька — это также термин для стержня с резьбой. Его можно использовать для скрепления между собой больших деталей с гайками на каждом конце, чтобы сформировать болт. Есть много других применений этого типа шпильки в качестве регулируемого элемента для конструкций и машин. Гайки могут перемещаться по стержню на большое расстояние, создавая при этом большое усилие.
• Шпильки с ответвлением: Они имеют небольшую длину резьбы на одном конце и предназначены для ввинчивания в резьбовое отверстие. Тогда у них есть хвостовик и более длинная резьба на другом конце, чтобы принять гайку.
• Двухсторонние шпильки: Они имеют одинаковую длину с резьбой на каждом конце, предназначены для крепления гаек, с хвостовиком посередине.
• Сварной болт: Они имеют машинную резьбу по всей длине с тонкой широкой головкой, чтобы облегчить их приваривание, как правило, к стальным изделиям, обеспечивая прочно прикрепленную шпильку.
• Шпилька с зажимом: Они имеют небольшую коническую головку с зубцами, предназначенную для постоянного вдавливания в листовой металл при затягивании.
• Крепежная шпилька: Полноразмерная резьба с плоской широкой головкой, часто с отверстиями в головке. Предназначен для соединения с композитными деталями с помощью прочной металлической шпильки.
• Дюбель: У них есть винт для дерева на одном конце и крепежный винт на другом. Они предназначены для постоянного ввинчивания в дерево, обеспечивая шпильку для крепления детали с помощью гайки.Для затяжки используется либо гнездо на конце крепежного винта, либо шестигранная форма между двумя резьбами.
Шпилька— Полное руководство по крепежу для труб
Шпилька, гайки, крепежные болты и шайбы также известны как материал для болтов или крепеж. Болтовое соединение — это термин, который используется для затяжки / создания соединения фланцевых соединений. Затяжка фланца обеспечивает герметичное соединение между прокладкой и фланцами.
ФланцыASME имеют минимум четыре отверстия под болты, а для фланцев большего диаметра количество отверстий под болты всегда кратно четырем.Выбор количества отверстий под болты зависит от коэффициента, например
.- Размер фланца
- Рабочее давление
- Рабочая температура
- Материал фланца
Различные типы креплений, используемых в трубопроводах
Болт шпильки
Шпилька имеет резьбу по всей длине или на обоих концах. Как показано на изображениях. Если шайбы не используются, он состоит из трех компонентов (две гайки и шпилька). Если бы вы использовали шайбу, их стало бы пять. Иногда используются дополнительные гайки для гидравлического натяжения со шпилькой большего размера.
Длины шпильки должно быть достаточно, чтобы покрыть всю гайку плюс 1,5–3 открытых витка резьбы. Следует избегать использования длинных шпилек, так как это увеличивает вероятность коррозии и других повреждений открытой резьбы, что затруднит последующее удаление.
ASME B16.5 дает требуемый размер шпильки. Длина шпильки зависит от типа прокладки и требований к максимальной открытой резьбе.
Машинный болт
Болты имеют резьбу на одном конце и шестигранную головку на другом.См. Изображение ниже. При этом трубные болты используются с фланцами более низкой прочности, такими как GRE / GRP, бронза. Обычно шайбы используются с болтом, чтобы предотвратить чрезмерную нагрузку на фланец.
Гайки
Обычно шестигранные гайки тяжелой серии, используемые со шпильками. Неподшипниковая поверхность гайки имеет фаску, в то время как грузоподъемная поверхность подшипника обработана шайбой или может иметь фаску.
Шайба
Шайба — это тонкая пластина с отверстием в центре.Шайбы распределяют нагрузку на поверхность фланца; это предотвращает повреждение фланца. По этой причине для неметаллического фланца потребовались шайбы. Используются разные типы шайб, такие как плоские, разрезные и конические пружины. На изображении показаны плоские и разрезные шайбы.
Шайбы конические — это специальные шайбы. Также известна как шайба Belleville Springs. Он обеспечивает герметичность болтовых соединений в местах, где существует вибрация, дифференциальное тепловое расширение и ползучесть болтов.
Эти условия могут изменить нагрузку на шпильку, что может привести к ослаблению соединения.Конические шайбы обеспечивают пружинящий эффект и предотвращают ослабление шпильки. Эта шайба обеспечивает высокие пружинные нагрузки с небольшими прогибами.
Спецификация шпильки и стандарт
Различные стандарты ASME используются для шпилек и гаек при производстве болтовых материалов. Список таких стандартов приведен ниже.
- Диаметр и длина шпильки и болта описаны в стандартах ASME B16.5 и B16.47
- ASME B1.1 Унифицированная дюймовая резьба для винтов (серия сердечников и тонких резьб — обычно для шпилек, используемых в трубопроводах, используются резьбы Cores)
- ASME B18.2.1 для квадратных и шестигранных болтов и винтов
- ASME B18.2.2 Квадратные и шестигранные гайки
- ASME B18.21.1 Стопорные шайбы
- ASME B18.22.1 Плоские шайбы
Материал шпильки Марки
Материал болтовых соединений можно разделить на три группы
- Высокая прочность
- Промежуточная прочность
- Низкая прочность
Материалы шпилек
Список марок материалов ASTM, используемых для изготовления шпилек, приведен в ASME B16.5, который является стандартом для фланцев.
- Используются для работы при высоких температурах и давлении ASTM A193 Gr B7, B7M, B5, B8.
- Используются низкотемпературные условия ASTM A320 Gr L7, L7A, L7B.
- Легированная сталь, закаленная и отпущенная, шпильки и болты марки материалов: ASTM A354 Gr BC, BD.
- Для специального применения используются ASTM A540 Gr B21 — B24.
Из этих марок наиболее популярными материалами являются ASTM A193 Gr B7 и B7M.
Материалы гаек
Гайки могут быть изготовлены из того же материала, что и шпилька, или из совместимой марки ASTM A194
.- В стандарте ASTM A194 перечислены совместимые марки материалов для гаек, используемых со шпилькой и болтом.
- Наиболее широко используемые марки материалов — ASTM A194 Gr 2,2H, 2HM, 8,8M
Материалы шайб
Обычно для изготовления шайб используется марка материала
.- ASTM F436, ASTM F844, ASTM F959
- Если не указано иное, шайба может быть изготовлена из любого совместимого материала марки
Покрытие на шпильках и гайках
Иногда компоненты болтовых соединений покрываются различными материалами покрытия для повышения их коррозионной стойкости.Это снизит затраты на обслуживание. Общие покрытия
- Хромирование
- Оцинковка
- Xylan
- PTFE
- Цинк
Это покрытие вы можете увидеть на изображении.
Проверка шпилек
При визуальном осмотре проверьте наличие дефектов поверхности и общего качества продукции
- Проверка на наличие повреждений резьбы и плохого снятия фаски на головке гаек и концах шпильки
Следующее должно быть подтверждено во время проверки размеров шпилек
- Шаг резьбы
- Диаметр шпильки и болта
- Длина
- Размер головки болта и гаек
Требования к маркировке
Маркировка шпильки
Требования к маркировке шпильки и болта указаны в Стандарте материалов ASTM A193 и A320.Разметку нужно сделать на концах шпильки или на головке болта. Из-за ограниченного пространства на шпильке и болте нанесена маркировка производителя и марка / класс материала.
СтандартASTM дает список маркировочных знаков для различных марок материалов. Посмотрите на изображение ниже ASTM A193 Gr B7M, помеченное как B7 на одном конце и опознавательным знаком производителя на других концах. В случае болта с шестигранной головкой оба символа нанесены на головку болта.
Маркировка гайки
Стандарт материалов ASTM A194 и A563 устанавливает требования к маркировке гаек.Маркировка должна быть сделана на ненесущей поверхности гайки. Маркируются только опознавательный знак производителя и марка / класс материала.
Вместо полного описания материала используется символ материала, как показано выше. Список символов приведен в стандарте ASTM.
Что такое горячее болтовое соединение?
Удаление фланцевых болтов на линии и оборудовании, находящемся под напряжением, когда установка работает, называется болтовым креплением горячим способом. Есть много причин для горячего болтового соединения, например,
- Замена корродированных или поврежденных болтов
- Обновление спецификации материалов / марок болтов
- Сведите к минимуму время, затрачиваемое на освобождение болтов во время остановки завода
Закручивание болтов в горячем состоянии — опасное занятие, и при его выполнении необходимо проявлять особую осторожность.
Разница между болтами, винтами и шпильками
«Винты» — это общий термин для крепежных изделий. Это обычные слова. В их состав входят: болты, винты, гайки. Пока есть крепежные детали с резьбой, все винты, гайки, болты и винты имеют одну общую черту, а именно резьбу. Помимо ветки, какие еще отличия? Ниже я расскажу о различиях между болтами, винтами и шпильками. Как отличить винтовые крепления? Давайте разберемся!
1.Болт: Механические детали, цилиндрические резьбовые соединения с гайками. Тип крепежа, состоящий из головки и винта (цилиндр с внешней резьбой), должен быть снабжен гайкой для крепления двух деталей со сквозными отверстиями. Такой тип соединения называется болтовым. Если гайка откручивается от болта, можно разделить две части, поэтому болтовое соединение является разъемным.
2. Шпилька: Тип застежки без головки и только с резьбой на обоих концах.При соединении один конец необходимо вкрутить в деталь с отверстием с внутренней резьбой, другой конец пропустить через деталь со сквозным отверстием, а затем накрутить гайку, даже если две части скреплены вместе как одно целое. Этот тип соединения называется шпилькой и также является разъемным соединением. Он в основном используется в тех случаях, когда одна из соединяемых частей имеет большую толщину, требует компактной конструкции или не подходит для крепления болтами из-за частой разборки.
3. Винт: это также своего рода крепеж, состоящий из двух частей, головки и винта. По назначению его можно разделить на три категории: крепежный винт, установочный винт и специальный винт. Крепежный винт в основном используется для деталей с плотной резьбой и плотного соединения между деталями со сквозным отверстием и не требует установки гайки (этот тип соединения называется винтовым соединением и также является разъемным соединением; оснащен гайкой для надежного соединения двух частей со сквозными отверстиями.) Установочный винт в основном используется для фиксации относительного положения между двумя частями. Для подъема деталей используются винты специального назначения, например, рым-болты.
Использование классификации
1. Шпильки bm = 1d обычно используются для соединения двух стальных соединителей; Двусторонние шпильки bm = 1,25d и bm = 1,5d обычно используются для соединений чугуна со сталью. Связь между частями; Двусторонняя шпилька bm = 2d обычно используется для соединения соединительной детали из алюминиевого сплава и соединительной детали из стали.Первый соединитель имеет отверстие с внутренней резьбой, а второй соединитель имеет сквозное отверстие.
2. Оба конца двухголовых шпилек должны быть совмещены с гайками и шайбами для двух соединенных частей со сквозными отверстиями.
Один конец приварной шпильки приваривается к поверхности соединяемой детали, а другой конец (конец с резьбой) проходит через соединяемую деталь со сквозным отверстием, затем надевается шайба и накручивается гайка. чтобы соединить две соединенные части в одну деталь.
Шпильки двигателя: Понимание преимуществ использования шпилек по сравнению с болтами и советы по достижению надлежащих зажимных нагрузок | 2011-12-20
Текст и фото автора.
В очень многих случаях внимание производителя двигателей сосредоточено только на выборе правильных компонентов для конкретной конструкции двигателя, определении надлежащих зазоров, объема и потока впуска и выпуска, обработки поверхности и точной сборки. Резьбовые соединения, жизненно важное звено, соединяющее все вместе, часто воспринимаются как должное.Здесь мы обсудим множество вопросов и проблем, непосредственно связанных с наиболее важными компонентами любого двигателя — шпильками и болтами и обращением с ними.
Основные шпильки
Для эксплуатационных или тяжелых условий эксплуатации по возможности предпочтительно использование шпилек вместо основных болтов крышки в тех случаях, когда имеется выбор. Шпильки позволяют получить гораздо более точные значения крутящего момента, поскольку шпильки не скручиваются во время затяжки, как болты.Поскольку шпильки остаются неподвижными во время затяжки гайки, шпильки растягиваются только по одной оси, обеспечивая гораздо более равномерное и точное усилие зажима. Кроме того, поскольку использование шпилек приводит к меньшему износу резьбы блока, это продлевает срок службы резьбовых отверстий в блоке на периоды обслуживания / восстановления. Это особенно важно при работе с блоками из сплава. Использование шпилек также упрощает установку основной крышки и способствует выравниванию основной крышки. Вероятность смещения основного колпачка меньше, поскольку шпильки остаются неподвижными во время зажима колпачка.
Советы по установке шпильки главной крышки
Перед началом установки тщательно очистите блок, крышки и шпильки. Любой мусор на резьбе может легко повлиять на качество зацепления резьбы и привести к неправильным показаниям динамометрического ключа.
[PAGEBREAK]
Для того, чтобы отверстия с внутренней резьбой в блоке были чистыми и однородными, по ним следует выполнить чеканку. Никогда не используйте метчик для выполнения этой задачи, так как это приведет к срезанию, срезанию и удалению материала резьбы, что может снизить прочность резьбы.Вместо этого используйте только специальные метчики для нарезания резьбы, которые будут восстанавливать резьбу путем «формовки» вместо нарезания. Также убедитесь, что ваш динамометрический ключ правильно откалиброван. Все динамометрические ключи следует проверять на калибровку не реже одного раза в год (чаще при интенсивном использовании). Следует проверять даже новые динамометрические ключи, так как нередко даже некоторые новые ключи выходят из калибровки на целых 10 фунт-футов.
Используйте последовательные методы затяжки. Другими словами, не нужно быстро переходить на одни орехи и медленно на другие.Лучший способ — медленно «ползти» к заданному значению. Быстрое нажатие на динамометрический ключ с храповым механизмом до щелчка может привести к получению неравномерных и неточных значений.
В большинстве случаев ввинчивайте шпильки в блок ТОЛЬКО FINGER-TIGHT или с очень небольшим предварительным натягом (определенные производители могут рекомендовать от 8 до 10 фут-фунтов. Предварительного натяга) . Не затягивайте шпильку двумя гайками и сильно затягивайте. Помните — значение крутящего момента, указанное для установки, относится только к затяжке гайки, а не самой шпильки!
Если вам нужна «фиксированная» установка (фиксация шпилек на месте для облегчения обслуживания в будущем), шпильки могут быть химически приклеены к резьбе блока.Если в будущем потребуется удаление шпильки, нагревание приведет к разрушению компаунда. Если используется фиксирующий компаунд, не забудьте сразу установить основную крышку до схватывания компаунда, чтобы избежать любого возможного смещения шпилек по отношению к колпачку. Это означает установку колпачка и затяжку гаек в соответствии со спецификациями до затвердевания резьбовой смеси. Это позволяет приложить необходимый предварительный натяг к резьбовому соединению шпильки с блоком до того, как смесь затвердеет.
Помните: в использовании фиксирующего химического вещества нет необходимости, если только вы не хотите обеспечить положение шпильки во время многократных и поспешных замен основной крышки.
При установке шпилек просто убедитесь, что достигнуто полное зацепление резьбы. Другими словами, убедитесь, что шпильки находятся «снизу вверх», а все резьбы вошли в зацепление.
После установки шпилек установите основные крышки и проверьте совмещение шпильки с крышкой (проверьте на заедание — крышки должны плавно скользить по шпилькам).
Смажьте открытую (тонкую) резьбу шпилек, а также не забудьте смазать шайбы и гайки. ПРИМЕЧАНИЕ. Характеристики крутящего момента могут отличаться в зависимости от используемой смазки.Moly lube обеспечивает более стабильные показания крутящего момента, чем другие масла. Если используется Moly, обязательно соблюдайте требования к крутящему моменту для Moly. Если используется масло, следуйте спецификациям для масла. Спецификации будут другими! Если вы смазываете маслом, но затягиваете в соответствии со спецификациями, указанными для молибдена, затяжка будет недостаточной. Если вы используете молибден, но следуете спецификациям для масла, вы перетянете.
С установленными колпачками гайки следует трижды затянуть с указанным крутящим моментом. Как отмечалось ранее, если на резьбу от шпильки к блоку наносится фиксирующий компаунд, гайки необходимо затянуть до того, как компаунд затвердеет.
Если блок должен быть выровнен, для достижения наилучших общих (и оптимальных долгосрочных) результатов, блок следует выровнять после установки шпильки и основной крышки. Другими словами, если вы переходите на шпильки, не используйте болты для процесса хонингования. Основные заглушки необходимо закрепить теми же крепежами, которые будут установлены при окончательной сборке.
Шпильки головки цилиндров
Опять же, как и в случае основных шпилек, использование шпилек всегда предпочтительнее, чем болтов.Однако это может варьироваться в зависимости от приложения. При использовании двигателя на улице или в ситуации, когда головки блока цилиндров трудно или невозможно снять с установленным двигателем, шпильки могут быть не лучшим выбором с точки зрения обслуживания головки блока цилиндров. Например, если главный цилиндр или другой компонент предотвращает снятие или установку головки цилиндров с двигателем, установленным в транспортном средстве, болты могут быть лучшим выбором просто с точки зрения практичности. Однако, если позволяет ситуация, использование шпилек теоретически обеспечит более качественную сборку.
Использование шпилек головки блока цилиндров упрощает установку головки блока цилиндров с точки зрения прокладки и выравнивания головки. Это особенно полезно в случаях, когда приходится часто снимать головку.
С точки зрения функции, использование шпилек обеспечивает более точную и постоянную нагрузку крутящим моментом. Когда болт установлен, затяжка приводит как к скручиванию (скручивающая нагрузка), так и к растяжению (вертикальная или осевая нагрузка). Это приводит к тому, что болт подвергается воздействию двух сил одновременно, а также испытывает фрикционные нагрузки при резьбовом зацеплении.Когда гайка затягивается на шпильке, шпилька растягивается только по своей вертикальной оси. Открытый конец (верх) шпильки имеет «тонкую» резьбу, которая позволяет более точные и, следовательно, точные показания крутящего момента, когда гайка затягивается (или затягивается с крутящим моментом / углом) в соответствии со спецификацией.
[PAGEBREAK]
Советы по установке шпильки с головкой
Убедитесь, что резьба в блоке и на шпильках чистая, чтобы обеспечить точные показания крутящего момента. Это критично!
Поскольку во многих областях применения имеются резьбовые отверстия цилиндров, открытые для водяных рубашек, очень важно покрыть нижнюю часть (конец блока) резьбы шпильки качественным герметиком для резьбовых соединений.Если вы уверены, что отверстия не открыты для воды, вы можете пропустить этот шаг, но если сомневаетесь, нанесите герметик. Это не повредит. Как и в случае шпилек основной крышки, если вы предпочитаете, чтобы шпильки устанавливались более «постоянно», вы можете нанести на резьбу фиксирующий состав. ВНИМАНИЕ: Если вы планируете химически «зафиксировать» шпильки головки на месте, не используйте анаэробный фиксирующий состав, поскольку этот тип фиксирующего состава может расширяться при отверждении. В зависимости от толщины стенки цилиндра это может привести к растрескиванию стенки цилиндра (поскольку состав расширяется и оказывает давление на заднюю часть стенки).Если вы планируете зафиксировать шпильки на месте, лучшим выбором будет нерасширяющийся материал, такой как JB Weld или аналогичный. Если в будущем вам потребуется удалить шпильки, приложите к шпильке концентрированное тепло, которое разрушит состав настолько, чтобы можно было удалить шпильку.
Каждый раз, когда применяется фиксирующий компаунд, головка блока цилиндров должна быть установлена сразу после установки шпильки, чтобы гайки можно было затянуть до требуемого значения до схватывания компаунда (шпильки должны быть предварительно нагружены, чтобы установка могла происходить в надлежащем натянутом состоянии, для обеспечения соосности шпильки).Установите шпильки в блок только вручную (или с небольшим предварительным натягом, если рекомендуется). ЗАПРЕЩАЕТСЯ затягивать шпильки двумя гайками и сильно затягивать. Пока происходит полное зацепление резьбы («ходовой» конец шпильки полностью вкручен в отверстие), зажимная нагрузка будет достигаться за счет затягивания гайки. Если шпильки слишком туго затянуты в блоке, они могут расколоться и вызвать несоосность прокладки головки и головки, что, по крайней мере, затруднит снятие или повторную установку головки в более позднее время.
Перед установкой гаек смажьте верхнюю «тонкую» резьбу на шпильках, шайбах и гайках и затяните гайки в надлежащей последовательности и с указанными значениями. Как указывалось ранее, значение крутящего момента будет варьироваться в зависимости от используемой смазки (масло или Moly lube), поэтому всегда обращайте особое внимание на инструкции по затяжке, предоставленные производителем шпильки. Гайки следует затянуть трижды.
с.
Всегда читайте инструкции по установке производителя шипов и следуйте им в буквальном смысле.Даже если конкретный тип шпильки с головкой предназначен для установки с небольшим предварительным натягом, НИКОГДА не затягивайте двойную гайку и сильно затягивайте шпильку, независимо от ее конструкции. В большинстве случаев шпильки следует устанавливать вручную, но, как уже отмечалось, для некоторых специальных шпилек и / или определенных применений требуется небольшая предварительная нагрузка. Качественные шпильки для вторичного рынка будут иметь внутренний шестигранник на верхнем конце, чтобы можно было использовать шестигранный ключ для установки / предварительной нагрузки / снятия. Прочитайте инструкции!
Шпильки, в отличие от болтов, также обеспечивают преимущества при установке компонентов.Шпильки действуют как направляющие штифты при выравнивании таких элементов, как прокладки, крышки двигателя и т. Д. Доступны шпильки (например, ARP) с «пулевыми» наконечниками, где имеется оголенный наконечник слегка уменьшенного диаметра. Это значительно упрощает установку гайки, позволяя опустить гайку на место до начала зацепления резьбы. Хорошими примерами этого являются шпильки карбюратора, шпильки распределителя, шпильки выпускного коллектора и шпильки масляного поддона. Вместо того, чтобы пытаться удерживать прокладку или деталь на месте, возясь с болтами, пытаясь выровнять болты по их отверстиям, прокладку или деталь можно опустить на шпильки (так что выравнивание не создает дополнительных проблем).Когда деталь выровнена на месте, можно установить шайбы и гайки, не заботясь о смещении детали и / или прокладки.
Еще одно преимущество использования шпилек состоит в том, что вам не нужно беспокоиться о недостаточной зажимной нагрузке из-за того, что слишком длинный болт попал в отверстие. Шпилька неподвижна, а зажимная нагрузка достигается за счет затяжки гайки.
Конечно, шпильки не могут применяться во всех ситуациях из-за конструкции компонентов. Например, впускной коллектор двигателя с V-образным блоком (в зависимости от конструкции) может располагать места крепления на противоположных углах (где отверстия для болтов на каждом углу наклона находятся внутри).Очевидно, что в этих случаях нельзя использовать шпильки, потому что вы никогда не сможете опустить впускной коллектор на угловые шпильки. Шпильки, если применимо, обеспечивают удобство установки и превосходную однородность зажима.
Шпилька и гайка или болт?
Поскольку большинство гоночных двигателей в настоящее время являются четырехтактными, многоцилиндровыми, подавляющее большинство шатунов, разработанных и изготовленных для гонок, относятся к разъемному типу. Это означает наличие надежных средств удержания двух частей стержня вместе с достаточной предварительной нагрузкой, и это обеспечивается резьбовыми крепежными деталями.Здесь есть два варианта. Первый и самый распространенный метод — использовать болт. Второй — установить шпильку, обычно в стержень, и обеспечить нагрузку путем затягивания гайки.
Болт часто предпочтительнее из-за меньшего количества деталей и более низкой стоимости. Головка болта часто физически меньше по диаметру и глубине, хотя использование болта с очень малой высотой головки может вызвать собственные проблемы с точки зрения повышенной концентрации напряжений и отсутствия сопротивления закруглению головки во время затяжки или разборки.Учитывая, что болт имеет разумные пропорции, можно задаться вопросом, зачем кому-то может понадобиться комбинация шпильки и гайки.
Однако есть веские причины, по которым некоторые инженеры могут предпочесть использовать шпильку и гайку, а не болт. Если предполагается, что двигатель будет перестроен, и вам необходимо повторно использовать шатуны, вы можете свести к минимуму повреждение внутренней резьбы в шатуне, оставив крепежную деталь с наружной резьбой постоянно установленной. Это необходимо для титановых шатунов, резьба которых более легко повреждается, чем их стальные аналоги.Комбинация шпильки и гайки также дает возможность полностью отказаться от внутренней резьбы шатуна, тем самым исключая любое возможное повреждение резьбы, а также устраняя связанную с этим концентрацию напряжений. В таких случаях шпилька должна быть спроектирована с функцией предотвращения вращения, и это часто достигается за счет использования D-образной головки.
Еще одна причина использования шпильки и гайки заключается в том, что поле напряжений в крепежном элементе отличается от поля напряжения в болте. Гайка и шпилька могут быть более гибкими, чем болт, особенно если выбран материал гайки с относительно низким модулем упругости.Это может снизить изгибающую нагрузку на застежку. Гибкость с точки зрения геометрии и модуля гайки означает, что концентрация напряжений на первой резьбе внутри гайки может быть минимизирована. Когда охватываемая застежка используется с гайкой с более низким модулем упругости, концентрация напряжений снижается по мере того, как внутренняя резьба изгибается больше, что позволяет задействовать большее количество внутренней резьбы и улучшает распределение нагрузки по длине гайки.
Шпилькимогут также иметь диаметры расположения, что исключает необходимость использования отдельных установочных штифтов или зубцов.Хотя те же элементы могут быть добавлены к болту, это часто не так, поскольку любое изменение натяга может добавить дополнительное трение в процедуру затяжки болта. В то время как крепежные детали шатуна обычно предварительно нагружаются с использованием управления растяжением, повышенные требования к крутящему моменту для преодоления трения на границе между вращающимся диаметром места и статическим шатуном увеличивают напряжение сдвига во время затяжки.
Написано Уэйном Уордом
В чем разница между болтами, винтами и шпильками
Болты, винты и шпильки широко используются в обрабатывающей промышленности.Несмотря на то, что они внешне похожи, каждый предмет имеет свое уникальное назначение и характеристики. Чтобы узнать больше о нюансах между болтами, винтами и шпильками, а также о том, какой из них подходит для вашего применения, продолжайте читать.
Согласно Руководству по машинному оборудованию, основное различие между болтами и винтами заключается в их назначении. Хотя всегда есть исключения из этого правила, болты обычно используются для сборки двух или более компонентов без резьбы. При использовании в сочетании с гайкой болт останется надежно закрепленным на компоненте без резьбы; таким образом, удерживая его вместе и служа своему прямому назначению.С другой стороны, винты используются с резьбовыми компонентами. Это не обязательно означает, что компонент или компоненты, используемые с винтами, должны иметь резьбу, поскольку установка винта может привести к нарезанию резьбы.
Как поясняется в Википедии, болты обычно используются для создания болтовых соединений, которые представляют собой комбинацию гайки, прилагающей усилие зажима, закрепляющего соединение сбоку. Вот почему многие болты имеют хвостовик без резьбы — он создает более прочный и эффективный дюбель. Таким образом, хвостовики без резьбы уже давно являются определяющей характеристикой болтов при сравнении их с аналогичными винтовыми аналогами.
Если все это звучит слишком запутанно, вот еще одно определение болта: это крепежный элемент с резьбой, предназначенный для вставки через отверстия в уже собранных компонентах, обычно используемый вместе с гайкой. Винт — это крепеж с внешней резьбой, который можно вставить в отверстия предварительно собранных компонентов, использовать для соединения с предварительно сформированной внутренней резьбой или создать собственную резьбу. Винты обычно затягиваются путем скручивания и поворота головки с крутящим моментом.
И, наконец, что не менее важно, шпилька — это металлический стержень или вал с резьбой с обеих сторон. Большинство шпилек длинные, хотя размеры могут варьироваться в зависимости от их предполагаемого назначения и применения. Шпильки не имеют «головки», как у винта или болта, которую можно повернуть для затяжки.
Будь то винт, болт или шпилька, обычно все они сделаны из нескольких разных металлов. Сюда входят углеродистая сталь, нержавеющая сталь, латунь, никелевый сплав и алюминиевый сплав. Производители должны использовать высококачественные металлы, чтобы снизить риск растрескивания, ржавчины и других повреждений, поскольку такие повреждения могут иметь катастрофические последствия для компонентов, в которых они используются.
Надеюсь, это поможет вам лучше понять различия между винтами, болтами и шпильками.
См. Болты Монро , Винты и Шпильки . .