Бакелитовая фанера Википедия
Древесно-слоистый пластик (ДСП) Не путать с «Древесно-стружечной плитой», которую также иногда упрощённо обозначают аббревиатурой ДСП, хотя для древесно-стружечных плит имеется своя аббревиатура — ДСтПДреве́сно-слои́стый пластик (ДСП) (лигнофоль, балинит, дельта-древесина) — материал, представляющий собой древесно-полимерный композит, изготавливаемый из листов лущеного шпона (берёзы и других пород, толщиной 0,35—0,65 мм, влажностью 6—10 %), склеенных синтетическими смолами резольного типа под давлением и температурой[1].
Области применения
Антифрикционные свойства, стойкость к воздействию агрессивных сред, абразивов; стабильность при сверхнизких температурах (–270 °С), механическая прочность, водостойкость, диэлектрические свойства позволяют применять ДСП в различных областях техники, таких как:
- Узлы трения.
- Зубчатые колеса.
- Закрытые и открытые металло-полимерные зубчатые передачи.
- Вкладыши подшипников скольжения.
- Для изготовления пуленепробиваемых дверей, банковского оборудования.
- Криогенная и космическая техника.
- В судостроительной промышленности для изготовления дейдвудных подшипников гребных валов.
- Для изготовления затворов гидротехнических сооружений.
- В авиационной технике лопасти; винты вертолётов.
- В транспортном машиностроении: настил полов в автобусах, троллейбусах, трамваях; направляющие эскалаторов метрополитена.
- В строительстве.
- В электротехнической промышленности для изготовления изоляторов, деталей трансформаторов высокого напряжения, выпрямителей (заменяет стеклопластик, текстолит и гетинакс).
- Для изготовления деталей машин текстильной промышленности.
- Как самосмазывающий антифрикционный материал, материал в качестве ползунов лесопильных рам и других аналогичных деталей.
- В металлургическом оборудовании.
- В горнодобывающем оборудовании.
Марки ДСП
В зависимости от расположения волокон древесины шпона в смежных слоях и назначения древесные слоистые пластики в России изготовливают следующих марок:- ДСП-А;
- ДСП-Б; ДСП-Б-э; ДСП-Б-м; ДСП-Б-т; ДСП-Б-о;
- ДСП-В; ДСП-В-э; ДСП-В-м;
- ДСП-Г; ДСП-Г-м.
Буквы А, Б, В, Г указывают порядок укладки шпона в пластике:
- А — волокна древесины шпона во всех слоях имеют параллельное направление или каждые 4 слоя с параллельным направлением волокон древесины шпона чередуются с одним слоем, имеющим направление волокон под углом 20—25° к смежным слоям.
- Б — каждые 8—12 слоев шпона с параллельным направлением волокон древесины шпона чередуются с одним слоем, имеющим перпендикулярное направление волокон древесины к смежным слоям.
- В — волокна древесины шпона в смежных слоях взаимно перпендикулярны.
- Г — волокна древесины шпона в смежных слоях последовательно смещены на угол 45°.
Буквы э, м, т и о определяют назначение материала:
- э — для изготовления конструкционных и электроизоляционных деталей аппаратуры высокого напряжения, электрических машин, трансформаторов, ртутных выпрямителей и т. п.
- м — как самосмазывающий антифрикционный материал, материал в качестве ползунов лесопильных рам и других аналогичных деталей
- т — для изготовления деталей машин текстильной промышленности
- о — как конструкционный и антифрикционный материал.
Размеры
Древесные слоистые пластики изготовляют прямоугольной формы в виде листов толщиной менее 15 мм и плит толщиной 15—60 мм, длиной 700—5600 мм, шириной 950—1500 мм.
Свойства
- Плотность — 1,3 г/см³
- Предел прочности:
- при сжатии — 100—180 МПа
- при растяжении — 140—280 МПа
- при изгибе — 150—280 МПа
- Прочность при скалывании по шву — 11—15 МПа
- Ударная вязкость — 25—80 кДж/м²
- Твердость по Бринеллю — 250 МПа
- Водопоглощение за 24 ч — 5—15 %
- Электрическая прочность:
- поперек слоев — 26—32 МВ/м
- вдоль слоев — 3—13 МВ/м
Древесно-слоистые пластики стойки в трансформаторном масле, уксусном альдегиде, моторном топливе, бутаноле, стироле; нестойки в окислителях, сильных кислотах и щелочах. Перерабатывают в изделия механической обработкой на обычных станках со специальными инструментами.
Технологический процесс изготовления
Получают последовательно пропиткой шпона толщиной 0,3—0,8 мм лиственных пород древесины (обычно березы) фенолоформальдегидной смолой или крезолоформальдегидной смолой в открытых ваннах или автоклавах (0,4—0,8 МПа), сушкой при ступенчатом нагревании до 90 °С, сборкой полученных препрегов в пакеты и прессованием их на этажных прессах (до 20 МПа, 150 °С) и обрезкой в размер.
Примечания
- ↑ ГОСТ 13913-78 «Пластики древесные слоистые (ДСП). Технические условия»
См. также
Литература
- Шейдин И. А., Пюдик П. Э. Технология производства древесных пластиков и их применение. — М., 1971.
- Баженов В. А., Карасев Е. И., Мерсов Е. Д. Технология и оборудование производства древесных плит и пластиков. — М., 1980.
- И. А. Шулепов, Ю. Г. Доронин. Древесные слоистые пластики. — М.: Лесная промышленность, 1987.
- ГОСТ 13913-78 «Пластики древесные слоистые. Технические условия».
- ГОСТ 20966-75 «Пластик древесный слоистый марки ДСП-Б-а. Технические условия».
Ссылки
Фанера — Википедия
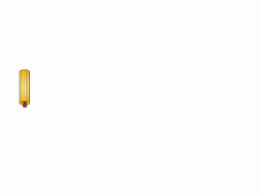
Фане́ра (древе́сно-сло́истая плита́) (др.-греч. φανερός — явный) — многослойный строительный материал, изготавливаемый путём склеивания специально подготовленного шпона. Количество слоёв шпона обычно нечётное, от 3 и более. Для повышения прочности фанеры слои шпона накладываются так, чтобы волокна древесины были строго перпендикулярны предыдущему листу.
Применение
Самодельный вездеход «Каракат» с кузовом из фанерыСтроительство
Классификация
Фанера называется продольной, если волокна в лицевых слоях направлены вдоль длинной стороны, в противном случае — поперечной.
Фанера из древесины как твёрдых, так и мягких пород выпускается нескольких типов и сортов, которые различаются назначением, сроком службы, внешним видом и стоимостью.
По предназначению — строительная, промышленная, упаковочная, мебельная и конструкционная.
По видам фанеру часто разделяют на два популярных вида — ФК (влагостойкая) и ФСФ (повышенной влагостойкости).
По типу обработки — ламинированная.
По внешнему виду (согласно ГОСТ 3916.1-96) (определяется количеством пороков и дефектов поверхности наружного слоя шпона): E (элита), I, II, III, IV.
По материалу, из которого изготовляется
- Хвойная фанера (изготавливается из шпона хвойных пород деревьев: лиственницы, сосны, пихты, ели). Иногда для изготовления фанеры используется шпон сибирского кедра — такая фанера используется в декоративных целях. Для хвойной фанеры обязательным является содержание хвойного шпона в наружных слоях — внутренние могут содержать шпон лиственных пород древесины.
- Берёзовая фанера (изготавливается из шпона берёзы) получила распространение практически во всех областях, но из-за относительно более высокой стоимости в строительстве используется не так широко, как хвойная.
- Фанера из тополя, которая производится преимущественно в Китае, существенно дешевле российских аналогов из берёзы и хвойных пород, однако уступает им по параметрам[источник не указан 477 дней].
По количеству слоев

- трёхслойная
- пятислойная
- многослойная
В основном листы фанеры имеют нечётное количество слоёв шпона: в этом случае шпон расположен симметрично относительно среднего слоя. Если слоёв шпона в фанере четыре, то центральные слои располагают и склеивают перпендикулярно наружным, что увеличивает общую прочность и стойкость к деформации.
По пропитке
Водостойкая фанера — материал, обработанный специальным образом для увеличения сопротивления влаге. Максимально увеличить влагостойкие характеристики фанеры может помочь ламинирование.
- ФБА — это листы фанеры, которые проклеены натуральным альбуминоказеиновым клеем. Преимущество фанеры ФБА в том, что она является экологически чистым строительным материалом, но её небольшая влагостойкость ограничивает применения этой марки.
- ФСФ (фанера, изготавливаемая с применением смоляного фенолформальдегидного клея). Эта фанера характеризуется относительно высокой износоустойчивостью, механической прочностью и высокой водостойкостью. ФСФ — один из самых популярных видов фанеры, используется в строительстве, производстве, кровельных работах. Допускается для применения в жилых помещениях, если класс эмиссии не превышает Е1.
- ФСФ-ТВ (фанера огнезащищенная). Обладает свойствами фанеры марки ФСФ, но не подверженная горению, относится к группе трудногорючих материалов. Применяется в пассажирском вагоностроении и промышленном/гражданском строительстве.
- ФК (фанера, получаемая при приклеивании шпонов карбамидным клеем). Обладая меньшими водостойкими характеристиками, ФК используется преимущественно при внутренней отделке помещений, в мебельном производстве, при изготовлении деревянной тары, при работе с конструкциями внутри помещения.
- ФКМ. В качестве клея при производстве фанеры ФКМ используются меламиновые и меламиноформальдегидные смолы.
- ФБ (фанера, пропитанная бакелитовым лаком, впоследствии склеивается). Этот вид обладает максимальной сопротивляемостью воздействию агрессивной среды и может использоваться в условиях тропического климата, при повышенной влажности и даже под водой.
- БС (фанера, пропитанная бакелитовым клеем, С — спирторастворимый). Эта фанера обладает фантастическими свойствами — сверхвысокой прочностью, стойкостью к агрессивным средам, гибкостью, упругостью, водонепроницаема, не гниёт, не раскисает. Её ещё называют авиационная фанера за то, что раньше использовалась только в авиа- и судостроении.
- БВ (фанера, пропитанная бакелитовым клеем, В — водорастворимый). Эта фанера обладает теми же свойствами, что и фанера БС, за исключением влагостойкости, поскольку клей, применяемый при склеивании слоев, водорастворим.
По виду обработки поверхностей
- НШ — нешлифованная фанера
- Ш1 — материал, шлифованный с одной стороны
- Ш2 — материал шлифованный с двух сторон
Виды и сорта фанеры
В настоящий момент ГОСТы предусматривают наличие пяти сортов фанеры, которые отличаются наличием и количеством допустимых дефектов обработки
Нормы ограничения пороков древесины и дефектов обработки
Наименование пороков древесины и дефектов обработки по ГОСТ 30427 | Фанера с наружными слоями из шпона сортов | ||||
E (элитная) | I сорт | II сорт | III сорт | IV сорт | |
1. Булавочные сучки | Не допускаются | Допускаются до 3 шт. на 1 м² поверхности листа | Допускаются | ||
2. Здоровые сросшиеся светлые и темные сучки | Не допускаются | Допускаются диаметром, мм, не более | Допускаются с трещинами шириной не более 1,5 мм | Допускаются | |
15 | 25 | ||||
в количестве на 1 м², шт., не более | |||||
5 | 10 | ||||
с трещинами шириной, мм, не более | |||||
0,5 | 1,0 | ||||
3. Частично сросшиеся, несросшиеся, выпадающие сучки, отверстия от них, червоточина | Не допускаются | Допускаются диаметром, мм, не более | |||
6 | 6 | 6 | 40 | ||
в количестве на 1 м² поверхности листа, шт., не более | без ограничения количества | ||||
3 | 6 | 10 | |||
4. Сомкнутые трещины | Не допускаются | Допускаются длиной, не более 200 мм в количестве не более 2 шт., на 1 м ширины листа | Допускаются | ||
5. Разошедшиеся трещины | Не допускаются | Допускаются длиной, мм, не более | |||
200 | 300 | без ограничения | |||
шириной, мм, не более | |||||
2 | 2 | 10 | |||
в количестве, шт., не более | |||||
2 | 2 | без ограничения | |||
при условии заделки замазками | Допускаются длиной до 600 мм, шириной до 5 мм при условии заделки замазкой | ||||
6. Светлая прорость | Не допускается | Допускается | |||
7. Темная прорость | Не допускается | Допускается в общем числе с нормами п. 2 настоящей таблицы | Допускается | ||
8. Отклонение в строении древесины | Допускается незначительное случайного характера, кроме темных глазков | Допускается | |||
9. Здоровое изменение окраски | Не допускается | Допускается не более, %, поверхности листа 5 | Допускается | ||
10. Нездоровое изменение окраски | Не допускается | Допускается | |||
11. Гниль | Не допускается | ||||
12. Наклон | Не допускается | Допускаются в общем числе с нормами п. 3 настоящей таблицы | |||
13. Нахлёстка в наружных слоях | Не допускается | Допускается длиной, мм, не более | Допускается | ||
100 | 200 | ||||
в количестве, шт., не более | |||||
1 | 2 | ||||
на 1 м ширины листа | |||||
14. Недостача шпона, дефекты кромок листа при шлифовании и обрезке | Не допускаются | Допускаются шириной, мм | |||
15. Наличие клеевой ленты | Не допускается | Допускается в нешлифованной фанере | |||
16. Просачивание клея | Не допускается | Допускается, %, не более | Допускается | ||
2 | 5 | ||||
поверхности листа | |||||
17. Царапины | Не допускаются | Допускаются | |||
18. Вмятина, отпечаток, гребешок | Не допускаются | Допускаются глубиной(высотой) в пределах значений предельных отклонений по толщине | Допускается | ||
19. Вырыв волокон | Не допускается | Допускается, %, поверхности листа, не более | Допускается | ||
5 | 15 | ||||
20. Прошлифовка | Не допускается | Допускается | |||
21. Покоробленность | В фанере толщиной до 6,5 мм не учитывается, толщиной 6,5 мм и более допускается со стрелой прогиба не более 15 мм на 1 м длины диагонали листа фанеры | ||||
22. Металлические включения | Не допускаются | Допускаются скобки из цветного металла | |||
23. Зазор в соединениях | Не допускается | Допускается шириной, мм, не более | Допускается | ||
1 | 2 | ||||
в количестве, шт., не более | |||||
1 | 1 | ||||
на 1 м ширины листа | |||||
24. Расслоение, пузыри, закорина | Не допускаются | ||||
25. Волнистость (для шлифованной фанеры), ворсистость, рябь | Не допускаются | Допускаются | |||
26. Шероховатость поверхности | Параметр шероховатости Rm по ГОСТ 7016, мкм, не более: для шлифованной фанеры — 100, для не шлифованной — 200 | ||||
27. Вставки из древесины | Не допускаются | Допускаются при заделке в количестве, шт., не более | |||
8 на 1 м2листа | без ограничения | ||||
28. Двойная вставка | Не допускается | Допускается, шт., не более 2 на 1 м2 листа | Допускается без ограничения | ||
Примечания: 1. Норма дефекта обработки «недостача шпона» относится и к внутренним слоям фанеры. |
Общими словами
- сорт Е (элита). Дефекты не допускаются, кроме незначительных изменений случайного характера в строении древесины;
- сорт I. Максимальная длина покоробленности или трещин для фанеры первого сорта не должна превышать 20 мм;
- сорт II. Допускаются трещины до 200 мм, вставки из древесины, просачивание клея площадью до 2 % от общей площади листа фанеры;
- сорт III. Допускаются червоточины до 10 шт. на квадратный метр при диаметре каждой не более 6 мм; общее количество перечисленных пороков не может быть больше 9;
- сорт IV. Фанера 4 сорта является крайне низкокачественной. Такая фанера может иметь следующие пороки: частично сросшиеся и выпавшие сучки — без ограничения; червоточины диаметром до 40 мм без ограничения; дефекты кромок листа глубиной до 5 мм;
Технология изготовления
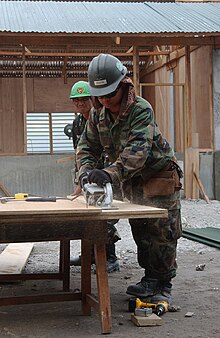
В технологическом процессе производства фанеры можно ориентировочно выделить 14 этапов, рассмотрим их по порядку:
1) Подготовка сырья к лущению
На начальном этапе происходит отбор качественного берёзового фанерного кряжа, он должен соответствовать ГОСТу 9462-88. По поступлении на завод сырьё гидротермически обрабатывается в варочных бассейнах.
2) Окорка сырья
Окорка — удаление с поверхности кряжа коры и луба. После произведения окорки бревна прогоняют через специальный сканер, определяющий кубатуру кряжа.
3) Разделка фанерного сырья
Для разделки сырья на чураки используется пильный агрегат, работающий в полуавтоматическом режиме. Получившиеся от разделки под определенную ширину листа отходы отправляются в отделение переработки отходов, а сырьё в виде чураков — в приемник-накопитель и на следующий этап, к лущильному станку.
4) Лущение, рубка и укладка шпона
Для лущения шпона используются лущильные станки, а рубка по размерам осуществляется ножницами, получаемый шпон в сыром виде на выходе имеет толщину в 1,15—1,18 мм. Получившаяся после лущения лента шпона подаётся к пневматическим ножницам, для раскроя на форматные листы в полуавтоматическом режиме. Лущёный шпон стопками подаётся к сушилке.
5) Сушка шпона
Сушится шпон с использованием газовых роликовых сушилок, работающих на топочных газах, а также и в термомасляной сушилке.
6) Сортировка шпона
После сушки шпон делится на несколько частей, одна из которых направляется на ребросклеивание и шпонопочинку, а другая — сразу на сортировку в соответствии с требованиями ГОСТ 3916.1-96 или требованиями заказчика. Неформатный, кусковой и оставшийся от обрезки шпон отправляется на ребросклеивание вдоль волокон на внутренние слои, а после обрезки поперёк — на линию усовки.
7) Склеивание шпона на «ус»
Склеенный на «ус» поперёк волокон шпон идёт на внутренние слои большеформатной фанеры
8) Ребросклеивание шпона
Для ребросклейки используются станки с подачей шпона вдоль и поперёк древесных волокон
9) Починка шпона
В починку шпона идут полоски шпона шириной до 49 мм, они подбираются по направлению волокон, цвету и породе древесины, толщине относительно требующих починки листов и плотно держатся в шпоне.
10) Приготовление и нанесение клея
Рецептура приготовления клея — ноу-хау любого фанерного завода, а наносится клей на шпон клеенаносящими станками, с помощью рифлёных металлических барабанов строго цилиндрической формы.
11) Сборка пакетов
Шпон с нанесенным клеем отправляют в наборку, где собираются пакеты, которые, проходя холодную подпрессовку, формируют будущие листы фанеры. Пакеты собираются в угольник, прижимаясь к упорам с двух сторон наборного стола. После холодной подпрессовки пакеты отправляют в загрузку горячего пресса.
12) Склеивание фанеры
Для склеивания фанеры используется горячий гидравлический пресс с электронной системой управления прессованием, механической загрузкой и выгрузкой. После пресса фанера развозится погрузчиком в стопы для выстройки. Стопы держатся в течение 24 часов в условиях цеха чтобы снять внутренние напряжения.
13) Обрезка фанеры и шлифование
В обрезке фанеры используются форматно-обрезные станки, а после обрезки её автопогрузчиком подают на сортировку или шлифовальный станок.
14) Сортировка, маркировка и упаковка.
Фанера подается на сортировочные площадки после обрезки и шлифования, где сортируется по ГОСТу 3916.1-96, после чего производится маркировка листов фанеры, упаковка её в стандартные транспортировочные пачки и маркировка пачек.
Производство в России
Фанера в России выпускается следующих основных форматов 1525х1525, 1220х2440, 2440х1220, 1250х2500, 2500х1250, 1500х3000, 3000х1500, 1525х3050 и 3050х1525мм. Различие в расположении длины и ширины относительно формата фанеры обозначает продольное или поперечное расположение волокон шпона по длинной стороне и указывает, что если формат заявлен как 1220х2440, то расположение слоёв шпона поперечное, а если 2440х1220 — продольное. Фанера с продольным расположением волокон шпона используется там, где требуется гибкость, а с поперечным — там, где требуется высокая жёсткость при изгибе.
Производство фанеры в России (млн. м³): 2002 г. — 1,8; 2003 г. — 2,0; 2004 г. — 2,2; 2005 г. — 2,6;
Фанерное производство в России расположено по большей части в привязке к регионам, богатым лесными ресурсами. Основная доля выпуска приходится на предприятия Северо-Западного федерального округа — около 35 % в общем объёме производства. В 2005 году экспорт составил 1,5 млн м³, то есть около 60 % всей произведённой в стране фанеры.
См. также
Примечания
Литература
- Григорьев М. А. Материаловедение для столяров, плотников и паркетчиков: Учебное пособие для ПТУ. — М.: Высшая школа, 1989. — 223 с. — 100 000 экз. — ISBN 5-06-000345-0.
- ГОСТ 3916.1-96 Фанера общего назначения с наружными слоями из шпона лиственных пород.
- ГОСТ 3916.2-96 Фанера общего назначения с наружными слоями из шпона хвойных пород.
- ГОСТ 13913-78 (ГОСТ на ДСП)
- ГОСТ 102-75 Фанера берёзовая авиационная.
- ГОСТ В-226-41 Дельта-древесина авиационная.
Ссылки
- Черкасов И. К. Фанера // БСЭ
Бакелитовая фанера Википедия
Древесно-слоистый пластик (ДСП) Не путать с «Древесно-стружечной плитой», которую также иногда упрощённо обозначают аббревиатурой ДСП, хотя для древесно-стружечных плит имеется своя аббревиатура — ДСтПДреве́сно-слои́стый пластик (ДСП) (лигнофоль, балинит, дельта-древесина) — материал, представляющий собой древесно-полимерный композит, изготавливаемый из листов лущеного шпона (берёзы и других пород, толщиной 0,35—0,65 мм, влажностью 6—10 %), склеенных синтетическими смолами резольного типа под давлением и температурой[1].
Области применения[ | ]
Антифрикционные свойства, стойкость к воздействию агрессивных сред, абразивов; стабильность при сверхнизких температурах (–270 °С), механическая прочность, водостойкость, диэлектрические свойства позволяют применять ДСП в различных областях техники, таких как:
- Узлы трения.
- Зубчатые колеса.
- Закрытые и открытые металло-полимерные зубчатые передачи.
- Вкладыши подшипников скольжения.
- Для изготовления пуленепробиваемых дверей, банковского оборудования.
- Криогенная и космическая техника.
- В судостроительной промышленности для изготовления дейдвудных подшипников гребных валов.
- Для изготовления затворов гидротехнических сооружений.
- В авиационной технике лопасти; винты вертолётов.
- В транспортном машиностроении: настил полов в автобусах, троллейбусах, трамваях; направляющие эскалаторов метрополитена.
- В строительстве.
- В электротехнической промышленности для изготовления изоляторов, деталей трансформаторов высокого напряжения, выпрямителей (заменяет стеклопластик, текстолит и гетинакс).
- Для изготовления деталей машин текстильной промышленности.
- Как самосмазывающий антифрикционный материал, материал в качестве ползунов лесопильных рам и других аналогичных деталей.
- В металлургическом оборудовании.
- В горнодобывающем оборудовании.
Марки ДСП[ | ]
В зависимости от расположения волокон древесины шпона в смежных слоях и назначения древесные слоистые пластики в России изготовливают следующих марок:
- ДСП-А;
- ДСП-Б; ДСП-Б-э; ДСП-Б-м; ДСП-Б-т; ДСП-Б-о;
- ДСП-В; ДСП-В-э; ДСП-В-м;
- ДСП-Г; ДСП-Г-м.
Буквы А, Б, В, Г указывают порядок укладки шпона в пластике:
- А — волокна древесины шпона во всех слоях имеют параллельное направление или каждые 4 слоя с параллельным направлением волокон древесины шпона чередуются с одним слоем, имеющим направление волокон под углом 20—25° к смежным слоям.
- Б — каждые 8—12 слоев шпона с параллельным направлением волокон древесины шпона чередуются с одним слоем, имеющим перпендикулярное направление волокон древесины к смежным слоям.
- В — волокна древесины шпона в смежных слоях взаимно перпендикулярны.
- Г — волокна древесины шпона в смежных слоях последовательно смещены на угол 45°.
Буквы э, м, т и о определяют назначение материала:
- э — для изготовления конструкционных и электроизоляционных деталей аппаратуры высокого напряжения, электрических машин, трансформаторов, ртутных выпрямителей и т. п.
- м — как самосмазывающий антифрикционный материал, материал в качестве ползунов лесопильных рам и других аналогичных деталей
- т — для изготовления деталей машин текстильной промышленности
- о — как конструкционный и антифрикционный материал.
Размеры
Бакелитовая фанера: характеристики, применение
Фанера бакелитовая является прочным, упругим, водостойким, износоустойчивым материалом, не уступающим по качествам даже низколегированной стали. Все это — благодаря специальной технологии, которая заключается в пропитке березового шпона бакелитовым клеем при высокой температуре и под давлением. Такая фанера, получившая название «морская», не боится ни воды, ни жары. Может эксплуатироваться при температурах от минус 50 до плюс 50 по шкале Цельсия.
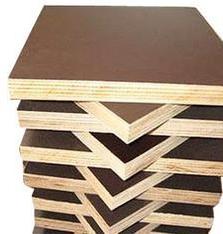
Способ изготовления
Первый этап. Для производства фанеры I сорта ее слои полностью погружают в смолу, для изготовления материала II сорта шпон просто смазывают.
Второй этап. Листы прессуют под давлением 4 МПа.
Третий этап. Фанеру охлаждают под давлением.
Высокое давление позволяет полностью пропитать слои и получить более тонкую фанеру. Кроме этого, прессование делает материал устойчивым к проникновению влаги.
Технические характеристики
Выпускают материал в виде листов шириной 1250 мм и 1500 мм, длина при этом может составлять 2800 мм, 5650 мм, 5700 мм.
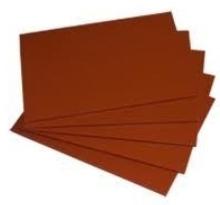
Фанера имеет гладкую поверхность, на которой по ГОСТу не допускаются вмятины, царапины, валики, отпечатки прокладок. Браком считается бакелитовая фанера с непромазанными и непропитанными местами, пузырями, недопрессовкой, расслоениями.
Сферы применения
Благодаря многим полезным качествам, бакелитовая фанера успешно эксплуатируется в различных отраслях. Таких, как автомобилестроение, судостроение, самолетостроение, машиностроение, гидротехническая промышленность, шоу-бизнес, цирковое искусство.
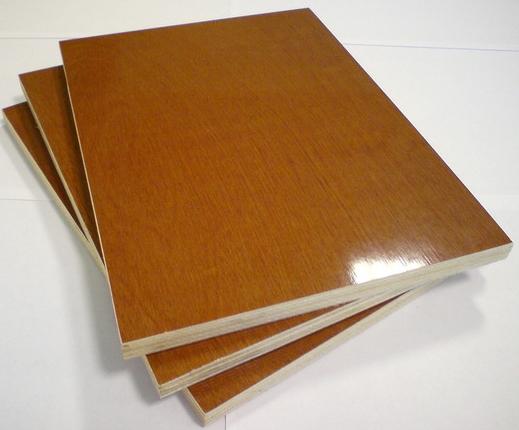
Сорта фанеры
На рынке представлены несколько марок бакелитовой фанеры: ФБС, ФБС-1, ФБС-1А. Первые два вида, обладающие повышенной водостойкостью и устойчивостью к огню, предназначены для использования в строительстве, судостроении. Третий вид разработан специально для автомобильной промышленности. Влагоустойчивость последней марки несколько ниже, поскольку смолой пропитаны только внешние слои, но при этом она и самая дешевая.
Верхние слои фанеры ФБС и ФБС-1 выполнены из шпона I сорта, внутренние — из шпона II шпона. ФБС-1А полностью изготовлена из сырья II сорта.
По способу механической обработки материал бывает нешлифованным, шлифованным (с одной или с двух сторон).
Преимущества фанеры бакелитовой перед низколегированной сталью
Почему специалисты склоняются в пользу фанеры? Наряду с такими качествами, как водостойкость, сверхпрочность, огнеустойчивость и упругость, материал отличается легкостью и не боится коррозии, что дает возможность эксплуатировать его в условиях повышенной влажности воздуха и даже под водой.
Изготавливается и продается бакелитовая фанера в Москве. Широкий ассортимент, низкие цены, круглосуточная отгрузка, прямые доставки, максимальное удобство для клиентов — основные принципы работы производителей.
Фанера — Вікіпедія
Матеріал з Вікіпедії — вільної енциклопедії.
Фане́ра[1] (запозичення із західноєвропейських мов, пор. нім. Furnier)[2] або дикт[3] (від нім. Dikte — «тонка дошка»)[4] — композитний матеріал у вигляді шаруватої клеєної деревини, що складається із склеєних між собою трьох і більше листів лущеного шпону із взаємно перпендикулярним розташуванням волокон деревини в суміжних шарах[5]
Фанера загального призначення повинна вироблятися, транспортуватися та зберігатися відповідно до вимог чинних на території України стандартів — ГОСТ 99-96 «Шпон лущеный. Технические условия», ГОСТ 3916.1-96 «Фанера общего назначения с наружными слоями из шпона лиственных пород. Технические условия» та ГОСТом 3916.2-96 «Фанера общего назначения из шпона хвойных пород. Технические условия».
Розміри і шаровість фанери регламентуються. Довжина (ширина) листів фанери від 1200 до 3660 мм, товщина від 3 до 30 мм. Допускається виготовляти фанеру інших розмірів відповідно до умов контракту.
Фанера на основі карбамідоформальдегідної смоли має високу токсичність, а вільний формальдегід, який виділяється з неї, має специфічний запах та подразнювальний вплив на організм людини[6].
Класифікація фанери загального призначення[ред. | ред. код]
Фанеру загального призначення поділяють:
- залежно від зовнішнього вигляду шпону — на сорти,
- за ступенем водостійкості клейового з’єднання — на марки: ФСФ — фанера підвищеної водостійкості; ФК — фанера водостійка.
- за ступенем механічної обробки поверхні — нешліфовану (НШ), шліфовану з одного боку — (Ш1), шліфовану з двох боків — (Ш2).
- за екологічною безпекою (за вмістом формальдегіду) — на класи емісії.
Залежно від зовнішніх шарів лущеного шпону (Е — еліта, I, II, III, IV — для листяних порід; Ех, Iх, IIх, IIIх, IVх — для хвойних порід) фанеру поділяють на сорти.
Умовне позначення фанери має містити: назву продукції; породу деревини зовнішніх та внутрішніх шарів; марку; поєднання сортів шпону зовнішніх шарів; клас емісії; вид обробки поверхні; розміри; стандарт.
Характеристики и сферы применения бакелитовой фанеры
19.04.2018

Бакелитовая фанера считается одним из самых прочных, водостойких и износоустойчивых материалов. Специалисты сравнивают ее качественные характеристики с низколегированной сталью, что стало возможно благодаря специальной технологии обработки. Материал не боится воды и высоких температур, прекрасно выдерживает перепады от -50 0C до + 50 0C. Средний срок эксплуатации бакелитовой фанеры составляет 15 лет, при этом использоваться она может в регионах с влажным климатом и даже под водой.
Особенности изготовления
Технология изготовления состоит из 3 основных этапов, в процессе которых березовый шпон пропитывается клеевым составом и подвергается высокому давлению. Производство выглядит следующим образом:
- пропитка — для получения фанеры 1 сорта каждый слой погружается в смолу, для получения 2 сорта шпон промазывают;
- прессование — листы помещают под пресс, давление которого составляет 4 Мпа;
- охлаждение — листам дают остынуть, при этом они продолжают оставаться под давлением.
В результате такой обработки на выходе получается тонкая фанера. Благодаря пропитке смолой и прессованию материал приобретает отличную устойчивость к влаге.
Характеристики материала
Фанера выпускается производителями в виде листов разной ширины. Этот параметр представлен двумя видами — 1500 и 1250 мм. Наибольшая длина листа составляет 5700 мм, средним считается размер 5650 мм. Самый маленький лист имеет длину 2800 мм. Допустимыми считаются отклонения по длине и ширине не более 40 и 20 мм соответственно. Погрешность толщины составляет до 2 мм, на рынке строительных материалов представлены предложения с толщиной листа от 5 до 20 мм. Максимальная плотность материала не превышает 1,2 Мпа.
Бакелитовая фанера отличается темными оттенками, наиболее часто встречается красно-коричневая гамма. Листы обладают гладкой поверхностью, на которой, согласно действующим нормам ГОСТ, не должно быть вмятин, царапин и валиков. Бракованным материалом считается фанера с участками, на которых отсутствует пропитка, имеются пузыри, признаки расслоения.
Где применяется и какие сорта существуют?
Благодаря уникальным качествам бакелитовая фанера сегодня широко используется в различных сферах и отраслях, начиная от шоу-бизнеса и заканчивая самолетостроением. Наиболее часто из такого материала изготавливают кровлю, полы, перегородки, опалубки, конструкции перекрытий и стенды.
Производитель выпускают сегодня несколько сортов фанеры, каждый из которых имеет свои преимущества и целевое назначение. При необходимости получить водостойкий жаропрочный материал рекомендуется обратить внимание на сорта ФБС или ФБС-1. Верхний слой такой фанеры изготовлен из шпона 1 сорта, внутренний – из 2 сорта, материал используется в сфере строительства и судостроения. ФБС-1А обладает меньшими показателями устойчивости к влаге и огню, изготавливается из шпона 2 сорта. Достоинством этого сорта фанеры является меньшая стоимость.
В чем преимущества бакелитовой фанеры?
Бакелитовая фанера часто выступает конкурентом низколегированной стали, и специалисты строительного рынка часто склоняются к выбору в ее пользу. Такая ситуация обусловлена наличием ряда неоспоримых преимуществ по сравнению с металлом. Показатели водостойкости, прочности и устойчивости к огню пропитанного под давлением шпона не уступают стали. При этом материал обладает небольшим весом и не подвержен коррозийным изменениям. Последнее свойство позволяет использовать фанеру в условиях с повышенными значениями влажности воздуха и в водной среде. Бакелитовая фанера производится и реализуется в Москве. Для удобства клиентов производители работают в режиме круглосуточной отгрузки, предоставляя покупателям максимально выгодные условия и широкий ассортимент продукции.
Please enable JavaScript to view the comments powered by Disqus.ООО УралПлитПром, Бакелитовая фанера (ФБВ, ФБС, ФБА)
Бакелитовая фанера изготавливается из разнонаправленного шпона, это обеспечивает высокую прочность материала. Из всех существующих видов фанеры именно фанера, склеенная при помощи бакелитового лака, считается наиболее жестким и прочным материалом. По сути бакелизированная фанера является древесным композитом и по своим свойствам близка к пластикам. В зависимости от состава клея можно получить ФБВ, ФБС и ФБА. Плотная структура бакелитовой фанеры обеспечивает материалу устойчивость ко многим физическим и химическим воздействиям. Ровная поверхность материала плюс устойчивость к влаге – идеальное решение для бетонной опалубки многократного использования.
Особые достоинства бакелизированной (бакелитовой) фанеры:
- износо- и водостойкость;
- упругость;
- устойчивость к температурным перепадам, солнечным лучам;
- повышенная огнеупорность;
- большой формат листов;
- устойчивость к воздействию морской воды, плесени;
- низкая степень горения;
- защищенность от разбухания/расслаивания;
- устойчивость к коррозии.
- Не впитывает масла и парафины
Надежность ФБ обеспечивает особый способ производства в несколько этапов. На первой стадии происходит пластификация березового шпона посредством пропитки водорастворимыми или спирторастворимыми смолами. Температура во время пропитки доводится до 270°С. Далее под определенным давлением (6 атмосфер) осуществляется прессование материала с последующим склеиванием.
Виды бакелитовой фанеры:
ФБВ – фанера, пропитанная водорастворимыми смолами. Обладает высокой механической прочностью, но не является водостойкой.
ФБС – фанера, пропитанная спирторастворимыми смолами. Водостойкая фанера с высокими прочностными характеристиками.
ФБА – фанера облегченная авиационная. Для ее производства используется наиболее экологичный по составу альбуминоказеиновый клей. Материал с меньшим процентом влагостойкости.
Чтобы добиться максимального качества фанеры и дополнительно защитить ее торцы от проникновения влаги, их покрывают эмалью специальной марки, либо бакелитовым лаком.
Применение бакелитовой фанеры:
- рекламная индустрия – щиты, иные конструкции;
- автомобилестроение – обшивка фургонов, полы;
- строительство – черновое покрытие под ламинат и паркет, опалубка, перегородочные конструкции, навесы, складские сооружения;
- судостроение – обшивка лодок, судов, яхт;
- оружейное производство – накладки, приклады;
Также бакелитовую фанеру с успехом используют для строительства понтонов, мостовых конструкций, шлюзов, плавучих доков и в авиастроении.
При необходимости в прочном, водостойком материале выгоднее и рациональнее купить бакелитовую фанеру, так как ей по некоторым показателям (особенно по весу и по цене) уступает даже сталь. Цену за лист фанеры бакелитовой конкретной марки вы узнаете в прайс-листе.


Бакелит — Википедия, вольна энциклопедия
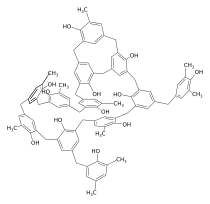
Бакелит ( Бакелит [1] ) — tworzywo sztuczne oparte na ywicy fenolowo-formdehydowej, prawdopodobnie jedno z pierwszych tworzyw sztucchal 9000 dukow 9000 dukow.
Technologia produkcji bakelitu została wynaleziona przez Leo Hendrika Baekelanda na początku XX wieku (1907–1909) [3] .
Jego głównymi zaletami jest niepalność, nietopliwość, nierozpuszczalność, niskie przewodnictwo elektryczne, dobra wytrzymałość dielektryczna, słziezoście de delektryczna, słzieš.Ponadto, bakelit może pracować w powietrzu o normalnej wilgotności oraz w oleju transformatorowym. Bakelit stosowany BYL przede wszystkim ш przemyśle elektrotechnicznym яко materiał konstrukcyjny я izolacyjny, Ораз ж wielu innych zastosowaniach, Gdzie potrzebne było tworzywo odporne на szereg czynników, A jednocześnie możliwe сделать formowania ш niemal dowolnych kształtach (poprzez odlewanie LUB prasowanie proszku) я podatne obróbce mechanicznej zarówno на зимно, як и на горе. W zastosowaniach praktycznych do bakelitu dodawano rozmaite wypełniacze, najczęściej włókniste, na przykład azbest, papier, mączkę drzewną [2] .
Patent na produkcję bakelitu już dawno wygasł. Wynalazek został zgłoszony w Urzędzie Patentów i Znaków Towarowych Stanów Zjednoczonych przez Leo H. Baekelanda w 1907 г. и патентный udzielono w 1909 (pod numerem US 942699 A) [4] . Słowny znak towarowy «Bakelite» został prawdopodobnie po raz pierwszy zarejestrowany w Europie 31 марта 1936 года Бакелит Корпорация, наступившее 20 марта 1956 года Powtórzyła firma Hexion Specialty Chemicals GmbH.
.бакелитовой фанеры — это … Что такое бакелитовая фанера?
промышленные полимеры основные — Введение химических соединений, используемых в производстве синтетических промышленных материалов. В промышленном производстве пластмасс, эластомеров, искусственных волокон, адгезивов и покрытий для поверхностей огромное количество полимеров…… Универсалиум
Пластик — это общий термин для широкого спектра синтетических или полусинтетических органических твердых материалов, пригодных для производства промышленных товаров.Пластмассы обычно представляют собой полимеры с высокой молекулярной массой и могут содержать другие вещества, чтобы…… Wikipedia
мебель — без мебели, прил. / ferr ni cheuhr /, сущ. 1. подвижные предметы, такие как столы, стулья, столы или шкафы, необходимые для использования или украшения в доме, офисе или тому подобное. 2. арматура, аппаратура или необходимые аксессуары для чего-либо. 3. оборудование для… Универсалиум
Распространение технологий в Канаде — В этой статье излагается история распространения или распространения технологий в Канаде.Технологии, выбранные для лечения, включают, в грубом порядке, транспорт, связь, энергию, материалы, промышленность, общественные работы, коммунальные услуги…… Wikipedia
Искусство, антиквариат и коллекции — ▪ 2003 г. Введение В 2002 году крупные выставки, такие как Documenta 11, отразили разнообразную природу современного искусства: художники из самых разных культур получили широкое признание за работы, начиная от инсталляции и заканчивая видео и живописью … Universalium
пластик — пластично, пластично, нареч./ пластик /, н. 1. Часто пластмассы. любой из группы синтетических или натуральных органических материалов, которым можно придать форму, когда они станут мягкими, а затем отвержденными, включая многие типы смол, смол, полимеров, производных целлюлозы,…… Универсалиум
альдегид — альдегидный, прил. / аль деух хуйд /, сущ. Chem. любой из класса органических соединений, содержащих группу CHO, которая дает кислоты при окислении и спирты при восстановлении. [1840 50; Универсал
Электрогитара — Струнный инструмент Fender Stratocaster Классификация Струнный инструмент (выщипывается пальцами или медиатором.)… Википедия
Маартен ван Северен — (5.6.1956, Антверпен, Бельгия 21.2.2005, Гент, Бельгия) Бельгийский дизайнер мебели. Резюме Сын художника-абстракциониста Маартен Ван Северен решил изучать архитектуру в художественной школе Гента; он проработал три года, прежде чем пойти работать в различных… Wikipedia
Вулканизированное волокно — Британский патент на вулканизированное волокно был получен в 1859 году англичанином Томасом Тейлором. [http: // www.deldot.gov/archaeology/henderson road / pdf / chap 4 the bounty.pdf; стр. 4 8.] Этот патент появился после появления целлулоида…… Википедия
Термореактивный полимер — Термореактивный пластик, также известный как термореактивный полимер, представляет собой полимерный материал, который необратимо отверждается. Отверждение может происходить путем нагревания (обычно выше 200 ° C (392 ° F)), химической реакции (например, двухкомпонентной эпоксидной смолы) или облучения…… Wikipedia
Бакелит — Википедия
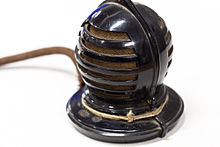
Бакелит и Бакелит sind Markenzeichen (Warenzeichen) для разнообразных производств Kunststoffe, ursprünglich (около 1909 г.) der Bakelite GmbH в Германии, и был später auch der Union Carbide Corporation в США. [1] Die eingetragenen Marken gehören der Hexion GmbH. [2]
Unter dem Namen Bakelit wurde der erste vollsynthetische, industrial produzierte Kunststoff [3] hergestellt und vermarktet, der 1905 vom belgischen Chemiker Leo Hendrik Baekeland entwickelt und nach ihm benan.Der duroplastische Kunststoff ist ein Phenoplast auf der Basis von Phenol und Formaldehyd. Formteile aus diesem Kunststoff werden durch Formpressen und Aushärten eines Phenolharz-Füllstoff-Gemisches in einer beheizten Form hergestellt. Später wurden als Bakelite auch andere Kunststoffe vermarktet, etwa Varianten von Phenoplasten, Aminoplaste, Epoxidharze und Polyesterharze. [1]
Lichtschalter aus Bakelit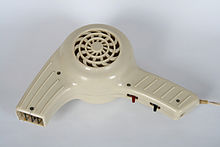
Baekeland Experimentierte Anfang des 20.Jahrhunderts mit Phenol und Formaldehyd. Er entdeckte, dass diese Stoffe in einer exothermen Reaktion zu einem Kunstharz полимеризиртен. Nach dem Entfernen des entstehenden Wassers lässt sich die noch weiche warme Masse (Pressmasse) в Formen Pressen und durch Wärme und Druck härten. Für das entsprechende Verfahren wurde 1907 ein Patent erteilt. [1]
Am 5. февраля 1909 г. Stellte Baekeland seine Entdeckung im New Yorker Club der Chemiker an der 55. Straße unter dem Namen Bakelit vor. [4]
Baekeland erkannte schnell die neuen Eigenschaften des Materials und gründete am 25. Mai 1910, zusammen mit den RÜTGERS-Werken, die Bakelite GmbH в Эркнер, Берлин. [5]
Phenol fiel zu dieser Zeit noch in großen Mengen als Abfallprodukt der Steinkohlendestillation an, und Baekeland beginn, Bakelit in großen Mengen zu produzieren.
Nach dem Zweiten Weltkrieg wurde das Bakelit-Werk in Erkner demontiert und verstaatlicht. 1948 wurde dort der VEB Plasta Erkner gegründet.Die Eigner verlegten den Firmensitz nach Letmathe bei Iserlohn in die Westzone. В 1957 году компания Phenolharz-Produktion начала свою деятельность в Дуйсбурге-Мейдерихе, после 1959 года, после того, как компания Epoxidharze produziert вердена. 1976 kam das Werk Frielendorf bei Kassel (ehemals Hoechst AG ) hinzu.
Ende der 1980er Jahre начал die Bakelite AG mit dem Erwerb von Gesellschaften im europäischen Ausland.
Ende April 2005 wurde die Bakelite AG von Borden Chemical Inc. mit Sitz in Ohio gekauft, welche wiederum die zwei Geschäftsbereiche Resolution Performance Products LLC и Resolution Specialty Materials LLC zu der Hexion Specialty Chemicals Inc. fusionierte. Zu diesen fusionierten Geschäftsbereichen gehörte auch die ehemalige Bakelite AG , die somit in Hexion aufging, welche zu den weltweit führenden Herstellern duroplastischer Kunststoffe zählt.
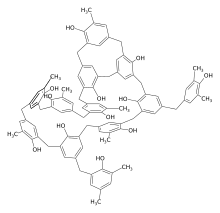
Die Polykondensation zur Herstellung von Phenol-Formaldehyd-Harz beginnt säurekatalysiert mit folgender Reaktion:
Das gebildete Dimer 3 kann dann erneut unter dem Einfluss einer Säure mit Phenol 1 und Formaldehyd 2 unter Wasserabspaltung reagieren.So bildet sich ein Trimer. Durch viele weitere derartige Kondensationsreaktionen entsteht schließlich Bakelit, ein vernetztes Makromolekül.
Nach dem Abkühlen und der Aushärtung des Kunststoffes ist dieser broadstandsfähig gegen Mechanische Einwirkungen, Hitze und Säuren. Im Gegensatz zu Thermoplasten lässt sich Bakelit auch durch Erwärmen nicht wieder verformen. Es ist Allerdings Relativ spröde, so dass Gegenstände aus diesem Material, etwa beim Aufprall auf den Boden, zerspringen können.
Phenolharze neigen zum Nachdunkeln und sind daher meist dunkelbraun oder schwarz eingefärbt. [6] In den Pressmassen enthalten sind zudem Zuschlagstoffe, wie Holzmehl, Gesteinsmehl oder Textilfasern, wodurch eine farbliche Marmorierung entstehen kann.
Bakelit ist auch sehr langlebig. Im Zweiten Weltkrieg verlor wahrscheinlich die U.S. Navy ein Bauteil aus Bakelit mit der Aufschrift VP-101 . Es trieb möglicherweise 60 Jahre im Müllstrudel des Pazifik, bevor es von einem Laysanalbatros verschluckt wurde. [7]
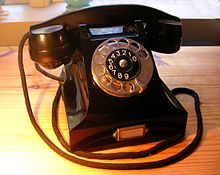
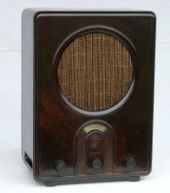
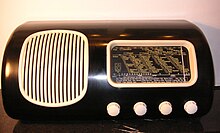
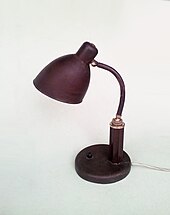
Nach dem Auslaufen des «Druck-Wärme» -Patents im Jahr 1927 verbreitete sich die Produktionsweise schnell — in den 1930er Jahren gab es bereits mehrere hundert Presswerke und Hersteller von Phenolharzpressmassen в Германии. Wesentlich war dabei die «Typisierung» der Pressmassen und der Presswerkserzeugnisse durch einen Verein der Hersteller.
Produkte aus Bakelit sind Haushalts- und Küchengegenstände (Griffe für Fenster, Türen, Pfannen und Kochtöpfe, Waffeleisen), Telefone (Modell W48), Ziergegenstände, Modeschmuck, Bälühärößen (Bestelehör) Modelleisenbahnen von Trix Express (1935-1955), Gehäuse für Geräte, Radios und Transformatoren sowie generell für elektrisches und thermisches Isolationsmaterial. Diese Eigenschaften prädestinierten Bakelit zum Einsatz в Крафтфарцойген (Zündspulen- und Zündkerzenstecker, Verteilerkappen, Isolierung von Vergasern und Kraftstoffpumpen gegenüber heißen Motorbauteilen).Karosserieteile des Trabants bestanden aus Baumwoll-faserverstärktem Phenolharz.
Bakelit diente in eingefärbter Form unter anderem als Schmuckstein-, Bernstein- und Elfenbeinersatz. Das statt Elfenbein verwendete Bakelit kam unter dem Namen «Ivorine» в ден Гендель. [8]
Фенол-Formaldehydharz вирда Noch verwendet, Венна Mechanische унд Thermische Belastbarkeit, сделайте geringe Entflammbarkeit унд Chemische Beständigkeit gefordert IST, Цум Beispiel в Schleifscheiben, Reibbelägen, Filterpapieren, Feuerfest-Materialien, Isolationsmaterialien, Maschinen-Bedienelementen унд Zur Imprägnierung beziehungsweise Tränkung фон Holz- унд Papierwerkstoffen (Leiterplatten).
Ähnliche Werkstoffe werden als Hitzeschild eingesetzt.
Produkte aus Bakelit sind wegen ihres Designs und ihrer Bedeutung für die Alltagskultur und die Industriegeschichte vielfach gesuchte Sammlerstücke. Liebhaber behavior, dass Bakelit im Gegensatz zu modernen Kunststoffen ein besseres Griffgefühl erzeuge.
Im Museum für angewandte Kunst (MAK) zeigt die Ausstellung Bakelit. Die Sammlung Georg Kargl von 15. Juli — 26. Oktober 2020 etwa 300 Gegenstände gestaltet aus oder mit Bakelit.Георг Каргль (1955–2018) военный галерист в Вене. [9] [10]
2003 wurde в Kierspe ein Bakelit-Museum eröffnet. In wechselnden Ausstellungen werden mehrere tausend Exponate gezeigt. Ein Großteil besteht aus der dem Heimatverein gestifteten Sammlung des Kiersper Fabrikanten, Carl-Heinz Vollmann von Fa. Reppel & Vollmann («Револит» -Продукт). [11]
- L.H. Baekeland: Bakelit, ein neues synthetisches Harz. In: Chemiker-Zeitung 35, Nr.33, 1909, с. 317–318.
- Дитрих Браун, Герд Коллин: 100 Jahre Bakelit. In: Chemie in unserer Zeit. Bd. 44, № 3, 2010, ISSN 0009-2851, S. 190–197.
- Сильвия Глейзер: Бакелит. In: Historische Kunststoffe im Germanischen Nationalmuseum. Verlag des Germanischen Nationalmuseums, Нюрнберг 2008, ISBN 978-3-936688-37-5, S. 14-20.
- ↑ a b c Eintrag zu Phenolharze.В: Römpp Online. Георг Тиме Верлаг, abgerufen am 12. июня 2014 г.
- ↑ Registernummer 505667 Registerauskunft Deutsches Patent- und Markenamt
- ↑ Вольфганг Кайзер: Kunststoffchemie für Ingenieure. 3. Auflage, Carl Hanser, München 2011, S. 13.
- ↑ Ирен Мейхснер: Aufbruch ins Kunststoffzeitalter. In: Kalenderblatt. Deutschlandfunk 5 февраля 2009 г.
- ↑ Firmengeschichte (Memento vom 4. April 2004 im Internet Archive ) auf der ehemaligen Website der Bakelite AG.
- ↑ Ханс-Дитер Якубке, Рут Керхер (Hrsg.): Lexikon der Chemie. Spektrum Akademischer Verlag, Гейдельберг 2001.
- ↑ Океаны отходов. Seattle Times, 23 апреля 2006 г., abgerufen am 24 января 2010 г. (английский).
- ↑ Peter Wulf Hartmann: Das grosse Kunstlexikon. Einträge Бакелит унд Ivorine .
- ↑ Bakelit im MAK: «Material der 1.000 Möglichkeiten» orf.at, 18. Juli 2020, abgerufen 18.Июль 2020.
- ↑ Бакелит. Die Sammlung Georg Kargl mak.at, 15. июл 2020, abgerufen 18. июл 2020.
- ↑ Stadt Kierspe (Heimatmuseum): Bakelitmuseum , abgerufen am 18. Juli 2020.
Бакелит — Википедия

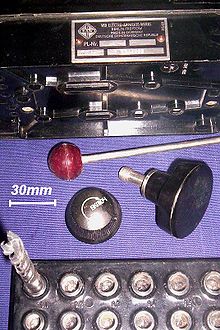
Die Bakelite GmbH und später auch Bakelite AG war von 1910–2004 ein deutsches Unternehmen zur Kunststoffherstellung.
Leo Hendrik Baekeland entwickelte 1905 Bakelit, einen duroplastischen Kunststoff auf der Basis von Phenolharz. 1907 erhielt er auf das Herstellungsverfahren ein US-Patent, 1908 das in Deutschland.В феврале 1909 года в США невод Эрфиндунг им Нью-Йоркер Клуб дер Chemiker vor, im Mai des nächsten Jahres gründete er als Minderheitenbeteiligung zusammen mit Julius Rütgers die Bakelite GmbH in Erkner bei Berlin. Zur Herstellung von Bakelit waren große Mengen an Phenol notwendig, die damals bei der Steinkohlendestillation der Rütgerswerke als Abfallprodukt anfielen.
Baekeland selbst gründete 1910 in den USA die General Bakelite Company , die die Patente hielt.Da das patentierte Bakelit oft plagiiert wurde, ging Baekeland konsequent dagegen vor. Einer der Plagiatoren, Sir Swinburne, vertrieb sein Phenolplastik unter dem Namen «Damard» (abgeleitet vom englischen «чертовски тяжело»). Nach mehreren Jahren Rechtsstreit fusionierten die Konkurrenzfirmen, die Damard Laqueurs Co. und andere verklagte Unternehmen ( Redmanol Co. , Condensite Co. ) mit Baekelands Firma zu einem Großunternehmen, die Baekelands Firma zu einem Großunternehmen, der der 19 sich Baekeland zur Ruhe gesetzt hatte, von Union Carbide übernommen wurde.
Ab 1910 stellte Bakelite GmbH в Erkner [1] als erster Betrieb der Welt в компании Fertigung Kunststoffteile her. Die Produkte waren breit gefächert, von Gehäusen und Sicherungen (wegen der isolierenden Eigenschaften von Bakelit) über Gegenstände des Alltages (Telefone, Radios, Füllfederhalter, und so weiter) bis hin zu militärischen Anwendungen. Bakelit ließ sich bei der Herstellung in jede gewünschte Form pressen, es war Allerdings danach nicht mehr verformbar wie Thermoplaste.Es war hitzebeständig, unlöslich, kostengünstig herzustellen und leitete den elektrischen Strom nicht. Allerdings konnte es nur in dunklen Farbtönen hergestellt werden, die bei Sonneneinstrahlung nachdunkelten.
1927 liefen die Patente von Baekelands Herstellungsverfahren aus und zahlreiche andere Hersteller kamen auf den Markt. Auf dem Gelände der Leipziger Technischen Messe verfügte das Unternehmen über einen großzügigen Messestand und in der Leipziger Altstadt über ein eigenes Gebäude — das «Bakelite-Haus» на Маркт.
Nach dem Ende des Zweiten Weltkriegs wurde die Bakelite GmbH in Erkner erst demontiert, und dann enteignet. 1948 wurde am Standort Erkner der VEB Plasta Erkner neu gegründet. Die Bakelite GmbH вернется в зону Westzone nach Iserlohn-Letmathe. [1] 1950 — 1952 wurde das dortige Bakelite-Werk errichtet und in Betrieb genommen.
Zahlreiche andere Kunststoffarten kamen in den 1950er Jahren auf den Markt. Sie hatten unter anderem den Vorteil в jedem gewünschten Farbton hergestellt werden zu können.Die Phenolharze blieben trotzdem im Markt, sie wurden nun aber eher in Gehäusen, Leiterplatten или Isolatoren eingesetzt.
1957 nahm das Werk in Werk Duisburg-Meiderich die Produktion der Phenolharze auf, 1959 kam die Produktion von Epoxidharzen hinzu. 1976 Erwarb das Unternehmen das Werk Frielendorf bei Kassel. Ab Ende der 1980er Jahre wurden von der Bakelite AG zahlreiche Firmen in Europa (Италия, Финляндия, Испания) и Азия (Япония, Южная Корея) hinzugekauft oder durch Kooperationen verbunden. [2]
2003 erwirtschaftete Bakelite mit etwa 1700 Beschäftigten einen Umsatz von 540 Mio. Евро. Es war einer der führenden europäischen Hersteller von Phenol- und Epoxidharzen sowie duroplastischen Formmassen. [3]
2004 verkaufte die Eigentümerin Rütgers AG die Bakelite AG и Borden Chemicals mit Firmensitz in den USA. Diese fusionierte 2005 mehrere Geschäftsbereiche zur Hexion Specialty Chemicals, die heute noch die Markenrechte an Bakelit besitzt und die deutschen Produktionsstandorte betreibt.Ende 2010 fusionierte Hexion mit der Momentive Performance Materials. Beide Unternehmen blieben selbstständig und versuchen, durch Kooperationen im Overhead-Bereich Kosten zuaren.
Unter dem Namen Momentive und zusammen mit Rütgers Chemicals wird die Geschichte des Bakelite-Unternehmens in der Route der Industriekultur aufgeführt. 2003 год был в Kierspe ein Bakelit-Museum eröffnet. In wechselnden Ausstellungen werden mehrere tausend Exponate gezeigt. [4]
- ↑ a b NRW-Stiftung: Bakelit , abgerufen am 5.Ноябрь 2017 г.
- ↑ Firmengeschichte (Memento vom 4. April 2004 im Internet Archive ) auf der ehemaligen Website der Bakelite AG
- ↑ Chemienews der Rütgers AG zum Verkauf der Bakelite AG, 8. Октябрь 2004 г.
- ↑ Stadt Kierspe (Heimatmuseum): Bakelitmuseum , abgerufen am 5 ноября 2017 г.
51.3635067.621266 Координаты: 51 ° 21 ′ 48,6 ″ N , 7 ° 37 ′ 16,6 ″ O
.