Авиационный алюминий: характеристики
Благодаря легкости, пластичности и стойкости к коррозии алюминий стал незаменимым материалом во многих производствах. Авиационный алюминий – группа сплавов, отличающихся повышенной прочностью с включением магния, кремния, меди и марганца. Дополнительную прочность сплаву придают при помощи т. н. «эффекта старения» — особого метода закалки под воздействием в течение длительного времени агрессивной атмосферной среды. Сплав был изобретен в начале 20 века, получив название дюралюминий, сейчас известен также под названием «авиаль».
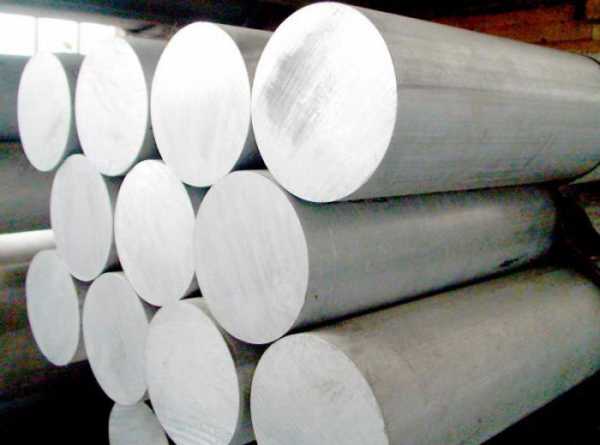
Определение. Исторический экскурс
Началом истории авиационных алюминиевых сплавов считается 1909 год. Немецкий инженер-металлург Альфред Вильм опытным путем установил, если сплав алюминия с незначительным добавлением меди, марганца и магния после закалки при температуре 500 °C и резкого охлаждения выдержать при температуре 20-25 градусов в течение 4-5 суток, он поэтапно становится тверже и прочнее, не теряя при этом пластичности. Процедура получила название «старение» или «возмужание». В процессе такой закалки атомы меди заполняют множество мельчайших зон на границах зерен. Диаметр атома меди меньше, чем у алюминия, потому появляется напряжение сжатия, вследствие чего повышается прочность материала.
Впервые сплав был освоен на немецких заводах Dürener Metallwerken и получил торговую марку Dural, откуда и произошло название «дуралюмин». Впоследствии, американские металловеды Р. Арчер и В. Джафрис усовершенствовали состав, изменив процентное соотношение, в основном магния. Новый сплав получил название 2024, который в различных модификациях широко применяется и сейчас, а все семейство сплавов — «Авиаль». Название «авиационный алюминий» этот сплав получил практически сразу после открытия, поскольку полностью заменил дерево и метал в конструкциях летательных аппаратов.
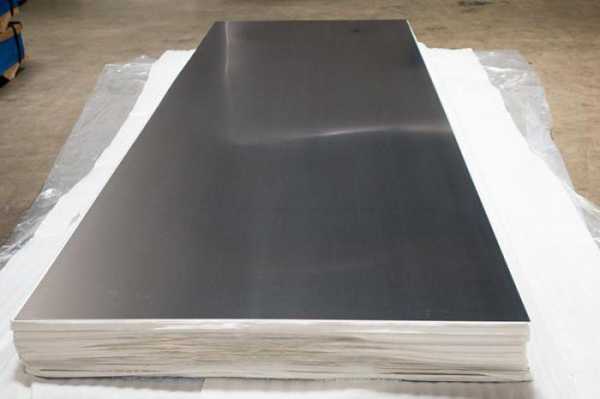
Основные виды и характеристики
Выделяют три основных группы:
- Семейства алюминий-марганец (Al-Mn) и алюминий-магний (Al-Mg). Основная характеристика – высокая, едва уступающая чистому алюминию коррозийная стойкость. Такие сплавы хорошо поддаются пайке и сварке, но плохо режутся. Не упрочняются термической обработкой.
- Коррозионно-стойкие сплавы системы алюминий-магний-кремний (Al-Mg-Si). Упрочняются термической обработкой, а именно закалкой при температуре 520 °C с последующим резким охлаждением воде и естественным старением около 10 суток. Отличительная характеристика материалов этой группы – высокая коррозионная стойкость при эксплуатации в обычных условиях и под напряжением.
- Конструкционные сплавы алюминий-медь-магний (Al-Cu-Mg). Их основа – легированный медью, марганцем и магнием алюминий. Изменяя пропорции легирующих элементов, получают авиационный алюминий, характеристики которого могут отличаться.
Материалы последней группы обладают хорошими механическими свойствами, но при этом весьма подвержены коррозии, чем первое и второе семейство сплавов. Степень подверженности коррозии зависит от вида обработки поверхности, которую все равно необходимо защищать лакокрасочным покрытием или анодированием. Коррозионная стойкость частично увеличивается введением в состав сплава марганца.
Помимо трех основных видов сплавов различают также ковочные сплавы, жаропрочные, высокопрочные конструкционные и др. обладающие необходимыми для конкретной сферы применения свойствами.
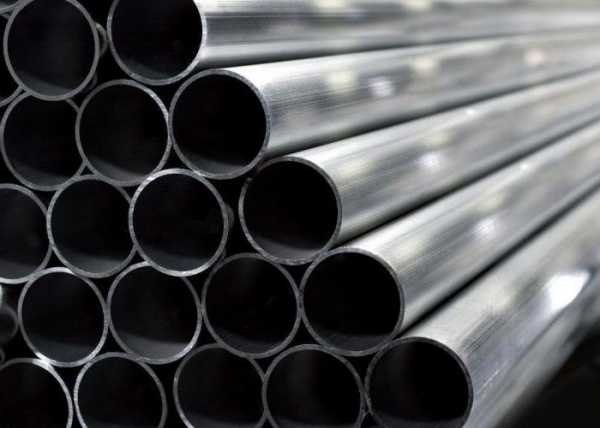
Маркировка авиационных сплавов
В международных стандартах первая цифра маркировки авиационного алюминия обозначает основные легирующие элементы сплава:
- 1000 – чистый алюминий.
- 2000 – дюралюмины, сплавы легированные медью. В определенный период – самый распространенный аэрокосмический сплав. В связи с высокой чувствительностью к коррозийному растрескиванию все чаще заменяются сплавами серии 7000.
- 3000 – легирующий элемент – марганец.
- 4000 – легирующий элемент – кремний. Сплавы известны также как силумины.
- 5000 – легирующий элемент – магний.
- 6000 – самые пластичные сплавы. Легирующие элементы – магний и кремний. Могут подвергаться термозакалке для повышения прочности, но по этому параметру уступают сериям 2000 и 7000.
- 7000 – термически закаленные сплавы, самый прочный авиационный алюминий. Основные легирующие элементы – цинк и магний.
Вторая цифра маркировки — порядковый номер модификации алюминиевого сплава после исходного – цифра «0». Две заключительные цифры – номер самого сплава, информация о его чистоте по примесям. В случае если сплав опытный, к маркировке добавляется пятый знак «Х».
На сегодняшний день, самые распространенные марки авиационного алюминия: 1100, 2014, 2017, 3003, 2024, 2219, 2025, 5052, 5056. Отличительными особенностями этих сплавов являются: легкость, пластичность, хорошая прочность, стойкость к трению, коррозии и высоким нагрузкам. В авиастроении наиболее широко используемые сплавы — авиационный алюминий 6061 и 7075.
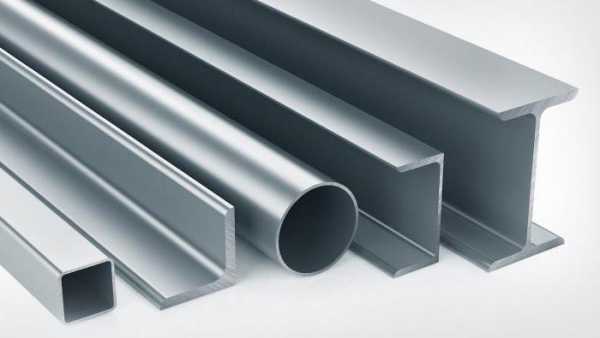
Состав
Основными легирующими элементами авиационного алюминия являются: медь, магний, кремний, марганец, цинк. Процентное содержание этих элементов по массе в сплаве определяют такие характеристики, как прочность, гибкость, стойкость к механическим воздействиям и др. Основа сплава – алюминий, основные легирующие элементы: медь (2,2-5,2% массы), магний (0,2-2,7%) и марганец (0,2-1%).
Семейство авиационных сплавов алюминия с кремнием (4-13% массы) с незначительным содержанием других легирующих элементов – медь, марганец, магний, цинк, титан, бериллий. Используется для изготовления сложных деталей, известный также как силумин или литейный алюминиевый сплав. Семейство сплавов алюминий-магний (1-13% массы) с другими элементами обладают высокой пластичностью и коррозионной стойкостью.
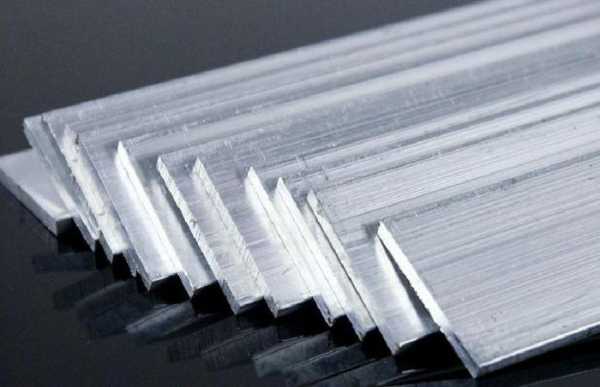
Роль меди в составе авиационного алюминия
Присутствие меди в составе авиационного сплава способствует его упрочнению, но в то же время плохо влияет на его коррозионную стойкость. Выпадая по границам зерен, в процессе закалки, медь делает сплав подверженным точечной коррозии, коррозии под напряжением и межзеренной коррозии. Зоны богатые медью более гальванически катодные, чем алюминиевая матрица вокруг, а потому более уязвимы для коррозии, происходящей по гальваническому механизму. Увеличение содержания меди в массе сплава до 12% повышает прочностные свойства за счет дисперсного упрочнения в процессе старения. При содержании меди в составе свыше 12% сплав делается хрупким.
Сферы применения
Алюминиевые сплавы являются наиболее востребованным металлом по продаже. Легкий вес авиационного алюминия, прочность делают этот сплав хорошим выбором для многих производств от самолетов до предметов быта (мобильные телефоны, наушники, фонарики). Алюминиевые сплавы применяются в судостроении, автомобилестроении, строительстве, производстве ж/д транспорта, в атомной промышленности.
Широко востребованы сплавы с умеренным содержанием меди (2014, 2024 др.). Профили из этих сплавов имеют высокую коррозийную стойкость, хорошую обрабатываемость, точечную свариваемость. Из них изготавливают ответственные конструкции самолетов, большегрузных автомобилей, военной техники.
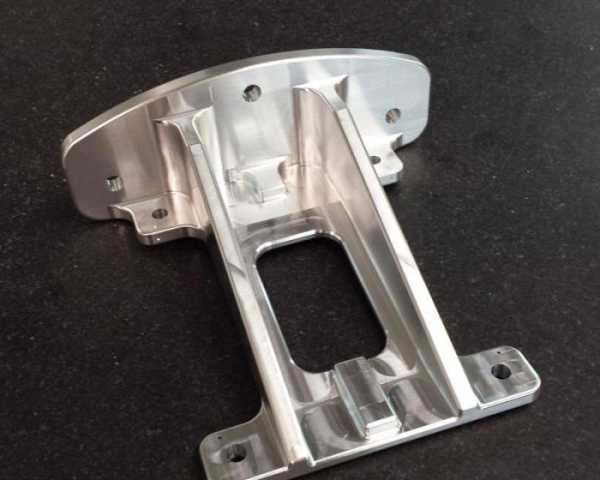
Особенности соединения авиационного алюминия
Сварка авиационных сплавов осуществляется исключительно в защитной среде инертных газов. Преимущественными газами являются: гелий, аргон или их смесь. Более высокой теплопроводностью обладает гелий. Это определяет более благоприятные температурные показатели сварочной среды, что позволяет достаточно комфортно соединять толстостенные элементы конструкций. Использование смеси защитных газов способствует более полному газоотводу. При этом вероятность образования пор в сварном шве значительно уменьшается.
Применение в авиастроении
Авиационные алюминиевые сплавы изначально специально создавались для строительства авиационной техники. Из них изготавливают корпуса летательных аппаратов, детали двигателей, шасси, топливные баки, крепежные устройства и др. Детали из авиационного алюминия используются в интерьере салона.
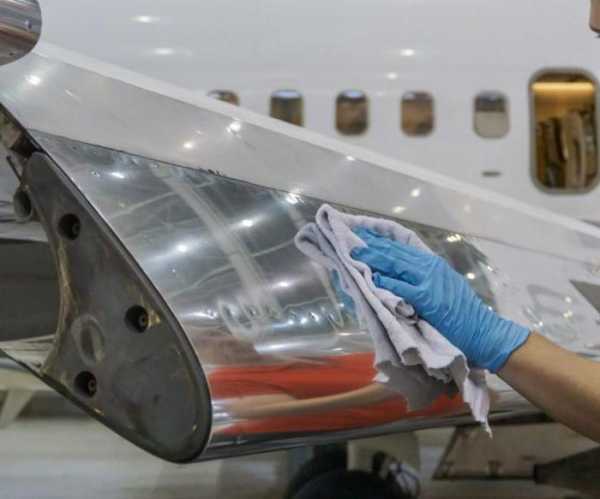
Алюминиевые сплавы серии 2ххх используют для производства деталей, подвергающихся воздействию высоких температур. Детали малонагруженных узлов, топливных, гидро- и маслосистем изготавливают из сплавов 3ххх, 5ххх и 6ххх. Наиболее широкое применение в авиастроении получил сплав 7075. Из него изготавливаются элементы для работы при значительной нагрузке, низких температурах с высокой стойкостью к коррозии. Основой сплава является алюминий, а основными легирующими элементами: магний, цинк и медь. Из него изготавливают силовые профили конструкций самолетов, элементы обшивки.
fb.ru
Алюминий в транспорте
Чтобы создать современное транспортное средство, будь то автомобиль, поезд, океанский лайнер или космический корабль, необходим алюминий. Поэтому транспортная индустрия — его главный мировой потребитель. На западе производители транспорта обеспечивают 26% спроса на первичный алюминий и 38% спроса на вторичный алюминий. И неудивительно: детали из этого легкого, прочного, устойчивого к коррозии металла могут служить десятки лет.
Кроме того, производители транспортных средств в наши дни стараются по максимуму заменить алюминием традиционные железо и сталь. Дело в том, что использование более легких материалов позволяет снизить вес автомобиля или вагона поезда — а значит, существенно сэкономить топливо. Алюминий занимает первое место среди металлов, используемых в самолетостроении — недаром этот металл называют «крылатым». Не будь его, авиация никогда бы не пережила настоящего подъема. Уже первый в мире самолет 1903 года, построенный братьями Райт, имел четырехцилиндровый двигатель в 12 лошадиных сил, заключенный в алюминиевый блок весом в 13,5 кг для облегчения конструкции. Легкий металл быстро заменил дерево, сталь и другие материалы, применяемые в авиастроении. Первый аэроплан, целиком построенный из алюминия, появился в начале 1920-х годов. С тех пор самолеты всех типов и размеров по большей части состоят из «крылатого металла» — на него приходится до 80% веса ненагруженного воздушного судна. Например, в знаменитом Boeing 747 содержится 75 тонн алюминия.
Более эффективный материал для воздухоплавания трудно выдумать: алюминиевые сплавы отлично переносят перегрузки и давление, с которыми сопряжены полеты на большой высоте; кроме того, алюминиевые панели прекрасно удерживают тепло внутри. Поскольку металл устойчив к коррозии, некоторые авиакомпании даже не красят свои воздушные суда, сокращая тем самым вес самолета на несколько сот килограммов.
Но больше всего производимого в мире алюминия используют все-таки автомобилестроительные компании. Впервые легкий металл начал применяться для изготовления декоративных элементов машин еще в 1914 году. Сегодня из него делают более 100 автомобильных деталей — и это число постоянно растет. Каркас, бампер, части кузова, подвеска, системы безопасности — для производства этих и многих других компонентов необходим алюминий.
Используя крылатый металл, можно снизить массу грузовика или автобуса на 1800–1900 кг, что позволяет перевозить значительно больше груза. Сэкономленная при этом энергия в 6–12 раз превышает энергию, необходимую для производства задействованного алюминия. Известно, что понижение веса автомобиля на 100 кг экономит 0,6 л бензина каждые 100 км. А чем меньше расходуется топлива, тем меньше оксида углерода попадает в атмосферу.
При проектировании современных автомобилей учитывается важная способность легкого металла поглощать кинетическую энергию. Во время автомобильных аварий удар, в основном, «сглаживают» именно алюминиевые элементы конструкции. Значит, использование этого материала существенно повышает безопасность автомобиля.
Кроме того, алюминиевые компоненты придают автомобилям современный высокотехнологичный вид. Чтобы в этом убедиться, достаточно посмотреть на Jaguar XJ-Type, ставший символом нового этапа в автомобильном дизайне. Его кузов полностью изготовлен из легкого металла!
Недавние исследования показали, что за последние годы использование алюминия европейскими автоконцернами резко возросло. В 1990 году на один автомобиль приходилось около 50 кг этого материала, а в 2005 — уже 132 кг. Эксперты считают, что к 2010 году этот показатель вырастет еще на 25 кг.
Российский автомобиль пока в среднем содержит всего 40 кг металла. Но здесь имеется солидный потенциал для роста: в производство запускаются новые отечественные модели, а иностранные производители проявляют все более и более активное участие в российской автомобильной индустрии. По оценкам экспертов, к 2025 году Россия займет четвертое место в мире по числу автомобилей. И к этому времени доля алюминия в каждом из них увеличится в разы. Из легкого металла делают вагоны суперскоростных поездов и современные вагоны метро — легкие, устойчивые к сжатию и сильнейшим вибрациям и при этом обеспечивающие низкий расход электричества. Поэтому для железнодорожников алюминий — настоящий материал будущего.
А вот для производства товарных вагонов этот металл используется давно — первый экземпляр был выпущен в 1931 году. В 1960-х из алюминия сделали крытые товарные вагоны, способные вмещать до 100 тонн груза. На каждый вагон уходило около 7 тонн алюминия — на 10 тонн меньше, чем потребовалось бы на аналогичный стальной.
Судостроители настолько ценят прочность и износостойкость этого металла, что даже создают корабли, сделанные из него целиком. Первое такое судно появилось в 1892 году во Франции и представляло собой яхту длиной чуть более 12 метров. Опыт оказался настолько удачным, что французы впоследствии построили огромный океанский лайнер длиной 315 метров: не только корпус, но и мебель этого гиганта были сделаны из алюминия. Даже через 30 лет активно использования «алюминиевые корабли» остаются почти новыми, не имея никаких признаков усталости металла. Их значительно легче поддерживать в идеальном состоянии, чем обычные.
Сегодня из легкого металла производят 50% подвесных моторов. А еще он активно используется при строительстве скоростных паромов, для которых критичен легкий вес. В современном пароме может содержаться до 400 тонн алюминия.
И, конечно же, алюминий широко используют при создании космических кораблей — с тех пор как на заре космической эры оболочку первого искусственного спутника Земли, запущенного в 1957 году, изготовили из алюминиевых сплавов, этот металл стал незаменим для открытий будущего. На алюминий приходится от одной двадцатой до половины веса ракеты и до 90% веса «шаттла».
Вот так десятки лет алюминий верой и правдой служит нам, позволяя не только с комфортом добираться из точки A в точку B, но и исследовать морские просторы и покорять космические пространства.
techliter.ru
Алюминиевая Ассоциация стимулирует применение алюминия в транспорте
Москва, 07 декабря. Алюминиевая Ассоциация будет способствовать максимальному использованию алюминиевых изделий в транспортном машиностроении. Такое заявление прозвучало на Международной конференции «Современные алюминиевые конструкции в транспорте», прошедшей в Москве и организованной НП «АПРАЛ».
В ходе конференции обсуждались текущие тенденции применения полуфабрикатов из алюминия в различных видах транспорта, современные решения по снижению их массы за счет использования инновационных компонентов и технологий, последние инжиниринговые разработки, перспективные технологии соединения и сварки алюминиевых конструкций, возможности для развития аддитивного производства. Участие в ее работе приняли представители компаний – членов Алюминиевой Ассоциации: ОК «РУСАЛ», «Арконик Россия», Опытный завод «Авиаль», «Сеспель», ЦНИИ КМ «Прометей» и др.
По данным Алюминиевой Ассоциации конечное потребление алюминия в мире по итогам 2017 г. составит 85 млн. т, из них 26% придется на долю транспорта. К 2021 г. спрос на алюминий вырастет до 95 млн. т и транспорт будет его крупнейшим потребителем.
В России же доля транспорта в структуре потребления алюминия не превышает 16%, значительно уступая строительству. Поэтому имеются большие возможности для увеличения потребления алюминия за счет серийного производства железнодорожных вагонов и цистерн, локализации производства алюминиевых кузовных деталей, авиационных кресел, теплообменников, кресел и контейнеров, строительства рыболовецких и круизных судов.
Использование алюминия в транспорте имеет хорошие перспективы благодаря надежности, длительному сроку и низкой стоимости эксплуатации, относительно невысокой цене и др.
«Уникальные свойства алюминия и большой интерес к нему со стороны машиностроительных компаний позволяют нам с оптимизмом смотреть на перспективы увеличения применения крылатого металла в транспорте уже в ближайшее время», — отметил Председатель Алюминиевой Ассоциации Валентин Трищенко.
www.aluminas.ru
ищем минусы и плюсы — АвтоМания
В автомобилестроении алюминий стали использовать еще с конца позапрошлого века: в 1899 году на выставке в Берлине показали концептуальный автомобиль Durkopp с облегченными кузовными панелями. А спустя всего три года ныне всем известный Карл Бенц представил первый двигатель из «крылатого» металла для участия в автогонках. Сегодня на применения алюминия в автомобильной промышленности, если верить оценке экспертов, приходится почти треть потребления всего производимого в мире серебристого металла. Так чем же он так хорош, помимо легкости?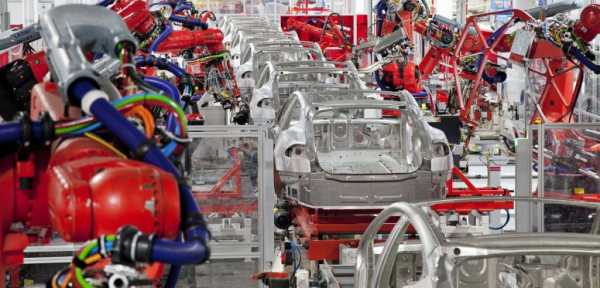
Плюсы использования алюминия
Основной плюс алюминия — соотношение его прочности к массе. В сравнении с классической сталью, он в среднем на 60% легче, что позволяет существенно снизить массу автомобиля, а также расход топлива и вредные выбросы.Если же копать глубже, то алюминий почти не ржавеет, не магнитится, а из-за хорошей пластичности легко обрабатывается давлением. Плюс процесс вторичной переработки «крылатого» металла прост: он может быть переплавлен раз за разом без потерь в свойствах. Эти нюансы не только упрощают, но и ускоряют производственные процессы, а также дают возможность инженерам постоянно экспериментировать со структурой металла, с различными видами и формами автомобильных деталей.
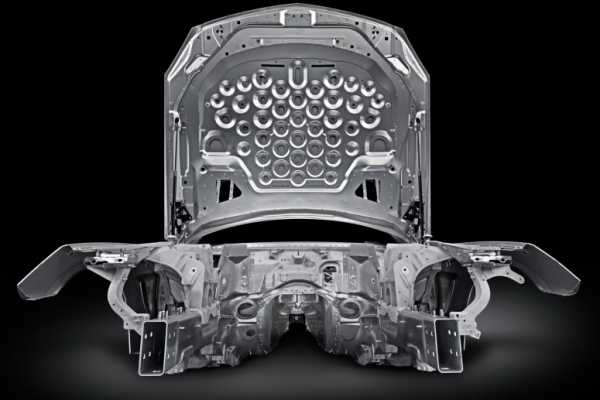
На управляемость машины алюминиевый скелет тоже влияет положительно, поскольку металл обладает высоким сопротивлением к торсионным нагрузкам. Такой кузов получается более жестким на скручивание, что добавляет машине устойчивости в поворотах и отзывчивости при рулежке. Вдобавок сделанные из алюминия детали подвески сокращают неподрессоренные массы автомобиля, что улучшает его плавность хода. Вроде бы идеальный материал…
Недостатки использования алюминия
Первый — производственный. Детали из алюминиевых сплавов технически сложно скрепляются друг с другом: требуются изощренные способы (лазерная сварка, клепка, склейка, болтовые соединения), а также узко-специализированное оборудование. К примеру, сварка алюминиевых элементов возможна только лазерным способом или же в среде инертного газа (например, аргона). При этом еще необходимо четко контролировать сварочный процесс, поскольку алюминий весьма капризный металл: в местах соединения могут образовываться трещины.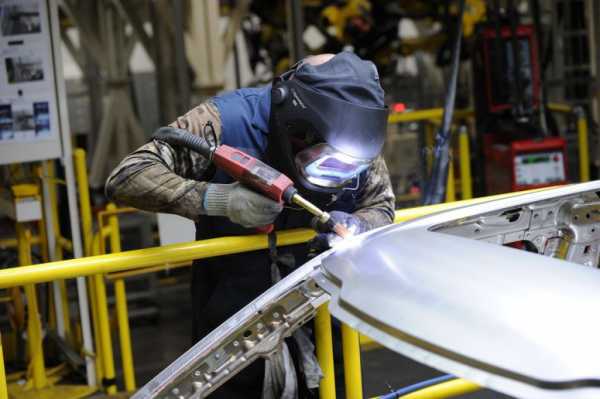
Третье — формы и размеры элементов. Чтобы изготовить, к примеру, алюминиевый кузов, который сравним или превосходит по прочности стальной, его конструкцию приходится делать «пухлой». Хороший пример — велосипедная рама: из стали она тонкая, а из алюминия толстая. Вот и некоторые элементы кузова автомобиля получаются пышными, из-за чего уменьшается полезное пространство внутри машины и ухудшается общая обзорность для водителя и пассажира (широкие передние, центральные и задние стойки). Вдобавок к этому, «крылатый» металл хорошо проводит шум, который приходится гасить дополнительными слоями изоляционного материала, увеличивая опять же расходы на производство машины.
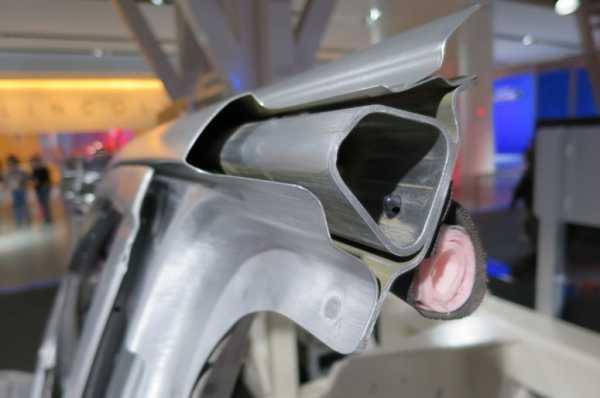
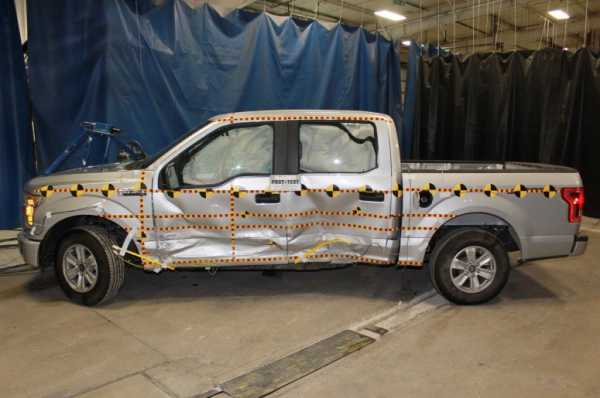
avtomaniya.com
Автомобилестроение – Алюминиевая Ассоциация
В 2014 году мировая автомобильная индустрия (без учета Китая) потребила 2,87 млн тонн алюминия. Ожидается, что к 2020 году эта цифра вырастет до 4,49 млн тонн. На рост потребления алюминия в автопроме влияют как увеличение производства самих автомобилей, так и рост содержания в них алюминия.
Каждый килограмм алюминия, использованный при изготовлении автомобиля, позволяет снизить общую массу машины на килограмм. Поэтому из алюминия производится все большее количество автомобильных деталей — радиаторы системы охлаждения двигателя, колесные диски, бампера, детали подвески, блоки цилиндров двигателя, корпуса трансмиссий и, наконец, детали кузова – капоты, двери и даже вся рама.
В результате с 1970-х годов доля алюминия в общем весе автомобиля увеличилась с 35 кг до сегодняшних 152 кг. Согласно прогнозам экспертов, к 2025 году среднее содержание алюминия в одном автомобиле достигнет 250 кг.
Основными методами производства автодеталей являются литье и штамповка из прокатанных листов и полос. Но некоторые из них изготавливаются необычным способом горячего прессования мелкого алюминиевого порошка – САП (спеченная алюминиевая пудра). Окисленную алюминиевую пудру помещают в алюминиевую же оболочку и нагревают до температуры чуть меньшей, чем плавление металла, и в горячем виде прессуют. Получившиеся изделия отличаются высокой прочностью и используются там, где нужны детали для работы в условиях высоких температур с низким коэффициентом трения – например, так делаются поршни двигателей.
У алюминия есть замечательное свойство – он отлично «гасит» удар, причем делает это в два раза эффективнее, чем сталь. Поэтому автопроизводители давно используют этот металл для изготовления бамперов. Алюминиевый кузов безопаснее стального еще и потому, что деформации в алюминиевых конструкциях локализуются в компактных зонах, не давая деформироваться другим частям кузова и сохраняя максимальную безопасность той части машины, где находятся пассажиры.
Эксперты утверждают, что в ближайшее десятилетие автопроизводители существенно увеличат использование алюминия в своих моделях. Легкий и прочный металл будет в большом количестве использоваться в деталях кузова либо для изготовления кузова целиком.
При этом многие автомобильные компании сегодня договариваются с производителями алюминия о создании производств замкнутого цикла, когда из идущих на лом алюминиевых деталей утилизируемых автомобилей создаются запчасти для новых машин. Сложно представить себе более экологичный вид промышленного производства.
www.aluminas.ru
ALUMINIUM 2018: учиться алюминию
ALUMINIUM 2018 в Дюссельдорфе
С 9 по 11 октября 2018 года в Дюссельдорфе пройдет очередной Конгресс АЛЮМИНИЙ 2018.
См. подробнее ALUMINIUM 2018
Как это было в 2016 году
С 29 ноября по 1 декабря 2016 года, в немецком Дюссельдорфе прошло важнейшее событие алюминиевой промышленности – глобальная Международная Выставка ALUMINIUM 2016.
Вся цепочка создания стоимости для алюминия
На выставке-ярмарке Алюминий 2016 в Дюссельдорфе участвовали более 900 компаний, огромных, крупных, средних и малых. Они охватывали всю цепочку создания стоимости (value chain) для алюминия: от глобальной добычи бокситов и выплавки первичного алюминия до частной деятельности, такой как, алюминиевый консалтинг и журналистика. Это значит, что алюминий дает вдохновение для творчества и работу сотням тысяч, а то и миллионам людей во всем мире.
Цепочка создания стоимости для алюминия
Алюминий в готовой продукции
Добрую половину из этой цепочки создания стоимости занимает применение алюминия в отраслях промышленности, которые производят готовую продукцию:
- автомобилестроение;
- строительство;
- авиация и космос;
- машины, агрегаты и товары массового потребления;
- транспорт;
- упаковка продукции.
Ниже представлен обзор применения алюминия в каждой из этих отраслей.
Автомобилестроение: самый важный рынок
Современный мегатренд к облегчению конструкций в транспортных средствах является источником постоянного роста применения алюминия в легковых автомобилях. Алюминия в автомобилях становится все больше и больше — в двигателях, корпусе, несущих элементах и шасси.
Этот тренд лучше виден в цифрах – масса алюминий на один автомобиль постоянно растет:
- Шестьдесят лет назад в автомобиле было в среднем 19 килограммов алюминия
- с 1990 до 2013 года доля алюминия в автомобиле выросла с 50 до 140 килограммов
- К 2020 году доля алюминий составит около 160-180 кг за счет применения алюминия не только в дорогих, но и в массовых моделях автомобилей
Алюминиевый автомобиль
Алюминий в строительстве: не только фасады
Строительная индустрия во всем мире все больше полагается на алюминий как на строительный материал. Малый вес и высокая прочность алюминия находят свое применение как в легких фасадных конструкциях и в несущих конструкциях мостов
В содружестве со стеклом алюминий задает тренды в современной архитектуре. Алюминий применяют, чтобы создавать архитектурные шедевры, которые демонстрируют отличную изоляцию от холода, жары и шума, разнообразные цветовые решения наружной поверхности зданий. Алюминиевые профили дают конструкторам возможности для реализации самых неожиданных технических решений для фасадов, дверей и окон и успешного внедрения их по всему миру.
Уже много лет алюминий применяют, чтобы создавать новые дизайнерские явления во внутренней обстановке зданий. От высококачественной мебели до ежедневных привычных вещей алюминий действительно является законодателем современных дизайнерских трендов.
Алюминиевый сад от РУСАЛА
Аэрокосмическая индустрия: технологии с будущим
Снижение веса является ключевым моментом в конструкции самолета. Все усилия направлены на снижение самолетом потребления топлива и выделения углекислого газа. Алюминий остается в самолете самым важным материалом.
Однако, все больше легкие металлы заменяют пластиками на основе углеродного волокна. Тем не менее, алюминиевая промышленность имеет твердую репутацию надежного партнера для производителей самолетов. В первую очередь, как источника большого потенциала для инноваций. Кроме того, серийное произодство деталей из углеродного волокна является не самым дешевым делом. В условиях конкуренции алюминиевая промышленность должна работать еще более напряженно. Поэтому несколько лет назад производители алюминия сфокусировались на композитных материалах.
Аэрокосмическая промышленность — это не тот рынок, который растет за счет расширения массового серийного производства. Поэтому новые технические находки по результатам научных исследований остаются основным источником роста. Что сегодня нужно, так это новые идеи, которые могли бы играть свою роль в будущем, в том числе и на земле.
Алюминий для космоса и авиации
Товары для офиса, дома, отдыха и спорта: еще больше алюминия
За счет легирования другими элементами, например, цинком, медью, кремнием или магнием, алюминий становится способным вомпринимать различные типы напряжений, которые возникают в машинах, агрегатах и изделиях. Дело металлургов – создавать подходящие алюминиевые сплавы, которые обладают заданными характеристиками.
В дополнение к своему малому весу алюминий имеет другие важные свойства, за которые его ценят инженеры-разработчики:
- химическая стойкость,
- разнообразие отделки поверхности,
- высокая проводимость тепла и электричества,
- высокая прочность,
- сложные формы литьем, прокаткой, ковкой, штамповкой или экструзией.
В последние годы у этих методов придания алюминию заданной формы появился серьезный конкурент — 3D-печать, особенно, для прототипов и малых серий изделий. Эксперты предсказывают 3D-печати огромный рынок. Мало того, что эта технология может быть более дешевой для производства отдельных изделий. Она может создавать детали с конструкционными характеристиками, которые нельзя получить традиционными технологиями.
Алюминиевое платье
Транспортное машиностроение: еще легче, еще эффективнее
В автобусах, грузовиках, вагонах или кораблях, на земле или на воде — везде алюминий дает идеи для современных, экологичных и экономичных решений в современном транспорте.
В рельсовом транспорте алюминий не только экономит энергию за счет своего малого веса, но также помогает поездам достигать более высоких скоростей. Четыре из пяти пассажирских вагонов в Западной Европе в настоящее время изготавливаются из алюминия.
Современные корабли должны быть быстрыми, манервенными, легкими и в тоже время прочными и долговечными. Все эти свойства им дают алюминиевые сплавы, которые применяются в современной судостроительной промышленности. Современные алюминиевые материалы обеспечивают все, что требуют корабли, яхты и катера: прочность, стойкость к коррозии, в том числе, в морской воде, а также , водо-, воздухо- и погодонепроницаемость.
В общественном транспорте, например, автобусах и трамваях, применение алюминия также дает свои выгоды. Современные городские автобусы с алюминиевым корпусом на несколько сотен килограммов легче, обычных автобусов.
Алюминий для транспорта
Упаковка: эффективная и непроницаемая
Функциональность, удобство и креативный дизайн — это только некоторые грани современной индустрии упаковки. Алюминий является одним из самых универсальных и эффективных упаковочных материалов, как в одиночку, так и в комбинации с другими материалами.
Алюминий обеспечивает надежную защиту продукции, но, что еще важнее для его рыночного успеха — это его непревзойденное удобство. Алюминиевые банки включают и аэрозольные банки. Эти аэрозольные банки дают нужную дозировку благодаря встроенной распылительной системе.
Переработка алюминиевой упаковки в Германии набирает обороты: из более, чем ста тысяч тонн алюминия, который применяется в упаковке, на переплавку поступает около 90 %. Для пивных банок результат даже выше — около 96 %.
Пора покупать билеты на самолет
Октябрь 2018 — это уже скоро. Самое время покупать билеты на самолет, пока они дешевые!
aluminium-guide.ru
Применение алюминия в автомобиле
Для автомобиля наиболее важным преимуществом алюминия и алюминиевых сплавов над сталями является их низкая плотность или, как часто говорят, удельный вес.
Зачем применять алюминий в автомобиле
Малая плотность
Плотность алюминиевых сплавов составляет в среднем 2,7 в граммах на кубический сантиметр по сравнению с 7,87 для сталей. Таким образом, плотность алюминиевых сплавов составляет только около 35 % от плотности сталей.
Модуль Юнга
Однако модуль упругости алюминиевых сталей равняется всего лишь 70 ГПа по сравнению с 207 ГПа для сталей. Это значит, что для одинаковой жесткости на изгиб алюминиевая балка должна быть на 43,5 % толще, чем стальная балка. Дело в том, что жесткость конструкционного элемента – балки, профиля или листа – из какого-либо материала прямо пропорциональна произведению модуля упругости этого материала на момент инерции поперечного сечения (Е·I) этого элемента. В результате, снижение веса, которое можно получить от применения алюминия по сравнению со сталью не будет пропорционально разнице в плотности этих двух материалов. В общем случае замена стальной балки на алюминиевую балку дает снижение веса примерно на 50 % (см. подробнее здесь).
И деформируемые, и литейные
Как литейные, так и деформируемые алюминиевые сплавы весьма широко применяются в автомобилях. Литейные алюминиевые сплавы применяются в основном для двигателя, трансмиссии и элементов подвески, тогда как деформируемые сплавы в виде листов и прессованных профилей применяются широко в конструкции кузова. Некоторые модели автомобилей, например Ауди А8 и Ауди А2, имеют полностью алюминиевый кузов.
См. еще Алюминий в автомобиле
Литейные алюминиевые сплавы
Сплавы с кремнием
Литейными алюминиевыми сплавами, которые применяют в автомобиле, являются в основном сплавы серии 300 (Al-Si-Cu или Al-Si-Mg), такие как:
- сплав 319 для впускного коллектора, головки цилиндра и корпуса трансмиссии;
- сплав 383 для блока цилиндров;
- сплав 356 для головки цилиндров и
- сплав А356 для колесных дисков и для рычагов подвески.
Главным легирующим элементом в этих сплавах является кремний, который обеспечивает им хорошие литейные свойства, в том числе, высокую жидкотекучесть. Эти сплавы отливают с применением ряда обычных методов от литья в песчаные формы и литья в стальные разъемные формы до более сложных методов литья, таких как, литье в постоянные формы и литье по выплавляемым моделям. Если к алюминиевой отливке предъявляются высокие требования по герметичности и количеству литейных дефектов, то применяют такие методы литья, как вакуумное литье под высоким давлением или литье в полужидком состоянии.
Сплавы с медью
Кроме литейных алюминиевых сплавов серии 3хх в автомобилях применяют также некоторые сплавы серии 2хх (Al-Cu). К ним относятся сплавы 201, 204 и 206, из которых отливают детали шасси, подвески и некоторые компоненты двигателя. Литейные алюминиевые сплавы обеих серий – и 2хх, и 3хх – являются термически упрочняемыми сплавами.
Таблица 2 – Химический состав литейных алюминиевых сплавов
Деформируемые алюминиевые сплавы
См. также Алюминиевые сплавы в автомобиле
Алюминиевые сплавы для теплообменников
Такие алюминиевые сплавы, как 1200 и 3005 применяются в теплообменниках, которые включают радиатор, трубы испарителя и ребра. Преимущества применения алюминия в таких изделиях состоит не только в том, что у алюминия очень высокая теплопроводность, но и в том, что у него значительно более высокое отношение прочность/плотность, чем у сплавов на основе меди, которые являются традиционными материалами для изготовления теплообменников.
Таблица 1 – Химический состав алюминиевых сплавов для теплообменников
Листовые алюминиевые сплавы
Листовыми алюминиевыми сплавами, которые применяют для панелей кузова, являются нагартовываемые сплавы серии 5ххх (Al-Mg), такие, как сплавы 5182, 5454 и 5754, а также термически упрочняемые сплавы серии 6ххх (Al-Mg-Si), такие как, 6009, 6061 и 6111.
Таблица 2 – Химический состав листовых алюминиевых сплавов
Сплавы серии 5ххх являются термически не упрочняемыми, то есть их практически невозможно упрочнить термической обработкой. Листы из этих сплавов поставляются в отожженном состоянии «О» и они получают деформационное упрочнение при выполнении операции штамповки из них листовых деталей.
Листы из сплавов серии 6ххх поставляются состоянии Т4, то есть в состоянии после закалки и естественного старения. Затем они получают упрочненное состояние Т6 за счет искусственного старения, которое происходит при нагреве в печи отверждения краски в ходе операции окраски.
Сплавы серии 5ххх хорошо поддаются формовке путем пластического деформирования. Однако, в ходе формовки листовых деталей из этих сплавов на их поверхности могут появляться следы пластической деформации растяжением (полосы Людера). Поэтому эти сплавы не применяют для наружных панелей, но применяют для внутренних панелей и деталей каркаса кузова. Листовые сплавы серии 6ххх не подвержены образованию полос Людера и поэтому их применяют как для внутренних и наружных панелей, так и для элементов каркаса кузова.
Алюминиевые сплавы для профилей
Сплавами для алюминиевых профилей — экструзионными алюминиевыми сплавами, которые применяются в конструкции автомобилей, являются:
- сплавы серии 6ххх (Al-Mg-Si) 6005, 6061, 6063 и 6082;
- сплавы серии 7ххх (Al-Zn-Mg): 7004, 7116, 7029 и 7129.
Профили из этих алюминиевых сплавов применяются для изготовления различных элементов каркаса кузова, усиления передних крыльев, опорной рамы двигателя, рамы сидений, балки бампера, детали рулевого управления.
Таблица 3 – Химический состав алюминиевых сплавов для профилей
Алюминиевые сплавы обеих серий – 6ххх и 7ххх – являются термически упрочняемыми путем нагрева под закалку (обработки на твердый раствор) с последующим естественным или искусственным старением. Сплавы серии 7ххх являются более трудными для прессования, чем сплавы серии 6ххх, особенно в случае сложных полых профилей. Они – сплавы серии 7ххх — кроме того, менее коррозионно стойкие и хуже свариваются.
Кузов: алюминиевый и стальной
Детали каркаса кузова автомобиля, такие как несущие элементы крыши, требуют многократной штамповки и сварки, когда их делают из стали. Если применять алюминий, то можно применять только один цельный прессованный алюминиевый профиль, который подвергают специальной обработке, например, гидроформингу. Применение только одного прессованного профиля вместо штампованного и сварного дает возможность сокращения количества необходимого оборудования и стоимости сборочных работ.
Штамповка алюминия по сравнению со сталью
В общем случае, способность алюминиевых сплавов к пластическому деформированию – пластической формовке – составляет около двух третей от такой способности у стали. Из-за более низкой способности к формовке сложные алюминиевые панели кузова могут потребовать несколько штамповочных операций или сборки из нескольких штампованных деталей.
Кроме того, из-за более низкого модуля упругости алюминия алюминиевые детали проявляют более высокую упругую отдачу после выполнения операции формовки, например, гибки. Поэтому алюминиевые штампованные детали труднее штамповать: они не так точно повторяют форму штампа, как стальные детали. В дополнение к этому алюминиевые сплавы имеют более высокую склонность к образованию царапин и следов инструмента, чем сталь и поэтому требуют большего количества смазки и большей чистоты поверхности штампового инструмента.
Особенности сварки алюминия
Хотя алюминиевые сплавы можно сваривать точечной сваркой сопротивления, как и сталь, существуют некоторые отличия ее применения для алюминия. При точечной сварке алюминия необходимо применять более высокую силу тока из-за его низкого электрического сопротивления и высокой теплопроводности. Сварочная сила тока для алюминиевых сплавов составляет 15-30 килоампер по сравнению с 8-10 килоампер для стали.
Это значит, что для контактной сварки алюминия нужны сварочные аппараты увеличенных размеров, а также повышенный расход электрической энергии.
Дуговая сварка плавлением (TIG и MIG) также могут применяться к алюминиевым сплавам. Однако из-за их высокой теплопроводности они требуют для сварки повышенного расхода энергии.
Из других методов соединения материалов, которые применяют для деталей из алюминиевых сплавов являются:
- самопробивные заклепки,
- запрессовка,
- клеевые соединения и
- комбинация контактной сварки с клеевым соединением.
Источник: Advanced Materials in Automotive Engineering, ed. Jason Rowe, Woodhead Publishing, 2012
aluminium-guide.ru