ΠΠΈΡΠ΅ΠΉΠ½ΡΠ΅ Π°Π»ΡΠΌΠΈΠ½ΠΈΠ΅Π²ΡΠ΅ ΡΠΏΠ»Π°Π²Ρ Ρ ΡΠΈΠ½ΠΊΠΎΠΌ ΠΈ ΠΌΠ°Π³Π½ΠΈΠ΅ΠΌ
ΠΠ»ΡΠΌΠΈΠ½ΠΈΠ΅Π²ΡΠ΅ ΡΠΏΠ»Π°Π²Ρ Π±ΡΠ²Π°ΡΡ Π΄Π΅ΡΠΎΡΠΌΠΈΡΡΠ΅ΠΌΡΠΌΠΈ ΠΈ Π»ΠΈΡΠ΅ΠΉΠ½ΡΠΌΠΈ. ΠΡΡ ΠΎΠ΄Π½ΡΠ΅ ΡΠ»ΠΈΡΠΊΠΈ Π΄Π΅ΡΠΎΡΠΌΠΈΡΡΠ΅ΠΌΡΡ ΡΠΏΠ»Π°Π²ΠΎΠ² ΠΏΠΎΠ΄Π²Π΅ΡΠ³Π°ΡΡ ΠΎΠ±ΡΠ°Π±ΠΎΡΠΊΠ΅ ΠΌΠ΅ΡΠΎΠ΄Π°ΠΌΠΈ ΠΎΠ±ΡΠ°Π±ΠΎΡΠΊΠΈ ΠΌΠ΅ΡΠ°Π»Π»ΠΎΠ² Π΄Π°Π²Π»Π΅Π½ΠΈΠ΅ΠΌ β ΠΏΡΠΎΠΊΠ°ΡΠΊΠΈ, ΠΏΡΠ΅ΡΡΠΎΠ²Π°Π½ΠΈΡ (ΡΠΊΡΡΡΡΠ·ΠΈΠΈ) ΠΈΠ»ΠΈ ΠΊΠΎΠ²ΠΊΠΈ.
Π Π΄Π΅ΡΠΎΡΠΌΠΈΡΡΠ΅ΠΌΡΠ΅, ΠΈ Π»ΠΈΡΠ΅ΠΉΠ½ΡΠ΅ Π°Π»ΡΠΌΠΈΠ½ΠΈΠ΅Π²ΡΠ΅ ΡΠΏΠ»Π°Π²Ρ ΠΈΠΌΠ΅ΡΡ, Π² ΠΏΡΠΈΠ½ΡΠΈΠΏΠ΅, ΠΎΠ΄Π½ΠΈ ΠΈ ΡΠ΅ ΠΆΠ΅ Π»Π΅Π³ΠΈΡΡΡΡΠΈΠ΅ ΡΠ»Π΅ΠΌΠ΅Π½ΡΡ. ΠΠ΄Π½Π°ΠΊΠΎ Π² Π΄Π΅ΡΠΎΡΠΌΠΈΡΡΠ΅ΠΌΡΡ ΡΠΏΠ»Π°Π²Π°Ρ ΠΈΡ ΡΠΎΠ΄Π΅ΡΠΆΠ°Π½ΠΈΠ΅ Π½Π°ΠΌΠ½ΠΎΠ³ΠΎ ΠΌΠ΅Π½ΡΡΠ΅, ΡΠ΅ΠΌ Π² Π»ΠΈΡΠ΅ΠΉΠ½ΡΡ . ΠΡΠ½ΠΎΠ²Π½ΡΠΌΠΈ Π»Π΅Π³ΠΈΡΡΡΡΠΈΠΌΠΈ ΡΠ»Π΅ΠΌΠ΅Π½ΡΠ°ΠΌΠΈ ΡΠ²Π»ΡΡΡΡΡ ΠΌΠ°Π³Π½ΠΈΠΉ, ΠΌΠ΅Π΄Ρ, ΠΊΡΠ΅ΠΌΠ½ΠΈΠΉ ΠΈ ΡΠΈΠ½ΠΊ. ΠΡΡΠ³ΠΈΠ΅ Π»Π΅Π³ΠΈΡΡΡΡΠΈΠ΅ ΡΠ»Π΅ΠΌΠ΅Π½ΡΡ β Π²ΡΠΏΠΎΠΌΠΎΠ³Π°ΡΠ΅Π»ΡΠ½ΡΠ΅ ΠΈ ΠΌΠΎΠ΄ΠΈΡΠΈΡΠΈΡΡΡΡΠΈΠ΅ β ΠΏΡΠΈΠΌΠ΅Π½ΡΡΡ Π΄Π»Ρ ΡΠ»ΡΡΡΠ΅Π½ΠΈΡ ΡΠΈΠ·ΠΈΡΠ΅ΡΠΊΠΈΡ ΠΈ ΠΌΠ΅Ρ Π°Π½ΠΈΡΠ΅ΡΠΊΠΈΡ ΡΠ²ΠΎΠΉΡΡΠ² ΠΎΡΠ»ΠΈΠ²ΠΎΠΊ ΠΈΠ· Π»ΠΈΡΠ΅ΠΉΠ½ΡΡ Π°Π»ΡΠΌΠΈΠ½ΠΈΠ΅Π²ΡΡ ΡΠΏΠ»Π°Π²ΠΎΠ².
ΠΠΈΡΠ΅ΠΉΠ½ΡΠ΅ ΡΠΏΠ»Π°Π²Ρ Π°Π»ΡΠΌΠΈΠ½ΠΈΠΉ-ΡΠΈΠ½ΠΊ-ΠΌΠ°Π³Π½ΠΈΠΉ
ΠΠ»ΡΠΌΠΈΠ½ΠΈΠ΅Π²ΡΠ΅ Π»ΠΈΡΠ΅ΠΉΠ½ΡΠ΅ ΡΠΏΠ»Π°Π²Ρ, Π»Π΅Π³ΠΈΡΠΎΠ²Π°Π½Π½ΡΠ΅ ΡΠΈΠ½ΠΊΠΎΠΌ ΠΈ ΠΌΠ°Π³Π½ΠΈΠ΅ΠΌ, ΡΠ΅ΡΠΌΠΈΡΠ΅ΡΠΊΠΈ ΡΠΏΡΠΎΡΠ½ΡΡΡΡΡ Π² ΠΏΡΠΎΡΠ΅ΡΡΠ΅ ΠΎΠ±ΡΡΠ½ΠΎΠ³ΠΎ Π²ΡΠ»Π΅ΠΆΠΈΠ²Π°Π½ΠΈΡ, ΡΠΎ Π΅ΡΡΡ Π΅ΡΡΠ΅ΡΡΠ²Π΅Π½Π½ΠΎΠ³ΠΎ ΡΡΠ°ΡΠ΅Π½Π΅Π½ΠΈΡ. ΠΡΠΈ ΡΡΠΎΠΌ ΠΌΠ°ΠΊΡΠΈΠΌΠ°Π»ΡΠ½Π°Ρ ΠΏΡΠΎΡΠ½ΠΎΡΡΡ Π΄ΠΎΡΡΠΈΠ³Π°Π΅ΡΡΡ ΡΠ΅ΡΠ΅Π· 20-30 ΡΡΡΠΎΠΊ ΠΏΠΎΡΠ»Π΅ ΡΠ°Π·Π»ΠΈΠ²ΠΊΠΈ ΠΈ ΠΏΡΠΈ Π²ΡΠ΄Π΅ΡΠΆΠΊΠ΅ ΠΏΡΠΈ ΠΊΠΎΠΌΠ½Π°ΡΠ½ΠΎΠΉ ΡΠ΅ΠΌΠΏΠ΅ΡΠ°ΡΡΡΠ΅. ΠΡΠΎ ΠΏΡΠΎΡΠ΅ΡΡ ΡΠΏΡΠΎΡΠ½Π΅Π½ΠΈΡ ΠΌΠΎΠΆΠ΅Ρ Π±ΡΡΡ ΡΡΠΊΠΎΡΠ΅Π½ ΠΈΡΠΊΡΡΡΡΠ²Π΅Π½Π½ΡΠΌ ΡΡΠ°ΡΠ΅Π½ΠΈΠ΅ΠΌ.
ΠΠ»ΡΠΌΠΈΠ½ΠΈΠ΅Π²ΡΠ΅ Π»ΠΈΡΠ΅ΠΉΠ½ΡΠ΅ ΡΠΏΠ»Π°Π²Ρ ΡΠ΅ΡΠΈΠΈ 7Ρ Ρ .Ρ
ΠΠΎ Π°ΠΌΠ΅ΡΠΈΠΊΠ°Π½ΡΠΊΠΎΠΉ ΠΊΠ»Π°ΡΡΠΈΡΠΈΠΊΠ°ΡΠΈΠΈ ΡΡΠΈ ΡΠΏΠ»Π°Π²Ρ ΠΎΡΠ½ΠΎΡΡΡΡΡ ΠΊ ΡΠ΅ΡΠΈΠΈ 7Ρ Ρ .Ρ . ΠΠ½ΠΈ ΠΈΠΌΠ΅ΡΡ ΠΏΡΠΎΡΠ½ΠΎΡΡΠ½ΡΠ΅ ΡΠ²ΠΎΠΉΡΡΠ²Π° ΠΎΡ ΡΡΠ΅Π΄Π½ΠΈΡ Π΄ΠΎ Π²ΡΡΠΎΠΊΠΈΡ . ΠΡΡΠ΅ΠΌ ΠΎΡΠΆΠΈΠ³Π° ΠΎΠ±Π΅ΡΠΏΠ΅ΡΠΈΠ²Π°Π΅ΡΡΡ Ρ ΠΎΡΠΎΡΠ°Ρ ΡΡΠ°Π±ΠΈΠ»ΡΠ½ΠΎΡΡΡ ΡΠ°Π·ΠΌΠ΅ΡΠΎΠ². ΠΠ²ΡΠ΅ΠΊΡΠΈΡΠ΅ΡΠΊΠ°Ρ ΡΠΎΡΠΊΠ° ΡΠΏΠ»Π°Π²ΠΎΠ² ΡΡΠΎΠΉ Π³ΡΡΠΏΠΏΡ ΡΠ²Π»ΡΠ΅ΡΡΡ Π²ΡΡΠΎΠΊΠΎΠΉ, ΡΡΠΎ Π±Π»Π°Π³ΠΎΠΏΡΠΈΡΡΠ½ΠΎ Π΄Π»Ρ Π΄Π΅ΡΠ°Π»Π΅ΠΉ, ΠΊΠΎΡΠΎΡΡΠ΅ ΠΏΠΎΠ΄Π²Π΅ΡΠ³Π°ΡΡΡΡ ΠΏΠ°ΠΉΠΊΠ΅. ΠΡΠΈ ΡΠΏΠ»Π°Π²Ρ ΠΈΠΌΠ΅ΡΡ Ρ ΠΎΡΠΎΡΡΡ ΠΌΠ΅Ρ Π°Π½ΠΈΡΠ΅ΡΠΊΡΡ ΠΎΠ±ΡΠ°Π±Π°ΡΡΠ²Π°Π΅ΠΌΠΎΡΡΡ. ΠΠ»Ρ Π½ΠΈΡ Ρ Π°ΡΠ°ΠΊΡΠ΅ΡΠ½Π° Π²ΡΡΠΎΠΊΠ°Ρ ΠΊΠΎΡΡΠΎΠ·ΠΈΠΎΠ½Π½Π°Ρ ΡΡΠΎΠΉΠΊΠΎΡΡΡ ΠΏΡΠΈ Π½Π΅ΠΊΠΎΡΠΎΡΠΎΠΉ ΡΠΊΠ»ΠΎΠ½Π½ΠΎΡΡΠΈ ΠΊ ΠΊΠΎΡΡΠΎΠ·ΠΈΠΈ ΠΏΠΎΠ΄ Π½Π°ΠΏΡΡΠΆΠ΅Π½ΠΈΠ΅ΠΌ. ΠΡ Π½Π΅ ΡΠ΅ΠΊΠΎΠΌΠ΅Π½Π΄ΡΡΡ Π΄Π»Ρ ΠΏΡΠΈΠΌΠ΅Π½Π΅Π½ΠΈΡ ΠΏΡΠΈ ΠΏΠΎΠ²ΡΡΠ΅Π½Π½ΡΡ ΡΠ΅ΠΌΠΏΠ΅ΡΠ°ΡΡΡΠ°Ρ . ΠΡΠΎΡΠ½ΠΎΡΡΠ½ΡΠ΅ ΡΠ²ΠΎΠΉΡΡΠ²Π° ΡΡΠΈΡ ΡΠΏΠ»Π°Π²ΠΎΠ² ΠΏΠΎΠ²ΡΡΠ°ΡΡΡΡ ΠΏΡΠΈ ΠΊΠΎΠΌΠ½Π°ΡΠ½ΠΎΠΉ Π² ΡΠ΅ΡΠ΅Π½ΠΈΠ΅ Π½Π΅ΡΠΊΠΎΠ»ΡΠΊΠΈΡ Π½Π΅Π΄Π΅Π»Ρ ΠΏΠΎΡΠ»Π΅ ΡΠ°Π·Π»ΠΈΠ²ΠΊΠΈ Π² ΡΠ΅Π·ΡΠ»ΡΡΠ°ΡΠ΅ ΡΠΏΡΠΎΡΠ½Π΅Π½ΠΈΡ ΠΏΠΎ ΠΌΠ΅Ρ Π°Π½ΠΈΠ·ΠΌΡ Π²ΡΠ΄Π΅Π»Π΅Π½ΠΈΡ Π²ΡΠΎΡΠΈΡΠ½ΠΎΠΉ ΡΠ°Π·Ρ. ΠΡΠΎΡ ΠΏΡΠΎΡΠ΅ΡΡ ΠΏΡΠΎΠ΄ΠΎΠ»ΠΆΠ°Π΅ΡΡΡ ΠΈ ΠΏΠΎΡΠ»Π΅ Π½Π΅ΡΠΊΠΎΠ»ΡΠΊΠΈΡ Π½Π΅Π΄Π΅Π»Ρ, Π½ΠΎ ΡΠΆΠ΅ Ρ ΡΠΌΠ΅Π½ΡΡΠ°ΡΡΠ΅ΠΉΡΡ ΡΠΊΠΎΡΠΎΡΡΡΡ. Π ΡΠΏΠ»Π°Π²Π°ΠΌ 707.0, 771.0 ΠΈ 772.0 ΠΌΠΎΠ³ΡΡ ΠΏΡΠΈΠΌΠ΅Π½ΡΡΡΡΡ ΡΠ΅ΡΠΌΠΈΡΠ΅ΡΠΊΠΈΠ΅ ΠΎΠ±ΡΠ°Π±ΠΎΡΠΊΠΈ ΡΠΈΠΏΠ° Π’6 ΠΈ Π’7.
ΠΠΈΡΠ΅ΠΉΠ½ΡΠ΅ ΡΠ²ΠΎΠΉΡΡΠ²Π°
ΠΠΈΡΠ΅ΠΉΠ½ΡΠ΅ ΡΠ²ΠΎΠΉΡΡΠ²Π° Π»ΠΈΡΠ΅ΠΉΠ½ΡΡ Π°Π»ΡΠΌΠΈΠ½ΠΈΠ΅Π²ΡΡ ΡΠΏΠ»Π°Π²ΠΎΠ² ΡΠΈΡΡΠ΅ΠΌΡ Π°Π»ΡΠΌΠΈΠ½ΠΈΠΉ-ΡΠΈΠ½ΠΊ-ΠΌΠ°Π³Π½ΠΈΠΉ Π²Π΅ΡΡΠΌΠ° ΠΏΠΎΡΡΠ΅Π΄ΡΡΠ²Π΅Π½Π½ΡΠ΅. ΠΠΎΡΡΠΎΠΌΡ Π΄Π»Ρ ΠΏΠΎΠ»ΡΡΠ΅Π½ΠΈΡ Ρ ΠΎΡΠΎΡΠΈΡ ΠΎΡΠ»ΠΈΠ²ΠΎΠΊ ΡΡΠ΅Π±ΡΠ΅ΡΡΡ ΠΆΠ΅ΡΡΠΊΠΈΠΉ ΠΊΠΎΠ½ΡΡΠΎΠ»Ρ ΡΡΠ»ΠΎΠ²ΠΈΠΉ Π·Π°ΡΠ²Π΅ΡΠ΄Π΅Π²Π°Π½ΠΈΡ. Π§ΡΠΎΠ±Ρ ΠΏΡΠ΅Π΄ΠΎΡΠ²ΡΠ°ΡΠΈΡΡ ΡΡΠ°Π΄ΠΎΡΠ½ΡΠ΅ Π΄Π΅ΡΠ΅ΠΊΡΡ ΠΏΡΠΈΠΌΠ΅Π½ΡΡΡ ΠΎΡ Π»Π°ΠΆΠ΄Π΅Π½ΠΈΠ΅ Ρ ΡΠΌΠ΅ΡΠ΅Π½Π½ΡΠΌΠΈ ΠΈ Π²ΡΡΠΎΠΊΠΈΠΌΠΈ ΡΠ΅ΠΌΠΏΠ΅ΡΠ°ΡΡΡΠ½ΡΠΌΠΈ Π³ΡΠ°Π΄ΠΈΠ΅Π½ΡΠ°ΠΌΠΈ. Π§Π°ΡΠ΅ Π΄Π»Ρ ΡΡΠΈΡ ΡΠΏΠ»Π°Π²ΠΎΠ² ΠΏΡΠΈΠΌΠ΅Π½ΡΡΡ Π»ΠΈΡΡΠ΅ Π² ΠΏΠ΅ΡΡΠ°Π½ΡΠ΅ ΡΠΎΡΠΌΡ, Π° ΠΏΡΠΈ Π»ΠΈΡΡΠ΅ Π² ΠΏΠΎΡΡΠΎΡΠ½Π½ΡΠ΅ ΡΠΎΡΠΌΡ ΠΌΠΎΠΆΠ½ΠΎ ΡΡΠΎΠ»ΠΊΠ½ΡΡΡΡΡ ΡΠΎ Π·Π½Π°ΡΠΈΡΠ΅Π»ΡΠ½ΡΠΌΠΈ ΡΡΡΠ΄Π½ΠΎΡΡΡΠΌΠΈ.
ΠΠΈΡΠ΅ΠΉΠ½ΡΠΉ Π°Π»ΡΠΌΠΈΠ½ΠΈΠ΅Π²ΡΠΉ ΡΠΏΠ»Π°Π² 771.0
Π₯ΠΈΠΌΠΈΡΠ΅ΡΠΊΠΈΠΉ ΡΠΎΡΡΠ°Π²
Π€ΠΎΡΠΌΡΠ»Π° ΡΠΏΠ»Π°Π²Π°: 7Zn-0,9Mg-0,13Cr
Π₯ΠΈΠΌΠΈΡΠ΅ΡΠΊΠΈΠΉ ΡΠΎΡΡΠ°Π²:
- ΠΌΠ΅Π΄Ρ: 0,10 % ΠΌΠ°ΠΊΡ.;
- ΠΌΠ°Π³Π½ΠΈΠΉ: 0,8-1,0 %;
- ΠΌΠ°ΡΠ³Π°Π½Π΅Ρ: 0,10 % ΠΌΠ°ΠΊΡ.;
- ΠΊΡΠ΅ΠΌΠ½ΠΈΠΉ: 0,15 % ΠΌΠ°ΠΊΡ.;
- ΠΆΠ΅Π»Π΅Π·ΠΎ: 0,15 % ΠΌΠ°ΠΊΡ.;
- Ρ ΡΠΎΠΌ: 0,06-0,20 %;
- ΡΠΈΠ½ΠΊ: 6,5-7,5 %;
- ΠΎΠ»ΠΎΠ²ΠΎ: 3,5 % ΠΌΠ°ΠΊΡ.;
- ΡΠΈΡΠ°Π½: 0,10-0,20 %;
- Π΄ΡΡΠ³ΠΈΠ΅: 0,05 % ΠΊΠ°ΠΆΠ΄ΠΎΠ³ΠΎ, 0,15 % Π² ΡΡΠΌΠΌΠ΅ ΠΌΠ°ΠΊΡ.;
- Π°Π»ΡΠΌΠΈΠ½ΠΈΠΉ: ΠΎΡΡΠ°Π»ΡΠ½ΠΎΠ΅.
Π‘Π²ΠΎΠΉΡΡΠ²Π°: ΠΌΠ΅Ρ Π°Π½ΠΈΡΠ΅ΡΠΊΠΈΠ΅ ΠΈ ΡΠΈΠ·ΠΈΡΠ΅ΡΠΊΠΈΠ΅
Π’ΠΈΠΏΠΈΡΠ½ΡΠ΅ ΠΌΠ΅Ρ Π°Π½ΠΈΡΠ΅ΡΠΊΠΈΠ΅ ΡΠ²ΠΎΠΉΡΡΠ²Π° (Π’5):
- ΠΏΡΠΎΡΠ½ΠΎΡΡΡ Π½Π° ΡΠ°ΡΡΡΠΆΠ΅Π½ΠΈΠ΅: 290 ΠΠΠ°;
- ΠΏΡΠ΅Π΄Π΅Π» ΡΠ΅ΠΊΡΡΠ΅ΡΡΠΈ: 260 ΠΠΠ°;
- ΠΎΡΠ½ΠΎΡΠΈΡΠ΅Π»ΡΠ½ΠΎΠ΅ ΡΠ΄Π»ΠΈΠ½Π΅Π½ΠΈΠ΅: 1,5 %;
- ΠΌΠΎΠ΄ΡΠ»Ρ ΡΠΏΡΡΠ³ΠΎΡΡΠΈ: 71,0 ΠΠΠ°.
Π€ΠΈΠ·ΠΈΡΠ΅ΡΠΊΠΈΠ΅ ΡΠ²ΠΎΠΉΡΡΠ²Π°:
- ΠΏΠ»ΠΎΡΠ½ΠΎΡΡΡ: 2,823 Π³/ΡΠΌ3;
- ΡΠ΅ΠΌΠΏΠ΅ΡΠ°ΡΡΡΠ° Π»ΠΈΠΊΠ²ΠΈΠ΄ΡΡ: 645 ΒΊΠ‘;
- ΡΠ΅ΠΌΠΏΠ΅ΡΠ°ΡΡΡΠ° ΡΠΎΠ»ΠΈΠ΄ΡΡ: 605 ΒΊΠ‘.
Π’Π΅ΡΠΌΠΈΡΠ΅ΡΠΊΠ°Ρ ΠΎΠ±ΡΠ°Π±ΠΎΡΠΊΠ°
ΠΡΠΎΡ ΡΠΏΠ»Π°Π² ΠΌΠΎΠΆΠ½ΠΎ ΡΠ΅ΡΠΌΠΈΡΠ΅ΡΠΊΠΈ ΠΎΠ±ΡΠ°Π±Π°ΡΡΠ²Π°ΡΡ Π½Π° ΡΠΎΡΡΠΎΡΠ½ΠΈΡ Π’2, Π’5, Π’51, Π’52 ΠΈ Π’71
Π’Π΅ΡΠΌΠΈΡΠ΅ΡΠΊΠ°Ρ ΠΎΠ±ΡΠ°Π±ΠΎΡΠΊΠ° Π½Π° ΡΠΎΡΡΠΎΡΠ½ΠΈΠ΅ Π’5:
- Π²ΡΠ΄Π΅ΡΠΆΠΊΠ° ΠΏΡΠΈ 180 ΒΊΠ‘ Π² ΡΠ΅ΡΠ΅Π½ΠΈΠ΅ 3-5 ΡΠ°ΡΠΎΠ²;
- ΠΎΡ Π»Π°ΠΆΠ΄Π΅Π½ΠΈΠ΅ Π²Π½Π΅ ΠΏΠ΅ΡΠΈ Π½Π° ΡΠΏΠΎΠΊΠΎΠΉΠ½ΠΎΠΌ Π²ΠΎΠ·Π΄ΡΡ Π΅.
Π’Π΅ΡΠΌΠΈΡΠ΅ΡΠΊΠ°Ρ ΠΎΠ±ΡΠ°Π±ΠΎΡΠΊΠ° Π½Π° ΡΠΎΡΡΠΎΡΠ½ΠΈΠ΅ Π’51:
- Π²ΡΠ΄Π΅ΡΠΆΠΊΠ° ΠΏΡΠΈ 205 ΒΊΠ‘ Π² ΡΠ΅ΡΠ΅Π½ΠΈΠ΅ 6 ΡΠ°ΡΠΎΠ²;
- ΠΎΡ Π»Π°ΠΆΠ΄Π΅Π½ΠΈΠ΅ Π²Π½Π΅ ΠΏΠ΅ΡΠΈ Π½Π° ΡΠΏΠΎΠΊΠΎΠΉΠ½ΠΎΠΌ Π²ΠΎΠ·Π΄ΡΡ Π΅.
Π’Π΅ΡΠΌΠΈΡΠ΅ΡΠΊΠ°Ρ ΠΎΠ±ΡΠ°Π±ΠΎΡΠΊΠ° Π½Π° ΡΠΎΡΡΠΎΡΠ½ΠΈΠ΅ Π’6:
- Π²ΡΠ΄Π΅ΡΠΆΠΊΠ° ΠΏΡΠΈ 580-595 ΒΊΠ‘ Π² ΡΠ΅ΡΠ΅Π½ΠΈΠ΅ 6 ΡΠ°ΡΠΎΠ²;
- ΠΎΡ Π»Π°ΠΆΠ΄Π΅Π½ΠΈΠ΅ Π²Π½Π΅ ΠΏΠ΅ΡΠΈ Π½Π° ΡΠΏΠΎΠΊΠΎΠΉΠ½ΠΎΠΌ Π²ΠΎΠ·Π΄ΡΡ Π΅ Π΄ΠΎ ΠΊΠΎΠΌΠ½Π°ΡΠ½ΠΎΠΉ ΡΠ΅ΠΌΠΏΠ΅ΡΠ°ΡΡΡΡ;
- ΡΡΠ°ΡΠ΅Π½ΠΈΠ΅ ΠΏΡΡΠ΅ΠΌ Π²ΡΠ΄Π΅ΡΠΆΠΊΠΈ Π² ΡΠ΅ΡΠ΅Π½ΠΈΠ΅ 3 ΡΠ°ΡΠΎΠ² ΠΏΡΠΈ ΡΠ΅ΠΌΠΏΠ΅ΡΠ°ΡΡΡΠ΅ 130 ΒΊΠ‘;
- ΠΎΡ Π»Π°ΠΆΠ΄Π΅Π½ΠΈΠ΅ Π½Π° ΡΠΏΠΎΠΊΠΎΠΉΠ½ΠΎΠΌ Π²ΠΎΠ·Π΄ΡΡ Π΅.
ΠΠ΅Ρ Π°Π½ΠΈΡΠ΅ΡΠΊΠ°Ρ ΠΎΠ±ΡΠ°Π±ΠΎΡΠΊΠ°
Π‘ΠΏΠ»Π°Π² 771.0 Π² ΡΠΎΡΡΠΎΡΠ½ΠΈΠΈ Π’5 ΠΈΠΌΠ΅Π΅Ρ Ρ ΠΎΡΠΎΡΡΡ ΡΡΠ°Π±ΠΈΠ»ΡΠ½ΠΎΡΡΡ ΠΈ ΠΎΠ±ΡΠ°Π±Π°ΡΡΠ²Π°Π΅ΠΌΠΎΡΡΡ ΡΠ΅Π·Π°Π½ΠΈΠ΅ΠΌ. ΠΠ³ΠΎ ΠΌΠΎΠΆΠ½ΠΎ ΡΡΠ΅Π·Π΅ΡΠΎΠ²Π°ΡΡ Π² 5 ΡΠ°Π· Π±ΡΡΡΡΠ΅Π΅, Π° ΡΠ²Π΅ΡΠ»ΠΈΡΡ Π² 2 ΡΠ°Π·Π° Π±ΡΡΡΡΠ΅Π΅, ΡΠ΅ΠΌ ΡΠ°ΠΊΠΈΠ΅ ΡΠΏΠ»Π°Π²Ρ ΠΊΠ°ΠΊ 356.0 ΠΈ 319.0.
Π‘Π²Π°ΡΠΊΠ°
ΠΠΎΠΆΠ΅Ρ ΡΠ²Π°ΡΠΈΠ²Π°ΡΡΡΡ Π³Π°Π·ΠΎΠ²ΠΎΠΉ Π΄ΡΠ³ΠΎΠ²ΠΎΠΉ ΡΠ²Π°ΡΠΊΠΎΠΉ Π²ΠΎΠ»ΡΡΡΠ°ΠΌΠΎΠ²ΡΠΌ ΠΈΠ»ΠΈ ΠΌΠ΅ΡΠ°Π»Π»ΠΈΡΠ΅ΡΠΊΠΈΠΌ ΡΠ»Π΅ΠΊΡΡΠΎΠ΄ΠΎΠΌ Ρ ΠΏΡΠΈΠΌΠ΅Π½Π΅Π½ΠΈΠ΅ΠΌ Π°Π»ΡΠΌΠΈΠ½ΠΈΠ΅Π²ΠΎΠ³ΠΎ ΡΠ²Π°ΡΠΎΡΠ½ΠΎΠ³ΠΎ ΡΠΏΠ»Π°Π²Π° 5356. Π Π·Π°Π²ΠΈΡΠΈΠΌΠΎΡΡΠΈ ΠΎΡ ΡΠ΅ΡΠΌΠΈΡΠ΅ΡΠΊΠΎΠ³ΠΎ ΡΠΎΡΡΠΎΡΠ½ΠΈΡ ΠΎΡΠ»ΠΈΠ²ΠΊΠΈ ΠΏΠΎΡΠ»Π΅ ΡΠ²Π°ΡΠΊΠΈ ΠΌΠΎΠΆΠ΅Ρ Π²ΠΎΠ·Π½ΠΈΠΊΠ½ΡΡΡ Π½Π΅ΠΎΠ±Ρ ΠΎΠ΄ΠΈΠΌΠΎΡΡΡ ΡΠΏΠ΅ΡΠΈΠ°Π»ΡΠ½ΠΎΠΉ ΡΠ΅ΡΠΌΠΈΡΠ΅ΡΠΊΠΎΠΉ ΠΎΠ±ΡΠ°Π±ΠΎΡΠΊΠΈ.
Π ΡΠΎΡΡΠΎΡΠ½ΠΈΠΈ Π’5 ΡΠ²Π°ΡΠΊΡ Π½Π΅ ΠΏΡΠΎΠΈΠ·Π²ΠΎΠ΄ΡΡ. ΠΠ»Ρ ΠΏΠΎΡΠ»Π΅Π΄ΡΡΡΠ΅ΠΉ ΡΠ²Π°ΡΠΊΠΈ ΠΏΡΠΎΠΈΠ·Π²ΠΎΠ΄ΡΡ ΡΠ΅ΡΠΌΠΈΡΠ΅ΡΠΊΡΡ ΠΎΠ±ΡΠ°Π±ΠΎΡΠΊΡ Π½Π° ΡΠΎΡΡΠΎΡΠ½ΠΈΠ΅ Π’51.
Π€Π°Π·ΠΎΠ²Π°Ρ Π΄ΠΈΠ°Π³ΡΠ°ΠΌΠΌΠ° Π°Π»ΡΠΌΠΈΠ½ΠΈΠΉ-ΡΠΈΠ½ΠΊ
ΠΡΡΠΎΡΠ½ΠΈΠΊ: Aluminum and Aluminum Alloys, ASM International, 1996
Π¦ΠΈΠ½ΠΊ-Π°Π»ΡΠΌΠΈΠ½ΠΈΠ΅Π²ΡΠ΅ ΡΠΏΠ»Π°Π²Ρ
ΠΠ°Π·Π½Π°ΡΠ΅Π½ΠΈΠ΅ ΠΈ ΠΎΠΏΠΈΡΠ°Π½ΠΈΠ΅
Π¦ΠΈΠ½ΠΊ-Π°Π»ΡΠΌΠΈΠ½ΠΈΠ΅Π²ΡΠ΅ ΡΠΏΠ»Π°Π²Ρ ΠΏΡΠΎΠΈΠ·Π²ΠΎΠ΄ΡΡΡΡ ΠΏΠΎΒ Π’Π£ 1721-025-00194286-2015.
Π¦ΠΈΠ½ΠΊ-Π°Π»ΡΠΌΠΈΠ½ΠΈΠ΅Π²ΡΠ΅ ΡΠΏΠ»Π°Π²Ρ ΠΈΡΠΏΠΎΠ»ΡΠ·ΡΡΡΡΡ Π΄Π»Ρ Π³ΠΎΡΡΡΠ΅Π³ΠΎ ΠΎΡΠΈΠ½ΠΊΠΎΠ²Π°Π½ΠΈΡ ΡΡΠ°Π»ΡΠ½ΠΎΠΉ ΠΏΠΎΠ»ΠΎΡΡ.
Π₯ΠΈΠΌΠΈΡΠ΅ΡΠΊΠΈΠΉ ΡΠΎΡΡΠ°Π²*
ΠΠ°ΡΡΠΎΠ²Π°Ρ Π΄ΠΎΠ»Ρ, % |
ΠΠ°ΡΠΊΠ° ΡΠΈΠ½ΠΊ — Π°Π»ΡΠΌΠΈΠ½ΠΈΠ΅Π²ΠΎΠ³ΠΎ ΡΠΏΠ»Π°Π²Π° | |||
Π¦Π0 | Π¦Π03 | Π¦Π04 | Π¦Π10 | |
Π¦ΠΈΠ½ΠΊ | ΠΡΡΠ°Π»ΡΠ½ΠΎΠ΅ | ΠΡΡΠ°Π»ΡΠ½ΠΎΠ΅ | ΠΡΡΠ°Π»ΡΠ½ΠΎΠ΅ | ΠΡΡΠ°Π»ΡΠ½ΠΎΠ΅ |
ΠΠ»ΡΠΌΠΈΠ½ΠΈΠΉ | - | ΠΎΡ 0,25 Π΄ΠΎ 0,35 | ΠΎΡ 0,36 Π΄ΠΎ 0,45 | ΠΎΡ 9,5 Π΄ΠΎ 10 |
Π‘Π²ΠΈΠ½Π΅Ρ | ΠΎΡ 0,1 Π΄ΠΎ 0,2 | ΠΎΡ 0,1 Π΄ΠΎ 0,2 | ΠΎΡ 0,1 Π΄ΠΎ 0,2 | ΠΎΡ 0,1 Π΄ΠΎ 0,2 |
ΠΠ΅Π»Π΅Π·ΠΎ | 0,01 | 0,01 | 0,01 | 0,018 |
ΠΠ°Π΄ΠΌΠΈΠΉ | 0,01 | 0,01 | 0,01 | 0,01 |
ΠΠ΅Π΄Ρ | 0,002 | 0,002 | 0,002 | 0,002 |
ΠΠ»ΠΎΠ²ΠΎ | 0,001 | 0,001 | 0,001 | 0,001 |
ΠΡΡΡΡΠΊ | 0,0005 | 0,0005 | 0,0005 | 0,0005 |
* Π‘ΠΎΠ΄Π΅ΡΠΆΠ°Π½ΠΈΠ΅ Π°Π»ΡΠΌΠΈΠ½ΠΈΡ, ΡΠ²ΠΈΠ½ΡΠ°, ΠΊΠ°Π΄ΠΌΠΈΡ ΠΈΠ»ΠΈ ΠΎΡΠ΄Π΅Π»ΡΠ½ΡΡ ΠΏΡΠΈΠΌΠ΅ΡΠ΅ΠΉ Π² ΡΠΏΠ»Π°Π²Π΅ ΠΌΠΎΠΆΠ΅Ρ Π±ΡΡΡ ΠΈΠ·ΠΌΠ΅Π½Π΅Π½ΠΎ ΠΏΠΎ ΡΡΠ΅Π±ΠΎΠ²Π°Π½ΠΈΡ ΠΏΠΎΡΡΠ΅Π±ΠΈΡΠ΅Π»Ρ. ΠΡΠΈ ΡΡΠΎΠΌ ΡΠΎΠ΄Π΅ΡΠΆΠ°Π½ΠΈΠ΅ ΡΠΈΠ½ΠΊΠ°, ΡΠΎΠΎΡΠ²Π΅ΡΡΡΠ²ΡΡΡΠ΅Π΅ ΠΎΠΏΡΠ΅Π΄Π΅Π»Π΅Π½Π½ΠΎΠΉ ΠΌΠ°ΡΠΊΠ΅ ΡΠΏΠ»Π°Π²Π°, Π΄ΠΎΠ»ΠΆΠ½ΠΎ Π±ΡΡΡ ΡΠ²Π΅Π»ΠΈΡΠ΅Π½ΠΎ (ΡΠΌΠ΅Π½ΡΡΠ΅Π½ΠΎ) Π½Π° Π²Π΅Π»ΠΈΡΠΈΠ½Ρ ΡΠΎΠ΄Π΅ΡΠΆΠ°Π½ΠΈΡ Π»Π΅Π³ΠΈΡΡΡΡΠΈΡ ΠΊΠΎΠΌΠΏΠΎΠ½Π΅Π½ΡΠΎΠ² ΠΈΠ»ΠΈ ΠΏΡΠΈΠΌΠ΅ΡΠ΅ΠΉ.
Π£ΠΏΠ°ΠΊΠΎΠ²ΠΊΠ° ΠΈ ΡΡΠ°Π½ΡΠΏΠΎΡΡΠΈΡΠΎΠ²ΠΊΠ°
Π¦ΠΈΠ½ΠΊ-Π°Π»ΡΠΌΠΈΠ½ΠΈΠ΅Π²ΡΠ΅ ΡΠΏΠ»Π°Π²Ρ Π¦Π0, Π¦Π03, Π¦Π04 Π²ΡΠΏΡΡΠΊΠ°ΡΡΡΡ Π² Π²ΠΈΠ΄Π΅ Π±Π»ΠΎΠΊΠΎΠ² ΠΌΠ°ΡΡΠΎΠΉ Π΄ΠΎ 1500 ΠΊΠ³, Β ΡΠΏΠ»Π°Π²Ρ Π¦Π0, Π¦Π10 β Π² Π²ΠΈΠ΄Π΅ ΡΡΡΠ΅ΠΊ ΠΌΠ°ΡΡΠΎΠΉ 19-25 ΠΊΠ³. ΠΠΎΠΏΡΡΠΊΠ°Π΅ΠΌΡΠ΅ ΠΎΡΠΊΠ»ΠΎΠ½Π΅Π½ΠΈΡ ΠΏΠΎ ΠΌΠ°ΡΡΠ΅ Π±Π»ΠΎΠΊΠΎΠ² ΠΈ ΡΠΏΠ°ΠΊΠΎΠ²ΠΊΠ° ΠΏΠΎ ΠΠΠ‘Π’ 3640.
Π’ΡΠ°Π½ΡΠΏΠΎΡΡΠΈΡΡΠ΅ΡΡΡ Π²ΡΠ΅ΠΌΠΈ Π²ΠΈΠ΄Π°ΠΌΠΈ ΠΊΡΡΡΡΡ ΡΡΠ°Π½ΡΠΏΠΎΡΡΠ½ΡΡ ΡΡΠ΅Π΄ΡΡΠ².
ΠΠ°ΡΠ°Π½ΡΠΈΠΉΠ½ΡΠΉ ΡΡΠΎΠΊ Ρ ΡΠ°Π½Π΅Π½ΠΈΡ
15 Π»Π΅Ρ Ρ ΠΌΠΎΠΌΠ΅Π½ΡΠ° ΠΈΠ·Π³ΠΎΡΠΎΠ²Π»Π΅Π½ΠΈΡ.
ΠΠΎ Π²ΠΎΠΏΡΠΎΡΠ°ΠΌ ΠΏΡΠΈΠΎΠ±ΡΠ΅ΡΠ΅Π½ΠΈΡ ΠΏΡΠΎΠ΄ΡΠΊΡΠΈΠΈ:
- ΠΠ°ΡΠ°Π»ΡΠ½ΠΈΠΊ ΠΎΡΠ΄Π΅Π»Π° ΡΠ±ΡΡΠ° ΠΠΠ Β«Π£ΠΠΠ-Π₯ΠΎΠ»Π΄ΠΈΠ½Π³Β» ΠΠΎΠ·Π»ΠΎΠ² Π’Π°ΡΠ°Ρ ΠΠ΅Π½Π½Π°Π΄ΡΠ΅Π²ΠΈΡ +7(34368)9-69-18
- ΠΠ°ΡΠ°Π»ΡΠ½ΠΈΠΊ ΠΊΠΎΠΌΠΌΠ΅ΡΡΠ΅ΡΠΊΠΎΠ³ΠΎ ΠΎΡΠ΄Π΅Π»Π° ΠΠΠ Β«Π§Π¦ΠΒ» ΠΠ΅ΡΡΠ½ΠΊΠΈΠ½ ΠΠ»Π΅ΠΊΡΠ°Π½Π΄Ρ ΠΠΈΡ Π°ΠΉΠ»ΠΎΠ²ΠΈΡ +7(351)799-00-20
Β ΠΠΎΡΡΠ΄ΠΎΠΊ ΠΏΡΠΈΡΠΌΠ° Π·Π°ΡΠ²ΠΎΠΊ
ugmk.com
ΠΠ»ΡΠΌΠΈΠ½ΠΈΠ΅Π²ΠΎ-ΡΠΈΠ½ΠΊΠΎΠ²ΡΠΉ ΡΠΏΠ»Π°Π² — ΠΠΎΠ»ΡΡΠ°Ρ ΠΠ½ΡΠΈΠΊΠ»ΠΎΠΏΠ΅Π΄ΠΈΡ ΠΠ΅ΡΡΠΈ ΠΈ ΠΠ°Π·Π°, ΡΡΠ°ΡΡΡ, ΡΡΡΠ°Π½ΠΈΡΠ° 1
ΠΠ»ΡΠΌΠΈΠ½ΠΈΠ΅Π²ΠΎ-ΡΠΈΠ½ΠΊΠΎΠ²ΡΠΉ ΡΠΏΠ»Π°Π²
CΡΡΠ°Π½ΠΈΡΠ° 1
ΠΠ»ΡΠΌΠΈΠ½ΠΈΠ΅Π²ΠΎ-ΡΠΈΠ½ΠΊΠΎΠ²ΡΠΉ ΡΠΏΠ»Π°Π² ΠΈΠΌΠ΅Π΅Ρ Ρ ΠΎΡΠΎΡΠΈΠ΅ Π»ΠΈΡΠ΅ΠΉΠ½ΡΠ΅ ΡΠ²ΠΎΠΉΡΡΠ²Π°, Ρ ΠΎΡΠΎΡΠ΅Π΅ ΡΠΎΠΏΡΠΎΡΠΈΠ²Π»Π΅Π½ΠΈΠ΅ ΠΈΡΡΠΈΡΠ°Π½ΠΈΡ, Π»Π΅Π³ΠΊΠΎ ΠΎΠ±ΡΠ°Π±Π°ΡΡΠ²Π°Π΅ΡΡΡ ΠΈ ΠΈΠΌΠ΅Π΅Ρ ΠΏΡΠΈ ΠΏΠ΅ΡΠ΅ΠΏΠ»Π°Π²ΠΊΠ΅ Π½Π΅Π±ΠΎΠ»ΡΡΠΈΠ΅ ΠΏΠΎΡΠ΅ΡΠΈ. ΠΠ΅Π±ΠΎΠ»ΡΡΠ°Ρ ΡΠ΅ΡΠΎΡ ΠΎΠ²Π°ΡΠΎΡΡΡ Π½Π° ΠΏΠΎΠ²Π΅ΡΡ Π½ΠΎΡΡΠΈ ΡΡΠ°ΠΌΠΏΠ° Π½Π΅ ΠΎΡΡΠ°ΠΆΠ°Π΅ΡΡΡ Π½Π° ΠΊΠ°ΡΠ΅ΡΡΠ²Π΅ ΠΏΠΎΠ²Π΅ΡΡ Π½ΠΎΡΡΠΈ ΠΎΡΡΡΠ°ΠΌΠΏΠΎΠ²Π°Π½Π½ΡΡ Π΄Π΅ΡΠ°Π»Π΅ΠΉ, ΡΡΠΎ ΠΎΡΠΎΠ±Π΅Π½Π½ΠΎ ΡΠ΅Π½Π½ΠΎ ΠΏΡΠΈ ΡΡΠ°ΠΌΠΏΠΎΠ²ΠΊΠ΅ ΠΎΠ±Π»ΠΈΡΠΎΠ²ΠΎΡΠ½ΡΡ Π΄Π΅ΡΠ°Π»Π΅ΠΉ Π°Π²ΡΠΎΠΌΠΎΠ±ΠΈΠ»Π΅ΠΉ ΠΈ ΡΠ°ΠΌΠΎΠ»Π΅ΡΠΎΠ². β[1]
ΠΠΎΠ½ΡΡΡΡΠΊΡΠΈΡ Π²ΡΡΡΠΆΠ½ΠΎΠ³ΠΎ ΡΡΠ°ΠΌΠΏΠ° ΠΈΠ· Π°Π»ΡΠΌΠΈΠ½ΠΈΠ΅Π²ΠΎ-ΡΠΈΠ½ΠΊΠΎΠ²ΠΎΠ³ΠΎ ΡΠΏΠ»Π°Π²Π° Π° ΠΏΡΠ΅ΡΡΠ΅ Π΄Π²ΠΎΠΉΠ½ΠΎΠ³ΠΎ Π΄Π΅ΠΉΡΡΠ²ΠΈΡ Π°Π½Π°Π»ΠΎΠ³ΠΈΡΠ½Π° ΠΊΠΎΠ½ΡΡΡΡΠΊΡΠΈΠΈ ΡΡΠ³ΡΠ½Π½ΠΎΠ³ΠΎ ΡΡΠ°ΠΌΠΏΠ°, Π·Π° ΠΈΡΠΊΠ»ΡΡΠ΅Π½ΠΈΠ΅ΠΌ Π½Π°ΠΏΡΠ°Π²Π»ΡΡΡΠ΅Π³ΠΎ ΡΡΡΡΠΎΠΉΡΡΠ²Π° ΠΏΡΠ°Π½ΡΠΎΠ½Π°. Π ΡΡΠ³ΡΠ½Π½ΡΡ ΡΡΠ°ΠΌΠΏΠ°Ρ Π½Π°ΠΏΡΠ°Π²Π»Π΅Π½ΠΈΠ΅ ΠΏΡΠ°Π½ΡΠΎΠ½Ρ ΠΎΠ±Π΅ΡΠΏΠ΅ΡΠΈΠ²Π°Π΅ΡΡΡ Π·Π°ΠΊΠ°Π»Π΅Π½Π½ΡΠΌΠΈ ΠΏΠ»Π°Π½ΠΊΠ°ΠΌΠΈ, ΡΠΊΡΠ΅ΠΏΠ»Π΅Π½Π½ΡΠΌΠΈ Π½Π° ΡΠ°ΠΌΠΎΠΌ ΠΏΡΠ°Π½ΡΠΎΠ½Π΅ ΠΈ Π½Π° ΡΡΠ΅Π½ΠΊΠ°Ρ ΠΏΡΠΈΠΆΠΈΠΌΠ°; Π² Π°Π»ΡΠΌΠΈΠ½ΠΈΠ΅Π²ΠΎ-ΡΠΈΠ½ΠΊΠΎΠ²ΡΡ ΡΡΠ°ΠΌΠΏΠ°Ρ ΡΠ°ΠΊΠΈΠ΅ ΠΏΠ»Π°Π½ΠΊΠΈ Π° ΠΏΡΠ°Π½ΡΠΎΠ½Π΅ ΠΈ Π° ΠΏΡΠΈΠΆΠΈΠΌΠ΅ ΠΎΡΡΡΡΡΡΠ²ΡΡΡ. ΠΠ»ΠΈΡΡ ΠΏΡΠ°Π½ΡΠΎΠ½Π° ΠΈ ΠΌΠ°ΡΡΠΈΡΡ ΠΎΡΠ»ΠΈΠ²Π°ΡΡ ΠΈΠ· ΡΡΠ³ΡΠ½Π°, ΡΠ°ΠΊ ΠΊΠ°ΠΊ ΠΎΠ±ΡΠ°Π±ΠΎΡΠΊΠ° ΠΈΡ Π½Π΅ Π²ΡΠ·ΡΠ²Π°Π΅Ρ Π·Π°ΡΡΡΠ΄Π½Π΅Π½ΠΈΠΉ ΠΈ Π½Π΅ ΡΠ²Π»ΡΠ΅ΡΡΡ ΡΡΡΠ΄ΠΎΠ΅ΠΌΠΊΠΎΠΉ ΠΎΠΏΠ΅ΡΠ°ΡΠΈΠ΅ΠΉ. β[2]
Π‘ΡΠΎΠΉΠΊΠΎΡΡΡ ΡΡΠ°ΠΌΠΏΠΎΠ², ΠΎΡΠ»ΠΈΡΡΡ ΠΈΠ· Π°Π»ΡΠΌΠΈΠ½ΠΈΠ΅Π²ΠΎ-ΡΠΈΠ½ΠΊΠΎΠ²ΠΎΠ³ΠΎ ΡΠΏΠ»Π°Π²Π°
, Π²ΠΏΠΎΠ»Π½Π΅ ΡΠ΄ΠΎΠ²Π»Π΅ΡΠ²ΠΎΡΠΈΡΠ΅Π»ΡΠ½Π°Ρ ( ΠΏΡΠΈΠΌΠ΅ΡΠ½ΠΎ 5000 — 6000 ΡΡ. ΠΡΠ»Π΅Π΄ΡΡΠ²ΠΈΠ΅ Π½Π΅Π²ΡΡΠΎΠΊΠΎΠΉ ΡΠ²Π΅ΡΠ΄ΠΎΡΡΠΈ ΡΡΠ°ΠΌΠΏΠΎΠ² ΡΠ°ΡΠ°ΠΏΠΈΠ½Ρ Π½Π° ΠΏΠΎΠ²Π΅ΡΡ Π½ΠΎΡΡΡΡ ΠΎΡΡΡΠ°ΠΌΠΏΠΎΠ²Π°Π½Π½ΡΡ Π΄Π΅ΡΠ°Π»Π΅ΠΉ Π½Π΅ ΠΏΠΎΡΠ²Π»ΡΡΡΡΡ Π΄Π°ΠΆΠ΅ ΠΈ Π² ΡΠ΅Ρ ΡΠ»ΡΡΠ°ΡΡ , ΠΊΠΎΠ³Π΄Π° ΡΡΡΡΠΈΠ΅ΡΡ ΠΏΠΎΠ²Π΅ΡΡ Π½ΠΎΡΡΠΈ ΡΡΠ°ΠΌΠΏΠΎΠ² ΠΎΠ±ΡΠ°Π±ΠΎΡΠ°Π½Ρ Π½Π΅Π΄ΠΎΡΡΠ°ΡΠΎΡΠ½ΠΎ ΡΡΠ°ΡΠ΅Π»ΡΠ½ΠΎ. ΠΡΠΎ ΠΎΠ±ΡΡΠΎΡΡΠ΅Π»ΡΡΡΠ²ΠΎ ΠΎΡΠΎΠ±Π΅Π½Π½ΠΎ ΡΠ΅Π½Π½ΠΎ ΠΏΡΠΈ ΡΡΠ°ΠΌΠΏΠΎΠ²ΠΊΠ΅ ΠΎΠ±Π»ΠΈΡΠΎΠ²ΠΎΡΠ½ΡΡ Π΄Π΅ΡΠ°Π»Π΅ΠΉ Π°Π²ΡΠΎΠΌΠΎΠ±ΠΈΠ»Π΅ΠΉ. β[3]ΠΡΠΈ ΠΈΠ·Π³ΠΎΡΠΎΠ²Π»Π΅Π½ΠΈΠΈ ΠΌΠ΅Π»ΠΊΠΈΡ ΡΠ΅ΡΠΈΠΉ Π΄Π΅ΡΠ°Π»Π΅ΠΉ Π²ΠΎΠ·ΠΌΠΎΠΆΠ½ΠΎ ΠΈΡΠΏΠΎΠ»ΡΠ·ΠΎΠ²Π°Π½ΠΈΠ΅ ΠΌΠ°ΡΡΠΈΡ ΠΈΠ· Π°Π»ΡΠΌΠΈΠ½ΠΈΠ΅Π²ΠΎ-ΡΠΈΠ½ΠΊΠΎΠ²ΡΡ ΡΠΏΠ»Π°Π²ΠΎΠ² ( Π½Π°ΠΏΡΠΈΠΌΠ΅Ρ, ΠΠ¦-13) ΠΈ Π½Π΅ΠΊΠΎΡΠΎΡΡΡ Π»Π΅Π³ΠΊΠΎΠΏΠ»Π°Π²ΠΊΠΈΡ ΡΠΏΠ»Π°Π²ΠΎΠ² [62], ΡΠ°ΠΊ ΠΊΠ°ΠΊ ΠΈΡ ΡΡΠΎΠΉΠΊΠΎΡΡΡ ΠΏΠΎ ΡΡΠ°Π²Π½Π΅Π½ΠΈΡ ΡΠΎ ΡΡΠ°ΠΌΠΏΠΎΠ²ΠΊΠΎΠΉ Π½Π° ΠΏΠ°Π΄Π°ΡΡΠΈΡ ΠΌΠΎΠ»ΠΎΡΠ°Ρ ΡΡΡΠ΅ΡΡΠ²Π΅Π½Π½ΠΎ ΠΏΠΎΠ²ΡΡΠ°Π΅ΡΡΡ ΠΈΠ·-Π·Π° ΡΠ°Π²Π½ΠΎΠΌΠ΅ΡΠ½ΠΎΠ³ΠΎ ΠΏΡΠΈΠ»ΠΎΠΆΠ΅Π½ΠΈΡ Π΄Π°Π²Π»Π΅Π½ΠΈΡ ΠΏΠΎ Π²ΡΠ΅ΠΉ ΠΏΠΎΠ²Π΅ΡΡ Π½ΠΎΡΡΠΈ ΡΡΠ°ΠΌΠΏΠ°. β[4]
ΠΡΠ½ΠΎΠ²Π°Π½ΠΈΠ΅ΠΌ ( ΠΊΠ°ΡΠΊΠ°ΡΠΎΠΌ) ΡΡΠ°ΠΌΠΏΠ° Π·Π΄Π΅ΡΡ ΡΠ»ΡΠΆΠΈΡ ΠΊΠΎΠ½ΡΡΡΡΠΊΡΠΈΡ ΠΈΠ· Π°Π»ΡΠΌΠΈΠ½ΠΈΠ΅Π²ΠΎ-ΡΠΈΠ½ΠΊΠΎΠ²ΠΎΠ³ΠΎ ΡΠΏΠ»Π°Π²Π°; ΠΏΠΎΠ²Π΅ΡΡ Π½ΠΎΡΡΡ Π΅Π΅ Π·Π°Π»ΠΈΠ²Π°Π΅ΡΡΡ ΡΠ΅ΡΠΌΠΎΡΡΡΠΎΠΉΡΠΈΠ²ΠΎΠΉ, Π½Π΅ Π΄Π°ΡΡΠ΅ΠΉ ΡΡΠ°Π΄ΠΊΠΈ, ΡΠ΅Π½ΠΎΠ»ΠΎΠ²ΠΎΠΉ ΡΠΌΠΎΠ»ΠΎΠΉ. β[5]
ΠΠ°Π³Π½ΠΈΡΠΎΠΏΡΠΎΠ²ΠΎΠ΄ ΡΠΎΡΡΠΎΠΈΡ ΠΈΠ· Π¨ — ΠΎΠ±ΡΠ°Π·Π½ΠΎΠ³ΠΎ ΡΠ΅ΡΠ΄Π΅ΡΠ½ΠΈΠΊΠ° ΠΈ Π·Π°ΠΌΡΠΊΠ°ΡΡΠ΅Π³ΠΎ ΡΡΠΌΠ°, Π·Π°Π»ΠΈΡΡΡ Ρ ΠΎΠ΄Π½ΠΎΠΉ ΡΡΠΎΡΠΎΠ½Ρ Π°Π»ΡΠΌΠΈΠ½ΠΈΠ΅Π²ΠΎ-ΡΠΈΠ½ΠΊΠΎΠ²ΡΠΌ ΡΠΏΠ»Π°Π²ΠΎΠΌ, Π² ΠΊΠΎΡΠΎΡΡΠΉ Π·Π°Π»ΠΎΠΆΠ΅Π½Ρ ΠΎΡ Π»Π°ΠΆΠ΄Π°ΡΡΠΈΠ΅ ΡΡΡΠ±ΠΊΠΈ. ΠΠ΅ΡΠ²ΠΈΡΠ½Π°Ρ ΠΎΠ±ΠΌΠΎΡΠΊΠ° Π²ΡΠΏΠΎΠ»Π½Π΅Π½Π° Π² Π²ΠΈΠ΄Π΅ ΡΠ΅ΠΊΡΠΈΠΉ ( Π³Π°Π»Π΅Ρ) ΠΈΠ· 6 Π²ΠΈΡΠΊΠΎΠ² ΠΏΠΎΠ»ΠΎΠ³ΠΎ ΠΌΠ΅Π΄Π½ΠΎΠ³ΠΎ ΠΏΡΠΎΠ²ΠΎΠ΄Π½ΠΈΠΊΠ° Ρ ΡΠ΅ΡΠΌΠΎΡΡΠΎΠΉΠΊΠΎΠΉ ΠΈΠ·ΠΎΠ»ΡΡΠΈΠ΅ΠΉ. ΠΠ°Π»ΠΈΠ²ΠΊΠ° ΠΎΠ±ΡΠ°Π·ΡΠ΅Ρ Π½Π΅Π·Π°ΠΌΠΊΠ½ΡΡΡΠΉ Π²ΠΈΡΠΎΠΊ, ΡΠ»ΡΠΆΠ°ΡΠΈΠΉ Π²ΡΠΎΡΠΈΡΠ½ΠΎΠΉ ΠΎΠ±ΠΌΠΎΡΠΊΠΎΠΉ. β[8]
ΠΠ»ΡΠΌΠΈΠ½ΠΈΠ΅Π²ΠΎ-ΡΠΈΠ½ΠΊΠΎΠ²ΡΠΉ ΡΠΏΠ»Π°Π², ΠΏΡΠΈΠΌΠ΅Π½ΡΠ΅ΠΌΡΠΉ Π΄Π»Ρ Π²ΡΡΡΠΆΠ½ΡΡ ΠΈ ΡΠΎΡΠΌΠΎΠ²ΠΎΡΠ½ΡΡ ΡΡΠ°ΠΌΠΏΠΎΠ² Π² Π°Π²ΡΠΎΠΌΠΎΠ±ΠΈΠ»ΡΠ½ΠΎΠΉ ΠΈ Π°Π²ΠΈΠ°ΡΠΈΠΎΠ½Π½ΠΎΠΉ ΠΏΡΠΎΠΌΡΡΠ»Π΅Π½Π½ΠΎΡΡΠΈ, ΡΠΎΠ΄Π΅ΡΠΆΠΈΡ. β[9]
ΠΠ° ΡΡΠ±Π΅ΠΆΠΎΠΌ ( Π² Π‘Π¨Π) Π΄Π»Ρ ΡΡΠΎΠΉ ΡΠ΅Π»ΠΈ ΠΏΡΠΈΠΌΠ΅Π½ΡΠ΅ΡΡΡ ΡΠΏΠ»Π°Π² ΠΊΠΈΡΠΊΡΠ°ΠΉΡ Π ΠΈ Π, ΡΠΎΡΡΠΎΡΡΠΈΠΉ ΠΈΠ· 3 5 — 4 5 % Π1, 2 5 — 3 7 % Π‘ΠΈ, 1 25 % Mg; ae 22 — — Ρ — 28 ΠΊΠ / Π»Ρ2 ( 220 — 280 ΠΠ½ / ΠΌ2), 8 3 %; ΡΠ΅ΠΌΠΏΠ΅ΡΠ°ΡΡΡΠ° ΠΏΠ»Π°Π²Π»Π΅Π½ΠΈΡ 365 — 390 Π‘. ΠΠ»ΡΠΌΠΈΠ½ΠΈΠ΅Π²ΠΎ-ΡΠΈΠ½ΠΊΠΎΠ²ΡΠΉ ΡΠΏΠ»Π°Π² ΠΈΠΌΠ΅Π΅Ρ Ρ ΠΎΡΠΎΡΠΈΠ΅ Π»ΠΈΡΠ΅ΠΉΠ½ΡΠ΅ ΠΊΠ°ΡΠ΅ΡΡΠ²Π°, Ρ ΠΎΡΠΎΡΠ΅Π΅ ΡΠΎΠΏΡΠΎΡΠΈΠ²Π»Π΅Π½ΠΈΠ΅ ΠΈΡΡΠΈΡΠ°Π½ΠΈΡ, Π»Π΅Π³ΠΊΠΎ ΠΎΠ±ΡΠ°Π±Π°ΡΡΠ²Π°Π΅ΡΡΡ ΠΈ ΠΈΠΌΠ΅Π΅Ρ ΠΏΡΠΈ ΠΏΠ΅ΡΠ΅ΠΏΠ»Π°Π²ΠΊΠ΅ Π½Π΅Π±ΠΎΠ»ΡΡΠΈΠ΅ ΠΏΠΎΡΠ΅ΡΠΈ. Π ΡΡΠΈΡ ΡΡΠ°ΠΌΠΏΠ°Ρ Π²Π΅ΡΡ Π½ΠΈΠ΅ ΠΈ Π½ΠΈΠΆΠ½ΠΈΠ΅ ΠΏΠ»ΠΈΡΡ ΠΎΡΠ»ΠΈΠ²Π°ΡΡ ΠΈΠ· ΡΡΠ³ΡΠ½Π°, Π° ΡΠ°Π±ΠΎΡΠΈΠ΅ ΡΠ°ΡΡΠΈ ( ΠΏΡΠ°Π½ΡΠΎΠ½ ΠΈ ΠΌΠ°ΡΡΠΈΡΡ) ΠΈΠ· ΠΏΡΠΈΠ²Π΅Π΄Π΅Π½Π½ΡΡ Π²ΡΡΠ΅ ΡΠΏΠ»Π°Π²ΠΎΠ². Π‘ΡΠΎΠΉΠΊΠΎΡΡΡ ΠΈΡ ΡΠΎΡΡΠ°Π²Π»ΡΠ΅Ρ 5000 — 6000 ΡΡ. β[10]
ΠΠ΅Π½Π΅Π΅ ΡΠ»ΠΎΠΆΠ½Π΅ΠΉ ΠΠ΅ΡΠ°Π»Ρ ΠΏΠΎΠ»ΡΡΠ°Π΅ΡΡΡ ΠΎΠ±ΡΡΠΆΠΊΠΎΠΉ Π³Π»Π°Π²Π½ΡΠΌ ΠΎΠ±ΡΠ°Π·ΠΎΠΌ Π·Π° ΡΡΠ΅Ρ ΠΏΡΠΎΠ΄ΠΎΠ»ΡΠ½ΠΎΠ³ΠΎ ΡΠ°ΡΡΡΠΆΠ΅Π½ΠΈΡ ΠΌΠ°ΡΠ΅ΡΠΈΠ°Π»Π°. ΠΠΎΠ»Π²Π°Π½Ρ, ΠΏΡΠΈΠΌΠ΅Π½ΡΠ΅ΠΌΡΠ΅ Π΄Π»Ρ ΠΎΠ±ΡΡΠΆΠΊΠΈ Π΄Π΅ΡΠ°Π»Π΅ΠΉ ΠΈΠ· ΠΏΠ»ΠΎΡΠΊΠΈΡ Π·Π°Π³ΠΎΡΠΎΠ²ΠΎΠΊ, ΠΈΠ·Π³ΠΎΡΠΎΠ²Π»ΡΡΡΡΡ ΠΈΠ· Π°Π»ΡΠΌΠΈΠ½ΠΈΠ΅Π²ΠΎ-ΡΠΈΠ½ΠΊΠΎΠ²ΡΡ ΡΠΏΠ»Π°Π²ΠΎΠ², Π° ΡΠ°ΠΊΠΆΠ΅ ΠΈ ΠΈΠ· ΡΠ±ΠΎΡΠ½ΡΡ Π΄Π΅ΡΠ΅Π²ΡΠ½Π½ΡΡ Π±ΡΡΡΠΊΠΎΠ² ΡΠ²Π΅ΡΠ΄ΠΎΠΉ ΠΏΠΎΡΠΎΠ΄Ρ; Π½Π°ΠΏΡΠ°Π²Π»Π΅Π½ΠΈΠ΅ Π²ΠΎΠ»ΠΎΠΊΠΎΠ½ Π΄ΡΠ΅Π²Π΅ΡΠΈΠ½Ρ Π΄ΠΎΠ»ΠΆΠ½ΠΎ Π±ΡΡΡ Π²Π΅ΡΡΠΈΠΊΠ°Π»ΡΠ½ΡΠΌ. ΠΠ»Ρ ΡΠ²Π΅Π»ΠΈΡΠ΅Π½ΠΈΡ ΡΡΠΎΠΉΠΊΠΎΡΡΠΈ Π΄Π΅ΡΠ΅Π²ΡΠ½Π½ΡΡ Π±ΠΎΠ»Π²Π°Π½ΠΎΠ² ΠΈΠ½ΠΎΠ³Π΄Π° ΠΏΠΎΠ²Π΅ΡΡ Π½ΠΈΡ Π½Π°ΠΊΠ»Π°Π΄ΡΠ²Π°ΡΡ ΠΌΠ΅ΡΠ°Π»Π»ΠΈΡΠ΅ΡΠΊΠΈΠΉ Π»ΠΈΡΡ, ΡΠΎΠΎΡΠ²Π΅ΡΡΡΠ²ΡΡΡΠΈΠΉ Π²Π½ΡΡΡΠ΅Π½Π½Π΅ΠΌΡ ΠΏΡΠΎΡΠΈΠ»Ρ Π³ΠΎΡΠΎΠ²ΠΎΠΉ Π΄Π΅ΡΠ°Π»ΠΈ. β[11]
ΠΡΠΈ ΠΈΡΠΏΠΎΠ»ΡΠ·ΠΎΠ²Π°Π½ΠΈΠΈ ΠΊΠ°Π½Π°ΡΠΎΠ² Π² ΠΊΠ°ΡΠ΅ΡΡΠ²Π΅ ΠΈΠ½Π²Π΅Π½ΡΠ°ΡΠ½ΡΡ ΡΠ»Π΅ΠΌΠ΅Π½ΡΠΎΠ² ΠΈΡ ΠΊΡΠ΅ΠΏΡΡ ΠΌΡΡΡΠ°ΠΌΠΈ ( ΡΡΠ°ΠΊΠ°Π½Π°ΠΌΠΈ), Π² ΠΊΠΎΡΠΎΡΡΡ Π·Π°Π΄Π΅Π»ΡΠ²Π°ΡΡ ΠΊΠΎΠ½ΡΡ ΠΊΠ°Π½Π°ΡΠ°. ΠΠ° ΠΊΠΎΠ½Π΅Ρ ΠΊΠ°Π½Π°ΡΠ° Π½Π°Π΄Π΅Π²Π°ΡΡ ΠΌΡΡΡΡ ( ΡΠΈΡ. 5), Π·Π°ΡΠ΅ΠΌ ΠΊΠΎΠ½Π΅Ρ ΡΠ°ΡΠΏΠ»Π΅ΡΠ°ΡΡ. ΠΠ°Π³ΠΈΠ±Π°ΡΡ ΠΎΡΠ΄Π΅Π»ΡΠ½ΡΠ΅ ΠΏΡΠΎΠ²ΠΎΠ»ΠΎΠΊΠΈ ΠΈ ΡΠ°ΡΠΏΠ»Π΅ΡΠ΅Π½Π½ΡΠΉ ΠΊΠΎΠ½Π΅Ρ ΠΊΠ°Π½Π°ΡΠ° Π·Π°Π»ΠΈΠ²Π°ΡΡ Π² ΡΡΠ°ΠΊΠ°Π½Π΅ ΠΌΡΡΡΡ ΡΠ°ΡΠΏΠ»Π°Π²Π»Π΅Π½Π½ΡΠΌ Π±Π°Π±Π±ΠΈΡΠΎΠΌ ΠΈΠ»ΠΈ ΡΠΏΠ΅ΡΠΈΠ°Π»ΡΠ½ΡΠΌ Π°Π»ΡΠΌΠΈΠ½ΠΈΠ΅Π²ΠΎ-ΡΠΈΠ½ΠΊΠΎΠ²ΡΠΌ ΡΠΏΠ»Π°Π²ΠΎΠΌ. β[12]
ΠΠ½ ΠΈΠΌΠ΅Π΅Ρ ΠΌΠ°Π³Π½ΠΈΡΠΎΠΏΡΠΎΠ²ΠΎΠ΄ Π±ΡΠΎΠ½Π΅Π²ΠΎΠ³ΠΎ ΡΠΈΠΏΠ° ΠΈΠ· ΡΡΠ°Π»ΠΈ Π44 ΡΠΎΠ»ΡΠΈΠ½ΠΎΠΉ 0 2 ΠΌΠΌ. Π‘ΠΎΡΡΠΎΠΈΡ ΠΈΠ· Π’ — ΠΎΠ±ΡΠ°Π·Π½ΠΎΠ³ΠΎ ΡΠ΅ΡΠ΄Π΅ΡΠ½ΠΈΠΊΠ° ΠΈ Π·Π°ΠΌΡΠΊΠ°ΡΡΠ΅Π³ΠΎ Π — ΠΎΠ±ΡΠ°Π·Π½ΠΎΠ³ΠΎ ΡΡΠΌΠ°. ΠΠ°Π³Π½ΠΈΡΠΎΠΏΡΠΎΠ²ΠΎΠ΄ Π·Π°Π»ΠΈΡ Π°Π»ΡΠΌΠΈΠ½ΠΈΠ΅Π²ΠΎ-ΡΠΈΠ½ΠΊΠΎΠ²ΡΠΌ ΡΠΏΠ»Π°Π²ΠΎΠΌ, Π² ΠΊΠΎΡΠΎΡΡΠΉ Π·Π°Π»ΠΎΠΆΠ΅Π½Ρ ΡΡΡΠ±ΠΊΠΈ ΠΎΡ Π»Π°ΠΆΠ΄Π΅Π½ΠΈΡ. Π’ΡΡΠ±ΠΊΠΈ ΠΈΠΌΠ΅ΡΡ ΡΠ°Π·ΠΌΠ΅Ρ 8Ρ X, 12 ΠΌΠΌ, ΡΡΠΎ Π·Π½Π°ΡΠΈΡΠ΅Π»ΡΠ½ΠΎ ΠΎΠ±Π»Π΅Π³ΡΠ°Π΅Ρ ΡΠΊΡΠΏΠ»ΡΠ°ΡΠ°ΡΠΈΡ. ΠΠ΅ΡΠ²ΠΈΡΠ½Π°Ρ ΠΎΠ±ΠΌΠΎΡΠΊΠ° ΠΌΠ½ΠΎΠ³ΠΎΠ²ΠΈΡΠΊΠΎΠ²Π°Ρ, Π΄ΠΈΡΠΊΠΎΠ²Π°Ρ. ΠΠ΅ Π²ΠΈΡΠΊΠΈ Π²ΡΠΏΠΎΠ»Π½Π΅Π½Ρ ΠΈΠ· ΡΡΡΠ±ΠΊΠΈ, ΠΈΠ·ΠΎΠ»ΠΈΡΠΎΠ²Π°Π½Π½ΠΎΠΉ ΡΠ΅ΡΠΌΠΎΡΡΠΎΠΉΠΊΠΎΠΉ ΠΈΠ·ΠΎΠ»ΡΡΠΈΠ΅ΠΉ. ΠΠ°ΠΆΠ΄Π°Ρ ΡΠ΅ΠΊΡΠΈΡ-Π·Π°Π»ΠΈΡΠ° Π°Π»ΡΠΌΠΈΠ½ΠΈΠ΅ΠΌ; Π·Π°Π»ΠΈΠ²ΠΊΠ° ΠΎΠ±ΡΠ°Π·ΡΠ΅Ρ ΠΎΠ΄ΠΈΠ½ Π½Π΅Π·Π°ΠΌΠΊΠ½ΡΡΡΠΉ Π²ΡΠΎΡΠΈΡΠ½ΡΠΉ Π²ΠΈΡΠΎΠΊ ΠΎΠ²Π°Π»ΡΠ½ΠΎΠΉ ΡΠΎΡΠΌΡ. ΠΠ»Ρ ΠΎΡΠ²ΠΎΠ΄Π° ΡΠ΅ΠΏΠ»Π° ΠΎΡ Π²ΡΠΎΡΠΈΡΠ½ΠΎΠΉ ΠΎΠ±ΠΌΠΎΡΠΊΠΈ Π² Π°Π»ΡΠΌΠΈΠ½ΠΈΠΉ Π·Π°Π»ΠΎΠΆΠ΅Π½Ρ ΡΡΡΠ±ΠΊΠΈ ΠΎΡ Π»Π°ΠΆΠ΄Π΅Π½ΠΈΡ ΠΈΠ· Π½Π΅ΡΠΆΠ°Π²Π΅ΡΡΠ΅ΠΉ ΡΡΠ°Π»ΠΈ. ΠΡΠ²ΠΎΠ΄Ρ ΠΏΠ΅ΡΠ²ΠΈΡΠ½ΠΎΠΉ ΠΎΠ±ΠΌΠΎΡΠΊΠΈ Π·Π°Π»ΠΈΡΡ ΡΠΏΠΎΠΊΡΠΈΠ΄Π½ΡΠΌ ΠΊΠΎΠΌΠΏΠ°ΡΠ½Π΄ΠΎΠΌ. ΠΠ·ΠΌΠ΅Π½Π΅Π½ΠΈΠ΅ & ΡΠΏΡΠΎΠΈΠ·Π²ΠΎΠ΄ΠΈΡΡΡ ΠΏΠ΅ΡΠ΅ΠΊΠ»ΡΡΠ΅Π½ΠΈΠ΅ΠΌ ΡΠΈΡΠ»Π° Π²ΠΈΡΠΊΠΎΠ² ΠΏΠ΅ΡΠ²ΠΈΡΠ½ΠΎΠΉ ΠΎΠ±ΠΌΠΎΡΠΊΠΈ ΠΈ ΠΏΠ°ΡΠ°Π»Π»Π΅Π»ΡΠ½ΠΎ-ΠΏΠΎΡΠ»Π΅Π΄ΠΎΠ²Π°ΡΠ΅Π»ΡΠ½ΡΠΌ Π²ΠΊΠ»ΡΡΠ΅Π½ΠΈΠ΅ΠΌ Π³Π°Π»Π΅Ρ Π½Π° Π²ΡΠΎΡΠΈΡΠ½ΠΎΠΉ ΡΡΠΎΡΠΎΠ½Π΅. β[14]
Π’Π²Π΅ΡΠ΄ΡΠ΅ ΠΏΡΠΈΠΏΠΎΠΈ ΠΌΠΎΠ³ΡΡ Π±ΡΡΡ ΠΈΠ·Π³ΠΎΡΠΎΠ²Π»Π΅Π½Ρ Π² Π²ΠΈΠ΄Π΅ ΠΏΡΡΡΠΊΠΎΠ², ΡΠΎΠ½ΠΊΠΈΡ Π»ΠΈΡΡΠΎΠ² ΠΈ Π³ΡΠ°Π½ΡΠ». ΠΡΠ»ΠΈ ΠΏΠΎΠ·Π²ΠΎΠ»ΡΠ΅Ρ ΠΌΠ΅ΡΠΎΠ΄ Π½Π°Π³ΡΠ΅Π²Π° Π΄Π΅ΡΠ°Π»ΠΈ ΠΏΡΠΈ ΠΏΠ°ΡΠ½ΠΈΠΈ ΠΈ Ρ Π°ΡΠ°ΠΊΡΠ΅Ρ ΡΠΎΠ΅Π΄ΠΈΠ½Π΅Π½ΠΈΡ, ΠΏΡΠΈΠΌΠ΅Π½ΡΡΡΡΡ ΠΊΠΎΠ»ΡΡΠ° ΠΈΠ»ΠΈ ΠΏΡΠΎΠΊΠ»Π°Π΄ΠΊΠ° ΠΈΠ· ΠΌΠ°ΡΠ΅ΡΠΈΠ°Π»Π° ΠΏΡΠΈΠΏΠΎΡ. ΠΡΠΎ ΠΎΠ±Π΅ΡΠΏΠ΅ΡΠΈΠ²Π°Π΅Ρ Π±ΠΎΠ»Π΅Π΅ ΡΠ°Π²Π½ΠΎΠΌΠ΅ΡΠ½ΠΎΠ΅ ΡΠ°ΡΠΏΡΠ΅Π΄Π΅Π»Π΅Π½ΠΈΠ΅ ΠΏΡΠΈΠΏΠΎΡ ΠΈ Π±ΠΎΠ»Π΅Π΅ ΡΠΊΠΎΠ½ΠΎΠΌΠΈΡΠ½ΠΎΠ΅ ΠΈΡΠΏΠΎΠ»ΡΠ·ΠΎΠ²Π°Π½ΠΈΠ΅ Π΅Π³ΠΎ. Π Π°Π·ΠΌΠ΅ΡΡ ΠΏΡΠΎΠ²ΠΎΠ»ΠΎΠΊΠΈ Π² Π·Π°Π²ΠΈΡΠΈΠΌΠΎΡΡΠΈ ΠΎΡ ΠΏΠ»ΠΎΡΠ°Π΄ΠΈ ΡΠΎΠ΅Π΄ΠΈΠ½Π΅Π½ΠΈΡ Π±Π΅ΡΡΡΡΡ ΠΎΠ±ΡΡΠ½ΠΎ ΠΎΡ 0 4 Π΄ΠΎ 1 5 ΠΌΠΌ, ΡΠΎΠ»ΡΠ³Π° Π΄Π΅Π»Π°Π΅ΡΡΡ ΡΠΎΠ»ΡΠΈΠ½ΠΎΠΉ 0 05 — 0 1 ΠΌΠΌ. ΠΠ»Ρ ΠΏΠ°ΠΉΠΊΠΈ Π°Π»ΡΠΌΠΈΠ½ΠΈΡ, ΠΊΠΎΡΠΎΡΠ°Ρ ΠΎΠ±ΡΡΠ½ΠΎ Π·Π°ΡΡΡΠ΄Π½Π΅Π½Π° ΠΈΠ· — Π·Π° ΠΏΡΠΎΡΠ½ΠΎΠΉ ΠΎΠΊΠΈΡΠ½ΠΎΠΉ ΠΏΠ»Π΅Π½ΠΊΠΈ, ΠΏΡΠΈΠΌΠ΅Π½ΡΡΡ Π°Π»ΡΠΌΠΈΠ½ΠΈΠ΅Π²ΠΎ-ΡΠΈΠ½ΠΊΠΎΠ²ΡΠ΅ ΡΠΏΠ»Π°Π²Ρ. ΠΠ°ΠΉΠΊΠ° ΠΏΡΠΎΠΈΠ·Π²ΠΎΠ΄ΠΈΡΡΡ ΡΠΏΠ΅ΡΠΈΠ°Π»ΡΠ½ΡΠΌΠΈ ΡΠ»ΡΡΡΠ°Π·Π²ΡΠΊΠΎΠ²ΡΠΌΠΈ ΠΏΠ°ΡΠ»ΡΠ½ΠΈΠΊΠ°ΠΌΠΈ. Π£Π»ΡΡΡΠ°Π·Π²ΡΠΊΠΎΠ²ΡΠ΅ ΠΊΠΎΠ»Π΅Π±Π°Π½ΠΈΡ Π»Π΅Π³ΠΊΠΎ ΡΠ°Π·ΡΡΡΠ°ΡΡ ΠΠΊΠΈΡΠ½ΡΡ ΠΏΠ»Π΅Π½ΠΊΡ. β[15]
Π‘ΡΡΠ°Π½ΠΈΡΡ: β βββ1 βββ2
www.ngpedia.ru
ΠΠ°ΠΊ ΠΎΡΠ»ΠΈΡΠΈΡΡ ΡΠΈΠ½ΠΊ ΠΎΡ Π°Π»ΡΠΌΠΈΠ½ΠΈΡ
ΠΡΠ»ΠΈΡΠΈΡΡ Π°Π»ΡΠΌΠΈΠ½ΠΈΠΉ ΠΎΡ Π΄ΡΡΠ³ΠΈΡ ΠΌΠ΅ΡΠ°Π»Π»ΠΎΠ² Π»Π΅Π³ΠΊΠΎ Π±Π»Π°Π³ΠΎΠ΄Π°ΡΡ Π΅Π³ΠΎ Π»Π΅Π³ΠΊΠΎΡΡΠΈ. ΠΠ΅ΡΠ°Π»Π» ΠΎΡΠ½ΠΎΡΠΈΡΡΡ ΠΊ ΡΠΈΡΠΎΠΊΠΎ ΡΠ°ΡΠΏΡΠΎΡΡΡΠ°Π½Π΅Π½Π½ΡΠΌ, Π²ΠΎΡΡΡΠ΅Π±ΠΎΠ²Π°Π½ Π² ΠΏΡΠΎΠΌΡΡΠ»Π΅Π½Π½ΠΎΠΉ ΠΈ ΠΏΠΈΡΠ΅Π²ΠΎΠΉ ΠΏΡΠΎΠΌΡΡΠ»Π΅Π½Π½ΠΎΡΡΠΈ. ΠΡΠ»ΠΈΡΠΈΡΡ ΡΠΈΠ½ΠΊ ΠΎΡ Π°Π»ΡΠΌΠΈΠ½ΠΈΡ ΡΠ°ΠΌΠΎΡΡΠΎΡΡΠ΅Π»ΡΠ½ΠΎ Π½Π΅ ΡΠΎΡΡΠ°Π²ΠΈΡ ΡΡΡΠ΄Π°. ΠΠ»Ρ ΡΡΠΎΠ³ΠΎ Π΄ΠΎΡΡΠ°ΡΠΎΡΠ½ΠΎ Π²Π»Π°Π΄Π΅ΡΡ Π½Π΅ΠΎΠ±Ρ ΠΎΠ΄ΠΈΠΌΡΠΌΠΈ Π·Π½Π°Π½ΠΈΡΠΌΠΈ ΠΈ ΠΌΠ΅ΡΠΎΠ΄ΠΈΠΊΠ°ΠΌΠΈ. ΠΡΠ΅Π΄Π»Π°Π³Π°Π΅ΠΌ ΠΎΠ·Π½Π°ΠΊΠΎΠΌΠΈΡΡΡΡ Ρ Π½ΠΈΠΌΠΈ ΠΏΠΎΠ΄ΡΠΎΠ±Π½Π΅Π΅.
ΠΠ°ΠΊ ΠΎΡΠ»ΠΈΡΠΈΡΡ ΡΠΈΠ½ΠΊ ΠΎΡ Π°Π»ΡΠΌΠΈΠ½ΠΈΡ?
ΠΠ»ΡΡΠ΅ΡΠ½Π°ΡΠΈΠ²Π½ΡΠΌΠΈ Π²Π°ΡΠΈΠ°Π½ΡΠ°ΠΌΠΈ, ΠΏΠΎΠ·Π²ΠΎΠ»ΡΡΡΠΈΠΌΠΈ ΠΎΡΠ²Π΅ΡΠΈΡΡ Π½Π° Π²ΠΎΠΏΡΠΎΡ ΠΊΠ°ΠΊ ΠΎΡΠ»ΠΈΡΠΈΡΡ ΡΠΈΠ½ΠΊ ΠΎΡ Π°Π»ΡΠΌΠΈΠ½ΠΈΡ, Π΄ΠΎΡΡΡΠΏΠ½ΡΠΌΠΈ Π² Π΄ΠΎΠΌΠ°ΡΠ½ΠΈΡ ΡΡΠ»ΠΎΠ²ΠΈΡΡ , ΡΠ²Π»ΡΡΡΡΡ ΡΠ»Π΅Π΄ΡΡΡΠΈΠ΅.
- Π Π°ΡΠΏΠΎΠ·Π½Π°Π²Π°Π½ΠΈΠ΅ ΠΏΠΎ ΡΠΈΠ·ΠΈΠΊΠΎ-Ρ ΠΈΠΌΠΈΡΠ΅ΡΠΊΠΈΠΌ Ρ Π°ΡΠ°ΠΊΡΠ΅ΡΠΈΡΡΠΈΠΊΠ°ΠΌ
ΠΠΈΠ½ΠΈΠΌΠ°Π»ΡΠ½ΡΡ ΡΠΊΠΎΠ»ΡΠ½ΡΡ Π·Π½Π°Π½ΠΈΠΉ Π΄ΠΎΡΡΠ°ΡΠΎΡΠ½ΠΎ Π΄Π»Ρ ΠΎΠΏΡΠ΅Π΄Π΅Π»Π΅Π½ΠΈΡ ΡΠΎΡΡΠ°Π²Π° ΠΈ ΡΠ°Π·Π½ΠΎΠ²ΠΈΠ΄Π½ΠΎΡΡΠΈ ΡΠ»Π΅ΠΌΠ΅Π½ΡΠ°. ΠΠ»ΡΠΌΠΈΠ½ΠΈΠΉ ΠΈΠΌΠ΅Π΅Ρ ΡΠ΅ΡΠ΅Π±ΡΠΈΡΡΡΠΉ ΠΎΡΡΠ΅Π½ΠΎΠΊ, ΠΌΠ°Π»ΡΠΉ Π²Π΅Ρ, Π³ΠΈΠ±ΠΊΠΈΠΉ. Π¦ΠΈΠ½ΠΊ ΠΈΠΌΠ΅Π΅Ρ Π³ΠΎΠ»ΡΠ±ΠΎΠ²Π°ΡΡΠΉ ΠΎΡΡΠ΅Π½ΠΎΠΊ, ΡΡΠΆΠ΅Π»Π΅ΠΉ ΠΏΡΠ΅Π΄ΡΠ΄ΡΡΠ΅Π³ΠΎ ΠΌΠ°ΡΠ΅ΡΠΈΠ°Π»Π°, ΠΏΡΠΈ ΠΎΠ±ΡΡΠ½ΡΡ ΡΡΠ»ΠΎΠ²ΠΈΡΡ Π½Π΅ Π³Π½Π΅ΡΡΡ. Π₯ΡΡΠΏΠΊΠΈΠΉ, Π±ΡΡΡΡΠΎ Π»ΠΎΠΌΠ°Π΅ΡΡΡ.
- ΠΠΏΡΠ΅Π΄Π΅Π»Π΅Π½ΠΈΠ΅ ΠΏΠΎ ΠΏΠ°ΡΠ°ΠΌΠ΅ΡΡΠ°ΠΌ ΠΏΠ»ΠΎΡΠ½ΠΎΡΡΠΈ
ΠΠ»Ρ ΠΎΠΏΡΠ΅Π΄Π΅Π»Π΅Π½ΠΈΡ ΡΠ°Π·Π½ΠΎΠ²ΠΈΠ΄Π½ΠΎΡΡΠΈ ΠΌΠ΅ΡΠ°Π»Π»Π° ΠΏΠΎ ΠΏΠ»ΠΎΡΠ½ΠΎΡΡΠΈ ΠΏΠΎΠ½Π°Π΄ΠΎΠ±ΠΈΡΡΡ ΠΌΠ΅ΡΠ½ΡΠΉ ΡΠΈΠ»ΠΈΠ½Π΄Ρ ΠΈ Π²ΠΎΠ΄Π°. Π‘ΡΡΡ ΠΌΠ΅ΡΠΎΠ΄ΠΈΠΊΠΈ Π·Π°ΠΊΠ»ΡΡΠ°Π΅ΡΡΡ Π² ΠΏΠΎΡΡΠ΅ΠΏΠ΅Π½Π½ΠΎΠΌ ΠΏΠΎΠ³ΡΡΠΆΠ΅Π½ΠΈΠΈ ΠΈΠ·Π΄Π΅Π»ΠΈΡ Π² ΠΆΠΈΠ΄ΠΊΠΎΡΡΡ. ΠΡΠΈ ΠΏΠΎΠ³ΡΡΠΆΠ΅Π½ΠΈΠΈ ΡΠ΅Π»Π° Π² Π²ΠΎΠ΄Ρ ΠΏΡΠΎΠΈΡΡ ΠΎΠ΄ΠΈΡ Π²ΡΡΠ²ΠΎΠ±ΠΎΠΆΠ΄Π΅Π½ΠΈΠ΅ ΠΎΠΏΡΠ΅Π΄Π΅Π»Π΅Π½Π½ΠΎΠ³ΠΎ ΠΊΠΎΠ»ΠΈΡΠ΅ΡΡΠ²Π° ΠΆΠΈΠ΄ΠΊΠΎΡΡΠΈ. ΠΡΠΈΠΌΠ΅Π½Π΅Π½ΠΈΠ΅ ΠΏΡΠΎΡΡΠ΅ΠΉΡΠ΅ΠΉ ΡΠΈΠ·ΠΈΡΠ΅ΡΠΊΠΎΠΉ ΡΠΎΡΠΌΡΠ»Ρ ΠΏΠΎΠ·Π²ΠΎΠ»ΡΠ΅Ρ Π²ΡΡΠΈΡΠ»ΠΈΡΡ ΠΏΠ»ΠΎΡΠ½ΠΎΡΡΡ ΠΌΠ°ΡΠ΅ΡΠΈΠ°Π»Π°. ΠΡΡΠ°Π»ΡΠ½ΠΎΠ΅ ΠΎΡΡΠ°Π΅ΡΡΡ Π·Π° ΡΠ°Π±Π»ΠΈΡΠ½ΡΠΌΠΈ Π΄Π°Π½Π½ΡΠΌΠΈ. ΠΡΠ»ΠΈ ΠΏΠΎΠ»ΡΡΠ΅Π½Π½ΡΠΉ ΠΏΠΎΠΊΠ°Π·Π°ΡΠ΅Π»Ρ Π±Π»ΠΈΠ·ΠΎΠΊ ΠΊ 2,7/ΠΌΠ», Π·Π½Π°ΡΠΈΡ ΠΏΠ΅ΡΠ΅Π΄ Π²Π°ΠΌΠΈ ΡΡΠΎΠΏΡΠΎΡΠ΅Π½ΡΠ½ΡΠΉ Π°Π»ΡΠΌΠΈΠ½ΠΈΠΉ.
- Π Π°ΡΠΏΠΎΠ·Π½Π°Π²Π°Π½ΠΈΠ΅ ΠΌΠ΅ΡΠ°Π»Π»Π° ΠΌΠ°Π³Π½ΠΈΡΠΎΠΌ
ΠΠ½ΠΎΠ³ΠΈΠΌ ΡΠ»Π΅ΠΌΠ΅Π½ΡΠΎΠΌ ΡΠ²ΠΎΠΉΡΡΠ²Π΅Π½Π½ΠΎ ΠΏΡΠΈΡΡΠ³ΠΈΠ²Π°Π½ΠΈΠ΅ ΠΌΠ°Π³Π½ΠΈΡΠΎΠΌ. ΠΠ΄Π½Π°ΠΊΠΎ, ΡΡΠΎ ΡΠ²ΠΎΠΉΡΡΠ²ΠΎ Π½Π΅ ΠΏΡΠΈΠΌΠ΅Π½ΠΈΠΌΠΎ ΠΊ Al. ΠΠΎΡΡΠΎΠΌΡ Π΄Π»Ρ ΠΎΠΏΡΠ΅Π΄Π΅Π»Π΅Π½ΠΈΡ ΠΊΠ°ΡΠ΅ΡΡΠ²Π΅Π½Π½ΡΡ Ρ Π°ΡΠ°ΠΊΡΠ΅ΡΠΈΡΡΠΈΠΊ Π΄ΠΎΡΡΠ°ΡΠΎΡΠ½ΠΎ ΠΊ ΠΈΠ·Π΄Π΅Π»ΠΈΡ ΠΏΠΎΠ΄Π½Π΅ΡΡΠΈ ΠΌΠ°Π³Π½ΠΈΡ. ΠΡΠ»ΠΈ ΠΌΠ΅ΡΠ°Π»Π» Π½ΠΈΠΊΠ°ΠΊΠΈΠΌ ΠΎΠ±ΡΠ°Π·ΠΎΠΌ Π½Π΅ ΠΎΡΡΠ΅Π°Π³ΠΈΡΡΠ΅Ρ, ΠΈ ΠΎΠ½ ΠΈΠΌΠ΅Π΅Ρ ΡΠ΅ΡΠ΅Π±ΡΠΈΡΡΡΠΉ ΠΎΡΡΠ΅Π½ΠΎΠΊ, Π·Π½Π°ΡΠΈΡ ΠΏΠ΅ΡΠ΅Π΄ Π²Π°ΠΌΠΈ Π°Π»ΡΠΌΠΈΠ½ΠΈΠΉ.
ΠΠ΄ΠΈΠ½ΡΡΠ²Π΅Π½Π½ΡΠΌ ΠΎΡΡΠΈΡΠ°ΡΠ΅Π»ΡΠ½ΡΠΌ ΠΌΠΎΠΌΠ΅Π½ΡΠΎΠΌ ΠΌΠ΅ΡΠΎΠ΄ΠΈΠΊΠΈ ΡΠ²Π»ΡΠ΅ΡΡΡ Π½Π΅Π²ΠΎΠ·ΠΌΠΎΠΆΠ½ΠΎΡΡΡ Π²ΡΠ΄Π΅Π»Π΅Π½ΠΈΡ ΡΠΏΠ»Π°Π². ΠΡΠ»ΠΈ Π² Π½Π΅ΠΌ ΡΠΎΠ΄Π΅ΡΠΆΠΈΡΡΡ Π±ΠΎΠ»ΡΡΠΎΠ΅ ΠΊΠΎΠ»ΠΈΡΠ΅ΡΡΠ²ΠΎ Π°Π»ΡΠΌΠΈΠ½ΠΈΡ, ΠΌΠ°Π³Π½ΠΈΡ ΡΠ°ΠΊΠΆΠ΅ Π½Π° Π½Π΅Π³ΠΎ Π½Π΅ ΠΎΠΊΠ°ΠΆΠ΅Ρ Π²ΠΎΠ·Π΄Π΅ΠΉΡΡΠ²ΠΈΡ. ΠΠΎΡΡΠΎΠΌΡ Π΄Π»Ρ ΠΎΠΏΡΠ΅Π΄Π΅Π»Π΅Π½ΠΈΡ ΡΠΈΡΡΠΎΡΡ ΡΠΏΠ»Π°Π²Π° ΠΏΡΠΈΠ΄Π΅ΡΡΡ ΠΈΡΠΏΠΎΠ»ΡΠ·ΠΎΠ²Π°ΡΡ Π΄ΠΎΠΏΠΎΠ»Π½ΠΈΡΠ΅Π»ΡΠ½ΡΠ΅ ΠΌΠ΅ΡΠΎΠ΄ΠΈΠΊΠΈ.
- Π’Π΅ΡΡΠΈΡΠΎΠ²Π°Π½ΠΈΠ΅ ΠΏΠΎ ΠΏΠ°ΡΠ°ΠΌΠ΅ΡΡΠ°ΠΌ ΡΠ΅ΠΏΠ»ΠΎΠΏΡΠΎΠ²ΠΎΠ΄Π½ΠΎΡΡΠΈ
ΠΠ°ΡΠ°ΠΌΠ΅ΡΡΡ ΡΠ΅ΠΏΠ»ΠΎΠΏΡΠΎΠ²ΠΎΠ΄Π½ΠΎΡΡΠΈ Π°Π»ΡΠΌΠΈΠ½ΠΈΡ Π½Π°ΠΌΠ½ΠΎΠ³ΠΎ Π²ΡΡΠ΅, ΡΠ΅ΠΌ Ρ Π΄ΡΡΠ³ΠΈΡ ΡΠ»Π΅ΠΌΠ΅Π½ΡΠΎΠ² ΡΠ°Π±Π»ΠΈΡΡ ΠΠ΅Π½Π΄Π΅Π»Π΅Π΅Π²Π°. ΠΠΎΡΡΠΎΠΌΡ ΠΎΠ΄ΠΈΠ½Π°ΠΊΠΎΠ²ΡΠΉ ΠΎΠ±ΡΠ΅ΠΌ ΠΆΠΈΠ΄ΠΊΠΎΡΡΠΈ ΠΏΡΠΈ ΠΎΠ΄ΠΈΠ½Π°ΠΊΠΎΠ²ΡΡ ΡΡΠ»ΠΎΠ²ΠΈΡΡ Π² Π°Π»ΡΠΌΠΈΠ½ΠΈΠ΅Π²ΠΎΠΉ ΠΏΠΎΡΡΠ΄Π΅ Π΄ΠΎΠ²ΠΎΠ΄ΠΈΡΡΡ Π΄ΠΎ ΠΊΠΈΠΏΠ΅Π½ΠΈΡ Π½Π°ΠΌΠ½ΠΎΠ³ΠΎ Π±ΡΡΡΡΠ΅Π΅. ΠΠ°ΠΊΡΠΈΠΌΠ°Π»ΡΠ½Π°Ρ ΡΠ΅ΠΌΠΏΠ΅ΡΠ°ΡΡΡΠ° ΠΏΠ»Π°Π²Π»Π΅Π½ΠΈΡ Al ΡΠΎΡΡΠ°Π²Π»ΡΠ΅Ρ 660 Π³ΡΠ°Π΄ΡΡΠΎΠ².
- Π Π°ΡΠΏΠΎΠ·Π½Π°Π²Π°Π½ΠΈΠ΅ Π°Π»ΡΠΌΠΈΠ½ΠΈΡ Ρ ΠΈΠΌΠΈΡΠ΅ΡΠΊΠΈΠΌΠΈ ΠΌΠ΅ΡΠΎΠ΄Π°ΠΌΠΈ
ΠΠΏΡΠ΅Π΄Π΅Π»ΠΈΡΡ Al Π»Π΅Π³ΠΊΠΎ. ΠΠΎΡΡΠ°ΡΠΎΡΠ½ΠΎ Π½Π° ΠΏΡΠ΅Π΄Π²Π°ΡΠΈΡΠ΅Π»ΡΠ½ΠΎ ΠΎΡΠΈΡΠ΅Π½Π½ΡΡ ΠΏΠΎΠ²Π΅ΡΡ Π½ΠΎΡΡΡ Π½Π°Π½Π΅ΡΡΠΈ ΡΠ΅Π»ΠΎΡΡ. Π§Π΅ΡΠ΅Π· Π½Π΅ΠΊΠΎΡΠΎΡΠΎΠ΅ Π²ΡΠ΅ΠΌΡ ΠΏΠΎΠ²Π΅ΡΡ Π½ΠΎΡΡΡ ΠΎΠΊΠΈΡΠ»ΠΈΡΡΡ, ΡΡΠΎ ΠΌΠΎΠΆΠ½ΠΎ Π±ΡΠ΄Π΅Ρ ΡΠ²ΠΈΠ΄Π΅ΡΡ Π²ΠΈΠ·ΡΠ°Π»ΡΠ½ΠΎ.
ΠΠ½Π°Π»ΠΎΠ³ΠΈΡΠ½Π°Ρ ΡΠ΅Π°ΠΊΡΠΈΡ ΠΏΡΠΎΠΈΡΡ ΠΎΠ΄ΠΈΡ ΠΏΡΠΈ Π²ΠΎΠ·Π΄Π΅ΠΉΡΡΠ²ΠΈΠΈ Π½Π° ΠΌΠ΅ΡΠ°Π»Π» ΠΊΠΈΡΠ»ΠΎΡΡ, Π² ΡΠΎΠΌ ΡΠΈΡΠ»Π΅Β ΠΈ ΡΠΎΠΊΠ° Π»ΠΈΠΌΠΎΠ½Π°. ΠΠ³ΡΠ΅ΡΡΠΈΠ²Π½ΠΎΠ΅ Π²ΠΎΠ·Π΄Π΅ΠΉΡΡΠ²ΠΈΠ΅ ΠΊΠΈΡΠ»ΠΎΡΡ ΠΏΡΠΎΡΠ²Π»ΡΠ΅ΡΡΡ ΠΏΠΎΡΠ²Π»Π΅Π½ΠΈΠ΅ΠΌ ΡΠ΅ΠΌΠ½ΠΎ-ΡΠ΅ΡΡΡ ΠΏΡΡΠ΅Π½, Π½Π°ΡΡΡΠ°ΡΡΠΈΡ Π²Π½Π΅ΡΠ½ΠΈΠΉ Π²ΠΈΠ΄ ΠΈΠ·Π΄Π΅Π»ΠΈΡ.
ΠΡΠ»ΠΈΡΠΈΠ΅ Π°Π»ΡΠΌΠΈΠ½ΠΈΡ ΠΎΡ ΡΠΏΠ»Π°Π²ΠΎΠ² Π½Π° ΠΈΡ ΠΎΡΠ½ΠΎΠ²Π΅
Π§ΡΠΎΠ±Ρ Π½Π°ΠΉΡΠΈ ΡΠ°Π·Π»ΠΈΡΠΈΡ ΠΌΠ΅ΠΆΠ΄Ρ Π°Π»ΡΠΌΠΈΠ½ΠΈΠ΅ΠΌ ΡΠΏΠ»Π°Π²Π°ΠΌΠΈ Π½Π° Π΅Π³ΠΎ ΠΎΡΠ½ΠΎΠ²Π΅ ΠΏΠΎΡΡΠ΅Π±ΡΠ΅ΡΡΡ ΠΏΡΠΎΠ²Π΅Π΄Π΅Π½ΠΈΠ΅ Π»Π°Π±ΠΎΡΠ°ΡΠΎΡΠ½ΡΡ ΠΈΡΡΠ»Π΅Π΄ΠΎΠ²Π°Π½ΠΈΠΉ. ΠΠ΄Π½Π°ΠΊΠΎ, ΠΡΠ»ΠΈΠ±ΠΈΠ½Ρ Π½Π°ΡΠ»ΠΈ Π½Π΅ΡΠΊΠΎΠ»ΡΠΊΠΎ ΡΠΏΠΎΡΠΎΠ±ΠΎΠ², ΠΊΠΎΡΠΎΡΡΠ΅ ΠΌΠΎΠΆΠ½ΠΎ ΠΈΡΠΏΠΎΠ»ΡΠ·ΠΎΠ²Π°ΡΡ ΡΠ°ΠΌΠΈΠΌ, Π² Π΄ΠΎΠΌΠ°ΡΠ½ΠΈΡ ΡΡΠ»ΠΎΠ²ΠΈΡΡ .
ΠΡΠΈ ΠΌΠ΅Ρ Π°Π½ΠΈΡΠ΅ΡΠΊΠΎΠΌ Π²ΠΎΠ·Π΄Π΅ΠΉΡΡΠ²ΠΈΠΈ Π½Π° Π΄ΡΡΠ°Π»Ρ, ΠΎΡ ΡΠΏΠ»Π°Π²Π° Π½Π΅ ΠΈΡΡ ΠΎΠ΄ΠΈΡ Π²ΡΡΠΎΠΊΠΎΠ³ΠΎ ΡΠ°ΡΡΠΎΡΠ½ΠΎΠ³ΠΎ Π·Π²ΠΎΠ½Π°. Π£Π΄Π°Ρ ΠΏΠΎ Al ΠΏΡΠΎΠ²ΠΎΡΠΈΡΡΠ΅Ρ ΠΏΠΎΡΠ²Π»Π΅Π½ΠΈΠ΅ Π·Π²ΠΎΠ½ΠΊΠΈΡ ΡΠ°ΡΡΠΎΡ, ΠΎΠ±Π»Π°Π΄Π°Π΅Ρ ΠΎΡΠΎΠ±ΡΠΌ Π±Π»Π΅ΡΠΊΠΎΠΌ, Π±Π»Π°Π³ΠΎΠ΄Π°ΡΡ ΠΊΠΎΡΠΎΡΠΎΠΌ ΠΌΠΎΠΆΠ½ΠΎ ΡΠ²ΠΈΠ΄Π΅ΡΡ ΡΠΎΠ±ΡΡΠ²Π΅Π½Π½ΠΎΠ΅ ΠΎΡΡΠ°ΠΆΠ΅Π½ΠΈΠ΅.
ΠΡΠΎΡΡΠΌ ΡΠΏΠΎΡΠΎΠ±ΠΎΠΌ ΠΎΠΏΡΠ΅Π΄Π΅Π»Π΅Π½ΠΈΡ Π½Π°Π»ΠΈΡΠΈΡ Π΄ΠΎΠΏΠΎΠ»Π½ΠΈΡΠ΅Π»ΡΠ½ΡΡ ΡΠ»Π΅ΠΌΠ΅Π½ΡΠΎΠ² Π² ΡΠΎΡΡΠ°Π²Π΅ Π°Π»ΡΠΌΠΈΠ½ΠΈΡ ΡΠ²Π»ΡΠ΅ΡΡΡ ΠΏΡΠΎΠ²Π΅ΡΠΊΠ° Π΅Π³ΠΎ ΠΏΠ΅ΡΠ΅ΠΊΠΈΡΡΡ Π²ΠΎΠ΄ΠΎΡΠΎΠ΄Π°. ΠΡΠΈ Π½Π°Π½Π΅ΡΠ΅Π½ΠΈΠΈ Π½Π° ΠΏΠΎΠ²Π΅ΡΡ Π½ΠΎΡΡΠ½ΡΠΉ ΡΠ»ΠΎΠΉ Π½Π΅ΡΠΊΠΎΠ»ΡΠΊΠΈΡ ΠΊΠ°ΠΏΠ΅Π»Ρ ΠΏΠ΅ΡΠ΅ΠΊΠΈΡΠΈ Π²ΠΎΠ΄ΠΎΡΠΎΠ΄Π° ΡΠΏΠ»Π°Π² Π½Π°ΡΠ½Π΅Ρ ΠΈΠ·ΠΌΠ΅Π½ΡΡΡ ΡΠ²Π΅Ρ Π² ΡΡΠΎΡΠΎΠ½Ρ ΠΏΠΎΡΠ΅ΠΌΠ½Π΅Π½ΠΈΡ, ΡΠ΅Π³ΠΎ Π½Π΅Π»ΡΠ·Ρ ΡΠΊΠ°Π·Π°ΡΡ ΠΏΡΠΎ Π°Π»ΡΠΌΠΈΠ½ΠΈΠΉ.
ΠΠΎΠ»Π΅Π΅ ΡΠΎΡΠ½ΠΎ ΠΎΠΏΡΠ΅Π΄Π΅Π»ΠΈΡΡ ΡΠΎΡΡΠ°Π² ΠΈΠ·Π΄Π΅Π»ΠΈΡ ΠΌΠΎΠΆΠ½ΠΎ ΠΏΠΎΡΡΠ΅Π΄ΡΡΠ²ΠΎΠΌ ΠΏΡΠΎΠ²Π΅Π΄Π΅Π½ΠΈΡ ΡΠΊΡΠΏΠ΅ΡΡΠΈΠ·Ρ ΠΏΡΠΎΡΠ΅ΡΡΠΈΠΎΠ½Π°Π»ΡΠ½ΡΠΌΠΈ ΡΠΊΡΠΏΠ΅ΡΡΠ°ΠΌΠΈ.
ΠΠ°ΠΊΠ»ΡΡΠ΅Π½ΠΈΠ΅
ΠΠ΅ΡΠΌΠΎΡΡΡ Π½Π° ΡΡ ΠΎΠΆΠ΅ΡΡΡ ΠΌΠ΅ΠΆΠ΄Ρ ΠΌΠ΅ΡΠ°Π»Π»Π°ΠΌΠΈ, ΠΎΠΏΡΠ΅Π΄Π΅Π»ΠΈΡΡ, Π³Π΄Π΅ ΠΊΠ°ΠΊΠΎΠΉ Π»Π΅Π³ΠΊΠΎ. ΠΠ½ΠΎΠ³ΠΎΡΠΈΡΠ»Π΅Π½Π½ΡΠ΅ ΠΌΠ΅ΡΠΎΠ΄ΠΈΠΊΠΈ ΠΏΠΎΠ΄ΡΠ²Π΅ΡΠΆΠ΄Π°ΡΡ, ΡΡΠΎ ΡΠ°ΠΌΡΠΌ ΠΏΠΎΠΏΡΠ»ΡΡΠ½ΡΠΌ ΠΈΠ· Π½ΠΈΡ ΡΠ²Π»ΡΠ΅ΡΡΡ ΠΎΠΏΡΠ΅Π΄Π΅Π»Π΅Π½ΠΈΠ΅ ΠΈΠ·Π΄Π΅Π»ΠΈΡ ΠΏΠΎ Π²Π΅ΡΡ. Π Π°Π·Π»ΠΈΡΠΈΡΡ ΠΈΠ·Π΄Π΅Π»ΠΈΡ ΠΌΠ΅ΠΆΠ΄Ρ ΡΠΎΠ±ΠΎΠΉ ΠΏΠΎΠΌΠΎΠΆΠ΅Ρ ΠΌΠ°ΡΡΠ° ΠΈ ΡΠ²Π΅Ρ. Π‘Π΅ΡΠ΅Π±ΡΠΈΡΡΡΠΉ Π°Π»ΡΠΌΠΈΠ½ΠΈΠΉ Π½Π°ΠΌΠ½ΠΎΠ³ΠΎ Π»Π΅Π³ΡΠ΅ ΡΠΈΠ½ΠΊΠ°. ΠΡΠ»ΠΈ Π²Ρ ΡΠΎΠΌΠ½Π΅Π²Π°Π΅ΡΠ΅ΡΡ, ΠΏΡΠ΅Π΄Π»Π°Π³Π°Π΅ΠΌ Π²ΠΎΡΠΏΠΎΠ»ΡΠ·ΠΎΠ²Π°ΡΡΡΡ Π΄ΡΡΠ³ΠΈΠΌΠΈ, Π²ΡΡΠ΅ΡΠΊΠ°Π·Π°Π½Π½ΡΠΌΠΈ ΠΌΠ΅ΡΠΎΠ΄ΠΈΠΊΠ°ΠΌΠΈ.
Β
anexmetall.ru
Π¦ΠΈΠ½ΠΊ-Π°Π»ΡΠΌΠΈΠ½ΠΈΠ΅Π²ΡΠ΅ ΡΠΏΠ»Π°Π²Ρ
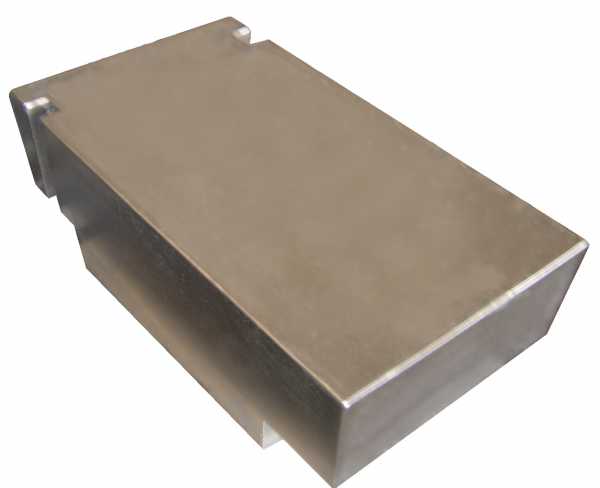
ΠΠ°Π·Π½Π°ΡΠ΅Π½ΠΈΠ΅ ΠΈ ΠΎΠΏΠΈΡΠ°Π½ΠΈΠ΅
Π¦ΠΈΠ½ΠΊ-Π°Π»ΡΠΌΠΈΠ½ΠΈΠ΅Π²ΡΠ΅ ΡΠΏΠ»Π°Π²Ρ ΠΏΡΠΎΠΈΠ·Π²ΠΎΠ΄ΡΡΡΡ ΠΏΠΎ Π’Π£ 647 Π Π 00200928-96-2000.
Π¦ΠΈΠ½ΠΊ-Π°Π»ΡΠΌΠΈΠ½ΠΈΠ΅Π²ΡΠ΅ ΡΠΏΠ»Π°Π²Ρ ΠΈΡΠΏΠΎΠ»ΡΠ·ΡΡΡΡΡ Π΄Π»Ρ Π³ΠΎΡΡΡΠ΅Π³ΠΎ ΠΎΡΠΈΠ½ΠΊΠΎΠ²Π°Π½ΠΈΡ ΡΡΠ°Π»ΡΠ½ΠΎΠΉ ΠΏΠΎΠ»ΠΎΡΡ.
Β
Π₯ΠΈΠΌΠΈΡΠ΅ΡΠΊΠΈΠΉ ΡΠΎΡΡΠ°Π²*Β
ΠΠ°ΡΡΠΎΠ²Π°Ρ Π΄ΠΎΠ»Ρ, % |
ΠΠ°ΡΠΊΠ° ΡΠΈΠ½ΠΊ — Π°Π»ΡΠΌΠΈΠ½ΠΈΠ΅Π²ΠΎΠ³ΠΎ ΡΠΏΠ»Π°Π²Π° |
|||
Π¦Π0 |
Π¦Π03 |
Π¦Π04 |
Π¦Π10 |
|
Π¦ΠΈΠ½ΠΊ |
ΠΡΡΠ°Π»ΡΠ½ΠΎΠ΅ |
ΠΡΡΠ°Π»ΡΠ½ΠΎΠ΅ |
ΠΡΡΠ°Π»ΡΠ½ΠΎΠ΅ |
ΠΡΡΠ°Π»ΡΠ½ΠΎΠ΅ |
ΠΠ»ΡΠΌΠΈΠ½ΠΈΠΉ |
- |
ΠΎΡ 0,25 Π΄ΠΎ 0,35 |
ΠΎΡ 0,36 Π΄ΠΎ 0,45 |
ΠΎΡ 9,5 Π΄ΠΎ 10 |
Π‘Π²ΠΈΠ½Π΅Ρ |
ΠΎΡ 0,1 Π΄ΠΎ 0,2 |
ΠΎΡ 0,1 Π΄ΠΎ 0,2 |
ΠΎΡ 0,1 Π΄ΠΎ 0,2 |
ΠΎΡ 0,1 Π΄ΠΎ 0,2 |
ΠΠ΅Π»Π΅Π·ΠΎ |
0,01 |
0,01 |
0,01 |
0,018 |
ΠΠ°Π΄ΠΌΠΈΠΉ |
0,01 |
0,01 |
0,01 |
0,01 |
ΠΠ΅Π΄Ρ |
0,002 |
0,002 |
0,002 |
0,002 |
ΠΠ»ΠΎΠ²ΠΎ |
0,001 |
0,001 |
0,001 |
0,001 |
ΠΡΡΡΡΠΊ |
0,0005 |
0,0005 |
0,0005 |
0,0005 |
Β * Π‘ΠΎΠ΄Π΅ΡΠΆΠ°Π½ΠΈΠ΅ Π°Π»ΡΠΌΠΈΠ½ΠΈΡ, ΡΠ²ΠΈΠ½ΡΠ°, ΠΊΠ°Π΄ΠΌΠΈΡ ΠΈΠ»ΠΈ ΠΎΡΠ΄Π΅Π»ΡΠ½ΡΡ ΠΏΡΠΈΠΌΠ΅ΡΠ΅ΠΉ Π² ΡΠΏΠ»Π°Π²Π΅ ΠΌΠΎΠΆΠ΅Ρ Π±ΡΡΡ ΠΈΠ·ΠΌΠ΅Π½Π΅Π½ΠΎ ΠΏΠΎ ΡΡΠ΅Π±ΠΎΠ²Π°Π½ΠΈΡ ΠΏΠΎΡΡΠ΅Π±ΠΈΡΠ΅Π»Ρ. ΠΡΠΈ ΡΡΠΎΠΌ ΡΠΎΠ΄Π΅ΡΠΆΠ°Π½ΠΈΠ΅ ΡΠΈΠ½ΠΊΠ°, ΡΠΎΠΎΡΠ²Π΅ΡΡΡΠ²ΡΡΡΠ΅Π΅ ΠΎΠΏΡΠ΅Π΄Π΅Π»Π΅Π½Π½ΠΎΠΉ ΠΌΠ°ΡΠΊΠ΅ ΡΠΏΠ»Π°Π²Π°, Π΄ΠΎΠ»ΠΆΠ½ΠΎ Π±ΡΡΡ ΡΠ²Π΅Π»ΠΈΡΠ΅Π½ΠΎ (ΡΠΌΠ΅Π½ΡΡΠ΅Π½ΠΎ) Π½Π° Π²Π΅Π»ΠΈΡΠΈΠ½Ρ ΡΠΎΠ΄Π΅ΡΠΆΠ°Π½ΠΈΡ Π»Π΅Π³ΠΈΡΡΡΡΠΈΡ ΠΊΠΎΠΌΠΏΠΎΠ½Π΅Π½ΡΠΎΠ² ΠΈΠ»ΠΈ ΠΏΡΠΈΠΌΠ΅ΡΠ΅ΠΉ.
Β
Π£ΠΏΠ°ΠΊΠΎΠ²ΠΊΠ° ΠΈ ΡΡΠ°Π½ΡΠΏΠΎΡΡΠΈΡΠΎΠ²ΠΊΠ°
Π¦ΠΈΠ½ΠΊ-Π°Π»ΡΠΌΠΈΠ½ΠΈΠ΅Π²ΡΠ΅ ΡΠΏΠ»Π°Π²Ρ Π¦Π0, Π¦Π03, Π¦Π04 Π²ΡΠΏΡΡΠΊΠ°ΡΡΡΡ Π² Π²ΠΈΠ΄Π΅ Π±Π»ΠΎΠΊΠΎΠ² ΠΌΠ°ΡΡΠΎΠΉ Π΄ΠΎ 1500 ΠΊΠ³, Β ΡΠΏΠ»Π°Π²Ρ Π¦Π0, Π¦Π10 β Π² Π²ΠΈΠ΄Π΅ ΡΡΡΠ΅ΠΊ ΠΌΠ°ΡΡΠΎΠΉ 19-25 ΠΊΠ³. ΠΠΎΠΏΡΡΠΊΠ°Π΅ΠΌΡΠ΅ ΠΎΡΠΊΠ»ΠΎΠ½Π΅Π½ΠΈΡ ΠΏΠΎ ΠΌΠ°ΡΡΠ΅ Π±Π»ΠΎΠΊΠΎΠ² ΠΈ ΡΠΏΠ°ΠΊΠΎΠ²ΠΊΠ° ΠΏΠΎ ΠΠΠ‘Π’ 3640.
Π’ΡΠ°Π½ΡΠΏΠΎΡΡΠΈΡΡΠ΅ΡΡΡ Π²ΡΠ΅ΠΌΠΈ Π²ΠΈΠ΄Π°ΠΌΠΈ ΠΊΡΡΡΡΡ ΡΡΠ°Π½ΡΠΏΠΎΡΡΠ½ΡΡ ΡΡΠ΅Π΄ΡΡΠ².
Β
ΠΠ°ΡΠ°Π½ΡΠΈΠΉΠ½ΡΠΉ ΡΡΠΎΠΊ Ρ ΡΠ°Π½Π΅Π½ΠΈΡ
15 Π»Π΅Ρ Ρ ΠΌΠΎΠΌΠ΅Π½ΡΠ° ΠΈΠ·Π³ΠΎΡΠΎΠ²Π»Π΅Π½ΠΈΡ.
electrozinc.ugmk.com
ΠΠ°Π»ΡΠ²Π°Π½ΠΈΡΠ΅ΡΠΊΠΎΠ΅ ΠΏΠΎΠΊΡΡΡΠΈΠ΅ Π°Π»ΡΠΌΠΈΠ½ΠΈΡ ΠΈ Π΅Π³ΠΎ ΡΠΏΠ»Π°Π²ΠΎΠ²
Π¦Π΅Π»Ρ Π³Π°Π»ΡΠ²Π°Π½ΠΈΡΠ΅ΡΠΊΠΈΡ ΠΏΠΎΠΊΡΡΡΠΈΠΉ Π°Π»ΡΠΌΠΈΠ½ΠΈΡ ΠΈ Π΅Π³ΠΎ ΡΠΏΠ»Π°Π²ΠΎΠ² β ΡΠΎΡΠ΅ΡΠ°ΡΡ ΡΡΠ΄ ΡΠ΅Π½Π½ΡΡ ΡΠ²ΠΎΠΉΡΡΠ² ΠΎΡΠ½ΠΎΠ²Π½ΠΎΠ³ΠΎ ΠΌΠ΅ΡΠ°Π»Π»Π° Β (ΡΠΏΠ»Π°Π²Π°) ΠΈ ΠΏΠΎΠΊΡΡΡΠΈΡ. ΠΠ»Ρ Π·Π°ΡΠΈΡΠ½ΠΎ-Π΄Π΅ΠΊΠΎΡΠ°ΡΠΈΠ²Π½ΠΎΠΉ ΠΎΡΠ΄Π΅Π»ΠΊΠΈ ΠΈΠ·Π΄Π΅Π»ΠΈΠΉ ΠΈΠ· Π°Π»ΡΠΌΠΈΠ½ΠΈΡ ΠΈ Π΅Π³ΠΎ ΡΠΏΠ»Π°Π²ΠΎΠ² ΠΏΡΠΈΠ±Π΅Π³Π°ΡΡ ΠΊ Π½Π°Π½Π΅ΡΠ΅Π½ΠΈΡ ΠΊΠΎΠΌΠ±ΠΈΠ½ΠΈΡΠΎΠ²Π°Π½Π½ΡΡ ΠΏΠΎΠΊΡΡΡΠΈΠΉ ΠΌΠ΅Π΄Ρ β Π½ΠΈΠΊΠ΅Π»Ρ β Ρ ΡΠΎΠΌ ΠΈΠ»ΠΈ Π½ΠΈΠΊΠ΅Π»Ρ β Ρ ΡΠΎΠΌ. Π ΡΠ΅Π»ΡΡ Π·Π°ΡΠΈΡΡ ΠΎΡ ΠΌΠ΅Ρ Π°Π½ΠΈΡΠ΅ΡΠΊΠΎΠ³ΠΎ ΠΈΠ·Π½ΠΎΡΠ° Π½Π°Π½ΠΎΡΡΡ ΡΡΠ°Π²Π½ΠΈΡΠ΅Π»ΡΠ½ΠΎ ΡΠΎΠ»ΡΡΡΠ΅ ΠΏΠΎΠΊΡΡΡΠΈΡ ΠΈΠ· Ρ ΡΠΎΠΌΠ°, Π΄Π»Ρ ΡΠΎΠΎΠ±ΡΠ΅Π½ΠΈΡ Π°Π½ΡΠΈΡΡΠΈΠΊΡΠΈΠΎΠ½Π½ΡΡ ΡΠ²ΠΎΠΉΡΡΠ² Π½Π°Π½ΠΎΡΡΡ ΠΏΠΎΠΊΡΡΡΠΈΡ ΠΈΠ· ΡΠΏΠ»Π°Π²Π° ΡΠ²ΠΈΠ½Π΅Ρ β ΠΎΠ»ΠΎΠ²ΠΎ ΠΈΠ»ΠΈ ΠΌΠ΅Π΄Ρ β ΠΎΠ»ΠΎΠ²ΠΎ. ΠΠ»Ρ ΠΎΠ±Π»Π΅Π³ΡΠ΅Π½ΠΈΡ ΠΈ ΡΡΠΊΠΎΡΠ΅Π½ΠΈΡ ΠΏΡΠΎΡΠ΅ΡΡΠ° ΠΏΠ°ΠΉΠΊΠΈ Π°Π»ΡΠΌΠΈΠ½ΠΈΠ΅Π²ΡΡ ΠΈΠ·Π΄Π΅Π»ΠΈΠΉ Π½Π°Π½ΠΎΡΡΡ ΠΎΠ»ΠΎΠ²ΡΠ½Π½ΡΠ΅, ΡΠ²ΠΈΠ½ΡΠΎΠ²ΠΎΠΎΠ»ΠΎΠ²ΡΠ½Π½ΡΠ΅ ΠΈΠ»ΠΈ ΡΠ΅ΡΠ΅Π±ΡΡΠ½ΡΠ΅ ΠΏΠΎΠΊΡΡΡΠΈΡ. ΠΠΎΡΠ»Π΅Π΄Π½ΠΈΠ΅ ΠΈΡΠΏΠΎΠ»ΡΠ·ΡΡΡ ΡΠ°ΠΊΠΆΠ΅ Π΄Π»Ρ ΡΠΌΠ΅Π½ΡΡΠ΅Π½ΠΈΡ ΠΏΠ΅ΡΠ΅Ρ ΠΎΠ΄Π½ΠΎΠ³ΠΎ ΡΠΎΠΏΡΠΎΡΠΈΠ²Π»Π΅Π½ΠΈΡ Π² ΠΌΠ΅ΡΡΠ°Ρ ΠΊΠΎΠ½ΡΠ°ΠΊΡΠΎΠ². ΠΠ°ΡΡΠ½Π½ΡΠ΅ ΠΏΠΎΠΊΡΡΡΠΈΡ ΠΎΠ±Π΅ΡΠΏΠ΅ΡΠΈΠ²Π°ΡΡ ΠΏΡΠΎΡΠ½ΠΎΠ΅ ΡΡΠ΅ΠΏΠ»Π΅Π½ΠΈΠ΅ Π°Π»ΡΠΌΠΈΠ½ΠΈΡ Ρ ΡΠ΅Π·ΠΈΠ½ΠΎΠΉ ΠΏΡΠΈ Π³ΠΎΡΡΡΠ΅ΠΌ ΠΏΡΠ΅ΡΡΠΎΠ²Π°Π½ΠΈΠΈ. ΠΠ»Ρ Π·Π°ΡΠΈΡΡ ΠΎΡ Π·Π°Π΅Π΄Π°Π½ΠΈΡ ΡΠ΅Π·ΡΠ±ΠΎΠ²ΡΠ΅ Π°Π»ΡΠΌΠΈΠ½ΠΈΠ΅Π²ΡΠ΅ Π΄Π΅ΡΠ°Π»ΠΈ ΡΠΈΠ½ΠΊΡΡΡ. ΠΠ°Π΄ΠΌΠΈΡΠΎΠ²Π°Π½ΠΈΡ ΠΏΠΎΠ΄Π²Π΅ΡΠ³Π°ΡΡ ΡΠ·Π»Ρ, Π² ΠΊΠΎΡΠΎΡΡΡ Π°Π»ΡΠΌΠΈΠ½ΠΈΠ΅Π²ΡΠ΅ Π΄Π΅ΡΠ°Π»ΠΈ ΡΠΎΠΏΡΡΠΆΠ΅Π½Ρ ΡΠΎ ΡΡΠ°Π»ΡΠ½ΡΠΌΠΈ, ΠΌΠ΅Π΄Π½ΡΠΌΠΈ ΠΈ Π΄ΡΡΠ³ΠΈΠΌΠΈ Π΄Π΅ΡΠ°Π»ΡΠΌΠΈ, Π² ΠΊΠΎΠ½ΡΠ°ΠΊΡΠ΅ Ρ ΠΊΠΎΡΠΎΡΡΠΌΠΈ ΡΡΠΈΠ»ΠΈΠ²Π°Π΅ΡΡΡ ΠΊΠΎΡΡΠΎΠ·ΠΈΡ.
Π Π°Π·Π»ΠΈΡΠ½ΡΠ΅ Π΄Π΅ΡΠ°Π»ΠΈ ΡΠ»Π΅ΠΊΡΡΠΎΠ½Π½ΡΡ ΠΏΡΠΈΠ±ΠΎΡΠΎΠ² ΠΏΠΎΠ΄Π²Π΅ΡΠ³Π°ΡΡ ΡΠ΅ΡΠ΅Π±ΡΠ΅Π½ΠΈΡ, Π·ΠΎΠ»ΠΎΡΠ΅Π½ΠΈΡ, ΠΏΠΎΠΊΡΡΡΠΈΡ ΠΏΠ»Π°ΡΠΈΠ½ΠΎΠ²ΡΠΌΠΈ ΠΌΠ΅ΡΠ°Π»Π»Π°ΠΌΠΈ ΠΈ ΠΈΡ ΡΠΏΠ»Π°Π²Π°ΠΌΠΈ.
Π‘ΠΏΠ΅ΡΠΈΡΠΈΡΠ΅ΡΠΊΠΈΠ΅ ΡΡΡΠ΄Π½ΠΎΡΡΠΈ Π½Π°Π½Π΅ΡΠ΅Π½ΠΈΡ Π³Π°Π»ΡΠ²Π°Π½ΠΈΡΠ΅ΡΠΊΠΈΡ ΠΏΠΎΠΊΡΡΡΠΈΠΉ Π½Π° ΠΈΠ·Π΄Π΅Π»ΠΈΡ ΠΈΠ· Π°Π»ΡΠΌΠΈΠ½ΠΈΡ ΠΈ Π΅Π³ΠΎ ΡΠΏΠ»Π°Π²ΠΎΠ² ΡΠ²ΡΠ·Π°Π½Ρ Ρ Π½Π°Π»ΠΈΡΠΈΠ΅ΠΌ Π½Π° ΠΈΡ ΠΏΠΎΠ²Π΅ΡΡ Π½ΠΎΡΡΠΈ Π΅ΡΡΠ΅ΡΡΠ²Π΅Π½Π½ΠΎΠΉ ΠΎΠΊΠΈΡΠ½ΠΎΠΉ ΠΏΠ»Π΅Π½ΠΊΠΈ, ΠΏΡΠ΅ΠΏΡΡΡΡΠ²ΡΡΡΠ΅ΠΉ ΠΏΡΠΎΡΠ½ΠΎΠΌΡ ΡΡΠ΅ΠΏΠ»Π΅Π½ΠΈΡ ΠΌΠ΅ΠΆΠ΄Ρ ΠΎΡΠ½ΠΎΠ²ΠΎΠΉ ΠΈ ΠΏΠΎΠΊΡΡΡΠΈΡΠΌΠΈ. ΠΡΠΎΠΌΠ΅ ΡΠΎΠ³ΠΎ, ΡΠΈΠ»ΡΠ½ΠΎ ΡΠ»Π΅ΠΊΡΡΠΎΠΎΡΡΠΈΡΠ°ΡΠ΅Π»ΡΠ½ΠΎΠ΅ Π·Π½Π°ΡΠ΅Π½ΠΈΠ΅ ΠΏΠΎΡΠ΅Π½ΡΠΈΠ°Π»Π° Π°Π»ΡΠΌΠΈΠ½ΠΈΡ, ΠΎΡΠ²ΠΎΠ±ΠΎΠΆΠ΄Π΅Π½Π½ΠΎΠ³ΠΎ ΠΎΡ ΠΎΠΊΠΈΡΠ½ΠΎΠΉ ΠΏΠ»Π΅Π½ΠΊΠΈ, ΠΏΡΠΈΠ²ΠΎΠ΄ΠΈΡ ΠΊ Π²ΡΡΠ΅ΡΠ½Π΅Π½ΠΈΡ ΠΈΠΎΠ½ΠΎΠ² ΠΏΠΎΠΊΡΡΠ²Π°Π΅ΠΌΠΎΠ³ΠΎ ΠΌΠ΅ΡΠ°Π»Π»Π° Π΄ΠΎ Π½Π°ΡΠ°Π»Π° ΠΏΡΠΎΡ ΠΎΠΆΠ΄Π΅Π½ΠΈΡ ΡΠ»Π΅ΠΊΡΡΠΈΡΠ΅ΡΠΊΠΎΠ³ΠΎ ΡΠΎΠΊΠ° ΡΠ΅ΡΠ΅Π· ΡΠ°ΡΡΠ²ΠΎΡ ΡΠ»Π΅ΠΊΡΡΠΎΠ»ΠΈΡΠ°, ΡΡΠΎ ΡΠΎΠΆΠ΅ Π½Π°ΡΡΡΠ°Π΅Ρ ΡΡΠ΅ΠΏΠ»Π΅Π½ΠΈΠ΅ ΠΌΠ΅ΠΆΠ΄Ρ ΠΏΠΎΠΊΡΡΡΠΈΠ΅ΠΌ ΠΈ ΠΎΡΠ½ΠΎΠ²ΠΎΠΉ. ΠΡΠ΅ΠΎΠ΄ΠΎΠ»Π΅Π½ΠΈΠ΅ ΡΡΠΈΡ ΡΡΡΠ΄Π½ΠΎΡΡΠ΅ΠΉ Π΄ΠΎΡΡΠΈΠ³Π°Π΅ΡΡΡ ΡΠΏΠ΅ΡΠΈΠ°Π»ΡΠ½ΡΠΌΠΈ ΠΌΠ΅ΡΠΎΠ΄Π°ΠΌΠΈ ΠΏΠΎΠ΄Π³ΠΎΡΠΎΠ²ΠΊΠΈ ΠΏΠΎΠ²Π΅ΡΡ Π½ΠΎΡΡΠΈ ΠΏΠΎΠΊΡΡΠ²Π°Π΅ΠΌΡΡ ΠΈΠ·Π΄Π΅Π»ΠΈΠΉ.
ΠΠ°ΠΈΠ±ΠΎΠ»Π΅Π΅ ΡΠ°ΡΠΏΡΠΎΡΡΡΠ°Π½Π΅Π½Π½ΡΠΌΠΈ ΠΌΠ΅ΡΠΎΠ΄Π°ΠΌΠΈ ΠΏΠΎΠ΄Π³ΠΎΡΠΎΠ²ΠΊΠΈ ΠΏΠΎΠ²Π΅ΡΡ Π½ΠΎΡΡΠΈ Π°Π»ΡΠΌΠΈΠ½ΠΈΠ΅Π²ΡΡ ΠΈΠ·Π΄Π΅Π»ΠΈΠΉ ΠΏΠ΅ΡΠ΅Π΄ Π½Π°Π½Π΅ΡΠ΅Π½ΠΈΠ΅ΠΌ Π³Π°Π»ΡΠ²Π°Π½ΠΈΡΠ΅ΡΠΊΠΈΡ ΠΏΠΎΠΊΡΡΡΠΈΠΉ ΡΠ²Π»ΡΡΡΡΡ ΡΠ»Π΅Π΄ΡΡΡΠΈΠ΅: 1) ΡΠΈΠ½ΠΊΠ°ΡΠ½ΡΠΉ, 2) Π°Π½ΠΎΠ΄ΠΈΡΠΎΠ²Π°Π½ΠΈΠ΅ Π² ΡΠΎΡΡΠΎΡΠ½ΠΎΠΉ ΠΊΠΈΡΠ»ΠΎΡΠ΅, 3) ΠΏΡΠ΅Π΄Π²Π°ΡΠΈΡΠ΅Π»ΡΠ½ΠΎΠ΅ ΡΠ»Π΅ΠΊΡΡΠΎΠ»ΠΈΡΠΈΡΠ΅ΡΠΊΠΎΠ΅ ΠΎΡΠ°ΠΆΠ΄Π΅Π½ΠΈΠ΅ ΡΠΎΠ½ΡΠ°ΠΉΡΠΈΡ ΡΠΈΠ½ΠΊΠΎΠ²ΡΡ ΠΈΠ»ΠΈ Π»Π°ΡΡΠ½Π½ΡΡ ΠΏΠΎΠΊΡΡΡΠΈΠΉ.
Π¦ΠΈΠ½ΠΊΠ°ΡΠ½ΡΠΉ ΠΌΠ΅ΡΠΎΠ΄ ΠΏΠΎΠ΄Π³ΠΎΡΠΎΠ²ΠΊΠΈ ΠΏΠΎΠ²Π΅ΡΡ
Π½ΠΎΡΡΠΈ Π°Π»ΡΠΌΠΈΠ½ΠΈΠ΅Π²ΡΡ
ΠΈΠ·Π΄Π΅Π»ΠΈΠΉ ΡΠ²ΠΎΠ΄ΠΈΡΡΡ ΠΊ ΠΈΡ
ΠΊΡΠ°ΡΠΊΠΎΠ²ΡΠ΅ΠΌΠ΅Π½Π½ΠΎΠΌΡ ΠΏΠΎΠ³ΡΡΠΆΠ΅Π½ΠΈΡ (Π½Π° 30β60 Ρ) Π² ΡΠ°ΡΡΠ²ΠΎΡ ΡΠΈΠ½ΠΊΠ°ΡΠ° Π½Π°ΡΡΠΈΡ. ΠΠΊΠΈΡΠ½Π°Ρ ΠΏΠ»Π΅Π½ΠΊΠ° ΠΏΡΠΈ ΡΡΠΎΠΌ ΡΠ°ΡΡΠ²ΠΎΡΡΠ΅ΡΡΡ ΠΈ ΠΈΠ·Π΄Π΅Π»ΠΈΡ ΠΏΠΎΠΊΡΡΠ²Π°ΡΡΡΡ ΡΠΎΠ½ΠΊΠΎΠΉ ΠΏΠ»Π΅Π½ΠΊΠΎΠΉ ΡΠΈΠ½ΠΊΠ° (0,1β0,15 ΠΌΠΊΠΌ), ΠΏΡΠ΅Π΄ΡΠΏΡΠ΅ΠΆΠ΄Π°ΡΡΠ΅ΠΉ ΠΏΠΎΠ²Π΅ΡΡ
Π½ΠΎΡΡΡ ΠΎΡ ΠΏΠΎΠ²ΡΠΎΡΠ½ΠΎΠ³ΠΎ ΠΎΠΊΠΈΡΠ»Π΅Π½ΠΈΡ. ΠΡΠΈ ΡΡΠΎΠΌ ΠΏΡΠΎΡΠ΅ΠΊΠ°ΡΡ ΡΠ»Π΅Π΄ΡΡΡΠΈΠ΅ ΡΠ΅Π°ΠΊΡΠΈΠΈ. ΠΠ° Π°Π½ΠΎΠ΄Π½ΡΡ
ΡΡΠ°ΡΡΠΊΠ°Ρ
:
Al + ΠΠΠ- βAl(ΠΠ)3 + ΠΠ΅,
Al(OΠ)3 β AlO2 + H2O + Π+
ΠΠ° ΠΊΠ°ΡΠΎΠ΄Π½ΡΡ
ΡΡΠ°ΡΡΠΊΠ°Ρ
:
Zn(OH)4 β Zn2+ + 40H-,
Zn2+ + 2e β Zn,
2Π+ + 2e β 2H β H2.
ΠΡΠ»Π΅Π΄ΡΡΠ²ΠΈΠ΅ Π²ΡΡΠΎΠΊΠΎΠ³ΠΎ ΠΏΠ΅ΡΠ΅Π½Π°ΠΏΡΡΠΆΠ΅Π½ΠΈΡ Π²ΠΎΠ΄ΠΎΡΠΎΠ΄Π° Π½Π° ΡΠΈΠ½ΠΊΠ΅ ΠΏΠΎΡΠ»Π΅Π΄Π½ΡΡ ΡΠ΅Π°ΠΊΡΠΈΡ Π·Π°ΡΡΡΠ΄Π½Π΅Π½Π° ΠΈ ΠΎΠ±ΡΠ°Π·ΠΎΠ²Π°Π½ΠΈΠ΅ ΡΠΈΠ½ΠΊΠΎΠ²ΠΎΠΉ ΠΏΠ»Π΅Π½ΠΊΠΈ Π½Π° ΠΏΠΎΠ²Π΅ΡΡ Π½ΠΎΡΡΠΈ Π°Π»ΡΠΌΠΈΠ½ΠΈΠ΅Π²ΡΡ ΠΈΠ·Π΄Π΅Π»ΠΈΠΉ Π½Π΅ ΡΠΎΠΏΡΠΎΠ²ΠΎΠΆΠ΄Π°Π΅ΡΡΡ Π·Π°ΠΌΠ΅ΡΠ½ΡΠΌ Π²ΡΠ΄Π΅Π»Π΅Π½ΠΈΠ΅ΠΌ Π²ΠΎΠ΄ΠΎΡΠΎΠ΄Π°.
Π§Π΅ΠΌ ΡΠΎΠ½ΡΡΠ΅ ΠΈ ΠΏΠ»ΠΎΡΠ½Π΅Π΅ ΡΠΈΠ½ΠΊΠΎΠ²Π°Ρ ΠΏΠ»Π΅Π½ΠΊΠ°, ΡΠ΅ΠΌ Π±ΠΎΠ»ΡΡΠ΅ ΠΏΡΠΎΡΠ½ΠΎΡΡΡ ΡΡΠ΅ΠΏΠ»Π΅Π½ΠΈΡ Π°Π»ΡΠΌΠΈΠ½ΠΈΠ΅Π²ΠΎΠΉ ΠΎΡΠ½ΠΎΠ²Ρ Ρ Π³Π°Π»ΡΠ²Π°Π½ΠΈΡΠ΅ΡΠΊΠΈΠΌ ΠΏΠΎΠΊΡΡΡΠΈΠ΅ΠΌ. ΠΠΎΠ»ΡΡΠ΅Π½ΠΈΡ ΠΏΠ»ΠΎΡΠ½ΠΎΠΉ ΠΏΠ»Π΅Π½ΠΊΠΈ ΡΠΏΠΎΡΠΎΠ±ΡΡΠ²ΡΠ΅Ρ Π²Π²Π΅Π΄Π΅Π½ΠΈΠ΅ Π² ΡΠΈΠ½ΠΊΠ°ΡΠ½ΡΠΉ ΡΠ°ΡΡΠ²ΠΎΡ, ΠΏΠΎΠΌΠΈΠΌΠΎ ΠΎΡΠ½ΠΎΠ²Π½ΡΡ ΠΊΠΎΠΌΠΏΠΎΠ½Π΅Π½ΡΠΎΠ² (ΠΎΠΊΠΈΡΠΈ ΡΠΈΠ½ΠΊΠ° ΠΈ Π΅Π΄ΠΊΠΎΠ³ΠΎ Π½Π°ΡΡΠ°), Ρ Π»ΠΎΡΠ½ΠΎΠ³ΠΎ ΠΆΠ΅Π»Π΅Π·Π° ΠΈ ΡΠ΅Π³Π½Π΅ΡΠΎΠ²ΠΎΠΉ ΡΠΎΠ»ΠΈ, Π° ΡΠ°ΠΊΠΆΠ΅ Π°Π·ΠΎΡΠ½ΠΎΠΊΠΈΡΠ»ΠΎΠ³ΠΎ Π½Π°ΡΡΠΈΡ. ΠΠΈΠΆΠ΅ ΠΏΡΠΈΠ²ΠΎΠ΄ΡΡΡΡ ΡΠ΅ΠΊΠΎΠΌΠ΅Π½Π΄ΡΠ΅ΠΌΡΠ΅ ΡΠΎΡΡΠ°Π²Ρ ΡΠΈΠ½ΠΊΠ°ΡΠ½ΡΡ ΡΠ°ΡΡΠ²ΠΎΡΠΎΠ² (Π³/Π») ΠΈ ΠΈΡ ΡΠ΅ΠΆΠΈΠΌΡ:
ΠΠ²ΡΠΊΡΠ°ΡΠ½ΠΎΠ΅ ΡΠΈΠ½ΠΊΠΎΠ²Π°Π½ΠΈΠ΅ ΠΌΠ΅ΡΠΎΠ΄ΠΎΠΌ ΠΏΠΎΠ³ΡΡΠΆΠ΅Π½ΠΈΡ ΡΠ°ΡΡΠΎ ΠΎΠ±Π΅ΡΠΏΠ΅ΡΠΈΠ²Π°Π΅Ρ Π»ΡΡΡΠ΅Π΅ ΡΡΠ΅ΠΏΠ»Π΅Π½ΠΈΠ΅ ΠΌΠ΅ΠΆΠ΄Ρ Π°Π»ΡΠΌΠΈΠ½ΠΈΠ΅Π²ΠΎΠΉ ΠΎΡΠ½ΠΎΠ²ΠΎΠΉ ΠΈ Π³Π°Π»ΡΠ²Π°Π½ΠΈΡΠ΅ΡΠΊΠΈΠΌ ΠΏΠΎΠΊΡΡΡΠΈΠ΅ΠΌ. ΠΠΎΡΠ»Π΅ 10β15-ΡΠ΅ΠΊ Π²ΡΠ΄Π΅ΡΠΆΠΊΠΈ Π² ΡΠΈΠ½ΠΊΠ°ΡΠ½ΠΎΠΌ ΡΠ°ΡΡΠ²ΠΎΡΠ΅ ΠΈΠ·Π΄Π΅Π»ΠΈΡ ΠΏΡΠΎΠΌΡΠ²Π°ΡΡ Π² Π²ΠΎΠ΄Π΅ ΠΈ ΠΏΠ΅ΡΠ΅Π½ΠΎΡΡΡ Π² ΡΠ°ΡΡΠ²ΠΎΡ Π°Π·ΠΎΡΠ½ΠΎΠΉ ΠΊΠΈΡΠ»ΠΎΡΡ, ΡΠ°Π·Π±Π°Π²Π»Π΅Π½Π½ΠΎΠΉ Π²ΠΎΠ΄ΠΎΠΉ Π² ΠΎΡΠ½ΠΎΡΠ΅Π½ΠΈΠΈ 1 : 1 Π΄Π»Ρ ΡΠ΄Π°Π»Π΅Π½ΠΈΡ ΡΠΈΠ½ΠΊΠΎΠ²ΠΎΠ³ΠΎ ΠΏΠΎΠΊΡΡΡΠΈΡ. ΠΠΎΡΠ»Π΅ ΡΡΠ°ΡΠ΅Π»ΡΠ½ΠΎΠΉ ΠΏΡΠΎΠΌΡΠ²ΠΊΠΈ Π² Π²ΠΎΠ΄Π΅ ΠΈΠ·Π΄Π΅Π»ΠΈΡ Π²Π½ΠΎΠ²Ρ ΠΏΠΎΠ³ΡΡΠΆΠ°ΡΡ Π² ΡΠΈΠ½ΠΊΠ°ΡΠ½ΡΠΉ ΡΠ°ΡΡΠ²ΠΎΡ.
ΠΠΈΠΆΠ΅ ΠΏΡΠΈΠ²Π΅Π΄Π΅Π½Π° ΡΡ Π΅ΠΌΠ° ΠΏΡΠΎΡΠ΅ΡΡΠ° Π½Π°Π½Π΅ΡΠ΅Π½ΠΈΡ Π³Π°Π»ΡΠ²Π°Π½ΠΈΡΠ΅ΡΠΊΠΈΡ ΠΏΠΎΠΊΡΡΡΠΈΠΉ Π½Π° Π°Π»ΡΠΌΠΈΠ½ΠΈΠ΅Π²ΡΠ΅ ΡΠΏΠ»Π°Π²Ρ ΠΏΡΠΈ ΠΏΠΎΠ΄Π³ΠΎΡΠΎΠ²ΠΊΠ΅ ΠΈΡ ΠΏΠΎΠ²Π΅ΡΡ Π½ΠΎΡΡΠΈ ΠΏΠΎ ΡΠΈΠ½ΠΊΠ°ΡΠ½ΠΎΠΌΡ ΡΠΏΠΎΡΠΎΠ±Ρ:
ΠΠ»Ρ ΠΏΠΎΠ΄Π³ΠΎΡΠΎΠ²ΠΊΠΈ ΠΏΠΎΠ²Π΅ΡΡ
Π½ΠΎΡΡΠΈ Π°Π»ΡΠΌΠΈΠ½ΠΈΠ΅Π²ΡΡ
ΡΠΏΠ»Π°Π²ΠΎΠ², Π»Π΅Π³ΠΈΡΠΎΠ²Π°Π½Π½ΡΡ
ΠΌΠ°Π³Π½ΠΈΠ΅ΠΌ, ΠΊ Π½Π°Π½Π΅ΡΠ΅Π½ΠΈΡ Π³Π°Π»ΡΠ²Π°Π½ΠΈΡΠ΅ΡΠΊΠΈΡ
ΠΏΠΎΠΊΡΡΡΠΈΠΉ ΡΠ΅ΠΊΠΎΠΌΠ΅Π½Π΄ΡΠ΅ΡΡΡ ΠΏΠΎΠ³ΡΡΠΆΠ°ΡΡ ΠΈΡ
Π² ΡΠ°ΡΡΠ²ΠΎΡ ΡΡΠ»ΡΡΠ°ΡΠ° ΡΠΈΠ½ΠΊΠ° Π² ΠΏΡΠΈΡΡΡΡΡΠ²ΠΈΠΈ ΡΡΠΎΡΠΈΡΡΠΎΠ²ΠΎΠ΄ΠΎΡΠΎΠ΄Π½ΠΎΠΉ ΠΊΠΈΡΠ»ΠΎΡΡ ΠΈΠ»ΠΈ Π² ΡΠ°ΡΡΠ²ΠΎΡ ΡΡΠΎΡΠ±ΠΎΡΠ°ΡΠ° ΡΠΈΠ½ΠΊΠ°. ΠΠΈΠΆΠ΅ ΠΏΡΠΈΠ²ΠΎΠ΄ΡΡΡΡ ΡΠΎΡΡΠ°Π²Ρ ΡΡΠΈΡ
ΡΠ°ΡΡΠ²ΠΎΡΠΎΠ² (Π³/Π») ΠΈ ΡΠ΅ΠΆΠΈΠΌΡ:
1)Β Β Β Β Β Β ZnSO4Β·7H2O …………….720
HF (48%-Π½Π°Ρ), % (ΠΎΠ±ΡΠ΅ΠΌΠ½.) . .Β Β Β Β 3,5
Π’Π΅ΠΌΠΏΠ΅ΡΠ°ΡΡΡΠ°, Β°Π‘…………..50
ΠΡΠΎΠ΄ΠΎΠ»ΠΆΠΈΡΠ΅Π»ΡΠ½ΠΎΡΡΡ, Ρ . . . .Β Β Β Β Β Β Β 20β60
2)Β Β Β Β Β Β Zn(BF4)2………………75
ΡΠ……………………..3,0
ΠΡΠΎΠ΄ΠΎΠ»ΠΆΠΈΡΠ΅Π»ΡΠ½ΠΎΡΡΡ, Ρ……….30
ΠΠ½ΠΎΠ΄ΠΈΡΠΎΠ²Π°Π½ΠΈΠ΅ Π² ΡΠΎΡΡΠΎΡΠ½ΠΎΠΉ ΠΊΠΈΡΠ»ΠΎΡΠ΅ ΠΏΡΠΈΠΌΠ΅Π½ΡΡΡ Π² Π‘Π¨Π Π΄Π»Ρ Π°Π»ΡΠΌΠΈΠ½ΠΈΠ΅Π²ΡΡ ΡΠΏΠ»Π°Π²ΠΎΠ², Π»Π΅Π³ΠΈΡΠΎΠ²Π°Π½Π½ΡΡ ΠΌΠ΅Π΄ΡΡ ΠΈ ΠΌΠ°ΡΠ³Π°Π½ΡΠ΅ΠΌ ΠΏΠ΅ΡΠ΅Π΄ Π³Π°Π»ΡΠ²Π°Π½ΠΈΡΠ΅ΡΠΊΠΈΠΌ ΠΌΠ΅Π΄Π½Π΅Π½ΠΈΠ΅ΠΌ. ΠΠ±ΡΠ°Π·ΡΡΡΠ°ΡΡΡ ΠΏΡΠΈ Π°Π½ΠΎΠ΄ΠΈΡΠΎΠ²Π°Π½ΠΈΠΈ Π² ΡΠΎΡΡΠΎΡΠ½ΠΎΠΉ ΠΊΠΈΡΠ»ΠΎΡΠ΅ ΠΎΠΊΠΈΡΠ½Π°Ρ ΠΏΠ»Π΅Π½ΠΊΠ° Π±ΠΎΠ»Π΅Π΅ ΡΠΎΠ½ΠΊΠ° ΠΈ Π±ΠΎΠ»Π΅Π΅ ΠΏΠΎΡΠΈΡΡΠ°, ΡΠ΅ΠΌ ΠΏΡΠΈ Π°Π½ΠΎΠ΄ΠΈΡΠΎΠ²Π°Π½ΠΈΠΈ Π² ΡΠ΅ΡΠ½ΠΎΠΉ ΠΊΠΈΡΠ»ΠΎΡΠ΅, Π½ΠΎ ΡΠ° ΡΠ°ΡΡΡ ΠΏΠ»Π΅Π½ΠΊΠΈ, ΠΊΠΎΡΠΎΡΠ°Ρ ΠΎΠ±ΡΠ°ΡΠ΅Π½Π° ΠΊ Π°Π»ΡΠΌΠΈΠ½ΠΈΠ΅Π²ΠΎΠΌΡ ΡΠΏΠ»Π°Π²Ρ (ΡΠ°ΠΊ Π½Π°Π·ΡΠ²Π°Π΅ΠΌΡΠΉ Π±Π°ΡΡΠ΅ΡΠ½ΡΠΉ ΡΠ»ΠΎΠΉ), ΡΠΎΠ»ΡΠ΅, ΡΠ΅ΠΌ Π² ΡΠ΅ΡΠ½ΠΎΠΉ ΠΊΠΈΡΠ»ΠΎΡΠ΅. ΠΠΎΡΡΠΎΠΌΡ Π°Π½ΠΎΠ΄ΠΈΡΠΎΠ²Π°Π½ΠΈΠ΅ Π² ΡΠΎΡΡΠΎΡΠ½ΠΎΠΉ ΠΊΠΈΡΠ»ΠΎΡΠ΅ ΠΏΡΠΎΠ²ΠΎΠ΄ΡΡ ΠΏΡΠΈ ΠΏΠΎΠ²ΡΡΠ΅Π½Π½ΠΎΠΌ Π½Π°ΠΏΡΡΠΆΠ΅Π½ΠΈΠΈ (30β60 Π).
ΠΠΎΠ½ΡΠ΅Π½ΡΡΠ°ΡΠΈΡ ΡΠΎΡΡΠΎΡΠ½ΠΎΠΉ ΠΊΠΈΡΠ»ΠΎΡΡ ΠΊΠΎΠ»Π΅Π±Π»Π΅ΡΡΡ Π² ΠΏΡΠ΅Π΄Π΅Π»Π°Ρ 250β500 Π³/Π», ΡΠ΅ΠΌΠΏΠ΅ΡΠ°ΡΡΡΠ° 25β30Β° Π‘, ΠΏΠ»ΠΎΡΠ½ΠΎΡΡΡ ΡΠΎΠΊΠ° 1,0β2,0 Π/Π΄ΠΌ2, ΠΏΡΠΎΠ΄ΠΎΠ»ΠΆΠΈΡΠ΅Π»ΡΠ½ΠΎΡΡΡ Π°Π½ΠΎΠ΄ΠΈΡΠΎΠ²Π°Π½ΠΈΡ ΠΎΠΊΠΎΠ»ΠΎ 10 ΠΌΠΈΠ½, ΡΠΎΠ»ΡΠΈΠ½Π° ΠΎΠΊΠΈΡΠ½ΠΎΠΉ ΠΏΠ»Π΅Π½ΠΊΠΈ ΠΏΡΠΈΠΌΠ΅ΡΠ½ΠΎ 3 ΠΌΠΊΠΌ.
ΠΡΠΈ Π°Π½ΠΎΠ΄ΠΈΡΠΎΠ²Π°Π½ΠΈΠΈ Π² ΡΠΎΡΡΠΎΡΠ½ΠΎΠΉ ΠΊΠΈΡΠ»ΠΎΡΠ΅ Π²ΡΡΡΠ΅ΡΠ°Π΅ΡΡΡ ΡΠ΅ΠΌ Π±ΠΎΠ»ΡΡΠ΅ Π·Π°ΡΡΡΠ΄Π½Π΅Π½ΠΈΠΉ, ΡΠ΅ΠΌ ΡΠΈΡΠ΅ Π°Π»ΡΠΌΠΈΠ½ΠΈΠΉ: Π΄Π»Ρ Π½Π΅Π»Π΅Π³ΠΈΡΠΎΠ²Π°Π½Π½ΠΎΠ³ΠΎ Π°Π»ΡΠΌΠΈΠ½ΠΈΡ ΡΡΡΠ΄Π½ΠΎ ΠΎΠ±Π΅ΡΠΏΠ΅ΡΠΈΡΡ Ρ ΠΎΡΠΎΡΠ΅Π΅ ΡΡΠ΅ΠΏΠ»Π΅Π½ΠΈΠ΅ Ρ Π³Π°Π»ΡΠ²Π°Π½ΠΈΡΠ΅ΡΠΊΠΈΠΌ ΠΏΠΎΠΊΡΡΡΠΈΠ΅ΠΌ.
Π Π΅ΠΊΠΎΠΌΠ΅Π½Π΄ΡΠ΅ΡΡΡ ΠΏΠ΅ΡΠ²ΡΠ΅ ΡΠ»ΠΎΠΈ ΠΌΠ΅Π΄ΠΈ ΠΎΡΠ°Π΄ΠΈΡΡ Π² ΠΏΠΈΡΠΎΡΠΎΡΡΠ°ΡΠ½ΠΎΠΌ ΡΠ»Π΅ΠΊΡΡΠΎΠ»ΠΈΡΠ΅ ΠΏΡΠΈ Π·Π½Π°ΡΠ΅Π½ΠΈΡΡ ΡΠ = 7Γ·8 (ΡΠΈΡ. 122).
Π ΠΈΡ. 122. ΠΠΈΠΊΡΠΎΡΠΎΡΠΎΠ³ΡΠ°ΡΠΈΡ Π°Π»ΡΠΌΠΈΠ½ΠΈΠ΅Π²ΠΎΠ³ΠΎ ΠΎΠ±ΡΠ°Π·ΡΠ°, ΠΏΠΎΠ΄Π²Π΅ΡΠ³Π½ΡΡΠΎΠ³ΠΎ Π°Π½ΠΎΠ΄ΠΈΡΠΎΠ²Π°Π½ΠΈΡ Π² ΡΠΎΡΡΠΎΡΠ½ΠΎΠΉ ΠΊΠΈΡΠ»ΠΎΡΠ΅ ΠΈ ΠΏΠΎΡΠ»Π΅Π΄ΡΡΡΠ΅ΠΌΡ ΠΌΠ΅Π΄Π½Π΅Π½ΠΈΡ ΠΈ Π½ΠΈΠΊΠ΅Π»ΠΈΡΠΎΠ²Π°Π½ΠΈΡ
ΠΠ΅ΡΠ°Π»Π» Π½Π° ΠΎΠΊΡΠΈΠ΄ΠΈΡΠΎΠ²Π°Π½Π½ΠΎΠΌ Π² ΡΠΎΡΡΠΎΡΠ½ΠΎΠΉ ΠΊΠΈΡΠ»ΠΎΡΠ΅ Π°Π»ΡΠΌΠΈΠ½ΠΈΠΈ Π½Π°ΡΠΈΠ½Π°Π΅Ρ ΠΎΡΠ°ΠΆΠ΄Π°ΡΡΡΡ Π² ΠΏΠΎΡΠ°Ρ Π² Π²ΠΈΠ΄Π΅ ΡΠΎΠ½ΠΊΠΎΠ΄ΠΈΡΠΏΠ΅ΡΡΠ½ΡΡ Π²ΠΎΠ»ΠΎΠΊΠΎΠ½, ΠΊΠΎΡΠΎΡΡΠ΅ ΠΏΠΎΡΠΎΠΌ ΡΡΠ°ΡΡΠ°ΡΡΡΡ ΠΌΠ΅ΠΆΠ΄Ρ ΡΠΎΠ±ΠΎΠΉ, ΠΏΠ΅ΡΠ΅Π±ΡΠ°ΡΡΠ²Π°Ρ ΠΌΠΎΡΡΠΊΠΈ ΡΡΠ΅Π· ΠΏΠ»Π΅Π½ΠΊΡ. Π’ΠΎ ΠΎΠ±ΡΡΠΎΡΡΠ΅Π»ΡΡΡΠ²ΠΎ, ΡΡΠΎ ΡΠ°ΠΌΠ° ΠΎΠΊΠΈΡΠ½Π°Ρ ΠΏΠ»Π΅Π½ΠΊΠ° ΠΏΡΠΎΡΠ½ΠΎ ΡΡΠ΅ΠΏΠ»Π΅Π½Π° Ρ ΠΎΡΠ½ΠΎΠ²ΠΎΠΉ, ΠΎΠ±Π΅ΡΠΏΠ΅ΡΠΈΠ²Π°Π΅Ρ ΡΠ°ΠΊΠΆΠ΅ ΠΏΡΠΎΡΠ½ΠΎΠ΅ ΡΡΠ΅ΠΏΠ»Π΅Π½ΠΈΠ΅ Ρ Π³Π°Π»ΡΠ²Π°Π½ΠΈΡΠ΅ΡΠΊΠΈΠΌ ΠΏΠΎΠΊΡΡΡΠΈΠ΅ΠΌ.
Π ΠΠ½Π³Π»ΠΈΠΈ ΠΈ Π‘Π¨Π ΡΠΈΡΠΎΠΊΠΎ ΠΏΡΠΈΠΌΠ΅Π½ΡΡΡ ΡΠ°ΠΊ Π½Π°Π·ΡΠ²Π°Π΅ΠΌΡΠΉ ΡΠΎΠ³Ρ-ΠΏΡΠΎΡΠ΅ΡΡ, Π·Π°ΠΊΠ»ΡΡΠ°ΡΡΠΈΠΉΡΡ Π² ΠΏΡΠ΅Π΄Π²Π°ΡΠΈΡΠ΅Π»ΡΠ½ΠΎΠΌ Π½Π°Π½Π΅ΡΠ΅Π½ΠΈΠΈ Π½Π° Π°Π»ΡΠΌΠΈΠ½ΠΈΠ΅Π²ΡΠ΅ ΠΈΠ·Π΄Π΅Π»ΠΈΡ ΡΠΎΠ½ΡΠ°ΠΉΡΠΈΡ ΡΠΈΠ½ΠΊΠΎΠ²ΡΡ ΠΈ Π»Π°ΡΡΠ½Π½ΡΡ ΠΏΠΎΠΊΡΡΡΠΈΠΉ. ΠΠΈΠΆΠ΅ ΠΏΡΠΈΠ²ΠΎΠ΄ΡΡΡΡ ΡΠΎΡΡΠ°Π²Ρ ΡΠ»Π΅ΠΊΡΡΠΎΠ»ΠΈΡΠΎΠ² (Π³/Π») ΠΈ ΠΈΡ ΡΠ΅ΠΆΠΈΠΌΡ Π΄Π»Ρ Π²Π°Π½Π½ ΡΠΈΠ½ΠΊΠΎΠ²Π°Π½ΠΈΡ (I) ΠΈ Π»Π°ΡΡΠ½ΠΈΡΠΎΠ²Π°Π½ΠΈΡ (II):
ΠΠΎ ΡΡΠΎΠΉ ΡΡ Π΅ΠΌΠ΅ ΠΎΠ±Π΅Π·ΠΆΠΈΡΠ΅Π½Π½ΡΠ΅ ΠΈΠ·Π΄Π΅Π»ΠΈΡ ΠΏΠΎΡΠ»Π΅ ΠΏΡΠΎΠΌΡΠ²ΠΊΠΈ ΡΡΠ°Π²ΡΡ Π² ΡΠ΅ΡΠ΅Π½ΠΈΠ΅ 5 Ρ Π² 5%-Π½ΠΎΠΉ HF ΠΈ ΠΎΡΠ²Π΅ΡΠ»ΡΡΡ Π² HNO3 (1 : 1). ΠΠΎΡΠ»Π΅ ΡΡΠ°ΡΠ΅Π»ΡΠ½ΠΎΠΉ ΠΏΡΠΎΠΌΡΠ²ΠΊΠΈ ΠΈΠ·Π΄Π΅Π»ΠΈΡ ΠΏΠΎΠ΄Π²Π΅ΡΠ³Π°ΡΡ Π³Π°Π»ΡΠ²Π°Π½ΠΈΡΠ΅ΡΠΊΠΎΠΌΡ ΠΏΠΎΠΊΡΡΡΠΈΡ Ρ ΠΌΠΈΠ½ΠΈΠΌΠ°Π»ΡΠ½ΡΠΌΠΈ ΠΏΠ΅ΡΠ΅ΡΡΠ²Π°ΠΌΠΈ ΠΌΠ΅ΠΆΠ΄Ρ ΠΎΠΏΠ΅ΡΠ°ΡΠΈΡΠΌΠΈ ΠΏΠΎ ΡΡ Π΅ΠΌΠ΅: ΡΠΈΠ½ΠΊΠΎΠ²Π°Π½ΠΈΠ΅ β ΠΏΡΠΎΠΌΡΠ²ΠΊΠ° Π² ΠΏΡΠΎΡΠΎΡΠ½ΠΎΠΉ Π²ΠΎΠ΄Π΅ β Π»Π°ΡΡΠ½ΠΈΡΠΎΠ²Π°Π½ΠΈΠ΅ β ΠΏΡΠΎΠΌΡΠ²ΠΊΠ° β Β Π½Π΅ΠΉΡΡΠ°Π»ΠΈΠ·Π°ΡΠΈΡ Π² ΡΠ»Π°Π±ΠΎΠΌ ΡΠ°ΡΡΠ²ΠΎΡΠ΅ Π²ΠΈΠ½Π½ΠΎΠΉ ΠΊΠΈΡΠ»ΠΎΡΡ β Π½ΠΈΠΊΠ΅Π»ΠΈΡΠΎΠ²Π°Π½ΠΈΠ΅ (Π² ΡΠ»Π΅ΠΊΡΡΠΎΠ»ΠΈΡΠ΅ Π±Π΅Π· Ρ Π»ΠΎΡΠΈΠ΄ΠΎΠ²) β ΠΏΡΠΎΠΌΡΠ²ΠΊΠ° Π² Ρ ΠΎΠ»ΠΎΠ΄Π½ΠΎΠΉ ΠΈ Π³ΠΎΡΡΡΠ΅ΠΉ Π²ΠΎΠ΄Π΅ β Π΄Π΅ΠΌΠΎΠ½ΡΠ°ΠΆ Ρ ΠΏΠΎΠ΄Π²Π΅ΡΠΎΠΊ β Π½Π°Π³ΡΠ΅Π² ΠΏΡΠΈ 200β250Β° Π‘ Π² ΡΠ΅ΡΠ΅Π½ΠΈΠ΅ 30 ΠΌΠΈΠ½.
ΠΡΠΈ Π½Π°Π½Π΅ΡΠ΅Π½ΠΈΠΈ Π³Π°Π»ΡΠ²Π°Π½ΠΈΡΠ΅ΡΠΊΠΈΡ
ΠΏΠΎΠΊΡΡΡΠΈΠΉ Π½Π° ΠΏΠΎΠ΄Π³ΠΎΡΠΎΠ²Π»Π΅Π½Π½ΡΠ΅ ΠΏΠΎ ΠΎΠ΄Π½ΠΎΠΌΡ ΠΈΠ· ΠΏΠ΅ΡΠ΅ΡΠΈΡΠ»Π΅Π½Π½ΡΡ
Π²ΡΡΠ΅ ΠΌΠ΅ΡΠΎΠ΄ΠΎΠ² Π°Π»ΡΠΌΠΈΠ½ΠΈΠ΅Π²ΡΠ΅ ΠΈΠ·Π΄Π΅Π»ΠΈΡ ΡΡΠ΅Π±ΡΠ΅ΡΡΡ ΡΠΎΠ±Π»ΡΠ΄Π°ΡΡ ΠΎΡΠΎΠ±ΡΠ΅ ΠΌΠ΅ΡΡ ΠΏΡΠ΅Π΄ΠΎΡΡΠΎΡΠΎΠΆΠ½ΠΎΡΡΠΈ. ΠΠ΅Π»ΠΎ Π² ΡΠΎΠΌ, ΡΡΠΎ ΡΠΈΠ½ΠΊΠΎΠ²Π°Ρ ΠΏΠ»Π΅Π½ΠΊΠ°, ΠΏΠΎΠ»ΡΡΠ΅Π½Π½Π°Ρ ΠΏΡΠΈ ΠΏΠΎΠ³ΡΡΠΆΠ΅Π½ΠΈΠΈ Π² ΡΠ°ΡΡΠ²ΠΎΡ ΡΠΈΠ½ΠΊΠ°ΡΠ°, ΡΠ°ΠΊ ΠΆΠ΅, ΠΊΠ°ΠΊ ΠΈ ΡΠΈΠ½ΠΊΠΎΠ²ΡΠ΅ ΠΈ Π»Π°ΡΡΠ½Π½ΡΠ΅ ΠΏΠ»Π΅Π½ΠΊΠΈ, ΠΏΠΎΠ»ΡΡΠ΅Π½Π½ΡΠ΅ ΠΌΠ΅ΡΠΎΠ΄ΠΎΠΌ ΡΠ»Π΅ΠΊΡΡΠΎΠΎΡΠ°ΠΆΠ΄Π΅Π½ΠΈΡ, ΡΡΠ΅Π·Π²ΡΡΠ°ΠΉΠ½ΠΎ ΡΠΎΠ½ΠΊΠΈ ΠΈ Π½Π° Π½ΠΈΡ
Π½Π΅ΠΎΠ±Ρ
ΠΎΠ΄ΠΈΠΌΠΎ Π½Π°Π½ΠΎΡΠΈΡΡ ΠΏΠ΅ΡΠ²ΡΠΉ ΡΠ»ΠΎΠΉ ΠΌΠ΅ΡΠ°Π»Π»Π° ΠΈΠ· ΡΠ°ΠΊΠΎΠ³ΠΎ ΡΠ»Π΅ΠΊΡΡΠΎΠ»ΠΈΡΠ° ΠΈ ΠΏΡΠΈ ΡΠ°ΠΊΠΎΠΌ ΡΠ΅ΠΆΠΈΠΌΠ΅, ΡΡΠΎΠ±Ρ ΠΈΡ
Π½Π΅ ΠΏΠΎΠ²ΡΠ΅Π΄ΠΈΡΡ. Π Π·Π°ΡΡΠ±Π΅ΠΆΠ½ΠΎΠΉ Π»ΠΈΡΠ΅ΡΠ°ΡΡΡΠ΅ ΡΠ΅ΠΊΠΎΠΌΠ΅Π½Π΄ΡΠ΅ΡΡΡ Π½Π° ΠΏΠΎΠ΄Π³ΠΎΡΠΎΠ²Π»Π΅Π½Π½ΡΠ΅ ΠΏΠΎ ΡΠΈΠ½ΠΊΠ°ΡΠ½ΠΎΠΌΡ ΠΌΠ΅ΡΠΎΠ΄Ρ ΠΈΠ·Π΄Π΅Π»ΠΈΡ Π½Π°Π½ΠΎΡΠΈΡΡ 1-ΠΉ ΡΠ»ΠΎΠΉ ΠΌΠ΅Π΄ΠΈ ΠΈΠ· ΡΠΈΠ°Π½ΠΈΡΡΠΎΠ³ΠΎ ΡΠ»Π΅ΠΊΡΡΠΎΠ»ΠΈΡΠ° Ρ Π½Π΅Π±ΠΎΠ»ΡΡΠΈΠΌ ΡΠΎΠ΄Π΅ΡΠΆΠ°Π½ΠΈΠ΅ΠΌ ΡΠ²ΠΎΠ±ΠΎΠ΄Π½ΠΎΠ³ΠΎ ΡΠΈΠ°Π½ΠΈΠ΄Π°. ΠΠΈΠΆΠ΅ ΠΏΡΠΈΠ²ΠΎΠ΄ΠΈΡΡΡ ΡΠΎΡΡΠ°Π² ΡΠ°ΠΊΠΎΠ³ΠΎ ΡΠ»Π΅ΠΊΡΡΠΎΠ»ΠΈΡΠ° (Π³/Π»):
CuCN….. 42Β Β Na2CO3 …. 30,0
NaCNΠΎΠ±Ρ … 49Β Β Β Β Β Β KNaC4H4O6Β·4H2O . 60,0
NaCNΡΠ²ΠΎΠ± . . . ΠΠΎ 3,8
Π’Π΅ΠΌΠΏΠ΅ΡΠ°ΡΡΡΠ° ΡΠ»Π΅ΠΊΡΡΠΎΠ»ΠΈΡΠ° Π² ΠΏΡΠ΅Π΄Π΅Π»Π°Ρ
38β43Β° Π‘, ΡΠ= = 10,2Γ·10,5.
ΠΠ·Π΄Π΅Π»ΠΈΡ Π·Π°Π²Π΅ΡΠΈΠ²Π°ΡΡ Π² Π²Π°Π½Π½Ρ ΠΏΠΎΠ΄ ΡΠΎΠΊΠΎΠΌ ΠΈ Π² ΡΠ΅ΡΠ΅Π½ΠΈΠ΅ 2 ΠΌΠΈΠ½ ΠΏΠΎΠ΄Π΄Π΅ΡΠΆΠΈΠ²Π°ΡΡ ΠΏΠ»ΠΎΡΠ½ΠΎΡΡΡ ΡΠΎΠΊΠ° 2,5 Π/Π΄ΠΌ2, ΠΏΠΎΡΠ»Π΅ ΡΠ΅Π³ΠΎ Π΅Π΅ ΡΠ½ΠΈΠΆΠ°ΡΡ Π΄ΠΎ 1,25 Π/Π΄ΠΌ2, ΠΏΠΎ ΠΊΡΠ°ΠΉΠ½Π΅ΠΉ ΠΌΠ΅ΡΠ΅ Π² ΡΠ΅ΡΠ΅Π½ΠΈΠ΅ 3β5 ΠΌΠΈΠ½. Π Π΄Π°Π»ΡΠ½Π΅ΠΉΡΠ΅ΠΌ ΠΌΠΎΠΆΠ½ΠΎ ΠΏΡΠΈ ΡΡΠΎΠΌ ΡΠ΅ΠΆΠΈΠΌΠ΅ Π½Π°ΡΠ°ΡΠΈΠ²Π°ΡΡ ΡΠ»ΠΎΠΉ ΠΌΠ΅Π΄ΠΈ Π΄ΠΎ ΡΡΠ΅Π±ΡΠ΅ΠΌΠΎΠΉ ΡΠΎΠ»ΡΠΈΠ½Ρ, ΠΈΠ»ΠΈ ΠΏΠΎΡΠ»Π΅ ΠΏΡΠΎΠΌΡΠ²ΠΊΠΈ Π² Π²ΠΎΠ΄Π΅ ΠΏΠ΅ΡΠ΅Π½ΠΎΡΠΈΡΡ ΠΈΠ·Π΄Π΅Π»ΠΈΡ Π² ΠΌΠ΅Π΄Π½ΡΡ ΠΊΠΈΡΠ»ΡΡ Π²Π°Π½Π½Ρ.
ΠΡΠΈ Π·Π°ΡΠΈΡΠ½ΠΎ-Π΄Π΅ΠΊΠΎΡΠ°ΡΠΈΠ²Π½ΠΎΠΌ Ρ
ΡΠΎΠΌΠΈΡΠΎΠ²Π°Π½ΠΈΠΈ ΠΈΠ·Π΄Π΅Π»ΠΈΡ ΠΏΠΎΡΠ»Π΅ ΠΌΠ΅Π΄Π½Π΅Π½ΠΈΡ ΠΏΠΎΠΊΡΡΠ²Π°ΡΡ Π½ΠΈΠΊΠ΅Π»Π΅ΠΌ ΠΈ Ρ
ΡΠΎΠΌΠΎΠΌ ΠΏΠΎ ΠΎΠ±ΡΠ΅ΠΏΡΠΈΠ½ΡΡΠΎΠΉ ΡΠ΅Ρ
Π½ΠΎΠ»ΠΎΠ³ΠΈΠΈ β Π»ΠΈΠ±ΠΎ Ρ ΠΏΡΠΎΠΌΠ΅ΠΆΡΡΠΎΡΠ½ΠΎΠΉ ΠΏΠΎΠ»ΠΈΡΠΎΠ²ΠΊΠΎΠΉ ΡΠΎ Π²ΡΠ΅ΠΌΠΈ Π²ΡΠΏΠΎΠΌΠΎΠ³Π°ΡΠ΅Π»ΡΠ½ΡΠΌΠΈ ΠΎΠΏΠ΅ΡΠ°ΡΠΈΡΠΌΠΈ, Π»ΠΈΠ±ΠΎ Π±Π΅Π· Π½ΠΈΡ
, Π΅ΡΠ»ΠΈ ΠΏΠΎΠΊΡΡΡΠΈΠ΅ ΠΎΡΡΡΠ΅ΡΡΠ²Π»ΡΠ΅ΡΡΡ Π² Π²Π°Π½Π½Π°Ρ
Ρ Π±Π»Π΅ΡΠΊΠΎΠΎΠ±ΡΠ°Π·ΠΎΠ²Π°ΡΠ΅Π»ΡΠΌΠΈ. ΠΠΌΠ΅ΡΡΠΎ ΠΌΠ΅Π΄Π½Π΅Π½ΠΈΡ Π² ΡΠΈΠ°Π½ΠΈΡΡΠΎΠΌ ΡΠ»Π΅ΠΊΡΡΠΎΠ»ΠΈΡΠ΅ ΠΌΠΎΠΆΠ½ΠΎ ΠΏΡΠΈ Π·Π°ΡΠΈΡΠ½ΠΎ-Π΄Π΅ΠΊΠΎΡΠ°ΡΠΈΠ²Π½ΠΎΠΌ Ρ
ΡΠΎΠΌΠΈΡΠΎΠ²Π°Π½ΠΈΠΈ Π½Π°ΡΠΈΠ½Π°ΡΡ Ρ Π»Π°ΡΡΠ½ΠΈΡΠΎΠ²Π°Π½ΠΈΡ Π² ΡΠ»Π΅ΠΊΡΡΠΎΠ»ΠΈΡΠ΅ ΡΠ»Π΅Π΄ΡΡΡΠ΅Π³ΠΎ ΡΠΎΡΡΠ°Π²Π° (Π³/Π»):
CuCN …. 26
NaCN …. 45
Zn(CN)2 β¦ 11
Na2CO3 … 7,5
Π’Π΅ΠΌΠΏΠ΅ΡΠ°ΡΡΡΡ ΠΏΠΎΠ΄Π΄Π΅ΡΠΆΠΈΠ²Π°ΡΡ Π² ΠΏΡΠ΅Π΄Π΅Π»Π°Ρ
27β30Β° Π‘, ΠΏΠ»ΠΎΡΠ½ΠΎΡΡΡ ΡΠΎΠΊΠ° ΠΎΠΊΠΎΠ»ΠΎ 1 Π/Π΄ΠΌ2, Π°Π½ΠΎΠ΄Ρ β Π»Π°ΡΡΠ½Π½ΡΠ΅ Ρ ΡΠΎΠ΄Π΅ΡΠΆΠ°Π½ΠΈΠ΅ΠΌ 70β75% Cu ΠΈ 25β30% Zn.
ΠΠ°ΡΠΈΡΠ½ΠΎ-Π΄Π΅ΠΊΠΎΡΠ°ΡΠΈΠ²Π½ΠΎΠ΅ Ρ
ΡΠΎΠΌΠΈΡΠΎΠ²Π°Π½ΠΈΠ΅ ΠΏΠΎΠ΄Π³ΠΎΡΠΎΠ²Π»Π΅Π½Π½ΡΡ
ΠΏΠΎ ΡΠΈΠ½ΠΊΠ°ΡΠ½ΠΎΠΌΡ ΠΌΠ΅ΡΠΎΠ΄Ρ ΠΈΠ·Π΄Π΅Π»ΠΈΠΉ ΠΏΠΎ ΡΡ
Π΅ΠΌΠ΅ NiβCr ΠΈΠ»ΠΈ NiβCuβNiβCr ΠΌΠΎΠΆΠ½ΠΎ ΠΎΡΡΡΠ΅ΡΡΠ²Π»ΡΡΡ ΠΈ Π±Π΅Π· Π½Π°Π½Π΅ΡΠ΅Π½ΠΈΡ ΠΏΠ΅ΡΠ²ΠΎΠ³ΠΎ ΡΠ»ΠΎΡ ΠΌΠ΅Π΄ΠΈ ΠΈΠ»ΠΈ Π»Π°ΡΡΠ½ΠΈ Π² ΡΠΈΠ°Π½ΠΈΡΡΡΡ
ΡΠ»Π΅ΠΊΡΡΠΎΠ»ΠΈΡΠ°Ρ
. ΠΠ»Ρ ΡΡΠΎΠΉ ΡΠ΅Π»ΠΈ ΠΌΠΎΠΆΠ½ΠΎ ΠΏΠΎ ΡΠΈΠ½ΠΊΠΎΠ²ΠΎΠΉ ΠΏΠ»Π΅Π½ΠΊΠ΅ Π½Π°Π½ΠΎΡΠΈΡΡ Π½ΠΈΠΊΠ΅Π»Ρ ΠΈΠ· ΠΎΠ±ΡΡΠ½ΠΎΠ³ΠΎ ΡΠ»Π΅ΠΊΡΡΠΎΠ»ΠΈΡΠ°, ΠΈΠ»ΠΈ ΠΈΠ· Π±ΠΎΠ»Π΅Π΅ ΠΏΠΎΠ΄Ρ
ΠΎΠ΄ΡΡΠ΅Π³ΠΎ Π΄Π»Ρ ΡΡΠΎΠΉ ΡΠ΅Π»ΠΈ ΡΠ»Π΅ΠΊΡΡΠΎΠ»ΠΈΡΠ° ΡΠΎΡΡΠ°Π²Π° (Π³/Π»):
NiSO4Β·7H2O…….100
Na2SO4Β·10H2O…………..15
H3ΠO3………………..10
ΠΠΈΠΌΠΎΠ½Π½ΠΎΠΊΠΈΡΠ»ΡΠΉ Π½Π°ΡΡΠΈΠΉ …Β Β Β Β Β Β Β 15
Π’Π΅ΠΌΠΏΠ΅ΡΠ°ΡΡΡΠ° ΡΠ»Π΅ΠΊΡΡΠΎΠ»ΠΈΡΠ° 40β45Β° Π‘; ΠΏΠ»ΠΎΡΠ½ΠΎΡΡΡ ΡΠΎΠΊΠ° 1,5β2 Π/Π΄ΠΌ2; ΡΠ~5,6. ΠΡΠΎΡΠ½ΠΎΠ΅ ΡΡΠ΅ΠΏΠ»Π΅Π½ΠΈΠ΅ Π½ΠΈΠΊΠ΅Π»Π΅Π²ΠΎΠ³ΠΎ ΠΏΠΎΠΊΡΡΡΠΈΡ Ρ Π°Π»ΡΠΌΠΈΠ½ΠΈΠ΅Π²ΠΎΠΉ ΠΎΡΠ½ΠΎΠ²ΠΎΠΉ ΠΎΠ±Π΅ΡΠΏΠ΅ΡΠΈΠ²Π°Π΅ΡΡΡ ΡΠΎΠ»ΡΠΊΠΎ Π² ΡΠ΅Π·ΡΠ»ΡΡΠ°ΡΠ΅ 30-ΠΌΠΈΠ½ Π½Π°Π³ΡΠ΅Π²Π° ΠΏΡΠΈ ΡΠ΅ΠΌΠΏΠ΅ΡΠ°ΡΡΡΠ΅ 200β250Β° Π‘. ΠΠ»Ρ ΠΏΡΠ΅Π΄ΡΠΏΡΠ΅ΠΆΠ΄Π΅Π½ΠΈΡ ΠΎΡ ΠΎΠΊΠΈΡΠ»Π΅Π½ΠΈΡ ΠΏΠΎΠ²Π΅ΡΡ
Π½ΠΎΡΡΠΈ Π½Π°Π³ΡΠ΅Π² ΡΠ΅ΠΊΠΎΠΌΠ΅Π½Π΄ΡΠ΅ΡΡΡ ΠΎΡΡΡΠ΅ΡΡΠ²Π»ΡΡΡ Π² ΠΏΠ΅ΡΠΈ Ρ ΠΈΠ½Π΅ΡΡΠ½ΠΎΠΉ Π°ΡΠΌΠΎΡΡΠ΅ΡΠΎΠΉ Π² ΡΠ΅Ρ
Π½ΠΈΡΠ΅ΡΠΊΠΎΠΌ ΠΊΠ°ΡΡΠΎΡΠΎΠ²ΠΎΠΌ ΠΌΠ°ΡΠ»Π΅ ΠΈΠ»ΠΈ Π² Π²Π°ΠΊΡΡΠΌΠ΅. ΠΡΠ»ΠΈ ΡΠ°ΠΊΠΎΠΉ Π½Π°Π³ΡΠ΅Π² ΡΠ²ΡΠ·Π°Π½ Ρ ΡΡΡΠ΄Π½ΠΎΡΡΡΠΌΠΈ, ΡΠΎ ΠΏΠ΅ΡΠ΅Π΄ Π½Π°Π½Π΅ΡΠ΅Π½ΠΈΠ΅ΠΌ Π½Π° Π½ΠΈΠΊΠ΅Π»Ρ Π΄ΡΡΠ³ΠΈΡ
Π³Π°Π»ΡΠ²Π°Π½ΠΈΡΠ΅ΡΠΊΠΈΡ
ΠΏΠΎΠΊΡΡΡΠΈΠΉ ΡΠΎΠ½ΠΊΠΈΠΉ ΡΠ»ΠΎΠΉ ΠΎΠΊΠΈΡΠ»ΠΎΠ² ΠΌΠΎΠΆΠ΅Ρ Π±ΡΡΡ ΡΠ΄Π°Π»Π΅Π½ Π»ΠΈΠ±ΠΎ ΠΏΠΎΠ»ΠΈΡΠΎΠ²ΠΊΠΎΠΉ, Π»ΠΈΠ±ΠΎ ΡΡΠ°Π²Π»Π΅Π½ΠΈΠ΅ΠΌ Π² ΡΠΌΠ΅ΡΠΈ ΡΠ΅ΡΠ½ΠΎΠΉ ΠΈ Π°Π·ΠΎΡΠ½ΠΎΠΉ ΠΊΠΈΡΠ»ΠΎΡ. ΠΠ»Ρ Π»Π΅Π³ΠΊΠΈΡ
ΡΡΠ»ΠΎΠ²ΠΈΠΉ ΡΠΊΡΠΏΠ»ΡΠ°ΡΠ°ΡΠΈΠΈ ΠΌΠΎΠΆΠ½ΠΎ ΠΎΠ³ΡΠ°Π½ΠΈΡΠΈΡΡΡΡ ΡΠ»ΠΎΠ΅ΠΌ Π½ΠΈΠΊΠ΅Π»Ρ ΡΠΎΠ»ΡΠΈΠ½ΠΎΠΉ 10 ΠΌΠΊΠΌ Ρ ΠΏΠΎΡΠ»Π΅Π΄ΡΡΡΠΈΠΌ Ρ
ΡΠΎΠΌΠΈΡΠΎΠ²Π°Π½ΠΈΠ΅ΠΌ Π½Π° ΡΠΎΠ»ΡΠΈΠ½Ρ Π΄ΠΎ 1 ΠΌΠΊΠΌ; Π΄Π»Ρ ΠΆΠ΅ΡΡΠΊΠΈΡ
ΡΡΠ»ΠΎΠ²ΠΈΠΉ ΡΠ΅ΠΊΠΎΠΌΠ΅Π½Π΄ΡΠ΅ΡΡΡ ΡΡΠΌΠΌΠ°ΡΠ½Π°Ρ ΡΠΎΠ»ΡΠΈΠ½Π° ΠΏΠΎΠΊΡΡΡΠΈΡ Niβ CuβNi 50 ΠΌΠΊΠΌ Ρ ΡΠΎΠ½ΠΊΠΈΠΌ ΡΠ»ΠΎΠ΅ΠΌ Ρ
ΡΠΎΠΌΠ°.
ΠΠ·Π½ΠΎΡΠΎΡΡΠΎΠΉΠΊΠΎΠΌΡ Ρ ΡΠΎΠΌΠΈΡΠΎΠ²Π°Π½ΠΈΡ ΡΠ°ΡΡΠΎ ΠΏΠΎΠ΄Π²Π΅ΡΠ³Π°ΡΡ Π΄Π²ΠΈΠ³Π°ΡΠ΅Π»ΠΈ ΡΠΈΠ»ΠΈΠ½Π΄ΡΠΎΠ² (Π½Π°ΠΏΡΠΈΠΌΠ΅Ρ, ΠΌΠΎΡΠΎΡΠΈΠΊΠ»ΠΎΠ²) ΠΈΠ· ΠΊΡΠ΅ΠΌΠ½ΠΈΡΡΡΡ Π°Π»ΡΠΌΠΈΠ½ΠΈΠ΅Π²ΡΡ ΡΠΏΠ»Π°Π²ΠΎΠ². ΠΠΎΡΠ»Π΅ ΠΎΠ±Π΅Π·ΠΆΠΈΡΠΈΠ²Π°Π½ΠΈΡ Π² ΡΠ΅Π»ΠΎΡΠ½ΠΎΠΌ ΡΠ°ΡΡΠ²ΠΎΡΠ΅ ΠΈ ΠΏΡΠΎΠΌΡΠ²ΠΊΠΈ ΡΠ»Π΅Π΄ΡΠ΅Ρ 1β2-ΠΌΠΈΠ½ ΡΡΠ°Π²Π»Π΅Π½ΠΈΠ΅ ΠΏΡΠΈ ΡΠ΅ΠΌΠΏΠ΅ΡΠ°ΡΡΡΠ΅, Π½Π΅ ΠΏΡΠ΅Π²ΡΡΠ°ΡΡΠ΅ΠΉ 15Β° Π‘, Π² ΡΠΌΠ΅ΡΠΈ HF : HNO3 Π² ΠΎΡΠ½ΠΎΡΠ΅Π½ΠΈΠΈ 1 : 5. Π₯ΡΠΎΠΌΠΈΡΠΎΠ²Π°Π½ΠΈΠ΅ ΠΎΡΡΡΠ΅ΡΡΠ²Π»ΡΡΡ Π² ΠΎΠ±ΡΡΠ½ΠΎΠΌ ΡΠ»Π΅ΠΊΡΡΠΎΠ»ΠΈΡΠ΅ ΠΏΡΠΈ ΡΠ΅ΠΌΠΏΠ΅ΡΠ°ΡΡΡΠ΅ 60Β±2Β°Π‘ ΠΏΠΎ ΡΠ΅ΠΆΠΈΠΌΡ: ΠΏΠ΅ΡΠ²ΡΠ΅ 5 ΠΌΠΈΠ½ ΠΏΡΠΈ ΠΏΠ»ΠΎΡΠ½ΠΎΡΡΠΈ ΡΠΎΠΊΠ° 35β45 Π/Π΄ΠΌ2, Π²ΡΠΎΡΡΠ΅ 5 ΠΌΠΈΠ½ 45β65 Π/Π΄ΠΌ2, ΠΎΡΡΠ°Π»ΡΠ½ΠΎΠ΅ Π²ΡΠ΅ΠΌΡ 65β80 Π/Π΄ΠΌ2.
ΠΠ°Π»ΡΠ²Π°Π½ΠΈΡΠ΅ΡΠΊΠΎΠ΅ Π»ΡΠΆΠ΅Π½ΠΈΠ΅ ΠΈΠ»ΠΈ ΠΏΠΎΠΊΡΡΡΠΈΠ΅ ΡΠ²ΠΈΠ½ΡΠΎΠ²ΠΎΠΎΠ»ΠΎΠ²ΡΠ½Π½ΡΠΌ ΡΠΏΠ»Π°Π²ΠΎΠΌ (Π΄Π»Ρ ΠΎΠ±Π»Π΅Π³ΡΠ΅Π½ΠΈΡ ΠΈ ΡΡΠΊΠΎΡΠ΅Π½ΠΈΡ ΠΏΡΠΎΡΠ΅ΡΡΠ° ΠΏΠ°ΠΉΠΊΠΈ), ΠΏΠΎΠ΄Π³ΠΎΡΠΎΠ²Π»Π΅Π½Π½ΡΡ ΠΏΠΎ ΡΠΈΠ½ΠΊΠ°ΡΠ½ΠΎΠΌΡ ΠΌΠ΅ΡΠΎΠ΄Ρ ΠΈΠ·Π΄Π΅Π»ΠΈΠΉ ΠΎΡΡΡΠ΅ΡΡΠ²Π»ΡΡΡ Π² ΠΎΠ±ΡΡΠ½ΡΡ ΡΠ»Π΅ΠΊΡΡΠΎΠ»ΠΈΡΠ°Ρ ΠΏΠΎΡΠ»Π΅ Π½ΠΈΠΊΠ΅Π»ΠΈΡΠΎΠ²Π°Π½ΠΈΡ ΠΈ 30-ΠΌΠΈΠ½ ΠΏΡΠΎΠ³ΡΠ΅Π²Π° ΠΈΠ»ΠΈ ΠΏΠΎΡΠ»Π΅ ΠΌΠ΅Π΄Π½Π΅Π½ΠΈΡ Π² ΡΠΈΠ°Π½ΠΈΡΡΠΎΠΌ ΡΠ»Π΅ΠΊΡΡΠΎΠ»ΠΈΡΠ΅.
Π¦ΠΈΠ½ΠΊΠΎΠ²Π°Π½ΠΈΡ Π°Π»ΡΠΌΠΈΠ½ΠΈΠ΅Π²ΡΠ΅ ΠΈΠ·Π΄Π΅Π»ΠΈΡ ΠΏΠΎΠ΄Π²Π΅ΡΠ³Π°ΡΡ ΡΡΠ°Π²Π½ΠΈΡΠ΅Π»ΡΠ½ΠΎ ΡΠ΅Π΄ΠΊΠΎ; Π»ΡΡΡΠΈΠ΅ ΡΠ΅Π·ΡΠ»ΡΡΠ°ΡΡ ΠΏΠΎΠ»ΡΡΠ°ΡΡΡΡ ΠΏΠΎΡΠ»Π΅ ΡΠΈΠ½ΠΊΠ°ΡΠ½ΠΎΠΉ ΠΎΠ±ΡΠ°Π±ΠΎΡΠΊΠΈ ΠΈ ΡΠ»Π΅ΠΊΡΡΠΎΠ»ΠΈΡΠΈΡΠ΅ΡΠΊΠΎΠ³ΠΎ ΡΠΈΠ½ΠΊΠΎΠ²Π°Π½ΠΈΡ Π² ΡΠ΅Π»ΠΎΡΠ½ΠΎ-ΡΠΈΠ°Π½ΠΈΡΡΡΡ ΡΠ»Π΅ΠΊΡΡΠΎΠ»ΠΈΡΠ°Ρ .
ΠΠ°Π΄ΠΌΠΈΡΠΎΠ²Π°Π½ΠΈΠ΅ ΠΏΡΠΈΠΌΠ΅Π½ΡΡΡ Π΄Π»Ρ Π·Π°ΡΠΈΡΡ ΠΎΡ ΠΊΠΎΠ½ΡΠ°ΠΊΡΠ½ΠΎΠΉ ΠΊΠΎΡΡΠΎΠ·ΠΈΠΈ ΡΠ·Π»ΠΎΠ², Π² ΠΊΠΎΡΠΎΡΡΡ
Π°Π»ΡΠΌΠΈΠ½ΠΈΠ΅Π²ΡΠ΅ Π΄Π΅ΡΠ°Π»ΠΈ ΡΠΎΠΏΡΡΠ³Π°ΡΡΡΡ Ρ Π΄Π΅ΡΠ°Π»ΡΠΌΠΈ ΠΈΠ· Π΄ΡΡΠ³ΠΈΡ
ΠΌΠ΅ΡΠ°Π»Π»ΠΎΠ². ΠΡΠΎΡΠ½ΠΎΠ΅ ΡΡΠ΅ΠΏΠ»Π΅Π½ΠΈΠ΅ ΠΊΠ°Π΄ΠΌΠΈΠ΅Π²ΡΡ
ΠΏΠΎΠΊΡΡΡΠΈΠΉ Ρ Π°Π»ΡΠΌΠΈΠ½ΠΈΠ΅Π²ΠΎΠΉ ΠΎΡΠ½ΠΎΠ²ΠΎΠΉ ΠΌΠΎΠΆΠ΅Ρ Π±ΡΡΡ ΠΎΠ±Π΅ΡΠΏΠ΅ΡΠ΅Π½ΠΎ ΠΏΠΎΡΠ»Π΅ ΠΏΡΠ΅Π΄Π²Π°ΡΠΈΡΠ΅Π»ΡΠ½ΠΎΠΉ ΠΎΠ΄Π½ΠΎΠΌΠΈΠ½ΡΡΠ½ΠΎΠΉ ΠΊΠ°ΡΠΎΠ΄Π½ΠΎΠΉ ΠΏΠΎΠ»ΡΡΠΈΠ·Π°ΡΠΈΠΈ ΠΏΡΠΈ ΠΏΠ»ΠΎΡΠ½ΠΎΡΡΠΈ ΡΠΎΠΊΠ° 2,5 Π/Π΄ΠΌ2 Π² ΡΠ°Π·Π±Π°Π²Π»Π΅Π½Π½ΠΎΠΌ ΠΏΠΎ ΡΠΎΠ΄Π΅ΡΠΆΠ°Π½ΠΈΡ ΠΊΠ°Π΄ΠΌΠΈΡ ΡΠ»Π΅ΠΊΡΡΠΎΠ»ΠΈΡΠ΅ ΠΈ ΠΏΠΎΡΠ»Π΅Π΄ΡΡΡΠ΅Π³ΠΎ ΠΊΠ°Π΄ΠΌΠΈΡΠΎΠ²Π°Π½ΠΈΡ Π² ΡΠ°Π±ΠΎΡΠ΅ΠΌ ΡΠ»Π΅ΠΊΡΡΠΎΠ»ΠΈΡΠ΅ ΠΏΡΠΈ ΠΏΠ»ΠΎΡΠ½ΠΎΡΡΠΈ ΡΠΎΠΊΠ° 1,5β3 Π/Π΄ΠΌ2 Π² ΡΠ΅ΡΠ΅Π½ΠΈΠ΅ Π²ΡΠ΅ΠΌΠ΅Π½ΠΈ, Π½Π΅ΠΎΠ±Ρ
ΠΎΠ΄ΠΈΠΌΠΎΠ³ΠΎ Π΄Π»Ρ ΠΎΡΠ°ΠΆΠ΄Π΅Π½ΠΈΡ ΡΠ»ΠΎΡ ΠΊΠ°Π΄ΠΌΠΈΡ Π·Π°Π΄Π°Π½Π½ΠΎΠΉ ΡΠΎΠ»ΡΠΈΠ½Ρ. ΠΠΈΠΆΠ΅ ΠΏΡΠΈΠ²Π΅Π΄Π΅Π½Ρ ΡΠΎΡΡΠ°Π²Ρ (Π³/Π») ΡΠ΅ΠΊΠΎΠΌΠ΅Π½Π΄ΡΠ΅ΠΌΡΡ
ΡΠ»Π΅ΠΊΡΡΠΎΠ»ΠΈΡΠΎΠ² Π΄Π»Ρ ΠΏΡΠ΅Π΄Π²Π°ΡΠΈΡΠ΅Π»ΡΠ½ΠΎΠ³ΠΎ ΠΏΠΎΠΊΡΡΡΠΈΡ (I) ΠΈ ΡΠ°Π±ΠΎΡΠ΅Π³ΠΎ ΡΠ»Π΅ΠΊΡΡΠΎΠ»ΠΈΡΠ° (II):
IΒ Β Β Β Β II
Cd……… Β Β Β Β 7,5 Β Β Β Β Β Β 27
NaCN……. Β 60,0 Β Β Β Β Β 100
ΠΠΎΠΌΠΈΠΌΠΎ ΠΎΡΠ½ΠΎΠ²Π½ΡΡ
ΠΊΠΎΠΌΠΏΠΎΠ½Π΅Π½ΡΠΎΠ², Π² ΡΠ°Π±ΠΎΡΠΈΠΉ ΡΠ»Π΅ΠΊΡΡΠΎΠ»ΠΈΡ Π²Π²ΠΎΠ΄ΡΡ Π±Π»Π΅ΡΠΊΠΎΠΎΠ±ΡΠ°Π·ΠΎΠ²Π°ΡΠ΅Π»Ρ. ΠΠΎΠΆΠ½ΠΎ ΡΠ°ΠΊΠΆΠ΅ ΠΊΠ°Π΄ΠΌΠΈΡΠΎΠ²Π°ΡΡ Π°Π»ΡΠΌΠΈΠ½ΠΈΠΉ ΠΏΠΎ ΠΌΠ΅Π΄Π½ΠΎΠΌΡ ΠΈΠ»ΠΈ ΡΠΈΠ½ΠΊΠΎΠ²ΠΎΠΌΡ ΠΏΠΎΠ΄ΡΠ»ΠΎΡ ΠΏΠΎΡΠ»Π΅ ΡΠΈΠ½ΠΊΠ°ΡΠ½ΠΎΠΉ ΠΎΠ±ΡΠ°Π±ΠΎΡΠΊΠΈ.
Π‘Π΅ΡΠ΅Π±ΡΠ΅Π½ΠΈΠ΅ Π°Π»ΡΠΌΠΈΠ½ΠΈΡ ΠΎΡΡΡΠ΅ΡΡΠ²Π»ΡΡΡ Π΄Π»Ρ ΠΏΠΎΠ²ΡΡΠ΅Π½ΠΈΡ ΡΠ»Π΅ΠΊΡΡΠΎΠΏΡΠΎΠ²ΠΎΠ΄Π½ΠΎΡΡΠΈ ΠΈ, Π² ΡΠ°ΡΡΠ½ΠΎΡΡΠΈ, Π΄Π»Ρ ΡΠΌΠ΅Π½ΡΡΠ΅Π½ΠΈΡ ΠΏΠ΅ΡΠ΅Ρ
ΠΎΠ΄Π½ΠΎΠ³ΠΎ ΡΠΎΠΏΡΠΎΡΠΈΠ²Π»Π΅Π½ΠΈΡ Π² ΠΌΠ΅ΡΡΠ°Ρ
ΠΊΠΎΠ½ΡΠ°ΠΊΡΠΎΠ². ΠΠΎΡΠ»Π΅ ΡΠΈΠ½ΠΊΠ°ΡΠ½ΠΎΠΉ ΠΎΠ±ΡΠ°Π±ΠΎΡΠΊΠΈ ΠΈΠ·Π΄Π΅Π»ΠΈΡ ΡΠ΅ΡΠ΅Π±ΡΡΡ ΠΏΠΎΡΠ»Π΅Π΄ΠΎΠ²Π°ΡΠ΅Π»ΡΠ½ΠΎ Π² ΡΡΠ΅Ρ
Π²Π°Π½Π½Π°Ρ
Ρ ΠΏΠΎΡΡΠ΅ΠΏΠ΅Π½Π½ΠΎ Π²ΠΎΠ·ΡΠ°ΡΡΠ°ΡΡΠ΅ΠΉ ΠΊΠΎΠ½ΡΠ΅Π½ΡΡΠ°ΡΠΈΠ΅ΠΉ ΡΠ΅ΡΠ΅Π±ΡΠ° ΠΈ ΡΠ±ΡΠ²Π°ΡΡΠ΅ΠΉ ΠΊΠΎΠ½ΡΠ΅Π½ΡΡΠ°ΡΠΈΠ΅ΠΉ ΡΠ²ΠΎΠ±ΠΎΠ΄Π½ΠΎΠ³ΠΎ ΡΠΈΠ°Π½ΠΈΠ΄Π°. Π ΠΏΠ΅ΡΠ²ΡΡ
Π΄Π²ΡΡ
Π²Π°Π½Π½Π°Ρ
ΠΈΠ·Π΄Π΅Π»ΠΈΡ Π²ΡΠ΄Π΅ΡΠΆΠΈΠ²Π°ΡΡ ΠΏΠΎ 10β15 Ρ ΠΏΡΠΈ ΠΏΠ»ΠΎΡΠ½ΠΎΡΡΠΈ ΡΠΎΠΊΠ° 1,5β2 Π/Π΄ΠΌ2. Π ΡΡΠΈΡ
Π²Π°Π½Π½Π°Ρ
Π²ΡΡ
ΠΎΠ΄ ΠΌΠ΅ΡΠ°Π»Π»Π° ΠΏΠΎ ΡΠΎΠΊΡ Π½Π΅Π±ΠΎΠ»ΡΡΠΎΠΉ ΠΈ Π½Π°Π±Π»ΡΠ΄Π°Π΅ΡΡΡ ΠΈΠ½ΡΠ΅Π½ΡΠΈΠ²Π½ΠΎΠ΅ Π²ΡΠ΄Π΅Π»Π΅Π½ΠΈΠ΅ Π²ΠΎΠ΄ΠΎΡΠΎΠ΄Π°. Π ΡΡΠ΅ΡΡΠ΅ΠΉ Π²Π°Π½Π½Π΅ ΠΏΠΎΠ΄Π΄Π΅ΡΠΆΠΈΠ²Π°Π΅ΡΡΡ ΠΏΠ»ΠΎΡΠ½ΠΎΡΡΡ ΡΠΎΠΊΠ° 0,5 Π/Π΄ΠΌ2 ΠΈ ΠΏΡΠΎΡΠ΅ΡΡ Π΄Π»ΠΈΡΡΡ Π΄ΠΎ ΠΏΠΎΠ»ΡΡΠ΅Π½ΠΈΡ ΡΠ»ΠΎΡ ΡΠ΅ΡΠ΅Π±ΡΠ° Π·Π°Π΄Π°Π½Π½ΠΎΠΉ ΡΠΎΠ»ΡΠΈΠ½Ρ. ΠΠΈΠΆΠ΅ ΠΏΡΠΈΠ²ΠΎΠ΄ΡΡΡΡ ΡΠΎΡΡΠ°Π²Ρ ΡΠ΅ΡΠ΅Π±ΡΡΠ½ΡΡ
ΡΠ»Π΅ΠΊΡΡΠΎΠ»ΠΈΡΠΎΠ² ΡΡΠΈΡ
ΡΡΠ΅Ρ
Π²Π°Π½Π½ (Π³/Π»):
I Β Β Β II Β Β Β III
Ag CN Β Β Β 1 Β Β Β 5 Β Β Β 30
Π CN Β Β Β Β 90 Β 68 Β Β 60
ΠΠ»Ρ Π»Π΅Π³ΠΊΠΈΡ
ΡΡΠ»ΠΎΠ²ΠΈΠΉ ΡΠΊΡΠΏΠ»ΡΠ°ΡΠ°ΡΠΈΠΈ ΠΌΠΎΠΆΠ½ΠΎ ΠΎΠ³ΡΠ°Π½ΠΈΡΠΈΡΡΡΡ ΡΠΎΠ»ΡΠΈΠ½ΠΎΠΉ ΡΠ΅ΡΠ΅Π±ΡΡΠ½ΠΎΠ³ΠΎ ΡΠ»ΠΎΡ 12,5 ΠΌΠΊΠΌ, Π΄Π»Ρ ΡΡΠ΅Π΄Π½ΠΈΡ
ΡΡΠ»ΠΎΠ²ΠΈΠΉ ΡΠΊΡΠΏΠ»ΡΠ°ΡΠ°ΡΠΈΠΈ 25 ΠΌΠΊΠΌ, Π° Π΄Π»Ρ ΠΆΠ΅ΡΡΠΊΠΈΡ
ΡΡΠ»ΠΎΠ²ΠΈΠΉ 50 ΠΌΠΊΠΌ.
ΠΠΎΠΊΡΡΡΠΈΠ΅ Π΄ΡΡΠ³ΠΈΠΌΠΈ Π΄ΡΠ°Π³ΠΎΡΠ΅Π½Π½ΡΠΌΠΈ ΠΌΠ΅ΡΠ°Π»Π»Π°ΠΌΠΈ. Π Π°Π·Π»ΠΈΡΠ½ΡΠ΅ Π΄Π΅ΡΠ°Π»ΠΈ ΡΠ»Π΅ΠΊΡΡΠΎΠ½Π½ΠΎΠΉ Π°ΠΏΠΏΠ°ΡΠ°ΡΡΡΡ, Π°Π²ΡΠΎΠΌΠ°ΡΠΈΠΊΠΈ ΠΈ ΡΠ΅Π»Π΅ΠΌΠ΅Ρ
Π°Π½ΠΈΠΊΠΈ Π² Π·Π°Π²ΠΈΡΠΈΠΌΠΎΡΡΠΈ ΠΎΡ ΡΡΠ»ΠΎΠ²ΠΈΠΉ ΡΠΊΡΠΏΠ»ΡΠ°ΡΠ°ΡΠΈΠΈ ΠΏΠΎΠ΄Π²Π΅ΡΠ³Π°ΡΡ Π·ΠΎΠ»ΠΎΡΠ΅Π½ΠΈΡ ΠΈΠ»ΠΈ ΠΏΠΎΠΊΡΡΠ²Π°ΡΡ ΠΌΠ΅ΡΠ°Π»Π»Π°ΠΌΠΈ ΠΏΠ»Π°ΡΠΈΠ½ΠΎΠ²ΠΎΠΉ Π³ΡΡΠΏΠΏΡ. ΠΠΎΠ»ΠΎΡΠ΅Π½ΠΈΠ΅ ΠΎΡΡΡΠ΅ΡΡΠ²Π»ΡΡΡ ΠΏΠΎΡΠ»Π΅ ΡΠΈΠ½ΠΊΠ°ΡΠ½ΠΎΠΉ ΠΎΠ±ΡΠ°Π±ΠΎΡΠΊΠΈ ΠΈ Π½Π°Π½Π΅ΡΠ΅Π½ΠΈΡ ΠΌΠ΅Π΄Π½ΠΎΠ³ΠΎ ΠΏΠΎΠ΄ΡΠ»ΠΎΡ ΠΈΠ· ΡΠΈΠ°Π½ΠΈΡΡΠΎΠ³ΠΎ ΡΠ»Π΅ΠΊΡΡΠΎΠ»ΠΈΡΠ° ΠΈΠ»ΠΈ Π½ΠΈΠΊΠ΅Π»Π΅Π²ΠΎΠ³ΠΎ ΠΏΠΎΠ΄ΡΠ»ΠΎΡ Ρ ΠΏΠΎΡΠ»Π΅Π΄ΡΡΡΠΈΠΌ 30-ΠΌΠΈΠ½ΡΡΠ½ΡΠΌ Π½Π°Π³ΡΠ΅Π²ΠΎΠΌ. Π’ΠΎΠ»ΡΡΡΠ΅ Π·ΠΎΠ»ΠΎΡΡΠ΅ ΠΏΠΎΠΊΡΡΡΠΈΡ (Π΄ΠΎ 25 ΠΌΠΊΠΌ) ΠΌΠΎΠ³ΡΡ Π±ΡΡΡ ΠΏΠΎΠ»ΡΡΠ΅Π½Ρ ΠΈΠ· ΡΠΈΠ°Π½ΠΈΡΡΠΎΠ³ΠΎ ΡΠ»Π΅ΠΊΡΡΠΎΠ»ΠΈΡΠ° (8 Π³/Π» Au, 20 Π³/Π» KCNΡΠ²ΠΎΠ±, 20 Π³/Π» K2ΠPO4 ΠΈ 20 Π³/Π» K2Π‘O3) ΠΏΡΠΈ ΡΠ΅ΠΌΠΏΠ΅ΡΠ°ΡΡΡΠ΅ 65β70 Β°Π‘ ΠΈ ΠΏΠ»ΠΎΡΠ½ΠΎΡΡΠΈ ΡΠΎΠΊΠ° 0,3β0,5 Π/Π΄ΠΌ2. Π ΠΏΠΎΡΠ»Π΅Π΄Π½Π΅Π΅ Π²ΡΠ΅ΠΌΡ ΡΡΠΏΠ΅ΡΠ½ΠΎ ΠΏΡΠΈΠΌΠ΅Π½ΡΡΡ ΡΠ°ΠΊ Π½Π°Π·ΡΠ²Π°Π΅ΠΌΡΠ΅ ΠΊΠΈΡΠ»ΡΠ΅ ΡΠΈΠ°Π½ΠΈΡΡΡΠ΅ ΡΠ»Π΅ΠΊΡΡΠΎΠ»ΠΈΡΡ Π·ΠΎΠ»ΠΎΡΠ΅Π½ΠΈΡ ΠΏΡΠΈΠΌΠ΅ΡΠ½ΠΎΠ³ΠΎ ΡΠΎΡΡΠ°Π²Π° (Π³/Π») ΠΈ ΡΠ΅ΠΆΠΈΠΌ:
ΠΠΎΠ»ΠΎΡΠΎ (Π² Π²ΠΈΠ΄Π΅ Π΄ΠΈΡΠΈΠ°Π½ΠΎΠ°ΡΡΠ°ΡΠ° ΠΊΠ°Π»ΠΈΡ) …………….10
ΠΠ°Π»ΠΈΠΉ Π»ΠΈΠΌΠΎΠ½Π½ΠΎΠΊΠΈΡΠ»ΡΠΉ…………80
ΠΠΈΠΌΠΎΠ½Π½Π°Ρ ΠΊΠΈΡΠ»ΠΎΡΠ° ………….20
ΡΠ………….5,5-6
Π’Π΅ΠΌΠΏΠ΅ΡΠ°ΡΡΡΠ°, Β°Π‘…………….70
ΠΠ»ΠΎΡΠ½ΠΎΡΡΡ ΡΠΎΠΊΠ°, Π/Π΄ΠΌ2…………0,5
ΠΠ»Ρ ΠΏΠΎΠ²ΡΡΠ΅Π½ΠΈΡ ΡΠ²Π΅ΡΠ΄ΠΎΡΡΠΈ ΠΈ ΠΈΠ·Π½ΠΎΡΠΎΡΡΠΎΠΉΠΊΠΎΡΡΠΈ Π·ΠΎΠ»ΠΎΡΡΡ
ΠΏΠΎΠΊΡΡΡΠΈΠΉ ΡΠ΅ΠΊΠΎΠΌΠ΅Π½Π΄ΡΠ΅ΡΡΡ Π² ΡΠ»Π΅ΠΊΡΡΠΎΠ»ΠΈΡ Π²Π²ΠΎΠ΄ΠΈΡΡ 15 ΠΌΠ³/Π» ΡΡΡΡΠΌΡ Π² Π²ΠΈΠ΄Π΅ ΠΊΠ°Π»ΠΈΡ ΡΡΡΡΠΌΡΠ½ΠΎΠ²ΠΈΠ½Π½ΠΎΠΊΠΈΡΠ»ΠΎΠ³ΠΎ. ΠΠΎΠΊΡΡΡΠΈΠ΅ ΠΏΡΠΈ ΡΡΠΎΠΌ ΡΠΎΠ΄Π΅ΡΠΆΠΈΡ Π΄ΠΎ 1 % Sb, ΠΌΠΈΠΊΡΠΎΡΠ²Π΅ΡΠ΄ΠΎΡΡΡ Π΄ΠΎΡΡΠΈΠ³Π°Π΅Ρ 180 ΠΊΠ³Ρ/ΠΌΠΌ2.
ΠΠ· ΠΌΠ΅ΡΠ°Π»Π»ΠΎΠ² ΠΏΠ»Π°ΡΠΈΠ½ΠΎΠ²ΠΎΠΉ Π³ΡΡΠΏΠΏΡ Π² Π½ΠΎΠ²ΡΡ ΠΎΡΡΠ°ΡΠ»ΡΡ ΡΠ΅Ρ Π½ΠΈΠΊΠΈ Π½Π°ΠΈΠ±ΠΎΠ»Π΅Π΅ ΡΠΈΡΠΎΠΊΠΎ ΠΏΡΠΈΠΌΠ΅Π½ΡΡΡ ΡΠΎΠ΄ΠΈΠ΅Π²ΠΎΠ΅ ΠΏΠΎΠΊΡΡΡΠΈΠ΅. ΠΠ»Ρ Π°Π»ΡΠΌΠΈΠ½ΠΈΠ΅Π²ΡΡ ΠΈΠ·Π΄Π΅Π»ΠΈΠΉ Π² ΠΎΠ΄ΠΈΠ½Π°ΠΊΠΎΠ²ΠΎΠΉ ΠΌΠ΅ΡΠ΅ ΠΌΠΎΠ³ΡΡ Π±ΡΡΡ ΠΈΡΠΏΠΎΠ»ΡΠ·ΠΎΠ²Π°Π½Ρ ΠΏΠΎΡΠ»Π΅ ΡΠΈΠ½ΠΊΠ°ΡΠ½ΠΎΠΉ ΠΏΠΎΠ΄Π³ΠΎΡΠΎΠ²ΠΊΠΈ ΠΌΠ΅Π΄Π½ΡΠΉ ΠΈ Π½ΠΈΠΊΠ΅Π»Π΅Π²ΡΠΉ ΠΏΠΎΠ΄ΡΠ»ΠΎΠΈ. Π’ΠΎΠ½ΠΊΠΈΠ΅ ΡΠΎΠ΄ΠΈΠ΅Π²ΡΠ΅ ΠΏΠΎΠΊΡΡΡΠΈΡ ΠΏΠΎΡΡΠ΄ΠΊΠ° 1β2 ΠΌΠΊΠΌ β ΠΌΠΎΠ³ΡΡ Π±ΡΡΡ ΠΏΠΎΠ»ΡΡΠ΅Π½Ρ ΠΈΠ· ΡΡΠ»ΡΡΠ°ΡΠ½ΠΎΠ³ΠΎ ΡΠ»Π΅ΠΊΡΡΠΎΠ»ΠΈΡΠ° Ρ ΡΠΎΠ΄Π΅ΡΠΆΠ°Π½ΠΈΠ΅ΠΌ 1β2 Π³/Π» Rh Π² Π²ΠΈΠ΄Π΅ ΡΠ΅ΡΠ½ΠΎΠΊΠΈΡΠ»ΠΎΠΉ ΡΠΎΠ»ΠΈ ΠΈ 20β25 ΠΌΠ»/Π» ΠΊΠΎΠ½ΡΠ΅Π½ΡΡΠΈΡΠΎΠ²Π°Π½Π½ΠΎΠΉ ΡΠ΅ΡΠ½ΠΎΠΉ ΠΊΠΈΡΠ»ΠΎΡΡ. ΠΠ»Ρ ΠΏΠΎΠ»ΡΡΠ΅Π½ΠΈΡ Π±ΠΎΠ»Π΅Π΅ ΡΠΎΠ»ΡΡΡΡ ΡΠΎΠ΄ΠΈΠ΅Π²ΡΡ ΠΏΠΎΠΊΡΡΡΠΈΠΉ ΡΠΎΠ΄Π΅ΡΠΆΠ°Π½ΠΈΠ΅ ΡΠΎΠ΄ΠΈΡ Π² ΡΠ»Π΅ΠΊΡΡΠΎΠ»ΠΈΡΠ΅ Π½Π΅ΠΎΠ±Ρ ΠΎΠ΄ΠΈΠΌΠΎ ΠΏΠΎΠ²ΡΡΠΈΡΡ Π΄ΠΎ 10β15 Π³/Π» ΠΈ Π²Π²Π΅ΡΡΠΈ 1 Π³/Π» ΡΠ΅Π»Π΅Π½ΠΎΠ²ΠΎΠΉ ΠΊΠΈΡΠ»ΠΎΡΡ, ΡΠ½ΠΈΠΆΠ°ΡΡΠ΅ΠΉ Π²Π½ΡΡΡΠ΅Π½Π½ΠΈΠ΅ Π½Π°ΠΏΡΡΠΆΠ΅Π½ΠΈΡ Π² ΠΏΠΎΠΊΡΡΡΠΈΠΈ ΠΈ ΠΏΠΎΠ·Π²ΠΎΠ»ΡΡΡΠ΅ΠΉ Π΄ΠΎΠ²Π΅ΡΡΠΈ Π΅Π³ΠΎ ΡΠΎΠ»ΡΠΈΠ½Ρ Π΄ΠΎ 25β50 ΠΌΠΊΠΌ. ΠΡΠΎΡΠ΅ΡΡ ΠΎΡΡΡΠ΅ΡΡΠ²Π»ΡΠ΅ΡΡΡ Ρ Π½Π΅ΡΠ°ΡΡΠ²ΠΎΡΠΈΠΌΡΠΌΠΈ (ΠΏΠ»Π°ΡΠΈΠ½ΠΎΠ²ΡΠΌΠΈ) Π°Π½ΠΎΠ΄Π°ΠΌΠΈ, ΠΏΡΠΈ ΡΠ΅ΠΌΠΏΠ΅ΡΠ°ΡΡΡΠ΅ 45β50Β° Π‘ ΠΈ ΠΏΠ»ΠΎΡΠ½ΠΎΡΡΠΈ ΡΠΎΠΊΠ° 1β2 Π/Π΄ΠΌ2. ΠΠ»Π΅ΠΊΡΡΠΎΠΎΡΠ°ΠΆΠ΄Π΅Π½Π½ΡΠΉ ΡΠΎΠ΄ΠΈΠΉ ΠΈΠΌΠ΅Π΅Ρ ΡΠ²Π΅ΡΠ΄ΠΎΡΡΡ ΠΏΠΎΡΡΠ΄ΠΊΠ° 800 ΠΊΠ³Ρ/ΠΌΠΌ2, Π±ΠΎΠ»ΡΡΡΡ ΠΊΠΎΡΡΠΎΠ·ΠΈΠΎΠ½Π½ΡΡ ΡΡΠΎΠΉΠΊΠΎΡΡΡ ΠΈ ΠΏΠΎ ΠΊΠΎΡΡΡΠΈΡΠΈΠ΅Π½ΡΡ ΠΎΡΡΠ°ΠΆΠ΅Π½ΠΈΡ ΡΠ²Π΅ΡΠ° ΡΡΡΡΠΏΠ°Π΅Ρ ΡΠΎΠ»ΡΠΊΠΎ ΡΠ΅ΡΠ΅Π±ΡΡ. Π ΠΎΡΠ»ΠΈΡΠΈΠ΅ ΠΎΡ ΡΠ΅ΡΠ΅Π±ΡΠ° ΡΠΎΠ΄ΠΈΠΉ Π½Π΅ ΡΡΡΠΊΠ½Π΅Π΅Ρ ΠΏΠΎΠ΄ Π΄Π΅ΠΉΡΡΠ²ΠΈΠ΅ΠΌ ΡΠ΅ΡΠΎΠ²ΠΎΠ΄ΠΎΡΠΎΠ΄Π°, ΠΈ, Π±ΡΠ΄ΡΡΠΈ Π½Π°Π½Π΅ΡΠ΅Π½ Π΄Π°ΠΆΠ΅ Π² ΡΠΎΠ½ΠΊΠΈΡ ΡΠ»ΠΎΡΡ (0,1β0,2 ΠΌΠΊΠΌ) Π½Π° ΡΠ΅ΡΠ΅Π±ΡΠΎ, Π·Π°ΡΠΈΡΠ°Π΅Ρ Π΅Π³ΠΎ ΠΎΡ ΠΏΠΎΡΡΡΠΊΠ½Π΅Π½ΠΈΡ.
ΠΡΠ΅ Π³Π°Π»ΡΠ²Π°Π½ΠΈΡΠ΅ΡΠΊΠΈΠ΅ ΠΏΠΎΠΊΡΡΡΠΈΡ Π·Π° ΠΈΡΠΊΠ»ΡΡΠ΅Π½ΠΈΠ΅ΠΌ ΡΠΈΠ½ΠΊΠ° ΠΊΠ°ΡΠΎΠ΄Π½Ρ ΠΏΠΎ ΠΎΡΠ½ΠΎΡΠ΅Π½ΠΈΡ ΠΊ Π°Π»ΡΠΌΠΈΠ½ΠΈΡ, Ρ. Π΅. Π·Π°ΡΠΈΡΠ°ΡΡ Π΅Π³ΠΎ ΠΎΡ ΠΊΠΎΡΡΠΎΠ·ΠΈΠΈ ΡΠΎΠ»ΡΠΊΠΎ ΠΏΡΠΈ ΡΡΠ»ΠΎΠ²ΠΈΠΈ ΠΎΡΡΡΡΡΡΠ²ΠΈΡ ΠΏΠΎΡ Π² ΠΏΠΎΠΊΡΡΡΠΈΠΈ. ΠΠ΅ΡΠΏΠΎΡΠΈΡΡΡΠ΅ ΠΏΠΎΠΊΡΡΡΠΈΡ ΠΎΠ±ΡΡΠ½ΠΎ ΠΏΠΎΠ»ΡΡΠ°ΡΡΡΡ Π² ΡΠ»ΠΎΡΡ Π΄ΠΎΡΡΠ°ΡΠΎΡΠ½ΠΎΠΉ ΡΠΎΠ»ΡΠΈΠ½Ρ ΠΈ ΠΏΡΠΈ ΡΠΎΠ±Π»ΡΠ΄Π΅Π½ΠΈΠΈ ΠΏΡΠ°Π²ΠΈΠ»ΡΠ½ΠΎΠ³ΠΎ ΡΠ΅ΠΆΠΈΠΌΠ° ΡΠ΅Ρ Π½ΠΎΠ»ΠΎΠ³ΠΈΡΠ΅ΡΠΊΠΎΠ³ΠΎ ΠΏΡΠΎΡΠ΅ΡΡΠ°. ΠΡΠ»ΠΈ Π°Π»ΡΠΌΠΈΠ½ΠΈΠ΅Π²ΡΠ΅ Π΄Π΅ΡΠ°Π»ΠΈ ΡΠΊΡΠΏΠ»ΡΠ°ΡΠΈΡΡΡΡΡΡ Π² ΡΡΠ»ΠΎΠ²ΠΈΡΡ ΡΠΌΠ°Π·ΠΊΠΈ, Π² ΡΡΡ ΠΎΠΉ Π°ΡΠΌΠΎΡΡΠ΅ΡΠ΅ ΠΈΠ»ΠΈ Π²Π°ΠΊΡΡΠΌΠ΅, ΡΠΎ ΠΏΠΎΡΠ°ΠΌΠΈ Π² ΠΏΠΎΠΊΡΡΡΠΈΡΡ ΠΌΠΎΠΆΠ½ΠΎ ΠΏΡΠ΅Π½Π΅Π±ΡΠ΅ΡΡ.
Π Π‘Π‘Π‘Π ΠΈ Π·Π° ΡΡΠ±Π΅ΠΆΠΎΠΌ ΠΏΡΠΎΠΌΡΡΠ»Π΅Π½Π½ΠΎΠ΅ ΠΏΡΠΈΠΌΠ΅Π½Π΅Π½ΠΈΠ΅ ΠΏΠΎΠ»ΡΡΠΈΠ»ΠΎ Π»ΡΠΆΠ΅Π½ΠΈΠ΅ Π°Π»ΡΠΌΠΈΠ½ΠΈΠ΅Π²ΡΡ ΠΏΠΎΡΡΠ½Π΅ΠΉ (Π΄Π»Ρ ΡΠ΅Π»Π΅ΠΉ ΠΏΡΠΈΡΠΈΡΠΊΠΈ) ΠΌΠ΅ΡΠΎΠ΄ΠΎΠΌ ΠΏΠΎΠ³ΡΡΠΆΠ΅Π½ΠΈΡ ΠΈΡ Π² ΡΠ°ΡΡΠ²ΠΎΡ ΡΡΠ°Π½Π½Π°ΡΠ° Π½Π°ΡΡΠΈΡ ΠΈΠ»ΠΈ ΠΊΠ°Π»ΠΈΡ. ΠΠΎΡΡΠ½ΠΈ ΠΎΠ±Π΅Π·ΠΆΠΈΡΠΈΠ²Π°ΡΡ ΠΏΠΎ ΠΎΠ΄Π½ΠΎΠΌΡ ΠΈΠ· ΠΌΠ΅ΡΠΎΠ΄ΠΎΠ², ΠΏΡΠΈΠ½ΡΡΡΡ Π΄Π»Ρ Π°Π»ΡΠΌΠΈΠ½ΠΈΠ΅Π²ΡΡ ΡΠΏΠ»Π°Π²ΠΎΠ². ΠΠΎΡΠ»Π΅ ΠΏΡΠΎΠΌΡΠ²ΠΊΠΈ Π² Π²ΠΎΠ΄Π΅ ΠΈΡ ΠΏΠΎΠ³ΡΡΠΆΠ°ΡΡ Π½Π° 20 Ρ Π² ΡΠ°Π·Π±Π°Π²Π»Π΅Π½Π½ΡΡ Π² ΠΎΡΠ½ΠΎΡΠ΅Π½ΠΈΠΈ (1:1) Π°Π·ΠΎΡΠ½ΡΡ ΠΊΠΈΡΠ»ΠΎΡΡ, Π²Π½ΠΎΠ²Ρ ΠΏΡΠΎΠΌΡΠ²Π°ΡΡ Π² Π²ΠΎΠ΄Π΅ ΠΈ Π½Π° 3β4 ΠΌΠΈΠ½ ΠΏΠΎΠ³ΡΡΠΆΠ°ΡΡ Π² ΡΠ°ΡΡΠ²ΠΎΡ, ΡΠΎΠ΄Π΅ΡΠΆΠ°ΡΠΈΠΉ 45β70 Π³/Π» Na2Sn(OH)6 ΠΈΠ»ΠΈ K2Sn(OH)6 ΠΏΡΠΈ ΡΠ΅ΠΌΠΏΠ΅ΡΠ°ΡΡΡΠ΅ 50β75Β° Π‘. ΠΡΠ½ΡΡΡΠ΅ ΠΈΠ· ΡΠ°ΡΡΠ²ΠΎΡΠ° ΡΡΠ°Π½Π½Π°ΡΠ° ΠΏΠΎΡΡΠ½ΠΈ ΠΏΡΠΎΠΌΡΠ²Π°ΡΡ Π² Ρ ΠΎΠ»ΠΎΠ΄Π½ΠΎΠΉ ΠΈ Π³ΠΎΡΡΡΠ΅ΠΉ Π²ΠΎΠ΄Π΅. Π’ΠΎΠ»ΡΠΈΠ½Π° ΠΎΠ»ΠΎΠ²ΡΠ½Π½ΠΎΠ³ΠΎ ΠΏΠΎΠΊΡΡΡΠΈΡ ΠΏΡΠΈ ΡΠ°ΠΊΠΎΠΌ ΡΠ΅ΠΆΠΈΠΌΠ΅ ΠΏΡΠΈΠΌΠ΅ΡΠ½ΠΎ 5 ΠΌΠΊΠΌ, ΡΠ²Π΅Ρ ΠΏΠΎΠΊΡΡΡΠΈΠΉ Π±Π΅Π»ΡΠΉ, ΠΌΠ°ΡΠΎΠ²ΡΠΉ. Π‘ΡΠ°Π½Π½Π°Ρ ΠΊΠ°Π»ΠΈΡ Π½Π΅ΡΠΊΠΎΠ»ΡΠΊΠΎ Π΄ΠΎΡΠΎΠΆΠ΅ ΡΡΠ°Π½Π½Π°ΡΠ° Π½Π°ΡΡΠΈΡ, Π½ΠΎ ΡΠ°ΡΡΠ²ΠΎΡΡ Π΅Π³ΠΎ Π±ΠΎΠ»Π΅Π΅ ΡΡΡΠΎΠΉΡΠΈΠ²Ρ ΠΈ ΠΌΠ΅Π½Π΅Π΅ ΠΏΠΎΠ΄Π²Π΅ΡΠΆΠ΅Π½Ρ Π³ΠΈΠ΄ΡΠΎΠ»ΠΈΠ·Ρ. ΠΠ»ΠΎΠ²ΡΠ½Π½ΡΠ΅ ΠΏΠΎΠΊΡΡΡΠΈΡ, ΠΏΠΎΠ»ΡΡΠ΅Π½Π½ΡΠ΅ ΠΌΠ΅ΡΠΎΠ΄ΠΎΠΌ ΠΏΠΎΠ³ΡΡΠΆΠ΅Π½ΠΈΡ Π² ΡΠ°ΡΡΠ²ΠΎΡ ΡΡΠ°Π½Π½Π°ΡΠ°, Π½Π΅Π΄ΠΎΡΡΠ°ΡΠΎΡΠ½ΠΎ ΡΡΠ΅ΠΏΠ»Π΅Π½Ρ Ρ ΠΎΡΠ½ΠΎΠ²ΠΎΠΉ, ΡΡΠΎΠ±Ρ ΠΈΠ·Π΄Π΅Π»ΠΈΡ Ρ ΡΠ°ΠΊΠΈΠΌΠΈ ΠΏΠΎΠΊΡΡΡΠΈΡΠΌΠΈ ΠΌΠΎΠΆΠ½ΠΎ Π±ΡΠ»ΠΎ ΠΏΠΎΠ΄Π²Π΅ΡΠ³Π°ΡΡ ΠΏΠ°ΠΉΠΊΠ΅. ΠΠ½ΠΈ Π½Π΅ ΠΌΠΎΠ³ΡΡ ΡΠ»ΡΠΆΠΈΡΡ ΡΠ°ΠΊΠΆΠ΅ ΠΏΡΠΎΠΌΠ΅ΠΆΡΡΠΎΡΠ½ΡΠΌ ΡΠ»ΠΎΠ΅ΠΌ Π΄Π»Ρ ΠΏΠΎΡΠ»Π΅Π΄ΡΡΡΠ΅Π³ΠΎ ΡΠ»Π΅ΠΊΡΡΠΎΠ»ΠΈΡΠΈΡΠ΅ΡΠΊΠΎΠ³ΠΎ ΠΎΡΠ°ΠΆΠ΄Π΅Π½ΠΈΡ ΠΎΠ»ΠΎΠ²Π°. ΠΠ»Ρ ΠΏΠ°ΠΉΠΊΠΈ Π½Π΅ΠΎΠ±Ρ ΠΎΠ΄ΠΈΠΌΠ° ΡΠΈΠ½ΠΊΠ°ΡΠ½Π°Ρ ΠΎΠ±ΡΠ°Π±ΠΎΡΠΊΠ° ΠΏΠΎΠ²Π΅ΡΡ Π½ΠΎΡΡΠΈ (ΠΈΠ»ΠΈ Π΄ΡΡΠ³Π°Ρ ΠΈΠ· ΠΏΡΠΈΠ²Π΅Π΄Π΅Π½Π½ΡΡ Π²ΡΡΠ΅) Ρ ΠΏΠΎΡΠ»Π΅Π΄ΡΡΡΠΈΠΌ Π½Π°Π½Π΅ΡΠ΅Π½ΠΈΠ΅ΠΌ ΠΏΠΎΠ΄ΡΠ»ΠΎΡ ΠΌΠ΅Π΄ΠΈ ΠΈΠ»ΠΈ Π½ΠΈΠΊΠ΅Π»Ρ.
www.stroitelstvo-new.ru
Π¦ΠΈΠ½ΠΊ-Π°Π»ΡΠΌΠΈΠ½ΠΈΠ΅Π²ΡΠ΅ ΠΏΠΎΠΊΡΡΡΠΈΡ | ΠΠ°Π»ΡΠ²Π°Π½ΠΎΠΏΠΎΠΊΡΡΡΠΈΠ΅
ΠΡ ΠΎΡΠΊΡΡΠ»ΠΈ Π½ΠΎΠ²ΡΡ Π»ΠΈΠ½ΠΈΡ: ΡΠΈΠ½ΠΊ-Π°Π»ΡΠΌΠΈΠ½ΠΈΠ΅Π²ΠΎΠ΅ ΠΏΠΎΠΊΡΡΡΠΈΠ΅. Π¦ΠΈΠ½ΠΊ-Π°Π»ΡΠΌΠΈΠ½ΠΈΠ΅Π²ΠΎΠ΅ ΠΏΠΎΠΊΡΡΡΠΈΠ΅ ΠΎΠ±Π΅ΡΠΏΠ΅ΡΠΈΠ²Π°Π΅Ρ Π·Π°ΡΠΈΡΡ ΠΎΡ ΠΊΠΎΡΡΠΎΠ·ΠΈΠΈ Π±ΠΎΠ»Π΅Π΅ 1000 ΡΠ°ΡΠΎΠ² Π² ΠΊΠ°ΠΌΠ΅ΡΠ΅ ΡΠΎΠ»ΡΠ½ΠΎΠ³ΠΎ ΡΡΠΌΠ°Π½Π° Π±Π΅Π· ΠΊΠΎΡΡΠΎΠ·ΠΈΠΈ ΠΌΠ΅ΡΠ°Π»Π»Π° ΠΎΡΠ½ΠΎΠ²Ρ. ΠΠΎΠ»ΡΡΠ°Π΅ΠΌΡΠ΅ ΡΠ΅Π·ΡΠ»ΡΡΠ°ΡΡ Π·Π°Π²ΠΈΡΡΡ ΠΎΡ ΡΠΎΠ»ΡΠΈΠ½Ρ Π±Π°Π·ΠΎΠ²ΠΎΠ³ΠΎ ΠΏΠΎΠΊΡΡΡΠΈΡ ΠΈΠ»ΠΈ Π½Π°Π½Π΅ΡΠ΅Π½Π½ΠΎΠ³ΠΎ Π³Π°Π»ΡΠ²Π°Π½ΠΈΡΠ΅ΡΠΊΠΎΠ³ΠΎ ΡΠ»ΠΎΡ.
ΠΠ° ΠΎΠ±ΡΠ°Π±ΠΎΡΠΊΡ ΠΏΡΠΈΠ½ΠΈΠΌΠ°ΡΡΡΡ ΠΌΠ΅ΡΠ°Π»Π»ΠΎΠΊΠΎΠ½ΡΡΡΡΠΊΡΠΈΠΈ Π³Π°Π±Π°ΡΠΈΡΠ°ΠΌΠΈ Π΄ΠΎ 2000Ρ 3000 ΠΌΠΌ.
ΠΠ»Π΅ΠΊΡΡΠΎΠΎΡΠ°ΠΆΠ΄Π΅Π½Π½ΡΠ΅ ΠΏΠΎΠΊΡΡΡΠΈΡ ΡΠΈΠ½ΠΊΠ° ΠΈ ΡΠΏΠ»Π°Π²ΠΎΠ² ΡΠΈΠ½ΠΊΠ° ΡΠΆΠ΅ ΠΌΠ½ΠΎΠ³ΠΎ Π»Π΅Ρ ΡΠ²Π»ΡΡΡΡΡ Π³Π»Π°Π²Π½ΡΠΌΠΈ ΠΏΠΎΠΊΡΡΡΠΈΡΠΌΠΈ, ΡΠ΄ΠΎΠ²Π»Π΅ΡΠ²ΠΎΡΡΡΡΠΈΠΌΠΈ ΡΡΠ΅Π±ΠΎΠ²Π°Π½ΠΈΡ ΠΌΠ½ΠΎΠ³ΠΈΡ ΠΎΡΡΠ°ΡΠ»Π΅ΠΉ ΠΏΡΠΎΠΌΡΡΠ»Π΅Π½Π½ΠΎΡΡΠΈ ΠΏΠΎ ΠΎΠ±Π΅ΡΠΏΠ΅ΡΠ΅Π½ΠΈΡ Π½ΡΠΆΠ½ΠΎΠΉ ΡΡΠ΅ΠΏΠ΅Π½ΠΈ Π·Π°ΡΠΈΡΡ ΠΎΡ ΠΊΠΎΡΡΠΎΠ·ΠΈΠΈ. ΠΠ° ΡΠ΅Π½Π΄Π΅Π½ΡΠΈΠ΅ΠΉ ΠΏΡΠΎΠΈΠ·Π²ΠΎΠ΄ΡΡΠ²Π° ΡΡΠ°Π»ΠΈ Π²ΡΡΠΎΠΊΠΎΠΉ ΠΏΡΠΎΡΠ½ΠΎΡΡΠΈ, ΡΠΆΠ΅ Π² Π½Π°ΡΠ°Π»Π΅ Π²ΠΎΡΡΠΌΠΎΠ³ΠΎ Π΄Π΅ΡΡΡΠΈΠ»Π΅ΡΠΈΡ ΠΏΡΠΎΡΠ»ΠΎΠ³ΠΎ ΡΡΠΎΠ»Π΅ΡΠΈΡ Π·Π½Π°ΡΠΈΡΠ΅Π»ΡΠ½ΠΎ Π²ΡΡΠΎΡ ΡΠΏΡΠΎΡ Π½Π° Π°Π»ΡΡΠ΅ΡΠ½Π°ΡΠΈΠ²Π½ΡΠ΅ ΠΏΠΎΠΊΡΡΡΠΈΡ, Π° Π³Π»Π°Π²Π½ΡΠΌ ΡΡΠ΅Π±ΠΎΠ²Π°Π½ΠΈΠ΅ΠΌ Π±ΡΠ»ΠΎ ΠΈΡΠΊΠ»ΡΡΠ΅Π½ΠΈΠ΅ Π²ΠΎΠ΄ΠΎΡΠΎΠ΄Π½ΠΎΠ³ΠΎ ΠΎΡ ΡΡΠΏΡΠΈΠ²Π°Π½ΠΈΡ.
Π‘ Π΄Π΅Π²ΡΡΠΎΠ³ΠΎ Π΄Π΅ΡΡΡΠΈΠ»Π΅ΡΠΈΡ ΠΏΡΠΎΡΠ»ΠΎΠ³ΠΎ Π²Π΅ΠΊΠ° ΡΠΈΠ½ΠΊ-Π°Π»ΡΠΌΠΈΠ½ΠΈΠ΅Π²ΡΠ΅ ΠΏΠΎΠΊΡΡΡΠΈΡ Π·Π°Π½ΡΠ»ΠΈ ΠΏΡΠΎΡΠ½ΠΎΠ΅ ΠΌΠ΅ΡΡΠΎ Π² ΠΏΡΠΎΠΌΡΡΠ»Π΅Π½Π½ΠΎΡΡΠΈ, ΠΎΡΠΎΠ±Π΅Π½Π½ΠΎ Π² Π°Π²ΡΠΎΠΌΠΎΠ±ΠΈΠ»ΡΠ½ΠΎΠΌ ΠΏΡΠΎΠΈΠ·Π²ΠΎΠ΄ΡΡΠ²Π΅.
Π¦ΠΈΠ½ΠΊ-Π°Π»ΡΠΌΠΈΠ½ΠΈΠ΅Π²ΠΎΠ΅ ΠΏΠΎΠΊΡΡΡΠΈΠ΅ ΠΏΡΠ΅Π΄ΡΡΠ°Π²Π»ΡΠ΅Ρ ΡΠΎΠ±ΠΎΠΉ Π½Π΅ΠΎΡΠ³Π°Π½ΠΈΡΠ΅ΡΠΊΠΎΠ΅, ΠΊΠΎΡΡΠΎΠ·ΠΈΠΎΠ½Π½ΠΎ-Π·Π°ΡΠΈΡΠ½ΠΎΠ΅ Π±Π°Π·ΠΎΠ²ΠΎΠ΅ ΠΏΠΎΠΊΡΡΡΠΈΠ΅, Π½Π°ΠΏΠΎΠ»Π½Π΅Π½Π½ΠΎΠ΅ Ρ Π»ΠΎΠΏΡΡΠΌΠΈ ΡΠΈΠ½ΠΊΠ° ΠΈ Π°Π»ΡΠΌΠΈΠ½ΠΈΡ. ΠΡΠΎ Π±Π°Π·ΠΎΠ²ΠΎΠ΅ ΠΏΠΎΠΊΡΡΡΠΈΠ΅, ΠΎΡΠ°ΠΆΠ΄Π°Π΅ΠΌΠΎΠ΅ ΠΌΠ΅ΡΠΎΠ΄Π°ΠΌΠΈ ΠΏΠΎΠ³ΡΡΠΆΠ΅Π½ΠΈΡ-Π²ΡΠ°ΡΠ΅Π½ΠΈΡ, Π²ΡΠ°ΡΠ΅Π½ΠΈΡ, ΠΏΠΎΠ³ΡΡΠΆΠ΅Π½ΠΈΡ-ΡΡΠ΅ΠΊΠ°Π½ΠΈΡ ΠΈΠ»ΠΈ ΡΠ°ΡΠΏΡΠ»Π΅Π½ΠΈΠ΅ΠΌ Π΄Π»Ρ ΠΊΡΠ΅ΠΏΠ΅ΠΆΠ½ΡΡ Π΄Π΅ΡΠ°Π»Π΅ΠΉ ΡΠ°ΠΊΠΈΡ ΠΊΠ°ΠΊ Π±ΠΎΠ»ΡΡ, Π²ΠΈΠ½ΡΡ, Π³Π°ΠΉΠΊΠΈ, ΠΏΡΡΠΆΠΈΠ½Ρ, Π·Π°ΠΆΠΈΠΌΡ, Π° ΡΠ°ΠΊΠΆΠ΅ ΡΡΠ°ΠΌΠΏΠΎΠ²Π°Π½Π½ΡΠ΅ Π΄Π΅ΡΠ°Π»ΠΈ ΠΈ Ρ.ΠΏ.
Π¦ΠΈΠ½ΠΊ-Π°Π»ΡΠΌΠΈΠ½ΠΈΠ΅Π²ΠΎΠ΅ ΠΏΠΎΠΊΡΡΡΠΈΠ΅ ΠΎΠ±Π΅ΡΠΏΠ΅ΡΠΈΠ²Π°Π΅Ρ Π·Π°ΡΠΈΡΡ ΠΎΡ ΠΊΠΎΡΡΠΎΠ·ΠΈΠΈ Π±ΠΎΠ»Π΅Π΅ 1000 ΡΠ°ΡΠΎΠ² Π² ΠΊΠ°ΠΌΠ΅ΡΠ΅ ΡΠΎΠ»ΡΠ½ΠΎΠ³ΠΎ ΡΡΠΌΠ°Π½Π° Π±Π΅Π· ΠΊΠΎΡΡΠΎΠ·ΠΈΠΈ ΠΌΠ΅ΡΠ°Π»Π»Π° ΠΎΡΠ½ΠΎΠ²Ρ. ΠΠΎΠ»ΡΡΠ°Π΅ΠΌΡΠ΅ ΡΠ΅Π·ΡΠ»ΡΡΠ°ΡΡ Π·Π°Π²ΠΈΡΡΡ ΠΎΡ ΡΠΎΠ»ΡΠΈΠ½Ρ Π±Π°Π·ΠΎΠ²ΠΎΠ³ΠΎ ΠΏΠΎΠΊΡΡΡΠΈΡ ΠΈΠ»ΠΈ Π½Π°Π½Π΅ΡΠ΅Π½Π½ΠΎΠ³ΠΎ Π³Π°Π»ΡΠ²Π°Π½ΠΈΡΠ΅ΡΠΊΠΎΠ³ΠΎ ΡΠ»ΠΎΡ.
ΠΠΏΡΠΈΠΌΠ°Π»ΡΠ½ΡΠΉ ΡΠ΅Π·ΡΠ»ΡΡΠ°Ρ ΠΎΠ±Π΅ΡΠΏΠ΅ΡΠΈΠ²Π°Π΅ΡΡΡ ΠΏΡΠΈ Π½Π°Π½Π΅ΡΠ΅Π½ΠΈΠΈ ΠΏΠΎΠΊΡΡΡΠΈΡ Π½Π° ΠΏΠΎΠ²Π΅ΡΡ Π½ΠΎΡΡΡ Π΄Π΅ΡΠ°Π»ΠΈ, ΠΎΠ±ΡΠ°Π±ΠΎΡΠ°Π½Π½ΡΡ Π΄ΡΠΎΠ±Π΅ΡΡΡΡΠΉΠ½ΡΠΌ ΠΌΠ΅ΡΠΎΠ΄ΠΎΠΌ ΠΈΠ»ΠΈ ΡΠΎΡΡΠ°ΡΠΈΡΠΎΠ²Π°Π½Π½ΠΎΠ΅(ΡΠΎΠ½ΠΊΠΈΠΌ ΡΠ»ΠΎΠ΅ΠΌ). Π’ΠΎΠ»ΡΠΈΠ½Π° Π½Π°Π½ΠΎΡΠΈΠΌΠΎΠ³ΠΎ ΠΏΠΎΠΊΡΡΡΠΈΡ ΠΌΠΎΠΆΠ΅Ρ Π±ΡΡΡ Π² ΠΈΠ½ΡΠ΅ΡΠ²Π°Π»Π΅ ΠΎΡ 6 ΠΈ 20 ΠΌΠΊΠΌ. ΠΠΎΠ»ΡΡΠ°Π΅ΠΌΠΎΠ΅ ΠΏΠΎΠΊΡΡΡΠΈΠ΅ Π½Π΅ ΠΈΠΌΠ΅Π΅Ρ Π²ΠΎΠ΄ΠΎΡΠΎΠ΄Π½ΠΎΠ³ΠΎ ΠΎΡ ΡΡΠΏΡΠΈΠ²Π°Π½ΠΈΡ.
ΠΡΠ΅ΠΈΠΌΡΡΠ΅ΡΡΠ²Π° ΡΠΈΠ½ΠΊ-Π°Π»ΡΠΌΠΈΠ½ΠΈΠ΅Π²ΠΎΠ³ΠΎ ΠΏΠΎΠΊΡΡΡΠΈΡ ΠΏΠ΅ΡΠ΅Π΄ Π³ΠΎΡΡΡΠΈΠΌ ΡΠΈΠ½ΠΊΠΎΠ²Π°Π½ΠΈΠ΅ΠΌ:
- ΠΡΠΈ Π³ΠΎΡΡΡΠ΅ΠΌ ΡΠΈΠ½ΠΊΠΎΠ²Π°Π½ΠΈΠΈ ΡΡΡΠ΅ΡΡΠ²ΡΠ΅Ρ ΠΎΠΏΠ°ΡΠ½ΠΎΡΡΡ ΠΏΠΎΠ½ΠΈΠΆΠ΅Π½ΠΈΡ ΡΠ²Π΅ΡΠ΄ΠΎΡΡΠΈ ΡΡΠ°Π»ΠΈ ΠΈΠ·-Π·Π° Π²ΡΡΠΎΠΊΠΎΠΉ ΡΠ΅ΠΌΠΏΠ΅ΡΠ°ΡΡΡΡ, Π² ΡΠΎ Π²ΡΠ΅ΠΌΡ ΠΊΠ°ΠΊ ΠΏΡΠΈ Π½Π°Π½Π΅ΡΠ΅Π½ΠΈΠΈ ΡΠΈΠ½ΠΊ-Π°Π»ΡΠΌΠΈΠ½ΠΈΠ΅Π²ΠΎΠ³ΠΎ ΠΏΠΎΠΊΡΡΡΠΈΡ Π½Π΅Ρ ΠΎΠΏΠ°ΡΠ½ΠΎΡΡΠΈ ΠΏΠΎΠ½ΠΈΠΆΠ΅Π½ΠΈΡ ΡΠ²Π΅ΡΠ΄ΠΎΡΡΠΈ, ΡΠ΅ΠΌΠΏΠ΅ΡΠ°ΡΡΡΠ°
- ΠΠ»Ρ Π³ΠΎΡΡΡΠ΅Π³ΠΎ ΡΠΈΠ½ΠΊΠΎΠ²Π°Π½ΠΈΡ Π½Π΅Π±Ρ ΠΎΠ΄ΠΈΠΌΠ° ΡΡΠ°Π»Ρ Π±ΠΎΠ»Π΅Π΅ Π²ΡΡΠΎΠΊΠΎΠ³ΠΎ ΠΊΠ°ΡΠ΅ΡΡΠ²Π°. ΠΠ»Ρ ΡΠΈΠ½ΠΊ-Π°Π»ΡΠΌΠΈΠ½ΠΈΠ΅Π²ΠΎΠ³ΠΎ ΠΏΠΎΠΊΡΡΡΠΈΡ ΠΌΠΎΠΆΠ½ΠΎ ΠΈΡΠΏΠΎΠ»ΡΠ·ΠΎΠ²Π°ΡΡ Π½Π΅ ΠΎΡΠ΅Π½Ρ ΠΊΠ°ΡΠ΅ΡΡΠ²Π΅Π½Π½ΡΡ ΡΡΠ°Π»Ρ.
- ΠΡΠΈ Π³ΠΎΡΡΡΠ΅ΠΌ ΡΠΈΠ½ΠΊΠΎΠ²Π°Π½ΠΈΠΈ ΡΡΡΠ΅ΡΡΠ²ΡΠ΅Ρ ΠΎΠΏΠ°ΡΠ½ΠΎΡΡΡ ΠΎΠ±ΡΠ°Π·ΠΎΠ²Π°Π½ΠΈΡ ΡΡΠ΅ΡΠΈΠ½ ΠΏΠΎΠ΄ Π΄Π΅ΠΉΡΡΠ²ΠΈΠ΅ΠΌ ΠΆΠΈΠ΄ΠΊΠΎΠ³ΠΎ ΠΌΠ΅ΡΠ°Π»Π»Π° Π° ΡΠ°ΠΊΠΆΠ΅ Π²ΠΎΠ΄ΠΎΡΠΎΠ΄Π½ΠΎΠΉ Ρ ΡΡΠΏΠΊΠΎΡΡΠΈ ΠΏΡΠΈ ΡΡΠ°Π²Π»Π΅Π½ΠΈΠΈ (ΠΏΠΎΠ΄Π³ΠΎΡΠΎΠ²ΠΊΠ°). ΠΡΠΈ Π½Π°Π½Π΅ΡΠ΅Π½ΠΈΠΈ ΡΠΈΠ½ΠΊ-Π°Π»ΡΠΌΠΈΠ½ΠΈΠ΅Π²ΠΎΠ³ΠΎ ΠΏΠΎΠΊΡΡΡΠΈΡ Π½Π΅Ρ ΠΎΠΏΠ°ΡΠ½ΠΎΡΡΠΈ ΠΎΠ±ΡΠ°Π·ΠΎΠ²Π°Π½ΠΈΡ ΡΡΠ΅ΡΠΈΠ½ ΠΈ Π²ΠΎΠ΄ΠΎΡΠΎΠ΄Π½ΠΎΠΉ Ρ ΡΡΠΏΠΊΠΎΡΡΠΈ.
- ΠΡΠΈ Π³ΠΎΡΡΡΠ΅ΠΌ ΡΠΈΠ½ΠΊΠΎΠ²Π°Π½ΠΈΠΈ ΠΏΠΎΠ²ΡΡΠ°Π΅ΡΡΡ Π²Π΅Ρ ΠΈΠ·Π΄Π΅Π»ΠΈΠΉ ΠΈΠ·-Π·Π° Π±ΠΎΠ»ΡΡΠΎΠΉ ΡΠΎΠ»ΡΠΈΠ½Ρ ΠΏΠΎΠΊΡΡΡΠΈΡ, Π½ΠΎ ΠΏΡΠΈ ΡΠΈΠ½ΠΊ-Π°Π»ΡΠΌΠΈΠ½ΠΈΠ΅Π²ΠΎΠΌ ΠΏΠΎΠΊΡΡΡΠΈΠΈ ΡΠΎΠ»ΡΠΈΠ½Π° ΠΏΠΎΠΊΡΡΡΠΈΡ Π·Π½Π°ΡΠΈΡΠ΅Π»ΡΠ½ΠΎ ΠΌΠ΅Π½ΡΡΠ΅.
- ΠΡΠΈ Π³ΠΎΡΡΡΠ΅ΠΌ ΡΠΈΠ½ΠΊΠΎΠ²Π°Π½ΠΈΠΈ ΡΡΡΠ΅ΡΡΠ²ΡΠ΅Ρ Π½Π΅ΠΎΠ±Ρ ΠΎΠ΄ΠΈΠΌΠΎΡΡΡ ΠΏΠΎΠ²ΡΠΎΡΠ½ΠΎΠ³ΠΎ Π½Π°Π½Π΅ΡΠ΅Π½ΠΈΡ ΡΠ΅Π·ΡΠ±Ρ (Π³Π°ΠΉΠΊΠΈ), Π° Π΄Π»Ρ ΡΠΈΠ½ΠΊ-Π°Π»ΡΠΌΠΈΠ½ΠΈΠ΅Π²ΠΎΠ³ΠΎ ΠΏΠΎΠΊΡΡΡΠΈΡ Π½Π΅Ρ Π½Π΅ΠΎΠ±Ρ ΠΎΠ΄ΠΈΠΌΠΎΡΡΠΈ ΠΏΠΎΠ²ΡΠΎΡΠ½ΠΎΠ³ΠΎ Π½Π°Π½Π΅ΡΠ΅Π½ΠΈΡ ΡΠ΅Π·ΡΠ±Ρ, ΠΏΠΎΡΡΠΎΠΌΡ ΠΊΠΎΡΡΠΎΠ·ΠΈΠΎΠ½Π½Π°Ρ Π·Π°ΡΠΈΡΠ° Π»ΡΡΡΠ΅.
- ΠΠΎΡΡΡΠ΅Π΅ ΡΠΈΠ½ΠΊΠΎΠ²Π°Π½ΠΈΠ΅ — ΡΡΠΎ ΠΎΡΠ΅Π½Ρ ΡΠ½Π΅ΡΠ³ΠΎΠ΅ΠΌΠΊΠΈΠΉ ΠΏΡΠΎΡΠ΅ΡΡ, Π² ΡΠΎ Π²ΡΠ΅ΠΌΡ ΠΊΠ°ΠΊ ΡΠΈΠ½ΠΊ-Π°Π»ΡΠΌΠΈΠ½ΠΈΠ΅Π²ΠΎΠ΅ ΠΏΠΎΠΊΡΡΡΠΈΠ΅ — ΠΏΡΠΎΡΠ΅ΡΡ Π³ΠΎΡΠ°Π·Π΄ΠΎ ΠΌΠ΅Π½Π΅Π΅ ΡΠ½Π΅ΡΠ³ΠΎΠ΅ΠΌΠΊΠΈΠΉ ΡΠ°ΠΊ ΠΊΠ°ΠΊ ΡΠ΅ΠΌΠΏΠ΅ΡΠ°ΡΡΡΠ° ΡΡΡΠΊΠΈ Π·Π½Π°ΡΠΈΡΠ΅Π»ΡΠ½ΠΎ Π½ΠΈΠΆΠ΅.
ΠΠ±Π»Π°ΡΡΠΈ ΠΏΡΠΈΠΌΠ΅Π½Π΅Π½ΠΈΡ ΡΠΈΠ½ΠΊ-Π°Π»ΡΠΌΠΈΠ½ΠΈΠ΅Π²ΠΎΠ³ΠΎ ΠΏΠΎΠΊΡΡΡΠΈΡ
- ΠΠΎΠΊΡΡΡΠΈΡ, ΡΠΎΠ΄Π΅ΡΠΆΠ°ΡΠΈΠ΅ ΠΠ’Π€Π(ΡΠ΅ΡΠ»ΠΎΠ½)
- ΠΡΠΎΠΈΠ·Π²ΠΎΠ΄ΡΡΠ²ΠΎ Π²Π΅ΡΡΡΠ½Π½ΡΡ ΡΡΡΠ±ΠΈΠ½
- ΠΠ°ΠΌΠ΅Π½Π° ΠΊΠ°Π΄ΠΌΠΈΡ
- ΠΠ». ΡΠΎΠ΅Π΄ΠΈΠ½ΠΈΡΠ΅Π»ΠΈ, Π·Π°ΠΆΠΈΠΌΡ
- CΡΡΠΎΠΈΡΠ΅Π»ΡΠ½Π°Ρ ΠΏΡΠΎΠΌΡΡΠ»Π΅Π½Π½ΠΎΡΡΡ
- Π’ΡΠΆΠ΅Π»ΠΎΠ΅ ΠΌΠ°ΡΠΈΠ½ΠΎΡΡΡΠΎΠ΅Π½ΠΈΠ΅, ΡΠΊΡΠΊΠ°Π²Π°ΡΠΎΡΡ, ΡΠ΅Π»ΡΡΠΊΠΎΠ΅ Ρ ΠΎΠ·ΡΠΉΡΡΠ²ΠΎ ΠΈ Ρ.Π΄.
- Π‘Π΅ΡΡ Π²ΠΎΠ΄ΠΎΡΠ½Π°Π±ΠΆΠ΅Π½ΠΈΡ
- ΠΠ΅ΡΡΠ΅Ρ ΠΈΠΌΠΈΡΠ΅ΡΠΊΠ°Ρ ΠΏΡΠΎΠΌΡΡΠ»Π΅Π½Π½ΠΎΡΡΡ
- ΠΡΡΠ°ΡΠ»ΠΈ Π½Π΅ΡΡΠ΅Π³Π°Π·ΠΎΠ²ΠΎΠΉ ΠΏΡΠΎΠΌΡΡΠ»Π΅Π½Π½ΠΎΡΡΠΈ
- Π‘Π΅ΠΊΡΠΎΡ ΠΌΠ΅Π΄ΠΈΡΠΈΠ½Ρ
- AΠ²ΠΈΠ°ΡΠΈΡ / ΠΠΎΠ΅Π½Π½Π°Ρ ΡΠ΅Ρ Π½ΠΈΠΊΠ°
- ΠΡΠ΅ΡΡΠΎΠ²Π°Π½Π½ΡΠ΅ ΠΈΠ·Π΄Π΅Π»ΠΈΡ, ΡΡΠ°ΠΌΠΏΠΎΠ²ΠΊΠ°
- Π-Π²ΠΎ Π΄Π΅ΡΠ°Π»Π΅ΠΉ Ρ ΡΡΠ΅Π±ΠΎΠ²Π°Π½ΠΈΠ΅ΠΌ Π²ΡΡΠΎΠΊΠΎΠΉ ΡΠΎΡΠ½ΠΎΡΡΠΈ
Π‘ΠΈΡΡΠ΅ΠΌΡ ΡΠΈΠ½ΠΊ-Π°Π»ΡΠΌΠΈΠ½ΠΈΠ΅Π²ΠΎΠ³ΠΎ ΠΏΠΎΠΊΡΡΡΠΈΡ Π½Π΅Π»ΡΠ·Ρ ΡΡΠ°Π²Π½ΠΈΠ²Π°ΡΡ Ρ ΠΎΠ±ΡΡΠ½ΡΠΌΠΈ ΠΏΠΎΡΠΎΡΠΊΠΎΠ²ΡΠΌΠΈ ΠΏΠΎΠΊΡΡΡΠΈΡΠΌΠΈ. ΠΡΠΎ ΠΎΡΠ΅Π½Ρ Ρ ΠΈΠΌΠΈΡΠ΅ΡΠΊΠΈ Π°ΠΊΡΠΈΠ²Π½Π°Ρ ΡΡΠ΅Π΄Π° Π½Π° ΠΎΡΠ½ΠΎΠ²Π΅ Ρ Π»ΠΎΠΏΡΠ΅Π² ΡΠΈΠ½ΠΊΠ° ΠΈ Π°Π»ΡΠΌΠΈΠ½ΠΈΡ. ΠΠ»ΠΎΡΠ½ΠΎ Π½Π°ΡΠ°ΠΆΠ΅Π½Π½ΡΠ΅ Ρ Π»ΠΎΠΏΡΡ ΠΏΠΎΠΊΡΡΠ²Π°ΡΡΡΡ Ρ ΠΈΠΌΠΈΡΠ΅ΡΠΊΠΈ Π°ΠΊΡΠΈΠ²Π½ΡΠΌ ΡΠ²ΡΠ·ΡΡΡΠΈΠΌ Π²Π΅ΡΠ΅ΡΡΠ²ΠΎΠΌ, ΠΊΠΎΡΠΎΡΠΎΠ΅ ΡΠ΅Π°Π³ΠΈΡΡΠ΅Ρ Ρ ΠΎΡΠ½ΠΎΠ²ΠΎΠΉ ΡΡΠ°Π»ΠΈ. ΠΡΠΎΡΠ΅ΡΡ ΠΎΡΠ²Π΅ΡΠΆΠ΄Π΅Π½ΠΈΡ ΠΏΡΠΎΡ ΠΎΠ΄ΠΈΡ ΠΏΡΠΈ ΡΠ΅ΠΌΠΏΠ΅ΡΠ°ΡΡΡΠ΅ ΠΎΡ 200Β° C Π΄ΠΎ 320Β° C (Π² Π·Π°Π²ΠΈΡΠΈΠΌΠΎΡΡΠΈ ΠΎΡ ΠΏΡΠΎΠ΄ΡΠΊΡΠ°), ΠΏΡΠΎΠ΄ΠΎΠ»ΠΆΠΈΡΠ΅Π»ΡΠ½ΠΎΡΡΡ — ΠΎΡ 20 Π΄o 40 ΠΌΠΈΠ½ΡΡ. Π Π΅Π·ΡΠ»ΡΡΠ°Ρ — ΡΡΡ ΠΎΠ΅ ΠΏΠΎΠΊΡΡΡΠΈΠ΅, ΠΎΠ±Π΅ΡΠΏΠ΅ΡΠΈΠ²Π°ΡΡΠ΅Π΅ ΠΎΡΠ»ΠΈΡΠ½ΡΡ Π·Π°ΡΠΈΡΡ ΠΎΡ ΠΊΠΎΡΡΠΎΠ·ΠΈΠΈ.
www.galvan.ru