Марочник сталей и сплавов онлайн
Механические свойства стали 12Х18Н10Т
Механические свойства стали при повышенных температурах
Температура испытаний, °С | Предел текучести, σ0,2, МПа | Временное сопротивление разрыву, σв, МПа | Относительное удлинение при разрыве, δ5, % | Относительное сужение, ψ, % | Ударная вязкость, KCU, Дж/см2 |
Закалка при 1050-1100 °С, охлаждение на воздухе | |||||
20 | 225 — 315 | 550 — 650 | 46 — 74 | 66 — 80 | 215 — 372 |
500 | 135 — 205 | 390 — 440 | 30 — 42 | 60 — 70 | 196 — 353 |
550 | 135 — 205 | 380 — 450 | 31 — 41 | 61 — 68 | 215 — 353 |
600 | 120 — 205 | 340 — 410 | 28 — 38 | 51 — 74 | 196 — 358 |
650 | 120 — 195 | 270 — 390 | 27 — 37 | 52 — 73 | 245 — 353 |
700 | 120 — 195 | 265 — 360 | 20 — 38 | 40 — 70 | 255 — 353 |
Ударная вязкость из стали, KCU, Дж/см
2Термообработка | Т= +20 °С | Т= -40 °С | Т= -75 °С |
Полоса 8х40 мм в состоянии покоя | 286 | 303 | 319 |
Чувствительность стали к охрупчиванию при старении
Время, часы | Температура, °С | Ударная вязкость, KCU, Дж/см2 |
Исходное состояние | - | 274 |
600 | 186 — 206 | |
5000 | 650 | 176 — 196 |
Жаростойкость стали
Среда | Температура, ºС | Группа стойкости или балл |
Воздух | 650 | 2 — 3 |
Воздух | 750 | 4 — 5 |
Свойства по стандарту ГОСТ 5582-75
Термообработка | Сечение, мм | Предел текучести, σ0,2, МПа | Временное сопротивление разрыву, σв, МПа | Относительное удлинение при разрыве, δ5, % | Относительное сужение, ψ, % | Твердость, НВ |
Листы горячекатанные и холоднокатанные: закалка при 1050-1080 °С, вода или воздух | До 3,9 | 205 | 530 | 40 | - | - |
Листы горячекатанные и холоднокатанные: нагартованные | - | 880 — 1080 | 10 | - | - |
Свойства по стандарту ГОСТ 5949-75
Термообработка | Сечение, мм | Предел текучести, σ0,2, МПа | Временное сопротивление разрыву, σв, МПа | Относительное удлинение при разрыве, δ5, % | Относительное сужение, ψ, % |
Твердость, НВ |
Прутки.![]() |
60 | 196 | 510 | 40 | 55 | - |
Механические свойства при испытаниях на длительную прочность
Температура испытания, °С | Предел ползучести, МПа | Скорость ползучести %/час | Предел длительной прочности, МПа | Длительность испытания, часы |
600 | 74 | 1/100000 | 147 | 10000 |
650 | 29 — 39 | 1/100000 | 78 — 98 | 10000 |
Свойства по стандарту ГОСТ 7350-77
Термообработка | Сечение, мм | Предел текучести, σ0,2, МПа | Временное сопротивление разрыву, σв, МПа | Относительное удлинение при разрыве, δ5, % | Относительное сужение, ψ, % | Твердость, НВ |
Листы горячекатанные и холоднокатанные: закалка при 1000-1080 °С, вода или воздух.![]() |
Свыше 4 | 236 | 530 | 38 | - | - |
Свойства по стандарту ГОСТ 9940-81
Термообработка | Сечение, мм | Предел текучести, σ0,2, МПа | Временное сопротивление разрыву, σв, МПа | Относительное удлинение при разрыве, δ5, % | Относительное сужение, ψ, % | Твердость, НВ |
Трубы бесшовные горячедеформированные без термообработки | 3,5 — 32 | - | 529 | 40 | - | - |
Свойства по стандарту ГОСТ 18143-72
Термообработка | Сечение, мм | Предел текучести, σ 0,2, МПа | Временное сопротивление разрыву, σв, МПа | Относительное удлинение при разрыве, δ5, % | Относительное сужение, ψ, % | Твердость, НВ |
Проволока термообработанная | 1,0 — 6,0 | - | 540 — 880 | 20 | - | - |
Свойства по стандарту ГОСТ 18907-73
Термообработка | Сечение, мм | Предел текучести, σ0,2, МПа | Временное сопротивление разрыву, σв, МПа | Относительное удлинение при разрыве, δ5, % | Относительное сужение, ψ, % | Твердость, НВ |
Прутки шлифованные, обработанные на заданную прочность | - | - | 580 — 830 | 20 | - | - |
Прутки нагартованные | До 5 | - | 930 | - | - | - |
Свойства по стандарту ГОСТ 25054-81
Термообработка | Сечение, мм | Предел текучести, σ0,2, МПа | Временное сопротивление разрыву, σв, МПа | Относительное удлинение при разрыве, δ5, % | Относительное сужение, ψ, % | Твердость, НВ |
Поковки.![]() |
До 1000 | 196 | 510 | 35 | 40 | - |
Физические свойства 12Х18Н10Т
Температура, °С | Модуль упругости, E 10— 5,МПа | Коэффициент линейного расширения, a 10 6, 1/°С | Коэффициент теплопроводности, l, Вт/м·°С | Удельная теплоемкость, C, Дж/кг·°С | Удельное электросопротивление, R 10 9, Ом·м |
20 | 1,98 | - | 15 | - | 725 |
100 | 1,94 | 16,6 | 16 | 462 | 792 |
200 | 1,89 | 17,0 | 18 | 496 | 861 |
300 | 1,81 | 17,2 | 19 | 517 | 920 |
400 | 1,74 | 17,5 | 21 | 538 | 976 |
500 | 1,66 | 17,9 | 23 | 550 | 1028 |
600 | 1,57 | 18,2 | 25 | 563 | 1075 |
700 | 1,47 | 18,6 | 27 | 575 | 1115 |
800 | - | 18,9 | 26 | 596 | - |
900 | - | 19,3 | - | - | - |
Сталь марки 12Х18Н10Т — Металлургическая компания
Марка: 12Х18Н10Т (старое название Х18Н10Т) (заменители: 08Х18Г8Н2Т, 10Х14Г14Н4Т, 12Х17Г9АН4, 08Х22Н6Т, 08Х17Т, 15Х25Т, 12Х18Н9Т) Класс: Сталь конструкционная криогенная Вид поставки: сортовой прокат, в том числе фасонный: ГОСТ 5949-75, ГОСТ 2590-2006, ГОСТ 2879-2006. ![]() Использование в промышленности: детали, работающие до 600 °С. Сварные аппараты и сосуды, работающие в разбавленных растворах азотной, уксусной, фосфорной кислот, растворах щелочей и солей и другие детали, работающие под давлением при температуре от —196 до +600 °С, а при наличии агрессивных сред до +350 °С.; сталь аустенитного класса |
Химический состав в % стали 12Х18Н10Т ( стар. Х18Н10Т ) | ||
C | до 0,12 | |
Si | до 0,8 | |
Mn | до 2 | |
Ni | 9 — 11 | |
S | до 0,02 | |
P | до 0,035 | |
Cr | 17 — 19 | |
Cu | до 0,3 | |
Ti | 0,4-1 | |
Fe | ~67 |
12Х18Н10Т труба, лента, проволока, лист, круг 12Х18Н10Т
Зарубежные аналоги марки стали 12Х18Н10Т ( стар.![]() | |
США | 321, 321H, S32100, S32109 |
Германия | 1.4541, 1.4878, X10CrNiTi18-10, X12CrNiTi18-9, X6CrNiTi18-10 |
Япония | SUS321 |
Франция | Z10CNT18-10, Z10CNT18-11, Z6CNT18-10, Z6CNT18-12 |
Англия | 321S31, 321S51, 321S59, LW18, LW24, X6CrNiTi18-10 |
Евросоюз | 1.4541, 1.4878, X10CrNiTi18-10, X6CrNiTi18-10KT |
Италия | X6CrNiTi18-11, X6CrNiTi18-11KG, X6CrNiTi18-11KT |
Испания | F.3523, X6CrNiTi18-10 |
Китай | 0Cr18Ni10Ti, 0Cr18Ni11Ti, 0Cr18Ni9Ti, 1Cr18Ni11Ti, H0Cr20Ni10Ti |
Швеция | 2337 |
Болгария | 0Ch28N10T, Ch28N12T, Ch28N9T, X6CrNiTi18-10 |
Венгрия | H5Ti, KO36Ti, KO37Ti, X6CrNiTi18-10 |
Польша | 0h28N10T, 1h28N10T, 1h28N12T, 1h28N9T |
Румыния | 10TiNiCr180, 12TiNiCr180 |
Чехия | 17246, 17247, 17248 |
Австрия | X6CrNiTi18-10KKW, X6CrNiTi18-10S |
Австралия | 321 |
Юж.![]() | STS321, STS321TKA, STSF321 |
Свойства и полезная информация: |
Удельный вес: 7920 кг/м3 Термообработка: Закалка 1050 — 1100oC, вода Температура ковки: начала 1200 °С, конца 850 °С. Сечения до 350 мм охлаждаются на воздухе Твердость материала: HB 10 -1 = 179 МПа Свариваемость материала: без ограничений, способы сварки: РДС (электроды ЦТ-26), ЭШС и КТС. Рекомендуется последующая термообработка Обрабатываемость резанием: в закаленном состоянии при HB 169 и σв=610 МПа, Кu тв. спл=0,85, Кu б. ст=0,35 Флокеночувствительность: не чувствительна Жаростойкость: в воздухе при Т=650 °С 2-3 группа стойкости, при Т=750 °С 4-5 группа стойкости Предел выносливости: σ-1=279 МПа, n=107 |
Механические свойства стали 12Х18Н10Т ( стар.![]() | ||||||
ГОСТ | Состояние поставки, режимы термообработки | Сечение,мм | σ0,2(МПа) | σв(МПа) | δ5(%) | ψ% |
ГОСТ 5949-75 | Прутки. Закалка 1020-1100 °С, воздух, масло или вода. | 60 | 196 | 510 | 40 | 55 |
ГОСТ 18907-73 | Прутки шлифованные, обработанные на заданную прочность. Прутки нагартованные. | — До 5 | — — | 590-830 930 | 20 — | — — |
ГОСТ 7350-77 (Образцы поперечные) ГОСТ 5582-75 (Образцы поперечные) | Листы горячекатанные и холоднокатанные: — закалка 1000-1080 °С, вода или воздух.- закалка 1050-1080 °С, вода или воздух.- нагартованные | Св.![]() До 3,9До 3,9 | 236205 — | 530530 880-1080 | 3840 10 | — — |
ГОСТ 25054-81 | Поковки. Закалка 1050-1100 °С, вода или воздух. | До 1000 | 196 | 510 | 35 | 40 |
ГОСТ 18143-72 | Проволока термообработанная. | 1,0-6,0 | — | 540-880 | 20 | — |
ГОСТ 9940-8 | Трубы бесшовные горячедеформированные без термообработки | 3,5-32 | — | 529 | 40 | — |
Механические свойства стали 12Х18Н10Т ( стар. Х18Н10Т ) при повышенных температурах | |||||
Температура испытаний, °С | σ0,2 (МПа) | σв(МПа) | δ5 (%) | ψ % | KCU (кДж / см2) |
Закалка 1050-1100 °С, охлаждение на воздухе | |||||
20 500 550 600 650 700 | 225-315 135-205 135-205 120-205 120-195 120-195 | 550-650 390-440 380-450 340-410 270-390 265-360 | 46-74 30-42 31-41 28-38 27-37 20-38 | 66-80 60-70 61-68 51-74 52-73 40-70 | 215-372 196-353 215-353 196-358 245-353 255-353 |
Механические свойства 12Х18Н10Т ( стар.![]() | ||||
Температура испытания, °С | Предел ползучести, МПа | Скорость ползучести %/ч | Предел длительной прочности, МПа, не менее | Длительность испытания, ч |
600 650 | 74 29-39 | 1/100000 | 147 78-98 | 10000 |
Ударная вязкость стали 12Х18Н10Т ( стар. Х18Н10Т ) KCU, (Дж/см2) | |||
Т= +20 °С | Т= -40 °С | Т= -75 °С | Термообработка |
286 | 303 | 319 | Полоса 8х40 мм в состоянии покоя |
Чуствительность стали 12Х18Н10Т ( стар.![]() | ||
Время, ч | Температура, °С | KCU, Дж/см |
Исходное состояние 5000 5000 | 600 650 | 274 186-206 176-196 |
Жаростойкость стали 12Х18Н10Т ( стар. Х18Н10Т ) | ||
Среда | Температура, ºС | Группа стойкости или балл |
Воздух | 650 750 | 2-3 4-5 |
Физические свойства стали 12Х18Н10Т ( старое название Х18Н10Т ) | ||||||
T (Град) | E 10— 5 (МПа) | a 10 6 (1/Град) | l (Вт/(м·град)) | r (кг/м3) | C (Дж/(кг·град)) | R 10 9 (Ом·м) |
20 | 1.![]() | 15 | 7920 | 725 | ||
100 | 1.94 | 16.6 | 16 | 462 | 792 | |
200 | 1.89 | 17 | 18 | 496 | 861 | |
300 | 1.81 | 17.2 | 19 | 517 | 920 | |
400 | 1.74 | 17.5 | 21 | 538 | 976 | |
500 | 1.66 | 17.9 | 23 | 550 | 1028 | |
600 | 1.57 | 18.2 | 25 | 563 | 1075 | |
700 | 1.47 | 18.6 | 27 | 575 | 1115 | |
800 | 18.9 | 26 | 596 | |||
900 | 19.3 |
Аргоноприемники и сосуды для хранения аргона
Описание
Аргоноприемники применяются в электровакуумной технике, металлургии, металлообработке, электросварке, при создании высокоточных приборов и микросхем, а также в тех производственных процессах, где необходимо создание абсолютно инертная атмосфера. Такую популярность можно объяснить тем, что аргон – очень распространенный, доступный и дешевый газ, который получают путем разделения воздуха на кислород и азот.
Поскольку аргон является криогенным газом, для его хранения необходимо использовать специальные сосуды, чтобы обеспечить безопасную работу.
Конструкция приемников аргона
Представляют собой горизонтальные или вертикальные сосуды с эллиптическими днищами для надземной установки.
Эксплуатацию проводят при давлении до 1,2 МПа. Это может привести к взрывоопасным и пожароопасным ситуациям. Для обеспечения безопасной эксплуатации на входе и выходе устанавливаются манометры, комплект предохранительной и запорной арматуры, останавливающей подачу газа в случае повышения давления на входе или выходе.
Часто ресиверы аргона поставляются и эксплуатируются вместе с другим технологическим оборудованием, компрессорами или испарительной системой.
Саратовский резервуарный завод изготавливает аргоноприемники со следующими параметрами:
- давление — до 1,2 МПа
- объем — от 1 м 3 до 200 м 3
- конструкция — надземная горизонтальная или вертикальная с эллиптическими головками на опорах
- диапазон температур продукта — от -60ºС до +300ºС
- минимальная температура окружающей среды — -60°С
Производство аргоновых ресиверов
Саратовский резервуарный завод имеет необходимые Сертификаты соответствия на производство воздухосборников и газоресиверов.
Для производства мы выбираем только высокопрочные материалы, не вступающие в химическую реакцию с эксплуатационным продуктом. Так, применяются следующие марки стали:
- сталь высокопрочная 09Г2С
- нержавеющая титансодержащая 12Х18Н10Т аустенитного класса
- коррозионностойкая 10Х17Н13М2Т
Аргоноприемники изготовляют из листовой стали, которой придают форму цельносварной цилиндрической обечайки, в которой предусмотрены служебные отверстия для установки люков и патрубков для сервисного осмотра и удаления отложений, подачи и подачи газа в конвейер.
Для защиты внутренних и внешних поверхностей от негативного воздействия окружающей среды или продукта эксплуатации обечайки и днища покрываются специальными антикоррозийными составами, значительно продлевающими срок службы оборудования. Цвет внешнего покрытия зависит от отзывов клиентов.
Качество продукции подтверждено Сертификатом соответствия и испытаниями на герметичность и высоким давлением, проведенными лабораторией.
Чертеж вертикального ресивера аргона объемом 16 м
3График форсунок
Тег № | Заявка | Диаметр, мм |
---|---|---|
А | смотровой люк | 450 |
Б | вход | 300 |
В | розетка | 300 |
Г | предохранительный клапан | 80 |
Д | регулятор мощности | 15 |
Е | манометр | 20 |
N | манометр | 10 |
Р | удаление конденсата | 25 |
Вопрос | дренаж | 50 |
К | дополнительный | 20 |
Сводную таблицу технических характеристик воздушных судов и ресиверов Вы можете посмотреть здесь.

Как заказать ресивер аргона на Саратовском резервуарном заводе?
Наши специалисты изготавливают воздушные резервуары, сосуды и ресиверы до 200 м 3 по индивидуальному заказу. Для расчета стоимости изготовления, доставки и монтажа:
- позвоните нам по телефону +7(8452)250-288
- отправить заполненную Анкету на электронную почту
- нажмите «Запрос цен», оформите, укажите контакты, и мы свяжемся с вами
Специалисты Саратовского резервуарного завода выполняют комплекс услуг по строительству объектов нефтегазового комплекса:
- инженерные изыскания
- проектирование строительных площадок
- производство приемников, воздушных судов и другого судового оборудования
- поставка и монтаж оборудования на объекте
Ресиверы водорода по цене производителя
Наименование
Ресиверы водорода устанавливаются на металлургических (для извлечения металлов), химических (для синтеза хлороводорода, аммиака, метилового спирта) и нефтехимических (для гидрирования жиров) , уголь и нефть) объектов, на объектах атомной энергетики, в электрогенераторах (для охлаждения от водородных установок), при сварочных работах тугоплавких материалов, в космической промышленности (как наиболее экологически чистое топливо высокой теплоемкости) и др. Они могут быть как емкостью для хранения конечного вещества, которое доставляется непосредственно Потребителю, так и промежуточной емкостью, откуда газ подается на дальнейшую производственную линию.
Строительство ресиверов водорода
Саратовский резервуарный завод имеет необходимые Сертификаты соответствия на изготовление емкостей и ресиверов воздуха.
Саратовский водохранилищный завод производит ресиверы водорода, разработанные специально для этого газа. Водород хранится в сжатом состоянии при избыточном давлении до 12 МПа.
Жесткие условия эксплуатации предопределили требования к выбору материала и конструкции. Основными параметрами конструкции ресиверов водорода являются: объем от 1 до 200 м 3 и предельное давление (до 12 МПа). Дополнительными факторами, влияющими на выбор стали и расчет толщины корпуса, являются температура окружающей среды (выше -60°C) и температура продукта (от -60°C до +300°C).
Очень важно сохранить герметичность в течение всего срока службы. Поэтому требуется точный расчет и выбор стали, устойчивой к химическому воздействию эксплуатационного продукта.
Для безопасного и долговечного хранения сжатого водорода мы используем марки стали, способные выдерживать внутренние нагрузки от давления и воздействия хранимого газа:
- нержавеющая титансодержащая 12Х18Н10Т аустенитного класса
- коррозионностойкая 10Х17Н13М2Т
- сталь высокопрочная 09Г2С
Ресивер водорода представляет собой надземный горизонтальный или вертикальный сосуд, который устанавливается на опоры. Эти сосуды работают под высоким давлением, поэтому головки выполнены эллиптическими. Для выполнения основных функций предусмотрен люк, патрубки и арматура, через которые осуществляется заполнение, откачка, отвод конденсата, технологический осмотр и очистка поверхности и т.д.
Важным элементом водородных ресиверов является предохранительный клапан, предотвращающий разрушение из-за повышения давления.
Ресиверы водорода изготовляют из листового металла, которому придают цилиндрическую форму. В обечайках выполнены отверстия для люка(ов), штуцеров и ниппелей. Эллиптические головки и опоры изготавливаются на специальном оборудовании. Затем все элементы свариваются.
Наружная и внутренняя поверхности покрыты составами для дополнительной защиты от коррозии.
Завершающий этап производства — испытания на герметичность, предельные давления и испытания на стойкость к агрессивным средам. Имея Лабораторию, наши специалисты могут гарантировать качество выпускаемой продукции, а высокопрофессиональные инженеры-конструкторы обеспечивают точность проектирования.
Чертеж ресивера водорода
Схема насадки
Тег № | Заявка |
---|---|
Б | вход |
Г | розетка |
К | линия баланса |
Дж | люк |
М | дренаж |
У | предохранительный клапан |
Ф | впуск |
F1 | впуск |
Н | для насоса |
N | манометр |
В комплект поставки ресивера водорода входят:
- сам сосуд
- комплект патрубков и фитингов
- технологическое оборудование (по требованию Заказчика)
- Сертификат продукта
Сводную таблицу технических характеристик воздушных судов и ресиверов Вы можете посмотреть здесь.
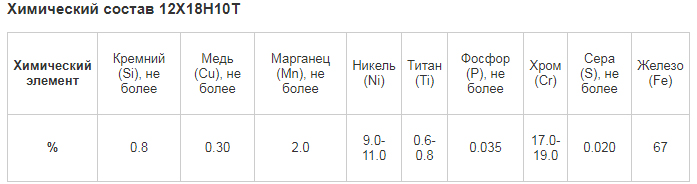