Производство стали. Сталелитейная промышленность :: SYL.ru
Без всякого сомнения, можно говорить о том, что сталь – это один из самых востребованных и важных конструкционных материалов. Он используется при конструировании транспорта, авиации, в строительстве и так далее. Стоит заметить, что сегодня производство стали развито очень хорошо. Эта отрасль металлургии считается одной из самых сложных и трудоемких. Давайте более подробно поговорим на данную тему и разберемся со всеми интересными нюансами и деталями.
О мировой сталелитейной промышленности
В 2014 году произошло некое восстановление металлургической промышленности, в частности сталелитейной, после кризиса 2012 года. Статистика показывает, что мировая выплавка ежегодно растет. К примеру, с 2001 по 2012 год объемы увеличились почти на 700 миллионов тонн. Тем не менее, цикличность производства делает сталелитейную промышленность относительно нестабильной отраслью.
Сегодня же можно говорить о том, что ежегодный спрос на данный материал будет постоянно увеличиваться. Страны с развитой инфраструктурой будут выступать в качестве главных покупателей. Обусловлено это необходимостью урбанизации и индустриализации. Из этого можно сделать простой вывод – производство стали никуда не денется, и будет только развиваться.
Кременчугский сталелитейный завод
Данное украинское предприятие известно практически во всем мире. По большей части тут отливаются детали для грузовых вагонов, в частности колеса. Помимо этого завод изготавливает литые детали для автомобильной промышленности и собственных ремонтных нужд. На этом заводе работает примерно 2 500 специалистов по состоянию на 2014 год. Но ввиду экономического кризиса на Украине и ухудшения отношений с Россией завод почти полностью остановился. Обусловлено это тем, что примерно 95% изготавливаемой продукции покупала РФ. В результате все чаще говорят о консервации завода, а после этого его могут просто разобрать.
Первые видимые ухудшения начались еще в 2009 году, когда компания потеряла большую часть своих активов. Уже в 2010 году завод стал банкротом, но свою работу не прекратил. Тем не менее, к 2013 году объемы производства сократились на 48%, что фактически означало остановку предприятия, это и случилось немного позже. Сейчас сложно сказать будет ли работать Кременчугский сталелитейный завод или нет.
Кислородно-конвертерный процесс
В настоящее время существует несколько способов получения стали. Один из них, он же основной – кислородно-конвертерный. Этот метод появился несколько позже бессемеровского. По сути, можно говорить о том, что процесс получения стали в конвертере точно такой же, но несколько усовершенствованный. Давайте немного разберемся с тем, как все работает.
В конвертер заливается жидкий чугун, который снизу продувается кислородом. В процессе происходит окисление примесей чугуна из-за чего и происходит его превращение в сталь. Причем, технология производства стали такова, что во время окисления вырабатывается тепло, которого достаточно для обеспечения необходимой температуры в камере. Как вы видите, это довольно простой метод, позволяющий получить качественный продукт за небольшое время. Температура в камере обычно поддерживается в диапазоне 1 600 градусов.
Мартеновский процесс
Это еще один популярный метод получения качественной стали. Суть заключается в том, что плавка осуществляется на поду в отражательной печи. Предварительно ее оснащают регенераторами, которые необходимы для подогрева воздуха или газа. Можно сказать, что сама идея такой плавки появилась достаточно давно, однако мартеновский процесс производства стали требует высокой температуры, чего добиться никак не удавалось. Но уже в 1864 году впервые использовали регенераторы, которые показали себя с лучшей стороны.
Чтобы получить сталь, в мартеновскую печь загружают шихту. В ее состав входит скрап, лом и чугун. В результате воздействия высокой температуры через некоторое время происходит плавка шихты, а дальше подаются специальные добавки. Они нужны для того, чтобы придать стали необходимые эксплуатационные свойства. Готовый продукт отливается в ковши и транспортируется к пункту назначения. Так как мартеновский метод довольно эффективный и не требует больших затрат, поэтому очень скоро стал основным чуть ли не во всем мире.
Про электросталеплавильное производство
Сегодня практически любой сталелитейный завод имеет в своем составе дуговые сталеплавильные печи. Помимо этого имеют место и печи постоянного и переменного тока, однако они используются редко и объемы выплавки с них невелики. Но вот электродуговые печи пользуются большой популярностью. Обусловлено это тем, что в них можно получить сталь электропечного сортамента. Тут довольно просто получить высоколегированные и легированные стали. В это же время добиться таких же хороших результатов в мартеновских печах и конвертерах не удается. Обусловлено это тем, что в дуговой печи осуществляется быстрый нагрев, что позволяет добавить большое количество легирующих элементов. Наряду с этим защита металла от угара дает хороший результат. В принципе, тут имеется возможность не только плавной регулировки температуры, но и точной, что тоже немаловажно. Ввиду того, что этот метод только развивается, можно говорить о его перспективности.
Производство стали в России
С российской металлургией знакомы во всем мире, так как она является довольно мощной и конкурентоспособной. Не исключением является такая отрасль, как сталелитейное производство. В настоящее время РФ занимает 5 место в мире по количеству производимой стали. Несмотря на то, что внутренние интересы в металле довольно высоки, по состоянию на 2012 год было экспортировано порядка 40% от общего количества продукции.
По статистике, за последние 10 лет наблюдается положительная динамика развития сталелитейной промышленности России. По сравнению с 1999 годом, в 2009 году производительность была увеличена примерно на 64%, что довольно существенно. В это же время многие лидирующие российские заводы не отстают от зарубежных конкурентов и догоняют их в плане производительности. В 2009-м году в России примерно 57% стали изготавливалось в кислородных конвертерах, 27% — в электродуговых печах и всего 16% — в мартеновских печах. В целом Российская Федерация ежегодно изготавливает порядка 4,5% от мирового производства. Но по статистике, эта цифра постепенно ползет вверх, что говорит о положительной динамике.
О ситуации в мире в 2014 году
Как было отмечено выше, после мирового кризиса в 2012 году сталелитейная промышленность оправилась только спустя несколько лет. Так, за это время всемирный спрос на данный металл увеличился на 3,3%. Многие эксперты отмечают, что случилось это потому, что в странах с развитой экономикой постоянно растет спрос на сталь. Наиболее интенсивно рост производства стали проходит в Китае. Там с 2013 года до 2015 было изготовлено больше на 3,5%. Нельзя не отметить и рост в Индии, где было произведено стали больше на 5,6%. В США же рост увеличения объемов производства основывается на увеличении спроса автомобильной промышленности. Планируется изготовить на 3% больше стали по сравнению с предыдущими годами. В Европе в 2012 и 2013 году была отрицательная тенденция, то есть потребление не увеличивалось, а уменьшалось. Но уже в 2014 году потребление выросло на 2,1%. Результат хоть и незначительный, но приятный.
О ценах и еще кое-что
Как было отмечено немного выше, металлургическая промышленность цикличная. Это говорит о том, что цены на металл постоянно изменяются: то они растут, то падают. Тем не менее, по сравнению с 2012 годом был замечен неплохой рост. Однако нужно понимать, что тут все зависит от стоимости исходного сырья. Чем дороже будет обходиться кокс, шихта, лом и другие продукты, тем дороже будет сталь. Нельзя и не обращать внимания на такой фактор, как перенасыщение рынка дешевой китайской продукцией. Это способно существенно снизить цены. Еще один интересный момент заключается в том, что многие потребители пытаются заменить сталь другими материалами. Вместо стальных лопат используют пластиковые, металлические детали заменяют полимерными. К примеру, кузов электрокара изготавливается уже не из стали, а из специального волокна, которое по заявлению производителя имеет отличные прочностные и эксплуатационные характеристики и значительно меньший вес.
Заключение
Как вы видите, на сегодняшний день есть несколько актуальных способов получения стали. Это конвертерный метод, мартеновский и плавка в дуговых печах. Каждый из них чем-то хорош и имеет свои недостатки. Тем не менее, производство стали в мире таково, что приходится пользоваться даже не самыми выгодными, с экономической точки зрения, способами. Одно можно сказать точно, цены на сталь будут постепенно расти, а объемы увеличиваться. Но это будет происходить до определенного момента. В любом случае, через некоторое время появятся лучшие материалы, которые будут иметь меньший вес, лучшее сопротивление коррозии и т.п. Сегодня они если и есть, то невыгодно выглядят на фоне металлических изделий из-за своей высокой стоимости. В принципе, на этом все.
www.syl.ru
Сталелитейное производство — Большая Энциклопедия Нефти и Газа, статья, страница 1
Сталелитейное производство
Cтраница 1
Сталелитейное производство может располагаться в виде отдельного комплекса на кузнечно-литейном заводе с учетом централизованной поставки стального литья машиностроительным заводам и горячих слитков кузнечному комплексу собственного завода. Возможно расположение в одном промышленном узле двух крупных централизованных заводов: литейного и кузнечного, с учетом организации поставок на центрокуз горячих слитков. [1]
Современное сталелитейное производство использует дуплекс-процесс, на первом этапе которого получают сплавы в мощных вакуумных дуговых или индукционных печах емкостью до нескольких десятков тонн. На втором этапе применяют вакуумные печи малой емкости, из которых производится отливка изделий. Однако вакуумная плавка — дело непростое. Получить и сохранить глубокий вакуум трудно и дорого. Кроме того, такие компоненты жаропрочных сплавов, как марганец и хром, при вакуумной плавке испаряются. [2]
В сталелитейном производстве марганец играет важную роль как десуль-фуратор. Он широко применяется также в качестве раскислителя расплавленной стали. Большая часть марганца при выплавке стали переходит в шлак. Хотя для этих целей обычно применяют ферромарганец, во многих случаях вге же идет и чистый марганец, особенно при выплавке специальных сталей или когда требуется максимально снизить содержание углерода и фосфора в металле. Его добавляют для целей очистки к сталям основной мартеновской плавки, кислой и основной электроплавки, а также к тигельной стали. [3]
В сталелитейном производстве первым продуктом, получаемым из железной руды, являются стальные слитки, из которых затем производят различные сталепрокатные изделия. Управляющий производством заметил слишком большую задержку между получением и непосредственным их прокатом на прокатных станах. В идеале прокатка слитков должна начинаться сразу после получения их из печи, чтобы уменьшить потребность повторного нагрева слитков. Первоначально эта проблема группой экспертов ИО была представлена в виде линейной модели, оптимизирующей баланс между производительностью литейной печи и пропускной способностью прокатного стана. В процессе исследования ситуации эксперты строили простые графики производительности плавильной печи, суммируя производство стальных слитков в течение ее трехсменной работы. Они обнаружили, что, хотя третья смена начинается в 23 часа, наибольшая производительность достигается только между 2 и 5 часами утра. Дальнейшие наблюдения показали, что операторы печи, работающие в третью смену, имели привычку в начале смены устроить себе довольно длительный период раскачки, наверстывая этот простой в утренние часы. Таким образом, данная проблема решалась простым выравниванием производства слитков в течение всех рабочих смен, для чего пришлось поработать с человеческим фактором. [4]
В сталелитейном производстве, как и в чугунолитейном, удельный вес машинной формовки и заливки литья на конвейерах на крупных объектах значительно выше, чем на слабо специализированных мелких объектах. [5]
В сталелитейном производстве первым продуктом, получаемым из железной руды, являются стальные слитки, из которых затем производят различные сталепрокатные изделия. Управляющий производством заметил слишком большую задержку между получением и непосредственным их прокатом на прокатных станах. В идеале прокатка слитков должна начинаться сразу после получения их из печи, чтобы уменьшить потребность повторного нагрева слитков. Первоначально эта проблема группой экспертов ИО была представлена в виде линейной модели, оптимизирующей баланс между производительностью литейной печи и пропускной способностью прокатного стана. В процессе исследования ситуации эксперты строили простые графики производительности плавильной печи, суммируя производство стальных слитков в течение ее трехсменной работы. Они обнаружили, что, хотя третья смена начинается в 23 часа, наибольшая производительность достигается только между 2 и 5 часами утра. Дальнейшие наблюдения показали, что операторы печи, работающие в третью смену, имели привычку в начале смены устроить себе довольно длительный период раскачки, наверстывая этот простой в утренние часы. Таким образом, данная проблема решалась простым выравниванием производства слитков в течение всех рабочих смен, для чего пришлось поработать с человеческим фактором. [6]
В сталелитейном производстве должно быть обращено особое внимание на улучшение теплового хозяйства мартеновских печей, на усиление завалочных, уборочных и транспортных средств п на значительно более интенсивное, чем это запроектировано, использование бессемеровских цехов. [7]
В сталелитейном производстве существует ряд разновидностей технологического процесса: мартеновский, бессемеровский, томасовский, электроплавильный. Все они основаны на плавке и обработке металла или обработке уже расплавленного чугуна с целью удаления из железа углерода, серы, кремния и других примесей. [8]
Однако закрытие сталелитейного производства, включенное во второй сценарий в конце 2002 г. приведет к уменьшению возможностей для обеспечения персонала работой, но руководство предприятия против увольнения работников. Следовательно, по мнению / Л / С, целью для руководства компании должно являться создание как можно большего количества новых прибыльных рабочих мест с настоящего момента до года закрытия производства, чтобы избежать или свести к минимуму вынужденное сокращение персонала и социальные издержки безработицы. [9]
Обухова в основании сталелитейного производства в России. [10]
Решающий шаг в совершенствовании сталелитейного производства был сделан в 50 — х годах XX века разработкой кислородно-конвертерного метода выплавки стали, который позволил использовать в качестве сырья не только чугун, но и стальной лом и руду, существенно повысить производительность и улучшить качество стали. В настоящее время этот метод, наряду с электроплавильным, преобладает. [11]
Мартеновский шлак — отход сталелитейного производства, содержащий не менее 80 % углекислого кальция в виде силикатов кальция и магния. В качестве полезных примесей в нем находится фосфор, марганец и многие другие микроэлементы. [12]
Что касается инструментальной стали, сталелитейные производства обычно поставляют три сорта стали, четко различающиеся между собой: высококачественная, качественная и обычная инструментальная. [14]
В области теории и практики доменного и сталелитейного производства, а также коксохимии долго и успешно работал акад. Его творческие усилия были направлены на создание новых конструкций печей для производства кокса, на расширение сырьевой базы коксохимической промышленности. Ученый предложил коксовать каменные угли с добавкой железной руды и колошниковой пыли. Так был впервые получен железококс — новый вид сырья для доменной плавки. [15]
Страницы: 1 2 3 4
www.ngpedia.ru
Производство стали – технология, оборудование, этапы
Производство стали сегодня осуществляется в основном из отработанных стальных изделий и передельного чугуна. Сталь представляет собой сплав железа и углерода, последнего в котором содержится от 0,1 до 2,14%. Превышение содержания углерода в сплаве приведет к тому, что он станет слишком хрупким. Суть процесса производства стали, в составе которой содержится гораздо меньшее количество углерода и примесей, по сравнению с чугуном, состоит в том, чтобы в процессе плавки перевести эти примеси в шлак и газы, подвергнуть их принудительному окислению.
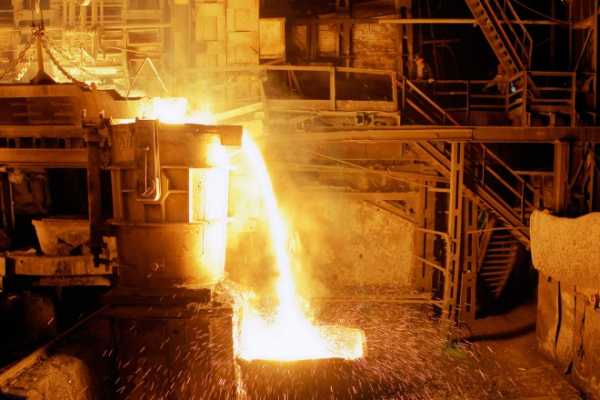
Процесс производства стали
Особенности процесса
Производство стали, осуществляемое в сталеплавильных печах, предполагает взаимодействие железа с кислородом, в процессе которого металл окисляется. Окислению также подвергаются углерод, фосфор, кремний и марганец, содержащиеся в передельном чугуне. Окисление данных примесей происходит за счет того, что оксид железа, образующийся в расплавленной ванне металла, отдает кислород более активным примесям, тем самым окисляя их.
Производство стали предполагает прохождение трех стадий, каждая из которых имеет свое значение. Рассмотрим их подробнее.
Расплавление породы
На данном этапе расплавляется шихта и формируется ванна из расплавленного металла, в которой железо, окисляясь, окисляет примеси, содержащиеся в чугуне (фосфор, кремний, марганец). В процессе этого этапа производства из сплава необходимо удалить фосфор, что достигается за счет содержания в шлаке расплавленного оксида кальция. При соблюдении таких условий производства фосфорный ангидрид (Р2О5) создает с оксидом железа (FeO) неустойчивое соединение, которое при взаимодействии с более сильным основанием — оксидом кальция (CaO) — распадается, и фосфорный ангидрид превращается в шлак.
Чтобы производство стали сопровождалось удалением из ванны расплавленного металла фосфора, необходима не слишком высокая температура и содержание в шлаке оксида железа. Чтобы удовлетворить эти требования, в расплав добавляют окалину и железную руду, которые и формируют в ванне расплавленного металла железистый шлак. Содержащий высокое количество фосфора шлак, формирующийся на поверхности ванны расплавленного металла, удаляется, а вместо него в расплав добавляются новые порции оксида кальция.
Кипение ванны расплавленного металла
Дальнейший процесс производства стали сопровождается кипением ванны расплавленного металла. Такой процесс активизируется с повышением температуры. Он сопровождается интенсивным окислением углерода, происходящим при поглощении тепла.
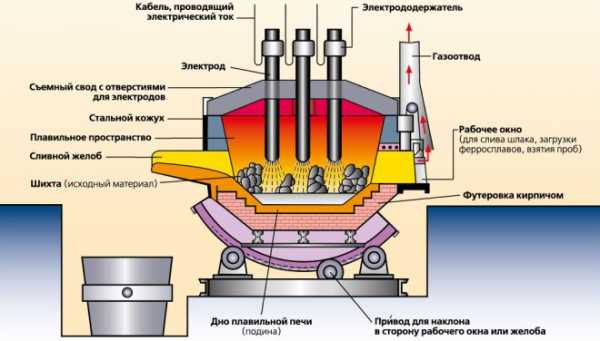
Процесс производства стали в электропечах
Производство стали невозможно без окисления излишков углерода, такой процесс запускают при помощи добавления в ванну расплавленного металла окалины или вдувания в нее чистого кислорода. Углерод, взаимодействуя с оксидом железа, выделяет пузырьки оксида углерода, что создает эффект кипения ванны, в процессе которого в ней снижается количество углерода, а температура стабилизируется. Кроме того, к всплывающим пузырькам оксида углерода прилипают неметаллические примеси, что способствует уменьшению их количества в расплавленном металле и приводит к значительному улучшению его качества.
На данной стадии производства из сплава также удаляется сера, присутствующая в нем в форме сульфида железа (FeS). При повышении температуры шлака сульфид железа растворяется в нем и вступает в реакцию с оксидом кальция (CaO). В результате такого взаимодействия образовывается соединение CaS, которое растворяется в шлаке, но раствориться в железе не может.
Раскисление металла
Добавление в расплавленный металл кислорода способствует не только удалению из него вредных примесей, но и увеличению содержания данного элемента в стали, что приводит к ухудшению ее качественных характеристик.
Чтобы уменьшить количество кислорода в сплаве, выплавка стали предполагает осуществление процесса раскисления, который может выполняться диффузионным и осаждающим методом.
Диффузионное раскисление предполагает введение в шлак расплавленного металла ферросилиция, ферромарганца и алюминия. Такие добавки, восстанавливая оксид железа, снижают его количество в шлаке. В результате растворенный в сплаве оксид железа переходит в шлак, распадается в нем, высвобождая железо, которое возвращается в расплав, а высвобожденные оксиды остаются в шлаке.
Производство стали с осаждающим раскислением осуществляется путем введения в расплав ферросилиция, ферромарганца и алюминия. Благодаря наличию в своем составе веществ, обладающих большим сродством к кислороду, чем железо, такие элементы образуют соединения с кислородом, который, отличаясь невысокой плотностью, выводится в шлак.
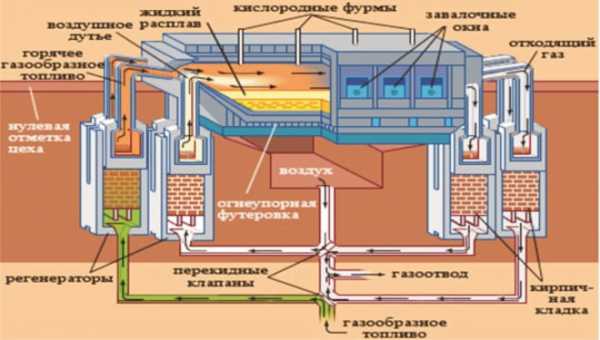
Производство стали в мартеновских печах
Регулируя уровень раскисления, можно получать кипящую сталь, которая не полностью раскислена в процессе плавки. Окончательное раскисление такой стали происходит при затвердевании слитка в изложнице, где в кристаллизующемся металле продолжается взаимодействие углерода и оксида железа. Оксид углерода, который образуется в результате такого взаимодействия, выводится из стали в виде пузырьков, также содержащих азот и водород. Полученная таким образом кипящая сталь, содержит незначительное количество металлических включений, что придает ей высокую пластичность.
Производство сталей может быть направлено на получение материалов следующего типа:
- спокойных, которые получаются, если в ковше и печи процесс раскисления полностью завершен;
- полуспокойных, которые по степени раскисления находятся между спокойными и кипящими сталями; именно такие стали раскисляются и в ковше, и в изложнице, где в них продолжается взаимодействие углерода и оксида железа.
Если производство стали предполагает введение в расплав чистых металлов или ферросплавов, то в результате получаются легированные сплавы железа с углеродом. Если в стали данной категории необходимо добавить элементы, которые имеют меньшее сродство к кислороду, чем железо (кобальт, никель, медь, молибден), то их вводят в процессе плавки, не опасаясь за то, что они окислятся. Если же легирующие элементы, которые необходимо добавить в сталь, имеют большее сродство к кислороду, чем железо (марганец, кремний, хром, алюминий, титан, ванадий), то их вводят в металл уже после его полного раскисления (на окончательном этапе плавки или в ковш).
Необходимое оборудование
Технология производства стали предполагает использование на сталелитейных заводах следующего оборудования.
Участок кислородных конверторов:
- системы обеспечения аргоном;
- сосуды конверторов и их несущие кольца;
- оборудование для фильтрации пыли;
- система для удаления конверторного газа.
Участок электропечей:
- печи индукционного типа;
- дуговые печи;
- емкости, с помощью которых выполняется загрузка;
- участок складирования металлического лома;
- преобразователи, предназначенные для обеспечения индукционного нагревания.
Участок вторичной металлургии, на котором осуществляется:
- очищение стали от серы;
- гомогенизация стали;
- электрошлаковый переплав;
- создание вакуумной среды.
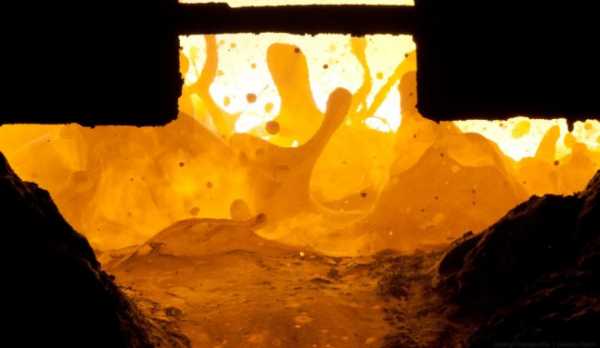
Кипящая сталь
Участок для реализации ковшовой технологии:
- LF-оборудование;
- SL-оборудование.
Ковшовое хозяйство, обеспечивающее производство стали, также включает в себя:
- крышки ковшей;
- ковши литейного и разливочного типа;
- шиберные затворы.
Производство стали также предполагает наличие оборудования для непрерывной разливки стали. К такому оборудованию относится:
- поворотная станина для манипуляций с разливочными ковшами;
- оборудование для осуществления непрерывной разливки;
- вагонетки, на которых транспортируются промежуточные ковши;
- лотки и сосуды, предназначенные для аварийных ситуаций;
- промежуточные ковши и площадки для складирования;
- пробочный механизм;
- мобильные мешалки для чугуна;
- оборудование для обеспечения охлаждения;
- участки, на которых выполняется непрерывная разливка;
- внутренние транспортные средства рельсового типа.
Производство стали и изготовление из нее изделий представляет собой сложный процесс, сочетающий в себе химические и технологические принципы, целый перечень специализированных операций, которые используются для получения качественного металла и различных изделий из него.
Оценка статьи:
Загрузка…Поделиться с друзьями:
met-all.org
Основы современного сталеплавильного производства | Металлургический портал MetalSpace.ru
Сталеплавильный процесс
Сталеплавильный процесс представляет собой сложную систему, в ходе которого выделяется или поглощается теплота, достигается или нарушается равновесие протекающих реакций, происходят другие энергетические процессы.
Для характеристики состояния системы используют величины, называемые параметрами состояния. Параметрами состояния являются давление, объем, концентрация, температура. Величины, характеризующие процесс или изменение системы, связанное с изменением параметров состояния, называют параметрами процесса. Ими являются:
- тепловой эффект реакции, Q;
- изменения свободной энергии, ΔG или изменение изобарного потенциала;
- изменение энтропии, ΔS;
- изменение энтальпии, ΔH;
- изменение давления, ΔP.
В сталеплавильной практике обычно приходится иметь дело с процессами, протекающими при постоянном давлении. Поэтому при буквенных символах параметров ставят индекс Р (давление). Например, Qр – тепловой эффект при постоянном давлении, Кр – константа равновесия процесса и так далее.
Характеристикой возможности протекания процесса служит величина изменения свободной энергии системы ΔG=ΔH — TΔS
Если величина ΔG меньше нуля, то при данной реакции выделяется энергия, идет самопроизвольный процесс. Если величина ΔG равна нулю, то это означает, что реакция достигла состояния равновесия. Если же величина ΔG больше нуля, то это значит, что самопроизвольный процесс протекать не может, и реакция протекает в обратном направлении.
Величина константы равновесия Кр характеризует в какой степени реакция протекает в ту или иную сторону. Величина ΔG и Кр связаны между собой соотношением:
ΔG=ΔH-TΔS
Можно записать
-RT*lnKp=ΔH−TΔS
R*lnKp=ΔS−ΔH/T
Следовательно, чем больше ΔS и чем меньше ΔН, тем полнее протекает реакция и чем выше температура, тем большее значение величины ΔS (выше энтропийный фактор) и меньшее величины ΔН (энтальпийный фактор).
В сталеплавильных агрегатах в большинстве случаев реакции протекают в растворах или с образованием растворов. Металл и шлак представляют собой растворы. Свойства же веществ в растворах отличаются от их свойств в чистом виде. Обычно для реакций в растворах значения концентраций компонентов заменяют значениями активностей этих компонентов в данном растворе. Активность компонента x обозначается ах и связана с концентрацией компонента соотношением:
ax=γx*Nx
где Nх – молярная концентрация компонента,
γx – коэффициент активности.
При рассмотрении реакций, в которых компонент растворен в металле, принято обозначать его в квадратных скобках. Например, углерод [С], раство-ренный в металле, марганец, растворенный в металле [Mn], и так далее. В тех случаях, когда речь идет о концентрации компонента в шлаке, используют кру-глые скобки. Например, (MnO), (FeO). И реакция, происходящая между раство-ренным марганцем в металле и растворенным оксидом железа в шлаке запи-шется в виде:
[Mn]+(FeO)=(MnO)+ Feж
Основными материалами для производства стали являются:
- передельный чугун;
- стальной лом (скрап).
Состав стали отличается от чугуна пониженным содержанием углерода и примесей (таблица 2).
Таблица 2- Состав передельного чугуна и низкоуглеродистой стали.
Материал | Состав, % | ||||
С | Si | Mn | P | S | |
Передельный чугун |
4-4,4 | 0,75-1,25 | До 1,75 | 0,15-0,3 | 0,03-0,07 |
Сталь низкоуглеродистая |
0,15-0,2 | 0,12-0,30 | 0,40-0,65 | 0,05 | 0,055 |
Поэтому сущностью передела чугуна в сталь является снижение содержа-ния углерода и примесей путем окисления их и удаления в шлак. В сталеплавильной практике особое значение имеют реакции окисления. Кислород для протекания этих реакций поступает из атмосферы, из железной руды или при продувки ванны кислородом.
Окисление углерода
Углерод, растворенный в металле, окисляется с образованием газа (СО) по реакциям:
[С]+1/2 О2г=СОг
кислородом, содержащимся в газовой фазе,
[С]+(FeO)=Feж+ СОг
кислородом, содержащимся в оксиде железа шлака,
[C]+[O]=COг
кислородом, растворенным в металле.
Повышение температуры во всех случаях благоприятствует протеканию реакции окисления углерода. Реакция окисления углерода занимает особое место в сталеплавильном производстве. Дело в том, что образующаяся при окислении углерода газовая фаза в виде пузырьков СО перемешивает ванну, выравнивает состав и темпе-ратуру металла, способствует процессу удаления газов и неметаллических включений.
Окисление кремния
Растворенный в металле кремний может окислятся по реакциям:
[Si]+O2г=(SiO2)
кислородом, содержащимся в газовой фазе,
[Si]+2(FeO)=(SiO2)+2Feж
кислородом, содержащимся в оксиде железа шлака,
[Si]+2[O]=SiO2
кислородом, растворенным в металле.
Эти реакции сопровождаются выделением большого количества тепла. При повышении температуры могут создаваться благоприятные условия для обратного восстановления некоторого количества кремния, когда в кислых про-цессах активность SiO2 в шлаке высока, а окисленность шлака мала. Повышение окисленности шлака способствует процессам окисления и удаления кремния и препятствует его восстановлению. Восстанавливать кремний из кислого шлака могут углерод, марганец, железо.
Окисление марганца
Марганец, растворенный в металле может окисляться по реакциям:
[Mn]+1/2O2г=(MnO)
кислородом содержащимся в атмосфере,
[Mn]+(FeO)=(MnO)+Feж
кислородом, содержащимся в оксиде железа шлака,
[Mn]+[O]=(MnO)
кислородом, растворенным в металле.
При повышении температуры плавки существует возможность протекания обратного процесса-восстановления марганца и перехода в металл. Марганец могут восстанавливать углерод, кремний, железо.
Температура, при которой прекратится окисление марганца и начнется его восстановление, зависит от состава металла и шлака. При кислом процессе закись марганца (MnO) вступает во взаимодействие с кислотными оксидами шлака и активность ее в кислом шлаке ниже, чем в основном. Поэтому в кислом процессе марганец окисляется легче и более полно, а восстанавливается менее полно, чем в основном.
На процессы окисления и восстановления марганца оказывает также вли-яние окисленность шлака. Чем выше окисленность шлака, тем полнее окисляется марганец и тем более высокая температура требуется для его восстановления.
Окисление фосфора
Фосфор является вредной примесью, ухудшает механические свойства стали при температурах ниже 0 °C и вызывает явление, называемое хладноломкостью. Фосфор попадает в сталь в основном из чугуна, так как в процессе доменной плавки он восстанавливается и переходит в чугун. Фосфор, растворенный в металле, может окислятся по реакциям:
4/5[P]+O2г=2/5(P2O5)
кислородом, содержащимся в атмосфере,
4/5[P] + (2FeO) = 2/5(P2O5)*2Feж
кислородом, содержащимся в оксидах железа шлака,
4/5[P]+2[O]=2/5(P2O5),
кислородом, растворенным в металле.
При повышении температуры могут создаться благоприятные условия для восстановления фосфора и перехода его снова в металл. Для того, чтобы удалить фосфор из металла и удержать его в шлаке, необходимо снижать активность Р2О5 в шлаке, путем наведения основного шлака с помощью добавок извести. При взаимодействии металла со шлаком, содержащим оксиды железа и кальция, протекает реакция:
2[P] + 5(FeO) + 4(CaO)4*(P2O5)
Образующееся прочное соединение )OP()CaO(524⋅связывает фосфор и пе-реводит его в шлак даже при высоких температурах.
Уменьшить активность Р2О5 в шлаке и тем самым способствовать удалению фосфора из металла можно путем смены шлака. Шлак, содержащий какое-то количество фосфора, близкое к равновесному с металлом, удаляют из агрегата (скачивают), а вместо него с помощью добавок, не содержащих фосфор, наводят новый шлак. После такой операции некоторое количество фосфора из металла переходит в новый шлак, пока не установится состояние, близкое к равновесию. Операцию скачивания и замены его новым шлаком можно проводить несколько раз до тех пор, пока в металле не останется очень мало фосфора. Такой метод используют при необходимости получить очень низкие концентрации фосфора в металле.
Удаление серы
Сера является вредной примесью, придает металлу крас-ноломкость, связанную с выделением при кристаллизации стали в межзеренном пространстве сульфидов железа, которые с железом образуют эвтектику, плавя-щуюся при температурах ниже 1000 °С. Слиток стали, содержащий большое количество серы, разрушается при горячей пластической обработке (ковка, штамповка, прокатка). При этом про-слойки, разобщающие зерна стали, находятся в жидком состоянии и способст-вуют разрушению металла при его деформации. Поэтому в большинстве случаев одной из главных задач при выплавке стали является удаление из металла серы.
В сталеплавильном агрегате удаление серы из расплавленного металла в шлак происходит в результате реакции:
Fe+[S]+CaO=(CaS)+(FeO)
Образующийся при реакции сульфид кальция CaS нерастворим в металле. Реакция протекает на поверхности раздела фаз (металл-шлак) и увеличение этой поверхности (перемешивание металла со шлаком, вдувание в металл CaO в виде порошка и другие способы) ускоряет эту реакцию и способствует более полному удалению серы. Если шлак, кроме СаО, содержит много MnO, то возможно удаление серы по реакции:
Fe+[S]+(MnO)=(MnS)+(FeO)
Образующийся сульфид марганца MnS почти нерастворим в металле и пе-реходит шлак. Скачивание шлака и наведение нового (чистого по сере) шлака также спо-собствует переходу новых порций серы из металла в шлак. Таким образом, для удаления примесей в плавильном агрегате для каждой из них создают определенные условия, проводя выплавку стали в несколько этапов.
ПОДЕЛИСЬ ИНТЕРЕСНОЙ ИНФОРМАЦИЕЙ
metalspace.ru
Сталелитейное производство — Справочник химика 21
Экономика сталелитейного производства [c.100]Огромна роль неорганических фторидов в технологии металлов вообше. Прежде всего следует вспомнить старое, как мир , сталелитейное производство. Почти половина всего добываемого флюорита (а это миллионы тонн) расходуется именно при выплавке стали, и потребности в металлургическом флюорите растут. [c.133]
Другим источником получения угольного газа в некоторых странах был коксовый газ — неизбежный побочный продукт нагревания каменных углей в коксовой печи при получении металлургического кокса в чугуноплавильном и сталелитейном производствах. Делались также попытки вырабатывать низкокалорийный газ в процессе газификации угля, чтобы затем из промежуточного газа синтеза (смеси окиси углерода и водорода) получать такие промышленные химические вещества, как аммиак и метанол. Однако эти разработки не нашли широкого применения в основном по двум причинам цены на уголь, особенно после Второй мировой войны, во многих районах земного шара, в частности в Европе, поднялись до уровня, намного превышающего цены на импортируемое жидкое нефтяное топливо открытие месторождений природного газа с высоким содержанием метана привело к замене им угольного газа во многих существующих газораспределительных сетях, например на юге Франции и в Италии. [c.13]
Решающий шаг в совершенствовании сталелитейного производства был сделан в 50-х годах XX века разработкой кислородно-конвертерного метода выплавки стали, который позволил использовать в качестве сырья не только чугун, но и стальной лом и руду, существенно повысить производительность и улучшить качество стали. В настоящее время этот метод, наряду с электроплавильным, преобладает. [c.49]
Гальванические осадки могут быть использованы при проведении соответствующей технологической и экологической экспертизы в черной металлургии в качестве легирующих добавок в сталелитейном производстве [88]. В этом случае к отходам гальванических производств предъявляют ряд требований они должны иметь определенный химический состав, а влажность не должна превышать 10 %. Допускается наличие в осадках Ре, Сг, N1, Са, но ограничивается содержание 2п, С1, Р, 8, Р. [c.66]
При анализе различных сплавов успешно применяют методы пламенной спектрофотометрии. В объектах сталелитейного производства натрий определяют с помощью пламенных фотометров и спектрофотометров. В последнем случае фоновое излучение железа, хрома и других компонентов в меньшей степени влияет на результаты анализа. Отмечается, что при использовании пламенного фотометра ФПФ-58 определению натрия не мешают 500 г/л хрома, 50 г/л железа, 2 г/л алюминия [15]. При больших содержаниях железа и хрома вводят поправку на фоновое излучение. [c.167]
Восстановление углеродом. Углерод с древнейших времен использовали в качестве восстановителя при выплавке металлов, он и сейчас находит широкое применение в сталелитейном производстве. Между углеродом и кислородом происходят следующие равновесные взаимодействия [c.142]
В сталелитейном производстве с 1957 г. начался массовый перевод мартеновских печей с мазута на газ. Производительность печей при этом повысилась на 5 %, а экономия топлива составила 5—6 %. [c.131]
Воду можно рассматривать как возобновляемый ресурс. Одна-ко, сравнивая стоимость необходимого для очистки оборудования со стоимостью водопроводной воды, очистку загрязненной органическими веществами воды обычно считают неэкономичной. Повторное использование промышленных сточных вод экономично только в тяжелой промышленности (энергетика,, сталелитейное производство и угледобывающая промышленность), где можно применять не такую чистую воду, как питьевая, и поэтому свести к минимуму обработку сточных вод. Основные трудности здесь связаны с наличием соединений, не поддающихся переработке. Возможно, эту проблему удастся решить, используя микроорганизмы, которые приобрели способность разрушать такие соединения (разд. 6.7). [c.270]
Освоить в промышленных масштабах обогащённое кислородом дутьё в доменном и сталелитейном производстве . [c.189]
Помимо железных руд, для выплавки чугуна используются шлаки сталелитейного производства, которые содержат 10—15% железа, сварочные шлаки (45—50% железа), железная окалина (до 70% железа), пиритный огарок. [c.173]
Кислород (вернее обогащенный кислородом воздух) применяют в доменном и сталелитейном производствах для ускорения процесса выплавки чугуна и стали, в цветной металлургии для [c.38]
Применение принудительного охлаждения в сталелитейном производстве способствует удлинению срока службы изложниц и улучшению структуры слитков. [c.383]
В ряде случаев нет необходимости использовать установку, имеющую в своем составе оборудование для обеспечения производства как чистого кислорода, так и чистого азота, в связи с тем, что потребителю необходим только един продукт (например, для ряда сталелитейных производств обычно не нужен чистый азот, а для предприятий химической промышленности не нужен технический кислород). Поэтому были созданы установки БР-1 А и БР-1 К. Первая установка имеет номинальную производительность в 12 500 ж /ч технологического кислорода концентрацией 95% Оа и 3500 м ч чистого сухого азота концентрацией 99,9% N3, вторая — 9000 м ч технологического кислорода и 3500 м ч сухого технического кислорода концентрацией 99,5% О . [c.48]
Мартеновский шлак — отход сталелитейного производства, содержащий не менее 80% углекислого кальция в виде силикатов кальция и магния. В качестве полезных примесей в нем находится фосфор, марганец и многие другие микроэлементы. [c.42]
Шлак сталелитейного производства завода им. В, И. Ленина Шл. от. 20 — 60 — — — [c.190]
Шлак сталелитейного производства Кировского завода Шл. Кир. 15-20 55-65 1-5 10-20 1-5 [c.190]
На протяжении 250 лет завод неоднократно подвергался реконструкции. Последняя реконструкция с 1976 по 1985 г. позволила расширить мощности сталелитейного производства до 10000 т с введением в строй корпуса оболочкового литья и расширить мощности кузнечного производства до 12000 т Это позволило устранить дисбаланс заготовительного и механосборочного производства. [c.13]
Для чугунолитейного производства Для сталелитейного производства [c.275]
Производство сжиженного кислорода является важным направлением в перерабатывающей промышленности. В настоящее время в США его производится порядка 13 млн. т в год, из которых 70% идет на нужды сталелитейной промышленности, а еще 10% — на другие металлоплавильные производства. В 1982 г. по объему производства сжиженный кислород занимал четвертое место после серной кислоты, азота и аммиака [Ма1ра5,1984]. Основное количество сжиженного кислорода производится на тех же предприятиях, где он и потребляется. Некоторые сталелитейные производства потребляют до 1000 т сжиженного кислорода в день. С установок по сжижению жидкий кислород может транспортироваться по трубопроводам. Одна из английских установок, где получают сжиженный кислород, имеет разветвленную сеть трубопроводов с общей [c.443]
Титрование по Рейнгардту — Циммерману. Важнейшим применением перманганатометрического титрования является определение Fe(II) в солянокислом растворе по Рейнгардту— Циммерману, так как в лабораториях металлургических и сталелитейных производств анализируемые пробы металлов обычно растворяют в соляной кислоте. С термодинамических позиций хлорид может окисляться перманганатом количественно, как это видно из значений стандартных потенциалов для Практически реакция проходит только в сильнокислых или концентрированных растворах хлоридов, в противном случае она замедлена. Е5 присутствии ионов Ре(П) реакция индуцируется, так что Ре(П) нельзя титровать перманганатом в солянокислой среде. Эту трудность преодолевают, добавляя к титруемому раствору большое количество соли Мп(П) и фосфорную кислоту. [c.173]
Основную долю себестоимости стали и стальных изделий (прокат) составляют затраты на материалы и энергию. В РФ 92% всех конструкций изготавливаются с использованием металлов, главным образом, черных. Продукция металлургической отрасли производства составляет около 70% всего ВНП. Поэтому, ма-териало- и энергоемкость сталеплавильного производства имеет большое экономическое значение. В табл. 5.2 приведены данные по энерго- и материалоемкости сталелитейного производства в различных странах по состоянию на 1992 год. [c.75]
Ориентировочные данные о концентрации загрязняющих веществ на поверхности, полученные расчетным путем (см. выше), основаны на предположении спокойной атмосферы и ровной открытой местности. Однако тагкого географического рельефа может не быть в той местности, где расположен завод. Например, важными экономическими факторам и, влияющими на выбор месторасположения предприятий тяжелой промышленности, являются сырьевая база, наличие поблизости угля или железнорудных месторождений для сталелитейного производства или речная долина, обеспечивающая дешевое транспортирование продуктов на баржах или судах. [c.43]
Волокно из нержавеющей стали со средним диаметром нити 5 мкм превращено в войлочную набивку, проникасмость которой 0,019 mV при нормальных температуре и давлении. Рассмотрите возможность использования такой набивки в качестве фильтра для горячих газов в сталелитейном производстве при следующих условиях [c.582]
Принципиальная схема кислородного компрессора 4ГМ10-40/35, служащего для подачи кислорода в конверторы малой емкости сталелитейных производств, представлена на рис. 12.7, в. Компрессор четырехрядный, трехступенчатый с двумя цилиндрами первой ступени он выполнен на унифицированной оппозитной базе 4М10 с пониженной средней скоростью поршня (Сср = = 2,75 м/с) в бесподвальном исполнении. В каждом ряду компрессора размещено по одному цилиндру, что обеспечивает простоту обслуживания, ремонтопригодность и возможность для размещения клапанов повышенного проходного сечения. [c.334]
Определение легких газов, таких как водород, кислород, азот, диоксид углерода, монооксид углерода, аргон и водяной пар, может вьтолняться с помощью масс-спектрометрии. Учитывая чувствительность масс-спектрометров при определении этих газов, масс-спектрометрию для промышленного контроля обычно применяют в процессах ферментации [16.4-34], для контроля топочных газов в сталелитейном производстве [16.4-35]. Другим основным применением промышленной масс-спектрометрии является мониторинг окружающей среды и атмосферы [16.4-36-16.4-38]. Масс-спектрометры также часто используются для определения различных углеводородов. При анализе сложных смесей этих веществ наблюдаются значительные перекрьтания линий в масс-спектрах, поэтому необходимо использование специальных методов обработки спектральной информации. Кроме того, масс-спектрометры применяются для обнаружения течей в заводских вакуумных системах [16.4-39]. [c.662]
Расплав компонентов катализатора, собирающийся на дне плавильной печи перерабатывают путем литья или отверждения. В зависимости от типа катализатора, сплав может состоять в основном из МоСо, WNi, Mo oVNi и различных примесей, таких как сера, углерод, железо, титан и хром. После того как сплав механически отделяется от абразивного компонента, он может непосредственно использоваться в сталелитейном производстве или в производстве сплавов. Если примеси — сера, кремний, углерод — присутствуют в нежелательных количествах, сплав можир очищать любым подходящим способом. [c.15]
Интерес к газификации в расплаве железа проявляется также в Великобритании. Так, фирма «Дэви Макки» предлагает использовать в качестве, газогенераторов существующие кислородные конвертеры сталелитейных производств одновремевно это является- переходным этапом к промышленному внедрению процесса. [c.47]
Примером утилизации отходящего фтора в сталелитейном производстве является улавливающая установка близ г. Прово (штат Юта, США), принадлежащая фирме U.S. Steel ompany . [c.20]
Сталелитейная промышленность долгие годы занимала первое место, потребляя более 50% всего плавикового шпата. Однако в настоящее время, хотя потребление СаРа и не снизилось, она все же отступила на второе место вследствие роста потребления плавикового шпата для получения фтористоводородной кислоты. В 1959 г. в сталелитейном производстве было израсхо-довано около 178 тыс. т, или 33% всего плавикового шпата. [c.26]
Ниобий и тантал относятся к числу карбидообразующих элементов и -находят себе применение в сталелитейном производстве в качестве легирующих примесей. Ниобий долгое время считался вредной примесью к танталу. В настоящее время считается, что ниобий даже эффективнее тантала в том смысле, ЧТО благодаря вдвое меньшему атомному весу может заменять тантал в половинном количестве по весу, давая такой л[c.168]
Для широкого применения в тяжело нагруженных механизмах, работающих во влажной и коррозионной среде (при производстве бумаги, цемента, резины, сахара, в чугуно- и сталелитейном производстве). [c.322]
Поскольку нефтетонливо применяется дл 1 бункеровки, для которой оно очень хорошо подходит, учитывая, что оно в жидком состоянии, а также имея в виду технические преимущества нефти в таких областях, как сталелитейное производство, можно установить цену значительно выше угольного эквивалента , взвесив ее только исходя из теплотворной способности (калорийности). [c.545]
Кислород (вернее обогащенный кислородом воздух) применяют в доменном и сталелитейном производствах для ускорения процесса выплавки чугуна и стали, в цветной метайлургни для ускорения процесса обжига руд цветных металлов и в ряде других производств. [c.42]
Сырье для обмасливаыня металлургические порошков в сталелитейном производстве [c.196]
На фиг. 296 показана одноступенчатая центробежная воздуходувка с отношением давлений до двух. Такие машины производительностью от 400 до 40 ООО м Ыас применяются ддя сжатия газов коксовых, известковых и колошниковых печей. Одноступенчатые и многоступенчатые центробежные воздуходувки широко применяются -для наддува и продувки двигателей внутреннего сгорания всех типов. На фиг. 297 изображен центробежный нагнетатель для авиационного двигателя с приводом от турбины, работающей на выпускных газах. При окружной скорости 450 мкек нагнетатель имеет производительность 4 м 1сек и отношение давлений П = 4. На фиг. 298 показан двухступенчатый центробежный компрессор с окружной скоростью 300 мкек примерно для того же отношения давлений, но меньшей производительности. В доменном и сталелитейном производстве применяются двух- и многоступенчатые воздуходувки большой производительности (фиг. 299) с отношением давлений от 2 до 4. На фиг. 300 изображена воздуходувная станция [c.431]
chem21.info
Технологические особенности сталеплавильного производства
Сталеплавильное производство — это получение стали из чугуна и стального лома в сталеплавильных агрегатах металлургических заводов. Сталеплавильное производство является вторым звеном в общем производственном цикле черной металлургии.
Сталь – многокомпонентный сплав железа с углеродом (С < 2,14%), кремнием, марганцем, серой, фосфором и другими примесями. Содержание углерода 2,14% соответствует максимальной растворимости углерода в аустените, находящемся в равновесии с цементитом при эвтектической температуре.
На современном этапе основными способами производства стали являются мартеновский, кислородно-конвертерный и электросталеплавильный. По своей природе они являются окислительными, так как превращение чугуна в сталь осуществляется путем снижения углерода и других примесей в результате их окисления. Вместе с тем, это не означает, что в сталеплавильных процессах не протекают реакции восстановления. Такие элементы, как Mn, Si, Cr, P, окислившиеся в первые периоды плавки, могут при определенных условиях снова восстанавливаться и переходить в металл.
Для производства стали в сталеплавильные печи загружают шихтовые материалы, включающие две основных части, взятых в соотношениях, найденных предварительными расчетами.
Металлическая часть шихты — стальной лом, скрап, чугун, раскислители и легирующие добавки. Лом и скрап загружают в твердом виде, чугун применяют как в твердом, так и в жидком состоянии в зависимости от варианта сталеплавильного процесса. Металлическая часть шихты, кроме железа, содержит примеси (углерод, марганец, кремний, сера, фосфор и др.), количество которых регламентируют в зависимости от состава выплавляемого металла.
Неметаллическая часть шихты — флюсующие добавки (известь, известняк и т. п.), твердые окислители (железная руда, агломерат, окисленные окатыши и т.п.) и добавочные материалы (плавиковый шпат, марганцевая руда, боксит, песок, бой шамотного кирпича). Главными компонентами флюсующих добавок являются СаО в извести или СаСОз в известняке. Количество примесей регламентируют, ограничивая верхние пределы их содержаний (особенно содержания диоксида кремния, серы и фосфора). Главными компонентами твердых окислителей являются оксиды железа, содержание которых должно быть как можно более высоким; количества SiO2, серы и фосфора также ограничивают. Добавочные материалы используют для изменения свойств шлаков или для наведения новых шлаков.
При производстве стали применяют жидкое (мазут) или газообразное (природный, коксовый и доменный газы) топливо. Основными составляющими топлива являются углерод и водород, которые находятся в виде различных соединений, а также в топливе всегда присутствуют кислород, азот, сера, влага и зола.
Кислород для сжигания топлива получают преимущественно методом глубокого охлаждения (до -200 0С) и последующей ректификации (разделения) атмосферного воздуха в специальных установках.
Сталеплавильные процессы являются окислительными, в чем и заключается главное отличие от доменного. В сталеплавильных печах происходит окисление кремния, марганца, углерода и фосфора, а также в некоторой степени и железа, хотя это нежелательно. Сталеплавильные агрегаты работают периодически. После очередного выпуска расплавов осуществляют восстановление (заправку) огнеупорной футеровки, так как в местах контакта ее со шлаком в процессе плавки она частично растворяется и переходит в шлаковую фазу. После заправки загружают сыпучие материалы (флюс и твердые окислители), металлический лом (скрап) и заливают чугун (в электродуговую печь чугун загружают в твердом виде). В период плавления происходит расплавление твердой шихты и формирование жидкой ванны металла и шлака. В этот период окисляются частично железо, значительная часть фосфора, кремний, часть марганца и углерода. После расплавления осуществляют доводку металла по температуре и составу. В этот период происходит окисление избыточного углерода и перемешивание (барботаж) ванны выделяющимися пузырями монооксида углерода СО. Металл нагревается до температуры ~1650°С, его раскисляют и выпускают. Раскисление осуществляют введением в жидкий металл таких элементов (Мn, Si, Al и т.п.), которые прочно связываются с кислородом, растворенным в металле, т. е. обладают высоким сродством к кислороду. При этом образующийся оксид элемента-раскислителя не растворяется в металле, а переходит в значительной степени в шлаковую фазу.
Похожие статьи:
poznayka.org
Литейное производство — Википедия
Материал из Википедии — свободной энциклопедии
Литейное производство — отрасль машиностроения, занимающаяся изготовлением фасонных деталей и заготовок путём заливки расплавленного металла в форму, полость которой имеет конфигурацию требуемой детали.
В процессе литья, при охлаждении металл в форме затвердевает и получается отливка — готовая деталь или заготовка, которая при необходимости (повышение точности размеров и снижения шероховатости поверхности) подвергается последующей механической обработке. В связи с этим перед литейным производством стоит задача получения отливок, размеры и форма которых максимально приближена к размерам и форме готовой детали. В машинах и промышленном оборудовании от 50%-ти до 95%-ти всех деталей изготовляют способом литья в формы.
Для изготовления отливок в разовых песчаных формах необходима специальная литейная оснастка, от конструкции и качества которой в значительной мере зависит качество и трудоемкость производства литья.
Литейная оснастка по своей роли в процессе изготовления отливок подразделяется на формообразующую (основную) и универсальную (вспомогательную).
Формообразующая оснастка представляет собой модельный комплект, в который входят: модели, стержневые ящики, элементы литниковой системы, модельные плиты, шаблоны для изготовления форм и стержней.
Модель — приспособление для получения внутренних рабочих поверхностей в литейной песчаной форме, которые после заполнения расплавом образуют отливку.
Способ получения изделий путём литья их из металла известен уже более пяти тысяч лет. Первыми отливками были несложные предметы домашнего обихода и украшения, отливаемые из меди и бронзы: котлы, рукомойники, серьги, кресты, кольца и т. д.
Изготовление литых изделий осуществляется из литейных сплавов, к которым относятся:
- Чугуны — серый литейный, ковкий и высокопрочный.
- Медные сплавы — латуни и
ru.wikipedia.org