Щебеночно-мастичный асфальтобетон: технология производства и укладки
Среди разновидностей асфальтовых покрытий выделяется щебеночно-мастичный асфальтобетон, его отличает повышенные показатели упругости, водостойкости и сдвигоустойчивости. Использованные при изготовлении материала стабилизирующие компоненты делают покрытие шероховатым и стойким к расслаиванию.
Материал был разработан в 60-х годах XX века в Германии и быстро распространился по всему миру. За границей представлено более десятка видов ЩМА, в нашей стране только три — представлены ЩМА 10, 15 и 20.
Особенности
Щебеночно-мастичный асфальтобетон долговечное покрытие, которое используют по всему миру. Основа материала – каркас из щебня высокого качества, он позволит повысить стойкость к деформации готового покрытия.
Объем битумного раствора больше, чем у конкурентов. Он заполняет все доступное пространство, что снижает пористость массы. По итогу получается покрытие устойчивое к внешним воздействиям и сроком эксплуатации в несколько раз больше других видов асфальтобетона.
Основные отличия от других асфальтобетонных смесей:
- Содержание щебня больше на 20-30%, чем в обычном растворе;
- Повышенное количество битума в массе;
- Форма и размер щебня строго контролируются;
- Добавление стабилизирующих добавок.
Жесткие требования к размеру частиц щебня связаны с — наличием большого объема пустот, которые заполняются мастикой из битума и возведением каркаса. Частицы щебня взаимодействуют между собой, а это способствует повышению показателей сдвигоустойчивости.
Покрытие из ЩМА обладает высокими показателями износостойкости даже при использовании шипованных шин, и предохраняет дорогу от возникновения колеи.
Состав асфальтобетона ЩМА
Состав щебеночно-мастичного асфальтобетона строго регулируется ГОСТ 31015-2002 «Смеси асфальтобетонные и асфальтобетон щебеночно-мастичные».
При изготовлении используются следующие компоненты:
- Щебень;
- Битумный раствор;
- Очищенный песок;
- Специальные добавки для стабилизации раствора;
- Минеральный порошок по госту16557-78.
Важно! Если при изготовлении битум можно заменить полимерно-битумных вяжущим, в этом случае стабилизирующие добавки можно не использовать.
Для используемого сырья обязательно предъявляются несколько условий:
- Для ЩМА берется щебень твердых пород с однородными зернами кубовидной формы;
- Песок только очищенной, мелкой или средней фракции;
Важно! В растворе щебеночно-мастичного асфальта количество щебня от массы 70-80%, битумного вяжущего 5,5 – 7,5%.
Смеси ЩМА используются для прокладки городских дорог и скоростных автомагистралей, так же рекомендуется их применять на аэродроме, для укладки взлетных полос и сета для посадки.
Производители предлагают три варианта щебеночно-мастичных смесей асфальтобетона, главное отличие – размер щебня:
- ЩМА 10;
- ЩМА 15;
- ЩМА 20.
Добавки, используемые при изготовлении ЩМА
Так как в составе щебеночно-мастичной асфальтобетонной смеси находится повышенный объем щебня и нефтяного битума, требуется использование специальных добавок, которые стабилизуют массу и оградят ее от расслаивания.
Использование стабилизирующих добавок позволит сохранить однородность массы, насытить раствор требуемыми качествами и удержать горячий раствор на поверхности основы из щебня.
Преимущества, которые дает применение добавок:
- Увеличение толщины битумной пленки;
- Гарантирует однородность массы;
- Устойчивость к расслаиванию.
Тип компонентов для стабилизации имеет большое значение при изготовлении и транспортировке. Они отличаются друг от друга, но главное, что все добавки повышают качества асфальта.
Стабилизирующие добавки в виде гранул и волокон выпускаются из следующих материалов:
- резина;
- полимеры;
- акрил;
- асбест;
- целлюлоза;
Так же применяют добавки из различных минеральных компонентов и термопластичных полимеров.
Производители большее предпочтение отдают именно добавкам на основе целлюлозы. Компоненты находятся в доступной ценовой категории и способны необходимое время удерживать битумный раствор на щебневой основе, что в свою очередь гарантирует защиту от расслаивания массы.
Используемые волокна обязательно должны быть очищены от примесей, иметь однородную структуру и быть одной длины.
Свойства добавки на основе целлюлозы:
- Влажность -8%;
- Термостойкость при температуре 220 градусов – 7%;
- Содержание волокон длиной 0,1-2,0 мм – 80%.
Добавки в виде волокон имеют несколько отрицательных качеств — они впитывают воду их окружающей среды, в том числе воздуха, поэтому необходимо внимательно отнестись к герметичности упаковки. Так же волокно плохо распределяются по смеси, а это в свою очередь увеличивает время на замешивание.
Преимущества щебеночно-мастичного асфальтобетона
Асфальтобетон на основе щебеночно-мастичной массы широко применяется во многих странах для любых нужд. Он обладает целым рядом достоинств, которые выгодно отличают его от других типов асфальтных покрытий.
Основные плюсы материала:
- Водонепроницаемость покрытия;
- Низкая стираемость покрытия;
- Не возникает колея;
- Высокие показатели морозоустойчивости;
- Хорошие показатели усталостной стойкости;
- Устойчивость к механическим воздействиям;
- Сдвигоустойчивость готового асфальта;
- Долговечность – в два раза дольше обычного асфальта;
- Покрытие имеет шероховатую поверхность, оно обеспечивает лучшее сцепление автомобиля с дорогой;
- Устойчивость к появлению трещин;
- Низкие показатели шума при движении автотранспортного средства;
- Устойчивость к климатическому воздействию.
Щебеночно-мастичный асфальтобетон это улучшенный вид асфальтобетона, его технические качества способствуют комфортному и безопасному движению по дороге.
Технология производства
Изготовление раствора щебеночно-мастичного асфальта предполагает смешивание предварительно нагретых щебня и песка в специальном смесителе с постепенным добавлением других компонентов:
- Минеральный порошок;
- Нефтяной битум или ПВБ;
- Добавки для стабилизации раствора (гранулы или волокна).
Температура готовки массы ШМА выше на 25 – 35 градусов больше обычных растворов. Повышенная температура требуется, потому что в отличии от обычного асфальта, смесь ложится более тонким слоем.
Важно! Заранее определитесь с видом связующей добавки.
Этапы приготовления раствора ЩМА:
- Собрать и подготовить необходимый щебень и песок – сырье должно быть определенной фракции, очищено от посторонних примесей, просеяно, хорошо просушено и дозировано.
- Отмерить нужное количество холодной добавки для стабилизации массы и минерального порошка;
- Подготовить битум – постепенно разогреть в специальной емкости и добавить модифицирующие компоненты, тщательно вымешать раствор.
- Отдельно смешать все сухие компоненты;
- Залить сухие элементы с горячим раствором нефтяного битума, постепенно вливая и тщательно размешивая до однородной структуры.
Полученная масса выгружается в специально оборудованные самосвалы – кузов с подогревом и защитный тент, и перевозится к месту асфальтоукладочных работ. Раствор используется в течение нескольких часов.
По технологии укладки щебеночно-мастичного асфальтобетона разрешается его применение как в мелких ручных работах при заделывании трещин и неровностей, так и полной укладки полотна дороги.
Укладка щебеночно-мастичного асфальтобетона
Согласно технологии укладки асфальта на щебеночно-песчанную смесь работы по починке или укладки дороги проводятся только в сухую теплую погоду:
- В весенний период температура от +5 градусов;
- В осеннее время года – минимум +10 градусов.
Примерный расход раствора от 50 – 150 кг/м 2, показатель средней толщины щебеночного основания под асфальт зависит от типа щебеночно-мастичного асфальтобетона:
- Для ЩМА 10 – толщина составляет 2-4 см,
- Для ЩМА 15 – толщина слоя — 3-5 см,
- Для ЩМА 20 – толщина слоя равна 4-6 см.
Процесс укладки щебеночно-мастичной смеси асфальтобетона
- Подготовка основания – поверхность очищают от старого покрытия (при необходимости), выравнивают, устраняют неровности, тщательно зачищают металлическими щетками. Затем при помощи сжатого воздуха сдувают пыль, грязь и мелкие частицы.
- Грунтовка поверхности – очищенное основание предварительно грунтуют жидким битумным раствором, это обеспечит оптимальный уровень сцепления ЩМА с поверхностью.
- Укладка смеси – несколько асфальтоукладчиков ставятся рядом с уступом, расстояние между техникой не более 30 см. машины должны быть оснащены системой горизонтального уровня с поперечным уклоном. Горячая смесь поступает непрерывно и равномерно распределяется по всей ширине дороги.
- Уплотнение массы – после укладки асфальта необходимо уплотнить массу с помощью катков, вес которых не меньше 8 – 10 тонн. Валы в обязательном порядке регулярно смазываются для облегчения работы, избежание прилипания и повреждения поверхности. Для этого используют либо эмульсию на основе керосина, либо обычный мыльный раствор.
- На готовом полотне не допускается дефекты, если они есть, то их необходимо сразу же устранить. Устранение происходит ручным методом – работники добавляют горячий раствор в проблемное место и трамбуют небольшими самоходными катками.
Важно! ЩМА укладывается тонким слоем, при этом сохраняет все свои технологические свойства.
Возможные проблемы и причины их возникновения
При несоблюдении правил укладки, перевоза материал или его утрамбовывания могут возникнуть различные проблемы. Самые распространенные из них:
- Раствор битума проявляется на поверхности готового покрытия – это проблема возникает при превышении установленной нормы объема битума в самом растворе ЩМА или при проведении предварительно грунтования основания.
- Появление сети мелких трещин на дорожном полотне – при уплотни асфальтобетона, смесь имела слишком низкую температуру.
- Возникновение широких трещин на асфальте – этот недостаток указывает на проблемы с укладчиком: плохой прогрев плит.
- Плохие показатели сдвигоустойчивости покрытия – этот недостаток проявляется, если на начальном этапе работ была использована геосетка с размером ячейки меньше или больше требуемой нормы.
Щебеночно-мастичный асфальтобетон по праву занимает лидирующие позиции при строительных работах по укладке дорожного покрытия. Его главные свойства – износостойкость, долговечность и безопасность, за счет шершавой поверхности, позволяют использовать материал для покрытия высоконагруженных мест — скоростных магистралей, аэропортов, морских портов.
betonov.com
Как производят, изготавливают асфальт? | Сыпучие материалы в Петербурге
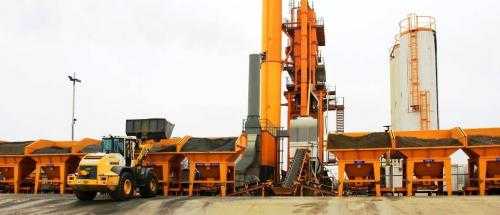
Содержание:
Получение битума из нефти Приготовление асфальтовой смеси Температурные условия для горячего асфальта Комплект оборудования Подготовка песка и щебня
Покрытие из асфальтобетона имеет очевидные преимущества:
- Дорожное полотно ровное, устойчивое к изнашиванию и повреждениям.
- Поверхность легко очищается, при этом на ней долго держится дорожная разметка.
- Покрытие практически готово к использованию по окончанию укладки.
- Поверхность имеет шероховатую структуру, что обеспечивает хорошее сцепление с дорогой колес транспортных средств.
Асфальт изготавливают под воздействием высоких температур с использованием природного либо дробленого песка. Вместо щебня в его составе может присутствовать гравий. Битум имеет органическое происхождение и оказывает вяжущее воздействие на получаемую смесь. При необходимости добавляют минеральный порошок.
Примерное соотношение названных элементов в асфальтовой смеси из трех компонентов следующее: не менее 80% дробленого щебня (гравия), около 6% битума и 10% песка.
Получение битума из нефти
Необходимым компонентом асфальтобетонных смесей является вязкий битум. Природный битум (асфальт – одна из его разновидностей) – это остаточный продукт переработки нефти. Технологически процесс получения битума на нефтеперерабатывающем комбинате выглядит так:
- Из сырой нефти выделяют частицы путем нагревания с последующим испарением летучих веществ.
- Наряду с другими нефтепродуктами, частицы перегоняют в асфальт.
- Полученный асфальт соединяют с летучими веществами.
- Конечный продукт подвергают воздействию низких температур.
- В результате испарения летучих веществ образуется твердый битум.
Переработанный битум становится полноценным товарным продуктом.
Приготовление асфальтовой смеси
Производство асфальтовой смеси строится по этапам:
- Производится расчет состава и взвешивание компонентов.
- Элементы для изготовления смеси проходят контроль качества и проверку на наличие посторонних включений.
- Твердые компоненты обрабатываются путем просеивания песка и дробления камня.
- Минеральные элементы (при необходимости, в целях просушки) и битум подвергаются раздельному нагреванию.
- Ингредиенты соединяют и тщательно перемешивают, избавляя смесь от элементов воздуха.
- Горячую асфальтовую смесь помещают в силос, где она хранится в нагретом состоянии до 4-х суток.
Температурные условия для горячего асфальта
При изготовлении горячей асфальтовой смеси соблюдают температурный режим:
- Сыпучие материалы нагревают до 200˚C для выведения влаги.
- Все компоненты смешивают при 160˚C.
- Готовая смесь может храниться до нескольких суток при температуре не менее 150˚C.
Комплект оборудования
Оборудование для изготовления асфальта состоит из:
- Агрегата питания.
- Сушильного агрегата.
- Сортировочного агрегата.
- Хранилища для битума.
- Элеватора горячих материалов.
- Агрегата для смешивания.
- Бункера готовой смеси.
- Кабины управления.
Асфальтосмесительная установка, в которой осуществляются все операции, может быть передвижной либо стационарной, работать циклически или же непрерывно. Стационарная установка располагается на территории асфальтового завода. Передвижная установка монтируется на базе прицепа или колесного шасси и удобна в транспортировке.
Подготовка песка и щебня
Технологически процесс подготовки инертных материалов строится следующим образом:
- Погрузчик, кран или конвейер подает песок и щебень со склада в бункер агрегата питания.
- Далее песок и щебень при помощи конвейера либо элеватора загружаются в барабан сушильного агрегата.
- В барабане материалы сушатся и нагреваются до нужной температуры. Для этого насосом в барабан подается топливо в жидком или газообразном состоянии. Вентиляторы подают необходимый для его сгорания воздух.
- Образующиеся при сушке горячие газы проходят очистку от пыли, проходя через систему улавливания.
nerudr.ru
Асфальтобетон литой: особенности строительства
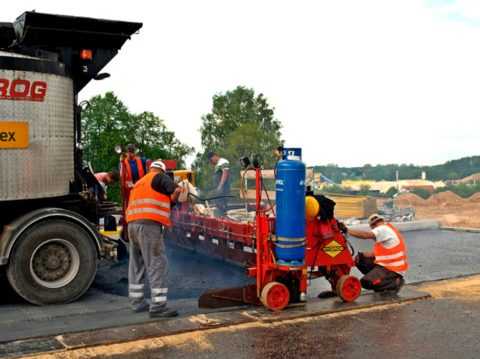
Укладка литого асфальтобетона
Асфальтобетон литой — это строительный материал, изготовленный по литьевой технологии на основе битумного вяжущего, минерального порошка, песка, щебня и специальных поверхностно активных добавок. Литая асфальтобетонная смесь готовится в смесителях принудительного действия путем смешивания в определенных пропорциях, нагретых до определенной температуры заполнителей и нефтяного битума.
Содержание статьи
Общая информация
Литые асфальтобетонные смеси обладают высокой подвижностью, поэтому легко распределяются по поверхности, и при рабочей температуре в 220°С укладываются в конструкцию дороги без уплотнения. С понижением температуры, данный материал затвердевает, образуя при этом прочное трещиностойкое и водонепроницаемое покрытие (см. видео в этой статье).
Асфальтобетоны, изготовленные с применением литой технологии, достаточно широко применяются при устройстве следующих видов дорожных покрытий:
- автомобильных дорог;
- городских улиц и площадей;
- мостовых сооружений;
- аэродромов;
- тоннелей;
- закрытых и открытых автостоянок;
- также используются для проведения ямочного ремонта дорожных конструкций.
Классификация и основные характеристики
Литые композиты отличаются друг от друга свойствами, фазовым составом асфальтобетонного вяжущего, количеством и качеством исходных минеральных компонентов, а также технологией изготовления.
Соотношение содержания компонентов асфальтовых смесей и область их применения, по ТУ на литой асфальтобетон, представлены в таблице ниже:
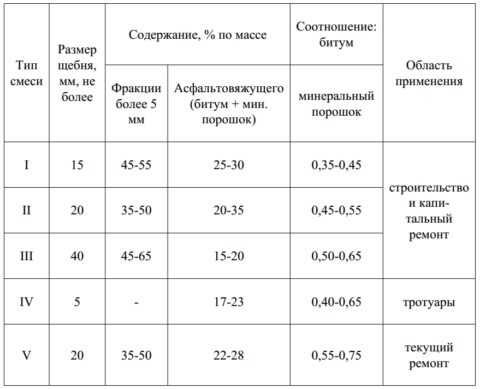
Состав литого асфальтобетона
В сравнении с классическими битумными растворами литые смеси обладают некоторыми отличительными характеристиками:
- повышенное содержание нефтебитумного вяжущего (11%) и минерального порошка (25%);
- большая вязкость;
- намного выше температура изготовления и укладки (220250°С).
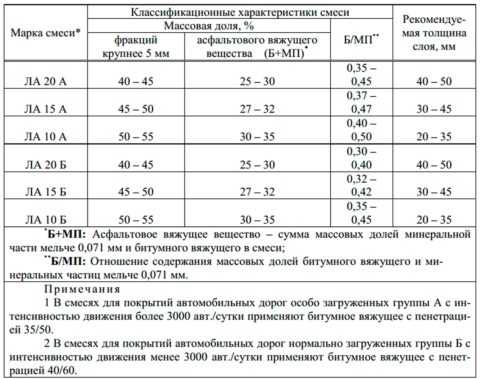
Классификация по маркам
В зависимости от применяемого вяжущего, литые асфальтобетоны могут иметь следующие составы:
- Стандартная смесь, приготовленная с использованием теплоустойчивого не модифицированного битума.
- Полимерасфальтобетон — в качестве основного компонента применяется полимерно-битумное вяжущее.
- Сероасфальтобетон — композитный материал. В качестве вяжущего выступают: модифицированная сера и дорожный битум. Использование технической серы позволяет снизить содержание битума в растворе и несколько уменьшить температуру приготовления.
- Резиноасфальтобетон — в качестве основного наполнителя используется резиновая крошка. Применение данного материала способствует повышению износостойкости покрытия, увеличивает его долговечность, и в ряде случаев, помогает сократить расход щебня.
Преимущества литого асфальтобетона:
- отсутствует необходимость уплотнения укладываемых слоев;
- повышенная коррозионная стойкость, износостойкость, водонепроницаемость;
- повышенная пластичность, содействующая поглощению напряжений;
- высокое сцепление с выше- или нижележащими слоями.
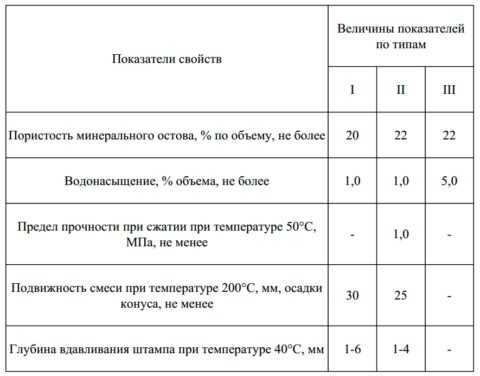
Показатели свойств
Наряду с рассмотренными преимуществами литые асфальтобетонные смеси обладают рядом существенных недостатков:
- высокая цена материала в сравнении с традиционными асфальтобетонами;
- при повышении температуры наблюдается низкая устойчивость пластическим деформациям (гребенка, колея и др.) ;
- невозможность укладки своими руками — устройство покрытий только с применением специальной техники и инструмента;
- высокая паронепроницаемость, что может приводить к образованию вздутий на поверхности укладываемых слоев, особенно при устройстве покрытий на цементобетонных основаниях.
Однако, исходя их многолетнего опыта использования материала, при технологически верно подобранном составе смеси, литой асфальтобетон 50 мм может с успехом выдерживать любые транспортные нагрузки в течении длительного промежутка времени.
Материалы
В зависимости от назначения, технологии укладки и условий эксплуатации покрытия состав литого асфальтобетона может варьироваться в соответствии с предложенной проектной документацией.
Стандартный набор компонентов представлен следующими материалами:
- нефтяной дорожный битум;
- песок;
- щебень или гравий;
- минеральный порошок.
- черный щебень.
Крупные заполнители — щебень
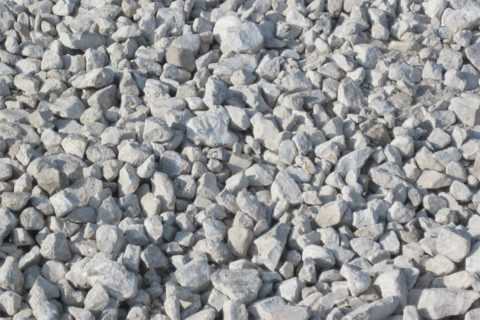
Щебень
Для производства щебня применяются прочные, морозостойкие горные породы или доменные металлургические шлаки. Прочность природных сырьевых материалов должна соответствовать 100–120 МПа, а пористых доменных шлаков более 80–100 МПа. Несколько пониженные требования к доменным шлакам компенсируются их хорошим сцеплением с вяжущим.
Щебень для литых смесей должен иметь остроугольную форму (куб, тетраэдр и пр.). Содержание плоских (лещадных) зерен ограничено 15%.
Подсказки: содержание пылеватых и глинистых частиц, в общем объеме заполнителя, не должно быть более 1%.
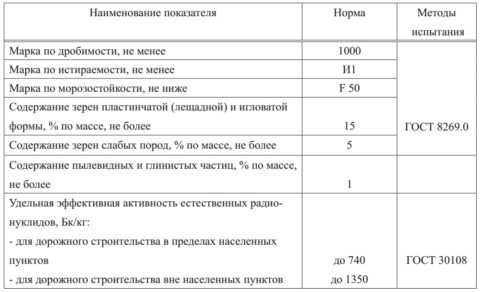
Требования, предъявляемые к щебню
Мелкий заполнитель — песок

Песок
Песок для приготовления литых асфальтобетонов получают путем дробления горных пород или кристаллических доменных шлаков. В зависимости от исходного материала, дробленый песок делят на два типа — марки 400 и 800.
Для производства первого вида применяют породы с прочностью не ниже 40 Мпа, второго — с прочностью более 80 Мпа. По фракциям — это средне- и крупнозернистые пески.
Подсказки: для обеспечения однородности асфальтобетонной смеси, мелкие заполнители, применяемые для приготовления раствора, должны быть постоянного (одинакового) зернового состава.
Характеристики песков и отсевов дробления, в зависимости от вида, марки и типа асфальта, должны соответствовать табличным значениям (см. фото).
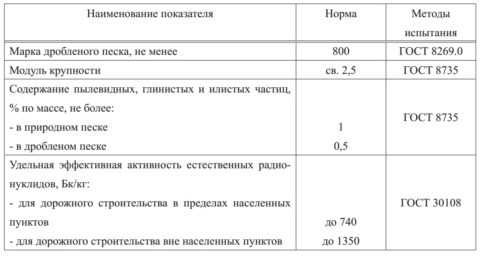
Требования к составу песка
Минеральный порошок
Данный материал является одним из главных структурирующих составляющих асфальтобетона.
Основное назначение порошка как наполнителя — это перевод нефтяного битума из объемного состояния в пленочное. Тем самым увеличивается вязкость и прочность структуры горячей литой смеси.
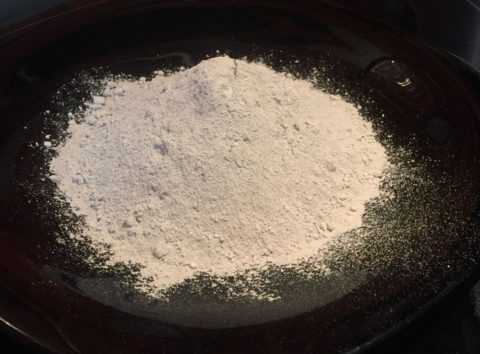
Минеральный порошок
Вместе с дорожным битумом минеральный структурирующий порошок образует качественную дисперсную систему, которая выполняет функции единого связывающего материала в растворе. Производят минеральный порошок путем размалывания известковых или доломитных пород, битуминозных известняков, а также доменных шлаков.
Совместная работа порошка и битума определяется коэффициентом гидрофильности (набухания) порошковой присадки, который обычно равен 1, 25 мм и более. Набухание раствора битума и порошка не должно быть более 2,5%.
В некоторых случаях, в качестве порошковой добавки, допускается применение местных материалов — порошкообразных отходов промышленности (топливная зола, зола-унос, отходы сахарного производства и др.). Качество этих материалов разнится поэтому, эффект действия и количество определенной добавки необходимо определять опытным путем для каждого конкретного типа смеси.
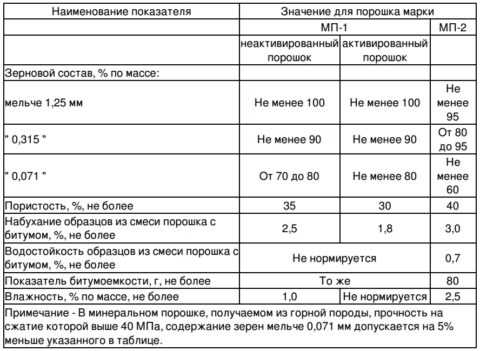
Минеральный порошок характеристики
Битум
Класс и марку жидкого или вязкого битума подбирают в зависимости от типа асфальтобетона, категории дороги, климатических условий, действующих в определенных районах строительства.
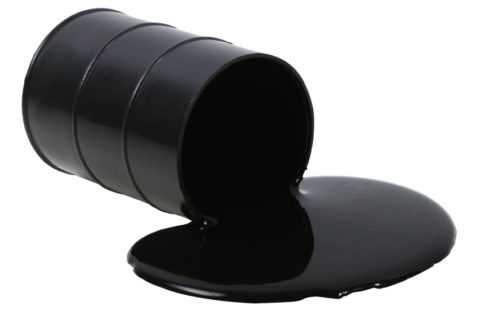
Битум
Для производства литых горячих смесей следует использовать дорожные битумы согласно ГОСТ 22245-90. Остальные технические характеристики представлены в таблице ниже.
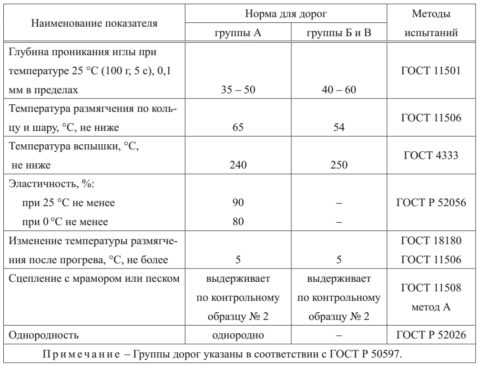
Битумы для литых асфальтобетонов требования
Черненый щебень
Для повышения износостойкости, улучшения сцепления колес автомобиля с дорожным покрытием, поверхность из литого асфальтобетона покрывают черным щебнем.
Черный, обработанный щебень
Это материал, получаемый методом смешивания и горячей пропитки, в специальной установке, щебня из вулканических или осадочных пород органическим вяжущим.
Для чернения щебня применяются смесительные агрегаты непрерывного или периодического действия. Вид вяжущего выбирают с учетом технологических особенностей конкретного типа дороги.
Технология приготовления заключается в сушке и нагреве щебня с одновременным разогревом вяжущего. Рекомендуемая температура приготовления указана в таблице.
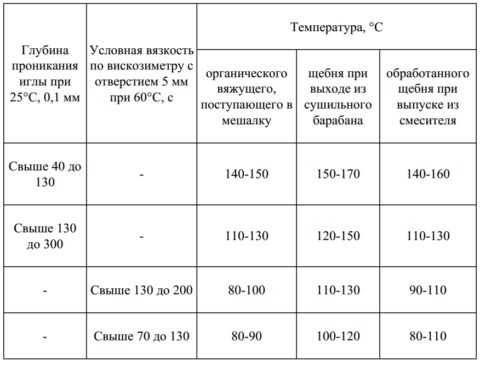
Температура нагрева материалов
Температурный режим процесса зависит от условий обработки и типа органического вяжущего. При теплой и сухой погоде (выше 10°С) руководствуются нижним пределом температуры (таблица), при температуре ниже 10°С — верхним.
Объем органического вяжущего для обработки щебня назначают согласно данных представленных в таблице ниже.
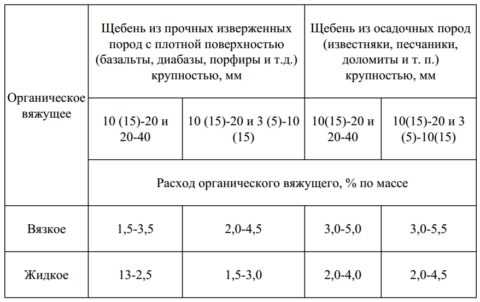
Ориентировочный расход вяжущего
Технология производства и укладки литого асфальта
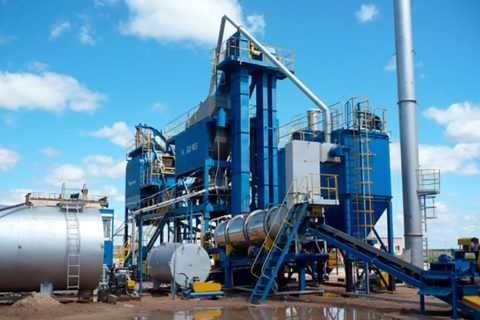
Завод по производству литого асфальта
Литая технология основывается на применении в качестве вяжущих вязких сортов нефтяных битумов.
Поэтому, приготовление смеси происходит под действием сравнительно высоких температур:
- температура битума — 160—180°С;
- минеральные заполнители нагревают до 190—240°С;
- температура готового асфальта составляет 200—220°С.
Литой способ производства асфальтобетона исключает его изготовление в местах укладки смесей, поскольку весь процесс требует точного соблюдения температурного режима.
Рекомендуемая температура
Производство
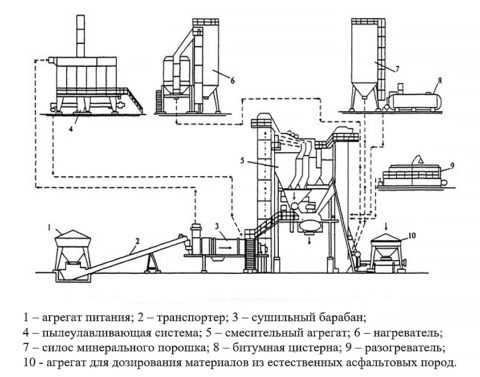
Принципиальная схема производства литого асфальта
Технологическая инструкция приготовления литого асфальтобетона:
- Холодные и влажные минеральные материалы, в расчетных соотношениях, загружают в агрегат питания, откуда при помощи наклонного транспортера сырье поступает в сушильный барабан. Там его просушивают и доводят до рабочей температуры.
- Нагретые компоненты подаются элеватором в сортировочное устройство.
- Разделенные на фракции песок и щебень через бункеры, предназначенные для горячего материала, следуют в дозаторы и по окончанию взвешивания загружаются в смесительный агрегат.
- Холодный минеральный структурирующий порошок доставляется элеватором в нагреватель, где вещество сушится и нагревается до оптимальной рабочей температуры, после этого поступает в расходный бункер.
- Осажденная в пылеуловителях пыль (отходы производства) подается в сортировочный агрегат, где дозируются и смешивается с песком и минеральным порошком.
- Горячий битум из нагревателя поступает в смесительный агрегат, где дозируется и подается в бункер к остальным компонентам.
- В главном смесителе осуществляется перемешивание всех составляющих.
- После этого готовая продукция отгружается в специальные транспортные средства (кохеры), оборудованные котлом-термосом или резервуаром, снабженным системой обогрева и перемешивания материала в момент доставки потребителю.
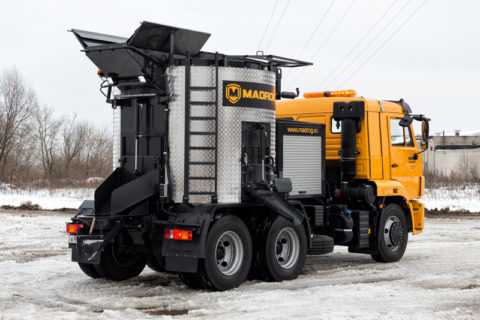
Машина—кохер
Укладка асфальта
Строительство покрытий из литых асфальтобетонных смесей необходимо выполнять в сухую и теплую погоду при температуре не ниже 5°С. Асфальтобетон в момент укладки должен иметь температуру 185—235°С, в зависимости от технологических условий и типа битумного вяжущего.
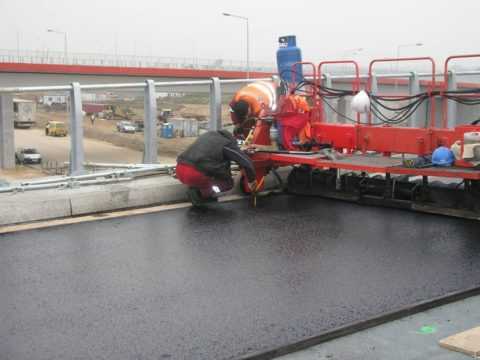
Покрытие из литых смесей
Работы по укладке литого асфальта проходят в следующей последовательности:
- подготовительные работы;
- разгрузка асфальтобетона;
- укладка;
- распределение и прессовка черного щебня.
Устройство покрытий при помощи асфальтоукладчика:
- К установленному в рабочее положение укладчику подъезжает термос-миксер для перегрузки раствора в бункер агрегата.
- Открывают заслонку термоса, включают шнеки в приемном бункере укладчика и сливают готовый асфальт.
- После загрузки нормируемого количества, начинают укладку.
- Асфальт укладывают со скоростью 1–3 м/мин. Скорость регулируют в зависимости от проектной толщины слоя. По мере расхода материала, оператор добавляет его из рядом стоящего кохера.
- При вынужденной остановке или окончании рабочей смены раствор необходимо полностью выработать или удалить из приемного бункера, а готовое покрытие, в месте будущего стыка, нужно отсечь упорным брусом. В следующую смену: брус снимают, прогревают место стыка и продолжают процесс укладки.
Устройство финишного покрытия из черного щебня
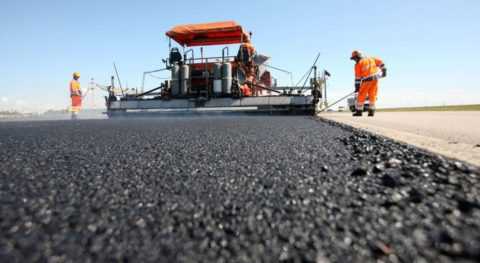
Покрытие черным щебнем
Черный щебень доставляется на объект автосамосвалами под пологом или в специальном изолируемом контейнере. Материал в момент распределения должен иметь температуру минимум 100°С.
Щебень укладывается способом рассева из расчета 10–15 кг/м2 по горячему основанию с рекомендуемой температурой 140—180°С. Материал может распределяться как вручную, так и механизированным способом (прицепной щебнераспределитель).
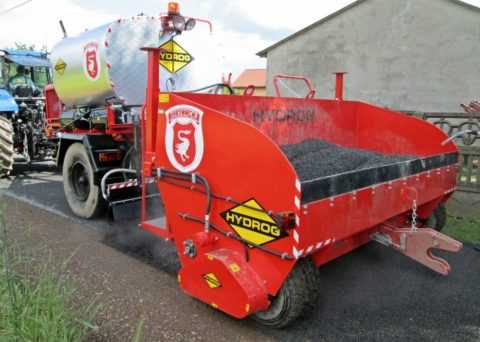
Щебнераспределитель
Работу катка можно начинать после достижения температуры покрытия 120°С. Движение автотранспорта допускается после окончательного остывания покрытия, но минимум — через 3 часа после укладки.
Литая асфальтобетонная смесь укладывается непрерывно и одновременно по всей ширине дороги, используя для этого нужное количество укладчиков, распределенных уступом на расстоянии друг от друга 25–30 м.
beton-house.com
Производство асфальтобетона, оборудование и технология приготовления асфальтобетона в заводских условиях
Ирина
Специалист отдела продаж ответит на все ваши вопросы!
+7 (800) 700-97-90
Одним из перспективных направлений деятельности в РФ является производство асфальтобетона, который используют для обустройства покрытия автомобильных дорог различного назначения. Асфальтобетон представляет собой строительный материал, который получают вследствие затвердевания смеси минеральных веществ с битумом. Технология получения асфальтобетона включает большой набор обязательных компонентов:
- Песок. Обеспечивает создание мелкозернистой основы, которая выполняет функции наполнителя мелких полостей и способствует распределению механического давления от поверхности дороги к грунту.
- Щебень. Создает требуемый уровень механической прочности, что является одной из главных характеристик асфальтобетонной смеси.
- Минеральные наполнители. В качестве этих компонентов используют измельченную горную породу (известняк, мел, песчаник). Эти наполнители позволяют асфальтобетонной смеси заполнять остаточные пустоты и значительно снижают себестоимость её производства.
- Битум. Является жидким связующим, которое склеивает все компоненты в единую монолитную смесь.
- Резина. Этот компонент вводится в виде измельченной крошки и предназначен для придания готовому асфальту высокой степени упругости, стойкости к воздействию влаги. Стоимость резины значительно увеличивает стоимость асфальта, поэтому её используют только для самых ответственных участков дороги с повышенной механической нагрузкой.
Правильное пропорциональное распределение всех этих компонентов позволяет получить асфальт, который будет обладать всеми необходимыми эксплуатационными параметрами.
Особенности производства асфальтобетона
Процесс производства асфальтобетона может выполняться при различных температурных режимах, что служит критерием для классификации асфальтной смеси на три различных категории:
- Холодные. Асфальтобетонный материал этого типа изготавливают с добавлением жидкого битума. Допускается длительное хранение и использование этой смеси при температуре не ниже +50С.
- Теплые. Асфальт этого типа изготавливают из жидкого битума и вязких связующих, поэтому температура их хранения должна составлять не менее 1000С.
- Горячие. Асфальтобетонная смесь изготавливается и укладывается при температуре не ниже 1200С.
В зависимости от фракции, используемых для изготовления асфальта компонентов, он подразделяется на три основных вида:
- Крупнозернистый. Данный материал отменно подходит для выполнения дорожного покрытия в нижних его слоях. Одним из основных компонентов этой смеси является щебень крупной и мелкой фракции.
- Мелкозернистый. Асфальтобетон этого типа применяют для обустройства верхнего покрытия у дорог общего пользования. В его состав входит щебень мелкой фракции, который может достигать величины 15 мм.
- Песчаный. Этот тип асфальта применяют для обустройства пешеходных дорожек и тротуаров. В состав этой асфальтной смеси вводят большое количество песка, битума и щебня с фракцией до 5,0 мм.
Технология изготовления смеси
Технология производства асфальтобетона состоит из нескольких основных этапов, которые включают все необходимые операции и работы:
- Входной контроль исходного сырья: минеральные добавки, битум, щебень, песок.
- Обработка инертных материалов: просеивание песка, разделение щебня по фракциям, разогрев битума.
- Доведение всех компонентов до требуемого уровня влажности и температуры нагрева.
- Перемешивание между собой всех составных компонентов асфальтобетонной смеси, что обеспечивает сцепление битума с песком, зернами щебня и минеральным наполнителем.
- Хранение готового асфальта в специальном бункере, где происходит поддержание требуемого температурного режима.
Забор готового продукта происходит непосредственно из бункера хранения, после чего его доставляют до места укладки с соблюдением всех технологических требований. Подобная технология изготовления асфальтобетона используется практически на всех отечественных заводах. Некоторые производители вводят в состав асфальта каучуковую крошку или латекс, что направлено на получение смеси с высокой степенью упругости.
Типы оборудования для производства
Оборудование для производства асфальтобетона в зависимости от технологических особенностей подразделяют на заводы непрерывного и циклического действия:
- Технологическая схема производства асфальтобетона на оборудовании непрерывного действия характеризуется отсутствием башни и грохота, которые необходимы для качественной сортировки исходного сырья. Все ингредиенты непрерывно подают в приемные бункеры, после чего они доводятся до требуемого состояния готовности к перемешиванию. Отсутствие грохота делает возможным случаи попадания в готовую асфальтобетонную смесь щебня некондиционных размеров или посторонних включения. Основное преимущество подобных заводов – компактные размеры и высокая степень мобильности.
- Технология приготовления асфальтобетона на оборудовании циклического действия характеризуется наличием грохота и приемных башен. Благодаря этому вспомогательному оборудованию обеспечивается высокая степень подготовки исходного сырья еще до подачи в бункер для перемешивания. Асфальтный завод циклического действия располагают вблизи крупных городов, где регулярно есть потребность в небольшом объеме асфальтобетонной смеси. Главное преимущество подобных технологических схем: изменение рецептуры до нескольких раз в день, без ухудшения качества готового продукта, возможность готовить асфальт небольшими порциями, высокое качество подготовки сырья. Главный недостаток подобных заводов – низкий уровень мобильности.
Приготовление асфальтобетона в заводских условиях требует наличия персонала соответствующего уровня квалификации, который будет уметь правильно снимать показания аппаратуры, знать все технологические особенности производства и быстро реагировать на отклонения от заданного технологического режима работы.
sdm-sam.ru
Современные технологии производства асфальтобетонных смесей
Асфальт (от греч. α’σφαλτος – горная смола) – смесь битумов (60…75% в природном и 13…60% в искусственном) с минеральными веществами: известняком, песчаником и др. Может применяться вместе с песком, гравием, щебнем для устройства дорожных и других покрытий.
Асфальт бывает как природного, так и искусственного происхождения. Природный асфальт образуется из тяжелых фракций нефти или их остатков в результате испарения ее легких составляющих и окисления под влиянием гипергенеза. Искусственный асфальт (асфальтобетонная смесь, АБС) – это строительный материал, получаемый после уплотнения смеси щебня, песка, минерального порошка и битума.
Исторически дороги мостили камнем, но с середины XIX в. во Франции, Швейцарии, Соединенных Штатах и ряде других стран для дорожных покрытий начинают применять битумно-минеральные смеси. Как показал опыт эксплуатации, асфальт оказался наиболее подходящим материалом для устройства дорожных покрытий. Основные его преимущества – это высокая скорость строительства, более низкая себестоимость и отличная ровность получаемых покрытий. Асфальтобетонные покрытия и сегодня остаются самыми распространенными при строительстве дорог, мостов, тоннелей и других сооружений.
Асфальтобетонные смеси делают из компонентов в заданной пропорции и степени гомогенности в асфальтосмесительных установках (АСУ). Для получения смеси высокого качества необходимо правильно выбрать ингредиенты, их физические свойства и интенсивность их перемешивания, точно определить пропорцию. При соблюдении всех требований получается гомогенная АБС со свойствами, отвечающими ГОСТу.
Существуют различные по принципу действия АСУ. В настоящее время наиболее известны циклическая (порционная) система смешивания и непрерывная (барабанная). Циклическая технология шире применяется в Европе, тогда как в США, Австралии, Канаде и Латинской Америке более популярны АСУ непрерывного действия. Такое разделение произошло из-за различной протяженности дорог в Европе и Америке. Согласно статистике в 2006 г. объем производства асфальтобетонных смесей в США превысил 500 млн. т, тогда как в Германии выпущено порядка 56 млн. т, во всей же Европе – около 350 млн. т. Сразу становится понятен разрыв в уровне между европейскими странами и США. На заре эры асфальтовых покрытий и в Штатах применяли заводы циклического действия, но в период дорожного бума и резкого роста потребности в асфальте встал вопрос снижения себестоимости его производства и увеличения производительности АСУ. Решением стало внедрение непрерывной технологии производства смесей, что и позволило значительно сократить себестоимость производства и повысить объемы выпуска смеси одной установкой.
Рассмотрим принципы, на которых построены эти технологии, и их преимущества.
Основным компонентом классического циклического асфальтобетонного завода (АБЗ) является система подачи инертных, предварительно дозирующая холодные инертные материалы, такие как щебень и песок, которые по наклонному конвейеру подаются в сушильный барабан, где нагреваются до заданной температуры потоками газа. Нагретые инертные подаются на элеватор горячих инертных и далее на вибрационный грохот, который рассеивает поток материала на разные фракции согласно количеству и размеру ячеек сит. В АБЗ некоторых производителей, например LINTEC GmbH & Co. KG, применяются не вибрационные грохоты, а барабанные, что позволяет снизить стоимость установки. Такие грохоты применяли когда-то и в отечественных АБЗ, но современные АСУ комплектуют именно вибрационными грохотами, так как они обеспечивают более точное разделение фракций. В барабанных грохотах возможно перераспределение мелких фракций в более крупные при максимальных нагрузках и при повышенной лещадности щебня, который может застревать в ситах и блокировать проход мелких фракций, что подтверждено опытом эксплуатации АСУ такого типа в России. Под грохотом расположены бункера горячих инертных, и в каждом хранится своя фракция. Согласно составу смеси, заданному в программе управления, из каждого бункера с отдельной фракцией в весовой хоппер дозируется по очереди требуемое количество материала. Отдельно установлен весовой хоппер для битума и хоппер для минерального порошка и пыли. Битум дозируется из битумохранилища, а минеральный порошок и пыль – из соответствующих силосов. Дозирование осуществляется с помощью динамического взвешивания всех компонентов смеси. Дозированные компоненты подаются в смесительную камеру, где перемешиваются. Средняя продолжительность общего цикла дозирования и перемешивания составляет 45 с, т. е. 80 циклов в час. Именно так определяется паспортная производительность циклических АБЗ – полезный объем смесительной камеры умножают на 80 циклов. Например, при смесителе в 2 т х 80 циклов получаем 160 т/ч.
АБЗ с горизонтальным скипом – по сути тележка, перемещающаяся по направляющим рельсовым опорам, которая доставляет смесь от смесителя к нужному бункеру хранения смеси и приводится в действие лебедочным механизмом с приводом. Хранилище асфальта разделено на разные отсеки – бункера, где можно хранить смеси с разной рецептурой. Очистка отходящих горячих газов из сушильного барабана происходит в рукавном фильтре, где осаждается пыль с помощью тканевых мешков (рукавов). Осажденная пыль обычно либо вывозится с АБЗ, либо подается в силос пыли, из которого дозируется в хоппер для минерального порошка в нужной пропорции с минеральным порошком. Битум хранится в цистернах, которые могут быть горизонтального, вертикального или мобильного исполнения. Процесс дозирования, смешивания и отгрузки смеси в самосвалы контролируется операторами из пункта управления. В большинстве современных АБЗ установлена микропроцессорная система управления, что облегчает работу, но в то же время средства ручного управления зачастую отсутствуют, и это не позволяет продолжать работу в случае сбоя компьютерной системы.
Многие узлы АБЗ непрерывного типа аналогичны узлам АБЗ циклического типа. Также дозирование холодных инертных осуществляется из холодных дозаторов, отличие которых в том, что они выполняют роль дозаторов, а не предварительных дозаторов, как в циклических АБЗ. В циклических АБЗ дозирование компонентов идет из бункеров горячих инертных в весовой хоппер, а из преддозаторов – только предварительная подача материала. Погрешность дозирования преддозаторов может достигать 10% и более, что несущественно для данного типа АБЗ, так как есть весовой контроль. В то же время в непрерывных АБЗ холодные дозаторы являются именно дозирующим устройством и обеспечивают высокую точность дозирования с погрешностью ±0,1%. Это достигается благодаря современному микропроцессорному управлению, приводам с частотным управлением, тахометрам на приводных валах с обратной связью и весовому мосту, установленному в наклонном конвейере. Холодные инертные точно дозируются из бункеров и подаются на наклонный конвейер, оснащенный грохотом негабарита, отсеивающим негабаритный щебень. Поток материала после грохота попадает на весовой мост, который динамически взвешивает суммарный объем инертных и корректирует работу дозаторов через систему обратной связи с программой управления. Взвешенный материал попадает в сушильно-смесительный барабан, где он, как и в циклическом АБЗ, сушится потоком нагретого газа от пламени горелки. После сушки нагретый материал смешивается в этом же агрегате с минеральным порошком, собственной пылью, битумом и другими компонентами. Полученная смесь выгружается из сушильно-смесительного барабана. Традиционно для хранения смеси применяют силосы круглого сечения со скребковым конвейером. Системы такого типа могут обеспечивать хранение 9 шт. х 300 т = 2700 т и более.
Также в составе непрерывного АБЗ есть битумное хранилище, силосы минерального порошка и собственной пыли. Есть рукавный фильтр с такими же тканевыми рукавами и системой эвакуации пыли или в силос, или назад в барабан, или в самосвал для вывоза.
Развитие конструкций АБЗ непрерывного типа можно разделить на три этапа – это барабанные смесители прямоточного типа, когда поток материала и горячего газа шел в одном направлении, что было не так эффективно, как в барабанах второго поколения – противоточных. Третьим этапом развития непрерывных АБЗ стала разработка барабанно-смесительных установок со встроенной горелкой и барабана Double Barrel («двойной барабан») компанией Astec Inc.
В прямоточных барабанах поток горячего газа идет параллельно инертным материалам. При таком нагреве газ может проходить через прорехи в завесе материала и не передавать тепло инертным. Температура выходящих газов высокая, что приводит к преждевременному износу тканевых фильтров. Материал попадает в зону горения пламени, из-за чего не полностью сгорает топливо и спекаются влажные инертные. Минеральный порошок и битум уносятся потоком газа в рукавный фильтр, и в результате фильтры загрязняются. Характерно низкое качество перемешивания смеси.
В противоточных барабанах материал подается с противоположной стороны барабана и движется навстречу горячему газу. Устранена проблема спекания и уноса инертных и битума. Время смешивания увеличено, и качество смесей повысилось. Также стало возможно добавление до 50% регенерированного асфальтового покрытия (РАП) с малым выбросом углеводородов, так как РАП подается после пламени горелки. Повысилась эффективность работы – расход топлива снизился, а производительность возросла. Модификацией этого типа является двухбарабанная система, когда один барабан сушит материал в противотоке, а нагретые инертные подаются во второй барабан, предназначенный только для смешивания. Такие АБЗ обеспечивают еще большее время смешивания и лучшее качество смеси.
Противоточные сушильно-смесительные барабаны и сегодня самый распространенный тип агрегатов для сушки и смешивания в АБЗ непрерывного типа. Смешивание в этих АБЗ происходит под воздействием гравитации – барабан, вращаясь, поднимает смесь лопатками, которая падает в определенный момент. При падении происходит смешивание. Такой тип смешивания часто называют гравитационным.
Принципиально новая система сушки и смешивания разработана и запатентована гениальным инженером Доном Броком. Д. Брок создал свою компанию Astec Inc. и начал производство АБЗ с запатентованной системой Double Barrel. За короткий период Astec Inc. выросла до уровня абсолютного лидера среди производителей АБЗ. Гениальность конструкции Double Barrel в том, что удалось совместить преимущества непрерывной технологии и циклической – низкая себестоимость производства смеси и качественное принудительное перемешивание, как в циклическом АБЗ.
Смесь подается в барабан Double Barrel и в противотоке нагревается. В конце сушильного барабана нагретая смесь через окна выгружается в смесительный барабан, одетый поверх сушильного. На вращающемся сушильном барабане наварены смесительные лопатки, которые перемешивают ингредиенты, находящиеся в статике, как и в циклическом АБЗ. Время смешивания составляет 90 с и рассчитано на производство ЩМА без снижения производительности и с возможностью добавления РАП до 50%. Основные преимущества Double Barrel – это самое низкое потребление топлива в индустрии, качественно промешанные, гомогенные смеси, простота эксплуатации и низкие расходы, высокая производительность при производстве смесей всех типов.
Теперь рассмотрим принципиальные различия между циклическим и непрерывным АБЗ и целесообразность их применения в тех или иных условиях.
Основное отличие этих технологий в системе дозирования и смешивания. В непрерывном АБЗ нет башни и дозирование сразу идет из холодных дозаторов, смесь идет непрерывным потоком. В циклическом АБЗ идет разгрохотка материала на фракции и весовое, порционное дозирование компонентов, а смесь выпускается порциями.
Циклические АБЗ позволяют проще и быстрее менять рецептуру смеси, в теории каждый замес может иметь другую рецептуру. Такие АБЗ наиболее востребованы при производстве асфальта в городах и мегаполисах, когда асфальт производят для нескольких укладочных комплексов. В то же время циклические АБЗ менее мобильны из-за башни. Башня имеет большие размеры, и для их снижения уменьшают размеры бункеров горячих инертных. В результате мобильный циклический АБЗ работает в режиме грохочения – горячие инертные бункера часто или переполнены одной фракцией, или пусты, что приводит либо к нарушению рецептуры, либо простоям и сбросу избытка нагретых фракций, в основном более крупных. Владелец АБЗ теряет объем выпуска асфальта и деньги на бесполезный нагрев сброшенного щебня. При выпуске ЩМА производительность может упасть на 40% от паспортной из-за добавления цикла сухого перемешивания и увеличения времени цикла.
Преимущество непрерывных АБЗ – в простоте конструкции. Они проще в транспортировке, возведении на новом месте и обслуживании. Такой АБЗ может быть запущен в работу в течение 3 дней и дать асфальт. Стоимость ниже, чем у циклического такой же производительности, а реальный выпуск асфальта в смену выше. Особенностью является то, что в реалиях России фракционный состав закупаемого щебня на карьерах может не соответствовать ГОСТу, а так как в этом типе АБЗ нет грохота, разделяющего на фракции инертный материал, иногда происходят нарушения в рецептуре смеси и состав инертных может меняться. Простым решением такой проблемы является установка отдельного грохота для предварительной подготовки инертных, благо на рынке предлагается огромное количество как стационарных, так и мобильных решений. Установка грохота позволяет контролировать состав инертных до их нагрева, а не когда деньги на нагревание уже потрачены. Тем более что даже с дополнительной комплектацией грохотом непрерывный АБЗ конкурентен по цене. При работе в городах и необходимости выпуска в течение одной смены асфальтобетонных смесей разных рецептур АБЗ комплектуют силосами длительного хранения, позволяющими хранить смесь до 4 суток. Например, один из производителей асфальта в США, имеющий в комплекте с АБЗ 6 силосов, менял рецептуру 50 раз в смену. Это делается просто – задается новая рецептура и по прошествии 40…60 с смесь подается в другой силос, где и накапливается новая смесь. При наличии опыта эксплуатации переход происходит просто и быстро. Точность дозирования инертных, минерального наполнителя, битума и других ингредиентов соответствует стандарту, что подтверждено опытом эксплуатации во всем мире и в России в том числе. Качество получаемых смесей, в том числе и ЩМА, на высоком уровне.
Каждая из технологий имеет свои особенности и преимущества. При выборе АБЗ еще раз взвесьте все «за» и «против» исходя из того, как вы планируете работать. Реалии современной России еще раз подтвердили, что при наличии мобильного АБЗ вы получаете возможность быстро реагировать на ситуацию и участвовать в подрядах не только в своем регионе.
os1.ru
Производство и укладка асфальта
Асфальт — это смесь битумов с минеральными материалами (гравием и песком). Асфальт может быть природного и искусственного происхождения. Под словом «асфальт» часто понимается такой термин как «асфальтобетон» — это искусственный каменный материал, получаемый в результате уплотнения асфальтобетонных смесей. Состоит этот материал из песка, щебня и минерального порошка (филера).
Асфальтобетон находит наиболее широкое применение при строительстве, при возведении городских, магистральных, аэродромных, дорожных и кровельных покрытий. Он применяется также в строительстве мостовых, гидротехнических, промышленных, жилищно-гражданских зданий и сооружений. Асфальтовые бетоны значительно более стойки к коррозийным воздействиям, чем цементные, но, к сожалению, боятся воздействия жидких топлив и масел.
Виды асфальтов
Искусственный асфальт может быть горячим. Он содержит вязкий битум, который укладывается и уплотняется при температуре не ниже 120 °C. Он также может быть теплым, в таком случае, вязкий битум укладывается при температуре от 40 до 80 °C. Искусственный асфальт может быть холодным, содержать жидкий битум, уплотняемый при низкой температуре окружающего воздуха (но не ниже 10 °C).
Битум — это смесь смолоподобных или твердых продуктов, которые представляют собой смесь углеводородов и их сернистых, кислородных и металлсодержащих производных. Битум не может быть растворен в воде, частично растворяется в бензоле и сероуглероде.
В зависимости от крупного заполнителя асфальтобетоны разделяются на:
- песчаные — отсутствует крупный заполнитель (щебень или гравий)
- гравийный — состоящий из гравия, песка, минерального порошка и битума
- щебеночный — состоящий из щебня, песка, минерального порошка и битума
Горячие и теплые асфальтобетоны в зависимости от использования их в дорожной конструкции разделяют на:
- плотные (для верхних слоев покрытия дорог)
- пористые (для нижнего слоя и оснований дорожных покрытий)
- высокопористые (также для нижнего слоя и оснований дорожных покрытий)
Асфальт с резиновой крошкой
Асфальт также может быть с резиновой добавкой. Резиновая добавка, содержащаяся в асфальте, создает препятствие для попадания внутрь воды, асфальтированный участок не разрушается, сохраняя свою твердость. Способ асфальтирования с использованием резиновой крошки имеет более высокую стоимость, но такой асфальт прослужит гораздо дольше и избавит от необходимости частого проведения ямочного ремонта, а, соответственно, снизит затраты в долгосрочном периоде. При высоких температурах происходит окисление обычного асфальта, асфальтированная дорога начинает расслаиваться из-за высвобождения мелкозернистых материалов. На стандартной асфальтированной дороге трещины начинают появляться довольно быстро.
Способ асфальтировки с использованием резиновой крошки позволят увеличить время появления трещин в несколько раз. Дело в том, что асфальт, содержащий резиновые добавки включает в себя 7-9% связующего материала. Резина выступает в качестве компонента наполнителя, что позволяет асфальту не терять мелкозернистые материалы под постоянным воздействием солнца.
Асфальт с резиновой добавкой доступен для производства на обычных заводах при помощи горячего смешения, но специалисты рекомендуют осуществлять его производство при помощи специализированных асфальтовых установок. Для данного вида производства существуют специализированные заводы.
Технология производства асфальта с резиновой добавкой
Технология производства асфальта с резиновой добавкой состоит из 2 этапов: на первом этапе происходит смешивание асфальта и резины, на втором этапе получается готовый продукт. В течении определенного времени после смешения резины и асфальта происходит реакция. Главным материалом для производства такого вида асфальта служат изношенные автомобильные шины.
Асфальтировку необходимо начинать со снятия верхнего слоя асфальтового покрытия, затем поверхность следует обработать специальной битумной эмульсией. Рекомендуемая толщина асфальтового слоя должна составлять 3-4см. В момент укладки температура асфальта с содержанием резиновой крошки составляет 150°С. Поверхность покрытия обрабатывается известковой водой после утрамбовки асфальта. Известь устраняет липкость асфальта после испарения воды. Это позволяет начинать эксплуатацию дорожного покрытия уже через 15 минут после завершения работ.
Важно заранее определить насколько интенсивно будет использоваться тот или иной участок обрабатываемой земли, насколько интенсивно будут производиться нагрузки на асфальт при его эксплуатировании. Разница становится очевидной при сравнении, какой по качеству потребуется асфальт, например, при облагораживании зон отдыха, и какими свойствами он должен обладать при выполнении дорожного покрытия масштабного значения. Важно выполнить качественную каркасную основу. Экономия на каркасной основе приведет к высоким затратам в дальнейшем.
Производство асфальта
Стандартный асфальт производится следующим образом: Влажный и холодный песок и щебень подается со складов в бункеры агрегата питания погрузчиками, кранами или конвейерами. Из бункеров песок и щебень непрерывно подается питателями на сборный ленточный конвейер, который расположен в нижней части агрегата питания.
Со сборного конвейера песок и щебень поступают на наклонный ковшовый элеватор. Он загружает щебень и песок в барабан сушильного агрегата. В барабане песок и щебень высушивается и нагревается до нужной температуры. Нагревание материала происходит за счет сжигания жидкого и газообразного топлива в топках сушильных агрегатов. Жидкое топливо хранится в специальных баках, в которых происходит его нагрев и подача насосом к форсунке сушильного агрегата.
При помощи вентиляторов к форсунке подается необходимый для сгорания топлива воздух. При просушивании материала и сжигании топлива образуются горячие газы и пыль, которые в дальнейшем поступают в пылеулавливающую. В пылеулавливающей системе пыль осаждается и затем подается к смесительному агрегату для использования. Очищенные от пыли горячие газы выбрасываются в атмосферу через дымовую трубу.
Заводы по производству асфальтобетонных масс относятся к высокомеханизированным предприятиям.
На таких заводах достигается полная автоматизация и механизация основных технологических операций.
Состав завода по производству асфальта
В состав асфальтового завода входят:
- смесительный цех (отвечает за приготовление асфальтобетонной массы)
- дробильно-сортировочный цех ( изготовление щебня)
- помольный цех (изготовление минерального порошка)
- цех битумного хозяйства
- паросиловое и энергосиловое отделения
- ремонтно-механические мастерские
- лаборатория при отделе технического контроля качества
promplace.ru
Асфальтобетон: состав и виды материала
Немногие знают, что такое асфальтобетон и чем он отличается от традиционного асфальта. Первое, что хочется отметить, это то, что асфальт и асфальтобетонная смесь – это абсолютно разные вещи. Асфальт представляет собой битум – черную горную смолу. А асфальтобетоны – это смеси битума с щебнем, гравием и(или) песком, а также многими иными материалами.
Смесь для создания покрытия
Обратите внимание!
В разговорной речи асфальтобетоны зачастую называются просто асфальтом.
Нормативная документация
Нормативные документы существуют как на сам асфальтобетонный раствор, так и на различные битумы. Технические характеристики битумных смесей регламентируются ГОСТом 9128.
А параметры битумов, в зависимости от целей их применения, оговариваются следующими документами:
- ГОСТ на строительные №6617;
- ГОСТ на кровельные №9548;
- ГОСТ на дорожные вязкие №22245.
Состав материала
Асфальто-бетонное покрытие используется в основном для обустройства дорожного полотна.
В такую смесь включают следующие компоненты:
- Песок;
- Щебень мелкого или среднего размера фракции, который составляет 85% от всей массы раствора;
- Минеральный порошок;
- Битум, являющийся связующим веществом для остальных компонентов раствора и составляющий 6% его массы.
Производство строительного материала такого типа предполагает соединение и тщательное перемешивание компонентов раствора, после чего производится моментальная его укладка.
Совет. Битум осуществляет свою связующую функцию только тогда, когда он является горячим.
Если смесь приготовили, укладку необходимо производить сразу же. Оставшаяся масса теряет свои основные свойства и становится непригодной для производства работ. Такой асфальт нельзя утрамбовать, и он становится хрупким.
Совет. Для того чтобы застывший асфальт не стал мусором, можно воспользоваться специализированным оборудованием таким, например, как установка для регенерации асфальтобетона ПМ 107.
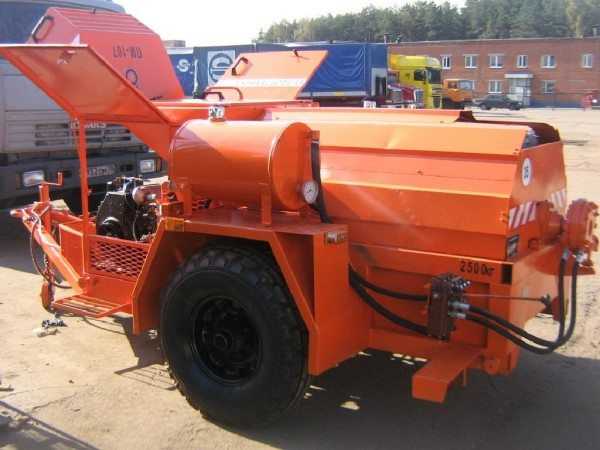
Оборудование для регенерации
Многих владельцев загородных домов волнует вопрос о том, что лучше асфальт или бетон? Ответ на этот вопрос является довольно спорным, т. к. при составлении сравнительной характеристики можно выявить, что оба этих материала обладают не такими уж и серьезными отличиями, за исключением такого показателя, как цена ремонта покрытия.
Еще один достаточно частый вопрос — можно ли класть асфальт на бетон? Конечно, можно, тем более что такой вариант укладки позволит наделить покрытие положительными характеристиками обоих этих материалов.
Виды смесей
На фото – процесс укладки материала
Различают три основных вида материала, которые применяется для того, чтобы укладывать асфальтно-бетонное покрытие.
При этом каждый из представленных видов асфальта обладает своим предназначением:
- Крупнозернистый. Данный тип раствора применяется для обустройства самых нижних слоев дорожного полотна. При его приготовлении используется мелкофракционный щебень для бетона с размерами зерна 5-15 мм и крупнофракционный 20-40 мм;
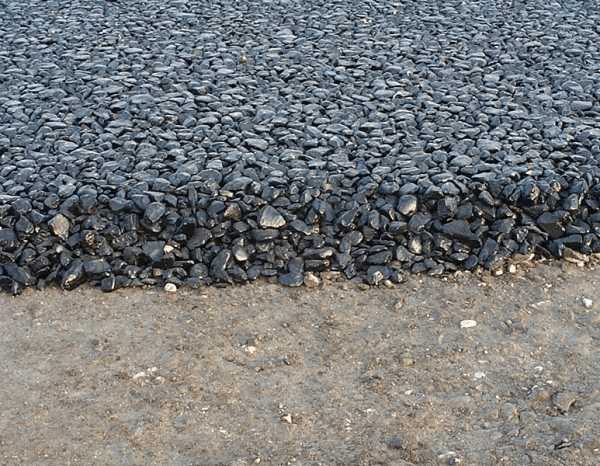
Крупнозернистый материал
- Мелкозернистый. Такая смесь применяется в процессе укладки покрытий на проезжих частях. Именно такой слой материала является верхним при обустройстве двухслойной конструкции. Одним из ингредиентов такой смеси является мелкофракционный щебень 5-15 мм размером;
- Песчаный. Такого типа раствор применяется для мощения тротуаров и пешеходных дорожек. В состав такого раствора входят в большом количестве песок и немного минерального наполнителя, битум и щебень с фракциями до 5 мм.
Технология изготовления
Существует три метода, по которым производится приготовление горячей смеси:
- Холодный;
- Теплый;
- Горячий.
Обратите внимание!
Инструкция по изготовлению раствора по таким методам отличается только температурой, до которой доводятся смешиваемые материалы.
Холодный метод приготовления предусматривает подогрев связующего вещества перед тем, как добавить его к остальным компонентам. Теплый и горячий методы предполагают добавление в подогретые компоненты горячего битума.
Приготовление горячего раствора
Технология приготовления такого типа материала своими руками предусматривает следующие этапы производства работ:
- Сушка инертных компонентов и доведение их до температуры 200 градусов;
- При температуре 160 градусов производится смешивание инертных компонентов с минеральным порошком и битумом;
- Хранение готовой смеси до использования при температуре 150-180 градусов.
Оборудование для производства
В роли оборудования для производства такого строительного материала используются асфальтобетонные установки или заводы.
Такое оборудование бывает трех видов:
- Мобильное;
- Стационарное;
- Ультрамобильное (Супермобильное).
Обратите внимание!
Ультрамобильность таких установок кроется не в их малых габаритных размерах, а в легкости транспортировки к месту производства работ.
Мобильная установка
Стационарные асфальтные заводы обладают производительностью приблизительно 80 тонн за час работы, а мобильные установки производят от 3 до 80 тонн. Цена мобильной установки напрямую зависит от ее производительности.
Обратите внимание!
Для организации бизнеса по производству асфальта придется приобрести также фронтальный погрузчик для транспортировки.
Производство смесей — это процесс, напрямую связанный с его укладкой. Поэтому приобретение комплекта оборудования для асфальтирования дорожного полотна может предполагать необходимость купить керноотборник для асфальтобетона.
В заключение
Уложенное дорожное полотно
Рассматриваемый материал – смесь, просто необходимая для обустройства качественного, пластичного и долговечного дорожного полотна. Правильно подобранные компоненты и точное соблюдение технологии изготовления согласно выбранного метода позволит создать поистине прочное бетонное покрытие, обладающее прекрасными эксплуатационными параметрами.
А видео в этой статье позволит вам узнать еще больше о типах, методах изготовления и основных компонентов обсуждаемой смеси.
masterabetona.ru