Технологический процесс производства меди
Медь, относимая по классификации к цветным металлам, стала известной в глубокой древности. Ее производство человек освоил раньше, чем железо. Это объяснимо как частым ее нахождением на земной поверхности в доступном состоянии, так и относительной легкостью производства меди путем извлечения ее из соединений. Свое название Cu она получила от острова Кипра, где древняя технология производства меди получила большое распространение.
Благодаря своей высокой электропроводимости (медь из всех металлов – вторая после серебра) она считается особенно ценным электротехническим материалом. Хотя электропровод, на который ранее шло до 50% мирового производства меди, сегодня чаще всего изготовляют из более доступного алюминия. Медь, наряду с большинством прочих цветных металлов, считается все более дефицитным материалом. Это связано с тем, что сегодня называются богатыми те руды, что содержат около 5% меди, а основная ее добыча ведется переработкой 0,5%-ных руд. В то время как в прошлые века эти руды содержали от 6 до 9% Cu.
Медь относят к тугоплавким металлам. При плотности в 8,98 г/см3 ее температуры плавления и кипения составляют соответственно 1083°C и 2595°C. В соединениях она обычно присутствует с валентностью I или II, реже встречаются соединения с трехвалентной медью. Соли одновалентной меди чуть окрашенные или совсем без цвета, а двухвалентная медь дает своим солям в водном растворе характерную окрашенность. Чистая медь представляет собой тягучий металл красноватого или розового (на изломе) цвета. В просвете тонкогом слоя она может казаться зеленоватой или голубой. Большинство соединений меди имеют такие же цвета. Этот металл присутствует в составе множества минералов, из них при производстве меди в России применяют только 17. Самое большое место в этом отводится сульфидам, самородной меди, сульфосолям и карбонатам (силикатам).
Способы производства меди
Среди способов производства меди из руд с концентратами выделяют пирометаллургический метод и гидрометаллургический. Последний не получил широкого распространения. Это продиктовано невозможностью одновременного с медью восстановления прочих металлов. Он используется для обработки окисленной или самородной руды с бедным содержанием меди. Отличаясь от него, пирометаллургический способ позволяет разработку любого сырья с извлечением всех компонентов. Очень эффективен он для подвергающихся обогащению руд.
Основной операцией такого процесса производства меди служит плавка. При ее производстве используют медные руды или их обожженные концентраты. В ходе подготовки к данной операции схемой производства меди предусмотрено их обогащение способом флотации. При этом руды, содержащие наряду с медью ценные элементы: теллур или селен, золото с серебром, стоит обогащать в целях одновременного перехода данных элементов в медный концентрат. Образованный таким методом концентрат может содержать до 35% меди, столько же железа, до 50% серы, а также пустую породу. Обжигу он подвергается в целях снижения до приемлемого содержания в нем серы.
Концентрат обжигается в преимущественно окислительной среде, что позволяет удалить примерно половины содержания серы. Полученный таким образом концентрат при переплавке дает довольно содержательный штейн. Еще обжиг помогает снизить вдвое расход топлива отражательной печью. Достигается это при качественном смешении состава шихты, обеспечивающем ее нагревание до 600ºС. Но богатые медью концентраты лучше перерабатывать, не обжигая, так как после этого возрастают утраты меди с пылью и в шлаке.
Итогом такой последовательности производства меди является деление объема расплава надвое: на штейн-сплав и шлак-сплав. Первую жидкость, как правило, составляют медные сульфиды и железные, вторую – окислы кремния, железа, алюминия и кальция. Переработку концентратов в сплав штейн ведут при помощи электрической либо отражательной печей различных видов. Чисто медные либо сернистые руды лучше плавить с помощью шахтных печей. К последним также стоит применить медно-серное плавление, позволяющее улавливать газы, одновременно извлекая серу.
В специальную печь небольшими порциями загружаются медные руды с кокс, а также известняки и оборотные продукты. Верхняя часть печи создает восстановительную атмосферу, нижняя часть – окислительную. По мере расплавления нижнего слоя масса медленно спускается вниз для встречи с разогретыми газами. Верхняя часть печи нагрета до 450 ºС, а температура отходящих газов составляет 1500 ºС. Это необходимо при создании условий очищения от пыли еще до того, как начнется выделение паров с серой.
В результате такой плавки получают штейн, включающий от 8 до 15% меди, шлак, главным образом содержащий известь с железным силикатом, а еще колошниковый газ. Из последнего после предварительного осаждения пыли удаляют серу. Задача увеличения в штейн-сплаве процента Cu при производстве меди в мире решается применением сократительной плавки. Она заключается в помещении в печь наряду со штейном кокса, флюса из кварца, известняка.
При нагревании смеси происходит процесс восстановления медных окисей и железных оксидов. Сплавляемые друг с другом железные и медные сульфиды составляют штейн первоначальный. Расплавляемый железный силикат при стекании вдоль поверхностей откосов принимают в себя прочие компоненты, пополняя шлак. Результатом такой плавки является получение обогащенного штейна со шлаком, включающих медь до 40% и 0,8% соответственно. Драгоценные металлы, такие как серебро с золотом, почти не растворяясь в сплаве шлака, целиком оказываются в сплаве штейна.
Производство черной и рафинированной меди
В ходе добычи черновой меди производством предусмотрено продувание штейн-сплава в конвертере бокового дутья воздухом. Это необходимо, чтобы окислить соединенное с серой железо и перевести его в состав шлака. Данная процедура называется конвертированием, она подразделяется на две стадии.
Первая состоит в изготовлении белого штейна посредством окисления железного сульфида с помощью флюса из кварца. Скапливающийся шлак удаляют, а на его место помещают очередную порцию первоначального штейна, восполняя постоянный объем его в конвертере. При этом в конвертере по ходу удаления шлака остается только белый штейн. Он содержит преимущественно сульфиды меди.
Следующей частью процесса конвертирования служит непосредственное изготовление черновой меди посредством переплавки белого штейна. Она получается путем окисления медного сульфида. Получаемая в ходе продувания медь черновая состоит уже на 99% из Cu с незначительным добавлением серы и различных металлов. При этом она еще не годится для технического использования. Поэтому после конвертирования к ней обязательно применяют метод рафинирования, т.е. очищения от примесей.
В производствах рафинированной меди требуемого качества медь черновая подвергается сначала огневому, потом электролитическому воздействию. Посредством его вместе с исключением ненужных примесей получают также содержащиеся в ней ценные компоненты. Для этого черновую медь на огневой стадии погружают в те печи, что применяют при переплавке концентрата меди в сплав штейна. А для электролиза необходимы специальные ванны, их изнутри покрывают винипластом либо свинцом.
Целью огневой стадии рафинирования является первичное очищение меди от примесей, необходимое для подготовки ее к следующей стадии рафинирования – электролитической. Из расплавляемой огневым методом меди вместе с растворенными газами и серой удаляются кислород, мышьяк, сурьма, железо и прочие металлы. Полученная таким способом медь может включать незначительное содержание селена с теллуром и висмутом, что ухудшает ее электропроводность и способность к обработке. Эти свойства особенно ценны для изготовления продукции из меди. Поэтому к ней применяют электролитическое рафинирование, позволяющее получение меди, пригодной для электротехники.
В ходе электролитического рафинирования анод, отливаемый из меди, прошедшей огневую стадию рафинирования, и катод из тонколистовой меди поочередно погружаются в ванну с сернокислым электролитом, через которую пропускают ток. Эта операция позволяет качественное очищение меди от вредных примесей с одновременным извлечением сопутствующих ценных металлов из анодной меди, являющей сплавом многих компонентов. Итогом такого рафинирования служит производство катодной меди особой чистоты, содержащей до 99,9% Cu, получение шлама, содержащего ценные металлы, селен с теллуром, а также загрязненного электролита. Он может быть использован для изготовления медного и никелевого купороса. Помимо этого неполное химическое растворение компонентов анода дает анодный скрап.
Электролитическое рафинирование выступает основным способом получения технически ценной меди для промышленности. В относящейся к странам-лидерам по производству меди России с ее помощью изготавливают кабельнопроводниковые изделия. Чистая медь широко применяется в электротехнике. Здесь также большое место занимают медные сплавы (латунь, бронза, мельхиор и др.) с цинком, железом, оловом, марганцем, никелем, алюминием. Медные соли нашли спрос в сельском хозяйстве, из них получают удобрения, катализаторы синтеза и средства для уничтожения вредителей.
promplace.ru
Производство меди | Металлургический портал MetalSpace.ru
В рудах медь находится в виде сернистых соединений (CuFeS2 – халько-пирит, Cu2S – халькозин, CuS – ковелин), оксидов (CuO, CuO) и гидрокарбонатов [CuCO3·Cu(OH)2,2CuCO3·Cu(OH)2]
Пустая порода руд состоит из пирита (FeS2), кварца (SiO2), различных соединений содержащих Al2O3, MgO, CaO, и оксидов железа.
В рудах иногда содержится значительные количества других металлов (цинк, золото, серебро и другие).
Известны два способа получения меди из руд:
- гидрометаллургический;
- пирометаллургический.
Гидрометаллургический не нашел своего широкого применения из-за невозможности извлекать попутно с медью драгоценные металлы.
Пирометаллургический способ пригоден для переработки всех руд и включает следующие операции:
- подготовка руд к плавке;
- плавка на штейн;
- конвертирование штейна;
- рафинирование меди.
Подготовка руд к плавке
Подготовка руд заключается в проведении обогащения и обжига. Обогащение медных руд проводят методом флотации. В результате получают медный концентрат, содержащий до 35% меди и до 50% серы. Концентраты обжигают обычно в печах кипящего слоя с целью снижения содержания серы до оптимальных значений. При обжиге происходит окисление серы при температуре 750 – 800 °С, часть серы удаляется с газами. В результате получают продукт, называемый огарком.
Плавку на штейн
Плавку на штейн ведут в отражательных или электрических печах при температуре 1250 – 1300 °С. В плавку поступают обожженные концентраты медных руд, в ходе нагревания которых протекают реакции восстановления оксида меди и высших оксидов железа
6CuO + FeS = 3Cu2O + FeO + SO2
FeS + 3Fe3O4 + 5SiO2 = 5(2FeO·SiO2) + SO2
В результате взаимодействия Cu2O с FeS образуется Cu2S по реакции:
Cu2O + FeS = Cu2S + FeO
Сульфиды меди и железа, сплавляясь между собой, образуют штейн, а расплавленные силикаты железа, растворяя другие оксиды, образуют шлак. Штейн содержит 15 – 55% Cu; 15 – 50% Fe; 20 – 30% S. Шлак состоит в основном из SiO2, FeO, CaO, Al2O3.
Штейн и шлак выпускают по мере их накопления через специальные отверстия.
Конвертирование штейна
Конвертирование штейна осуществляется в медеплавильных конвертерах (рисунок 44) путем продувки его воздухом для окисления сернистого железа, перевода железа в шлак и выделения черновой меди.
Конвертеры имеют длину 6 – 10 м и наружный диаметр 3 – 4 м. Заливку расплавленного штейна, слив продуктов плавки и удаление газов осуществляют через горловину, расположенную в средней части корпуса конвертера. Для продувки штейна подается сжатый воздух через фурмы, расположенные по образующей конвертера. В одной из торцевых стенок конвертера расположено отверстие, через которое проводится пневматическая загрузка кварцевого флюса, необходимого для удаления железа в шлак.
Процесс продувки ведут в два периода. В первый период в конвертер заливают штейн и подают кварцевый флюс. В этом периоде протекают реакции окисления сульфидов
2FeS + 3O2 = 2Fe + 2SO2,
2Cu2S + 3O2 = 2Cu2O + 2SO2
Образующаяся закись железа взаимодействует с кварцевым флюсом и удаляется в шлак
2FeO + SiO2 = (FeO)2·SiO2
По мере накопления шлака его частично сливают и заливают в конвертер новую порцию исходного штейна, поддерживая определенный уровень штейна в конвертере. Во втором периоде закись меди взаимодействует с сульфидом меди, образуя металлическую медь
2Cu2O + Cu2S = 6Cu + SO2
Таким образом, в результате продувки получают черновую медь, содержащую 98,4 – 99,4% Cu. Полученную черновую медь разливают в плоские изложницы на ленточной разливочной машине.
Рафинирование меди.
Для получения меди необходимой чистоты черновую медь подвергают огневому и электролитическому рафинированию. При этом, помимо удаления примесей можно извлекать также благородные металлы.
При огневом рафинировании черновую медь загружают в пламенную печь и расплавляют в окислительной атмосфере. В этих условиях из меди удаляются в шлак те примеси, которые обладают большим сродством к кислороду, чем медь.
Для ускорения процесса рафинирования в ванну с расплавленной медью подают сжатый воздух. Большинство примесей в виде оксидов переходят в шлак (Fe2O3, Al2O3, SiO2), а некоторые примеси при рафинировании удаляются с газами. Благородные металлы при огневом рафинировании полностью остаются в меди. Кроме благородных металлов в меди в небольших количествах присутствуют примеси сурьмы, селена, теллура, мышьяка. После огневого рафинирования получают медь чистотой 99 – 99,5%.
Для удаления этих примесей, а также для извлечения золота и серебра медь подвергают электролитическому рафинированию.
Электролиз ведут в специальных ваннах, футерованных внутри свинцом или другим защитным материалом. Аноды изготовляют из меди огневого рафинирования, а катоды – из тонких листов чистой меди. Электролитом служит раствор сернокислой меди. При пропускании постоянного тока анод растворяется и медь переходит в раствор. На катодах разряжаются ионы меди, осаждаясь на них прочным слоем чистой меди.
Находящиеся в меди примеси благородных металлов выпадают на дно ванны в виде остатка (шлама). После электролитического рафинирования получают медь чистотой 99,95 – 99,99%.
ПОДЕЛИСЬ ИНТЕРЕСНОЙ ИНФОРМАЦИЕЙ
metalspace.ru
способы, технология, схема производства, методы в промышленности
Особенности медных руд
Медьсодержащие руды характеризуются как многоэлементные. Наиболее часто встречающиеся соединения бывают с:
- железом;
- серой;
- медью.
В незначительной концентрации могут присутствовать:
- никель;
- золото;
- платина;
- серебро.
Месторождения во всем мире имеют примерно одинаковый набор химических элементов в составе руды, отличаются лишь их процентным соотношением. Чтобы получить чистый металл, используют различные промышленные способы. Почти 90% металлургических предприятий используют одинаковый метод производства чистой меди – пирометаллургический.
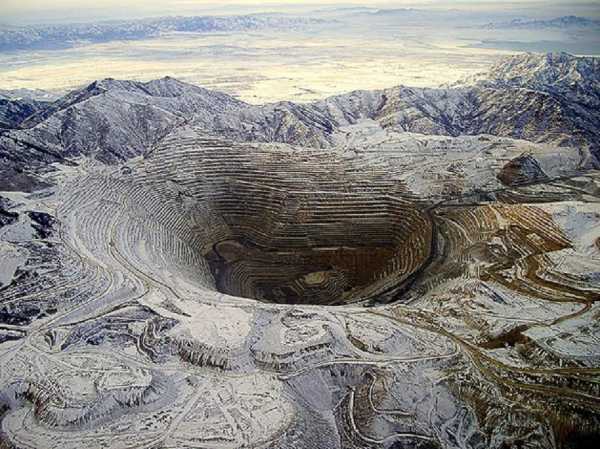
Один из самых больших карьеров по добыче руди приносит 17 миллионов тонн меди в год
Схема этого процесса позволяет также получать металл из вторичного сырья, что для промышленности является существенным плюсом. Поскольку месторождения относятся к группе не восполняемых – запасы с каждым годом уменьшаются, руды беднеют, а их добыча и производство становится дорогим. Это, в конечном счете, влияет на цену металла на международном рынке. Кроме пирометаллургического метода, существуют еще способы:
- гидрометаллургический;
- метод огневого рафинирования.
Стадии пирометаллургического производства меди
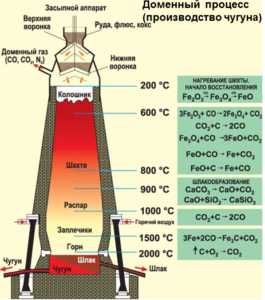
Общие способы получения метала из руды
Промышленное получение меди с использованием пирометаллургического способа имеет преимущества перед другими методами:
- технология обеспечивает высокую производительность – с ее помощью можно получать метал из породы, в которой содержание меди даже ниже 0,5%;
- позволяет эффективно перерабатывать вторичное сырье;
- достигнута высокая степень механизации и автоматизации всех этапов;
- при его использовании значительно сокращаются выбросы вредных веществ в атмосферу;
- метод экономичный и эффективный.
Обогащение
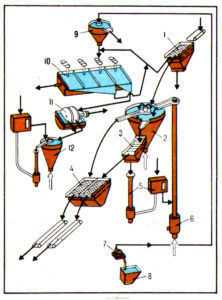
Схема обогащения руды
На первом этапе производства необходимо подготовить руду, которую доставляют на обогатительные комбинаты прямо с карьера или шахты. Часто встречаются большие куски породы, которые предварительно нужно измельчить.
Происходит это в огромных дробильных агрегатах. После дробления получается однородная масса, с фракцией до 150 мм. Технология предварительного обогащения:
- в большую емкость засыпается сырье и заливается водой;
- затем добавляется кислород под давлением, чтобы образовалась пена;
- частицы металла прилипают к пузырькам и поднимаются наверх, а пустая порода оседает на дне;
- далее, медный концентрат отправляется на обжиг.
Обжиг
Этот этап направлен на то, чтобы максимально снизить содержание серы. Рудную массу помещают в печь, где устанавливается температура 700–800оС. В результате термического воздействия содержание серы сокращается в два раза. Сера окисляется и испаряется, а часть примесей (железа и других металлов) переходит в легкошлакуемое состояние, которое облегчит в дальнейшем плавку.
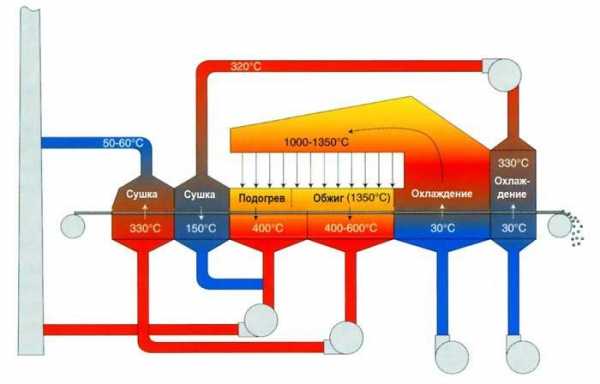
Обжиг руды для снижения уровня серы
Этот этап можно опустить, если порода богатая и содержит после обогащения 25–35% меди, его используют только для бедных руд.Плавка на штейн
Технология плавки на штейн позволяет получить черновую медь, которая различается по маркам: от МЧ1 – самая чистая до МЧ6 (содержит до 96% чистого металла). В ходе процесса плавки, сырье погружается в специальную печь, в которой температура поднимается до 1450оС.
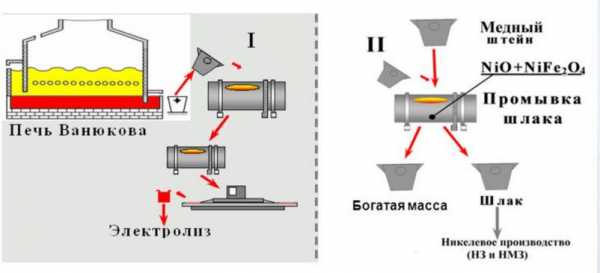
Технология переработки медной руды и получение черной меди
После расплавления массы она продувается сжатым кислородом в конвертерах. Они имеют горизонтальный вид, а дутье осуществляется через боковое отверстие. В результате продува сульфиды железа и серы окисляются и переводятся в шлак. Тепло в конвертере образуется за счет протекания раскаленной массы, он дополнительно не нагревается. Температура при этом составляет 1300оС.
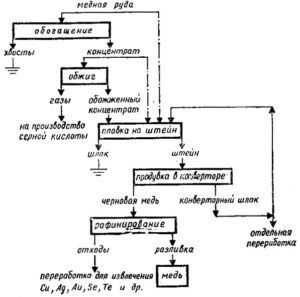
Общая схема выплавки меди
На выходе из конвертера получают черновой состав, который содержит до 0,04% железа и 0,1% серы, а также до 0,5% прочих металлов:
- олова;
- сурьмы;
- золота;
- никеля;
- серебра.
Такой черновой металл отливается в слитки массой до 1200 кг. Это так называемая анодная медь. Многие производители останавливаются на этом этапе, реализуют такие слитки. Но поскольку часто производство меди сопровождается добычей драгоценных металлов, которые содержатся в руде, то на обогатительных комбинатах используется технология рафинирования чернового сплава. При этом выделяются и сохраняются прочие металлы.
Рафинирование с использованием катодной меди
Технология получения рафинированной меди довольно простая. Ее принцип используют даже для чистки медных монет от окислов в домашних условиях. Схема производства выглядит следующим образом:
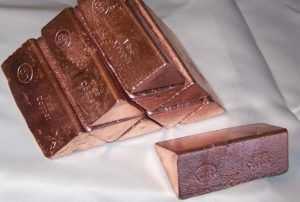
Слитки рафинированной меди
- черновой слиток помещается в ванну с электролитом;
- в качестве электролита используется раствор со следующим содержанием:
- сульфат меди – до 200 г/л;
- серная кислота – 135–200 г/л;
- коллоидные добавки (тиомочевина, столярный клей)– до 60 г/л;
- вода.
- температура электролита должна быть до 55оС;
- помещаются в ванну пластины катодной меди – тонкие листы чистого металла;
- подключается электричество. В это время происходит электрохимическое растворение металла. Частицы меди концентрируются на катодной пластине, а прочие включения оседают на дне и называются шлам.
Для того, чтобы процесс получения рафинированной меди протекал быстрее, анодные слитки должны быть не более 360 кг.
Весь процесс электролиза протекает в течение 20–28 суток. За этот период вынимают катодную медь до 3–4 раз. Вес пластин получается до 150 кг.
Как это делается: добыча меди
В процессе рафинирования, на катодной меди могут образовываться дендриты – наросты, которые сокращают расстояние до анода. В результате чего снижается скорость и эффективность реакции. Поэтому, при возникновении дендритов, их незамедлительно удаляют.
Технология гидрометаллургического производства меди
Медная руда также может содержать золото
Этот способ не получил широкого распространения, поскольку, при этом можно потерять драгоценные металлы, содержащиеся в медной руде.
Его использование оправдано, когда порода бедная – содержит менее 0,3% красного металла.
Как получить медь гидрометаллургическим способом?
Вначале порода измельчается до мелкой фракции. Затем помещается в щелочной состав. Чаще всего используют растворы серной кислоты или аммиака. Во время реакции медь вытесняется железом.
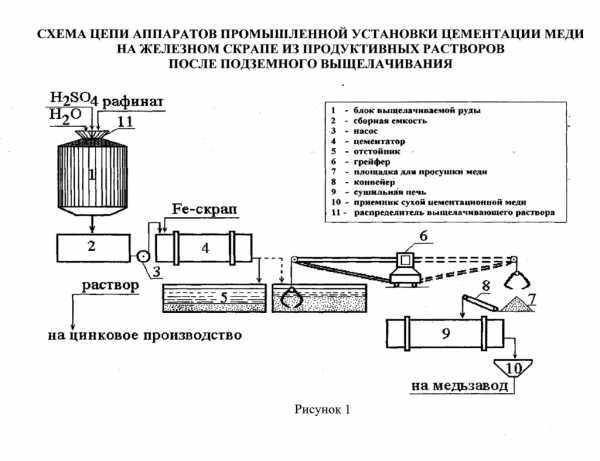
Цементация меди железом
Оставшиеся после выщелачивания растворы солей меди проходят дальнейшую обработку – цементацию:
- в раствор помещают железную проволоку, листы или прочие обрезки;
- в ходе химической реакции железо вытесняет медь;
- в результате металл выделяется в виде мелкого порошка, в котором содержание меди достигает 70%. Дальнейшее очищение происходит путем электролиза с использованием катодной пластины.
Технология огневого рафинирования черновой меди
Этот способ получения чистой меди используется, когда исходное сырье – медный лом.
Процесс протекает в специальных отражательных печах, которые топятся углем или нефтью. Растопленная масса наполняет ванну, в которую вдувают воздух по железным трубам:
- диаметр труб – до 19 мм;
- давление воздуха – до 2,5 атм;
- емкость печи – до 250 кг.
В процессе рафинирования окисляется медное сырье, выгорает сера, затем металлы. Окислы не растворяются в жидкой меди, а всплывают на поверхность. Чтобы их удалить, используется кварц, который помещается в ванну еще до начала процесса рафинирования и размещается вдоль стенок.
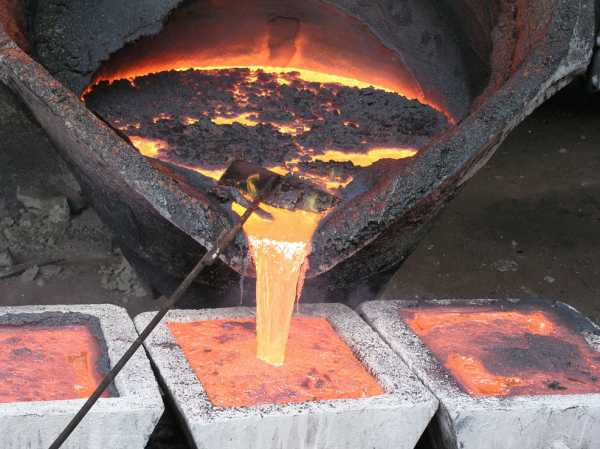
Рафинирование меди
Если в металлоломе присутствует никель, мышьяк или сурьма, то технология усложняется. Процент содержания никеля в рафинированной меди можно снизить лишь до уровня 0,35%. Но если присутствуют остальные компоненты (мышьяк и сурьма), то образуется никелевая «слюдка», которая растворяется в меди, и ее удалить не получится.
Видео: Медные руды Урала
ecology-of.ru
Производство меди
Наиболее ценным свойством меди является ее электропроводность, чем меньше металл содержит примесей, тем выше электропроводность. Поэтому для токопроводящих элементов (проволока, шины) применяют медь высших марок с содержанием меди 99,9%. Менее чистая медь, содержащая больше примесей, идет на производство сплавов — латуней и бронз.
Медь получают из руд с содержанием этого металла не ниже 0,5%. В природе встречаются около 30—40 медных минералов. Из сульфидных минералов наиболее распространен халькопирит.
Если для получения одной тонны чугуна перерабатывается до 2,5 т железной руды, то для производства одной тонны меди — до 200 т медной руды.
Получают медь из сульфидных руд по следующей схеме:
1. Дробление руды в дробилках с последующим измельчением в шаровых мельницах.
2. Флотаци онное обогащение — флотация. Тонко измельченную руду смешивают с небольшим количеством особого флотореагента, например ксантогената калия и извести, и подают в камеру флотационной машины. Ксантогенат калия покрывает тонкой пленкой частицы сульфидных минералов меди. Известь создает в пульпе определенную щелочность и предупреждает обволакиванием пленкой ксантогената частиц других минералов. В флотационной машине к частицам минералов меди прилипают пузырьки воздуха и выносят их на поверхность пульпы. Добавка пенообразователей (соснового масла, сланцевой смолы и др.) позволяет создать на поверхности пульпы устойчивую пену, удерживающую частицы минералов меди.
Полученный таким образом концентрат с флотомашины имеет большую влажность. Поэтому его обезвоживают последовательно сгущением в сгустителях и фильтрацией на фильтрах, затем сушат во вращающихся сушилках барабанного типа.
Примерно 90% всех добываемых медных руд подвергают флотационному обогащению, а 10%-направляют непосредственно в металлургическую обработку — плавку или выщелачивание. Медные концентраты содержат 20—30% Сu.
3. Обжиг. Высокосернистые руды и концентраты подвергают в многоподовых печах и в печах кипящего слоя обжигу при температуре до 850°С в окислительной атмосфере. При этом выгорает значительная часть серы. Продуктом обжига является обожженная шихта — огарок и газы, содержащие сернистый ангидрид, который используют для производства серной кислоты.
4. Плавка в отражательной печи. Плавят сырую, подсушенную или обожженную шихту при температуре до 1500—1550°С. При этом атмосфера в печи должна быть нейтральная или слабоокислительная. Цель плавки — сульфидирование меди и перевод ее в штейн (оплав сульфидов) при одновременном ошлаковании большей части железа кремнеземом. Окислы металлов и пустой породы, взаимодействуя, образуют шлак, который легче штейна и в ванне печи располагается над ним.
5. Конвертирование. Штейн в конверторе продувают воздухом в течение 16—24 ч в присутствии кварцевого флюса. В результате продувки сера выгорает, газы поступают в сернокислотное производство, полученная черновая медь содержит 97,5—99,5% Сu, остальное примеси. Черновую медь подвергают огневому рафинированию, а затем электролизу для очистки от примесей и извлечения из нее благородных металлов.
6. Огневое рафинирование. Черновую медь расплавляют в специальной печи (или заливают в нее жидкую медь) и рафинируют отри температуре 1200°С.
Для удаления железа, цинка, серы и других примесей вначале осуществляет окисление жидкой меди продувкой воздухом. Полученная закись меди хорошо растворяется и реагирует со всеми имеющимися в жидкой меди примесями. Образующиеся окислы примесей всплывают на поверхность ванны, где и ошлаковываются. После удаления примесей закись меди восстанавливают (операция «дразнение»), получая конечный продукт—анодную («красную») медь с содержанием 99—99,7% Сu.
7. Электролитическое рафинирование. Этому подвергают огневую и анодную медь для получения наиболее чистой меди с содержанием ее 99,9%. Электролиз ведут в водном растворе сульфата меди, содержащем свободную серную кислоту. В результате электролиза чистая медь осаждается на катодах (тонких листах электролитической меди), а на дне ванны собирается шлам, который в дальнейшем перерабатывают для извлечения благородных металлов.
Возможно, Вас так же заинтересует:mse-online.ru
6.1. Производство меди | Материаловед
Для получения меди применяют медные руды (содержание меди – 1…6 %), а также отходы меди и ее сплавов.
Медь в природе находится в виде сернистых соединений (CuS, Cu2S), оксидов (CuO, Cu2O), гидрокарбонатов (Cu(OH)2), углекислых соединений (CuCO3) в составе сульфидных руд и самородной металлической меди.
Наиболее распространенные руды – медный колчедан и медный блеск, содержащие 1…2 % меди.
90 % первичной меди получают пирометаллургическим способом, 10% — гидрометаллургическим.
Гидрометаллургический способ – получение меди путём её выщелачивания слабым раствором серной кислоты и последующего выделения металлической меди из раствора. Метод используют при переработке бедных руд, он не позволяет извлекать попутно с медью драгоценные металлы.
Получение меди пирометаллургическим способом состоит из обогащения, обжига, плавки на штейн, продувки в конвертере, рафинирования.
Обогащение медных руд производится методом флотации и окислительного обжига.
Метод флотации основан на использовании различной смачиваемости медьсодержащих частиц и пустой породы. Сущность флотации состоит в избирательном прилипании некоторых минеральных частиц, взвешенных в водной среде, к поверхности пузырьков воздуха, с помощью которых эти минеральные частицы поднимаются на поверхность. Метод позволяет получать медный порошкообразный концентрат, содержащий 10…35 % меди.
Медные руды и концентраты, содержащие большие количества серы, подвергаются окислительному обжигу. В процессе нагрева концентрата или руды до 700…800 0C в присутствии кислорода воздуха сульфиды окисляются и содержание серы снижается почти вдвое против исходного. Обжигают только бедные (с содержанием меди 8…25 %) концентраты, а богатые (25…35 % меди) плавят без обжига.
После обжига руда и медный концентрат подвергаются плавке на штейн, представляющий собой сплав, содержащий сульфиды меди и железа (Cu2S, FeS). Штейн содержит 20…50 % меди, 20…40 % железа, 22…25 % серы, около 8 % кислорода и примеси никеля, цинка, свинца, золота, серебра. В зависимости от химического состава руды и ее физического состояния штейн получают либо в шахтных печах, если сырьем служит кусковая медная руда, содержащая много серы, либо в отражательных печах, если исходным продуктом является порошкообразный флотационный концентрат. Чаще всего плавка производится в пламенных отражательных печах. Температура в зоне плавки — 1450 0C.
Полученный медный штейн, в целях окисления сульфидов и железа подвергают продувке сжатым воздухом в горизонтальных конвертерах с боковым дутьём. Образующиеся окислы переводят в шлак, а серу – в SO2. Тепло в конвертере выделяется за счёт протекания химических реакций без подачи топлива. Температура в конвертере составляет 1200…1300 ºC. Таким образом, в конвертере получают черновую медь, содержащую 98,4…99,4 % меди, 0,01…0,04 % железа, 0,02…0,1 % серы и небольшое количество никеля, олова, сурьмы, серебра, золота. Эту медь сливают в ковш и разливают в стальные изложницы или на разливочной машине.
Черновую медь рафинируют для удаления вредных примесей, проводят огневое, а затем электролитическое рафинирование.
Сущность огневого рафинирования черновой меди заключается в окислении примесей, имеющих большее сродство к кислороду, чем медь, удалении их с газами и переводе в шлак. После огневого рафинирования получают медь чистотой 99…99,5 %. Её разливают в изложницы и получают чушки для дальнейшей выплавки сплавов (бронзы и латуни) или слитки для электролитического рафинирования.
Электролитическое рафинирование проводят для получения чистой от примесей меди (99,95 % Cu).
Электролиз осуществляют в ваннах, где анод изготавливают из меди огневого рафинирования, а катод – из тонких листов чистой меди. Электролитом служит водный раствор CuSO4 (10…16 %) и H2SO4 (10…16 %).
При пропускании постоянного тока анод растворяется, медь переходит в раствор, а на катодах разряжаются ионы меди, осаждаясь на них слоем чистой меди.
Примеси осаждаются на дно ванны в виде шлама, который идёт на переработку в целях извлечения металлов: серебра, сурьмы, селена, теллура, золота и др…
Катоды выгружают через 5…12 дней, когда их масса достигнет 60…90 кг. Их тщательно промывают, а затем переплавляют в электропечах.
Медь по чистоте подразделяется на марки: М0 (99,95 % Cu), М1 (99,9 %), М2 (99,7 %), М3 (99,5 %), М4 (99 %).
xn--80aagiccszezsw.xn--p1ai
41. Особенности производства меди
Медь встречается в самородном виде. В настоящее время медь производят металлургическим способом, отделением ее от кислорода и серы. Не смотря на то, что содержание меди в земной коре невелико (0,01%), она не рассеянный метал и концентрируется в медных рудах, где содержание её порядка 5%. По свойствам медь близка к серебру и золоту. Чистая медь имеет ряд ценных технических свойств. Высокая пластичность, высокая электро- и теплопроводность, малая окисляемость — всё это обусловило широкое применение меди. Кроме того медь является основой важнейших сплавов — латуней и бронз. Высокая электропроводность меди обусловливает её преимущественное применение в электротехнике как проводникового металла. После серебра медь стоит на втором месте по электропроводности.
Получение меди.
Медь получают главным образом пирометаллургическим способом, сущность которого состоит в производстве меди из медных руд, включающем ее обогащение, обжиг, плавку на полупродукт — штейн, выплавку из штейна черновой меди и ее очистку от примесей (рафинирование).
Для производства меди применяют медные руды, содержащие 1 — 6% Cu, а также отходы меди и ее сплавов. В рудах медь обычно находится в виде сернистых соединений, оксидов или гидрокарбонатов. Перед плавкой медные руды обогащают и получают концентрат. Для уменьшения содержания серы в концентрате его подвергают окислительному обжигу. Полученный концентрат переплавляют в отражательных или электрических печах. Восстанавливаются оксид меди (CuO) и высшие оксиды железа.
Сульфиды меди и железа сплавляются и образуют штейн, а расплавленные силикаты железа растворяют другие оксиды и образуют шлак. После этого расплавленный медный штейн заливают в конвертеры и продувают воздухом для окисления сульфидов меди и железа и получения черновой меди. Черновая медь содержит 98,4-99,4% Cu и небольшое количество примесей. Эту медь разливают в изложницы. Черновую медь рафинируют для удаления вредных примесей и газов. Сначала производят огневое рафинирование в отражательных печах. Примеси S, Fe, Ni, As, Sb и другие окисляются кислородом воздуха, подаваемым по стальным трубкам, погруженным в расплавленную черновую медь. Затем удаляют газы, для чего снимают шлак и погружают в медь сырое дерево. Пары воды перемешивают медь и способствуют удалению других газов. Ванну жидкой меди покрывают древесным углем и погружают в нее деревянные жерди. При сухой перегонке древесины, погруженной в медь, образуются углеводороды.
После огневого рафинирования получают медь чистотой 99-99,5%. Из нее отливают чушки для выплавки сплавов меди (бронзы и латуни) или плиты для электролитического рафинирования.
Электролитическое рафинирование проводят для получения чистой от примесей меди (99,5% Cu). Электролиз ведут в ваннах, покрытых изнутри винипластом или свинцом. Аноды делают из меди огневого рафинирования, а катоды — из листов чистой меди. При пропускании постоянного тока анод растворяется, медь переходит в раствор, а на катодах разряжаются ионы меди.
Примеси (мышьяк, сурьма, висмут и др.) осаждаются на дно ванны, их удаляют и перерабатывают для извлечения этих металлов. Катоды выгружают, промывают и переплавляют в электропечах.
Реализация этой схемы на различных переделах, особенно на начальных этапах до получения медного штейна, может проводиться в различных печах и в различных технологических вариантах. В рассматриваемой схеме первый передел медной руды — это обогащение. Однако бывают случаи, когда руды, обогащенные серой (свыше 35%), плавят без обогащения для извлечения из них не только меди, но и серы. Однако основная масса добываемой из недр земли сульфидной медной руды подвергается флотационному обогащению.
studfiles.net
Производство меди | Металлургический портал MetalSpace.ru
В рудах медь находится в виде сернистых соединений (CuFeS2 – халько-пирит, Cu2S – халькозин, CuS – ковелин), оксидов (CuO, CuO) и гидрокарбонатов [CuCO3·Cu(OH)2,2CuCO3·Cu(OH)2]
Пустая порода руд состоит из пирита (FeS2), кварца (SiO2), различных соединений содержащих Al2O3, MgO, CaO, и оксидов железа.
В рудах иногда содержится значительные количества других металлов (цинк, золото, серебро и другие).
Известны два способа получения меди из руд:
- гидрометаллургический;
- пирометаллургический.
Гидрометаллургический не нашел своего широкого применения из-за невозможности извлекать попутно с медью драгоценные металлы.
Пирометаллургический способ пригоден для переработки всех руд и включает следующие операции:
- подготовка руд к плавке;
- плавка на штейн;
- конвертирование штейна;
- рафинирование меди.
Подготовка руд к плавке
Подготовка руд заключается в проведении обогащения и обжига. Обогащение медных руд проводят методом флотации. В результате получают медный концентрат, содержащий до 35% меди и до 50% серы. Концентраты обжигают обычно в печах кипящего слоя с целью снижения содержания серы до оптимальных значений. При обжиге происходит окисление серы при температуре 750 – 800 °С, часть серы удаляется с газами. В результате получают продукт, называемый огарком.
Плавку на штейн
Плавку на штейн ведут в отражательных или электрических печах при температуре 1250 – 1300 °С. В плавку поступают обожженные концентраты медных руд, в ходе нагревания которых протекают реакции восстановления оксида меди и высших оксидов железа
6CuO + FeS = 3Cu2O + FeO + SO2
FeS + 3Fe3O4 + 5SiO2 = 5(2FeO·SiO2) + SO2
В результате взаимодействия Cu2O с FeS образуется Cu2S по реакции:
Cu2O + FeS = Cu2S + FeO
Сульфиды меди и железа, сплавляясь между собой, образуют штейн, а расплавленные силикаты железа, растворяя другие оксиды, образуют шлак. Штейн содержит 15 – 55% Cu; 15 – 50% Fe; 20 – 30% S. Шлак состоит в основном из SiO2, FeO, CaO, Al2O3.
Штейн и шлак выпускают по мере их накопления через специальные отверстия.
Конвертирование штейна
Конвертирование штейна осуществляется в медеплавильных конвертерах (рисунок 44) путем продувки его воздухом для окисления сернистого железа, перевода железа в шлак и выделения черновой меди.
Конвертеры имеют длину 6 – 10 м и наружный диаметр 3 – 4 м. Заливку расплавленного штейна, слив продуктов плавки и удаление газов осуществляют через горловину, расположенную в средней части корпуса конвертера. Для продувки штейна подается сжатый воздух через фурмы, расположенные по образующей конвертера. В одной из торцевых стенок конвертера расположено отверстие, через которое проводится пневматическая загрузка кварцевого флюса, необходимого для удаления железа в шлак.
Процесс продувки ведут в два периода. В первый период в конвертер заливают штейн и подают кварцевый флюс. В этом периоде протекают реакции окисления сульфидов
2FeS + 3O2 = 2Fe + 2SO2,
2Cu2S + 3O2 = 2Cu2O + 2SO2
Образующаяся закись железа взаимодействует с кварцевым флюсом и удаляется в шлак
2FeO + SiO2 = (FeO)2·SiO2
По мере накопления шлака его частично сливают и заливают в конвертер новую порцию исходного штейна, поддерживая определенный уровень штейна в конвертере. Во втором периоде закись меди взаимодействует с сульфидом меди, образуя металлическую медь
2Cu2O + Cu2S = 6Cu + SO2
Таким образом, в результате продувки получают черновую медь, содержащую 98,4 – 99,4% Cu. Полученную черновую медь разливают в плоские изложницы на ленточной разливочной машине.
Рафинирование меди.
Для получения меди необходимой чистоты черновую медь подвергают огневому и электролитическому рафинированию. При этом, помимо удаления примесей можно извлекать также благородные металлы.
При огневом рафинировании черновую медь загружают в пламенную печь и расплавляют в окислительной атмосфере. В этих условиях из меди удаляются в шлак те примеси, которые обладают большим сродством к кислороду, чем медь.
Для ускорения процесса рафинирования в ванну с расплавленной медью подают сжатый воздух. Большинство примесей в виде оксидов переходят в шлак (Fe2O3, Al2O3, SiO2), а некоторые примеси при рафинировании удаляются с газами. Благородные металлы при огневом рафинировании полностью остаются в меди. Кроме благородных металлов в меди в небольших количествах присутствуют примеси сурьмы, селена, теллура, мышьяка. После огневого рафинирования получают медь чистотой 99 – 99,5%.
Для удаления этих примесей, а также для извлечения золота и серебра медь подвергают электролитическому рафинированию.
Электролиз ведут в специальных ваннах, футерованных внутри свинцом или другим защитным материалом. Аноды изготовляют из меди огневого рафинирования, а катоды – из тонких листов чистой меди. Электролитом служит раствор сернокислой меди. При пропускании постоянного тока анод растворяется и медь переходит в раствор. На катодах разряжаются ионы меди, осаждаясь на них прочным слоем чистой меди.
Находящиеся в меди примеси благородных металлов выпадают на дно ванны в виде остатка (шлама). После электролитического рафинирования получают медь чистотой 99,95 – 99,99%.
ПОДЕЛИСЬ ИНТЕРЕСНОЙ ИНФОРМАЦИЕЙ
metalspace.ru