Технология производства поликарбоната: сотового и монолитного
В качестве инженерного пластика поликарбонат приобрел большую известность и популярность. Материал является линейным полиэфиром. В промышленности используется только ароматическая группа данного вещества. На его основе создаются композиции, относящиеся к специальным полимерам. В промышленности технология производства поликарбоната разделена на два основных этапа: синтез мелкозернистого полуфабриката и создание из него листового строительного материала. Обычно их осуществляют на разных предприятиях.
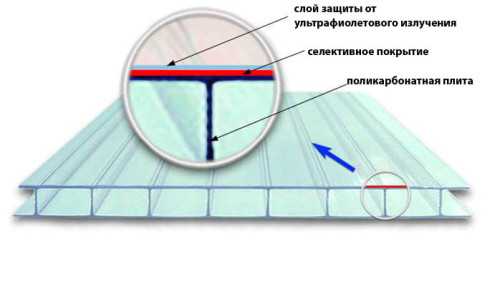
Схема листа сотового поликарбоната.
Изготовление исходного сырья
До недавнего времени промышленное изготовление гранул для дальнейшей переработки производилось только методом межфазной поликонденсации. Процесс полимеризации при этом происходит на границе раздела жидкости и газа, то есть двух фаз. Для производства используются двухатомный фенол и угольная кислота (фосген). В реакции также участвуют определенный органический растворитель и пиридин, служащий и катализатором, и акцептором.
К достоинствам данной методики, по которой и сейчас производится свыше 80% полимера, относится невысокая, до 25°С, температура реакции и сравнительно небольшие затраты энергии. Кроме того, она позволяет получать разнообразные виды поликарбоната, в том числе высокой молекулярной массы. Основным недостатком является присутствие в реакции фосгена, обладающего высокой токсичностью. Полученный полимер нуждается в очистке от побочных продуктов и от остатков реагентов. Как следствие, на его промывку уходит много воды. Это, в свою очередь, приводит к большому объему сточных вод. Осаждение полученной массы производится специальным реагентом, к примеру, ацетоном.
Схема монтажа сотового поликарбоната.
Более новая технология производства методом переэтерификации позволяет осуществлять реакцию в расплаве при температуре от 250 до 300 °С. Реакция основана на химическом взаимодействии двух основных ингредиентов: дифенилолпропана и диметилового эфира угольной кислоты. Это позволяет сэкономить на растворителе и обойтись без токсичного фосгена. Недостаток же заключается в том, что выделяется побочный продукт, анизол, мировая потребность в котором ничтожно мала. Из-за этого его просто приходится сжигать. Кроме того, при такой методике увеличиваются расход энергии и затраты на особо чистые реагенты. Наконец, данный способ пока не дает возможности создавать высокомолекулярный поликарбонат.
При необходимости в выделенную и промытую полимерную массу добавляют какой-нибудь краситель. Затем ее сушат, еще теплой пропускают через экструдер для получения крупинок или прутьев, а потом фасуют в многослойные мешки.
Химические реакции, в результате которых получается поликарбонат, являются необратимыми, а синтезированная продукция — нетоксичной.
Поскольку приобрести очень дорогую лицензию на производство гранул могут позволить себе лишь немногие фирмы, большинство предприятий для дальнейшей переработки предпочитает покупать готовое сырье.
Вернуться к оглавлению
Очистка, плавление и экструзия
Схема крепления листов поликарбоната к металлическому каркасу.
На предприятии гранулы из мешков перегружают в специальные бункеры, которые называются силосами. Силос имеет дно в виде воронки, через которую происходит отбор сырья. Гранулы поликарбоната попадают на пневмотранспортер, который доставляет их в устройство для очистки — циклон. Циклон работает по принципу центрифуги, отбрасывая в сторону частички пыли. Затем необходимое количество сырья отмеряют в автоматическом дозаторе, после чего гранулы загружаются в камеру для плавления.
Чтобы улучшить качество материала и придать ему необходимые свойства, в плавильную камеру добавляют определенные присадки. Они смогут предотвратить конденсацию влаги на поверхности листа, наделить его свойством отталкивания воды и грязи. Добавление металлической крошки улучшает отражение инфракрасного излучения и позволяет материалу лучше сохранять тепло. Благодаря ей поликарбонат приобретает модный оттенок «металлика». Смесь постоянно перемешивается и постепенно нагревается до 250-290 °С. Газы, которые при этом выделяются, отводят наружу.
Поскольку даже при такой высокой температуре расплав имеет очень вязкую консистенцию, ровный материал в виде ленты из него удобнее всего формировать путем экструзии, то есть продавливания через особую матрицу — фильеру. Одновременно с этим лента может покрываться тонкой пленкой, защищающей от разрушительного воздействия ультрафиолетового излучения. На завершающем этапе с помощью пресса ленте придают необходимую толщину. При этом происходит окончательное сглаживание неровностей. После этого остается только разрезать ленту на листы необходимого размера.
Экструдер используется для производства поликарбоната различной структуры: как монолитного, так и сотового. Матрица определяет строение получаемого листа.
Вернуться к оглавлению
Технология производства методом литья
Из пластика можно изготавливать не только листовой материал, но и отливать готовые изделия или отдельные детали. Их формируют при помощи литья под давлением, а сосуды — методом выдувного литья. Чтобы создать пленку толщиной всего 125-640 мкм, используется раствор поликарбоната в метиленхлориде. Для этого берут пластик с высокой молекулярной массой.
Перед началом процесса литья под давлением исходный материал высушивают в бункерных сушилках при температуре 110-120 °С. Преимущество такой обработки состоит в отсутствии повторного впитывания влаги при хранении или транспортировке. Затем материал поступает в нагревательный цилиндр, где его доводят путем нагрева до вязко-текучего состояния.
Особенность производства литых деталей заключается в относительно невысоком, до 150-160°С, повышении температуры расплава и разогревании формы до 80-100°С. Процесс осуществляется на литьевом автомате. Он разделен на отдельные технологические этапы. Сначала смыкается форма для заливки, потом осуществляется впрыскивание разогретого материала. В форме происходит его уплотнение под давлением 70-150 МПа. Затем поликарбонат выдерживается в форме еще некоторое время, необходимое для остывания. Наконец, форма размыкается, а готовая деталь вынимается.
Следует заметить, что каждому способу производства поликарбонатной продукции должны соответствовать определенные марки пластика — литьевые, экструзионные, экструзионно-литьевые, а также для выдувного литья. В некоторых случаях производится изменение характеристик полимера путем армирования стеклянными или графитовыми волокнами.
polikarbonatstroy.ru
Производство поликарбоната: современные технологии (видео)
Благодаря универсальным техническим характеристикам, таким как легкость, прочность, коррозийная стойкость, поликарбонаты являются очень востребованным материалом в различных отраслях промышленности: в производстве автомобилей, электротехнической, электронной промышленности, в производстве предметов бытового потребления и т.д. Составляя серьезную конкуренцию металлу и стеклу, за счет увеличения потребления конструкционных материалов доля литого и сотового поликарбонатов на мировом рынке с каждым годом завоевывает все новые позиции.

Поликарбонат это материал, обладающий следующими свойствами: устойчив к морозам, способен выдержать кратковременный нагрев до 153 ºС, а также циклические перепады температур от +100ºС до -253ºС.
Производство поликарбоната — сложный технологический процесс, в основе которого лежит использование двухатомного фенола и угольной кислоты.
Поликарбонат является линейным полиэфиром этих двух составляющих компонентов. В зависимости от природы, поликарбонаты разделяются на алифатические, жирноароматические и ароматические. Практическое значение имеет лишь ароматический поликарбонат. Поликарбонаты относятся к разряду аморфных, инженерных пластиков, а изготовленные на их основе композиции — к специальным полимерам.
Достоинства поликарбоната
Схема структур сотового поликарбоната.
Широкий диапазон использования литого и сотового поликарбоната обусловлен универсальными термическими, оптическими и механическими свойствами данного материала. Так, поликарбонат обладает высокой прочностью и жесткостью в сочетании с довольно высокой стойкостью к различным ударным воздействиям, в том числе и при повышенной или пониженной температуре.
Поликарбонат — морозостойкий, оптически прозрачный материал, способный выдерживать кратковременный нагрев до 153ºС и циклические перепады температур от +100ºС до -253ºС. Поликарбонат устойчив к агрессивному воздействию окислителей, растворов солей, кислот, но не обладает устойчивостью к действию щелочей, органических растворителей и концентрированных кислот.
Вернуться к оглавлению
Современные технологии изготовления поликарбоната
Процесс создания поликарбоната базируется на использовании одной из следующих технологий: поликонденсации, переэтерификации или межфазной поликонденсации.
Поликонденсация — это метод синтеза полимеров, базирующийся на реакциях замещения мономеров и/или олигомеров, которые, взаимодействуя между собой, образовывают побочные низкомолекулярные соединения.
Переэтерификация диарилкарбонатов проводится с ароматическими диоксисоединениями (так называемый нефосгенный способ). В качестве диоксисоединения выступает 2,2-бис-(4-оксифенил) пропан (диан, бисфенол А).
В промышленном производстве поликарбоната в настоящее время используется способ, базирующийся на межфазной поликонденсации. Согласно данному методу производится взаимодействие динатриевой соли бисфенола А с фосгеном в присутствии оснований. Протекающие при взаимодействии процессы практически необратимы. Данная технология используется для производства 80% поликарбоната в мире.
Наша отечественная технология также применяет метод межфазной поликонденсации фосгена с бисфенолом А. Очевидными недостатками данного метода является высокая токсичность реагента, склонность к образованию побочных продуктов и необходимость последующей очистки образующегося полимера от изначально применяемых реагентов и побочных компонентов.
Схема устройства оптического поликарбоната.
Производство полимеров на основе новейших технологий ориентировано на нефосгенный метод выпуска, который базируется на процессах взаимодействия диметилового эфира угольной кислоты (ДМУК) и дифенилолпропана. Подобное решение позволяет перевести технологическую процедуру получения ПК из фазы жидкого состояния в расплав, исключить экологически опасный фосген и существенно увеличить объемы производства.
Бесфосгенный метод по всем параметрам, кроме энергетических расходов, превосходит традиционные технологии. Но пока и он не лишен некоторых недостатков, в число которых входит побочное выделение анизола, не имеющего на данном этапе полезного применения в том объеме, который образуется в ходе нефосгенной реакции. Мировое потребление анизола в настоящее время составляет до 7 тыс. тонн, поэтому излишки материала отправляются на сжигание. Еще одним существенным минусом нефосгенной технологии является невозможность получения ряда марок поликарбоната — высокомолекулярного поликарбоната и сополимеров на основе поликарбоната.
Поликарбонатный гранулят, как известно, является основой для производства листов поликарбоната, в число которых входит и сотовый поликарбонат. Этот материал представляет собой листы ячеистой структуры, выполненные из полимера в виде сот, которые состоят из двух слоев, соединенных посредством внутренних ребер жесткости между собой. Сотовый поликарбонат — легкий, устойчивый к коррозийным процессам, ударопрочный материал с хорошими теплоизоляционными и светопрозрачными свойствами.
На рынке, помимо обычного сотового поликарбоната, можно встретить и более долговечный его аналог — полимер, покрытый специальным защитным слоем, устойчивым к ультрафиолетовому излучению. Благодаря своим универсальным свойствам сотовый поликарбонат очень востребован в строительстве и сельском хозяйстве. В зависимости от толщины, он выступает в качестве прекрасного материала для оборудования навесов, арок, крыш, витрин, перегородок, бассейнов, теплиц, балконов, автобусных остановок, вокзалов, стадионов и т.д., поэтому в число целевых потребителей материала входят автостоянки, муниципалитет, рекламные и дизайнерские компании, АЗС, подрядчики, тепличные хозяйства и сельскохозяйственные предприятия.
Вернуться к оглавлению
Изготовление сотового поликарбоната
Для производства сотового поликарбоната используются поликарбонатные гранулы. Изготовление материала включает в себя прохождение гранулами цикла определенных технологических процессов. Производство сотового поликарбоната предполагает наличие:
Схема воздействия солнечных лучей на поликарбонат.
- гранул поликарбоната;
- специализированного оборудования;
- специальных химических добавок.
Вначале закупается поликарбонатный гранулят. Стоит учитывать, что, в зависимости от цвета гранул (которые могут быть белыми, цветными и прозрачными), в конечном итоге получится материал определенной цветовой гаммы. Поэтому при покупке стоит обращать внимание на цвет сырья.
После взвешивания, сортировки, очистки от пыли для производства листов гранулы поступают на плавление.
В камере плавления гранулы переходят из твердого состояния в жидкое, к ним добавляются специальные компоненты, способствующие улучшению характеристики будущего материала. В конечном итоге образуется однородная смешанная масса.
Далее начинается процесс экструзии, в ходе которого бесформенная масса преобразуется в нужную структуру, монолитную или сотовую. Помимо основного процесса экструзии, поликарбонатная масса одновременно подвергается соэкструзии тонкой пленкой, поглощающей ультрафиолетовое излучение, что способствует сохранению превосходной прочности материала.
На следующем этапе прозрачный или цветной сотовый поликарбонат в виде тонких пластин, скрепленных между собой прочными ребрами жесткости, подается на конвейер.
После остывания пластины поликарбоната нарезаются на нужные размеры, складируются и в многослойных, защищенных от проникновения влаги мешках поступают на хранение.
polikarbonatstroy.ru
Поликарбонаты производство — Справочник химика 21
Для получения дифенилолпропана, пригодного в производстве поликарбонатов, японские исследователи рекомендуют перед отгонкой фенола удалять хлористый водород. После синтеза реакционную массу разбавляют водой, нагревают до 65—70 °С и разделяют на два слоя (верхний — фенол и вода, нижний — дифенилолпропан и фенол). Добавление воды и разделение слоев повторяют несколько раз, после чего нижний слой перегоняют в вакууме (остаточное давление 15—20 мм рт. ст.) при повышении температуры до 200 °С. [c.126]Получаемый продукт отличается хорошим качеством и может быть использован в производстве эпоксидных полимеров и поликарбонатов, где требования к качеству сырья особенно высоки, а также в других областях. [c.158]
В дифенилолпропане, выделенном из реакционной массы описанными в гл. III—V способами, остается некоторое количество побочных продуктов. Присутствие же примесей строго ограничивается, в частности в дифенилолпропане, используемом для производства поликарбонатов. [c.160]
Схема процесса производства поликарбоната непрерывным методом представлена на рис. 51. [c.76]
Схема 7. Производство поликарбоната. [c.712]
Получение поликарбоната. Последовательность операций при производстве поликарбоната методом поликоиденсации представлена на схеме 7. Дифенилолпропан смешивают с водным раствором едкого натра, взятого в эквимолекулярном количестве к выделяющемуся хлористому одороду. В аппарат для поликондепсации, снабженный мешалкой и рубашкой для охлаждения водой, загружают все количество смеси дифенилолпропана и едкого натра, а затем постепенно добавляют раствор фосгена в хлористом метилене. Реакцию поликонденсации проводят при температуре 20—30 и непрерывном перемешивании смеси. Образование полимера ускоряется добавлением третичных аминов или четвертичного аммониевого основания. Величину среднего молекулярного веса полимера можно регулировать введением в реактор тга/)ет-бутилфенола. [c.712]
Чистота БФА, получаемого с использованием серной кислоты в качестве катализатора, достаточна для производства ФС, однако для получения эпоксидных смол и особенно поликарбоната необходима дополнительная очистка продукта либо перекристаллизацией из толуола, либо кристаллизацией в виде аддукта БФА — фенол. [c.30]
Реакции получения и технология производства поликарбонатов [c.118]
Планом развития промышленности пластических масс в девятой пятилетке предусматривается дальнейшее увеличение производства поликарбонатов, организованного в СССР по периодическому методу. Настоятельная необходимость в этом вызвана большим интересом к этому классу полимеров со стороны целого ряда отраслей народного хозяйства как к материалу, обладающему уникальными свойствами. [c.5]
В книге сделана попытка систематизировать работы по химии, технологии и переработке поликарбонатов, опубликованные за последние 10 лет (до 1974 г.), и показать перспективы развития производства поликарбонатов. [c.6]
Значительные усовершенствования технологии получения поликарбоната методом фосгенирования позволили сделать этот промышленный способ производства поликарбонатов наиболее экономичным в настоящее время [15]. [c.8]
Динамика роста промышленного производства поликарбонатов в различных странах характеризуется следующими данными (табл. 1) [10—13]. [c.8]
В США начало промышленного производства поликарбоната относится к 1960 г. [c.9]Динамика роста производства поликарбоната на основе бисфенола А в США приведена в табл. 2 [16, 17, 18, т. 2, с. 251—253]. [c.9]
Из приведенных данных видно, что мировое производство поликарбоната имеет тенденцию к повышению. [c.11]За последние годы разработан и внедрен в промышленное производство (мощность 16 000 т/год) новый полностью непрерывный двухстадийный метод получения поликарбонатов [8]. Удельный расход сырья в этом методе меньше, чем в периодическом причем значительно сокращены затраты на оборудование. Схема процесса представлена на рис. 11. [c.71]
Производство и сбыт бисфеиола А, эпоксидных сиол и поликарбонатов в США [37] (в тыс. т) [c.347]
Год Производство бисфеиола А Сбыт эпоксидных смол Сбыт поликарбонатов [c.347]
Помимо самого дифенилолпропана важное трименение имеет и ряд его производных (галогенпроизводные, гидрированный ди-феннлолпропан, оксиалкилированные производные и другие).рОб-ширные возможности применения дифенилолпропана и его производных в различных отраслях промышленности вызвали огромный интерес исследователей и технологов к разработке экономичных способов его производства и методов очистки для получения продукта высокой чистоты. Последнее обстоятельство связано с тем, ч о в ряде производств, например в синтезе поликарбонатов, к дифенилолпропану как к сырью предъявляются весьма высокие требования. 1 [c.6]
Из поликарбонатов можно получать пленки и волокна, перерабатывать в изделия разными методами. Поликарбонаты в качестве конструкционного материала успешно конкурируют с металлом, древесиной, стеклом. Потребителями поликарбонатов являются электротехническая и электронная промышленность, производство изделий технического и бытового назначения, где поликарбонаты вытесняют металлы их используют в производстве пленочных и ли-стошх материалов, а также красок и noKpbiTHH.J [c.51]
Сообщалось , что фирма Union arbide (США) выпускает два сорта дифенилолпропана — бис-фенол А и бис-фенол НР (специальный сорт для производства поликарбонатов). Показатели для этих сортов такие [c.160]
Лримечания. 1. МЕМ-0,79 Дженерал электрик — сополимео поликарбоната с полидиметилсилоксаном МУ Шор 40 (70) — полые волокна производства ФРГ (г. Дортмунд), материал не указывается. [c.289]
Производство поликарбонатов Поликарбонаты (линейные термопла- [c.283]
Поликарбонаты способь ы сохранять заданные размеры. Благодаря этому, а также высоким прочностным показателям и теплостойкости поликарбонаты широко применяются для производства различных деталей аппаратов. Высокая удельная ударная вязкость дает возможность применять поликарбонаты в каче- [c.410]
Технологический процесс производства поликарбоната периодическим методом (рис. 50) состоит из следующих стадий фосгенирование дифенилол-пропаиа, промывка раствора полимера, высаждение полимера и выделение его из суспензии, сушка полимера и регенерация растворителей и осадителей. [c.76]
Ацетон СНз—СО—СНз —жидкость (т. кип. 56,1 °С), полностью смешиваемая с водой и многими органическими веществами. Он вв ьма огнеопасен и дает с воздухом взрывоопасные смеси в пределах концентраций 2,2—13,0% (об.). Ацетон широко применяют Е сачс стве растворителя и промежуточного продукта органического синтеза. Из него получают дифенилолпропан (для производства эпоксидных полимеров и поликарбонатов), диацетоновый спирт, из( бутилметилкетоп, метилметакрилат (через ацетонциангидрин), внпнлметилкетон и другие ценные вещества. [c.376]Фильтр испытан с положительными результатами в производстве поликарбоната на стадии фильтрования суспензий растворителя (ацетона и метилхлорида) и в производстве пластмасс при очистке растворов полисульфона от асканита. Разработан размерный ряд фильтров ДдАр с поверхностью фильтрования 5 10 и 20 [c.239]
Третьим по масштабам потребления фенола является быстро развивающееся производство дифенилолпропана (производство дифенилолпропана конденсацией фенола и ацетона описано в работе [28]). Дифенилолпропан служит 0СН0В1Ньш сырьем для изготовления эпоксидных смол, а также для получения широкого круга термостойких полимеров полиарилатов, поликарбонатов, полисульфонов, фориловых смол. Уже в 1972 г. в США для производства дифенилолпропана расходовалось около 100 тыс. т фенола [29] к 1990 г. потребность в феноле для указанных целей возрастет примерно до 750 тыс. т [10], что выдвигает дифенилол-пропан на второе место среди потребителей фенола. В настоящее время создаются установки единичной мощности до 90 тыс. т дифенилолпропана в год [30]. [c.58]
В одиннадцатой пятилетке и в перспективе будет расширено производство новых конструкционных пластмасс — поликарбонатов, полиацеталей (полиформальдегида), полибутилентерефта-лата и др., что обеспечит дальнейший прогресс в отраслях новой и новейшей техники значительно повысится уровень удовлетворения потребности в пластмассах развивающихся отраслей строительства и строительной индустрии, деревообрабатывающей промышленности будет организовано производство полимерных труб в крупных масштабах увеличится выпуск пластмасс ДЛЯ обеспечения производства товаров народного потребления. В целях повышения уровня обеспечения сельского хозяйства, мелиорации и водного хозяйства полимерами для строительства парников и теплиц, оросительных систем и трубопроводов, складов для хранения удобрений будет увеличено [c.22]
ПОЛИЭФИРЫ (простые и сложные). П. простые — высокомолекулярные соединения, макромолекулы которых содержат эфирные связи. Наибольшее значение среди простых П. имеют полиокси-метилен, пептон, эпоксидные смолы. Они используются в прои. шодстве конструкционных материалов, в качестве пленкообразующих веществ, эмульгаторов, диэлектриков и др. Сложные П.— высокомолекулярные соединения, получаемые поликонденсацией многоосновных кислот или их ангидридов с многоатомными спиртами. К П. с. относятся такие природные соединения, как нуклеиновые кислоты, даммар, шеллак, акароид, янтарь и др. К синтетическим П. с. относятся смолы алкидные, полиэтилентерефталат, полиакрилаты, поликарбонаты и др. Они широко используются в качестве пленкообразующих веществ, синтетических волокон, в электро- и радиотехнике, для изготовления высококачественных электроизоляционных материалов, как вяжущее в производстве стеклопластиков, [c.200]
Производство 3,3-ди(хлорметил)оксяциклобутана, поликарбоната, сополимеров этилена с пропиленом на базе нефтяных попутных газов полимеров высших полиолефинов на базе нефтяных попутных газов. [c.235]
В нашей стране директивами XXIV съезда КПСС по пятилетнему плану развития народного хозяйства на 1971—1975 гг. предусмотрено увеличение выпуска пластических масс и синтетических полимеров в 2 раза. Намечено улучшить качество пластических масс и изделий из них, освоить производство высокопрочных, термостойких, электроизоляционных, коррозионноустойчивых и других новых полимерных материалов и довести к концу пятилетки удельный вес производства термопластов (в том числе поликарбонатов) в общем объеме выпуска синтетических полимеров и пластмасс до 40—43%- [c.5]
В промышленности производство поликарбоната на основе бисфенола А в настояш,ее время осуш,ествляется двумя методами методом фосгенирования при комнатной температуре по реакции межфазной поликонденсации и методом переэтерификации в расплаве с применением в качестве исходного сырья диарилкарбонатов, из которых наиболее широко используется дифенилкар-бонат. [c.8]
В ФРГ промышленное производство поликарбоната началось с 1958 г., вскоре после получения Шнеллом (в 1956 г.) технически пригодного полимера. В настоящее время основное производство поликарбоната марки макролон сосредоточено на фирме Байер Фарбенфаб-рикен А. Г. . Свойства поликарбоната достаточно подробно описаны в монографии Шнелла [И]. [c.9]
Недавно появилось сообщение о производстве в США поликарбонатов на основе циклоалифатических диоло В, в частности 2,2,4,4-тетраметилциклобутандиола-1,3, изделия из которого легко поддаются поверхностной закалке и отжигу и отличаются высокой прочностью, что позволяет использовать их для производства оптических деталей [19]. [c.9]
chem21.info
Кальцинированная сода Карбонат производство — Справочник химика 21
Получают при производстве кальцинированной соды (карбоната натрия). Качество товарного продукта определяется следующими показателями [c.706]Другой пример. Кальцинированная сода (карбонат натрия) вырабатывается и потребляется в громадных количествах. Б 1974 г. в СССР было произведено 4,5 млн. т кальцинированной соды. Основным способом ее производства является аммиачный споив [c.118]
Карбонат натрия (кальцинированная сода) применяется в производстве стекла, мыла, при варке целлюлозы, для обработки бокситов в производстве алюминия, для нейтрализации кислых компонентов при очистке нефтепродуктов и т. д. Гидрокарбонат натрия используется как источник углекислого газа при выпечке хлеба, газировании, огнетушении. Гидрокарбонаты выполняют важную физиологическую функцию, регулируя кислотность крови. [c.136]
Исследовался также процесс электролиза с ионообменной диафрагмой с получением хлора и карбоната или бикарбоната натрия [13]. При размещении производства хлора на содовом заводе электролитические щелока могут быть направлены для карбонизации на производство кальцинированной соды или для регенерации Nh4 из фильтровой жидкости [14]. И в том и в другом случае взамен каустической соды получают более дешевую кальцинированную соду. Пока эти методы не нашли широкого применения в мировой промышленности. В нашей стране и в ближайшие 20—30 лет вряд ли будут созданы условия, благоприятствующие применению этих методов в промышленности. [c.282]
Новый способ подвода энергии в реакционную зону разложения карбоната кальция и разработанные для него термодинамические методы расчета электродинамического реактора, методы расчета настроечных параметров адаптивной системы по рассогласованиям параметров процессов получения бутадиена и извести могут быть использованы на производствах бутадиена для каучуков (например, на ЗАО Каучук г.Стерлитамака) и кальцинированной соды (например, на ОАО Сода г.Стерлитамака) для перехода от традиционной технологии к малоинерционным легкоуправляемым, с [c.4]
Едкий натр (каустическая сода), едкое кали, карбонат натрия (кальцинированная сода). Все эти продукты негорючи и невзрывоопасны, расходуются в больших количествах в производстве промежуточных продуктов и красителей. [c.19]
Наиболее широкое применение получили щелочные реагенты, а среди них — известь, получаемая обжигом при температуре 900—1200° С известняков, мела и доломитов. Помимо окиси кальция, в состав извести входят карбонат кальция, окись магния, примеси из глины и песка. В зависимости от содержания окиси магния известь делят на кальциевую (- 7% MgO) и магнезиальную (У 7% MgO). Чаще всего известь используют в гашеном виде. Образующаяся при гашении известь-пушонка содержит до 67% СаО и MgO. Реже применяют измельченный карбонат кальция [2,3], негашеную известь [4—6], кальцинированную соду и едкий натр [7, стр. 75], бикарбонат натрия [2] при очистке сточных вод — отходы цементного производства и шлаки, содержащие СаО [8]. Из-за малой растворимости гашеную известь дозируют чаще всего в виде известкового молока, содержащего до 15% СаО, но иногда используют и насыщенные растворы (0,12—0,13% СаО). [c.257]
В производстве кальцинированной соды хлористый аммоний получают также из отработанных растворов хлористого кальция. Выпариванием этих растворов концентрацию хлористого кальция повышают до 50%. Полученный раствор загружают в автоклав и насыщают аммиаком и углекислым газом. Выпавший в осадок карбонат кальция отфильтровывают, а хлористый аммоний выкристаллизовывают из раствора [30]. [c.406]
В производстве кальцинированной соды аммиачным методом после отделения кристаллического бикарбоната натрия получают маточный раствор, содержащий хлориды аммония и натрия, карбонат и бикарбонат аммония и другие соли. Обычно, этот раствор подвергают дистилляции для выделения аммиака, который снова возвращают в содовый процесс. [c.247]
Отбеливающие средства, содержащие активный хлор 69 Раствор гипохлорита натрия (методы производства) 69 Обменное разложение белильной извести и кальцинированной соды в водной среде (70).—Электролиз раствора хлористого натрия (70).—Хлорирование раствора карбоната натрия (70).—Хлорирование раствора каустической соды (71) [c.67]
В 1985 г. в нашей стране произведено 5028 тыс. т карбоната натрия (кальцинированной соды) и 3056 тыс. т гидроксида натрия (каустической соды) [21]. На производство только этих видов химической продукции с учетом упомянутых расходных коэффициентов потребовалось более 13 млн. т поваренной соли. Значительная часть этой соли добывается в виде рассола растворением отложений каменной соли через буровые скважины. [c.12]
В производстве кальцинированной соды аммиачным методом после отделения кристаллического бикарбоната натрия получают маточный раствор, содержащий хлориды аммония и натрия, карбонат и бикарбонат аммония и другие соли. Обычно этот раствор подвергают дистилляции для выделения аммиака, который снова возвращают в содовый процесс. Хлористый аммоний может быть выделен выпариванием маточного раствора и высаливанием поваренной солью. [c.177]
Карбонаты составляют одну из наиболее важных групп наполнителей. В эту группу входят карбонаты кальция, бария, магния, а также смеси или комплексы карбонатов кальция и магния. Наибольшее применение находит карбонат кальция в виде природных продуктов (мел, известняк, мрамор) и осажденного мела, получаемого специально или а качестве побочного продукта производства кальцинированной соды. Наполнители этой группы проявляют высокую химическую активность к карбоксилсодержащим пленкообразующим (алкидным и другим), что приводит к значительному повышению защитных свойств покрытий, таких, как водостойкость, коррозионная стойкость, твердость и т. д. Недостатком алки-дных и других карбоксилсодержащих лакокрасочных материалов, в состав которых входят карбонатные наполнители, является склонность их к повышению вязкости и загустеванию при хранении.. [c.430]
В лакокрасочной промышленности применяются природные карбонаты кальция — мел, известняк, специально получаемые осажденные карбонаты кальция, а также побочные продукты производств кальцинированной соды и магнезии. Некоторые сорта карбоната кальция применяются в качестве самых дешевых наполнителей. [c.396]
В эту группу входят карбонаты кальция, бария и магния, а также минералы, являющиеся смешанными солями. Наиболее технически важен карбонат кальция природный (мел, известняк, мрамор) и осажденный, изготавливаемый специально или побочный продукт производства кальцинированной содь . [c.233]
Кальцинированная сода, или карбонат натрия, находит большое применение, и ее производство относится к крупнотоннажному. В больших количествах кальцинированная сода применяется при получении едкого натра, в производстве стекла, цветных металлов (А1, Ы1,У), для очистки нефтепродуктов, в мыловарении, текстильной промышленности, в производстве искусственного шелка и проч. [c.233]
Основным сырьем в производстве кальцинированной соды являются хлорид натрия и карбонат кальция. В качестве вспомогательных материалов используют аммиак, воду, топливо и пар. Они необходимы для осуществления технологического процесса, но не влияют на состав конечного продукта. [c.26]
Синтез проводят следующим образом. На первой стадии щелочь реагирует с диоксидом углерода с образованием карбоната натрия (кальцинированная сода). Полученную смесь подвергают взаимодействию с хлоридом кальция (фильтрат производства гипохлорита натрия). Осажденный мел фильтруют и сушат. Фильтрат, содержащий в основном хлорид натрия, соответствует требованиям к рассолу, подаваемому на электролиз. Показатели качества полученного таким способом мела и нормы по ГОСТ 8253 — 79 приведены в таблице. [c.178]
В химической промышленности потребляется в среднем 10% товарной углекислоты. Она применяется, например, в производстве моче-ьины, кальцинированной соды, карбонатов и бикарбонатов натрия и калия, оксикарбоновых кислот, для создания инертной среды при проведении некоторых реакций и т. д. [c.463]
Природные растворимые соли встречаются в виде солевых залежей или естественных растворов (рассолы, рапы) озер, морей и подземных источников. Основные составляющие солевых залежей или рапы соляных озер хлорид натрия, сульфат натрия, хлориды и сульфаты калия, магния и кальция, соли брома, бора, карбонаты (природная сода). Советский Союз обладает мощными месторождениями ряда природных солей. В СССР имеется более половины разведанных мировых запасов калийных солей (60%) и огромные ресурсы природного и коксового газа для получения азотнокислых и аммиачных солей (азотных удобрений). В СССР есть большое количество соляных озер, рапа которых служит источником для получения солей натрия, магния, кальция, а также соединений брома, бора и др. Основными методами эксплуатацни твердых солевых отложений являются горные разработки в копях и подземное выщелачивание. Добычу соли в копях ведут открытым или подземным способом в зависимости от глубины залегания пласта. Таким путем добывают каменную соль, сульфат натрия (тенардит), природные соли калия и магния (сильвинит, карналлит) и т. д. Подземное выщелачивание является способом добычи солей (главным образом поваренной соли) в виде рассола. Этот метод удобен, когда поваренная соль должна применяться в растворенном виде — для производства кальцинированной соды, хлора и едкого натра и т. п. Подземное выщелачивание ведут, размывая пласт водой, накачиваемой в него через буровые скважины. Естественные рассолы образуются в результате растворения пластов соли подпочвенными водами. Добыча естественных рассолов производится откачиванием через буровые скважины при помощи глубинных насосов или сжатого воздуха (эрлифт). Естественные растворы поваренной соли, используемые как сырье для содовых и хлорных заводов, донасыщают каменной солью в резервуарах-сатураторах и подвергают очистке. Иногда естественные рассолы [c.140]
Карбонат натрия Naj Oj lOHjO — важнейший продукт основной химической промышленности. Используется практически во всех сферах химического производства. Безводная соль называется кальцинированной содой. [c.221]
После отделения кристаллов перхлората аммония маточные растворы обрабатывают Oj и образующийся бикарбонат выпадает в осадок. Преимуществом всех методов обмена с карбонатами аммония является получение в качестве отхода кальцинированной соды, однако масштабы производства перхлората аммония несоизмеримы с масштабами производства кальцинированной соды. Поэтому при сравнительно малом масштабе производства дополнительные затраты, связанные с использованием карбонатной схемы, не окупаются стоимостью получаемой кальцинированйой соды. [c.451]
При использовании в качестве сырья кальцинированной соды возникают большие трудности при промывке осадка. В качестве побочного продукта получают сульфид натрия в виде кристаллов (30% N393) или в виде плава (60% НагЗ). При этом методе производства на 1 г карбоната бария по расчету расходуется сырого сернистого барня (65% ВаЗ). — 1,3 т, кальцинированной соды — 535 кг [30]. [c.424]
Главным потребителем хлорида натрия является химическая промышленность. Хлорид натрия является сырьем для производства карбоната натрия (кальцинированной соды) аммиачным способом (1,55 т Na l на 1 т Na2 03), хлора и гидроксида натрия (каустической соды) методом электролиза (от 1,59 до [c.12]
В производстве кальцинированной соды используется только содово-известковый способ очистки рассола, реагентами в котором служат КагСОз и СаО. Способ сводится к тем же, как и при содово-каустической очистке рассола, реакциям ионного обмена и, соответственно, к образованию труднорастворимых осадков карбоната кальция и гидроксида магния. [c.170]
Осаждение примесей кальция и магния при низкой температуре (12—20 °С) накладывает свои особенности на процесс рассолоочистки в производстве кальцинированной соды. Более вероятным становится образование пересыщенных по СаСОз растворов. По данным [235] кривая титрования ионов кальция имеет резко выраженный максимум, что обусловлено или пересыщением раствора по СаСОз, или выделением в первый момент метастабильной модификации СаСОз. Возможно также образование основных карбонатов за счет введенных гидроксильных ионов (при добавлении основания или извести), что подтверждается уменьшением фактического избытка гидроксильных ионов в очищенном рассоле по сравнению с добавленным количеством для осаждения магния. При этом происходит увеличение щелочности уплотняющегося шлама, а также возрастание pH отстаивающейся суспензии, что объясняется переходом первично образовавшихся основных солей различного состава в среднюю соль, а также десорбцией той щелочи, которая была адсорбирована в момент осаждения. Данные явления наиболее характерны для суспензий, полученных при 10 °С. В этих условиях наблюдается также повышенная начальная вязкость суспензий, причем в большей степени суспензий, богатых гидроксидом магния. Со временем происходит дегидратация осадка и вязкость приближается к значению, характерному для очищенного рассола. При повышенных температурах не отмечено заметной разницы между начальной и конечной вязкостью суспензии и очищенного рассола. [c.171]
Получаемый в промышленности безводный карбонат натрия Nag Og называется кальцинированной содой. Гидрокарбонат натрия NaH Og под названием питьевой, или двууглекислой, соды применяется в медицине и в кондитерском производстве. [c.212]
Особенностью состава этой группы сточных вод является отсутствие органических и минеральных соединений серы, фосфора и галогенов. Вследствие этого образующийся при окпсле-нии натрийорганических соединений карбонат натрия (см. гл. 4) не взаимодействует с компонентами газовой среды, и расплав после огневых реакторов состоит в основном из карбоната натрия. При низких концентрациях других минеральных примесей в сточных водах и применении стойких в контакте с расплавом футеровок возможно получение продукта, содержащего 98% Na2 03 и более. Такой продукт можно использовать в ряде производственных процессов вместо кальцинированной соды (при нейтрализации кислых сточных вод в качестве щелочного раствора для нейтрализации газообразных кислот и их ангидридов в процессах огневого обезвреживания отходов, содержащих соединения серы, фосфора и галогенов для очистки тары и рабочих мест в пищевой промышленности в производстве некоторых видов стекла в процессах флотации руд цветных металлов в производстве едкого натра и т. д.). [c.260]
На один моль л-диамина необходимо брать два моля одинаковых или различных моноаминов. В молекуле п-диамина о-положение должно быть свободно, а в молекуле моноамина должны быть свободны п-положение для образования индамина и лг-положение — для того, чтобы можно было осуществить циклизацию в азин. Второй моноамин, вступающий в реакцию с индамином, должен быть первичным. В качестве окислителя применяют гидроокись железа, хромовую кислоту и двуокись марганца, являющуюся отходом сахаринового производства. Сафранин В вытеснен в крашении Сафранином Т, но нашел применение в фотографии в качестве десенсибилизатора, позволяющего проявлять панхроматические пластинки в рассеяном свете. Продажный Сафранин Т (Г. Вильямс, 1859) (ВАЗР С1 841), в основном состоит из высшего гомолога, получаемого из неочищенного о-толуидина, содержащего анилин. о-Толуи-дин сначала обрабатывают ограниченным количеством азотистой кислоты для частичного превращения первичных аминов в аминоазосоединения, которые затем непосредственно восстанавливают железом и кислотой до смеси анилина, о-толуидина, п-фенилендиамина н п-толуилендиамина. Эту смесь моно- и диаминов затем окисляют до индамина и проводят азиновую циклизацию. Сафранин Т экстра концентрированный является однородным и симметрично построенным соединением, получаемым восстановлением о-аминоазотолуола в смесь о-толуидина и п-толуилендиамина, окислением этой смеси бихроматом и соляной кислотой и последующей конденсацией с анилином при кипячении после нейтрализации массы карбонатом кальция. Для очистки красителя его обрабатывают бихроматом и серной кислотой при 95°, подщелачивают кальцинированной содой, добавляют сульфид натрия, фильтруют и высаливают краситель. Сафранин Т красит хлопчатобумажную ткань по танниновой протраве [c.877]
Карбонат кальция. Карбонат кальция применяется в виде мела, известняка и осажденного материала, изготовляемого специально или квляюптегося побочным продуктом производства кальцинированной соды или магнезии. Карбонат кальция известен также под названиями мел для побелки, парил скне белила. Некоторые сорта его применяют в качестве самых дешевых наполнителей. [c.235]
Технико-экономическая характеристика процесса получения содопродуктов может быть улучшена за счет повышения качества содопродуктов, совершенствования аппаратуры и систем )егулирования и автоматизации технологических процессов. Товышение качества содопродуктов должно идти по пути снижения содержания примесей в товарных продуктах (особенно кальцинированной соды) и улучшения их физических характеристик. Так как примесями в товарной соде является в основном карбонат и сульфат калия, снижение содержания этих примесей в товарной соде позволит увеличить выпуск товарных сульфата калия и поташа. Увеличение выпуска калийных солей, а также товарных продуктов с улучшенными физическими свойствами (тяжелая и гранулированная сода, гранулированный поташ для электровакуумной промышленности и т. д.), а также освоение выпуска специальных сортов поташа (для производства химических реактивов) значительно повысит эффективность процесса комплексной переработки нефелинов. [c.295]
chem21.info
Карбонат натрия Кальцинированная сода производство
Природные растворимые соли встречаются в виде солевых залежей или естественных растворов (рассолы, рапы) озер, морей и подземных источников. Основные составляющие солевых залежей или рапы соляных озер хлорид натрия, сульфат натрия, хлориды и сульфаты калия, магния и кальция, соли брома, бора, карбонаты (природная сода). Советский Союз обладает мощными месторождениями ряда природных солей. В СССР имеется более половины разведанных мировых запасов калийных солей (60%) и огромные ресурсы природного и коксового газа для получения азотнокислых и аммиачных солей (азотных удобрений). В СССР есть большое количество соляных озер, рапа которых служит источником для получения солей натрия, магния, кальция, а также соединений брома, бора и др. Основными методами эксплуатацни твердых солевых отложений являются горные разработки в копях и подземное выщелачивание. Добычу соли в копях ведут открытым или подземным способом в зависимости от глубины залегания пласта. Таким путем добывают каменную соль, сульфат натрия (тенардит), природные соли калия и магния (сильвинит, карналлит) и т. д. Подземное выщелачивание является способом добычи солей (главным образом поваренной соли) в виде рассола. Этот метод удобен, когда поваренная соль должна применяться в растворенном виде — для производства кальцинированной соды, хлора и едкого натра и т. п. Подземное выщелачивание ведут, размывая пласт водой, накачиваемой в него через буровые скважины. Естественные рассолы образуются в результате растворения пластов соли подпочвенными водами. Добыча естественных рассолов производится откачиванием через буровые скважины при помощи глубинных насосов или сжатого воздуха (эрлифт). Естественные растворы поваренной соли, используемые как сырье для содовых и хлорных заводов, донасыщают каменной солью в резервуарах-сатураторах и подвергают очистке. Иногда естественные рассолы [c.140]Природные растворимые соли встречаются в виде солевых залежей или естественных растворов (рассолы, рапы) озер, морей и подземных источников. Основные составляющие солевых залежей или рапы соляных озер хлорид натрия, сульфат натрия, хлориды и сульфаты калия, магния и кальция, соли брома, бора, карбонаты (природная сода). Советский Союз обладает мощными месторождениями природных солей. В СССР имеется более половины разведанных мировых запасов калийных солей (60%), более трети мирового запаса фосфорных солей и огромные ресурсы природного и коксового газа для получения азотнокислых и аммиачных солей (азотных удобрений). У нас есть большое количество соляных озер, рапа которых служит источником для получения солей натрия, магния, кальция, а также соединений брома, бора и др. Основными методами эксплуатации твердых солевых отложений являются горные разработки в копях и подземное выщелачивание. Выемку соли в копях ведут открытым или подземным способом в зависимости от глубины залегания пласта. Таким путем добывают каменную соль, сульфат натрия (тенардит), природные соли калия и магния (сильвинит, карналлит) и т. д. Подземное выщелачивание является способом добычи солей (главным образом поваренной соли) в виде рассола. Этот метод удобен, когда поваренная соль должна применяться в растворенном виде —для производства кальцинированной соды, хлора и едкого натра и т. п. Подземное выщелачивание ведут, размывая пласт водой, накачиваемой в него через буровые скважины. Естественные рассолы [c.70]
Наиболее широкое применение получили щелочные реагенты, а среди них — известь, получаемая обжигом при температуре 900—1200° С известняков, мела и доломитов. Помимо окиси кальция, в состав извести входят карбонат кальция, окись магния, примеси из глины и песка. В зависимости от содержания окиси магния известь делят на кальциевую (- 7% MgO) и магнезиальную (У 7% MgO). Чаще всего известь используют в гашеном виде. Образующаяся при гашении известь-пушонка содержит до 67% СаО и MgO. Реже применяют измельченный карбонат кальция [2,3], негашеную известь [4—6], кальцинированную соду и едкий натр [7, стр. 75], бикарбонат натрия [2] при очистке сточных вод — отходы цементного производства и шлаки, содержащие СаО [8]. Из-за малой растворимости гашеную известь дозируют чаще всего в виде известкового молока, содержащего до 15% СаО, но иногда используют и насыщенные растворы (0,12—0,13% СаО). [c.257]
В производстве кальцинированной соды аммиачным методом после отделения кристаллического бикарбоната натрия получают маточный раствор, содержащий хлориды аммония и натрия, карбонат и бикарбонат аммония и другие соли. Обычно этот раствор подвергают дистилляции для выделения аммиака, который снова возвращают в содовый процесс. Хлористый аммоний может быть выделен выпариванием маточного раствора и высаливанием поваренной солью. [c.177]
Синтез проводят следующим образом. На первой стадии щелочь реагирует с диоксидом углерода с образованием карбоната натрия (кальцинированная сода). Полученную смесь подвергают взаимодействию с хлоридом кальция (фильтрат производства гипохлорита натрия). Осажденный мел фильтруют и сушат. Фильтрат, содержащий в основном хлорид натрия, соответствует требованиям к рассолу, подаваемому на электролиз. Показатели качества полученного таким способом мела и нормы по ГОСТ 8253 — 79 приведены в таблице. [c.178]
Отфильтрованный бикарбонат натрия превращают при нагревании в безводный карбонат натрия ( кальцинированную соду ). Двуокись углерода вновь возвращают в производство это количество составляет половину количества, необходимого для процесса производства. Остальную половину получают из известняка путем прокаливания. Образующуюся при этом окись кальция используют с целью выделения аммиака из хлорида аммония (стр. 401), полученного на основной стадии этого способа. Аммиак также возвращают в производство с минимальными потерями. Следовательно, сырьем являются только поваренная соль и известняк, а единственным отходом — хлорид кальция. [c.486]
В 1985 г. в нашей стране произведено 5028 тыс. т карбоната натрия (кальцинированной соды) и 3056 тыс. т гидроксида натрия (каустической соды) [21]. На производство только этих видов химической продукции с учетом упомянутых расходных коэффициентов потребовалось более 13 млн. т поваренной соли. Значительная часть этой соли добывается в виде рассола растворением отложений каменной соли через буровые скважины. [c.12]
Исследовался также процесс электролиза с ионообменной диафрагмой с получением хлора и карбоната или бикарбоната натрия [13]. При размещении производства хлора на содовом заводе электролитические щелока могут быть направлены для карбонизации на производство кальцинированной соды или для регенерации Nh4 из фильтровой жидкости [14]. И в том и в другом случае взамен каустической соды получают более дешевую кальцинированную соду. Пока эти методы не нашли широкого применения в мировой промышленности. В нашей стране и в ближайшие 20—30 лет вряд ли будут созданы условия, благоприятствующие применению этих методов в промышленности. [c.282]
Исходным сырьем для производства кальцинированной соды являются карбонатное сырье (известняк или мел) и хлористый натрий. Карбонат кальция обжигают с целью получения двуокиси углерода и извести. Двуокись углерода расходуется на карбонизацию водноаммиачного раствора хлористого натрия, а известь — на разложение хлористого аммония с целью регенерации циркулирующего аммиака. [c.425]
Карбонат натрия (кальцинированная сода) применяется в производстве стекла, мыла, при варке целлюлозы, для обработки бокситов в производстве алюминия, для нейтрализации кислых компонентов при очистке нефтепродуктов и т. д. Гидрокарбонат натрия используется как источник углекислого газа при выпечке хлеба, газировании, огнетушении. Гидрокарбонаты выполняют важную физиологическую функцию, регулируя кислотность крови. [c.136]
Едкий натр (каустическая сода), едкое кали, карбонат натрия (кальцинированная сода). Все эти продукты негорючи и невзрывоопасны, расходуются в больших количествах в производстве промежуточных продуктов и красителей. [c.19]
Сода кальцинированная (карбонат натрия, или углекислый натрий). Применяется для мойки аппаратуры и подщелачивания среды. В микробиологическом производстве используется синтетическая сода (ГОСТ 5100—64), содержащая 96,8%, химически чистого вещества. [c.84]
Другой пример. Кальцинированная сода (карбонат натрия) вырабатывается и потребляется в громадных количествах. Б 1974 г. в СССР было произведено 4,5 млн. т кальцинированной соды. Основным способом ее производства является аммиачный споив [c.118]
В производстве кальцинированной соды аммиачным методом после отделения кристаллического бикарбоната натрия получают маточный раствор, содержащий хлориды аммония и натрия, карбонат и бикарбонат аммония и другие соли. Обычно, этот раствор подвергают дистилляции для выделения аммиака, который снова возвращают в содовый процесс. [c.247]
Получают при производстве кальцинированной соды (карбоната натрия). Качество товарного продукта определяется следующими показателями [c.706]
Кальцинированная сода, или карбонат натрия, находит большое применение, и ее производство относится к крупнотоннажному. В больших количествах кальцинированная сода применяется при получении едкого натра, в производстве стекла, цветных металлов (А1, Ы1,У), для очистки нефтепродуктов, в мыловарении, текстильной промышленности, в производстве искусственного шелка и проч. [c.233]
Одним из основных физико-химических превращений, происходящих при обжиге твердых материалов, является их термическая диссоциация, т. е. разложение молекул на более простые под действием высокой температуры. Диссоциация твердых материалов сопровождается, как правило, выделением газообразных веществ двуокиси углерода, паров воды и др. Один из видов диссоциации при обжиге — кальцинация, т. е. удаление конституционной воды или углекислоты. Примерами кальцинации могут служить облшг известняка и других карбонатов в производстве извести, соды и карбида кальция, обезвоживание бикарбоната натрия в производстве кальцинированной соды, производство безводного сульфата натрия из природного минерала мирабилита Ма2504-ЮН2О. [c.89]
Отбеливающие средства, содержащие активный хлор 69 Раствор гипохлорита натрия (методы производства) 69 Обменное разложение белильной извести и кальцинированной соды в водной среде (70).—Электролиз раствора хлористого натрия (70).—Хлорирование раствора карбоната натрия (70).—Хлорирование раствора каустической соды (71) [c.67]
Карбонат натрия — белый кристаллический порошок, пл. 2,53 г/см , т. пл. 853° С, насыпная плотность около 0,5 т/м . Водные растворы соды имеют сильно щелочную реакцию в результате гидролиза Naa Og. Кальцинированная сода применяется в промышленности неорганических веществ, для получения остальных содо-продуктов и ряда солей в металлургии, в стекольной промышленности, для очистки нефтепродуктов, в целлюлозно-бумажной, лакокрасочной, текстильной, кожевенной и многих других отраслях промышленности. Основные потребители более сильного основания — едкого натра — алюминиевая, нефтеперерабатывающая, цел-люлозно-бумажная, мыловаренная, лакокрасочная отрасли промышленности, производство искусственного шелка, промышленность органического синтеза. Кальцинированная сода представляет собой соль сильного основания и слабой кислоты. Получение этого многотоннажного продукта служит примером крупного солевого производства, основанного на хемосорбционных процессах в системе жидкость — газ. [c.88]
Основным сырьем в производстве кальцинированной соды являются хлорид натрия и карбонат кальция. В качестве вспомогательных материалов используют аммиак, воду, топливо и пар. Они необходимы для осуществления технологического процесса, но не влияют на состав конечного продукта. [c.26]
В производстве едкого натра содовый раствор, получаемый декарбонизацией сырого бикарбоната или растворением кальцинированной соды, обрабатывают известью или известковым молоком. При этом происходит следующая реакция, сопровождающаяся осаждением карбоната кальция [c.38]
Главным потребителем хлорида натрия является химическая промышленность. Хлорид натрия является сырьем для производства карбоната натрия (кальцинированной соды) аммиачным способом (1,55 т Na l на 1 т Na2 03), хлора и гидроксида натрия (каустической соды) методом электролиза (от 1,59 до [c.12]
Карбонат натрия Naj Og, или сода, присутствует в воде некоторых озер. Из водного раствора эта соль кристаллизуется в виде кристаллогидрата Na Oj ЮНаО, который называется кристаллической содой. При прокаливании происходит обезвоживание и образуется так называемая кальцинированная сода ЫзгСОз. Сода имеет важное промышленное значение. В больших количествах ее применяют в производстве стекла, мыла, бумаги, едкого натра, в домашнем обиходе и пр. [c.223]
Карбонат натрия Naj Oj lOHjO — важнейший продукт основной химической промышленности. Используется практически во всех сферах химического производства. Безводная соль называется кальцинированной содой. [c.221]
При использовании в качестве сырья кальцинированной соды возникают большие трудности при промывке осадка. В качестве побочного продукта получают сульфид натрия в виде кристаллов (30% N393) или в виде плава (60% НагЗ). При этом методе производства на 1 г карбоната бария по расчету расходуется сырого сернистого барня (65% ВаЗ). — 1,3 т, кальцинированной соды — 535 кг [30]. [c.424]
В химической промышленности потребляется в среднем 10% товарной углекислоты. Она применяется, например, в производстве моче-ьины, кальцинированной соды, карбонатов и бикарбонатов натрия и калия, оксикарбоновых кислот, для создания инертной среды при проведении некоторых реакций и т. д. [c.463]
Получаемый в промышленности безводный карбонат натрия Nag Og называется кальцинированной содой. Гидрокарбонат натрия NaH Og под названием питьевой, или двууглекислой, соды применяется в медицине и в кондитерском производстве. [c.212]
Особенностью состава этой группы сточных вод является отсутствие органических и минеральных соединений серы, фосфора и галогенов. Вследствие этого образующийся при окпсле-нии натрийорганических соединений карбонат натрия (см. гл. 4) не взаимодействует с компонентами газовой среды, и расплав после огневых реакторов состоит в основном из карбоната натрия. При низких концентрациях других минеральных примесей в сточных водах и применении стойких в контакте с расплавом футеровок возможно получение продукта, содержащего 98% Na2 03 и более. Такой продукт можно использовать в ряде производственных процессов вместо кальцинированной соды (при нейтрализации кислых сточных вод в качестве щелочного раствора для нейтрализации газообразных кислот и их ангидридов в процессах огневого обезвреживания отходов, содержащих соединения серы, фосфора и галогенов для очистки тары и рабочих мест в пищевой промышленности в производстве некоторых видов стекла в процессах флотации руд цветных металлов в производстве едкого натра и т. д.). [c.260]
На один моль л-диамина необходимо брать два моля одинаковых или различных моноаминов. В молекуле п-диамина о-положение должно быть свободно, а в молекуле моноамина должны быть свободны п-положение для образования индамина и лг-положение — для того, чтобы можно было осуществить циклизацию в азин. Второй моноамин, вступающий в реакцию с индамином, должен быть первичным. В качестве окислителя применяют гидроокись железа, хромовую кислоту и двуокись марганца, являющуюся отходом сахаринового производства. Сафранин В вытеснен в крашении Сафранином Т, но нашел применение в фотографии в качестве десенсибилизатора, позволяющего проявлять панхроматические пластинки в рассеяном свете. Продажный Сафранин Т (Г. Вильямс, 1859) (ВАЗР С1 841), в основном состоит из высшего гомолога, получаемого из неочищенного о-толуидина, содержащего анилин. о-Толуи-дин сначала обрабатывают ограниченным количеством азотистой кислоты для частичного превращения первичных аминов в аминоазосоединения, которые затем непосредственно восстанавливают железом и кислотой до смеси анилина, о-толуидина, п-фенилендиамина н п-толуилендиамина. Эту смесь моно- и диаминов затем окисляют до индамина и проводят азиновую циклизацию. Сафранин Т экстра концентрированный является однородным и симметрично построенным соединением, получаемым восстановлением о-аминоазотолуола в смесь о-толуидина и п-толуилендиамина, окислением этой смеси бихроматом и соляной кислотой и последующей конденсацией с анилином при кипячении после нейтрализации массы карбонатом кальция. Для очистки красителя его обрабатывают бихроматом и серной кислотой при 95°, подщелачивают кальцинированной содой, добавляют сульфид натрия, фильтруют и высаливают краситель. Сафранин Т красит хлопчатобумажную ткань по танниновой протраве [c.877]
Получение стекла ведут сплавлением двуокиси кремния (кварца, кремня) с карбонатом кальция (в виде известняка, мрамора, известкового шпата) с кальцинированной содой или с сульфатом натрия и углем. Для калиевых стекол вместо соды применяют поташ, для свинцовых стекол вместо карбоната кальция — окись свинца и т. д. Сплавление производят в ваннах или в больших огнеупорных тиглях, в стеклоплавильных горшках . Печи обычно обогревают генераторным газом с применением тонок (Сименса. В таких топках горячий отходяш ий газ используют для нагревания камер, выложенных огнеупорным к пичом через эти камеры затем пропускают газы перед их сжиганием, так что они попадают в печь, будучи уже нагретыми до высокой температуры. В последнее время в производстве стекла введено также электроплавление. На современных предприятиях тигли и ванны, в которых выплавляют оптическое стекло (т. е. стекло для оптических приборов), чаще всего покрывают изнутри платиной. [c.492]
chem21.info
Производство карбоната калия — Справочник химика 21
из «Производство соды»
Выделение двойной соли. Производство карбоната калия включает ряд технологических операций, предназначенных для выделения из раствора примесей, мешающих получению стандартного продукта, и получения собственно К2СО3. Основными примесями, препятствующими получению кондиционного поташа из маточника второй стадии выделения соды, являются карбонат натрия, сульфат и хлорид калия. В соответствии с растворимостью водно-солевой системы Ыа , К СО , С1 —Н2О карбонат натрия может быть выделен из раствора при упаривании в виде двойной соли МаКСОз. [c.272]Одновременно в процессе упаривания совместно с двойной солью выделяется в твердую фазу и сульфат калия. [c.273]
В соответствии с растворимостью системы сульфат калия должен выделяться полностью, однако из-за склонности его к образованию пересыщенных растворов равновесные концентрации не достигаются. Содержание сульфата калия в маточно.м растворе двойной соли равно 0,3—0,4% (мол.). Содержание карбоната натрия в маточнике двойной соли при температуре упаривания 130—140 °С в соответствии с растворимостью системы составляет около 4 % (мол.). [c.273]
Перед выделением двойной соли маточник второй стадии выделения соды смещивают с маточником стадии выделения поташа. Возврат поташного маточника на стадию выделения двойной соли позволяет выделить из него весь поташ с содержанием карбоната натрия, не превышающим допустимое по стандарту, и снизить содержание твердой фазы в суспензии двойной соли. Растворы стадии выделения двойной соли содержат до 60 % солей, поэтому температура их кипения при атмосферном давлении повышается до 30—140°С. Увеличение температурной депрессии растворов определяет теплотехнические схемы выпарных установок на стадии выделения двойной соли. При использовании греющего пара давлением 0,5—0,7 МПа применяют двухкорпусные противоточные или трехкорпусные смешанного тока выпарные установки. Продукционным корпусом батареи является корпус, работающий при атмосферном давлении. Теплотехническая схема двухкорпусной противоточной выпарной установки представлена на рис. 68. [c.273]
Суспензия двойной соли плохо осветляется и сгущается в гравитационных отстойниках, поэтому ее разделяют без предварительного сгущения на центрифугах типа ФГП. Фильтрат после центрифуг направляют на выделение хлорида калия или поташа. Осадок из центрифуг поступает на растворение в карбонатном растворе, который упаривается на стадии концентрирующей выпарки. Для удобства транспортирования осадка на ножи центрифуги подается упаренный раствор, смывающий осадок в сборник растворения. [c.274]
Производство хлорида калия. Хлорид калия выделяется из растворов при получении поташа с регламентированным содержанием хлоридов. При большом содержании хлоридов в карбонатных растворах производства глинозема хлорид калия необходимо выделять и для производства высококачественной соды. В последнем случае хлорид калия приходится выделять в две стадии —из раствора после второй стадии выделения соды и из растворов поташной части процесса. [c.274]
При переработке карбонатных растворов с большим и средним содержанием хлоридов калия в поташной части процесса выделяется из маточника двойной соли, при малом содержании хлоридов — из маточных растворов после выделения поташа. В соответствии со свойствами водно-солевой системы хлорид калия может быть выделен в твердую фазу путем охлаждения раствора. Так как содержание воды в растворах, насыщенных солями, при понижении температуры увеличивается, то для предотвращения кристаллизации с хлоридом калия других солей раствор перед кристаллизацией должен быть разбавлен дозированным количеством воды. [c.274]
Если процесс кристаллизации осуществляют в вакуум-кристаллизационных установках, количество воды увеличивается для компенсации ее самоиспарения (в соответствии с тепловым балансом установки). [c.274]
Условия кристаллизации хлорида калия аналогичны условиям кристаллизации сульфата калия. Поэтому для достижения полноты его выделения и получения осадка с удовлетворительным гранулометрическим составом необходимо применять кристаллизаторы с накоплением твердой фазы в кристаллорастн-теле. По сравнению с раствором после стадии выделения сульфата калия растворы хлорида калия обладают более высокой депрессией и более склонны к вспениванию при пониженном давлении. Поэтому для поддержания температуры кристаллизации 20—25 °С применяют вакуум-кристаллизаторы с комприми-рованием всего сокового пара продукционных корпусов. Вакуум-испарители установок должны иметь большие диаметр и высоту по сравнению с размерами установок кристаллизации сульфата калия. В результате охлаждения раствора до 20—25 °С в твердую фазу выделяются хлорид калия и небольшое количество сульфата калия. В маточном растворе остается 7—9 г/дм хлоридов в пересчете на хлорид-ион, что позволяет получить из него при последующей переработке поташ первого сорта. [c.275]
Суспензия хлорида калия из кристаллизатора направляется на осветление в гравитационные сгустители. Скорость осветления суспензии около 2 м/ч. Сгущенная суспензия, содержащая 30—50 % (масс.) твердой фазы, разделяется на центрифугах типа ФГН. Осадок хлорида калия влажностью 4—6 % сушат и направляют на склад готовой продукции. Кроме хлорида калия готовый продукт содержит до 5 % сульфата калия и 5—8 % поташа. [c.275]
Производство поташа. Технологическая схема и режимы получения поташа определяются содержанием хлоридов в маточнике двойной соли и требованиями к качеству продукта. Из маточника двойной соли с относительно малым содержанием хлоридов (до 10 г/дм ) поташ первого сорта выделяется при охлаждении раствора до 50—60°С в поверхностных кристаллизаторах при перемешивании суспензии. [c.275]
Полутораводный поташ сушат в прямоточных вращающихся сушилках при непосредственном контакте материала с топочным газом. Темперал ура топочных газов на входе в сушилку 700 °С, на выходе из сушилки — 200—220 °С. Очистку выходящих из сушилки газов от пыли осуществляют в сухом циклоне, санитарную очистку —в пенном газоочистителе. Схема сушки поташа аналогична схеме сушки соды. После сушилки поташ влажностью 0,2—1,0 % механическим транспортером подается на укупорку и далее на склад готовой продукции. [c.276]
Для получения поташа первого сорта из маточников двойной соли, содержащих до 4 % (мол.) хлоридов, предварительно выделяют хлорид калия, как было описано выше. Маточник хлорида калия упаривают при атмосферном давлении до получения раствора плотностью 1630—1635 кг/м . Упаренный раствор охлаждают в кристаллизаторах до 50—60 С с выделением в твердую фазу полутораводного поташа. Маточный раствор после отделения твердой фазы направляется на смешение с раствором перед выделением двойной соли. При увеличении степени упаривания хлоридного маточника до получения раствора плотностью 1650—1670 кг/м в процессе кристаллизации выделяется поташ, по содержанию примесей соответствующий продукту второго сорта. [c.276]
Как отмечалось выше, в некоторых отраслях промышле.ч-ности предъявляются повышенные требования к качеству карбоната калия. Так, для предприятий по производству электровакуумного стекла необходим кальцинированный поташ с содержанием сульфатов, не превышающим 0,1 % (масс.) в пересчете на ион 50Г, хлоридов не более 0,01 % (масс.) в пересчете на ион С1- и влаги не более 0,6 %. [c.276]
По гранулометрическому составу продукт не должен содержать фракции размером более 1 мм, количество фракции размером менее 0,2 мм не должно превышать 15 % (масс.). [c.276]
Упаренный раствор К2СО3 охлаждают до 50—60 °С в поверхностных кристаллизаторах. В результате кристаллизации в твердую фазу выделяется полутораводный поташ, химический состав которого соответствует составу поташа, используемого в производстве электровакуумного стекла. После сушки и выделения фракции размером 1—0,2 мм такой продукт отправляется потребителям. [c.277]
Вернуться к основной статье
chem21.info
Оборудование для производства сотового поликарбоната: станки, сырье и технология
Сотовый поликарбонат — листы, имеющие структуру ячеек. То есть это – лист, состоящий из слоев, разделенных между собой ребрами жесткости в виде сот. Поликарбонат активно применяется для проведения строительных работ и для нужд сельского хозяйства. Производство поликарбоната, при правильном подходе, может стать хорошим бизнесом.
Изготовление сотового поликарбоната: оборудование
Для производства этого материала используется линия экструзии. Существуют разновидности этой линии, которые оснащены также специальным оборудованием, которое используется для нанесения на листы поликарбоната специального слоя, защищающего материал от действия солнечных лучей. Использование экструзионной линии для производства сотового поликарбоната позволяет выпускать лист, имеющий такие габаритные размеры: 4-16\2100 мм. За одну минуту производится 5 метров такого листа.
Выбрав качественное оборудование для производства одноразовой посуды можно запустить прибыльное дело.
Открытие шиномонтажа — отличное решение. Здесь Вы узнаете какое оборудование для этого необходимо.
Состав производственной линии
Линия, которая используется для производства этого материала, состоит из таких основных узлов:
Загрузчик исходного сырья – данная часть производственной линии выполняет функцию загрузки рабочего сырья, из которого будет формироваться лист поликарбоната (гранулы и сыпучий материал). Загруженное сырье проходит предварительную сушку на протяжении 24 часов. Максимальная температура, которая используется для сушки, достигает 150 градусов. Все операции (загрузка, установка времени и температуры просушки сырья) устанавливаются в автоматическом режиме.
- Экструдер – преимущественно используется одношнековый вариант экструдера. Он состоит из прочного сплава стали, что гарантирует его прочность и длительный срок эксплуатации. Функция экструдера заключается в том, что расплавленный исходный материал при помощи шнека выдавливается через формовочные отверстия, что придает сплаву определенную форму.
- Головка – состоит из высококачественной стали. Оборудована отверстием определенного размера. Основное ее предназначение заключается в том, что через отверстие головки проходит расплавленная масса, и в результате она приобретает определенную толщину. В комплекте производственной линии идет три головы, которые позволяют придавать расплавленной массе такую толщину (4-8 мм\9-12 мм\13-16 мм).
- Вакуумный формировщик – основание формировщика состоит из матрицы. Расплавленная масса проходит под матрицей и под действием вакуума вытягивается, приобретая определенную форму. После окончания процесса формировки масса охлаждается.
- Транспортировочная линия – состоит из 8 транспортировочных роликов, диаметр которых составляет 70 мм. При помощи транспортировочной линии лист передвигается к следующему отделу производственной линии для дальнейшей обработки.
- Сушка – камера, в которой при помощи использования инфракрасных лучей происходит сушка формированного листа материала. В камере поддерживается стабильная температура в автоматическом режиме. Мощность данной камеры составляет 40 кВт
- Выгрузочная установка с установленной боковой порезкой – данный отдел линии оснащен мощным мотором, мощность которого составляет 2,2 кВт. На установке смонтировано оборудование, которое выполняет резку поликарбонатного листа. Процесс порезки осуществляется современным дисковым ножом.
В процессе изготовления часто применяются линии по производству сотового поликарбоната, которые оснащены некоторыми дополнительными функциями, например способны осуществлять покрытие листа защитной пленкой и др.
Технология производства поликарбоната
Технология производства сотового поликарбоната довольно сложная и трудоемкая и состоит из нескольких этапов:
- Очистка гранул поликарбоната. От цвета гранул зависит цвет поликарбонатных листов. В специальной центрифуге гранулы очищаются от посторонних элементов и пыли. Далее они подаются для дальнейшей переработки. При некачественной очистке гранул исходный материал не будет иметь чистого цвета, а, следовательно, и не будет отличаться высоким качеством.
- Плавление сырья. При помощи автоматического дозатора отбирается определенное количество гранул, которые потом поступают в специальную камеру, где они из твердого состояния переходят в жидкое. Под действием высокой температуры гранулы расплавляются. На этом же этапе происходит включение разнообразных добавок и присадок, которые придают исходному материалу определенные свойства. Например, металлическую крошку добавляют для придания поликарбонату прочности, красители придают материалу определенный цвет, присадки препятствую накоплению влаги на поверхности поликарбоната, добавки для отражения ультрафиолетовых лучей и др. Все эти добавки и присадки способствуют улучшению качества и характеристик поликарбоната.
- Придание листам формы. В результате использования процесса экструзии расплавленная масса получает сотовую структуру. Структура сотового поликарбоната состоит из двух листов, между которыми находятся ребра жесткости, имеющие сотовую структуру (от сюда и название поликарбоната – сотовый). После завершения данного этапа на конвейер выходят листы определенной толщины (от 4 до 16 мм).
- Узел нарезки. После полного остывания листов при помощи дискового ножа происходит их нарезка. Существует стандартный размер листа поликарбоната (6120\2100 или 1200\2100). При необходимости можно устанавливать другие параметры нарезки листов.
- Контроль качества. Поликарбонат должен соответствовать неким стандартам. Именно поэтому после завершения его нарезки при помощи специального оборудования происходит контроль качества материала (определяется равномерность листа, выявляется присутствие посторонних частиц, определяется равномерность цвета, проверяется надежность материала и пр).
Ознакомившись с советами по выбору оборудования для производства керамической плитки, можно открыть собственное производство и получать постоянный доход.
Открыть собственную автомойку проще, чем Вы думаете. Всё о подборе оборудования здесь.
Чтобы получить качественную металлочерепицу, нужно правильно наладить производство. Подробнее на http://buisiness-oborudovanie.com/dlya-metallokonstrukcij/oborudovanie-dlya-proizvodstva-metallocherepicy/.
После завершения окончательной проверки качества, листы сотового поликарбоната формируются в пачки и на поддонах поступают на склад.
Современное оборудование для производства сотового поликарбоната
На современном производстве используется несколько моделей оборудования, которое используется для производства сотового поликарбоната.
Например, модель Модель FUJ — 150/34 . С линии сходят листы поликарбоната, толщина которых составляет от 4 до 16 мм, а их габаритные размеры достигают таких параметров: 1100\2200 мм.
Довольно большой популярностью пользуются модели SJ90\36 или SJ120\36. Между этими моделями линий по производству сотового поликарбоната нет существенных различий.
Развитие современных методов и технологий способствует созданию все более современных линий, которые используются для производства такого популярного, надежного и недорогого материала, как поликарбонат.
Видео про изготовление сотового поликарбоната
buisiness-oborudovanie.com