Изготовление графитированных электродов
Основными составляющими угольных электродов и электродной массы для самоспекающихся электродов являются антрацит и каменноугольный кокс. Для изготовления графитированных электродов применяют малозольные нефтяной, сланцевые и пековый коксы.
Для повышения эксплуатационных свойств электродов в шихту вводят искусственный и реже естественный графит, а также бой графитированных электродов. Для связывания твердых составляющих шихты электродных изделий применяют средне- и высокотемпературный каменноугольные пеки, а для производства электродной массы — среднетемпературный каменноугольный пек или смесь его с каменноугольной смолой.
При производстве электродной продукции сырые материалы дробят и прокаливают (за исключением графита и обожженного боя) в ретортных или трубчатых вращающихся печах, в результате чего увеличивается их плотность, удаляется основное количество летучих, повышается электропроводность и механическая прочность. Прокаленные материалы измельчают на дробилках и в мельницах различных типов с последующим рассевом материалов на барабанных ситах или вибрационных грохотах.
Подготовленные материалы точно дозируют по видам сырья и его гранулометрическому составу и затем подают в смесительные машины, куда задают и связующее, причем жидкие пек и смолу предварительно нагревают для удаления влаги и частично летучих веществ. В результате тщательного перемешивания при температуре ~150° С получается однородная смесь, называемая электродной массой, которую используют для последующей переработки на электроды, или выдается в качестве готовой продукции, применяемой для самоспекающихся электродов.
Электроды получают на гидравлических прессах методом выдавливания массы через мундштук при давлении (50—200) · 105 Па (50—200 кгс/см2) в зависимости от сечения изделия.
Спрессованные электроды охлаждают водой на специальных рольгангах и затем обжигают в многокамерных газовых печах непрерывного действия. В результате обжига связующее превращается в кокс, что обеспечивает резкое повышение механической прочности, электропроводности и термической стойкости электродов. Обжиг ведут при температурах 1200—1300° С под сводом печи в защитной засыпке из мелкого коксика, предохраняющей электроды от сгорания и деформации. Продолжительность обжига зависит от размеров и плотности изделий и обычно составляет 320—400 ч.
Для получения графитированных электродов обожженную заготовку подвергают графитизации в электрических печах сопротивления при 2500—3000° С в течение 50—60 ч, причем сопротивлением в этих печах служат сами электроды и пересыпка — коксик фракции 10— 30 мм. Общая продолжительность графитизации, включая загрузку, графитизацию, остывание и разгрузку печи, составляет 7—10 сут. В результате графитизации повышается электропроводность, теплопроводность и химическая стойкость, уменьшается твердость электродов.
Обожженные угольные и графитированные электроды подвергают механической обработке: обточке цилиндрической поверхности, обработке торцов и нарезке ниппельных гнезд. Ниппельное соединение обеспечивается ниппелем с винтовой нарезкой, ввинчиваемым в ниппельные гнезда в торцах электродов. У угольных электродов иногда нарезают на одном конце электрода конический ниппель, а на другом конце —коническое гнездо. Для графитированных электродов применяют цилиндрические и конические ниппели (рис. 43). Ниппели вытачивают из специальных заготовок, обладающих высокой плотностью и механической прочностью, что обеспечивается дополнительной пропиткой обожженных заготовок пеком под давлением 5-106 Па (5 ат) при температуре 280—300° С.
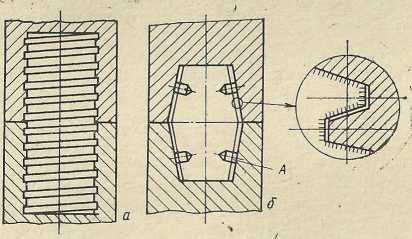
Для повышения эксплуатационных качеств графитированных электродов в ряде случаев на их поверхность наносят различные защитные покрытия, или их пропитывают различными солями, или вводят в массу при их изготовлении различные добавки, снижающие окисление электрода во время его службы. Это позволяет снизить расход электродов на 20—30%.
metallurgy.zp.ua
Производство графитированных электродов
Во всем мире графитированные электроды применяют в отраслях промышленности, где для технологических целей необходимо постоянно нагревать вещества или среду. Способность изделий проводить электрический ток при экстремально высоких температурах позволяет использовать их везде, где выпуск продукции связан со сложными и опасными производственными процессами.
Графитированные электроды выпускают из углеродосодержащего сырья: каменного угля, графита, антрацита, отходов плавления стали. Пройдя специальную обработку, они выдерживают температуры до +3000-3500оС. В сочетании с электропроводностью и термостойкостью это делает их незаменимыми в металлургической, химической промышленности, судостроении, других отраслях хозяйства.
Виды и маркировка графитированных электродов
Графитовый неплавкий электрод – изделие цилиндрической формы длиной 1000-2700 мм, диаметром 75-708 мм. По краям есть готовые ниппельные гнезда с конической, трапециальной или цилиндрической резьбой для ввинчивания ниппеля. Это помогает нарастить длину изделия по мере его расхода при плавлении стали.
Маркировка графитированных электродов:
Э – электрод; Г – графитированный; П – пропитанный, в основном пеком; С – специальный, для применения в разных сферах производства.
Популярные марки графитовых изделий:
- 1) ЭГ, предназначены для работы с электрическим током плотностью 25 А/см2, производятся из нефтесодержащего кокса, пека каменного угля. Используются в рудовосстановительных печах, электротермических аппаратах. В изделиях маркировки ЭГ-1 и ЭГ-2 разное только удельное сопротивлением.
- 2) ЭГС, выпускаются из игольчатого кокса, пека каменного угля. Используются в руднотермических и сталеплавильных печах, рафинировочных агрегатах.
- 3) ЭГП, графитированные с пропиткой. Основу составляет каменноугольный труднорастворимый пек, нефтяной кокс, пропитка – из пека. Используются в ферросплавных печах, для литья металла, аппаратах электродуговой сварки.
- 4) ЭГСП, изготовленные из игольчатого кокса, с пропиткой из пека. Применяются в руднотермических, электротермических агрегатах, электродуговых сварочных аппаратах.
Характеристики продукции
Графитированные электродов производят на основе угольных. У них есть схожие характеристики: низкое сопротивление, предельная чистота, повышенная стойкость к агрессивным химическим средам, но есть и отличия.
Особенности графитированных изделий:
обладают высокой упругостью, теплопроводностью, стоят дороже угольных, но качество на порядок выше; не трескаются при высоких температурах, обладают высокой электропроводность, причем при нагреве прочность материала повышается; используются в паре с любым присадочным металлическим материалом, легче угольных поддаются обработке, резке, сварка с ними быстрая, качественная; более устойчивы к окислению, воздействию химреагентов, включая хлорсодержащие вещества; используют при больших сопротивлениях тока, допустимый ток в 2-3 раза плотнее, чем у угольных; за счет сниженного удельного сопротивления снижаются расходы электродов при плавлении стали.
Заказать и купить
ООО «НПП АВЕРС» предлагает заказать и купить графитированные электроды от производителя. Сотрудничаем с физическими, юридическими лицами, отгрузка продукция возможна любыми партиями. Отправка осуществляется по России, в страны СНГ: Армению, Азербайджан, Беларусь, Молдавию, Киргизию, Казахстан, Туркменистан, Таджикистан, Узбекистан.
Если остались вопросы, звоните на номер: +7 (350) 220-94-94 или обратитесь по адресу: г. Челябинск, Троицкий тракт 486, офис 203.
amasgroup.ru
Изготовление графитированных электродов
Каменноугольный кокс и антрацит – это основные компоненты электродной массы и угольных электродов для самоспекающихся электродов. Чтобы изго¬товить графитированные электроды используются малозольные нефтяной, пековый и сланцевые коксы. Введение в шихту искусственного и иногда естественного графита вместе с боем графитированных электродов позволяет повысить эксплуатационные свойства электродов. Использование средне и высокотемпературного каменноугольного пека позволяет связывать твердые компоненты шихты изделий из электродов, а при производстве электродной массы применяют чистый каменноугольный пек средней температуры или смесь пека с каменноугольной смолой.Для производства электродных изделий сырые материалы дробят и прокаливают (кроме графита и обожженного боя) в трубчатых или ретортных печах с вращающимся барабаном. Это способствует увеличению их плотности, удалению основной массы летучих веществ, повышению механической прочности и электропроводности. После прокаливания материалы измельчают в мельницах различных видов и на дробилках, а затем рассевают их на вибрационных гро¬хотах или барабанных ситах.
После подготовки рассчитывают точную дозировку материалов, которая зависит от типа сырья и его гранулометрических составляющих. Затем материал вместе со связующим загружается в смесительные машины, при этом жидкие смола и пек заранее нагреваются для удаления частично летучих веществ и влаги. Тщательное смешивание при ~150 °С приводит к образованию однородной смеси – электродной массы. Эта масса используется для переработки на электроды либо выпускается в чистом виде для изготовления самоспекающихся электродов.
Для получения электродов на гидравлических прессах массу выдавливают через мундштук при давлении (50—200) • 105 Па (50—200 кгс/см2), которое зависит от сечения изделия.
Электроды в спрессованном состоянии охлаждаются при помощи воды на специальных рольгангах и обжигаются в секционных газовых печах непрерывного действия. В печах связующее становится коксом, благодаря чему резко увеличивается механическая прочность электродов, их термическая стойкость и электропроводность. Обжиг осуществляется при 1200—1300 °С в печи в специальной засыпке из мелкого коксика, которая препятствует сгоранию или деформации электродов. Длительность обжига колеблется в зависимости от величины и плотности изделий от 320 до 400 ч.
Графитированные электроды можно получить путем обжига заготовки в электрических печах сопротивления при 2500—3000 °С за 50—60 ч, при этом сами электроды и пересыпка — коксик фракции 10— 30 мм являются здесь сопротивлением. Процесс графитизации, с учетом этапов загрузки материала, его графитизации, остывания и разгрузки печи, занимает 7—10 сут. Это позволяет повысить электропроводность, химическая стойкость, теплопроводность, а также уменьшить твердость электродов.
После этого начинается механическая обработка электродов: обтачивается цилиндрическая поверхность, обрабатываются торцы и нарезаются ниппельные гнезда. Для ниппельного соединения используются ниппеля с винтовой нарезкой, ввинчиваемые в ниппельные гнезда в торцах электродов. Для угольных электродов иногда используется конический ниппель на одном конце, и коническое гнездо – на другом. Цилиндрические и конические ниппели используется у графитированных электродов (рис. 1). Ниппели изготавливаются из специальных заготовок с механической прочностью и высокой плотностью, получаемых благодаря пропитыванию обожженных заготовок пеком при давлении 5-106 Па (5 ат) и температуре 280—300 °С.
Рис. 1 – Соединение электродов при помощи цилиндрического (а) и конического (б) ниппелей (А – пековая пробка)
Для того чтобы улучшить качество эксплуатации графитированных электродов, могут быть использованы различные защитные покрытия, пропитывать различными солями или добавлять в массу различные вещества, уменьшающие окисление электрода. Благодаря этому расход электродов снижается на 20—30 %.
metallplace.ru
Производство графитированных электродов — Справочник химика 21
из «Облагораживание и применение нефтяного кокса»
В электродном производстве коксы прокаливают в газовых ретортных печах при 1300—1400 °С в течение 24 ч. За столь длительное время кокс прогревается гораздо более равномерно по всей массе и получается более однородной структуры, чем при прокалке во вращающихся печах. В этом случае обессеривание коксов протекает глубже (удаляется до 35% от исходного содержания серы). Выделение сернистых соединений при прокалке сернистого кокса в ретортных нечах сопровождается, по данным электродных заводов [29], сильным разрушением огнеупорной кладки — динаса (в 4 раза большим, чем при прокалке малосернистого кокса). В случае содержания в коксе более 7—8 мае. % летучих куски кокса спекаются, что приводит к нарушению режима прокалки и выгрузки. [c.154]В дальнейшем заготовки графитируют в электрических печах сопротивления при температурах 2300—3000 °С в течение 2—3 суток. Полный цикл с охлаждением длится 7—8 суток. Удельный расход электроэнергии при графитировании электродов составляет 5000—6000 кет ч/т. для больших печей и около 7500 кет ч1т для малых. [c.155]
После графитирования электроды обрабатывают делают гнезда, нарезают ниппели и т. д. Весь процесс от прокалки кокса до обработки готовых изделий длится примерно один месяц. Диаметры графитированных электродов для электропечей достигают 600— 750 мм, длина—1800 мм и более. [c.155]
Испытание графитированных электродов, полученных на основе сернистого кокса, в промышленных электропечах металлургических заводов позволяет сделать вывод о возможности и целесообразности внедрения сернистого кокса для производства электродов. [c.155]
По данным М. А. Фриша [29], в настоящее время без существенного изменения технологии электродного производства возможна добавка кускового сернистого кокса в количестве до 15% на сухую шихту при производстве графитированных электродов. [c.155]
Вернуться к основной статье
chem21.info
Электроды графитированные от производителя
Сделать запрос на электроды вы можете написав нам на почту
Графитированные электроды применяются для плавки металлов в электродуговых рудотермических, сталеплавильных печах.
Актуальные цены на октябрь 2017г. : Уточняйте позвонив нам по телефону или отправив запрос на почту. Сроки изготовления и поставки :2-3 недели, у нас свое производство, электроды до 200-го диаметра мы производим сами, без посредников.
Материал изготовления:Подбор марки графита производится индивидуально под требования заказчика, доступные варианты:ЭГ(ЭГ-15, ЭГ-20, ЭГ-25) ЭГП, ЭГС, ЭГСП, а также их аналоги производства китай: RP(эг). HP(эгп), SHP(эгс), UHP(эгсп),
Размеры изделия:Доступные размеры графитированных электродов в диаметре от 75 до 200мм.
Условия доставки:Организовать отправку графитированных электродов мы можем как по России так и по странам СНГ а именно: Азербайджан, Армения, Белорусия, Казахстан, Киргизия, Молдавия, Таджикистан, Туркменистан, Узбекистан
Важно:
Для получения максимально низкой цены в коммерческом, указывайте предполагаемый годовой обьем закупа в заявке.
При отправке запроса на изготовление желательно также сразу указать марку материала, размеры требуемых электродов, если нужен счет или комерческое — то прикрепляйте карточку предприятия к письму.
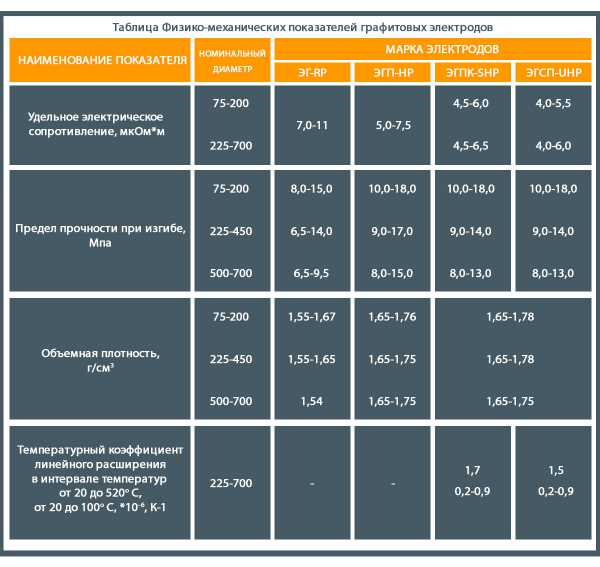
Электроды графитированные
Наша компания «НПП Аверс» осуществляет серийное производство и поставки обширной номенклатуры изделий из графита. Мы предлагаем электроды графитированные по умеренным ценам в количествах, необходимых заказчику. Изготавливаемая нашим предприятием продукция соответствует требованиям национального стандарта ГОСТ Р МЭК 60239-2014 и международного IEC 60239:2005.
Электроды графитированные ЭГ имеют цилиндрическую форму заданного диаметра и длины, и изготавливается методом обточки из стержней. Материалом для производства данных изделий является углерод, получаемый из кокса по классической технологии путем термического передела, обжига при определенной температуре и графитизации. В торцах изделий делаются гнезда с цилиндрической или метрической резьбой для объединения нескольких деталей при помощи ниппелей в сборку – колонну.
Назначение и области применения графитированных электродов
Данные элементы широко используются в металлургии для обеспечения процесса выплавки различных сортов чугуна и стали, в том числе и высоколегированных. Производимые нашей компанией электроды графитированные для электродуговых печей используются для создания дуги в сталеплавильной печи. При этом в рабочей зоне температура может достигать 1800C, что обеспечивает переход шихты из твердого состояния в жидкое. Полученный в результате данного процесса полупродукт проходит дополнительную обработку для получения расплава с требуемым химическим составом.
Графитированные электроды используются в дуговых сталеплавильных, ферросплавных, руднотермических и рафинировочных печах переменного и постоянного тока. Изделия вводятся в рабочую зону через отверстия в верхней части технологического оборудования. На них подается ток от мощного трансформатора, напряжение колеблется в пределах от 50 до 300 В, а в некоторых печах может достигать 1200 В. Токопроводящие элементы по мере использования выдвигаются вниз при помощи специальных механизмов.
В ходе выплавки металла происходит расход материала электрода со стороны электрической дуги. Для сохранения непрерывности процесса предусмотрена возможность наращивания электрода с другой стороны посредством соединения нескольких элементов в колонну с использованием конусообразных ниппелей. Существуют также моноэлектроды с одного конца, которого нарезана резьба, а с другого имеется соответствующее гнездо.
Номенклатура изделий
Наша компания осуществляет выпуск наиболее полного ассортимента изделий для металлургической промышленности. В частности мы производим следующие виды токоведущих элементов для дуговых сталеплавильных и других видов электрических печей:
Электроды графитированные ЭГ 25 с удельным сопротивлением от 7,0 до 8,0 мкОм*м в зависимости от диаметра.
Предел прочности детали на изгиб составляет от 6,4 до 7,8 МПа.
Электроды графитированные ЭГ150 с объемной плотностью в 1,61 г/см3 и содержанием зольных примесей не более 0,2-0,3%.
Модуль упругости изделия зависит от внешнего диаметра и колеблется в пределах от 7 до 9 ГПа.
Электроды графитированные ЭГ 200 с предельным значением плотности тока в процессе плавления до 200 А.
Описываемые изделия различаются по наружным размерам. Существует 18 разновидностей электродов графитированных с номинальным диаметром от 75 до 750 мм. Действующий ГОСТ допускает отклонение фактических параметров в пределах от 2 до 15 мм в соответствии со спецификацией.
Наша компания осуществляет выпуск нормальных и коротких электродов семи типоразмеров. Длина изделий составляет от 1000 до 2700 мм с предельным отклонением от 50 до 75 мм. Процентное соотношение коротких и нормальных изделий в каждой партии оговаривается с потребителем особо.
Преимущества и особенности электродов графитированных
Широкое применение данных изделий в металлургии обусловлено, прежде всего, невысокой стоимостью. Качественные электроды графитированные, цена которых в нашей компании значительно ниже среднерыночной, имеют ряд преимуществ перед аналогами:
Материал не окисляется при больших температурах.
Малое электрическое сопротивление значительно снижает потери тока во время плавки.
Простота изготовления.
Незначительный расход изделия в процессе работы.
Отсутствие склонности к растрескиванию, деформации и разрушению.
ООО «НПП Аверс» предлагает всем заинтересованным лицам и организациям электроды графитированные купить по умеренной цене. Наша компания готова выполнить разовые заявки от клиентов и наладить регулярные поставки продукции по согласованному графику. Оформить заявку можно непосредственно на сайте компании в соответствующем разделе или позвонив по контактному телефону. Наши специалисты проконсультируют вас по всем интересующим вопросам.
amasgroup.ru
Графитированные электроды
Графитированные (графитовые) электроды и их применение
Графитированные (графитовые) электроды преимущественно находят применение при выплавке стали в дуговых электросталеплавильных печах и в процессах рафинирования стали при внепечной обработки в агрегатах печь-ковш. Графитированные электроды также используются и в других процессах плавки, например, плавки на штейн в руднотермических печах.
Дуговая электрическая печь при производстве стали обеспечивает большую эксплуатационную гибкость по сравнению с кислородным конвертером, так как может быть остановлена и перезапущена вновь относительно быстро, что дает возможность оперативно отвечать на запросы потребителей и динамику рынка. Именно поэтому дуговые печи широко применяются и небольшими сталелитейными заводами, и в литейном производстве. Соответственно, спрос на такой расходный материал, как графитированные электроды, неуклонно повышается.
Электрические дуговые печи работают с использованием либо переменного электрического тока или постоянного электрического тока. Подавляющее большинство электродуговых печей используют переменный ток. Каждая из этих печей, как правило, использует девять электродов (в трех колоннах по три электрода в каждой) за один раз. Остальные электродуговые печи, которые используют постоянный ток, как правило, используют одну колонну из трех электродов. В процессе плавки электроды постепенно потребляются, что требует добавление нового электрода. Графитированные электроды соединяются между собой посредством ниппельного соединения, для чего с обоих концов каждого электрода делается резьбовое ниппельное гнездо. Размер электродов варьируется в зависимости от размера печи, параметров трансформатора тока и планируемой производительности печи. Электроды могут быть как небольшие – 75 миллиметров в диаметре, так и довольно крупные – до 750 мм в диаметре и до 2800мм в длину. Соответственно, один графитированный электрод может весить в зависимости от размера от пяти килограмм и до двух тонн.
Особенности в сфере производства и реализации графитированных электродов
Электроды в настоящее время являются единственными доступными продуктами, которые обладают высоким уровнем электропроводности и способностью поддержания высокого уровня тепла в электрической дуговой печи в процессе производства стали. В настоящее время происходит активное развитие технологий производства графитированных электродов и постоянное повышение их качества для удовлетворения современных требований, поскольку любые изменения в металлургических, электрических и механических условиях эксплуатации могут оказать существенное влияние на поведение электродов. Новые технологии плавки в современных печах большого объема и повышенной мощности приводят к более быстрому прогреву электродов, чем в малых печах и требуют значительного повышения устойчивости электродов к термическим и механическим воздействиям. Повышение эффективности работы электродуговых печей приводит к снижению величины потребления графитированных электродов на тонну произведенной стали в электродуговых печах (удельного расхода).
Поставляемые ООО «Новые индустриальные технологии» графитированные электроды соответствуют условиям эксплуатации современных дуговых печей и обладают высокой механической прочностью, отличной теплопроводностью, низким электрическим сопротивлением, что имеет решающее значение для экономичного расхода.
Марки графитированных электродов
Графитированные электроды марки ЭГ (RP – regular power), а также ниппели производятся на основе каменноугольного пека и нефтяного кокса. Подходят для осуществления работы на плотностях тока до 25 А/см2 в дуговых сталеплавильных, рафинировочных ферросплавных, руднотермических печах и прочих электротермических устройствах.
Показатель | Диаметр, мм | RP |
Удельное электросопротивление, | ≤ 300 | 8,5 |
Предел прочности при изгибе, | ≤ 300 | 8,5 |
Плотность, | ≤ 300 | 1,53 |
Модуль Юнга, ГПа, не более | ≤ 300 | 9,3 |
Графитированные электроды марки ЭГП (HP — high power),а также ниппели производятся на основе каменноугольного пека и нефтяного кокса и имеют дополнительную пропитку пеком. Подходят для осуществления работы в дуговых сталеплавильных печах высокой мощности и установках печь-ковш.
Показатель | Диаметр, мм | HP |
Удельное электросопротивление, | ≤ 400 | 6,5 |
Предел прочности при изгибе, | ≤ 400 | 10,5 |
Плотность, | ≤ 400 | 1,62 |
Модуль Юнга, ГПа, не более | ≤ 400 | 12,0 |
Электроды графитированные марки ЭГСП (UHP – ultra high power), а также ниппели производятся на основе игольчатого кокса и каменноугольного пека и имеют дополнительную пропитку пеком.
Показатель | Диаметр, мм | UHP |
Удельное электросопротивление, | ≤ 400 | 5,5 |
Предел прочности при изгибе, | ≤ 400 | 11,0 |
Плотность, | ≤ 400 | 1,66 |
Модуль Юнга, ГПа, не более | ≤ 400 | 14,0 |
ООО «Новые индустриальные технологии» (Екатеринбург) является официальным поставщиком и дилером известных отечественных и зарубежных производителей графитированных электродов, что гарантирует высокое качество поставляемой продукции.
newindtech.ru
Способ изготовления графитированных электродов
ССР
ОПИСАНИЕ ИЗОБРЕТЕНИЯ
К АВТОРСКОМУ СВИДЕТЕЛЬСТВУ
Подтгисная группа 1 120
А. В, Кукса и B. B. TIOIICBCB
СПОСОБ ИЗГОТОВЛЕИИЯ ГРАФИТИ РОВА ИИЫХ ЭЛЕКТРОДОВ
Заявлено 27 июля 196I l,à Хо 7 1013., 2-1 в Комитет по делам изобретений и откр .тии при Сонете Чиниетров СССР
Опубликовано в «Ьюллетеие и.,oo:Iете..ий» Хо 7 за 1о62 г.
Обычно:IpHKIBHHcxlbIE покрыт»я алек.1 рogoB $311 31cкт1зопе 1еЙ подвергаются окислению, что приво ит и повышенному расходу электродов и большим простоям печей.
По сушествующим способам для защиты от окисления поверхности электродов их покрывают слоем керамической массы, которая при наГреве 06р23 l ет Зап111т!1у 10 Оооло 1к i 113 гл111103еъ1а Il крем нсЗема (3BT. cB.
М 90171). При этом покрытие электродов керамической массы осуществляется предприятием, производящим плавку.
В отличие от известны.; cIIocoOQB B описываемом, с целью повышения работоспособности электродов, предлагается в качестве защитного слоя применять шамотографитовую смесь, предохраняюшую от сгорания.
Для этого при изготовлении электродов íà Нх поверхность впрессовывается слой из графитошамота: механической смеси графита и шамота, затворенной на каменноугольной смоле.
Процесс обжига и графитизация электродов осуществляются по обычной технологии производстза графитированных электродов.
На фиг. 1 схематично изображено строение электрода в зажиме головки элект ододержателя; на фиг. 2 — то же, в раоочем пространстве печи.
Отформованный сырой элсктро1 состоит нз сердцевины 1 и графитошамота 2. С продвижением электрода B рабочее пространство печи углерод графитошамота 2 сгорает и Ila,товерхности электрода образуется инертная оболочка из шамота 8. которая предохраняет сердцевину 1 от интенсивного окисления Таким образом, в рабочем пространстве печи графитированный электрод и:.еоб;.:етает третий защитный слой — шамот 8. № 145948
Предмет изобретения
Способ изготовления графитированных электродов с покрытием их поверхности защитным слоем против окисления, о т л и ч а ю щ и йс я тем, что, с целью повышения работоспособности электрода, в качестве защитного слоя применяют шамотографитовую смесь, которую наносят на поверхность электрода путем .прессования в процессе изготовления электрода.
Фиг 1
Риг Г
Составитель описания А. H. Бидевкин
Редактор Р. Б. Кауфман текрсд T. и. Курилко Корректор В. Андрианов
Поди. к печ. 17Х-62 r формат бум. 70; 108 /, Объем 0,18 изд. л.
Зак. 4988 Тираж 750 Цена 4 коп.
ЦБТИ Комитета по делам изобретений и открытий при Совете Министров СССР
Москва, Центр, М, Черкасский пер., д. 2/б.
Типография ЦБТИ, Москва, Петровка, 14.
www.findpatent.ru