производство сухих смесей — как производят сухие смеси
Сухая смесь – это специализированная по назначению и однородная по составу смесь вяжущего вещества, наполнителей и добавок, полностью готовая к замешиванию раствора. Как правило, готовая сухая смесь, как узкоспециализированное решение, всегда удобнее в работе и обладает в совокупности лучшими характеристиками, чем универсальный цементно-песчаный раствор.
В качестве простейшего примера возьмем кладочные работы. Профессиональные каменщики знают, что раствор, изготовленный на РБУ (растворно-бетонном узле, на больших стройках никто не мешает раствор вручную) на порядок удобнее того, что можно приготовить в домашних условиях. Известный “дедовский” способ повысить пластичность раствора – добавить в него немного моющего средства. Еще лучше использовать суперпластификатор С3, который сейчас продается на любом крупном строительном рынке. Но современные пластификаторы работают еще лучше, вот почему заводской кладочный раствор с точки зрения удобства работы не идет ни в какое сравнение с самодельным. А удобство означает скорость и более высокое качество работы. Заводская универсальная сухая смесь также содержит в своем составе все необходимые добавки и поэтому отлично подходит для кладочных и штукатурных работ.
Не будем забывать и о наполнителях, чаще всего в смесях на основе цемента это песок. Так как доля наполнителя в сухих смесях составляет не менее 70%, очевидно, его качество также напрямую влияет на характеристики смеси. Для цементно-песчаного раствора оптимальным является чистый песок средней крупности без посторонних включений. Пылеватый мелкий карьерный песок (а в некоторых регионах частнику порой трудно приобрести другой песок) снижает прочность раствора, что вынуждает увеличивать соотношение цемента. В производстве сухих смесей используется только чистый (мытый, просеянный) песок определенной фракции.
Смесь для кладки, или универсальная – самый простой вид сухой строительной смеси. В конце концов, еще не так давно было уже хорошо, если в наличии был только цемент и песок. Это к тому, что готовая кладочная смесь по большому счету лишь увеличивает удобство и скорость работы (хотя и этого немало), и при необходимости можно обойтись без нее. А вот приготовить самостоятельно аналоги других смесей так же легко не получится.
Начнем с того, что большая часть современных добавок к строительным растворам просто не продается в розницу. А производство многих сухих смесей подразумевает до 5-6 и более добавок. И даже если эти добавки можно было бы приобрести в магазине, практической пользы в этом мало. Дело в том, что большинство добавок и модификаторов требуют очень точной дозировки. В условиях современного производства соотношением компонентов сухих смесей заведует электроника. На стройке же надо работать, а не заниматься ерундой.
Один пример. Известно, что жидкое стекло придает изделию из раствора на основе цемента гидроизолирующие свойства. Но оно также является ускорителем реакции твердения цемента. Попробуйте лишь немного увеличить долю жидкого стекла (а речь идет об 1-1,5% ЖС от массы смеси и ошибиться в пропорции, отмеряя на глаз очень легко) и раствор затвердеет моментально, еще в бетономешалке. Поэтому на производстве в сухие смеси включают комплекс добавок. Например, одна добавка для гидроизоляции, другая для увеличения времени жизни раствора после затворения, третья как пластификатор и т.п.
Помимо химических добавок, вступающих в реакцию с вяжущими компонентами сухих смесей, в готовых смесях широко используются различные инертные добавки. Это может быть пенопластовая крошка для снижения объемного веса материала, фибра как армирующие волокна, гранитная крошка для придания поверхности шероховатости и другие материалы.
Однажды попробовав работу специализированными сухими смесями, многие строители (особенно отделочники-штукатуры) теперь попросту отказываются мешать цемент с песком. Неспециалисту также проще научиться работать с готовыми составами, это еще один плюс в копилку сухих смесей.
Группа BESTO производит и продает все основные виды ССС произведенных на основе высококачественного цемента м500 д0 «Евроцемент».
www.avtobeton.ru
Производство сухих строительных смесей: география поставок оборудования ВСЕЛУГ
01.10.2004
А.В. ТЕЛЕШОВ, директор, А.Б. ДОЛГОПОЛОВ, инженер-конструктор, машиностроительная компания ВСЕЛУГ™ (Москва)
Машиностроительная компания ВСЕЛУГ™ изготавливает оборудование для работы с сыпучими материалами более 10 лет. Продукция компании ориентирована на ряд отраслей промышленности, первое место среди которых занимает промышленность строительных материалов. Приоритетным направлением в этой отрасли является поставка комплексов по производству сухих смесей.
В объеме продаж компании более 70% приходится на комплектные технологические линии. Каждая линия индивидуальна, разрабатывается в соответствии с заданием и пожеланиями заказчика, но при этом состоит преимущественно из серийно выпускаемого оборудования.
В составе линий по производству сухих смесей мы поставляем:
– интенсивные смесители ВСЕЛУГ Торнадо™ объемом 0,3–3 м3;
– машины для фасовки смесей в мешки ВСЕЛУГ Турбо™ и ВСЕЛУГ Аэропресс™;
– машины для загрузки мешков в вагоны, автомобили и на поддоны ВСЕЛУГ Консоль™;
– классификаторы для разделения сухого песка на фракции ВСЕЛУГ Каскад™;
– машины для упаковки смесей в мягкие контейнеры емкостью 500–1500 кг;
– машины для упаковки смесей в пакеты емкостью 1–5 кг;
– оборудование для распаковки исходных компонентов;
– оборудование для погрузки смесей навалом;
– объемные дозаторы легких заполнителей;
– весовые дозаторы добавок;
– винтовые конвейеры;
– ковшовые элеваторы;
– рукавные фильтры.
Заводы по производству сухих строительных смесей имеют в своем составе одну или несколько технологических линий. Работа по компоновке технологической схемы будущего производства ведется в тесном контакте с заказчиками.
После определения часовой производительности и планируемого ассортимента продукции уточняется возможность закупки всех необходимых сырьевых компонентов и способы их доставки, требования к степени автоматизации технологического процесса, способам упаковки и отгрузки продукции. Совместно со специалистами заказчика мы выбираем место размещения производства.
При этом территориальные участки оцениваются с учетом имеющихся объектов производственной инфраструктуры, складских помещений, подъездных путей.
В составе линии поставляется автоматизированная система управления. На объекте наши специалисты осуществляют пусконаладочные работы, настройку программного обеспечения в соответствии со специфическими требованиями заказчика, обучение обслуживающего персонала.
Свою задачу мы видим в выполнении комплекса инжиниринга и стремимся обеспечить заказчиков всем необходимым – выполняем разработку чертежей строительных конструкций, изготавливаем металлоконструкции и силосы.
Результатом деятельности компании ВСЕЛУГ™ в течение последних пяти лет стали более 50 успешно реализованных проектов в области производства сухих смесей.
Среди них технологические комплексы производительностью от 3 до 60 т/ч.
Крупнейшим центром по производству смесей, безусловно, является Московская область. Здесь на оборудовании ВСЕЛУГ™ выпускается продукция компаний «Старатели»
(четыре технологические линии), «Consolit», «Ivsil», «Боларс». В сентябре введен в действие завод по производству смесей французской компании «Emfi» (рис. 2).
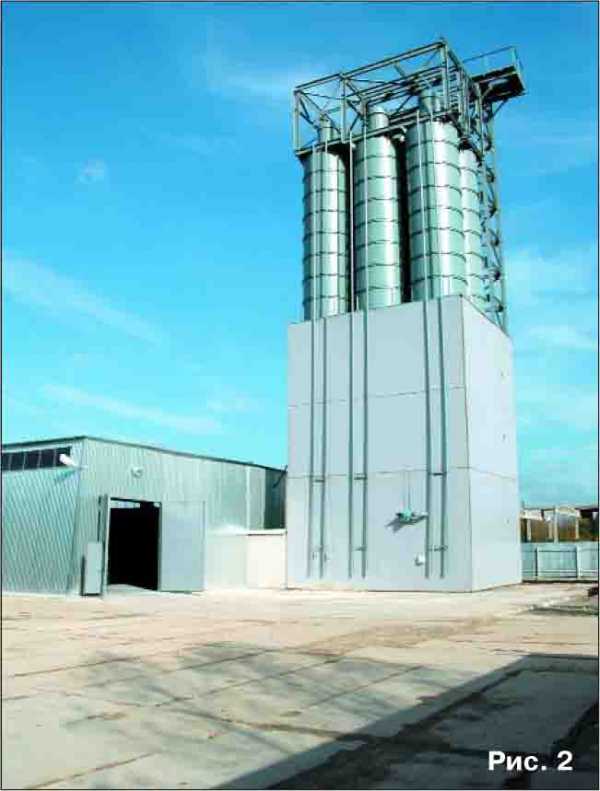
Одна из особенностей рынка Москвы заключается в широком применении дешевых универсальных смесей. Объем реализации этой продукции велик, а темпы роста не уступают темпам развития рынка модифицированных смесей. В 2004 г. компания выполнила заказ на поставку линии по производству универсальных смесей производительностью 60 т/ч.
Вторым по величине производственным центром является Ленинградская область. Самый крупный производитель смесей здесь – компания «MC-Bauchemie Russia» (торговая марка «Плитонит») – имеет три технологические линии ВСЕЛУГ™. Среди наших новых заказчиков в этом регионе компании «Гидротекс» и «Северное управление строительства».
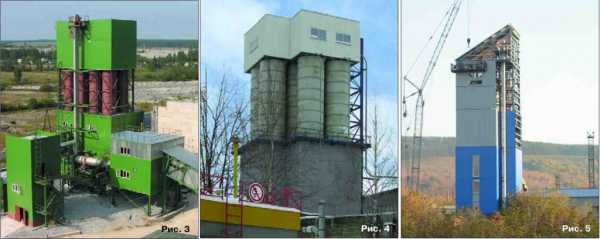
В отличие от Москвы и Санкт-Петербурга ввод в действие новых производств на Урале часто опережает работу по продвижению продукции на рынок. Только один из построенных заводов (компания «Гипсополимер» в Перми) в течение первого года работы был переведен на двухсменный режим (рис. 4).
Аналогичная ситуация складывается в Сибири. За последний год введены в действие заводы и новые линии компаний «Ливна Холдинг» и «Геркулес» в Новосибирской области, завод компании «Кузбасспромсервис» в Кемеровской области (рис. 5). В октябре состоялась официальная церемония открытия завода компании «ПСО АСК» в Омске (рис. 6)
В Нижнем Новгороде компания «EK Кемикал» завершает реализацию проекта по выпуску гипсовых смесей на второй технологической линии, которая дополнит линию цементных смесей, находящуюся в эксплуатации с середины 2003 г.
В южных регионах производство ССС развивается менее интенсивно. Пущены небольшие комплексы по производству смесей на Белгородском комбинате строительных материалов, Волгоградском гипсовом заводе. В Ростовской области работает линия фирмы ТиМ.Успешно развивается рынок сухих смесей Казахстана. Здесь нашими заказчиками являются компания «Алит» из Астаны и компания «Семейцемент» (Семипалатинский цементный завод), пустившая в действие завод по производству смесей модульного типа (рис. 7).
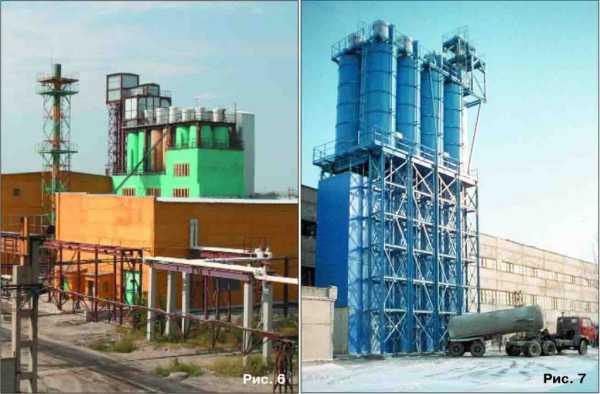
Анализируя тенденции развития производства сухих смесей в целом, нужно отметить две особенности, отличающие российские заводы от западноевропейских. Это меньшая единичная мощность линий и меньшее число используемых в производстве основных компонентов.
С другой стороны, обращает на себя внимание изменение в подходе к автоматизации. Если недавно полностью автоматизированные линии воспринимались как ненужная роскошь, то теперь ведущие производители смесей предпринимают реальные шаги для того, чтобы полностью исключить из производства человеческий фактор.
Статистика продаж оборудования ВСЕЛУГ™ для производства сухих смесей свидетельствует, что новая отрасль строительной индустрии развивается нарастающими темпами. Наряду с заказами от наших старых партнеров мы получаем много запросов, проектируем и поставляем оборудование для компаний, приходящих в этот бизнес из других областей.
Всех заинтересованных в организации современного производства сухих смесей гарантированного качества, в модернизации и расширении действующих производств мы приглашаем к сотрудничеству.
Все статьи
vselug.ru
Состав сухих строительных смесей для самоделкиных
Ранее в статьях по изготовлению садового декора уже не раз приводился различный состав сухих строительных смесей (а также клея), которые могли бы использовать в своих работах самоделкины.
Сегодня пришло время объединить и дополнить основополагающие подходы к выбору и применению добавок для сухих строительных смесей (ССС) и более подробно рассказать о их влиянии на время и качество проводимых работ по изготовлению садового декора, а также строительстве и отделки поверхности.
С о д е р ж а н и е
- Минеральные вяжущие вещества. Достоинства и недостатки.
- Химические и полимерные добавки в сухие строительные смеси. Что и когда добавлять.
- Наполнители в ССС. Их необходимость и распределение.
Основной состав сухих строительных смесей включает минеральные вяжущие вещества
Для изготовления искусственного камня, а также декоративной штукатурки, одним из основных компонентов сухой строительной смеси является цемент, гипс и гашеная известь.
Они и есть минеральные вяжущие. При смешивании с водой образуется пластичная смесь, которая постепенно застывает и каменеет.
Главные показатели отвердевшего камня – его прочность, водонепроницаемость, длительный срок эксплуатации.
Если в состав сухой строительной смеси входит плотный и крепкий наполнитель, то прочность искусственного камня определяется качеством минерального вяжущего, водоцементным соотношением и степенью (завершенностью) реакции гидратации.
Смесь цемента с водой (в отличии от гипса) имеет больший объем по сравнению с продуктом гидратации. Поэтому происходит небольшая усадка массы, у гипса наоборот – расширение. В связи с этим смешивать цемент и гипс для ускорения застывания смеси (как это советуют многие самоделкины), крайне не желательно. Необходимое и допустимое количество гипса, входящего в состав цемента, уже обеспечено заводом-изготовителем (1-4%).
Усадка сильно зависит от условий, в которых происходит застывание раствора. Поэтому постоянно приходится напоминать: чтобы не образовывались трещины на поверхности застывающего камня, необходимо несколько дней держать изделие закрытым полиэтиленовой пленкой. Она сохраняет необходимую влажность воздуха и самого изделия, что в свою очередь позволяет оптимально осуществить реакцию гидратации. Созревание и укрепление цементного камня будет проходить еще несколько недель, но самые важные первые дни.
Гипс и цемент как минеральные вяжущие неплохо работают на сжатие, но слабо справляются с воздействиями при растяжении и изгибе.
Что же сделать, чтобы избежать этих ограничений? Как обеспечить полную гидратацию цемента, когда габариты изделия или площадь обрабатываемой поверхности не позволяют использовать гидроизоляционную пленку? Как сделать липким раствор, чтобы он обеспечивал хорошую адгезию к стальной или пластмассовой арматуре (при изготовлении садовой скульптуры), а также к не впитывающим воду поверхностям?
Помочь в решении этих вопросов смогут химические и полимерные добавки в сухие строительные смеси.
Химические и полимерные добавки в сухие строительные смеси. Что и когда добавлять
Если Вы читали статьи на kamsaddeco.com об изготовлении различного каменного декора, то заметили, что практически все предлагаемые составы цементной смеси отличаются друг от друга.
Это объясняется тем, что универсальный продукт всегда обходится дороже. А в каждом конкретном случае состав минеральных составляющих должен быть оптимальным, тогда и количество добавок в приготовленной смеси будет минимальным. А для самоделкиных этот критерий является едва ли не самым главным, так как позволяет обеспечить наименьшую стоимость проводимых работ.
Основной добавкой (практически для всех видов смеси) являются порошкообразные эфиры целлюлозы. Параметр, определяющий дозировку (0,1-0,5%), называется вязкостью и может иметь очень большой диапазон значений, начиная с десятков единиц до нескольких сотен тысяч единиц. Чем больше вязкость целлюлозы, тем меньше ее необходимо добавлять в сухую смесь.
Чтобы сэкономить на затратах, хотелось бы так и поступить. Но на заводах-изготовителях подход обратный и причина в том, что при больших значениях вязкости, очень трудно удерживать технологический процесс в заданных пределах при использовании ССС. Так для клеевых смесей рекомендуется использовать эфиры целлюлозы с вязкостью 1500-3000 единиц. Но тут у самоделкиных для проведения экспериментов огромное поле деятельности. Можно получить нестандартные интересные результаты при использовании больших значениях полимера.
Главным полезным свойством эфиров целлюлозы является способность удерживать воду в массе раствора. Вода очень быстро испаряется или впитывается в пористую основу (бетон, кирпич, гипс, картон и т.д.). Поэтому основу предварительно грунтуют, а готовое изделие укрывают полиэтиленовой пленкой.
Эти процедуры можно частично или полностью исключить при использовании в растворе эфиров целлюлозы. Благодаря этой добавки, раствор после нанесения еще на полчаса дольше (при равных условиях) сохраняет пластичность и клеющую способность.
Дополнительно целлюлоза обладает загущающими свойствами. Реакция гидратации проходит более четко на всех участках смеси. Готовое изделие или поверхность имеет лучшие показатели по прочности на сжатие и изгиб.
Для придания смеси большей липкости и уменьшения сползания раствора с вертикальной поверхности применяется редиспергируемый порошок (РПП). Дозировка составляет от 1% и выше в зависимости от задачи и марки РПП.
При разведении сухой смеси в воде порошок растворяется и затем при отверждении полимеризуется. В порах камня образуются гибкие связи, которые значительно упрочняют изделие или поверхность и эластично армируют камень.
Чтобы получить особо гибкие (мы еще этого не делали) изделия, применяют двухкомпонентные системы. При этом вместо воды используют разбавленную полимерную дисперсию. Очень часто мастера называют ее жидким латексом. Его также используют в модифицированных растворах для изготовления садовой скульптуры и декоративных изделий для сада.
Если состав сухой строительной смеси подбирается самостоятельно, то надо обязательно учитывать область ее применения.
Не зря изготовители ССС пишут на упаковке допустимую толщину наносимого слоя. Он определяется количеством в смеси целлюлозы и РПП.
При толстостенном нанесении раствора передозировка целлюлозы опасна тем, что при внешнем застывании внутренняя часть раствора остается еще мягкой. В таком случае раствор лучше наносить несколькими слоями с последовательной просушкой каждого слоя.
При недостатке целлюлозы возможно появление трещин.
Переизбыток РПП приводит к значительному росту стоимости проводимых работ, а также их усложнению из-за чрезмерного прилипания раствора к рабочему инструменту.
Поэтому в зависимости от назначения состав сухих строительных смесей может быть двух категорий: нормальный уровень и повышенный (также как в статье об оригинальных плитках в части состава клея).
Ранее (например, тут) не раз указывалось на недопустимость введения в состав сухих строительных смесей (на основе цемента) клея ПВА и КМЦ и вот почему.
Клей КМЦ применяется как загуститель для не щелочных систем (не для цемента). И редиспергируемый порошок ПВА применяется как клей тоже только для не щелочных систем в теплых условиях.
Рассмотренные выше полимерные вяжущие щелочестойкие и обеспечивают совместимость с цементом.
Эти добавки в сухие строительные смеси являются основными при работе с бетоном с целью изготовления садового декора.
Дополнительно в смесях можно использовать такие химические добавки как: порообразователи, диспергаторы, антивспениватели, ускорители и замедлители схватывания, гидрофобизаторы, разжижители (пластификаторы), армирующие волокна. Частично они также применялись в ранее представленных работах на страницах kamsaddeco.com. Более подробно будем с ними знакомиться при изготовлении нового садового декора.
А теперь переходим к очень важной главе сегодняшней статьи – наполнители в ССС.
Наполнители в сухих строительных смесях. Их необходимость и распределение
Для изготовления малых архитектурных форм и садового декора таких, как беседки, скульптуры, вазы, садовая мебель, мангалы и барбекю, место для костра, различные формы искусственного камня, садовые дорожки и площадки, подпорные стенки, небольшие строения и т.д., используются различные по составу цементные растворы, в состав которых обязательно входят какие-либо пассивные и/или активные наполнители.
При изготовлении сухих смесей специалисты выполняют требования определенных стандартов в том числе и по наполнителям.
В нашем случае при работе в саду важнее использовать практические советы и опыт бывалых самоделкиных, которые мы и учитываем.
В ранее опубликованных статьях на страницах kamsaddeco.com (в частности тут) уже приводились основные параметры и свойства добавок и наполнителей, а также их объемные количества в составах смесей для различного применения.
К наполнителям, входящим в состав сухих строительных смесей, относятся: кварцевый песок, песок из шлаков, зола-унос, кварц молотый, горный песок, крошка из кирпича, мраморная и доломитовая мука, мел. В декоративные составы также в качестве наполнителя включают вермикулит, мелкую мраморную крошку, молотое стекло и другие компоненты.
Наполнители должны содержать как можно меньше примесей, ухудшающих адгезию раствора. Так глина в песке в количестве 1,0-1,5% ухудшает адгезию клея примерно в два раза.
При изготовлении пластичного бетона для декоративных форм редко используется щебень. В саду он включается в состав бетона для строительства фундаментов, водоемов, каких-то оснований, например, бетонных фигур, площадок, дорожек или подпорных стен.
Для изготовления садового декора обычно в состав бетона входит мелкая гранитная крошка или промытый отсев.
Теперь еще несколько важных моментов в подборе наполнителей, входящих в состав сухих строительных смесей, которые необходимо учитывать при самостоятельной дозировке.
Применительно к наполнителям специалисты используют понятие “гранулометрический состав” или “модуль крупности”. Для чего нужны эти характеристики?
В предыдущей главе указывалось, что надо стараться подготовить оптимальный состав сухой смеси с целью экономии средств и получения максимальных механических показателей.
Для этого необходимо подобрать наполнители таким образом, чтобы обеспечивалась их плотная упаковка в цементной смеси. Чем меньше остается свободного незаполненного места, тем лучше будут показатели. При этом мы экономим цемент и можем заменить его на более высокого качества. Также экономятся дорогостоящие полимерные и химические добавки. Очень важно принимать во внимание пористость наполнителей. И чаще всего мы с этим сталкиваемся при изготовлении искусственного камня и декора из гипертуфа.
Иногда некоторые жалуются, что их изделия разваливаются уже через несколько лет эксплуатации. Обычно при подготовки раствора вода льется “на глаз” и мало кто предупреждает, что надо не спешить и выждать, пока пористый наполнитель (вспученный перлит, торф или мох) полностью не насытится и перестанет забирать из раствора воду, так необходимую для полной гидратации цемента.
Этот момент также надо учитывать при введении в состав сухих смесей красителя для окраски бетона. Так, например, желтый железооксидный пигмент потребляет значительно больше воды, чем другие.
В то же время особенность рыхлых наполнителей можно использовать как положительное свойство при изготовлении больших декоративных поверхностей с целью частичной или полной замены дорогостоящих эфиров целлюлозы. Эта процедура позволит увеличить открытое время отверждения без использования гидроизоляционной пленки.
Еще один очень важный параметр, влияющий на качество сухой смеси – это удельная площадь поверхности наполнителя.
Чем мельче наполнитель, тем больше его удельная площадь поверхности. В этом случае для достижения достаточной подвижности раствора требуется больше воды. Если, например, в смесь добавляется кварцевая мука, а количество воды и цемента остается прежним, то трещин не избежать.
♦ Большая удельная поверхность наполнителя требует дополнительного количества вяжущего.
Ранее в статьях не раз обращалось внимание читателей на мелкозернистый бетон. И задача его не в получении качественной финишной обработки, а в получении очень прочного камня для тонкостенных и ажурных изделий.
Для его изготовления применяются наполнители близкие по удельной поверхности к параметру цементного зерна. При этом по аналогии с цементом они начинают работать как активные вяжущие и частично заменяют его работу. Здесь убиваем сразу трех зайцев – экономим цемент, избегаем при этом образования трещин и получаем камень повышенной прочности.
Еще раз для сравнения несколько цифр: зерно обычного цемента в среднем составляет 40…80 мкм, у маршалита – 50…100 мкм, у золы – 12…25 мкм, у микрокремнезема – 2…10 мкм.
Из этих данных видно, что наиболее активные свойства имеет микрокремнезем. Его и золу чаще всего используют специалисты для частичной замены цемента и получения лучших характеристик искусственного камня.
Считается, что при отсутствии или малом количестве наполнителя размером менее 100 мкм цементный раствор формирует недостаточное количество кристаллов камня и имеет нежелательные аморфные и рыхлые образования, приводящие к потери прочности.
Надо также отметить, что размер зерна не полностью определяет требования по улучшению механических характеристик. Важен химический состав наполнителя. Так, например, добавка мела с таким же размером зерна уменьшит прочность камня в несколько раз.
Химическая активность SiO2 пока не отменялась.
И наконец еще одно правило: если Вы оптимально подобрали состав наполнителей, то получите и минимально возможное соотношение воды к суммарному вяжущему веществу. При этом получите максимальные механические свойства искусственного камня для своего садового декора.
Всем удачи и до новых встреч на страницах kamsaddeco.com.
Статьи на тему
Химия в бетоне
Выбор инструмента для изготовления декоративного бетона
Бетон в работах Гауди
Особенности пластификаторов
Смесь пигментов для получения заданного оттенка
Декоративная бетонная поверхность
Тонкие плитки
Пустотелый ангел
Постройки из ферроцемента
kamsaddeco.com
Производство сухих строительных смесей | Идеи для бизнеса 💲
Статья про производство сухих смесей, оборудование и технологию изготовления. Коротко и подробно о самом главном в этом бизнесе
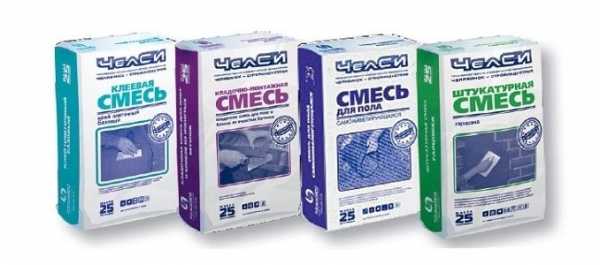
Сухие строительные смеси очень широко применяются в строительстве самих зданий, а также, такой вид агрегатного состояния оптимален для материалов внутренней и внешней отделки. Сухая смесь очень удобна для доставки, прохождения всех этапов продажи, и применения непосредственно по назначению. Они готовы к применению, необходимо лишь перед использованием добавить положенное количество воды и строительную смесь и он превращается в готовый материал.
Производство строительных смесей начинается с горнодобывающего предприятия. При помощи их извлекается из месторождений необходимые компоненты, и именно они будут применяться далее в качестве сырья.
Содержание
- 1. Оборудование для производства строительных смесей
- 2. Технология производства сухих смесей + видео
Чтобы организовать производство строительных смесей, необходимо иметь целую разновидность дробильных машин, которые поступательно смогут из больших глыб доставленного минерала сделать необходимый порошок. Индивидуально для каждой технологии изготовления подбираются дробильные машины. Производители таких машин смогут не только предложить самые подходящие, а и будет возможность выбрать линии конвейера. Они являются важным элементом для быстрого протекания процесса производства.
Список основного оборудования для производства строительных смесей:
- Смеситель;
- Фасовочный бункер и шнек;
- Сушка для песка;
- Вибросито для просеивания;
- Весы электронные;
- Товарные весы.
Стандартные строительные смеси состоят обычно из двух следующих компонентов:
Их доли разняться исходя из марки цемента и желаемой марки готового продукта — обычно М150 или М200.
Если добавить в этот список поверхностно-активные вещества (ПАВ), то такую смесь можно уже использовать для пола или кладки плитки. ПАВ делают готовый раствор более пластичным.
ПАВ способны повышать поверхностное натяжение у поверхности раздела фаз, например на границах раздела фаз-твердое тело, вода-воздух. Мельчайшие частицы ПАВ адсорбируются , другими словами связываются прочно с внутренней поверхностью раздела тел, образуя на этих поверхностях молекулярные слои толщиной в одну молекулу.
Видео как делают строительные смеси на мини-заводе:
Величина этого адсорбционного слоя относится к диаметру цементной частицы, так же как толщина спички к высоте 30-этажного дома. Применение однако в малых дозах добавок ПАВ к цементным системам существенно меняет их свойства. Используемые при производстве строительных смесей поверхностно-активные добавки, по определяющему эффекту действия на цементные системы условно можно разделить на три группы:
- Гидрофилизующие;
- Гидрофобизующие;
- Воздухововлекающие.
Гидрофилизующие добавки способны при затворении водой вяжущего предотвращать слипание отдельных цементных частиц между собой на определенный срок. В таком случае несколько замедляется коагуляция новообразований, то есть высвобождается вместе с тем некоторое количество воды которое как бы застревает обычно в коагуляционных структурах. Требуемая удобоукладываемость строительной смеси с добавкой по этой причине достигается при меньшем количестве воды затворения, чем без добавки.
Наибольшее распространение в практике приготовления цементных бетонов и растворов получили гидрофилирующие добавки на основе лигносульфатов-сульфитно-дрожжевой бражки (СДБ). Она способна несколько замедлить твердение бетона в раннем возрасте и поэтому на заводах ЖБИ применяют ее в сочетании с добавками ускорителями твердения строительных смесей.
Суперпластификаторы — новые эффективные разжижители бетонной смеси — в большинстве случаев представляют синтетические полимеры — производные меламиновой смолы или нафталинсульфокислоты. Применяют суперпластификаторС-3(НИИЖБ) — на основе нафталинсульфокислоты, суперпластификатор 10-03 (ВНИИЖелезобетон) — продукт конденсации сульфированного меламина с формальдегидом и др. При введении в бетонную смесь суперпластификатора резко увеличивается ее подвижность и текучесть.
Воздействуя на строительную смесь, как правило, в течение 2…3 ч с момента введения, суперпластификаторы под действием щелочной среды подвергаются частичной деструкции и переходят в другие вещества, безвредные для бетона и не тормозящие процесса твердения. Суперпластификаторы, вводимые в строительную смесь в количестве 0,15…1,2% от массы цемента, разжижают строительную смесь в большей мере, чем обычные пластификаторы. Пластифицирующий эффект сохраняется, как правило, 1…2 ч после введения ПАВ, а через 2…3 ч он уже невелик.
Суперпластификаторы используются при производстве строительных смесей как единолично, так и в комплексе с другими добавками, например с сульфитно-дрожжевой бражкой (СДБ) и нитрит-нитрат-хлоридом кальция (ННХК). При использовании комплексной добавки содержание каждой из них составляет: «10-03» — 0,3-1,2%; ННХК — 1,5…2,5% и СДБ — 0,1…1,15 % от массы цемента.
Суперпластификаторы позволяют существенно снизить В/Ц, повысить подвижность раствора, изготовить изделия высокой прочности, насыщенных арматурой из изопластичных строительных смесей.
Гидрофобизующие добавки, как правило, существенно повышают нерасслаиваемость, связанность бетонной (растворной) смеси, находящейся в покое. При действии внешних механических факторов (при перемешивании, укладке и т. д.) бетонная или растворная строительная смесь с добавкой отличается повышенной пластичностью. Такое свойство гидрофобизующих строительных смесей объясняется специфическим смазочным действием тончайших слоев по-верхностно-активныхвеществ, распределяемых в растворе.
Кроме того, эти добавки предохраняют цементы от быстрой потери активности при перевозке или хранении. В качестве гидрофобизующих ПАВ раньше применялись в основном природные продукты — некоторые животные жиры, алеиновая и стеариновая кислоты. Развитие химической промышленности дало возможность широко использовать в производстве новые гидрофобизующие добавки— битумные дисперсии (эмульсии и эмульсосуспензии), нафтеновые кислоты и их соли, окисленные, синтетические жирные кислоты и их кубовые остатки, кремнийорганические полимеры и др.
Воздухововлекающие добавки позволяют получать бетонные (растворные) смеси с некоторым дополнительным количеством воздуха. Чтобы повысить пластичность строительной смеси, обычно увеличивают объем вяжущего теста. Вовлекая воздух, увеличивается объем вяжущего теста без введения лишнего цемента. Поэтому удобоукладываемость такой системы повышается.
К тому же воздухововлекающие ПАВ образуют и ориентированные слои, активные в смазочном отношении. Широко применяют воздухововлекающие добавки на основе смоляных кислот: смолу нейтрализованную воздухововлекающую (СНВ), омыленный древесный пек и др.
К ускорителям твердения цемента, увеличивающим нарастание прочности бетона, особенно в ранние сроки, относятся хлорид кальция, сульфат натрия, нитрит-нитрат-хлоридкальция и др.
Читают сейчас:
Влияние хлористого кальция на повышение прочности бетона объясняется его каталитическим воздействием на гидратацию C3S и C2S, а также реакцией с С3А и C4AF. Ускорители твердения не рекомендуется применять в железобетонных конструкциях и предварительно напряженных изделиях с диаметром арматуры менее 5 мм и для изделий автоклавного твердения, эксплуатирующихся в среде с влажностью более 60%. Сульфат натрия может вызвать появление высолов на изделиях.
В нитрит-нитрат-хлоридекальция ускоряющее действие хлорида сочетается с ингибирующим действием нитрата кальция. Противоморозные добавки — поташ, хлорид натрия, хлорид кальция и другие — понижают точку замерзания воды, чем способствуют твердению бетона при отрицательных температурах. Для замедления схватывания применяют сахарную патоку и СДБ, ГКЖ-10иГКЖ-94.
Пено- и газообразователи применяют для изготовления ячеистых бетонов. К пенообразователям относятся клееканифольные, смолосапониновые, алюмосульфонафтеновые добавки, а также пенообразователь ГК. В качестве газообразователей применяют алюминиевую пудру ПАК-3 и ПАК-4.
Комбинированные ПАВ, например пластификатор СДБ, ускоритель твердения (хлористый кальций) с ингибитором (нитратом натрия), способствуют экономии цемента. При этом ускоритель твердения нейтрализует некоторое замедление твердения готовой строительной смеси в раннем возрасте.
Специальные добавки обеспечивают получение водонепроницаемых растворов или бетонов, регулируют сроки схватывания и др.
Во время приготовления бетонных строительных смесей добавляют следующие виды химических ПАВ, которые способны улучшить характеристики будущего бетона и уменьшить одновременно расход цемента во время производства:
Пав используются также довольно широко и в виде пластифицирующих добавок, которые позволяют не только экономить цемент но и интенсифицировать процесс твердения . Также за счет использования пластификаторов, удается снизить энергозатраты при приготовлении бетонных смесей. Применении ПАВ в рациональных, и строго дозированных количествах, позволяет снизить энергозатраты во время приготовления бетонных смесей до 50 процентов.
Широко используются в производстве строительных смесей на ряду с другими видами добавок суперпластификаторы С-3,НИЛ-10, С-4,10-03, КМБ и другие. Использование таких пластификаторов позволяет увеличивать на много прочность бетона, уменьшить водопотребность бетонной массы не уменьшая подвижность и удобоукладываемость.использование суперпластификатора 10-03 показало что увеличение подвижности бетонной смеси происходит в 7 раз.
При уменьшении доли цемента и при использовании такого же пластификатора 10-03, водопотребность бетонной массы уменьшается в два раза. Прочность бетонной массы,при этом после суточного твердения возрастает примерно до 70 процентов,а при тепловой обработки до 20 процентов.
Суперпластификаторы готовятся на основе меламиноформальдегидных смол. Также на основе продуктов конденсации нафталинсульфокислоты, формальдегида, модифицированных лигносульфонатами. На ряду с этими суперпластификаторами на предприятиях по производству бетонов применяются активно и более дешевые пластификаторы.
В частности в роли ПАВ широко используют в строительных смесях более дешевый хлорид кальция в качестве ускорителя твердения вяжущих веществ. Но такой пластификатор вызывает коррозию стальной арматуры и уменьшает стойкость бетона ( цементного камня) в сульфатной среде. Поэтому применение такой добавки в бетонах ограничено.
Сульфат натрия используют преимущественно при тепловлажностной обработке бетона.Использование сульфата натрия дает снижение расхода цемента до 10 процентов,а также сокращается время тепловлажной обработки бетона, цикл обработки может сократится от 20 до 30 процентов.
Нитрат натрия также применяется в основном при тепловлажной обработки строительной смеси. Использование нитрат натрия совместно с пластификатором СДБ сокращает время пропаривания до 25%, а расход цемента уменьшается до 14%. Для увеличения водопроницаемости бетона в состав бетона вводят нитрат кальция.
Комплексные добавки в основном влияют на такие важные характеристики строительной смеси, как темп роста прочности будущего бетона, подвижность, сроки схватывания, усадка, морозостойкость, коррозионная стойкость и другие.
Применение комплексных добавок в строительной смеси главным образом вызвано необходимостью уменьшить коррозию стальной арматуры, усадку, а также возможность увеличения прочности. Введение комплекса таких солей как CaCl2+NaNO2, позволяет исключить практически полностью коррозию стальной арматуры. Коррозия арматуры в бетоне происходит за счет агрессивных ионов хлора, которые регулируется солями CaCl2+NaNO2. Для увеличения прочности в строительную смесь вводят хлорид кальция.
Применение Na2SO4 ( от 0,8 до 1.2 % ) совместно с СДБ (0,15…0,2%) при использовании кассетной технологии, существенно снижается расход цемента -от 8 до 10 процентов. Экономить цемент и сокращать время затраченное на пропаривание бетонных изделий позволяет также СДБ+NaOH. Влияние расхода цемента на прочность пропаренного бетона с добавками : KCl + (0,5 + 1,2)% Na2SO4 и Na2S2O3 + (0,7 + 1)% Na2SO4 и других показано в таблице-1.
Таблица-1. Влияние вида и количество комплексных добавок на расход цемента
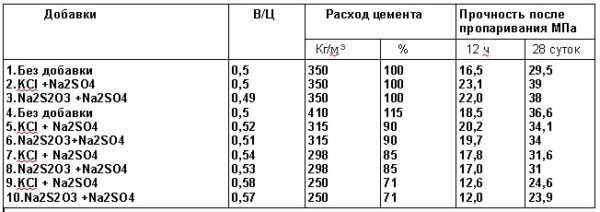
Они позволяют снизить расход цемента с 350 до 298 кг/м³, то есть получить экономию до 15% вяжущего с сохранением отпускной и марочной прочности бетона. В связи с ограниченным обеспечением строительной индустрии электролитами большое значение имеет их применение в комплексе с ПАВ. При этом резко повышается эффективность химических добавок, сокращается в 3…6 раз потребное количество электролитов.
При использовании нитрит-нитрат-хлорид кальция (ННХК) в количестве 2…3 % от массы цемента заданная подвижность бетонной смеси достигается при меньшем ( на 6,1…6,5 %) расходе цемента. При использовании 0,5 % ННХК пластифицирующее действие отсутствует. Применение комплексной добавки из СДБ и 0,5 % ННХК оказывает сильное пластифицирующее действие и позволяет не только снизить расход цемента на 10% но и уменьшить жесткость смеси с 19 до 10 с.
Введение ПАВ и ННХК улучшает технологические свойства бетона. При введении в бетон комплексных добавок ( при соответствующем сокращении расхода цемента на 9…12 %) получается бетон с F 500…F 1000,что увеличивает срок службы конструкций. Предельное количество пластифицирующих добавок в расчете на сухое вещество приведено в таблицу-2.
Таблица-2. Рекомендуемое количество пластифицирующих, а также пластифицирующе-воздухововлекающих добавок для тяжелого и легкого бетонов.
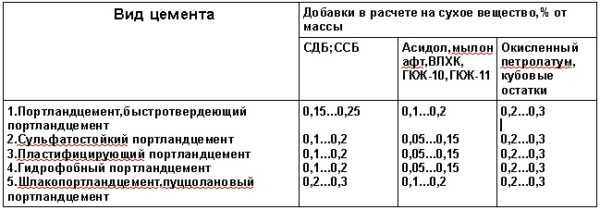
Рекомендуемое количество воздухововлекающих добавок в строительных смесях для тяжелых и легких бетонов, % по массе следующее:
- СНВ, СПД, ЦИНПС 1-0,005…0,025;
- КМ, БС, ГК, СМПН-0,05…0,15;
- ГКЖ-94-0,06…0,08( расход приведен по сухому веществу).
inask.ru
Производство сухих строительных смесей 💲
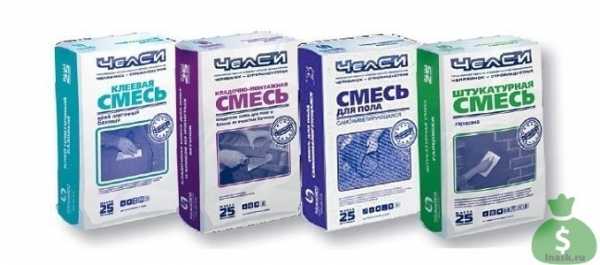
Сухие строительные смеси очень широко применяются в строительстве самих зданий, а также, такой вид агрегатного состояния оптимален для материалов внутренней и внешней отделки. Сухая смесь очень удобна для доставки, прохождения всех этапов продажи, и применения непосредственно по назначению. Они готовы к применению, необходимо лишь перед использованием добавить положенное количество воды и строительную смесь и он превращается в готовый материал.
Производство строительных смесей начинается с горнодобывающего предприятия. При помощи их извлекается из месторождений необходимые компоненты, и именно они будут применяться далее в качестве сырья.
Содержание
- 1 Оборудование для производства строительных смесей
- 2 Технология производства сухих смесей + видео
Оборудование для производства строительных смесей
Чтобы организовать производство строительных смесей, необходимо иметь целую разновидность дробильных машин, которые поступательно смогут из больших глыб доставленного минерала сделать необходимый порошок. Индивидуально для каждой технологии изготовления подбираются дробильные машины. Производители таких машин смогут не только предложить самые подходящие, а и будет возможность выбрать линии конвейера. Они являются важным элементом для быстрого протекания процесса производства.
Список основного оборудования для производства строительных смесей:
- Смеситель;
- Фасовочный бункер и шнек;
- Сушка для песка;
- Вибросито для просеивания;
- Весы электронные;
- Товарные весы.
Технология производства сухих смесей + видео
Стандартные строительные смеси состоят обычно из двух следующих компонентов:
Их доли разняться исходя из марки цемента и желаемой марки готового продукта — обычно М150 или М200.
Если добавить в этот список поверхностно-активные вещества (ПАВ), то такую смесь можно уже использовать для пола или кладки плитки. ПАВ делают готовый раствор более пластичным.
ПАВ способны повышать поверхностное натяжение у поверхности раздела фаз, например на границах раздела фаз-твердое тело, вода-воздух. Мельчайшие частицы ПАВ адсорбируются , другими словами связываются прочно с внутренней поверхностью раздела тел, образуя на этих поверхностях молекулярные слои толщиной в одну молекулу.
Видео как делают строительные смеси на мини-заводе:
Величина этого адсорбционного слоя относится к диаметру цементной частицы, так же как толщина спички к высоте 30-этажного дома. Применение однако в малых дозах добавок ПАВ к цементным системам существенно меняет их свойства. Используемые при производстве строительных смесей поверхностно-активные добавки, по определяющему эффекту действия на цементные системы условно можно разделить на три группы:
- Гидрофилизующие;
- Гидрофобизующие;
- Воздухововлекающие.
Гидрофилизующие добавки способны при затворении водой вяжущего предотвращать слипание отдельных цементных частиц между собой на определенный срок. В таком случае несколько замедляется коагуляция новообразований, то есть высвобождается вместе с тем некоторое количество воды которое как бы застревает обычно в коагуляционных структурах. Требуемая удобоукладываемость строительной смеси с добавкой по этой причине достигается при меньшем количестве воды затворения, чем без добавки.
Наибольшее распространение в практике приготовления цементных бетонов и растворов получили гидрофилирующие добавки на основе лигносульфатов-сульфитно-дрожжевой бражки (СДБ). Она способна несколько замедлить твердение бетона в раннем возрасте и поэтому на заводах ЖБИ применяют ее в сочетании с добавками ускорителями твердения строительных смесей.
Суперпластификаторы — новые эффективные разжижители бетонной смеси — в большинстве случаев представляют синтетические полимеры — производные меламиновой смолы или нафталинсульфокислоты. Применяют суперпластификаторС-3(НИИЖБ) — на основе нафталинсульфокислоты, суперпластификатор 10-03 (ВНИИЖелезобетон) — продукт конденсации сульфированного меламина с формальдегидом и др. При введении в бетонную смесь суперпластификатора резко увеличивается ее подвижность и текучесть.
Воздействуя на строительную смесь, как правило, в течение 2…3 ч с момента введения, суперпластификаторы под действием щелочной среды подвергаются частичной деструкции и переходят в другие вещества, безвредные для бетона и не тормозящие процесса твердения. Суперпластификаторы, вводимые в строительную смесь в количестве 0,15…1,2% от массы цемента, разжижают строительную смесь в большей мере, чем обычные пластификаторы. Пластифицирующий эффект сохраняется, как правило, 1…2 ч после введения ПАВ, а через 2…3 ч он уже невелик.
Суперпластификаторы используются при производстве строительных смесей как единолично, так и в комплексе с другими добавками, например с сульфитно-дрожжевой бражкой (СДБ) и нитрит-нитрат-хлоридом кальция (ННХК). При использовании комплексной добавки содержание каждой из них составляет: «10-03» — 0,3-1,2%; ННХК — 1,5…2,5% и СДБ — 0,1…1,15 % от массы цемента.
Суперпластификаторы позволяют существенно снизить В/Ц, повысить подвижность раствора, изготовить изделия высокой прочности, насыщенных арматурой из изопластичных строительных смесей.
Гидрофобизующие добавки, как правило, существенно повышают нерасслаиваемость, связанность бетонной (растворной) смеси, находящейся в покое. При действии внешних механических факторов (при перемешивании, укладке и т. д.) бетонная или растворная строительная смесь с добавкой отличается повышенной пластичностью. Такое свойство гидрофобизующих строительных смесей объясняется специфическим смазочным действием тончайших слоев по-верхностно-активныхвеществ, распределяемых в растворе.
Кроме того, эти добавки предохраняют цементы от быстрой потери активности при перевозке или хранении. В качестве гидрофобизующих ПАВ раньше применялись в основном природные продукты — некоторые животные жиры, алеиновая и стеариновая кислоты. Развитие химической промышленности дало возможность широко использовать в производстве новые гидрофобизующие добавки— битумные дисперсии (эмульсии и эмульсосуспензии), нафтеновые кислоты и их соли, окисленные, синтетические жирные кислоты и их кубовые остатки, кремнийорганические полимеры и др.
Воздухововлекающие добавки позволяют получать бетонные (растворные) смеси с некоторым дополнительным количеством воздуха. Чтобы повысить пластичность строительной смеси, обычно увеличивают объем вяжущего теста. Вовлекая воздух, увеличивается объем вяжущего теста без введения лишнего цемента. Поэтому удобоукладываемость такой системы повышается.
К тому же воздухововлекающие ПАВ образуют и ориентированные слои, активные в смазочном отношении. Широко применяют воздухововлекающие добавки на основе смоляных кислот: смолу нейтрализованную воздухововлекающую (СНВ), омыленный древесный пек и др.
К ускорителям твердения цемента, увеличивающим нарастание прочности бетона, особенно в ранние сроки, относятся хлорид кальция, сульфат натрия, нитрит-нитрат-хлоридкальция и др.
Читают сейчас:
Влияние хлористого кальция на повышение прочности бетона объясняется его каталитическим воздействием на гидратацию C3S и C2S, а также реакцией с С3А и C4AF. Ускорители твердения не рекомендуется применять в железобетонных конструкциях и предварительно напряженных изделиях с диаметром арматуры менее 5 мм и для изделий автоклавного твердения, эксплуатирующихся в среде с влажностью более 60%. Сульфат натрия может вызвать появление высолов на изделиях.
В нитрит-нитрат-хлоридекальция ускоряющее действие хлорида сочетается с ингибирующим действием нитрата кальция. Противоморозные добавки — поташ, хлорид натрия, хлорид кальция и другие — понижают точку замерзания воды, чем способствуют твердению бетона при отрицательных температурах. Для замедления схватывания применяют сахарную патоку и СДБ, ГКЖ-10иГКЖ-94.
Пено- и газообразователи применяют для изготовления ячеистых бетонов. К пенообразователям относятся клееканифольные, смолосапониновые, алюмосульфонафтеновые добавки, а также пенообразователь ГК. В качестве газообразователей применяют алюминиевую пудру ПАК-3 и ПАК-4.
Комбинированные ПАВ, например пластификатор СДБ, ускоритель твердения (хлористый кальций) с ингибитором (нитратом натрия), способствуют экономии цемента. При этом ускоритель твердения нейтрализует некоторое замедление твердения готовой строительной смеси в раннем возрасте.
Специальные добавки обеспечивают получение водонепроницаемых растворов или бетонов, регулируют сроки схватывания и др.
Во время приготовления бетонных строительных смесей добавляют следующие виды химических ПАВ, которые способны улучшить характеристики будущего бетона и уменьшить одновременно расход цемента во время производства:
- Индивидуальные — ПАВ, электролиты, полимерные смолы и другие.
- Комплексные — ПАВ (СДБ+ГКЖ-94,СДБ+СНВ и другие), комплексные электролиты следующих соединений (ННК+ННХК).
- Комплексные — ПАВ и электролиты (СДБ+Na2SO4; СДБ+ННХК, СДБ+Na2SO4; СДБ+NaNO3 и другие).
Пав используются также довольно широко и в виде пластифицирующих добавок, которые позволяют не только экономить цемент но и интенсифицировать процесс твердения . Также за счет использования пластификаторов, удается снизить энергозатраты при приготовлении бетонных смесей. Применении ПАВ в рациональных, и строго дозированных количествах, позволяет снизить энергозатраты во время приготовления бетонных смесей до 50 процентов.
Широко используются в производстве строительных смесей на ряду с другими видами добавок суперпластификаторы С-3,НИЛ-10, С-4,10-03, КМБ и другие. Использование таких пластификаторов позволяет увеличивать на много прочность бетона, уменьшить водопотребность бетонной массы не уменьшая подвижность и удобоукладываемость.использование суперпластификатора 10-03 показало что увеличение подвижности бетонной смеси происходит в 7 раз.
При уменьшении доли цемента и при использовании такого же пластификатора 10-03, водопотребность бетонной массы уменьшается в два раза. Прочность бетонной массы,при этом после суточного твердения возрастает примерно до 70 процентов,а при тепловой обработки до 20 процентов.
Суперпластификаторы готовятся на основе меламиноформальдегидных смол. Также на основе продуктов конденсации нафталинсульфокислоты, формальдегида, модифицированных лигносульфонатами. На ряду с этими суперпластификаторами на предприятиях по производству бетонов применяются активно и более дешевые пластификаторы.
В частности в роли ПАВ широко используют в строительных смесях более дешевый хлорид кальция в качестве ускорителя твердения вяжущих веществ. Но такой пластификатор вызывает коррозию стальной арматуры и уменьшает стойкость бетона ( цементного камня) в сульфатной среде. Поэтому применение такой добавки в бетонах ограничено.
Сульфат натрия используют преимущественно при тепловлажностной обработке бетона.Использование сульфата натрия дает снижение расхода цемента до 10 процентов,а также сокращается время тепловлажной обработки бетона, цикл обработки может сократится от 20 до 30 процентов.
Нитрат натрия также применяется в основном при тепловлажной обработки строительной смеси. Использование нитрат натрия совместно с пластификатором СДБ сокращает время пропаривания до 25%, а расход цемента уменьшается до 14%. Для увеличения водопроницаемости бетона в состав бетона вводят нитрат кальция.
Комплексные добавки в основном влияют на такие важные характеристики строительной смеси, как темп роста прочности будущего бетона, подвижность, сроки схватывания, усадка, морозостойкость, коррозионная стойкость и другие.
Применение комплексных добавок в строительной смеси главным образом вызвано необходимостью уменьшить коррозию стальной арматуры, усадку, а также возможность увеличения прочности. Введение комплекса таких солей как CaCl2+NaNO2, позволяет исключить практически полностью коррозию стальной арматуры. Коррозия арматуры в бетоне происходит за счет агрессивных ионов хлора, которые регулируется солями CaCl2+NaNO2. Для увеличения прочности в строительную смесь вводят хлорид кальция.
Применение Na2SO4 ( от 0,8 до 1.2 % ) совместно с СДБ (0,15…0,2%) при использовании кассетной технологии, существенно снижается расход цемента -от 8 до 10 процентов. Экономить цемент и сокращать время затраченное на пропаривание бетонных изделий позволяет также СДБ+NaOH. Влияние расхода цемента на прочность пропаренного бетона с добавками : KCl + (0,5 + 1,2)% Na2SO4 и Na2S2O3 + (0,7 + 1)% Na2SO4 и других показано в таблице-1.
Таблица-1. Влияние вида и количество комплексных добавок на расход цемента
Они позволяют снизить расход цемента с 350 до 298 кг/м?, то есть получить экономию до 15% вяжущего с сохранением отпускной и марочной прочности бетона. В связи с ограниченным обеспечением строительной индустрии электролитами большое значение имеет их применение в комплексе с ПАВ. При этом резко повышается эффективность химических добавок, сокращается в 3…6 раз потребное количество электролитов.
При использовании нитрит-нитрат-хлорид кальция (ННХК) в количестве 2…3 % от массы цемента заданная подвижность бетонной смеси достигается при меньшем ( на 6,1…6,5 %) расходе цемента. При использовании 0,5 % ННХК пластифицирующее действие отсутствует. Применение комплексной добавки из СДБ и 0,5 % ННХК оказывает сильное пластифицирующее действие и позволяет не только снизить расход цемента на 10% но и уменьшить жесткость смеси с 19 до 10 с.
Введение ПАВ и ННХК улучшает технологические свойства бетона. При введении в бетон комплексных добавок ( при соответствующем сокращении расхода цемента на 9…12 %) получается бетон с F 500…F 1000,что увеличивает срок службы конструкций. Предельное количество пластифицирующих добавок в расчете на сухое вещество приведено в таблицу-2.
Таблица-2. Рекомендуемое количество пластифицирующих, а также пластифицирующе-воздухововлекающих добавок для тяжелого и легкого бетонов.
Рекомендуемое количество воздухововлекающих добавок в строительных смесях для тяжелых и легких бетонов, % по массе следующее:
- СНВ, СПД, ЦИНПС 1-0,005…0,025;
- КМ, БС, ГК, СМПН-0,05…0,15;
- ГКЖ-94-0,06…0,08( расход приведен по сухому веществу).
Мало информации по теме? Поиск подскажет:
Автор статьи: Максим Миллер — о авторе. Бизнесмен, инвестор, финансовый консультант Facebook |
inask.ru