Производство стали: способы, технология и сырье
Сталь – это прочный материал и основной конструкционный материал для машиностроения. Он представляет сплав железа с углеродом, содержание которого в структуре составляет 0,01–2,14%. В состав также входят в незначительных количествах кремний, марганец и сера. Этот материал обладает исключительными механическими свойствами: твердостью и ковкостью, благодаря им он считается основным конструкционным материалом в машиностроении. Трудно представить, что могло бы заменить материал. Но активное развитие производство стали и других металлов. Из стали изготавливаются самые разнообразные изделия – от канцелярских скрепок до станин многотонных прессов и обшивки корпусов морских судов.
Содержание
- Процесс производства
- Особенности процесса
- Особенности второго этапа
- Раскисление
- Мартеновский способ
- Конвертерный метод
- Особенности процесса
- Кислородно-конвертерный способ получения стали
- Электросталеплавильный способ
- Особенности электроиндукционных печей
- Виды получаемых сталей по химическому составу
Процесс производства
Производится сталь плавкой. Исходным сырьем служат чугун, лом самой стали или чугуна, окатыши, флюсы и ферросплавы.
Сам чугун по природе – недостаточно твердый и хрупкий материал, поэтому имеет ограниченное применение.
Однако, он незаменим в качестве сырья для получения стали. Суть плавки состоит, в случае применения передельного чугуна, в снижении процентного содержания углерода в нем до требуемого уровня.
Выводятся не предусмотренные в конечной рецептуре примеси. Традиционный состав шихты представляет 55% чугуна и 45% стального лома (скрапа). Существует также рудный процесс, когда к компонентам добавляется рудный материал или скрап-процесс для переработки отходов машиностроительного производства.
Чтобы в процессе плавки примеси и углерод легче выводился из состава компонентов, они переводятся в газы и шлак. В первую очередь при взаимодействии чугуна с кислородом железо окисляется, образуя закись железа FeO.
Одновременно окисляются C, Si, Mn и P, при этом происходит отдача кислорода оксидом железа химически активным примесям. К массе шихты добавляют флюс для лучшего растворения металла: известняк или известь, боксит. В качестве топлива используют каменноугольную пыль, жидкий мазут, природный или коксовый газ.
Особенности процесса
Процесс производства стали происходит последовательно в три этапа.
Первый этап – расплавление породы. На этапе его проведения формируется расплав в ванне и окисляется металл, отдавая одновременно кислород кремнию, фосфору и марганцу.
Одна и главных задач этого этапа – удаление фосфора. Для ее осуществления требуется сравнительно невысокая температура и присутствие в достаточном количестве FeO. При взаимодействии ингредиентов фосфорный ангидрид образует с оксидом железа нестойкое соединение (FeO)3 + P2O5.
Присутствие в шлаке более стойкого основания СаО вызывает замещение FeO. В результате оно связывает фосфорный ангидрит в другое соединение (CaO)4 х P2O5 + 4 Fe, чего и требовалось добиться.
Чистый Fe высвободился в расплаве, а фосфор образовал шлак, который удаляется с зеркала металла и утилизируется за ненадобностью. Поскольку фосфорный ангидрид преобразует состав шлака, процесс должен идти непрерывно.
Поэтому FeO должен непрерывно пополняться за счет загрузки новых партий железной руды и окалины, наводящих в расплаве железистый шлак.
Особенности второго этапа
Технология производства стали на втором этапе называется кипением стали. Основное назначение заключается в процентном снижении содержания углерода за счет окисления. FeO + C = CO + Fe.
Реакция окисления происходит более интенсивно при кипении и сопровождается поглощением тепла. Поэтому необходимо создавать постоянный приток тепла в ванну, а также для выравнивания температуры в расплаве.
При такой реакции окисления интенсивно выделяется газ оксида углерода CO, что вызывает бурное кипение в жидком агрегатном состоянии, по этой причине процесс называют кипением. Чтобы излишки углерода интенсивнее преобразовывались в окись, производство качественной стали предусматривает вдувание чистого кислорода и добавление в расплавленную структуру окалины. Поэтому таким важным является качество сырья для производства стали. Все исходные материалы проходят щепетильную проверку.
Немаловажным на этом этапе является вывод серы, благодаря чему повышается качество конечной стали. Используемая в компонентах сера, присутствует не в прямом виде, а в форме сульфида железа FeS.
При высоких температурах компонент также взаимодействует с оксидом СаО, образуя сульфид кальция CaS, который растворяется в шлаке, не соединяясь с железом. Это позволяет беспрепятственно выводить сульфид за пределы ванны.
Раскисление
Третий этап – раскисление металла. После добавления кислорода (на предыдущем этапе) требуется снизить его содержание в чистой стали. Использованием О2 удалось добиться окисления примесей, но его остаточное присутствие в конечном продукте снижает качественные характеристики металла. Требуется удалить или преобразовать окислы FeO, связав кислород с другими металлами.
Для этого существуют два метода раскисления:
- диффузионное;
- осаждающее.
При диффузионном методе в расплавленный состав вводят добавки: алюминий, ферромарганец и ферросилиций. Они восстанавливают оксид железа и переводит в шлак. В шлаке оксид распадается и высвобождает чистое железо, которое поступает в расплав. Второй высвободившийся элемент – кислород улетучивается в окружающую среду.
Осаждающий метод предусматривает введение добавок, имеющих большее сродство с кислородом, чем Fe. Происходит замещение этими веществами железа в окисле. Они, как менее плотные, всплывают и выводятся вместе со шлаком.
Процесс раскисления продолжается при затвердевании слитка, в кристаллической структуре которого оксид железа и углерод взаимодействуют. В результате чего вместе с пузырьками азота, водорода он выводится.
Чем больше при раскислении выводится включений различных металлов, тем выше ковкость получаемой стали. Для проверки раскаленный кусок металла подвергают ковке, на нем не должны образовываться трещины. Такая проверка пробы говорит о правильном проведении процесса раскисления.
В зависимости от степени раскисления специалисты могут получить:
- спокойную сталь полного раскисления;
- кипящую раскисленную не полностью сталь, когда процесс выведения пузырьков угарного газа СО продолжается в ковше и изложнице.
Для получения легированных сталей с добавками некоторых металлов в расплавленный металл добавляются ферросплавы или чистые металлы. Если они не окисляются (Ni, Co, Mo), то такие добавки могут вводиться на любом этапе плавки. Более чувствительные к окислению металлы Si, Mn, Cr, Ti добавляют в ковш или, что обычно и происходит, в форму для отливки металла.
Существуют основные способы получения стали в сталеплавлении.
Мартеновский способ
Этот способ применяется для производства сталей высокого качества, применяемых в особо ответственных деталях машинах и точных механизмах.
В свое время он заменил трудоемкие и малопроизводительные тигельную и пулдинговую плавки, применявшиеся ранее.
Емкость загрузки одной отражательной печи, используемой при этом методе, достигает 500 тонн. Особенностью мартеновского способа является возможность переплавки не только передельного чугуна, но и металлургических отходов, металлического лома.
Температура нагрева жидкой стали достигает 2 тыс. градусов. Этот результат достигается специальной конструкцией мартеновской печи:
- применением дополнительного тепла регенераторов, получаемого сжиганием коксовального или доменного газа в струе горячего воздуха;
- отражения от свода закачиваемого газа в результате сгорание топлива в нем происходит над ванной с металлом, что способствует быстрому нагреву содержимого;
- применением реверсирования нагревающего потока.
Мартеновская печь состоит из следующих элементов:
- рабочего пространства с огнеупорной футеровкой стенок и завалочными окнами;
- подины (основания) из магнезитового кирпича;
- свода печи;
- головки печи;
- шлаковика для выведения пыли;
- регенератора с перекидными клапанами.
Процесс плавки занимает от 4 до 12 часов. С целью ускорения процесса плавки объем закачиваемого кислорода превышает потребности, что повышает производительность плавки на 20–30%.
Конвертерный метод
В конверторах выплавляют сорта стали для производства автомобильного листа, инструментальной стали сварных конструкций и других стальных заготовок. По качеству они уступают мартеновскими применяются для изготовления менее ответственных изделий.
В них содержится больше примесей, чем при мартеновском изготовлении. Благодаря высокому объему загрузки одной печи до 900 тонн, способ считается самым производительным, поэтому получил широкое распространение.
Производство стали и другого вида металла этим методом основано на продувке жидкого чугуна воздухом или кислородом под давлением 0,3–0,35 МПа, при этом металл разогревается до 1600 градусов. Плавка скоротечна и длится до 20 минут. За это время происходит окисление углерода, кремния и марганца, содержащихся в сырье, которые извлекаются из ванны с расплавом шлака.
Конвертер представляет сосуд ретортообразной (грушевидной) формы, состоящий из стальных листов с футеровкой изнутри. Для заливки чугуна и выпуска готовой стали используется одно отверстие, в него также загружается чугун и скрап.
Особенности процесса
Вместе с ними загружаются шлакообразующие вещества: известь и бокситы. Корпус охвачен опорным кольцом, прикрепленным к поворотным цапфам. С их помощью сосуд наклоняется и через это отверстие – летку выливается готовая сталь. Нижняя продувка осуществляется через сквозные отверстия (фурмы), сделанные в днище печи.
Исторически повелось, что используемый везде способ называется томасовским, бессемеровским. В прошлом веке преобладающим стал мартеновский процесс. Нагрев регенератора осуществляется продувкой печных газов, после чего он нагревается холодный воздух, поступающий на расплав.
В современных конструкциях чаще применяют верхний способ, при котором продувка на огромной скорости осуществляется через опускаемые к поверхности металла сопла. В России преимущественно используется именно верхняя продувка печей.
Находясь под струей воздуха, чугун интенсивно окисляется в зоне контакта. Поскольку его концентрация значительно больше других примесей, преимущественно образуется оксид железа. Но он растворяется в шлаке. Поэтому металл обогащается выделяемым кислородом.
Окисляются C, Cr и Mn, снижая процентное содержание в структуре металла. Окисление сопровождается выделением тепла. Благодаря присутствию шлаков СаО и FeO до разогрева происходит выведение фосфора в самом начале продувки.
Шлак с ним сливается и наводится новый. Производство стали сопровождается экспресс-анализами и контролем текущих изменений приборами контроля, вмонтированных в печь. Содержание фосфора в чугуне не должно превышать 0,075%.
Кислородно-конвертерный способ получения стали
Производство стали сегодня осуществляется в основном этим способом. На долю кислородно-конверторного производства совсем недавно приходилось до 60% мирового производства стали.
Однако, этот процент снижается в связи с появлением электродуговых печей (ЭДП). Продувка печей осуществляется чистым кислородом (99,5%) под высоким давлением.
Продукт кислородно-конвертерной печи представляет сталь с заданными химическими свойствами. Она поступает в машину непрерывного литья заготовок (МНЛЗ), где материал застывает в форме блюма или плиты. Для получения определенных жестких параметров металл подвергается вторичной переработке.
Электросталеплавильный способ
Производство стали электрической плавкой обладает рядом неоспоримых преимуществ. Этот способ считается основным при выплавке высококачественных легированных сталей.
Достигаемая при этом высокая температура позволяет выплавлять стали, содержащие тугоплавкие металлы:
- молибден;
- вольфрам;
- ванадий.
Высокое качество достигается практическим отсутствием в сталях фосфора, серы и кислорода. Этот способ также применяется для производства широкой номенклатуры строительных сталей.
Выделение тепла не связано с потреблением окислителя, а происходит в результате преобразования электрической энергии в тепловую. Она выделяется при прохождении электрической дуги или наведения вихревых токов. В зависимости от принципа работы печи подразделяются на электродуговые и индукционные.
Электродуговая печь способна принять одновременно от 3,5 до 270 тонн сырья:
- жидкой стали из конвертеров;
- скрапа;
- железной руды.
Она имеет несколько электродов из графитосодержащего материала, к которым подводится электрическое напряжение. Время плавки составляет до 1,5 часа, при этом температура дуги достигает 6 тыс. градусов.
Особенности электроиндукционных печей
В электроиндукционных печах сталь выплавляют в небольших по объему (4,5–60 тонн) емкостях, именуемых огнеупорными тиглями. Вокруг тигля располагается индуктор, состоящий из большого количества витков провода.
При прохождении переменного тока внутри индуцируются вихревые токи большой силы, вызывающее плавление содержимого тигля. Электромагнитные силы одновременно перемешивают расплав стали. Продолжительность плавки в таких печах не превышает 45 мин.
Электросталеплавильный способ производит мало дыма, пыли и меньше излучает световой энергии. Однако, высокая стоимость электрооборудования при малой вместительности ограничивает применение этого способа.
Схема электросталеплавильной печи
Помимо рассмотренных вариантов, существуют не только основные способы производства стали. В современном сталеплавлении используется плавка в вакуумных индукционных печах и обогащение процентного содержания железа в окатышах плазменно-дуговым переплавом.
Виды получаемых сталей по химическому составу
Производимая этими методами сталь делится, в зависимости от химического состава, на две большие группы:
- углеродистую;
- легированную.
Процентное содержание элементов в углеродистой стали:
Наименование | Fe | С | Si | Mn | S | P |
Содержание в процентах | до 99,0 | 0,05–2,0 | 0,15–0,35 | 0,3–0,8 | до 0,06 | до 0,07 |
В углеродистых сталях прочность недостаточно сочетается с пластичностью. Недостаток устраняется введением добавок других металлов, такая сталь называется легированной.
Согласно ГОСТ 5200 выделяют три группы легированных сталей с допустимым содержанием примесей:
- низколегированная не более 2,5%;
- среднелегированная в диапазоне 2,5–10%;
- высоколегированная свыше 10%.
С каждым годом способы плавки усовершенствуются благодаря вводу в строй нового высокотехнологичного оборудования. Это позволяет получать в сталелитейной промышленности высококачественные стали с оптимальным содержанием добавок и металлов.
Видео по теме: Производство чугуна и стали
Производство стали
Самый часто используемый строительный материал в мире
Ежегодно производится около 1,1 млрд тонн стали, при этом данные цифры быстро растут. Данный удивительный материал можно найти везде: в многоэтажных зданиях, мостах, поездах, машинах и в используемых ежедневно предметах, таких как винты, бумажные скрепки, кастрюли и ножи.
Производство стали является «горячей» темой
Удивительными являются также различные технологии производства стали. Самым известным из них является процесс Линц-Донавиц (ЛД процесс), также известный как процесс производства стали с применением кислорода.
Жидкий чушковый чугун и металлолом подаются в ЛД конвертер и добавляется шлакообразователь для образования окалины. Кислород вдувается в сплав через фурму. При этом сгорают вредные для стали элементы, такие как сера, фосфор и углерод, которые превращаются в газ или окалину. Лом плавится под воздействием большого количества жара.
Широко распространены также сталелитейные заводы с электросталеплавильными печами. Дуга от трех графитовых электродов направляется на расплавляемый материал и создает температуры до 3 500 °C, при которых происходит плавление. Процесс плавления занимает около 30–45 минут.
Типичным объемом партии для обоих способов является 100–150 т. Существуют также формы для стали объемом до 350 т.
Дальнейшая обработка: Нерафинированная сталь льется в разливочный ковш под конвертером/электрической печью. Такой ковш расположен на ковшовом челноке. После литья челнок перемещается из-под конвертера и передает материал крановым весам для транспортировки.
Технология пневматической транспортировки может использоваться для нагнетания углерода и угля в домны для снижения зависимости от металлургического кокса и снижения производственных затрат.
RotoFeed используется как волюметрический дозатор с приводом с регулируемой частотой вращения, а интеграция технологии взвешивания позволяет создать гравиметрическую систему, которая обеспечивает точное дозирование с погрешностью менее ±1% и коэффициентом загрузки 10:1.
Альтернативный процесс производства железа
Schenck Process работает с рядом признанных лидеров отрасли, среди которых Siemens VAI, POSCO и Hismelt, и поставляет им сырьевой материал и системы дозировки, которые сочетают в себе точность и надежность при производстве металла неизменно высокого качества.
Steel Plant Process Iron Blast Furnace
Steel Plant Process Mini Mill
Steel Plant Process Integrated Mill
Steel Plant Process Blast Furnace
Посетите нас
- YouTube
Загрузки
Щелкните мышью по флагу, чтобы загрузить файл на своем языкеСпециальный раздел / исследования
Schenck Process enabling an alternative iron making process
Pneumatic Conveying system for Pulverised Coal Injection into Blast Furnaces
Heavy News: SCHENCK Weighing Systems for teeming and ladle transfer cranes
Heavy News: Simple and Reliable Weighing Solution
Advanced in-process weighing systems for steel production: accurate and reliable by maintenance-free design
Карты технологических процессов
Steel Plant Process Iron Blast Furnace
Steel Plant Process Mini Mill
Steel Plant Process Integrated Mill
Steel Plant Process Blast Furnace
Брошюры
Компетентность в производстве стали
Pneumatic conveying for iron & steel and non-ferrous production plants
Соответствующие изделия
Производство стали | History of Western Civilization II
25.
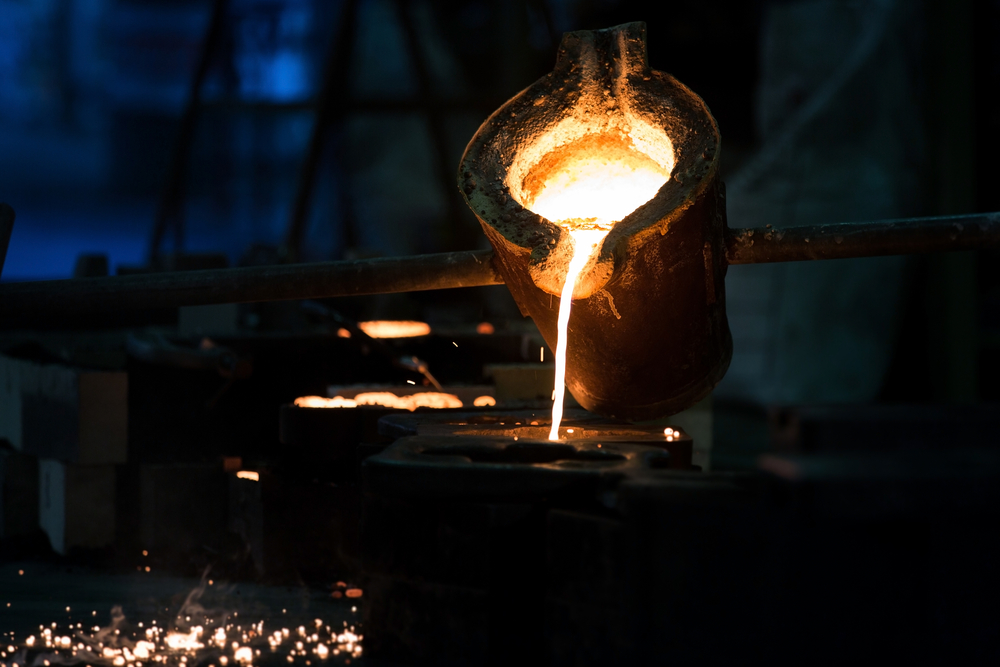
До 1860 года сталь была дорогой и производилась в небольших количествах, но разработка технологии производства тигельной стали Бенджамином Хантсманом в 1740-х годах, бессемеровский процесс в 1850-х годах и Процесс Сименса-Мартина в 1850–1860-х годах привел к массовому производству стали, что стало одним из ключевых достижений Второй промышленной революции.
Цель обучения
Постулировать влияние улучшения производства стали на развитие промышленности.
Ключевые моменты
- Сталь представляет собой сплав железа и других элементов, прежде всего углерода, который широко используется в строительстве и других областях благодаря своей высокой прочности на растяжение и низкой стоимости. Основным металлом стали является железо. Впервые он был произведен в древности, но за два десятилетия до промышленной революции производство стали, которое в то время было дорогим товаром, было усовершенствовано, и его использовали только там, где железо не годилось.
- Бенджамин Хантсман разработал свою технику изготовления тиглей в 1740-х годах. Он смог получить удовлетворительную стальную отливку в глиняных тиглях, каждый из которых вмещал около 34 фунтов блистерной стали. Был добавлен флюс, и они были покрыты и прогреты коксом в течение примерно трех часов. Затем расплавленную сталь заливали в формы, а тигли использовали повторно. Долгое время Хантсман экспортировал всю свою продукцию во Францию, так как местные производители отказывались работать со сталью более твердой, чем они уже использовали.
- Сталь часто называют первой из нескольких новых областей промышленного массового производства, характеризующих Вторую промышленную революцию. Примерно до 1860 года сталь все еще была дорогим продуктом. Проблема массового производства дешевой стали была решена в 1855 году Генри Бессемером с введением конвертера Бессемера на его сталелитейном заводе в Шеффилде, Англия. Дальнейшие эксперименты Горана Фредрика Йоранссона и Роберта Форестера Мушета позволили Бессемеру усовершенствовать то, что впоследствии стало известно как бессемеровский процесс.
- Хотя изначально Бессемер встретил отпор и был вынужден сам заняться эксплуатацией своего процесса, в конце концов лицензии были поданы в таком количестве, что Бессемер получил гонорары, превышающие миллион фунтов стерлингов. К 1870 году бессемеровская сталь широко использовалась для изготовления корабельных листов. Бессемеровский процесс также сделал стальные железные дороги конкурентоспособными по цене. Опыт быстро доказал, что сталь обладает гораздо большей прочностью и долговечностью и может выдерживать более тяжелые и быстрые двигатели и автомобили.
- После 1890 г. бессемеровский процесс постепенно вытесняется мартеновским. Карл Вильгельм Сименс разработал регенеративную печь Сименса в 1850-х годах. Эта печь работала при высокой температуре за счет использования регенеративного предварительного нагрева топлива и воздуха для горения. В 1865 году Пьер-Эмиль Мартен получил лицензию от Siemens и применил свою регенеративную печь для производства стали. Процесс Сименса-Мартина был медленнее, и поэтому его было легче контролировать.
Это также позволило плавить и очищать большое количество стального лома, еще больше снижая затраты на производство стали и перерабатывая другие неприятные отходы.
- К началу 20 века процесс Сименса-Мартина стал ведущим процессом производства стали. Доступность дешевой стали позволяла строить более крупные мосты, железные дороги, небоскребы и корабли. Другими важными стальными изделиями были стальной трос, стальной стержень и листовая сталь, которые позволяли создавать большие котлы высокого давления, а также высокопрочная сталь для машин. Военная техника также значительно улучшилась.
Ключевые термины
- Вторая промышленная революция
- Фаза быстрой индустриализации в последней трети 19 века и начале 20 века, также известная как технологическая революция. Хотя ряд его характерных событий можно отнести к более ранним инновациям в производстве, таким как создание станкостроения, разработка методов изготовления взаимозаменяемых деталей и изобретение бессемеровского процесса, обычно он датируется периодом между 1870 и 1914 г.
- Бессемеровский процесс
- Первый недорогой промышленный процесс массового производства стали из расплавленного чугуна до разработки мартеновской печи. Ключевым принципом является удаление примесей из железа путем окисления с воздухом, продуваемым через расплавленное железо. Окисление также повышает температуру массы железа и поддерживает ее в расплавленном состоянии.
- стальной тигель
- Термин, который применяется к стали, изготовленной двумя разными способами в современную эпоху и произведенной в разных местах на протяжении всей истории. Его изготавливают путем плавления железа и других материалов. Он производился в Южной и Центральной Азии в эпоху средневековья, но методы производства высококачественной стали были разработаны Бенджамином Хантсманом в Англии в 18 веке. Однако в процессе Хантсмана в качестве сырья использовались железо и сталь, а не прямое преобразование из чугуна , как в более позднем бессемеровском процессе.
Однородная кристаллическая структура этой литой стали улучшила ее прочность и твердость по сравнению с предыдущими формами стали.
- цементация
- Устаревшая технология производства стали путем науглероживания железа. В отличие от современного производства стали, это увеличило количество углерода в железе. По-видимому, он был разработан до 17 века. Сталелитейная печь Derwentcote, построенная в 1720 году, является самым ранним сохранившимся примером печи, использующей эту технологию.
- науглероживание
- Процесс термообработки, при котором железо или сталь поглощают углерод, в то время как металл нагревается в присутствии углеродсодержащего материала, такого как древесный уголь или монооксид углерода. Цель состоит в том, чтобы сделать металл более твердым. В отличие от современного производства стали, этот процесс увеличил количество углерода в железе.
Сталь представляет собой сплав железа и других элементов, прежде всего углерода, который широко используется в строительстве и других областях благодаря своей высокой прочности на растяжение и низкой стоимости. Основным металлом стали является железо, которое может принимать две кристаллические формы: объемно-центрированную кубическую (ОЦК) и гранецентрированную кубическую (ГЦК), в зависимости от температуры. Именно взаимодействие этих аллотропов с легирующими элементами, прежде всего с углеродом, придает стали и чугуну ряд уникальных свойств. В схеме BCC атом железа находится в центре каждого куба, а в схеме FCC — по одному в центре каждой из шести граней куба. Углерод, другие элементы и включения в железе действуют как упрочняющие агенты, препятствующие движению дислокаций, которые в противном случае возникают в кристаллических решетках атомов железа.
Сталь (с более низким содержанием углерода, чем у чугуна, но выше, чем у кованого железа) была впервые произведена в древности, но за два десятилетия до промышленной революции производство стали, которая в то время была дорогим товаром, было усовершенствовано. там, где железо не годится, например, для передовых инструментов и пружин. Бенджамин Хантсман разработал свою технику изготовления тиглей в 1740-х годах. После многих экспериментов Хантсман смог изготовить удовлетворительную стальную отливку в глиняных тиглях, каждый из которых вмещал около 34 фунтов блистерной стали. Был добавлен флюс, и они были покрыты и прогреты коксом в течение примерно трех часов. Затем расплавленную сталь заливали в формы, а тигли использовали повторно. Местные производители столовых приборов отказались покупать литейную сталь Huntsman, так как она была тверже, чем немецкая сталь, которую они привыкли использовать. Долгое время Хантсман экспортировал всю свою продукцию во Францию. Блистерная сталь, используемая Huntsman в качестве сырья, была изготовлена процессом цементации или науглероживания железа. Науглероживание – это процесс термической обработки, при котором железо или сталь поглощают углерод, в то время как металл нагревается в присутствии углеродсодержащего материала, такого как древесный уголь или монооксид углерода. Цель состоит в том, чтобы сделать металл более твердым. В отличие от современного производства стали, этот процесс увеличил количество углерода в железе.
Сталь часто называют первой из нескольких новых областей промышленного массового производства, которые характеризуют Вторую промышленную революцию, начавшуюся примерно в 1850 году, хотя метод массового производства стали не был изобретен до 1860-х годов и стал широко доступным в 1870-е годы после того, как процесс был изменен для обеспечения более однородного качества.
Примерно до 1860 года сталь была дорогим продуктом, производилась в небольших количествах и использовалась в основном для изготовления мечей, инструментов и столовых приборов. Все крупные металлические конструкции изготавливались из кованого или чугунного литья. Проблема массового производства дешевой стали была решена в 1855 году Генри Бессемером с введением конвертера Бессемера на его сталелитейном заводе в Шеффилде, Англия. В бессемеровском процессе расплавленный чугун из доменной печи загружали в большой тигель, а снизу через расплавленное железо продували воздух, воспламеняя растворенный углерод кокса. По мере выгорания углерода температура плавления смеси повышалась, но тепло от горящего углерода обеспечивало дополнительную энергию, необходимую для поддержания смеси в расплавленном состоянии. После снижения содержания углерода в расплаве до заданного уровня тягу воздуха отключали. Типичный бессемеровский конвертер мог преобразовать 25-тонную партию чугуна в сталь за полчаса. Бессемер продемонстрировал этот процесс в 1856 году, и к 1864 году операция прошла успешно.
Преобразователь Бессемера, печатное издание, изданное в 1867 году в Великобритании.
Хотя бессемеровский процесс больше не используется в коммерческих целях, во время его изобретения он имел огромное промышленное значение, поскольку снижал стоимость производства стали, что привело к широкой замене чугуна сталью. Внимание Бессемера было привлечено к проблеме стали. производство в попытке улучшить конструкцию орудий. Бессемер передал лицензию на свой процесс пяти производителям железа, но с самого начала у компаний были большие трудности с производством стали хорошего качества. Йоран Фредрик Йоранссон, шведский мастер по производству чугуна, используя более чистый чугун из древесного угля из этой страны, был первым, кто сделал хорошую сталь с помощью этого процесса, но только после многих попыток. Его результаты побудили Бессемера попробовать более чистое железо, полученное из камберлендского гематита, но имели лишь ограниченный успех, потому что количество углерода было трудно контролировать. Роберт Форестер Мушет после тысяч экспериментов на металлургическом заводе Даркхилл показал, что количество углерода можно контролировать, удаляя почти весь его из железа, а затем добавляя точное количество углерода и марганца в виде шпигелейзена (ферромарганцевого сплава). ). Это улучшило качество готового продукта и повысило его пластичность.
Когда Бессемер попытался убедить производителей использовать его усовершенствованную систему, он столкнулся с общим отпором и, в конце концов, был вынужден сам заняться эксплуатацией процесса. Он построил сталелитейный завод в Шеффилде в рамках делового партнерства с другими компаниями, такими как W & J Galloway & Sons, и начал производство стали. Сначала выпуск был незначительным, но постепенно масштабы операции увеличивались до тех пор, пока конкуренция не стала эффективной, и торговцы сталью не осознали, что фирма Генри Бессемера и Ко занижает их продажи на 10–15 фунтов стерлингов за тонну. . Этот довод в пользу кармана быстро подействовал, и лицензии были поданы в таком количестве, что в качестве гонораров за использование его процесса Бессемер получил сумму, значительно превышающую миллион фунтов стерлингов. К 1870 году бессемеровская сталь широко использовалась для изготовления корабельных листов. К 1850-м годам скорость, вес и количество железнодорожных перевозок ограничивались прочностью используемых рельсов из кованого железа. Решением стало использование стальных рельсов, которые благодаря бессемеровскому процессу стали конкурентоспособными по цене. Опыт быстро доказал, что сталь обладает гораздо большей прочностью и долговечностью и может выдерживать более тяжелые и быстрые двигатели и автомобили.
Однако Мушет ничего не получил и к 1866 году был нищим и больным. В том же году его 16-летняя дочь Мэри поехала в Лондон одна, чтобы встретиться с Бессемером в его офисе, утверждая, что его успех был основан на результатах работы ее отца. Бессемер решил выплачивать Мушету ежегодную пенсию в размере 300 фунтов стерлингов, очень значительную сумму, которую он делал более 20 лет, возможно, чтобы удержать Мушетов от судебного иска.
После 1890 года бессемеровский процесс постепенно вытесняется мартеновским производством стали. Сэр Карл Вильгельм Сименс разработал регенеративную печь Siemens в 1850-х годах и заявил в 1857 году, что она рекуперирует достаточно тепла, чтобы сэкономить 70–80% топлива. Эта печь работала при высокой температуре за счет использования регенеративного предварительного нагрева топлива и воздуха для горения. При регенеративном предварительном нагреве выхлопные газы из печи перекачиваются в камеру, содержащую кирпичи, где тепло от газов передается кирпичам. Затем поток печи меняется на противоположный, так что топливо и воздух проходят через камеру и нагреваются кирпичами. С помощью этого метода мартеновская печь может достигать температур, достаточно высоких для плавки стали, но Siemens изначально не использовал ее для этого. В 1865 году французский инженер Пьер-Эмиль Мартен получил лицензию от Siemens и впервые применил свою регенеративную печь для производства стали. Наиболее привлекательной характеристикой регенеративной печи Siemens является быстрое производство большого количества основной стали, используемой, например, для строительства высотных зданий.
Печь Сименс с 1895 года
Наиболее привлекательной характеристикой регенеративной печи Siemens было быстрое производство большого количества стали, используемой, например, для строительства высотных зданий. С помощью метода Сименса мартеновская печь могла достигать температур, достаточно высоких для плавки стали, но изначально Сименс не использовал ее для этого. Именно Мартин первым применил регенеративную печь для производства стали. Процесс Сименса-Мартина дополнил, а не заменил бессемеровский процесс. Он был медленнее и, следовательно, его было легче контролировать. Это также позволило плавить и очищать большое количество стального лома, еще больше снижая затраты на производство стали и перерабатывая другие неприятные отходы. Худшим его недостатком было и остается то, что плавление и рафинирование шихты занимает несколько часов. Кроме того, рабочая среда вокруг мартеновской печи была и остается чрезвычайно опасной.
Процесс Сименса-Мартина стал ведущим процессом производства стали к началу 20 века. Доступность дешевой стали позволяла строить более крупные мосты, железные дороги, небоскребы и корабли. Другими важными стальными изделиями, также изготовленными с использованием мартеновского процесса, были стальной трос, стальной стержень и листовая сталь, которые позволили использовать большие котлы высокого давления, и высокопрочная сталь для машин, что позволило создать гораздо более мощные двигатели, шестерни и оси. чем это было возможно ранее. С большим количеством стали также стало возможным строить гораздо более мощные орудия и лафеты, танки, боевые бронированные машины и военные корабли.
Должности
- Производство стали
«Науглероживание». https://en.wikipedia.org/wiki/Науглероживание. Википедия CC BY-SA 3.0.
«Промышленная революция». https://en.wikipedia.org/wiki/Industrial_Revolution. Википедия CC BY-SA 3.0.
«Вторая промышленная революция». https://en.wikipedia.org/wiki/Вторая_промышленная_революция. Википедия CC BY-SA 3.0.
«Бенджамин Хантсман». https://en.wikipedia.org/wiki/Бенджамин_Хантсман. Википедия CC BY-SA 3.0.
«Тигельная сталь». https://en.wikipedia.org/wiki/Crucible_steel. Википедия CC BY-SA 3.0.
«Мартеновская печь». https://en.wikipedia.org/wiki/Open_hearth_furnace. Википедия CC BY-SA 3.0.
«Черная металлургия». https://en.wikipedia.org/wiki/Черная металлургия. Википедия CC BY-SA 3.0.
«История черной металлургии (1850–1970 гг.)». https://en.wikipedia.org/wiki/History_of_the_steel_industry_(1850%E2%80%931970).
Википедия CC BY-SA 3.0.
«Процесс цементации». https://en.wikipedia.org/wiki/Cementation_process. Википедия CC BY-SA 3.0.
«Шпигелейзен». https://en.wikipedia.org/wiki/Шпигелейзен. Википедия CC BY-SA 3.0.
«Бессемеровский процесс». https://en.wikipedia.org/wiki/Бессемер_процесс. Википедия CC BY-SA 3.0.
«Генри Бессемер». https://en.wikipedia.org/wiki/Генри_Бессемер. Википедия CC BY-SA 3.0.
«Сталь». https://en.wikipedia.org/wiki/Сталь. Википедия CC BY-SA 3.0.
«Отражательная печь». https://en.wikipedia.org/wiki/Reverberatory_furnace. Википедия CC BY-SA 3.0.
«КонвертерB.jpg». https://commons.wikimedia.org/wiki/Файл:ConverterB.jpg. Общественное достояние Викисклада.
«Siemensmartin12nb.jpg». https://commons.wikimedia.org/wiki/Файл:Siemensmartin12nb.jpg. Общественное достояние Викисклада.
Производство зеленой стали: как страны Большой семерки могут помочь изменить глобальный ландшафт
Гонка продолжается, но не все могут принять в ней участие. Существуют серьезные различия в доступе к финансам, технологиям, навыкам и политическим обязательствам, особенно в странах с развивающейся экономикой. Амбициозные проекты в таких странах, как Европа и Южная Корея, получают общественную поддержку и подкрепляются твердыми национальными обязательствами в той мере, в какой политики планируют создать законодательные рамки для управления переходными процессами. В то же время существует риск того, что компании, работающие в других регионах, останутся позади. Это ставит под угрозу глобальные климатические амбиции, поскольку наносит ущерб усилиям компаний по созданию цепочек создания стоимости экологически чистой стали, охватывающих весь мир.
Необходимость более тесной координации и международного сотрудничества при переходе отрасли является не чем иным, как критической. Только совместными усилиями мир может свести промышленные выбросы к нулю.
Декарбонизация отрасли набирает небывалые обороты, но не везде. Хотя все государства G7 (Канада, Франция, Германия, Италия, Япония, Великобритания и США) и ЕС объявили о своих обязательствах по климатической нейтральности на период до 2050 года, их усилия в настоящее время направлены на национальный и региональный контекст. Объединение усилий может вывести промышленную декарбонизацию в центр внимания международной политики. Как показал Tracker, инвестиции и инновации в обезуглероживание стали, скорее всего, будут осуществляться в юрисдикциях или на рынках с надежной политической средой. Последнее коммюнике «Большой семерки» по энергетике и климату закладывает основу для новой программы промышленной политики, но за этим должны последовать действия. Поскольку главы государств и правительств собираются на саммит лидеров G7 2021 года, им необходимо сигнализировать о поддержке этой программы на высшем уровне со стороны правительства.
Правительства стран «большой семерки» могут сделать свой вклад в промышленную декарбонизацию с помощью следующих мер:
- Скоординированная политика по созданию рынков экологически чистой стали. Рынок экологически чистых промышленных товаров все еще находится на ранней стадии развития. Политика со стороны спроса должна быть введена в действие сейчас.
Но они требуют согласованных сигналов и согласованных процедур в наших глобальных цепочках поставок. Им нужны стандартизированные комплексные методы расчета для отчетности об интенсивности выбросов. Чтобы сделать эти расчеты, исследователям потребуется сбор прозрачных данных о технологиях замены футеровки доменных печей, использовании топлива, загрузке мощностей и т. д. Только тогда можно будет правильно сравнить и понять воздействие продукции на окружающую среду.
- Думайте в глобальном масштабе, поскольку сырая сталь продается на международном уровне. По потреблению стали страны G7 занимают второе место после Индии и Китая. Опираясь на существующие корпоративные, национальные и международные усилия по установлению стандартов «зеленых» закупок, страны «Большой семерки» должны взять на себя обязательство работать вместе над разработкой согласованных требований к продукции и критериев для «зеленой» стали, а затем связать их с амбициозными целями государственных и частных закупок.
Министерская инициатива по глубокой промышленной декарбонизации чистой энергии (IDDI) ищет 10 национальных правительств, которые в течение следующих трех лет примут на себя обязательства по экологически чистой политике государственных закупок стали, при этом первый набор национальных обязательств будет объявлен на COP26. Страны G7 должны присоединиться к этой инициативе и заявить о своей поддержке. Совместный подход к созданию политической основы, укрепляющей рынки «зеленой» стали со стороны «Большой семерки» и связанных с ней экономических зон, послужит сильным сигналом и задаст четкое направление для глобального сталелитейного сектора. В основе этого процесса лежит необходимость разработки прозрачной, научно обоснованной методологии оценки и отчетности по интенсивности выбросов при производстве стали.
- Координация усилий по объединению и увеличению инвестиций в исследования, разработки и развертывание. Технологии обезуглероживания сталелитейного сектора доступны, поэтому наиболее неотложной задачей перехода является демонстрация и развертывание, а не фундаментальные исследования.
Green Steel Tracker также показывает, как много стран и компаний идут по тому же пути, сосредоточившись на производстве стали на основе водорода. С преобладающим направлением декарбонизации страны G7 имеют очевидные основания для объединения и совместного использования ресурсов, чтобы снизить затраты на разработку этих технологий и обеспечить распространение более чистых технологий на международном уровне. Страны G7 должны взять на себя обязательство поддержать эту инициативу и поставить перед собой амбициозные цели по инвестированию в коммерческие демонстрационные проекты и выход на рынок. Кроме того, странам Большой семерки следует инвестировать в экономику замкнутого цикла и инновации со стороны спроса, такие как меры по обеззараживанию стального лома и инновации для уменьшения чрезмерного проектирования. Такие инновации имеют решающее значение для сведения выбросов в этом секторе к нулю.
- Включить переходное финансирование. Для обезуглероживания секторов тяжелой промышленности были выделены ограниченные климатические и государственные финансы.