Технология производства асфальтобетона | ООО «СДМ»
Одним из перспективных направлений деятельности в РФ является производство асфальтобетона, который используют для обустройства покрытия автомобильных дорог различного назначения. Асфальтобетон представляет собой строительный материал, который получают вследствие затвердевания смеси минеральных веществ с битумом. Технология получения асфальтобетона включает большой набор обязательных компонентов:
- Песок. Обеспечивает создание мелкозернистой основы, которая выполняет функции наполнителя мелких полостей и способствует распределению механического давления от поверхности дороги к грунту.
- Щебень. Создает требуемый уровень механической прочности, что является одной из главных характеристик асфальтобетонной смеси.
- Минеральные наполнители. В качестве этих компонентов используют измельченную горную породу (известняк, мел, песчаник). Эти наполнители позволяют асфальтобетонной смеси заполнять остаточные пустоты и значительно снижают себестоимость её производства.
- Битум. Является жидким связующим, которое склеивает все компоненты в единую монолитную смесь.
- Резина. Этот компонент вводится в виде измельченной крошки и предназначен для придания готовому асфальту высокой степени упругости, стойкости к воздействию влаги. Стоимость резины значительно увеличивает стоимость асфальта, поэтому её используют только для самых ответственных участков дороги с повышенной механической нагрузкой.
Правильное пропорциональное распределение всех этих компонентов позволяет получить асфальт, который будет обладать всеми необходимыми эксплуатационными параметрами.
Особенности производства асфальтобетона
Процесс производства асфальтобетона может выполняться при различных температурных режимах, что служит критерием для классификации асфальтной смеси на три различных категории:
- Холодные. Асфальтобетонный материал этого типа изготавливают с добавлением жидкого битума. Допускается длительное хранение и использование этой смеси при температуре не ниже +50С.
- Теплые. Асфальт этого типа изготавливают из жидкого битума и вязких связующих, поэтому температура их хранения должна составлять не менее 1000С.
- Горячие. Асфальтобетонная смесь изготавливается и укладывается при температуре не ниже 1200С.
В зависимости от фракции, используемых для изготовления асфальта компонентов, он подразделяется на три основных вида:
- Крупнозернистый. Данный материал отменно подходит для выполнения дорожного покрытия в нижних его слоях. Одним из основных компонентов этой смеси является щебень крупной и мелкой фракции.
- Мелкозернистый. Асфальтобетон этого типа применяют для обустройства верхнего покрытия у дорог общего пользования. В его состав входит щебень мелкой фракции, который может достигать величины 15 мм.
- Песчаный. Этот тип асфальта применяют для обустройства пешеходных дорожек и тротуаров. В состав этой асфальтной смеси вводят большое количество песка, битума и щебня с фракцией до 5,0 мм.
Технология изготовления смеси
Технология производства асфальтобетона состоит из нескольких основных этапов, которые включают все необходимые операции и работы:
- Входной контроль исходного сырья: минеральные добавки, битум, щебень, песок.
- Обработка инертных материалов: просеивание песка, разделение щебня по фракциям, разогрев битума.
- Доведение всех компонентов до требуемого уровня влажности и температуры нагрева.
- Перемешивание между собой всех составных компонентов асфальтобетонной смеси, что обеспечивает сцепление битума с песком, зернами щебня и минеральным наполнителем.
- Хранение готового асфальта в специальном бункере, где происходит поддержание требуемого температурного режима.
Забор готового продукта происходит непосредственно из бункера хранения, после чего его доставляют до места укладки с соблюдением всех технологических требований. Подобная технология изготовления асфальтобетона используется практически на всех отечественных заводах. Некоторые производители вводят в состав асфальта каучуковую крошку или латекс, что направлено на получение смеси с высокой степенью упругости.
Типы оборудования для производства
Оборудование для производства асфальтобетона в зависимости от технологических особенностей подразделяют на заводы непрерывного и циклического действия:
- Технологическая схема производства асфальтобетона на оборудовании непрерывного действия характеризуется отсутствием башни и грохота, которые необходимы для качественной сортировки исходного сырья.
Все ингредиенты непрерывно подают в приемные бункеры, после чего они доводятся до требуемого состояния готовности к перемешиванию. Отсутствие грохота делает возможным случаи попадания в готовую асфальтобетонную смесь щебня некондиционных размеров или посторонних включения. Основное преимущество подобных заводов – компактные размеры и высокая степень мобильности.
- Технология приготовления асфальтобетона на оборудовании циклического действия характеризуется наличием грохота и приемных башен. Благодаря этому вспомогательному оборудованию обеспечивается высокая степень подготовки исходного сырья еще до подачи в бункер для перемешивания. Асфальтный завод циклического действия располагают вблизи крупных городов, где регулярно есть потребность в небольшом объеме асфальтобетонной смеси. Главное преимущество подобных технологических схем: изменение рецептуры до нескольких раз в день, без ухудшения качества готового продукта, возможность готовить асфальт небольшими порциями, высокое качество подготовки сырья.
Главный недостаток подобных заводов – низкий уровень мобильности.
Приготовление асфальтобетона в заводских условиях требует наличия персонала соответствующего уровня квалификации, который будет уметь правильно снимать показания аппаратуры, знать все технологические особенности производства и быстро реагировать на отклонения от заданного технологического режима работы.
Щебень для асфальта ГОСТ Р 58406.2-2020
Российские дороги ждут инновационные решения – евроасфальт. С лета 2023 года исключается использование на дорогах общего пользования асфальтобетонных смесей, выпущенных по устаревшим ГОСТам.
Вместо классических покрытий автодорожным организациям предстоит использовать так называемый Супервейв (объемно-функциональное покрытие), в народе его окрестили «евроасфальтом»).
С 1 июля 2020 года действует ГОСТ Р 58406.2-2020 «Дороги автомобильные общего пользования. Смеси горячие асфальтобетонные и асфальтобетон. Технические условия».
Инновации родом из США
Разработали Супервейв в Соединенных штатах, где ученые преследовали цель создать составы с учетом чёткого попадания в климатические условия работы полотна и будущей транспортной нагрузки.
Superpave (от англ. Superior Performing Asphalt Pavements) – это инновационный метод разработки составов асфальтобетонов с максимальной эксплуатационной надежностью.
«Суперпейв» стал разработкой Стратегической программы исследования дорожного хозяйства (Strategic Highway Research Program). Данный продукт был разработан в США в 1992 году международными экспертами. Главный «козырь» таких асфальтобетонов – повышенный межремонтный срок эксплуатации. Это достигается за счёт повышения устойчивости дорожного полотна к следующим факторам:
- абразивный износ;
- остаточные деформации;
- механические повреждения;
- усталостные растрескивания;
- низкотемпературное трещинообразование.
Евроасфальт же имеет отличия от Супервейв – способ подбора смеси иной, но общий принцип и материалы аналогичны. Методика разработки таких асфальтобетонов на сегодняшний день самая инновационная. Сегодня при выборе асфальтовых покрытий учитывается только общая категория всей дороги в целом. Российские реалии зачастую показывают, что одна и та же дорога даже на небольшом участке может пересекать несколько климатических зон и переносить категорически различные нагрузки. Всё это требует индивидуального подхода к выбору материалов, особенно, для постройки дорог опорной сети и проектов БКАД. Например, новые покрытия будут использоваться для строительства трассы М-12 «Москва-Казань», на участки которой уже поставляются материалы производства «Уральский щебень».
Федеральные чиновники предполагают, что сроки службы новых дорожных покрытий должны продлиться в 2 раза – с нынешних 4-5 до 12 лет. А капитальный ремонт будет производиться и того реже – раз в 24 года.
Эта существенная экономия бюджетов и должна стать стимулом к повсеместному распространению новых асфальтобетонных смесей.
Столичные регионы перешли на Супервейв и Евроасфальт еще в 2020 году. Причина – рост транспортной нагрузки, активный трафик более 40 000 автомашин в сутки требует покрытий с минимальной просадкой. Для производства прогрессивных марок асфальта необходим щебень узких фракций.
Производство щебня для асфальта по ГОСТ Р 58406.2-2020
Постепенно АБЗ модернизируют оборудование, переходя на щебень по ГОСТ 32703-2014. Не смотря на увеличение стоимости (евроасфальты в среднем на 15% дороже традиционных), специалисты оптимистично смотря на производство по новым стандартам. Так как технологически производить Супервейв проще. Не все карьеры сегодня готовы обеспечить производство евро фракций щебня для АБЗ. Завод «Уральский щебень» работает модернизированное оборудование, которое с 2020 года выпускает узкие еврофракции для новых видов покрытий. Производство евро щебня 4-8 в Свердловской области также налажено на партёрском предприятии — карьере ООО «ТД «Уралдоломит».
Дорожные предприятия нуждаются в квадратных фракциях, которые имеют отличные от привычных размеры:
- щебень фракции 5,6-8 (кубовидный),
- щебень фракции 11,2-16 (кубовидный),
- щебень фракции 11,2-16 (кубовидный),
- щебень фракции 11,2-16,
- щебень фракции 45-63,
- щебень фракции 16-31,5,
- щебень фракции 5,6-8 (кубовидный),
- щебень фракции 8-11,2 (кубовидный),
- щебень фракции 11,2-16 (кубовидный),
- щебень фракции 16-22,4 (кубовидный).
При изготовлении асфальта Супервейв крайне важно попадание в рецептуру, так как колебания от породы к породе недопустимо. Плотные горные породы, такие как диориты, со стабильной объемной плотностью, как нельзя лучше адаптированы для совместной работы с битумом. Мы быстро доставим пробы щебня по запросу для оценки соответствия вашей рецептуре. Достаточно сделать запрос у менеджера по телефону +7 (343) 354-70-80.
Щебеночный карьер в п. Покровск-Уральский полностью готов обеспечить протребности отечественных застройщиков в евро-фракциях для Супервейв. При этом производственных мощностей (более 2 млн тонн в год) достаточно для того, чтобы не прекращать выпуск традиционных фракций ГОСТ 8267-93 20-40, 40-70 мм. Все варианты продукции для автодорожного строительства вы найдете на нашем сайте.
Щебень для асфальта: фракции и как выбрать
Щебень – один из основных компонентов асфальтобетона. От него зависят прочность и долговечность дорог. Кроме того, материал отвечает за то, насколько прочно шины автомобилей сцепляются с покрытием, а значит – и за безопасность трасс. Поэтому требования к щебню в этом случае предъявляются высокие.
В компании Грунтовозов вы можете купить щебень для асфальта с доставкой до вашего объекта по минимальной цене.
- Щебень для асфальта
- Как выбрать щебень для асфальта
- Вид
- Фракция
- Лещадность
- Адгезия
- Прочность
- Истираемость
- Морозостойкость
- Содержание зерен слабых пород
- Содержание пылевидных частиц и комков глины
- Водопоглощение
- Насыпная плотность
- Радиоактивность
- Какой щебень подойдет для асфальтобетона
- Какой щебень не подойдет для асфальтобетона
По процентному содержанию щебня асфальт делится на типы:
- А – 50-60%
- Б – 40-50%
- В – 30-40%
В усовершенствованном щебеночно-мастичном асфальтобетоне количество щебня повышено до 70-80%. Такое покрытие отличается высокой упругостью и устойчивостью к расслоению.
В следующей части статьи вы узнаете, на что следует ориентироваться при выборе материала.
Как выбрать щебень для асфальта
Поверхность асфальта должна выдерживать множество нагрузок. По ней ходят люди, проезжают тысячи автомобилей. Оказывают негативное влияние и атмосферные факторы – перепады температур, осадки. Поэтому для изготовления асфальтобетона следует выбирать особый щебень. Требования к нему достаточно высокие.
При выборе следует обратить внимание на следующие свойства щебня:
- Вид
- Фракцию
- Лещадность
- Адгезию
- Прочность
- Истираемость
- Морозостойкость
- Содержание зерен слабых пород
- Содержание пылевидных частиц и комков глины
- Водопоглощение
- Насыпную плотность
- Радиоактивность
Большинство характеристик регулируется ГОСТами 9128-2013 (для асфальтобетонных смесей) и 8267-93 (для щебня в строительных работах). Подробное описание каждого свойства с его нормативными показателями вы найдете ниже.
Вид
Для изготовления асфальтобетона рекомендуют брать щебень из пород магматического происхождения.
Среди них:
- Гранит
- Диорит
- Габбро
- Базальт
- Диабаз
- Сиенит
Они обладают достаточной прочностью, износоустойчивостью, высокой морозостойкостью и могут переносить большие нагрузки.
Неплохими характеристиками обладают некоторые метаморфические породы:
- Серпентинит
- Амфиболит
По прочности и морозостойкости они не уступают популярным граниту или габбро. Амфиболит может даже превосходить некоторые магматические разновидности. Его часто используют при изготовлении асфальта на взлетных полосах.
Щебень из осадочных пород (известняка, доломита, песчаника, брекчии) в дорожном строительстве используют редко. Но он широко применяется при изготовлении асфальта для дворов, пешеходных дорожек, тротуаров, дорог низких категорий. Ведь цена у этого продукта ниже. Но для ответственных работ следует выбирать разновидности с высокими показателями прочности и морозостойкости.
Фракция
Согласно ГОСТу, в состав асфальтобетона должны входить частицы с размерами 40 мм, 20 мм, 15 мм, 10 мм и 5 мм. Процентное соотношение частиц зависит от разновидности.
Оптимальный состав асфальта могут обеспечить следующие фракции щебня:
- 5-10
- 5-15
- 5-20
- 10-15
- 10-20
- 15-20
- 20-40
Среди перечисленных видов есть стандартные (5-10, 5-20, 10-20, 20-40) и нестандартные (5-15, 10-15, 15-20). С помощью нестандартных фракций можно лучше регулировать зерновой состав асфальтобетонной смеси. Но они есть не на всех предприятиях, так как для получения нужно иметь сита с определенным размером ячеек.
По зерновому составу асфальтобетон разделяют на:
- Асфальт с крупным щебнем (или крупнозернистый) с максимальным размером частиц 40 мм
Для его изготовления чаще всего используется фракция 20-40.Более мелкий щебень (5-10, 5-20, 10-20) добавляется для увеличения плотности.
- Асфальт с мелким щебнем (он же мелкозернистый, до 20 мм)
Основу составляют фракции 5-20 и 10-20. Также для улучшения зернового состава добавляют 5-15, 10-15, 15-20.
Крупнозернистые смеси используются для создания нижних слоев асфальтового покрытия. Они обеспечивают прочность и упругость. Сверху полотно заливают мелкозернистым асфальтобетоном, чтобы покрытие было ровным, а нагрузка одинаково распределялась по всей площади.
Лещадность
Оптимальная форма щебня для асфальта – кубическая и тетраэдрическая. Такие камни хорошо трамбуются и уплотняются. Но в процессе дробления породы могут образовываться игловидные и плоские частицы. Их называют лещадными.
Государственные стандарты строго прописывают, сколько этих зерен может быть в асфальтобетоне:
- До 15% для типа А (I и II группы по лещадности)
- До 25% для типа Б (III группа)
- До 35% для типа В (IV группа)
Чем меньше лещадность, тем плотнее и прочнее получается асфальт. Поэтому для автомагистралей с интенсивным трафиком рекомендуют брать материал первой группы. Для покрытия двора или дорожек вполне подойдет щебень со средней лещадностью. Он стоит дешевле.
Адгезия
Щебень хорошо сцепляется с поверхностью битума благодаря шероховатой поверхности и разницы электрических потенциалов камня и вяжущего вещества. Это свойство называют адгезией. У разных видов она может отличаться.
Для проверки образец обрабатывают битумом, а после высыхания опускают в кипящую воду на 30 минут. От щебня с хорошими адгезивными свойствами вяжущий компонент не отлипает. Если поверхность камня оголяется наполовину, адгезия считается удовлетворительной. Такой материал можно использовать для асфальтирования пешеходных зон, дорог с невысоким трафиком. Если битум отстает больше, чем на 50%, такой щебень для асфальта не годится.
Прочность
Щебень испытывается на прочность путем механического (раздавливающего) действия. Делают это в лаборатории. Для этого образец сжимают в цилиндре с определенной силой.
После этого определяют 2 параметра:
- Давление, которое необходимо приложить для разрушения зерен
- Потерю массы после отсеивания мелких частиц (марку по дробимости)
Прочность при сжатии магматических и метаморфических пород должна быть не меньше 100-120 МПа. Для осадочных допускаются цифры 80-100 МПа. Эти разновидности щебня используют для покрытий с меньшей нагрузкой. Кроме того, осадочные породы лучше сцепляются с битумом, что само по себе обеспечивает прочность асфальта.
Марку по дробимости выбирают в зависимости от вида асфальта:
- А – от М1200
- Б – от М1200 (для осадочных пород от М1000)
- Бх (холодный асфальт) – от М1000 (для осадочных – от М800)
- В – от М800 (для осадочных от М600)
Если взять щебень со слишком низкой маркой по дробимости, он быстро разрушится под давлением транспорта. На асфальте появятся небольшие дефекты, которые со временем превратятся в ямы. Прочность влияет и на другие показатели, о которых мы поговорим дальше.
Истираемость
Асфальтовое покрытие постоянно подвергается динамическим нагрузкам, ведь по нему ездят автомобили, двухколесный транспорт, ходят сотни людей. Устойчивость к таким воздействиям определяется маркой по истираемости. Испытания щебня проводят в барабанах, прокручивая образцы с металлическими шариками. Затем подсчитывают потерю массы и по ее проценту присваивают марку.
Щебень по этому показателю тоже выбирают в зависимости от типа асфальтобетона:
- А – И1 (до 25% потери массы)
- Б – И1 или И2 (25-35%) для осадочных пород
- Бх – И2
- В – И3 (35-45%)
На истираемость влияет прочность щебня. Показатель всегда выше у гранита, базальта, амфиболита, ниже у серпентинита, известняка.
Морозостойкость
Вы, наверное, не раз замечали, как после зимы асфальт на дорогах трескается или просто сползает. Почему это происходит?
Температура в холодное время года зачастую опускается ниже нуля. При этом в мелких трещинах и порах замерзает вода, которая попадает в них вместе с осадками, превращаясь в лед. Он расширяется и постепенно разрушает покрытие. Чем меньше таких пустот, тем дольше прослужат дорога или тротуар.
В первую очередь устойчивость к морозам зависит от щебня. Чем он прочнее, тем меньше реагирует на перепады температур. Выбирать материал стоит в зависимости от региона. Для строительства в тропической, субтропической и умеренной зонах морозостойкость щебня должна быть не ниже F50 (наш регион также расположен в умеренной). Это значит, что материал должен выдерживать до 50 циклов заморозки и оттаивания. Хотя для дорожного строительства часто берут камни с более высокими показателями.
Морозостойкость во многом зависит от прочности щебня. Например, у магматических и метаморфических пород она в среднем F200-F300, у осадочных бывает больше F100-F150.
Содержание зерен слабых пород
В щебне почти всегда есть примеси других, более слабых пород. Чем прочнее исходный материал, тем меньше таких включений. Например, согласно ГОСТу, если прочность материала М1000-М1400, в нем должно содержаться не больше 5% зерен слабых пород (от общей массы), а при М400-М800 – до 10%.
Слабые зерна разрушаются под воздействием ударов и давления, что ведет к нарушению целостности асфальтового покрытия. Поэтому их содержание не должно превышать нормы, прописанные в ГОСТе.
Содержание пылевидных частиц и комков глины
Глиной щебень загрязняется во время добычи. Пылевидные частицы могут также попадать в материал из карьеров или образовываться в процессе дробления. Если таких примесей много, повышается водопоглощение щебня, ухудшается его сцепление с битумом. В результате снижаются морозостойкость и прочность асфальтобетона.
Содержание пылевидных и глинистых частиц в щебне для асфальта не должно превышать 0,5%. Если их больше, материал промывают. Но такая процедура несет дополнительные затраты. Поэтому лучше сразу покупать чистый продукт, в котором количество примесей не превышает нормы. Меньше всего их в щебне из прочных магматических пород (гранитном, диоритовом, габбро).
Водопоглощение
Способность поглощать воду свойственна любой горной породе. Больше всего жидкости впитывают в себя разновидности с высокой пористостью (туф, известняк, песчаник), намного меньше – плотные магматические породы.
При высоком показателе водопоглощения падает прочность материала и снижается его морозостойкость. Для снижения параметра иногда щебень сразу после дробления обрабатывают кремнийорганическими жидкостями, жидким битумом, отработанным машинным маслом. Такая методика применяется в тех случаях, когда нужно получить материал с очень низким водопоглощением. Например, это практикуют при создании покрытий на взлетных полосах и автомагистралях в регионах с высоким уровнем годовых осадков или на заболоченной местности.
Насыпная плотность
Насыпная плотность показывает, какой объем будет занимать определенная масса щебня при свободной засыпке в траншею или в кузов автомобиля. Показатель важно знать, чтобы правильно рассчитать количество транспорта для перевозки, перевести кубометры в килограммы и наоборот. Подробнее о том, как это делается, вы можете прочитать в разделе Калькулятор.
Показатель зависит от вида щебня и фракции. В среднем он равен 1500 кг/м3, но для точных расчетов лучше проверить цифры по сертификату. Они могут изменяться от 1300 кг/м3 до 1600 кг/м3.
Подробнее об этом показателе читайте в разделе Насыпная плотность сыпучих материалов, а также на странице Насыпная плотность щебня.
Радиоактивность
Некоторые магматические породы (в первую очередь гранит) имеют природную радиоактивность. В редких случаях щебень может загрязнятся техногенным путем. Для безопасности следует проверить показатель перед использованием материала для асфальтобетона.
Существует несколько классов радиоактивности. Они регулируются ГОСТом.
Породу с определенным фоном используют для разных целей:
- До 370 Бк/кг – ее можно применять для любого асфальтобетона
- До 740 Бк/кг – ее не желательно использовать для дорог в пределах жилой зоны
- До 1500 Бк/кг – она подходит для асфальтирования дорог вне жилых массивов, городов и сел
Щебень с более высокими показателями можно применять лишь по согласованию с СЭС. Но в природе очень редко встречаются породы с такой естественной радиоактивностью.
Какой щебень подойдет для асфальтобетона
Итак, подведем итог всему выше сказанному.
Оптимальным выбором для создания асфальтобетона будут следующие разновидности щебня:
- Габбро 5-10 и 10-15, а также гранитный 5-10, 5-20 и 20-40 для асфальтирования трасс с интенсивным движением
- Амфиболитовый 10-20 и 20-40, гранитный 10-20 и диоритовый 5-20 для шоссе с небольшим трафиком (например, дороги между домами или подъездные), так как у них II группа по лещадности
- Габбро 15-20, диоритовый 20-40, серпентинитовый 5-20 и 20-40, известняковый 5-20 и 20-40 для асфальтирования пешеходных дорожек и двора (III и IV группы по лещадности)
Дальше мы расскажем, какой материал не подходит для производства асфальта.
Какой щебень не подойдет для асфальтобетона
Далеко не весь щебень годится для производства асфальтобетона. Как мы уже сказали выше, к материалу предъявляются особые требования. Если их не учитывать, покрытия получатся слабыми, быстро испортятся, поэтому придется тратить дополнительные средства на их ремонт.
Для асфальтобетона не стоит использовать следующие разновидности:
- Известняк с высокой пористостью и низкой прочностью (ниже М600)
В пористом материале будет накапливаться влага, он будет быстрее разрушаться под воздействием низких температур. Кроме того, карбонатные породы содержат растворимые соли, что ведет к низкой водостойкости. Это в большей мере касается известнякового щебня с примесями гипса. - Песчаник, ракушечник и туф
Это слабые осадочные породы, которые не выдерживают больших нагрузок. Ракушечник и туф – высокопористые материалы, поэтому они совсем не подходят для асфальта. - Мрамор
Этот материал не слишком прочный, имеет низкую морозостойкость. Кроме того, он доступен не во всех регионах, иногда стоит дорого. - Кварц
Минерал достаточно прочный, но встречается редко.Он ценится, в первую очередь, за свой красивый внешний вид. К тому же, его цена всегда высокая, поэтому добавлять кварцевый щебень в асфальт нерационально.
- Гравий
Он образуется вследствие природного выветривания скальных пород. Гравийный щебень не подходит для трасс с интенсивным движением. Для асфальта во дворах и пешеходной зоне он вполне годится, но перед закупкой следует внимательно проверять его характеристики.
Если вы решили асфальтировать двор, дорожки в саду, подъезд к участку или гаражу, не стоит покупать все компоненты отдельно и делать смесь самостоятельно. Это повлечет дополнительные затраты. Без качественного оборудования и опыта у вас вряд ли получится сделать прочное покрытие. Лучше приобрести готовый асфальт. Только учтите, что сам по себе этот материал дорогой. Поэтому использовать его не всегда логично. Дешевле обойдется срезка асфальта. Это недорогая и качественная альтернатива асфальтобетону. Подробнее об этом материале, его свойствах и сферах применения читайте на странице Срезка асфальта.
Выражаю согласие с политикой конфиденциальности
Заказать звонок
О том, как еще можно использовать щебень и для каких работ он подходит, вы можете узнать на наших страницах:
- Применение щебня
- Щебень для дорожных работ
- Щебень для грунтовых дорог
- Щебень для благоустройства территории
- Щебень для дорожек
- Щебень для отсыпки участков, площадок и дворов
- Щебень для уплотнения грунта
- Щебень для ландшафтного дизайна
- Щебень для альпийской горки
- Щебень для габионов
- Щебень для клумб
- Щебень для пруда
- Щебень для сухого ручья
- Щебень для строительных работ
- Полы из щебня в гараже
- Щебень для бетона
- Щебень для дренажа
- Щебень для забора
- Щебень для расклинцовки
Если вы хотите узнать о разновидностях щебня, рекомендуем следующие страницы:
- Виды щебня
Если вы хотите подробно прочитать о характеристиках и свойствах щебня, рекомендуем следующие страницы:
- Характеристики и свойства щебня
- Характеристики и свойства амфиболитового щебня
- Характеристики и свойства амфиболитового щебня 10-20
- Характеристики и свойства амфиболитового щебня 20-40
- Характеристики и свойства амфиболитового щебня 40-120
- Характеристики и свойства гранитного щебня
- Характеристики и свойства гранитного щебня 5-10
- Характеристики и свойства гранитного щебня 5-20
- Характеристики и свойства гранитного щебня 5-25
- Характеристики и свойства гранитного щебня 10-20
- Характеристики и свойства гранитного щебня 20-40
- Характеристики и свойства гранитного щебня 20-70
- Характеристики и свойства гранитного щебня 25-60
- Характеристики и свойства гранитного щебня 40-70
- Характеристики и свойства диоритового щебня
- Характеристики и свойства диоритового щебня 5-20
- Характеристики и свойства диоритового щебня 20-40
- Характеристики и свойства диоритового щебня 40-70
- Характеристики и свойства известнякового щебня
- Характеристики и свойства известнякового щебня 5-20
- Характеристики и свойства известнякового щебня 20-40
- Характеристики и свойства кварцевого щебня
- Характеристики и свойства кварцевого щебня 20-40
- Характеристики и свойства мраморного щебня
- Характеристики и свойства мраморного щебня 5-10
- Характеристики и свойства мраморного щебня 5-20
- Характеристики и свойства мраморного щебня 10-20
- Характеристики и свойства мраморного щебня 20-40
- Характеристики и свойства мраморного щебня 40-70
- Характеристики и свойства серпентинитового щебня
- Характеристики и свойства серпентинитового щебня 5-20
- Характеристики и свойства серпентинитового щебня 20-40
- Характеристики и свойства серпентинитового щебня 40-70
- Характеристики и свойства щебня габбро
- Характеристики и свойства щебня габбро 5-10
- Характеристики и свойства щебня габбро 10-15
- Характеристики и свойства щебня габбро 15-20
- Характеристики и свойства щебня габбро 20-80
- Характеристики и свойства щебня габбро 80-120
О том, как добывают щебень, читайте здесь:
- Добыча щебня
В компании Грунтовозов вы можете приобрести следующие виды щебня по фракциям:
- Щебень 5-10
- Щебень 5-20
- Щебень 5-25
- Щебень 10-15
- Щебень 10-20
- Щебень 15-20
- Щебень 20-40
- Щебень 20-70
- Щебень 20-80
- Щебень 25-60
- Щебень 40-70
- Щебень 40-120
- Щебень 80-120
В продаже имеются следующие разновидности амфиболитового щебня:
- Щебень амфиболитовый 10-20
- Щебень амфиболитовый 20-40
- Щебень амфиболитовый 40-120
В продаже имеется щебень габбро:
- Щебень габбро 5-10
- Щебень габбро 10-15
- Щебень габбро 15-20
- Щебень габбро 20-80
- Щебень габбро 80-120
Если вы хотите купить гранитный щебень, рекомендуем следующие страницы:
- Щебень гранитный 5-10
- Щебень гранитный 5-20
- Щебень гранитный 5-25
- Щебень гранитный 10-20
- Щебень гранитный 20-40
- Щебень гранитный 20-70
- Щебень гранитный 25-60
- Щебень гранитный 40-70
Мы продаем следующие виды диоритового щебня:
- Щебень диоритовый 5-20
- Щебень диоритовый 20-40
- Щебень диоритовый 40-70
Известняковый щебень, представленный у нас в продаже:
- Щебень известняковый 5-20
- Щебень известняковый 20-40
В продаже имеется щебень кварцевый:
- Щебень кварцевый 20-40
Если вы хотите купить мраморный щебень, рекомендуем следующие страницы:
- Щебень мраморный 5-10
- Щебень мраморный 5-20
- Щебень мраморный 10-20
- Щебень мраморный 20-40
- Щебень мраморный 40-70
В продаже имеются следующие разновидности пироксенитового щебня:
- Щебень пироксенитовый 5-20
- Щебень пироксенитовый 20-40
- Щебень пироксенитовый 40-70
Если вам нужен серпентинитовый щебень, рекомендуем ознакомиться со следующими страницами:
- Щебень серпентинитовый 5-20
- Щебень серпентинитовый 20-40
- Щебень серпентинитовый 40-70
С перечнем всех разновидностей щебня, представленных у нас в продаже, вы можете познакомиться на странице Щебень.
Заполнитель — Pavement Interactive
Заполнитель — это собирательный термин для минеральных материалов, таких как песок, гравий и щебень, которые используются со связующей средой (например, водой, битумом, портландцементом, известью и т. д.) для образования смеси. материалы (например, асфальтобетон и портландцементный бетон). По объему заполнитель обычно составляет от 92 до 96 процентов HMA и от 70 до 80 процентов портландцементного бетона. Заполнитель также используется для базовых и подстилающих слоев как для нежестких, так и для жестких покрытий.
Агрегаты могут быть натуральными или искусственными. Природные заполнители обычно извлекаются из более крупных горных пород открытым способом (карьером). Добытая порода обычно измельчается до пригодных для использования размеров путем механического дробления. Произведенный заполнитель часто является побочным продуктом других отраслей обрабатывающей промышленности.
В этом разделе кратко обсуждаются источники заполнителя и разработка карьеров, затем описываются основные минеральные, химические и физические свойства заполнителя, наиболее важные для дорожных покрытий, и типичные тесты, используемые для определения этих свойств. В следующем источнике содержится более подробная информация о заполнителе:
Источники заполнителей
Заполнители могут поступать как из природных, так и из искусственных источников. Природные заполнители образуются из горных пород, которые подразделяются на три широкие геологические классификации (Roberts, et al., 1996):
- Магматические породы
- Эти горные породы в основном кристаллические и образуются в результате охлаждения расплавленного скального материала под земной корой (магмой).
- Осадочные породы
- Эти горные породы образуются из отложившегося нерастворимого материала (например, остатков существующих горных пород, осевших на дне океана или озера). Этот материал превращается в камень под действием тепла и давления. Осадочные породы имеют слоистый внешний вид и далее классифицируются в зависимости от их преобладающего минерального состава на известняковые (известняк, мел и т. д.), кремнистые (кремни, песчаник и т.
д.) или глинистые (сланцы и т. д.).
- Метаморфическая порода
- Это магматические или осадочные породы, подвергшиеся воздействию тепла и/или давления, достаточно сильному, чтобы изменить свою минеральную структуру, чтобы она отличалась от исходной породы.
Искусственная горная порода обычно состоит из промышленных побочных продуктов, таких как шлак (побочный продукт металлургической обработки, обычно получаемый при обработке стали, олова и меди) или специальная горная порода, полученная с особыми физическими характеристиками, отсутствующими в природной горной породе (например, низкая плотность легкого заполнителя).
Производство заполнителей
Заполнители производятся в карьере или шахте (рис. 1), основной функцией которых является преобразование породы на месте в заполнитель с заданными характеристиками. Обычно горная порода взрывается или выкапывается из стен карьера, а затем уменьшается в размерах с помощью ряда грохотов и дробилок. Некоторые карьеры также способны промывать готовый заполнитель.
Минеральные свойства
Минеральный состав заполнителя в значительной степени определяет его физические характеристики и его поведение в качестве материала дорожного покрытия. Таким образом, при выборе источника заполнителя знание минеральных свойств карьерной породы может дать отличный ключ к пригодности полученного заполнителя. Кордон (1979) содержит некоторые общие рекомендации по заполнителю, используемому в HMA.
Таблица 1. Требуемые свойства горных пород для HMA
(из Cordon, 1979 г., ссылка на Roberts et al., 1996 г.)
Тип породы | Твердость, Прочность | Стойкость к зачистке 1,2 | Текстура поверхности | Измельченная форма |
---|---|---|---|---|
Магматические | ||||
Гранит | Ярмарка | Ярмарка | Ярмарка | Ярмарка |
Сиенит | Хорошо | Ярмарка | Ярмарка | Ярмарка |
Диорит | Хорошо | Ярмарка | Ярмарка | Хорошо |
Базальт (ловушка) | Хорошо | Хорошо | Хорошо | Хорошо |
Диабаз (ловушка) | Хорошо | Хорошо | Хорошо | Хорошо |
Габбро (трэп-рок) | Хорошо | Хорошо | Хорошо | Хорошо |
Осадочные | ||||
Известняк | Бедный | Хорошо | Хорошо | Ярмарка |
Песчаник | Ярмарка | Хорошо | Хорошо | Хорошо |
Черт | Хорошо | Ярмарка | Бедный | Хорошо |
Сланец | Бедный | Бедный | Ярмарка | Ярмарка |
Метаморфический | ||||
Гнейс | Ярмарка | Ярмарка | Хорошо | Хорошо |
Сланец | Ярмарка | Ярмарка | Хорошо | Ярмарка |
Шифер | Хорошо | Ярмарка | Ярмарка | Ярмарка |
Кварцит | Хорошо | Ярмарка | Хорошо | Хорошо |
Мрамор | Бедный | Хорошо | Ярмарка | Ярмарка |
Серпантин | Хорошо | Ярмарка | Ярмарка | Ярмарка |
Примечания:
|
В целом взаимосвязь между минеральными и физическими свойствами довольно сложна, что затрудняет точное предсказание того, как будет вести себя конкретный источник заполнителя, основываясь только на минеральных свойствах.
Химические свойства
Хотя для сыпучего заполнителя они относительно не важны, химические свойства заполнителя важны для материала дорожного покрытия. В HMA химический состав поверхности заполнителя может определить, насколько хорошо вяжущее асфальтового вяжущего будет прилипать к поверхности заполнителя. Плохая адгезия, обычно называемая отслаиванием, может привести к преждевременному разрушению конструкции. В ПКК заполнители, содержащие реакционноспособные формы кремнезема, могут активно реагировать со щелочами, содержащимися в цементном тесте. Это расширение может привести к растрескиванию, вздутию поверхности и отслаиванию. Обратите внимание, что некоторые химические свойства заполнителя могут меняться со временем, особенно после измельчения заполнителя. Только что измельченный заполнитель может проявлять другое сродство к воде, чем тот же заполнитель, который был измельчен и оставлен в запасе на год.
Ниже приведены типичные химические свойства, измеряемые для заполнителей:
- Отслаивание
- Щелочно-агрегатная реакция
Физические свойства
Физические свойства заполнителя являются наиболее очевидными свойствами заполнителя, и они также самым непосредственным образом влияют на поведение заполнителя либо в качестве компонента материала дорожного покрытия, либо в качестве материала основания или подстилающего слоя. Обычно измеряемыми физическими свойствами заполнителя являются (Roberts et al., 1996):
- Градация и размер
- Прочность и стойкость к истиранию
- Долговечность и надежность
- Форма частиц и текстура поверхности
- Чистота и вредные материалы
- Содержание влаги
Это не единственные физические свойства заполнителей, а наиболее часто измеряемые. Тесты, используемые для количественной оценки этих свойств, в основном носят эмпирический характер. Физические свойства заполнителя могут меняться со временем. Например, только что измельченный заполнитель может содержать больше пыли и, следовательно, быть менее восприимчивым к связыванию с битумным вяжущим 9.0003
Заполнитель как основной материал
Заполнитель часто используется сам по себе в качестве несвязанного основания или подстилающего слоя. При использовании как таковой заполнитель обычно характеризуется предыдущими физическими свойствами, а также общей жесткостью слоя. Жесткость слоя характеризуется теми же тестами, которые используются для характеристики жесткости грунтового основания.
Зачем ты собираешь ресурсы для шоссе?
На недавнем семинаре эксперты обсудили проблемы истощения источников и проблемы будущих поставок, связанных с этим важнейшим строительным материалом.
Устойчивые источники заполнителей, такие как этот карьер и завод заполнителей, расположенный недалеко от региона роста в Северной Вирджинии, а также проблемы с будущими поставками песка, гравия и других материалов для строительства дорог были в центре внимания недавнего семинара TRB.
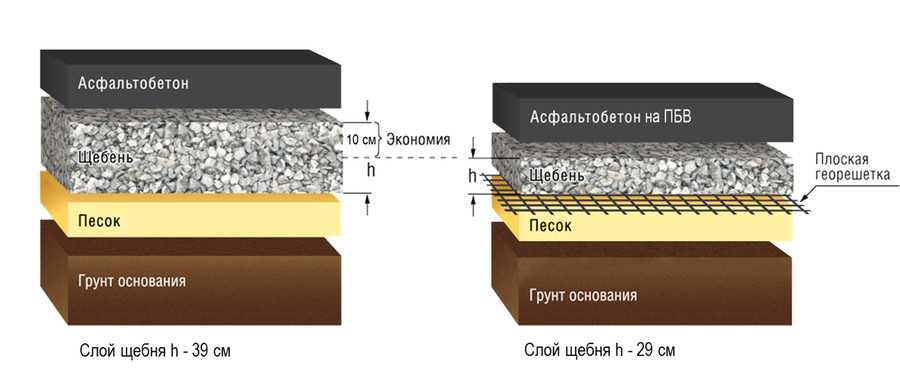
Песок, гравий, щебень и, все чаще, промышленные побочные продукты и регенерированные строительные материалы в буквальном смысле являются основой транспортной инфраструктуры страны. Эти материалы, которые в совокупности называются заполнителями, необходимы для строительства, сохранения и восстановления дорог и мостов. Заполнители влияют на долговечность, прочность, модуль упругости, термические свойства и все важные, связанные с безопасностью свойства поверхностей движения: трение и сцепление.
Щебень и гравийный щебень являются основными источниками большинства заполнителей для дорожного покрытия. Их угловатые формы хорошо работают в тех случаях, когда трение между частицами увеличивает прочность дорожного покрытия, например, в случае зернистых оснований и слоев асфальта. Для портландцементного бетона также широко используются природный песок, гравий и щебень в покрытиях и сооружениях. Природный песок, как мелкий заполнитель для бетона, закреплен в спецификациях дорожных агентств, потому что его округлая форма способствует удобоукладываемости бетона. Использование измельченных, угловатых и промышленных мелких заполнителей в бетоне, строительном растворе и цементном растворе более сложно, но в некоторых областях может быть необходимо.
Чтобы быть полезными для дорожных агентств, в первую очередь заполнители должны быть достаточного качества, чтобы соответствовать как первоначальным проектным требованиям, так и долгосрочным целям жизненного цикла. Лица, принимающие решения в отрасли, регулярно рассматривают альтернативные смеси, переработанные источники и сорта, а также другие заполнители, указанные для проектов. Разработка спецификаций, которые позволяют больше смешивать для достижения целей производительности, может помочь сохранить заполнители премиум-класса для критически важных применений.
Обеспечение устойчивых поставок заполнителей требует заблаговременного планирования и балансировки сложной матрицы инженерных, географических и геологических переменных и интересов сообщества. Совокупные ресурсы, будь то карьеры, ямы, переработанные материалы или побочные продукты производства, более устойчивы, если они расположены рядом с проектами. Однако во многих случаях материалы должны доставляться грузовиками на проектные площадки из отдаленных мест.
«Дорожная отрасль и общественность должны быть более осведомлены о важности агрегатов для местной экономики и региональной транспортной инфраструктуры», — говорит Хорхе Э. Паган-Ортис, директор Управления исследований и исследований инфраструктуры Федерального управления автомобильных дорог (FHWA). Разработка. «Знание местонахождения текущих и потенциальных будущих источников заполнителей важно для стратегического планирования и защиты ресурсов».
Зная больше о местных ресурсах, чиновники могут планировать и проектировать проекты дорог, чтобы оптимизировать использование различных типов местных природных и переработанных заполнителей. Использование доступных на месте заполнителей снижает транспортные расходы и энергию, затрачиваемую на перемещение этих тяжелых сыпучих материалов. Оптимальное использование местных заполнителей также снижает интенсивность движения грузовиков и количество осевых нагрузок на систему автомагистралей. Более того, сообщества могут добывать высококачественные заполнители, прежде чем использовать землю для других целей, таких как озера, парки или новые застройки. Тем не менее, предварительное планирование, а также экологические и ландшафтные архитектурные соображения имеют решающее значение для мелиорации и освоения совокупных земель.
В январе 2011 года на ежегодном собрании Совета по транспортным исследованиям (TRB) 90 th эксперты из США и Европы собрались на семинар на тему «Совокупное истощение источников и будущее предложение». Представители FHWA, Геологической службы США (USGS), государственных департаментов транспорта (DOT), промышленности и научных кругов обсудили будущее устойчивых источников минеральных агрегатов и связанные с этим проблемы, стоящие перед многими штатами и транспортными агентствами. Ниже приведены основные моменты их выступлений.
Совокупные потребности для автомагистралей и сооружений
Как по объему, так и по тоннажу заполнители превосходят все другие материалы, используемые в построенной инфраструктуре дорог и мостов. Как определено ASTM International в ASTM D 8-02, заполнитель представляет собой «гранулированный материал минерального состава, такой как песок, гравий, ракушка, шлак или щебень, используемый с вяжущей средой для образования строительных растворов или бетона, или отдельно, как в базовых слоях, железнодорожных балластах и т. д.».
Циркуляр Геологической службы США 1176 Заполнители из природных и переработанных источников: экономическая оценка применения в строительстве — анализ потоков материалов (1998) уточняет определение следующим образом: «заполнители — это… материалы, природные или искусственные, которые либо измельчаются и смешиваются со вяжущим для образования битумного или цементного бетона, либо обрабатываются отдельно для образования таких продуктов, как железная дорога. балласт, фильтрующие слои или флюсовый материал». Обработанные и необработанные заполнители также используются для местных гравийных дорог или других дорог с заполнителем, проездов и парковок.
Как правило, природные заполнители добывают в каменоломнях, а также в песчаных и гравийных карьерах. Однако агентства все чаще используют переработанные, регенерированные и альтернативные материалы из побочных продуктов, такие как доменный и сталелитейный шлак, другие побочные продукты горнодобывающей промышленности или производства, а также регенерированное асфальтовое покрытие и переработанный бетонный заполнитель. Однако эти альтернативные материалы в настоящее время покрывают лишь небольшую часть общих совокупных потребностей автомагистралей. Опрос инженеров-материаловедов штата DOT, проведенный в 2010 году Подкомитетом по материалам Американской ассоциации государственных служащих автомобильных дорог и транспорта (AASHTO), выявил использование восстановленного асфальтового покрытия (в асфальтовых смесях) и использование переработанного бетонного заполнителя (в основном в приложениях для основания) в большинство штатов.
Здесь показаны примеры природных заполнителей, используемых в строительстве: (a) природный гравий, часто используемый в качестве крупного заполнителя в бетоне, (b) крупный заполнитель из щебня, обычно используемый в асфальтовых смесях для дорожного покрытия и бетона, и (c) a слой уплотненного щебня, используемый в качестве зернистого основного материала.

Согласно отчетам Геологической службы США, производство и использование заполнителей в США сократились во время экономического спада в 2008-2010 гг. Однако спрос на заполнители всех типов и видов использования в 2007 и 2008 годах составлял порядка 2,5–3 миллиардов тонн (от 2,2 до 2,7 метрических тонн) в год и может вернуться к этому уровню, когда объемы строительства вернутся. Билл Лангер, геолог-исследователь агрегатов Геологической службы США, который выступил с двумя презентациями на семинаре TRB, говорит, что для удовлетворения заявленных текущих и будущих потребностей в инфраструктуре может потребоваться увеличение годового совокупного производства на 70 процентов в течение 5-летнего периода. если ремонт инфраструктуры начат всерьез. Далее, добавляет он, «природный заполнитель широко распространен на территории Соединенных Штатов, но местонахождение заполнителя определяется геологией и не подлежит обсуждению».
На этой карте показано общее расположение совокупных ресурсов на граничащих с США территориях.

В некоторых регионах геологически доступны месторождения песка, гравия и горных пород, пригодных для производства щебня, если вообще имеются. Например, природного заполнителя не хватает на Прибрежной равнине и заливе Миссисипи, на плато Колорадо и в бассейне Вайоминга, на покрытом льдом Среднем Западе, Высоких равнинах и на не покрытых льдом Северных равнинах. Кроме того, многие источники заполнителя в других регионах, например в некоторых частях Тихоокеанского северо-запада, не отвечают требованиям по физическим характеристикам и долговечности или содержат загрязняющие вещества или вредные материалы, которые ограничивают использование.
Предполагаемое совокупное использование в США (в миллионах тонн) В других регионах развитие или действия сообщества могут препятствовать добыче ресурсов. В населенных районах вмешательство в конфликтующие виды землепользования, давление сообщества, условия выдачи разрешений, экологические проблемы и противодействие со стороны растущего числа интернет-групп по борьбе с добычей полезных ископаемых препятствуют или ограничивают развитие многих подходящих ресурсов.
Проблема ограниченного предложения становится особенно острой в случае фрикционных заполнителей, необходимых для изнашиваемых поверхностей тротуаров и мостов, для которых требуются заполнители с твердыми минералами, которые не будут легко стираться или полироваться в условиях движения. Во многих частях страны, где преобладающим заполнителем является известняк, устойчивые к полировке материалы необходимо транспортировать на большие расстояния и с повышенными затратами. По мере того, как государственные DOT продолжают усилия по повышению безопасности на сельских и двухполосных дорогах, все большее значение приобретают более качественные заполнители или смеси с хорошим коэффициентом трения для покрытий. Для мультитекстурной поверхности можно использовать смеси прочных заполнителей с разной износостойкостью.
Использование переработанных материалов
FHWA оценивает потребность транспортной отрасли США в заполнителях для дорожных покрытий примерно в 700 миллионов тонн (630 миллионов метрических тонн) в год. Согласно презентации 2009 года Питера Стефаноса, директора Управления технологий дорожного покрытия FHWA, существует огромная потребность в сокращении спроса на первичные минеральные ресурсы в системе автомобильных дорог страны, и один из способов сделать это — переработка.
Как сообщается в исследовании FHWA Восстановленное асфальтовое покрытие в асфальтовых смесях: состояние практики (FHWA-HRT-11-021), по состоянию на 2007 год в дорожной отрасли использовалось до 100 миллионов тонн (91 миллион метрических тонн) регенерированного асфальтового покрытия. Аналогичным образом, Американская ассоциация производителей бетонных покрытий (ACPA) в своем Engineering Bulletin (EB043P) за 2009 г. оценивает, что строительная отрасль использует еще 100 миллионов тонн (91 миллион метрических тонн) вторичного бетонного заполнителя и других измельченных и битых бетонных материалов в расчете на год. По оценкам Ассоциации по переработке строительных материалов (CMRA), еще большее количество дробленого или битого бетона ежегодно перерабатывается для различных целей и продуктов (включая заполнители). В частности, ассоциация указывает на использование заполнителей из переработанного бетона в заполнителях (основах дорог), товарных бетонных смесях, асфальтовых покрытиях, стабилизации грунта, укладке труб и ландшафтных материалах.
Тип агрегата | 2007 | 2008 | 2009 |
---|---|---|---|
Песок и гравий | 1 380 | 1 170 | 921 |
Щебень | 1 820 | 1 610 | 1 290 |
Регенерированное асфальтовое покрытие* | 11 | 16 | 18 |
Переработанный бетонный заполнитель* | 11 | 17 | 14 |
Сумма свыше | 3 222 | 2 813 | 2 243 |
Песок и гравий, импортированные в США | 5 | 6 | 3 |
Щебень, импортированный в США | 21 | 23 | 13 |
Сумма свыше | 3 248 | 2 842 | 2 259 |
Источник: Геологическая служба США. |
Указать точное количество сложно, потому что переработанные и восстановленные материалы часто повторно используются в одном и том же проекте. Оценки USGS переработанных и регенерированных материалов основаны на количествах, хранящихся и продаваемых для использования в других местах, только производителями или подрядчиками, которые ответили на его ежегодный опрос, поэтому истинный объем используемых регенерированных материалов, вероятно, намного выше. Фактически, на вопросник ответили лишь около трети опрошенных строительных компаний и переработчиков щебня. В настоящее время Геологическая служба США ежегодно проводит опрос этих компаний, производящих переработанные материалы, и работает над улучшением сбора данных об использовании регенерированного асфальтового покрытия и регенерированного бетонного заполнителя.
Усилия штатов по устойчивому развитию
Имеющиеся данные свидетельствуют о том, что совокупное использование вторичного сырья на уровне штатов растет. Журнал Public Works сообщает в своем выпуске за март 2011 года, что Министерство транспорта Техаса (TxDOT) увеличило использование регенерированного асфальтового покрытия с 467 000 тонн (424 000 метрических тонн) в 2008 году до 827 000 тонн (750 000 метрических тонн) в 2010 году. Несмотря на это большое увеличение, регенерированные заполнители по-прежнему удовлетворяют лишь небольшой процент потребностей TxDOT.
Программа устойчивого развития материалов Департамента транспорта штата Орегон (ODOT) направлена на сокращение, повторное использование, переработку и «упреждающее управление всеми земляными материалами, необходимыми и/или произведенными в результате строительных и ремонтных работ ODOT». Цель программы состоит в том, чтобы определить и удовлетворить потребности отдела в источниках материалов и утилизации посредством идентификации и управления объектами, стратегического планирования, а также утилизации и утилизации избыточных или отходов материалов от одного проекта к другому.
По словам Рассела Фроста, координатора по совокупным ресурсам в ODOT по всему штату, в 2009 году в рамках программы строительства мостов Департамента было повторно использовано или переработано более 21 000 тонн (19 000 метрических тонн) чистой засыпки, 40 000 тонн (36 000 метрических тонн) бетона и 44 000 тонн. (40 000 метрических тонн) асфальтобетонных материалов.
Орегон, как и ряд других штатов и агентств, изучил свои совокупные ресурсы и отложил часть этих ресурсов для использования в будущем, чтобы защитить их от конкурирующих видов землепользования. В 2002 г. штат подготовил отчет в сотрудничестве с FHWA, Сводная инвентаризация ресурсов и исследование прогноза потребностей (FHWA-OR-RD-03-03), основанное на цели планирования штата Орегон по защите природных ресурсов и сохранению живописных и исторических районов и открытых пространств. В отчете объясняется, как ODOT может оценивать участки, производящие заполнители, и инициировать действия по землепользованию для сохранения и защиты значительных участков. Орегон также поддерживает базу данных Сводной системы исходной информации, размещенную на его сайте внутренней сети. База данных является основным инструментом, который ODOT использует для управления почти 700 источниками материалов по всему штату.
Этот асфальтный завод расположен в месте добычи песка и гравия, где готовится склад регенерированного асфальтового покрытия для смешивания и переработки в асфальтовые смеси.
В этом карьере в Харрисонбурге, штат Вирджиния, переработанный щебень складируется для использования или дальнейшего дробления и сортировки с целью получения заполнителей меньшего размера для использования в строительстве.
Другие штаты, такие как Аляска, Калифорния, Мэриленд и шесть штатов Новой Англии, также провели исследования или приняли законодательство в отношении совокупных ресурсов. В Калифорнии, например, в 1919 году был принят Закон о добыче полезных ископаемых и мелиорации.75, требующий от округов наличия достаточных разрешенных совокупных ресурсов для удовлетворения спроса на следующие 50 лет. Кроме того, в большинстве штатов требуются планы рекультивации и повторного использования участков после извлечения разрешенных совокупных ресурсов. В некоторых случаях государственное или местное агентство получает землю для общественных целей, таких как дороги, парковые насаждения, водохранилища или сооружения для пополнения запасов подземных вод.
Программа управления запасами материалов Аляски
По словам Дэвида Стэнли, главного инженера-геолога Департамента транспорта и общественных сооружений Аляски, и Питера Хардкасла, старшего инженера-геолога R&M Consultants, Inc., Аляска разрабатывает программу управления запасами материалов. в рамках управления геотехническими активами. Геотехнические активы включают участки материалов и другие объекты, требующие мониторинга, такие как откосы горных пород и грунта, сетка камнепадов, анкеры и анкеры, насыпи и основания дорожного покрытия, подпорные стены, фундаменты, туннели и геотехнические инструменты. Проект включает в себя оценку запасов и условий на площадке, руководствуясь принципами управления транспортными активами. Стэнли говорит, что в трех регионах штата — северном, центральном и юго-восточном — имеется около 2800 участков дорожной сети, из которых около одной трети являются действующими. Еще около 250 материальных объектов расположены в сельских аэропортах и до сих пор не инвентаризированы.
Аляска сталкивается с рядом проблем, связанных с ее совокупным предложением, в том числе с ограниченными транспортными системами для доставки материалов, участками материалов, переоборудованными для других целей, а также проблемами с полосой отвода и землепользованием. Программа будет включать в себя разработку доступной для поиска базы данных участков с материалами, обзор доступных источников гравия и обоснование регулирующим органам необходимости получения и удержания участков. В конечном счете, говорит Хардкасл, программа «поможет избежать конфликтов при планировании, таких как мегапроекты, и обеспечит непрерывность работы, несмотря на текучесть кадров. Система будет портативной, простой в использовании и рассчитана на будущие сбои в программе».
Департамент транспорта и общественных сооружений штата Аляска присвоил каждому объекту класс доступности и задокументировал подробную информацию о местоположении, а также о качестве и количестве материалов для использования в различных приложениях. «Данные об управлении активами будут полезны для обеспечения достаточного количества материалов в будущем и защиты источников для операций по добыче материалов и совместного использования участков с другими агентствами», — говорит Стэнли. «Данные также будут поддерживать передовые методы, включая буферы между участками и прилегающими частными владениями, исправление проблем с табличками статуса земли и записями, а также соблюдение экологических требований, таких как правила стока ливневых вод».
Другие цели программы Аляски включают разработку стандартов производительности, которые департамент может применять к объектам материальных ценностей, и облегчение управления геотехническими активами для принятия долгосрочных решений, касающихся этих материальных активов.
Общественные проблемы, связанные со снабжением и транспортировкой
В дополнение к усилиям по повторному использованию существующих материалов и каталогизации местонахождения агрегатных объектов государства сталкиваются с проблемами, возникающими на пересечении путей снабжения, транспортировки материалов и государственной политики. Автомагистрали обеспечивают надежные коридоры для доступа к природным ресурсам, транспортировки продуктов на рынки и обеспечения удобной мобильности для сообществ. После строительства автомагистралей в сельских или отдаленных районах, которые обеспечивают доступ к шахтам, сельскому хозяйству, лесам и зонам отдыха, обычно требуется меньше агрегатов для обслуживания и модернизации. Однако те, которые обслуживают городские и пригородные рынки страны, а также интермодальные узлы, требуют большего количества заполнителей для обслуживания и ремонта. Но часто рядом с этими зонами повышенного спроса отсутствуют шахты по добыче щебня и другие источники.
Здесь показан участок из песка и гравия на Холден-Крик на северной стороне хребта Брукс, к югу от озера Гэлбрейт на Аляске. В этом месте бригады дробят гравийные заполнители для строительства дорог.
По словам Марка Круменахера, отраслевого консультанта GZA GeoEnvironmental, выдача разрешений на совокупные источники связана с рядом проблем. В дополнение к землепользованию и экологическим нормам, в более населенных районах продолжающееся развитие и рост населения затрагивают существующие и потенциальные совокупные источники добычи полезных ископаемых. «Все труднее расширять источники по горизонтали или открывать новые участки, если нет достаточного запаса земли», — говорит Круменахер. «Производители заполнителя иногда могут разрабатывать свои месторождения глубже, если существует материал достаточного качества, но это часто дорого и сопряжено со значительными инженерными проблемами».
Использование агрегатов и относительный уровень требуемого качества
Более низкое качество | Засыпка и подстилка |
---|---|
Основание, выбор материала и улучшение основания | |
Базовый курс (не связанный и стабилизированный)
| |
Дороги с заполнителем (гравийные дороги) | |
Уплотнитель чипа, материал покрытия | |
Бетон на портландцементе
| |
Горячий асфальт и теплый асфальт
| |
Более высокое качество | Дренаж и каменная наброска |
Агрегаты фильтров |
В Mineral Commodity Summarys 2011 Министерство внутренних дел США и Геологическая служба США указывают на влияние государственных и разрешительных проблем на доступность щебня, песка и гравия, заявляя, что «[m] Ожидалось, что транспортировка песка и гравия вдали от густонаселенных центров будет продолжаться там, где этому препятствуют экологические, земельные и местные правила зонирования».
Что касается щебня, в отчете говорится: «Ожидается, что нехватка щебня в некоторых городских и промышленных районах будет продолжать расти из-за местных правил зонирования и альтернативных вариантов освоения земель. вдали от крупных населенных пунктов». Что касается переработанных заполнителей, в отчете признается, что «переработанный асфальт и портландцементные бетоны все чаще заменяют первичный заполнитель, хотя процент от общего количества заполнителя, полученного за счет переработанных материалов, в 2010 году оставался очень низким».
Итог: Большая часть естественных совокупных потребностей для автомагистралей в более населенных районах должна будет поступать издалека с увеличением стоимости, заторов и потребления энергии. То есть, если только государственные, местные и муниципальные организации не планируют в долгосрочной перспективе оптимизировать использование существующих ресурсов более близкого заполнителя и облегчить транспортировку заполнителей по железной дороге и воде, когда они доступны.
Заполнители и FHWA
Признавая важность устойчивых поставок качественных заполнителей для строительства и обслуживания дорог на национальном уровне, FHWA сотрудничает с Международным центром исследования заполнителей при Техасском университете и Техасском университете A&M для финансирования исследований. проекты, связанные как с бетоном, так и с асфальтом. Партнерство создало техническую рабочую группу с федеральными, государственными, университетскими и отраслевыми экспертами, участвующими в экспертной оценке текущих совокупных исследований и изучении потребностей в исследованиях в области шоссе и транспорта.
Для асфальтовых покрытий важны фрикционные свойства крупного заполнителя, поскольку они воздействуют на поверхность покрытия. Здесь показаны три образца полированного крупного заполнителя, лежащие на поверхности асфальтового покрытия.
Группа предоставляет обновленную информацию Комитету TRB по минеральным заполнителям и работает над дорожной картой исследований заполнителей для определения технологических и устойчивых инноваций, необходимых для гранулированных основ заполнителей, технологии бетона (особенно с использованием промышленного песка) и смесей для асфальтового покрытия. Сопоставление будущих региональных потребностей с доступностью является важным элементом этого обсуждения. Баланс между землепользованием и наличием ресурсов является частью сложной матрицы, в которой участвует общественность на многих уровнях, включая рассмотрение на уровне государственных и столичных организаций планирования.
Европейский опыт и перспективы
Европейцы тоже обеспокоены устойчивостью местных поставок заполнителей, как сообщил Эндрю Доусон, доцент Ноттингемского университета в Соединенном Королевстве, изучающий вопросы предложения заполнителей в Европе. С 1987 года Европейская ассоциация агрегаторов продвигает интересы европейской индустрии агрегатов, представляя ассоциации-члены по вопросам экономической, технической, экологической политики, а также политики в области здравоохранения и безопасности. Ассоциация Annual Review 2009-2010 приведены данные о производстве и использовании за 2008 год. Согласно отчету, в целом в Европе добывается примерно 3,3 миллиарда тонн (3 миллиарда метрических тонн), что превышает текущий совокупный объем производства в США. Из этого общего количества 2 процента составляют природный песок и гравий, извлеченные из источников морского дна, а 6 процентов поступает путем переработки.
Исследователи FHWA используют дефлектометр падающего груза, буксируемый за этим фургоном, для проверки уплотненного гранулированного основания на участке исследовательского покрытия в округе Лаудоун, штат Вирджиния. Этот исследовательский проект был разработан в сотрудничестве с участием FHWA, государственных DOT, университетских исследователей и представителей промышленности.
В течение следующих 5–10 лет производство в Европе может вырасти до 4,4 млрд тонн (4 млрд метрических тонн). В первую тройку стран с точки зрения процента переработки (около 20 процентов от общего объема производства приходится на переработанные источники) входят Бельгия, Нидерланды и Великобритания, которые в настоящее время перерабатывают почти все доступные строительные материалы и материалы для сноса. Ссылаясь на отчет Университета Леобена, Австрия, Доусон отмечает, что в Европе значение 15 процентов будет представлять собой общую переработку, и что в среднесрочной перспективе переработка вряд ли превысит 10 процентов производства из-за ограничений материалов для сноса и экономики. транспорта.
Доусон сообщает, что разрешенные совокупные запасы в Европе сокращаются из-за конкурирующего землепользования, отсутствия стратегической политики и планирования, политического стремления к локализации принятия решений, экологических ограничений, а также сложности и неопределенности системы разрешений. В качестве примера отсутствия планирования Доусон приводит сбор данных по совокупным показателям в Европе непоследовательным и неполным. «Большая часть этого собирается промышленностью, и многие правительства не оценивают совокупные ресурсы. Поэтому трудно установить политику. Органы планирования должны проводить картографирование полезных ископаемых. решения навязываются местным властям, которые не имеют достаточно широкого взгляда, что препятствует развитию национальной и региональной политики».
Но, по его словам, Инициатива Европейской Комиссии по сырью для ЕС, запущенная в 2008 году, может стать шагом в правильном направлении. Инициатива направлена на создание стратегии решения вопросов, связанных с сырьем, и подкрепление этой стратегии законодательством. «Заполнители хорошо представлены в планах, — говорит Доусон, — что очень важно, поскольку доступность заполнителей из региональных и местных источников имеет важное значение для экономического развития с учетом логистических ограничений и транспортных расходов».
Взгляд в будущее
Будущее дорог общего пользования зависит от надежных и устойчивых поставок заполнителей с уровнем качества, необходимым для строительства и обслуживания долговечных и прочных дорожных покрытий и транспортных сооружений. Государственным и местным DOT необходим доступ к качественным источникам первичных заполнителей — песка, гравия, гравийного щебня и щебня — восстановленного асфальтового покрытия, переработанного бетонного заполнителя, дробленого щебня, переработанных/восстановленных заполнителей после восстановления дорожного покрытия и полной глубины. реконструкции и других альтернативных побочных материалов для поддержки их программ строительства автомагистралей.
Хотя использование переработанного заполнителя растет, многие отраслевые эксперты сомневаются, что предложение удовлетворит спрос. Таким образом, добыча заполнителей остается необходимостью и должна осуществляться экологически безопасным и устойчивым способом. Поскольку отдельные карьеры и шахты истощаются и больше не могут поставлять заполнители, агентства и землевладельцы должны будут выполнить планы рекультивации, чтобы повторно использовать землю для других целей, одобренных планирующими агентствами, таких как озера, места обитания рыб, парки, зеленые насаждения, подземные воды. перезарядка, многоцелевые жилые и коммерческие объекты, места отдыха и заповедники дикой природы.
Как и в случае с энергоресурсами, жизнеспособные решения для совокупных поставок зависят от местоположения и местных условий. Презентации семинара TRB и продолжающиеся обсуждения среди отраслевых экспертов подчеркивают необходимость уделить внимание этому важному вопросу: обеспечению устойчивых источников минеральных заполнителей и переработанных заполнителей для транспортной системы завтрашнего дня.
Источник: Геологическая служба США. * Преобразовано из метрических тонн и представлено в виде трех или менее знаков без десятичных знаков. Оценки Геологической службы США за 2010 год примерно такие же или чуть меньше, чем за 2009 год.: 909 млн тонн песка и гравия и 1 320 млн тонн щебня. Обратите внимание, что эти данные по регенерированному асфальтовому покрытию и переработанному бетонному заполнителю соответствуют сообщениям Геологической службы США и, вероятно, являются чрезвычайно низкими, отчасти из-за ограниченной информации обследования. Автодорожная промышленность (ACPA, CMRA, FHWA и Национальная ассоциация асфальтовых покрытий) оценила количество регенерированного и переработанного асфальта и бетонных материалов, используемых в строительстве, примерно в 100 миллионов тонн каждого. Действия по повторному использованию включают использование подрядчиком или силами технического обслуживания в том же проекте или соседнем проекте материалов основания или обочины, или использование в качестве выбранного материала, где требуется укрепление или модификация земляного полотна.
Отдельные решения для обеспечения устойчивых поставок заполнителей
— Билл Лангер, USGS |
Миллионы метрических тонн | Песок и гравий (включая морской) | Щебень | Вторичное/вторичное |
---|---|---|---|
Австрия | 62 | 32 | 6 |
Бельгия | 15 | 42 | 16 |
Чехия | 27 | 44 | 4 |
Дания | 48 | 0 | 10 |
Финляндия | 25 | 60 | 1 |
Франция | 172 | 237 | 23 |
Германия | 271 | 218 | 74 |
Ирландия | 25 | 25 | 0 |
Италия | 225 | 135 | 8 |
Нидерланды | 100 | 0 | 24 |
Норвегия | 15 | 52 | 0 |
Польша | 131 | 49 | 23 |
Португалия | 61 | 15 | 17 |
Словакия | 13 | 21 | 1 |
Испания | 134 | 244 | 6 |
Швеция | 19 | 67 | 7 |
Швейцария | 37 | 5 | 5 |
Великобритания | 67 | 114 | 62 |
Ричард К. Мейнингер, PE, – инженер-строитель, изучающий дорожные работы, в группе по материалам дорожного покрытия в Управлении исследований и развития инфраструктуры FHWA. Базируясь в Исследовательском центре Turner-Fairbank Highway Research Center в Маклине, штат Вирджиния, в основные обязанности Майнингера входит управление исследовательскими проектами, связанными с бетоном и заполнителями, в лабораториях центра, а также проектами сторонних исследователей. У него М.С. и Б.С. степени в области гражданского строительства Университета Мэриленда, Колледж-Парк.
Стивен Дж. Стоковски, П.Г., — технолог по агрегатам и специалист по петрографии в SES Group & Associates, LLC, подрядчике FHWA в исследовательском центре Turner-Fairbank Highway. У него есть М.С. по геологии Школы горного дела и технологий Южной Дакоты в Рапид-Сити, Южная Дакота, и степень бакалавра наук. по геологии Университета Джорджа Вашингтона в Вашингтоне, округ Колумбия.
Для получения дополнительной информации свяжитесь с Ричардом Майнингером по телефону 202-493-3191 или по электронной почте richard. [email protected] или со Стивеном Стоковски по телефону 202-49.3-3403 или [email protected]. См. также Совокупную доступность ресурсов в континентальных Соединенных Штатах, включая предложения по решению проблем нехватки, качества и окружающей среды (отчет Open-File 2011-1119), доступный по адресу http://pubs.usgs.gov/of/2011/1119.
Авторы хотели бы отметить вклад следующих комитетов TRB, организовавших семинар: Дороги с малой интенсивностью движения (AFB30), Исследование и классификация горных пород (AFP20) и Минеральные заполнители (AFP70).
Продукция — Jurgensen Companies
Уже более 85 лет мы являемся предпочтительным поставщиком асфальтобетонных покрытий и заполнителей. Мы обслуживаем как государственные учреждения, так и частные компании в Индиане, Кентукки и Огайо.
ОНЛАЙН-ЗАЯВКА НА КРЕДИТ
Наши агрегаты регулярно используются для больниц, школ, церквей, мостов, стадионов или других инфраструктурных проектов.
Асфальтобетонные изделия Jurgensen создают покрытия, которые легко обслуживать и быстро возводить, обеспечивая при этом безопасную, плавную и бесшумную езду.
Наши геотекстили и георешетки можно использовать для стабилизации, дренажа и гидроизоляции. Эти продукты удовлетворят все ваши потребности в строительстве.
Заполнители
9
Мы предлагаем различные продукты из щебня, песка и гравия в процессе дробления, просеивания и промывки.
9
Расположен в центре, всего в нескольких минутах от I-75 и I-70, мы загружаем самосвалы и самосвалы. Мы даже наполняем специальные разбрасыватели сельскохозяйственной извести, а также продаем ее в мешках по 50 фунтов.
9
Мы являемся экспертами в производстве измельченной 100% натуральной извести с высоким содержанием кальция и низким содержанием магния.
9
Мы гордимся тем, что производим переработанные продукты, которые не только безопасны для окружающей среды, имеют высокое качество и готовы к использованию в строительстве.
Мы являемся ведущим производителем строительных материалов в Огайо, Индиане и Кентукки. Мы поддерживаем сообщества, в которых мы работаем, предоставляя материалы, необходимые для качества жизни. На 16 предприятиях в основном производят щебень, песок и гравий. Независимо от того, является ли проект больницей, школой, церковью, мостом, стадионом или другим инфраструктурным проектом, для выполнения работы используется заполнитель.
Jurgensen Aggregates управляет распределительными предприятиями в Огайо, Индиане и Кентукки.
Наши заполнители используются в самых разных областях строительства, включая асфальт, бетон, жилое и коммерческое строительство. Они также используются в сельскохозяйственных и экологических целях. Размер нашей продукции варьируется от каменной наброски, крупных камней, используемых для борьбы с эрозией, до извести, мелкой пыли, используемой фермерами для нейтрализации кислотности почвы.
Заполнители продаются по размеру в зависимости от области применения. Технологии производства включают взрывные работы, дноуглубительные работы, дробление и сортировку для удовлетворения потребностей наших клиентов. Наши лаборатории контроля качества отслеживают и проверяют наши производственные материалы для проверки качества и градации. Мы также являемся основным поставщиком наполнителей из карбоната кальция, которые производятся в одном месте (Piqua Materials) методами измельчения и воздушной классификации. Эти наполнители широко используются в мастиках, пластмассах, армированных волокном, и во многих других областях. Jurgensen Aggregates продолжает расширять свою деятельность, добавляя новейшие технологии и доступное оборудование. Наша команда хорошо обучена и твердо привержена отличному обслуживанию клиентов и их удовлетворенности
Асфальт и эмульсии
9
Пористое асфальтовое покрытие повышает эффективность управления ливневыми стоками за счет устранения необходимости в традиционных системах трубопроводов.
9
Наша технология теплых смесей обеспечивает экологически чистое асфальтовое покрытие.
9
Компания Jurgensen является эксклюзивным производителем и дистрибьютором Trackless Tack. Trackless Tack — это усовершенствованная эмульсионная клейкая смесь для асфальта, специально разработанная для чрезвычайно быстрого высыхания.
Протяженность дорог и автомагистралей с твердым покрытием в Соединенных Штатах превышает 2,6 миллиона миль. Девяносто три процента из них покрыты асфальтом. Многие из них представляют собой асфальтовые покрытия на всю глубину; другие представляют собой асфальтовые покрытия, используемые для восстановления характеристик изнашивающихся бетонных покрытий.
Асфальт — самый перерабатываемый материал в Америке. Восстановленный асфальт можно использовать не только как «черный камень» — битумный цемент в восстановленном дорожном покрытии реактивируется, чтобы стать неотъемлемой частью нового дорожного покрытия. Переработанный асфальт 9Цемент 0003
заменяет часть нового асфальтового вяжущего, необходимого для дорожного покрытия, что снижает затраты дорожных агентств.
Асфальтовые покрытия просты в уходе, быстро возводятся и обеспечивают безопасную, плавную и бесшумную езду. Асфальтовые покрытия просто обеспечивают высочайший уровень управляемости по самой экономичной цене.
Геотекстиль и ткани
9
Мы предлагаем георешетки, которые обычно используются для укрепления подпорных стен, а также подстилающих оснований или грунтов под дорогами или сооружениями.
9
У нас есть стандартный или тяжелый геотекстиль для различных применений
9
Это геотекстиль промышленного стандарта, выполняющий функции разделения и стабилизации в маргинальных почвенных условиях, который вы можете приобрести непосредственно у нас.
9
Компания Jurgensen предлагает мембраны с отслаивающейся и наклеиваемой лентой, используемые в качестве барьеров для влаги и гасителей напряжения при укладке дорожного покрытия.
9
Мы также продаем верхние ткани, используемые для продления срока службы новых асфальтовых покрытий.