Производство графитированных электродов
Во всем мире графитированные электроды применяют в отраслях промышленности, где для технологических целей необходимо постоянно нагревать вещества или среду. Способность изделий проводить электрический ток при экстремально высоких температурах позволяет использовать их везде, где выпуск продукции связан со сложными и опасными производственными процессами.
Графитированные электроды выпускают из углеродосодержащего сырья: каменного угля, графита, антрацита, отходов плавления стали. Пройдя специальную обработку, они выдерживают температуры до +3000-3500оС. В сочетании с электропроводностью и термостойкостью это делает их незаменимыми в металлургической, химической промышленности, судостроении, других отраслях хозяйства.
Виды и маркировка графитированных электродов
Графитовый неплавкий электрод – изделие цилиндрической формы длиной 1000-2700 мм, диаметром 75-708 мм. По краям есть готовые ниппельные гнезда с конической, трапециальной или цилиндрической резьбой для ввинчивания ниппеля. Это помогает нарастить длину изделия по мере его расхода при плавлении стали.
Маркировка графитированных электродов:
Э – электрод; Г – графитированный; П – пропитанный, в основном пеком; С – специальный, для применения в разных сферах производства.
Популярные марки графитовых изделий:
- 1) ЭГ, предназначены для работы с электрическим током плотностью 25 А/см2, производятся из нефтесодержащего кокса, пека каменного угля. Используются в рудовосстановительных печах, электротермических аппаратах. В изделиях маркировки ЭГ-1 и ЭГ-2 разное только удельное сопротивлением.
- 2) ЭГС, выпускаются из игольчатого кокса, пека каменного угля. Используются в руднотермических и сталеплавильных печах, рафинировочных агрегатах.
- 3) ЭГП, графитированные с пропиткой. Основу составляет каменноугольный труднорастворимый пек, нефтяной кокс, пропитка – из пека. Используются в ферросплавных печах, для литья металла, аппаратах электродуговой сварки.
- 4) ЭГСП, изготовленные из игольчатого кокса, с пропиткой из пека. Применяются в руднотермических, электротермических агрегатах, электродуговых сварочных аппаратах.
Характеристики продукции
Графитированные электродов производят на основе угольных. У них есть схожие характеристики: низкое сопротивление, предельная чистота, повышенная стойкость к агрессивным химическим средам, но есть и отличия.
Особенности графитированных изделий:
обладают высокой упругостью, теплопроводностью, стоят дороже угольных, но качество на порядок выше; не трескаются при высоких температурах, обладают высокой электропроводность, причем при нагреве прочность материала повышается; используются в паре с любым присадочным металлическим материалом, легче угольных поддаются обработке, резке, сварка с ними быстрая, качественная; более устойчивы к окислению, воздействию химреагентов, включая хлорсодержащие вещества; используют при больших сопротивлениях тока, допустимый ток в 2-3 раза плотнее, чем у угольных; за счет сниженного удельного сопротивления снижаются расходы электродов при плавлении стали.
Заказать и купить
ООО «НПП АВЕРС» предлагает заказать и купить графитированные электроды от производителя. Сотрудничаем с физическими, юридическими лицами, отгрузка продукция возможна любыми партиями. Отправка осуществляется по России, в страны СНГ: Армению, Азербайджан, Беларусь, Молдавию, Киргизию, Казахстан, Туркменистан, Таджикистан, Узбекистан.
Если остались вопросы, звоните на номер: +7 (350) 220-94-94 или обратитесь по адресу: г. Челябинск, Троицкий тракт 486, офис 203.
Угольные (графитовые) электроды для сварки, резки и строжки. Работа на больших токах с удалением значительных слоев металла. Возможность сварки меди, латуни и бронзы. Соединение путем расплавления металла проводов, шин, контактов из меди и алюминия.
В 1882 году российский ученый Н. Н. Бенардос впервые в мире соединил металлические детали с помощью электродуговой сварки. В своей установке он использовал неплавящиеся угольные электроды и раздельную подачу присадочного материала и флюса. Основываясь на этом методе, Бенардос также разработал сварку в защитном газе и электродуговую резку. Через шесть лет была изобретена сварочная технология с использованием плавящихся электродов, которые со временем практически полностью вытеснили угольные. В настоящее время последние ограничены в своем применении тремя основными направлениями: удаление излишков металла, дуговая резка и сварка отдельных материалов.
На просторах российского интернета в статьях о сварочных технологиях нередко можно встретить такое название, как «графитовый электрод». Не вдаваясь в подробности причин этого явления, следует отметить, что ГОСТ не предусмотрено изготовление сварочных электродов из графита. Государственным стандартом регламентированы только графитовые спектральные электроды, применяемые для лабораторных исследований. Производители могут выпускать угольные и графитовые стержни как фасонные изделия по ТУ 1915-086–00200851, но таким образом, как правило, изготавливают только толстые электроды для разделки лома и обработки отливок.
Кроме того, металлургические предприятия, на которых применяют графитированные электроды для электродуговых печей, самостоятельно производят нестандартные сварочные электроды из обломков этих крупногабаритных изделий, которые, по сути, тоже можно назвать графитовыми.


Рисунок 1 — Графитовый электрод
Назначение угольных электродов
Угольные электроды, в основном, используются для заделки дефектов в поковках, литых заготовках и металлопрокате, снятия излишков металла с поверхности сварочных швов и массивных заготовок, а также при сварке отдельных видов металлов и их сплавов. Обычно их применяют при таких видах работ, как:
- устранение приливов, раковин и прочих дефектов;
- строжка корней сварочных швов;
- срезание прихваток и старой сварки;
- прожигание отверстий;
- срезание заклепок;
- сварка металлических заготовок с тонкими краями;
- сваривание цветных металлов;
- сварочное соединение жил и шин при электротехнических работах.
При срезании лишнего металла обычно применяют метод строжки — выдувание кипящего металла из сварочной ванны узконаправленным потоком сжатого воздуха (см. далее). Таким способом вычищаются каверны в литых заготовках и поковках, а также снимается дефектный слой металла со сварных швов.
Применение этих изделий для сварки цветных металлов, в основном, ограничено чугуном, медью и ее сплавами (см. таблицу).
№ | Материал детали | Материал присадочных прутков | Флюс | Доп. условия |
---|---|---|---|---|
1 | Медь | Оловянно-фосфористая бронза, кремнистая латунь и медь (М1 или МСр1). | Бура с добавками древесного угля, гидрофосфата натрия и кремниевой кислоты. | — |
2 | Бронза | Тот же, что и основное изделие. | Для оловянистых бронз — бура, для алюминиевых бронз — хлориды и фториды. | Перед сваркой прогреть до 250÷350 °C. |
3 | Латунь | Тот же, что и основное изделие. | — | Погружение конца угольного стержня в расплавленный металл, чтобы дуга была полностью окружена парами цинка. |
4 | Чугун | Чугунные прутки марок А и Б. | На основе буры. | — |
Сварка угольными электродами листового проката обычно производится без использования присадочных прутков, путем расплавления металла кромок заготовки. При этом толщина свариваемых листов обычно составляет 1÷2 мм, а их края соединяются или встык с отбортовкой (подогнутыми кромками) или внахлест.
Устройство и характеристики
Угольные электроды — это стержни круглого или прямоугольного сечения, изготовленные из электротехнического угля, который представляет собой смесь углерода (в виде кокса или антрацита), сажи и связующих веществ (каменноугольная смола или жидкое стекло). Круглые изготавливают методом экструзии и поставляются потребителям в виде стержней диаметром от 4 до 18 мм и длиной 250÷700 мм, а прямоугольные — методом прессования в формах. Помимо типоразмеров ГОСТ также применяются специальные стержни увеличенной толщины (15х15, 20х20 и т. п.), изготовленные по ТУ.
Угольные электроды намного дешевле и прочнее графитовых. Но удельное сопротивление электротехнического угля в несколько раз выше, чем у графита. Поэтому для улучшения электротехнических характеристик угольных стержней их поверхность покрывают медью.
В качестве примера в таблице приведены основные параметры круглых омедненных угольных электродов марки ВДК длиной 305 мм.
Диаметр (мм) | Рабочий ток (А) | Удаление металла (г/см) | Канавка (ширина/глубина) (мм) | Толщина реза (мм) |
---|---|---|---|---|
4 | 150÷200 | 10 | 6÷8/3÷4 | 7 |
6 | 300÷350 | 18 | 9÷11/4÷6 | 9 |
8 | 400÷500 | 33 | 1÷13/6÷9 | 11 |
10 | 500÷550 | 49 | 13÷15/8÷12 | 13 |
Обязательное условие применения этих изделий — выполнение работ только на прямой полярности. При обратном включении дуга очень неустойчива, качество шва из-за науглероживания металла получается низким, рабочая температура угольного стержня гораздо выше, что увеличивает скорость его испарения.
Виды угольных электродов
Нормативной базой для производства отечественных угольных электродов является ГОСТ 10720-75, содержащий описание трех типов таких изделий: ВДК, ВДП, СК, — которые могут выпускаться как омедненными, так и без покрытия. ВДК (воздушно-дуговые круглые) должны изготавливаться длиной 300 мм и четырех типоразмеров по диаметру. СК (сварочные круглые) — длиной 250 мм и шести типоразмеров по диаметру. ВДП (воздушно-дуговые плоские) — длиной 350 мм и двух сечений. По запросу заказчика разрешается изготавливать изделия СК с линейным размером до 700 мм.
Кроме отечественных электродов на российском рынке представлена продукция известных международных сварочных брендов и производителей из Восточной Азии. Шведский концерн ESAB предлагает свыше двадцати видов омедненных угольных электродов. Кроме изделий, используемых для сварки на постоянном токе прямой полярности, в номенклатуре ESAB присутствуют четыре типоразмера для сварки на переменном токе. А известный немецкий производитель сварочных принадлежностей ABICOR BINZEL, рекламируя свою продукцию, акцентирует внимание на том, что она изготовлена из «синтетического графита» (т. е. графитированного углерода). Вполне вероятно, что эти изделия спрессованы из порошка, полученного из остатков и лома металлургических графитированных электродов.
Помимо этого, на рынке присутствуют прессованные электроды из электротехнического и графитированного углерода, которые изготавливаются на заказ производителями угольных и графитовых изделий по ТУ 1915-086–00200851.
Как правило, они представляют собой прямоугольные стержни толщиной 10, 20, 30 и более миллиметров и применяются для объемных работ на больших сварочных токах: разделке металлургического лома, устранении прибылей на отливках, сквозной резке толстого металла и пр.
Советы по сварке
При сварке медных проводников следует помнить, что в первую очередь нужно подготовить и очистить свариваемые поверхности, а затем надежно их зафиксировать. Сварка медных проводов и шин осуществляется только в положении сверху вниз, т. к. расплавленная медь обладает повышенной текучестью. При этом используется флюс «борный шлак». Еще одной особенностью данного типа электродов является то, что процесс плавления у них почти неразличим, т. к. практически сразу начинается испарение (электротехнический уголь плавится при температуре 3800 °C, а испаряется — при 4200 °C).
Рекомендуемый угол заточки торцов угольных стержней — 60÷70°, но для сварки цветных металлов их необходимо затачивать под углом 20÷40°. Листовую медь толщиной до 4 мм можно сваривать без использования присадочных прутков (но с обязательной отбортовкой кромок), а свыше 4 мм — встык с присадочным материалом и разделкой кромок под углом 45°. Технология сварки латуни требует разделки кромок под углом 60÷70° с притуплением торцов на 1÷2 мм. Сварка производится путем погружения конца стержня, который должен быть полностью окутан парами цинка.


Рисунок 5 — Провода из латуни
Строжка угольным электродом
Строжка — это удаление узкого поверхностного слоя с использованием электродуговой сварки угольными электродами. Само слово ведет свое происхождение от глагола «строгать», т. к. этот процесс в чем-то аналогичен обработке пазов на строгальном станке. Технология строжки основана на разогреве металла электрической дугой до температуры кипения с последующим выдуванием его из сварочной ванны узконаправленным потоком воздуха. Строжка выполняется на глубины до десятков миллиметров, а ее производительность, зависящая от толщины угольного электрода и силы тока, измеряется в граммах удаленного металла на сантиметр канавки.
При выполнении строжки электрод под наклоном 30÷45° равномерно перемещают вперед, формируя канавку, которая на несколько миллиметров шире и глубже диаметра электрода. Строжка производится специальным воздушно-дуговым резаком, который имеет устоявшееся жаргонное название «строгач». Контактная пластина с соплами для подачи воздуха расположена на нижней губке строгача, поэтому поток воздуха направлен вдоль нижней части электрода в сторону сварочной ванны (см. рис. ниже). Подача воздуха должна прекращаться через несколько секунд после разрыва контакта электрода с металлом.


Рисунок 6 — Направление воздуха при сварке
Применение сварки угольными электродами для соединения электротехнических шин из меди и алюминия подробно регламентировано инструкцией «Росэлектромонтажа» И 1.08-08. Но там ничего не говорится о сварке проводов. Вместе с тем в интернете достаточно много фотографий, демонстрирующих использование такой сварки при монтаже электропроводки в обычных квартирах и офисных помещениях. Однако найти даже упоминание о нормативном документе, регламентирующем такую технологию, нам пока что не удалось. Если вам что-нибудь известно об этом, пожалуйста, напишите комментарий к этой статье.
Производство и назначение графитовых электродов
Для чего нужны графитовые электроды?
Графитовые электроды используются для изготовления стали методом электрической переплавки в дуговой сталеплавильной печи. Этот метод считается более благоприятным и удобным с точки зрения экологии, чем использование обычных плавильных печей.
В электродуговой печи для плавки стали располагаются три проводящих стержня, каждый из которых складывается из трёх графитовых электродов. Они передают электроэнергию в печь, которая и расплавляет лом и на выходе выдаёт сырую сталь. Графитовые электроды являются одной из основных составляющих такой печи.
Это расходные материалы. Со временем они изнашиваются и их нужно заменить на новые. И здесь появляется рынок с большими поставками и продажами таких материалов.
Почему цена на графитовые электроды повысилась?
В 2016 году цена графитовых электродов в среднем составляла менее 2.000 $ за одну тонну. И при такой стоимости мировые производители графита почти не зарабатывали деньги. Поэтому некоторые поставщики просто покинули рынок.
Кроме того, Китай серьёзно занялся вопросом закрытия нелегальных сталелитейных предприятий, которые загружают окружающую среду. Но эта сталь пользовалась спросом. Потому частично этот спрос удовлетворили производители, которые используют дуговые электроплавильные печи. Они производят сталь, практически не нанося вред окружающей среде. И конечно им нужен графит. Поэтому спрос на графит вырос.
Для производства графитовых электродов нужен игольчатый кокс, а в последнее время цены на этот ресурс выросли., так как он считается хорошим материалом для производства батарей, а также графитовых форм из Китая.
В целом цены на основное сырьё для производства графитовых стержней выросли. И с повышением цен покупатели начали нервничать и беспокоиться, из-за этого цены повысились ещё больше.
По большому счёту заметно сокращение объёмов предложения, усиление спроса и повышение цен на сырьё. Также стоит учитывать настроение участников рынка в отношении доллара. В связи с этим цены увеличились практически в 15 раз, начиная с 2016 года.
Привлекут ли высокие цены новых производителей?
Возможно, что из-за высоких цен на рынок выйдут новые производители графитовых электродов. Могут начать работу те предприятия, которые закрылись ранее из-за низких цен. Для этого потребуется не так много средств.
Но считается, что всё не так радужно, потому что участники рынка полагают, что в Китае имеются избыточные производственные мощности. И Китай уже начал собственное производство графитовых электронных стержней, что отпугивает многих и это отпугивает многих инвесторов в связи с сильной конкуренцией. Так что купить графитовые электроды теперь можно напрямую от производителя по оптимальной цене.
Во всё мире присутствует тенденция к более экологичному производству стали. Поэтому можно сделать вывод о том, что спрос на графит будет только расти.
Оцените статью: Поделитесь с друзьями!Не нашли то, что искали? Вернитесь к поиску планировок квартир по параметрам типового проекта. Поддержите проект, расскажите о tipdoma.com в социальных сетях:
Изготовление графитированных электродов
Каменноугольный кокс и антрацит – это основные компоненты электродной массы и угольных электродов для самоспекающихся электродов. Чтобы изго¬товить графитированные электроды используются малозольные нефтяной, пековый и сланцевые коксы.Введение в шихту искусственного и иногда естественного графита вместе с боем графитированных электродов позволяет повысить эксплуатационные свойства электродов. Использование средне и высокотемпературного каменноугольного пека позволяет связывать твердые компоненты шихты изделий из электродов, а при производстве электродной массы применяют чистый каменноугольный пек средней температуры или смесь пека с каменноугольной смолой.
Для производства электродных изделий сырые материалы дробят и прокаливают (кроме графита и обожженного боя) в трубчатых или ретортных печах с вращающимся барабаном. Это способствует увеличению их плотности, удалению основной массы летучих веществ, повышению механической прочности и электропроводности. После прокаливания материалы измельчают в мельницах различных видов и на дробилках, а затем рассевают их на вибрационных гро¬хотах или барабанных ситах.
После подготовки рассчитывают точную дозировку материалов, которая зависит от типа сырья и его гранулометрических составляющих. Затем материал вместе со связующим загружается в смесительные машины, при этом жидкие смола и пек заранее нагреваются для удаления частично летучих веществ и влаги. Тщательное смешивание при ~150 °С приводит к образованию однородной смеси – электродной массы. Эта масса используется для переработки на электроды либо выпускается в чистом виде для изготовления самоспекающихся электродов.
Для получения электродов на гидравлических прессах массу выдавливают через мундштук при давлении (50—200) • 105 Па (50—200 кгс/см2), которое зависит от сечения изделия.
Электроды в спрессованном состоянии охлаждаются при помощи воды на специальных рольгангах и обжигаются в секционных газовых печах непрерывного действия. В печах связующее становится коксом, благодаря чему резко увеличивается механическая прочность электродов, их термическая стойкость и электропроводность. Обжиг осуществляется при 1200—1300 °С в печи в специальной засыпке из мелкого коксика, которая препятствует сгоранию или деформации электродов. Длительность обжига колеблется в зависимости от величины и плотности изделий от 320 до 400 ч.
Графитированные электроды можно получить путем обжига заготовки в электрических печах сопротивления при 2500—3000 °С за 50—60 ч, при этом сами электроды и пересыпка — коксик фракции 10— 30 мм являются здесь сопротивлением. Процесс графитизации, с учетом этапов загрузки материала, его графитизации, остывания и разгрузки печи, занимает 7—10 сут. Это позволяет повысить электропроводность, химическая стойкость, теплопроводность, а также уменьшить твердость электродов.
После этого начинается механическая обработка электродов: обтачивается цилиндрическая поверхность, обрабатываются торцы и нарезаются ниппельные гнезда. Для ниппельного соединения используются ниппеля с винтовой нарезкой, ввинчиваемые в ниппельные гнезда в торцах электродов. Для угольных электродов иногда используется конический ниппель на одном конце, и коническое гнездо – на другом. Цилиндрические и конические ниппели используется у графитированных электродов (рис. 1). Ниппели изготавливаются из специальных заготовок с механической прочностью и высокой плотностью, получаемых благодаря пропитыванию обожженных заготовок пеком при давлении 5-106 Па (5 ат) и температуре 280—300 °С.
Рис. 1 – Соединение электродов при помощи цилиндрического (а) и конического (б) ниппелей (А – пековая пробка)
Для того чтобы улучшить качество эксплуатации графитированных электродов, могут быть использованы различные защитные покрытия, пропитывать различными солями или добавлять в массу различные вещества, уменьшающие окисление электрода. Благодаря этому расход электродов снижается на 20—30 %.
Современные высокотехнологические способы получения сталей и сплавов основываются на электродуговых процессах.
Электрическая дуга – явление, известное всем, кто хоть раз соприкасался с электричеством. Часто дуга возникает в местах разрыва электрических контактов и сопровождается ярким свечением. Это явление свидетельствует о возникновении в области электрической дуги чрезвычайно высоких температур (более 3000 С) и имеет важное практическое применение (создание мощного источника света, как например, в прожекторах или создание рабочей зоны для высокотемпературной обработки – плавки, сварки…).
Для обеспечения устойчивой электрической дуги применяют различные технические приемы. К ним относится использование графитовых электродов, к которым подводится электрический ток, например, в угольных электродуговых лампах нашедших широкое применение в прожекторах и кинопроекторах ХХ века. В промышленности и, особенно, в металлургии все намного масштабнее. Графитовые электроды, применяемые для создания электрической дуги в зоне плавки металла, иногда имеют диаметр до 1 метра.
Откуда же берутся такие уникальные изделия как графитовые электроды? Графитовые электроды производят из углеродосодержащих материалов на специальных электродных заводах в результате целого ряда технологических операций. Графит, из которого состоят электроды промышленного использования, называется искусственным и отличается от привычного многим графита в стержнях карандашей. Метод получения искусственного электродного графита был изобретен более 100 лет назад и носит название по имени изобретателя Ачесона – ачесоновский графит. Ачесон – американский исследователь (1856–1931), который пытался получить из распространенных форм углерода (кокса, угля) алмаз, но в итоге открыл метод получения искусственного графита, который используется и поныне.
Несмотря на такой солидный возраст метода и достаточно хорошо освоенную технологию получения ачесоновского графита, в настоящее время нет единой теории, объясняющей собственно физику превращения исходных материалов в графит. Не вызывает сомнений, что процесс производства искусственного графита является чрезвычайно «наукоемким».
Из чего же изготавливают искусственный графит? Исходными материалами являются нефтяной кокс и каменноугольный пек, которые смешиваются в заданной пропорции и затем проходят обработку в механических прессах, где им придается определенная геометрическая форма (часто цилиндрическая). Затем, выполняется предварительная высокотемпературная обработка (обжиг) при температурах около 1200 С. В результате обжига заготовки электродов приобретают определенную однородность, так как каменноугольный пек переходит в твердое состояние с внутренней коксовой структурой. После обжига заготовки электродов помещаются в специальную графитировочную печь. Через заготовки пропускают электрический ток большой мощности (сотни килоампер). Температура заготовок в середине печи достигает 3000 С. Кампания графитирования длится несколько дней, в течение которых электрический ток подводится по заранее разработанному регламенту. Общее количество электроэнергии, подведенной при графитировании может превышать 700 МВт∙час (иногда более 1 млн кВт∙час) за одну кампанию графитирования. Такое упрощенное описание технологического процесса, конечно же, не раскрывает научно-технические особенности всех его этапов (переделов – на языке производственников). Со времени изобретения и до сегодняшнего дня в технологический процесс производства графитовых электродов внесено много технических решений, изобретений, помогающих усовершенствовать сам процесс и конечную продукцию (графитовые электроды). Главным требованием к конечному продукту (графитовым электродам), которое предъявляют потребители-металлурги, является электрическое сопротивление собственно электрода. Чем выше это сопротивление, тем большая часть электроэнергии, которая пропускается через электрод, будет расходоваться не на технологический процесс, а на нерациональное преодоление электрического сопротивления электрода и, как следствие, рассеиваться в виде теплоты. Качество электродов у потребителей оценивается известным для специалистов значением удельного электрического сопротивления (УЭС) материала электродов. Для лучших образцов мирового уровня этот параметр достигает 3,5 мкОм•м; среднее значение, позволяющее производителю быть конкурентоспособным составляет 4,5…5 мкОм•м. Одним из главных технологических факторов, который обеспечивает низкие значения УЭС электродов является температура при графитировании. Проверено, что если значение минимальной температуры графитируемых заготовок в печи превышают 2600 С, то качество электродов будет заведомо высоким.
Если теперь перейти к оценке экономических показателей электродного производства, то очевидно, что процесс изготовления электродов является чрезвычайно затратным. Стоимость только электроэнергии, израсходованной на одну кампанию графитирования, может достигать десятков тысяч долларов. Отсюда, любое, сколь бы малым оно ни было, сокращение затрат электродного производства может дать ощутимый экономический эффект.
Вся продукция производится на основе углеродосодержащего сырья – антрацита, каменного угля и др., а также их производном – коксе. Эти материалы, будучи соответствующим образом обработанными, обладают очень важным свойством – способностью выдерживать высокие температуры. Достаточно сказать, что графит при отсутствии доступа воздуха может выдерживать температуры до 3000 С. Уникальное сочетание физических свойств – высокая электропроводность и термостойкость делает углеродосодержащие материалы безальтернативными в металлургическом производстве. Их также применяют как теплозащитные (в качестве футеровки высокотемпературных зон) и, одновременно, электропроводные материалы при производстве алюминия и магния, как футеровочные в доменном производстве и т.д. Сегодня ученые открывают все новые и новые свойства углерода и углеродосодержащих материалов, находя им, практическое применение в, казалось бы, невозможных для этих материалов областях – это суперсовременные корпуса военных самолетов, нано-материалы в микроэлектронике и пр.
Где рождаются угольные электроды — ZAVODFOTO.RU
Продолжая рассказывать про самые передовые и смелые предприятия (которые не бояться блогеров и чувствуют тренды) в нашей стране, никак нельзя пропустить крупнейший в России электродный завод, причём он же и самый молодой в отрасли, я про Новосибирский электродный завод хочу рассказать сегодня. Он находится в посёлке Линёво в Искитимском районе Новосибирской области, а это в 79 км к югу от Новосибирска. Предприятие специализируется на выпуске графитированных электродов марок ЭГСП, ЭГП и ЭГ, угольных электродов, катодных блоков, кокса нефтяного прокаленного и электродной массы. Вся эта продукция используется для производства алюминия, выплавки стали, в металлургии чистых металлов, в химической промышленности, в машиностроении и энергетике.
Осенью 1963 года к юго-востоку от станции Евсино, в степи, вешками было обозначено начало строительства Новосибирского электродного завода. Изначально предлагалось две площадки, где появится этот гигант – одна в районе Бердска, другая, как раз в районе станции Евсино. Почему именно здесь? Тут всё просто. Дело в том, что сырьём для угольных электродов служит антрацит, а его здесь было очень много, поблизости находится Горловское месторождение, а оно входит в тройку лучших в мире. И вот 3 августа 1965 года стройке был объявлен зелёный свет. В 1966 году на стройку из Новочеркасского электродного завода приехал главный инженер Алексей Обудовский. Это был первый специалист электродщик в этих местах.
2. Склад антрацита
В качестве сырья для изготовления угольных электродов используются антрацит, нефтяной кокс и искусственный графит собственного производства. Сырье на Новосибирском электродном заводе хранится на закрытых складах раздельно по типам и маркам.
3. Склад №1 хранения нефтяного кокса
Параллельно с заводом, рос и рабочий посёлок для будущих работников завода. В 1968 году здесь ввели в строй первые значительные объекты: два жилых дома и скважину, которая давала воду, медпункт, школу, котельную, детский сад и столовую. Матушка природа периодически испытывала строителей, так, например, зимы 1968 и 1969 года отличились температурами под — 55°, но в итоге слабаков тут не оказалось… В 1972 году состоялся частичный ввод мощностей нового электродного завода.
4. А здесь довольно мило, теперь понимаю, почему меня сюда так долго не пускали, боялись, что я все яблоки у них съем :).
5. Далее мы попадаем в прокалочный цех.
Прежде чем приступить к производству угольных электродов, сырьё (антрацит и нефтяной кокс) вначале подвергают кальцинации, т.е. прокаливанию при высокой температуре. Прокаливание необходимо для того, чтобы удалить влагу и другие ненужные вещества, а также предать необходимую прочность и электропроводность. Вот в таких прокалочных печах всё и происходит, а там, между прочим, ой, как горячо, примерно 1300 °С.
6.
Вращающая прокалочная печь из себя представляет стальной барабан, внутри футерованный, т.е. специально отделанный огнеупорным кирпичом и установленным под углом 3,5 градусов к горизонту. В нижнем торце барабана («горячая головка») установлена газовая гарелка, а также через него производится и выгрузка прокаленного материала. Через верхний же торец барабана («холодная головка») производится загрузка прокаленного материала и отводятся отходящие газы. Сам барабан печи установлен на специальных роликоопорах и приводится во вращение электродвигателем через венцовую шестерню. Именно за счёт этого вращения и наклонного расположения печи и происходит перемещение прокаливаемого материала вдоль печи. Прокалочная печь имеет четыре скорости вращения от 0,7 до 2,1 оборота в минуту. Это позволяет регулировать время нахождения материала в печи и соответственно степень прокаливания материала. Длина печи составляет 60 м.
Прокаленный материал после печи попадает в холодильник, который представляет собой тоже металлический барабан, установленный на роликоопорах под углом 1,5 градуса к горизонту, при этом его горячая головка расположена выше холодной. Барабан вращается также при помощи электродвигателя. Корпус холодильника орошается водой для более эффективного охлаждения.
7.
Электрокальцинатор. Температура обработки в электрокальцинаторе достигает 1800 °С. Он также задействован в операции прокаливания. Из себя он представляет печь сопротивления, где тепловыделяющим элементом служит прокаливаемый материал, через который пропускается электрический ток. Работает он в постоянном режиме. Электрокальцинатор состоит из металлической шахты, внутри выложенной огнеупорным кирпичом, также имеются два токоподвода. Верхним токоподводом служит электрод, расположенный по оси шахты, а в качестве нижнего токоподвода используется угольный электрод, навинченный на водоохлаждаемый фальшниппель, расположенный также вдоль оси шахты. Расстояние между токоподводами составляет 2-2,5 м.
8.
9.
10. Управление всеми процессами прокаливания осуществляется отсюда.
11.
12. Каменноугольный пек поступает на завод в жидком виде в вагон-цистернах, собственно, одна такая прямо перед нами.
13.
14.
3 июля 1974 года Министерство цветной металлургии СССР издало приказ «О создании Новосибирского электродного завода». Этот день и стал официальной датой рождения нашего сегодняшнего предприятия.
15.
16.
В целях мотивации и ускорения процесса, в 1976 году завод был объявлен всесоюзной ударной комсомольской стройкой. И как это обычно было тогда, сюда со всех концов нашей страны стали массово приезжать строители, монтажники, водители, крановщики и т.д. Как результат, уже 26 сентября 1977 года была разожжена первая печь цеха обжига, а 1 ноября 1977 года была выпущена первая электродная масса. В связи с этим был подписан акт Государственной комиссии «О приеме промышленных мощностей НовЭЗа». Дальше больше – в 1978 году запустили цех механической обработки углеграфитовых изделий (в настоящее время ЦМОЭП), 19 апреля 1979 года был отпрессован первый подовый блок, а 10 октября 1982 года — получена первая графитовая заготовка.
17.
В 2006 году завод попадает под крыло Группы Энергопром, что позволило предприятию дальше расти и успешно развиваться. Кстати, в состав Группы компаний «Энергопром» входят ещё два электродных завода — Челябинский и Новочеркасский, а также ООО «Донкарб Графит» (площадки в Новочеркасске и Челябинске). Сегодня, как и раньше, Новосибирский электродный завод является градообразующим для посёлка, а также вносит существенный вклад в целом в экономику Новосибирской области. Выпускаемый ассортимент довольно широк: это крупногабаритные угольные электроды, электроды графитированные и ниппели, катодная продукция, блоки угловые и боковые, антрацит прокаленный, доменные блоки, масса электродная, масса холоднонабивная низкоусадочная, фасонные и мелкофасонные изделия, нефтяные прокаленные коксы. Между прочим, свыше 60 % стран мира охотно покупают их продукцию.
18.
19. Рядом по соседству находится ещё одно крупное предприятие — Сибирский Антрацит. Я к ним тоже напрашиваюсь, может и у них когда-нибудь побываю. А так эта компания- ведущий в России и в мире производитель высококачественного антрацита Ultra High Grade (UHG). Именно они как раз и ведут добычу угля на месторождениях Горловского угольного бассейна в Искитимском районе Новосибирской области. Предприятие объединяет 2 угольных разреза и 2 обогатительные фабрики.
Далее мы попадаем смесильно-прессовый цех, где производится размол, рассев прокаленных материалов по заданной рецептуре и составу, а также смешивание определенных фракций и прессование заготовок.
20.
Этот цех занимает целое здание в несколько этажей (44 метра вверх и ещё 4 метра вниз), где сырье, как на американских горках, то поднимается вверх, то также стремительно падает вниз, потом снова вверх и так до тех пор, пока не придёт к нужной кондиции. Итак, первоначально мы поднимаемся вверх.
Вкратце техпроцесс выглядит следующим образом. Прокаленный материал, поступивший сюда, поступает вначале в бункера запаса и потом по трансп
ГОСТ, отличие от угольных, применение и т. д.
Соединить элементы из стали и сплавов можно при помощи сварки. Для проведения процедуры используют расходные материалы, свойства которых соответствуют характеру выполняемых работ — например, графитовый электрод. Соединения, созданные таким способом, получаются прочными, отличаются хорошей электропроводимостью, долговечны.
Производственный процесс и ГОСТы
Электроды с графитным покрытием производят в соответствии с ГОСТ Р МЭК 60239-2014. Для их изготовления применяют малозольный кокс нефтяной, к которому присоединяют электродный бой — примерно десятую часть от общей массы. Для связывания составляющих используют каменноугольный пек.
Для получения продукции исходные материалы дробят, накаливают, подвергают измельчению. Затем их распределяют на фракции, дозируют, перемешивают с добавлением скрепляющего материала.
После получения электродной массы ее загоняют под пресс, в результате получают «зеленые» электроды. Их высушивают, отправляют на обжиг, выполняют графитизацию и механическую обработку.
После проведения обжига электродов в соответствии с технологией связующее вещество становится коксом. У него меняются свойства, повышается электро- и теплопроводность, улучшается механическая сопротивляемость.
Процесс графитизации выполняется при температуре +2700…+2900ºС, по времени может занять 100 или более часов. Для нагревания применяют электроды и углеродистую засыпку, которая обеспечивает защиту от окисления.
После окончания технологического процесса образуется графит с кристаллической структурой, примеси восстанавливаются и улетучиваются. Характеристики твердости и электросопротивления понижаются, что способствует улучшению процесса механической обработки. Чтобы замедлить скорость расходования изделий, выполняется пропитывание специальными веществами, помогающими защититься от окисления.
Покрытия, выполненные на основе кремния, железа и алюминия, образуют защитную пленку из оксидов. Это уменьшает потери в результате окислений. Использование алюминия помогает понизить сопротивление электродов, у тока плотность повышается и составляет 21-25 А/см².
Классификация электродов из графита
На современном рынке представлены разные марки графитированных изделий, которые отличаются по виду материала, использованному для изготовления. Это в основном графит, но качество его не одинаковое.
Используя разные сорта, получают такие изделия:
- Графитированные стержни для сварки.
- Коллоидно-графитовые изделия.
- Пропитанные — для комплексов «ковш-печь».
- Специальные — для работы с агрегатами высокой мощности, которые используют в крупной промышленности.
Чтобы технологические процессы проходили в нужной последовательности, подбирать материалы надо правильно. При этом учитывается, какой тип электродов подходит для процессов, осуществляемых на производстве.
Графитированные разновидности удобно применять на металлургических предприятиях. Такие электроды способны обеспечить ввод электрической энергии в процессах, которые связаны с повышенными температурами.
Состав электродов из графита и качественные свойства
Электроды для сварки из графита сконструированы из 2 рабочих частей, между которыми размещена прокладка. В состав основных элементов может входить прессованный уголь, алюминий и т.д. Особенность графитовых электродов заключается в способности без задержки проводить ток, стойком выдерживании повышенной температуры.
Прочие достоинства материалов таковы:
- Доступная цена.
- Не прилипают к изделиям при прогревании.
- Стойкость к появлению трещин.
- Небольшой период нагревания.
- Чтобы образовалась стойкая полноценная дуга, хватает силы тока в 5-10 А.
- Соединение термостойкое, не портится под действием коррозии.
Для проведения работ с использованием графитовых электродов могут применяться сварочные аппараты инверторного типа.
С примесью угля
Электроды из графита могут иметь в составе уголь или кокс с особым содержанием. У качественных изделий правильная форма, поверхность лишена трещин и дефектов. Во время проведения сварки они не растрескиваются.
Работу с использованием таких электродов осуществляют при постоянном токе прямой полярности. Дуга получается стойкой, длина — 6-15 мм. Угольные изделия для улучшения свойств и расширения области применения можно подвергнуть графитированию методом термообработки.
С добавлением меди
Для сваривания элементов из меди используется модификация с названием «карандаш». Это медно графитовый электрод, который производят в разных видах:
- Круглый — подходит для работы во многих сферах.
- Бесконечный, применяемый в качестве экономичного варианта.
- Плоский — с квадратным или прямоугольным сечением.
- Полукруглый — подойдет для выполнения резки.
- Полый — удобен для формирования канавок, строжки.
Разнообразие модификаций допускает расширение области использования изделий.
Плюсы и минусы использования
У графитного электрода можно перечислить такие достоинства:
- Повышенная стойкость к влиянию тока.
- Хорошая электропроводность, обеспечивающая минимум потерь расходных материалов.
- Нет окисления при повышении температуры, что увеличивает срок службы электрода.
- Не требуется применять при работе специальные держатели — достаточно простых.
Недостатки:
- Действие изделий ограниченное, для использования в особых условиях надо приобретать дополнительные материалы с разной формой наконечников.
- Диаметр стержней — от 6 мм, поэтому при необходимости выполнить тонкое соединение возникают сложности.
При выборе электродов надо руководствоваться условиями, в которых предстоит их использовать. Если свойства графитовых не подходят для выполняемых работ, нужно найти другой вариант.
Чем графит отличается от угля
Графитовые стержни для работ по свариванию проводов считаются более практичными, чем угольные. При обработке они удобнее и смогут обеспечить прочное, долговечное соединение.
У изделий с угольной обмазкой электропроводность ниже из-за повышенного сопротивления. Работа с ними требует от оператора наличия опыта, поскольку во время процесса образуется дуга с повышенной температурой, способная разрушить свариваемую скрутку.
Графитовые электроды серого цвета, с легким оттенком металла. Угольные — черного. Чтобы работать с ними, часто используют держатели. Это немного осложняет процесс сварки.
Для проведения сварочных работ с использованием инверторного аппарата, дополненного регулятором усиления, лучше выбирать расходные материалы из графита. Швы, полученные с их помощью, получаются более прочными, чем при сварке угольными электродами, у них высокая сопротивляемость к окислению.
Область применения графитированных электродов
Графитовые электроды нужны при разных операциях. Они применяются при проведении обработки поверхностей перед сваркой, резкой заготовок, зачистки кромок деталей из металла.
Их также используют при плавлении чугуна, сплавов, для дуговых печей. Наличие ниппелей облегчает соединение стержней между собой. Такая подготовка позволяет отладить подачу расходных материалов для сварки в печах.
Используя графитовые стержни для сварки медных проводов и дуговой резки, можно уменьшить количество брака и дефектов швов.
Они подходят и для проведения таких операций:
- Сварки элементов из цветного металла.
- Заваривания дефектов, полученных из-за нарушений технологии литья.
- Наплавления элементов из твердого сплава на металлическую основу.
Электроды для сварки могут использоваться с присадкой, которая подается во время проведения работ или помещается в место, где располагается шов.
Чтобы уменьшить окисление элементов во время сваривания, необходимо выполнить такие действия:
- Для печей обеспечить герметичность.
- Температуру поверхности электродов ограничить в допустимых пределах.
- Использовать защитные покрытия.
- Снизить длину нагретой части, тщательно продумывая размещение печного свода.
- Обеспечить улучшение свойств электродов.
Для работы со сверхмощными дуговыми печами допускается применение стержней из меди с наконечником из графита.
Расход электродов и регулирование тока при работе
Регулирование тока для сваривания проводов выполняют в диапазоне 30-120 А.
Точную мощность должен определить сварщик, руководствуясь следующими факторами:
- При соединении одной жилы с другой, если их диаметр составляет 1,5 мм, аппарат настраивают на 70 А.
- Если выполняется сварка 3 проводов с таким же сечением, должен быть установлен ток 81-91 А.
- Чтобы соединить 3 жилы 2,5 мм, настраивают силу тока на 81-101 А.
- Для 4 жил 3 мм ток надо установить на 101-121 А.
Результат, достигаемый при сварочных работах с использованием графитовых стержней, во многом зависит от опыта мастера.
Требования к безопасности при работе
Углеграфитовые электроды требуют соблюдения правил техники безопасности:
- Провода должны быть обесточены перед проведением сварки.
- Необходимо использовать средства индивидуальной защиты — это может быть специальная одежда и обувь, маска, перчатки.
- Участок, на котором выполняются работы, должен быть освобожден от легковоспламеняющихся предметов.
- После окончания сварочных работ выполняйте изоляцию скруток. Для этого применяется изолента или термоусадочные трубки. Их надевают на провода и прогревают с помощью фена.
Соблюдая такие рекомендации для сварки медных проводов, можно легко выполнять качественное соединение элементов.
Технология создания скруток с последующей сваркой
К участку, где скрутка выходит из изоляции, необходимо подсоединить металлический радиатор — это помогает не допускать плавления изоляции. Чаще других выбирают элементы из меди. Она обладает высокой теплопроводностью. Перед тем как начинать варить жилы проводов, надо выполнить подготовку.
Поверхность проводов зачищают от изоляции. Скрутка должна быть максимально плотной, чтобы витки находились в тесном контакте. Оптимальной длиной для нее считается 5-6 см.
Такие предосторожности облегчают сваривание скруток жил проводов с электродами для любых металлов.
Алюминиевые провода
Соединение алюминиевых проводов проводят с помощью флюса. Это порошок, помещенный внутрь проволоки, который способен расплавлять и продуцировать защитный газ. При таком способе сварные кромки защищены от окисления из-за контакта с кислородом.
Силу тока для проведения сварочных работ выставляют с использованием регулятора. Опытные мастера при выполнении соединений могут просто выжидать нужное время для удержания дуги.
Медные жилы
При выполнении скруток из медных жил концы их отрезают на одном и том же расстоянии.
Там, где радиатор будет фиксироваться к проводам, нужно присоединять зажим массы агрегата, затем подносить к подрезанным краям графитовый электрод. Контакт при этом не должен занимать много времени — оптимальной длительностью считают секунду. За этот период воздействия на месте окончания скрутки формируется расплавленный медный шарик.
Модели графитовых электродов
Графитированные электроды для электродуговых печей:
- ЭГС — в составе каменный пек, игольчатый кокс. Применяют такие материалы в основном для рафинировочных приборов.
- ЭГ — изготовлены с добавлением нефтяного кокса и каменноугольного пека. Такие электроды нужны в промышленной сфере, если плотность тока не превышает 25 А/см².
- ЭГП — электродный стержень, применяемый для резки. Состав как у ЭГ. Чтобы получить хороший результат, выполняется дополнительная пропитка изделия.
- ЭГСП — в состав входят каменноугольный пек, игольчатый кокс. Диаметры изделий могут различаться, от них зависит удельное электросопротивление.
В аббревиатурах буквы расшифровываются так: «Г» — графитированный стержень, «П» — пропитка, «Э» — электрод. «С» означает «специальный», такие изделия допускается использовать не в одной, а в нескольких сферах.
графитовый электрод — огнеупор Rongsheng
Описание
Описание графитового электродаГрафитовый электрод будет представлять собой высокотемпературный проводящий графитовый материал, сердцевина которого состоит из нефтяного кокса, каменноугольного кокса в качестве наполнителя, каменноугольной смолы в качестве связующего. Мы производим графитовые электроды и ниппели к ним. Графитовые электроды характеризуются низким сопротивлением, хорошей электропроводностью и теплопроводностью, высокой стойкостью к окислению и тепловому удару, высокой механической прочностью и т. Д.
Каталог
★ Применение графитового электрода
★ Классификация графитовых электродов
★ Графитовые электроды Фотографии продукта
★ Длина и диаметр и допустимое отклонение графитового электрода
★ Технические характеристики графитового электрода RP, HP, UHP
★ Технические характеристики графитового электрода высокой плотности (HD)
★ Технические характеристики квази-сверхвысокового графитового электрода (EGPK-SHP)
★ Преимущества графитового электрода
★ Использование графитового электрода
★ Наши предложения перед подключением электрода
★ При подключении электродов, пожалуйста, обратите внимание
★ Применение графитового электрода
★ Применение графитового электрода
1 для дуговой печи EAF;
2 для рудно-термической печи; для печи сопротивления;
3 для производства профилированных графитовых изделий;
4 для производства фасонных графитовых изделий.
Диаметр электродов: от 75 до 800мм. Мы можем изготовить различные спецификации в соответствии с требованиями заказчика.
Наши преимущества: Производитель из Китая; Купить напрямую с завода; Высококачественные продукты; Выгодная цена.
★ Классификация графитовых электродов
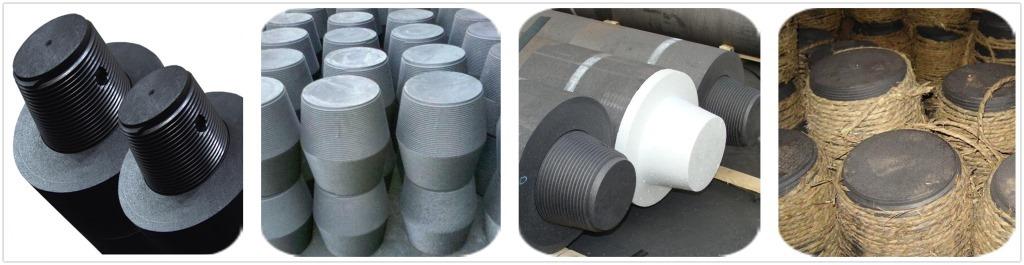
★ Длина & Диаметр & Допустимое отклонение o f Графитовый электрод
Номинальный диаметр | Фактический Диаметр | Длина (мм) | допуск | ||||
мм | дюймов | мак | шахты | Минимальный размер черной части | Длина | короткая длина | |
75 | 3 | 78 | 73 | 72 | 1400/1600 | ± 100 | -275 |
100 | 4 | 103 | 98 | 97 | 1400/1600 | ||
130 | 5 | 132 | 127 | 126 | 1400 | ||
150 | 6 | 154 | 149 | 146 | 1400/1600/1800 | ||
175 | 7 | 180 | 174 | 172 | 1400/1600 | ||
200 | 8 | 205 | 200 | 197 | 1600/1800 | ||
225 | 9 | 230 | 225 | 222 | 1600/1800 | ||
250 | 10 | 255 | 251 | 248 | 1600/1800 | ||
300 | 12 | 307 | 302 | 299 | 1600/1800/2000 | ||
350 | 14 | 357 | 352 | 349 | 1600/1800/2000 | ||
400 | 16 | 409 | 403 | 400 | 1600/1800/2000/22000 | ||
450 | 18 | 460 | 454 | 451 | 1600/1800/2000/22000 | ||
500 | 20 | 511 | 505 | 502 | 1600/1800/2000/22000 | ||
550 | 22 | 562 | 556 | 553 | 1800/2000/2200/2400 | ||
600 | 24 | 613 | 607 | 604 | 2000/2200/2400/2700 | ||
650 | 26 | 663 | 659 | 656 | 2000/2200/2400/2700 | ||
700 | 28 | 714 | 710 | 707 | 2000/2200/2400/2700 |
★ Технические характеристики графитового электрода RP, HP, UHP
Имя | Единица | Номинальный диаметр | ||||||
UHP сверхвысокой мощности | HP Superstrong | RP обычная мощность | ||||||
≤Φ400 | ≥Φ450 | ≤Φ400 | ≥Φ450 | ≤Φ300 | ≥Φ350 | |||
Удельное сопротивление | Электрод | Ом · м | ≤5.5 | ≤6,5 | ≤8,5 | |||
Ниппель | ≤4,5 | ≤5,5 | ≤6,5 | |||||
Прочность на изгиб | Электрод | МПа | ≥11,0 | ≥10,5 | ≥9,8 | ≥8,5 | ≥7.0 | |
Ниппель | ≥20.0 | ≥16,0 | ≥15,0 | |||||
модуль упругости | Электрод | ГПа | ≤14,0 | ≤12,0 | ≤9,3 | |||
Ниппель | ≤18,0 | ≤16,0 | ≤14,0 | |||||
Плотность | Электрод | г / см3 | ≥1.66 | ≥1,67 | ≥1,62 | 1,6 | ≥1,53 | ≥1,52 |
Ниппель | ≥1,75 | ≥1.73 | ≥1.69 | |||||
Коэффициент Теплового Расширения | Электрод | 10-6 / ℃ | ≤1,5 | ≤2,4 | ≤2,9 | |||
Ниппель | ≤1.4 | ≤2,2 | ≤2,8 | |||||
золы | % | ≤0,3 | ≤0,3 | ≤0,5 | ||||
Примечание: 1.Kefifientent содержание золы и тепловое расширение в качестве эталонного индекса, коэффициент теплового расширения (100 ℃ ~ 600 ℃), изготовление на заказ. |
★ Технические характеристики графитового электрода высокой плотности (HD)
Имя | Единица | Номинальный диаметр | ||||||
75-200 мм | 250-300 мм | 400-500 мм | ||||||
высший сорт | первый класс | высший сорт | первый класс | высший сорт | первый класс | |||
Удельное сопротивление (не более) | Электрод | Ом · м | 8.0 | 9,0 | 8,0 | 9,0 | 8,0 | 9,0 |
Ниппель | 7,5 | 7,5 | 7,5 | |||||
Прочность на изгиб (не менее) | Электрод | МПа | 10 | 9 | 8 | |||
Ниппель | 13 | 13 | 13 | |||||
Модуль упругости (не более) | Электрод | ГПа | 12 | 12 | 12 | |||
Ниппель | 14 | 14 | 14 | |||||
Плотность (не менее) | Электрод | г / см3 | 1.58 | 1,58 | 1,58 | |||
Ниппель | 1,68 | 1,68 | 1,68 | |||||
Коэффициент теплового расширения (не более) | Электрод | 10-6 / ℃ | 2,7. | 2,7. | 2,7. | |||
Ниппель | 2,5 | 2.5 | 2,5 | |||||
Зольность (не более) | % | 0,3 | 0,3 | 0,5 | ||||
Примечание: 1. Коэффициент зольности и теплового расширения в качестве справочного показателя. |
★ Технические характеристики квази-сверхвысокового графитового электрода (EGPK-SHP)
Наименование | Единица | Номинальный диаметр (мм) | ||
300, 350, 400 | 450, 500 | |||
Удельное сопротивление (не более) | Электрод | Ом · м | 6.2 | 6,5 |
Ниппель | 5,5 | 5,5 | ||
Прочность на изгиб (не менее) | Электрод | МПа | 10,5 | 10 |
Ниппель | 16 | 16 | ||
Модуль упругости (не более) | Электрод | ГПа | 14 | 14 |
Ниппель | 18 | 18 | ||
Плотность (не менее) | Электрод | г / см3 | 1.65 | 1,64 |
Ниппель | 1,72 | 1,7 | ||
(не более) | Электрод | 10-6 / ℃ | 1,5 | 1,5 |
Ниппель | 1,4 | 1,4 | ||
Зольность (не более) | % | 0.3 | 0,3 | |
Примечание: 1. Зональность как справочный индекс. |
Если у вас есть какие-либо требования, пожалуйста, свяжитесь с нами. Наши инженеры помогут вам и предоставят соответствующие консультации.
★ Преимущества графитового электрода
1 Процесс производства графитовых электродов прост, высокая эффективность, небольшие потери графита
2 Высокая скорость обработки, снижение затрат на производство
Доступны 3 различных размера, включая большой диаметр
4 Наши графитовые электроды очень долговечны и имеют длительный срок службы
★ Использование графитового электрода
1 Для дуговых печей дуговых электропечей.Графитовые электроды чаще всего используются в углеплавильной электропечи.
2 Для замкнутой дуги
3 Для резисторной печи
4 Для производства графитовых изделий. Заготовка из графитового электрода также используется для обработки различных тиглей, форм, лодок и нагревательных элементов и других графитовых изделий. Например, в промышленности кварцевого стекла для каждого производства 1 тонны электрической плавильной трубки требуется графитовый электрод 10 м, для каждого кварцевого кирпича в 1 тонну необходимо потреблять 100 кг графитового электрода.
★ Наши предложения перед подключением электрода
1 Пожалуйста, сначала проверьте внутреннюю резьбу электрода. Если нить не повреждена, обратитесь к продавцу, чтобы проверить, может ли электрод работать должным образом.
2 Пожалуйста, очистите электроды сжатым воздухом перед подключением.
3 Когда электрод вдавливается в отверстие электрода на одном конце, на другом конце можно подготовить прокладку, чтобы избежать поломки ниппеля.
★ Когда Подключение t he Электроды, обратите внимание
1 медленно падают, когда новый электрод находится прямо над отверстием, соединенным с электродом.
2 Поместите изолятор между двумя электродами, и электрод медленно опускается, чтобы предотвратить разрыв электродного отверстия и резьбу ниппеля.
3 Слегка поднимите новый электрод, затем снимите изолятор, соедините два электрода.
4 Затяните электроды с помощью правильного гаечного ключа и указанного крутящего момента.
Что такое графитовый электрод?
Графитовый электрод , проводник, который выделяет электрическую энергию в форме электрической дуги, используется для нагрева и расплавления стальных отходов в электродуговой печи. В настоящее время они являются единственными продуктами с высокой электрической проводимостью и способны поддерживать чрезвычайно высокую выработку тепла в этой сложной среде. В связи с растущим спросом на качественную сталь в аэрокосмической, автомобильной и электронной промышленности графитовые электроды также становятся все более популярными.
Почему графитовый электрод?

- Графитовый материал обладает лучшей электрохимической стабильностью. Этот тип электрода имеет низкий коэффициент потерь.
- Графитовый электрод прост в обработке, а скорость обработки, очевидно, выше, чем у медного электрода.
- графит имеет малый вес и хорошую тепло- и электропроводность.
Графитовый электрод , имеющий вышеуказанные незаменимые эксплуатационные преимущества, играет незаменимую роль в области высокотемпературного производства, такого как выплавка чугуна и стали, электролитический алюминий, ферросплав, карбид кальция, промышленная плавка кремния и желтого фосфора.
В зависимости от мощности электропечи, нагрузки на трансформатор, разницы сырья, используемого при производстве электродов, и физико-химических показателей готовых электродов, графитированные электроды делятся на три типа:

UHP Графитовый электрод.
Изготовлен из высококачественного игольчатого кокса и обработан методом продольной графитизации (LWG). Температура графитизации может быть до 2800 ° C — 3000 ° C. Готовые изделия имеют меньшее электрическое сопротивление и линейное расширение, хорошую стойкость к тепловому удару и большую плотность тока.
Узнать больше
л.с.
В качестве сырья используется качественный нефтяной кокс или игольчатый кокс низкого качества. Его физические и механические свойства выше, чем у графитового электрода RP, например, более низкое электрическое сопротивление и позволяет большую плотность тока.
Узнать больше
RP Графитовый электрод.
Нефтяной кокс обычного качества принят для производства. Этот тип графитового электрода обработан при низкой температуре графитизации.Допустимая плотность тока ниже, чем у графитового электрода высокого давления. Графитовые электроды обычной мощности указаны с допустимой плотностью тока менее 17 А / см 2 .
Узнать большеОсновные приложения

EAF сталеплавильного производства.
EAF сталеплавильное производство является основной областью применения графитового электрода. Производство электродуговой сталеплавильной стали в Китае составляет около 18% сырой стали. 70% — 80% потребления графитового электрода используется при производстве стали ЭДП.При выплавке стали в ЭДП графитовый электрод используется для подачи электрического тока в печь. А высокотемпературный источник тепла для плавки генерируется дугой между электродом и стальным ломом.

Дуговая печь под флюсом
Дуговая печь под флюсом в основном используется для производства промышленного желтого фосфора и кремния. Требуется использовать графитовый электрод для погружной электропечи с высокой плотностью тока. Для производства 1 т кремния требуется около 100 кг графитового электрода, а для производства 1 т желтого фосфора — около 40 кг графитового электрода.

LF (Ковш-Печь)
Ковшовая печь установлена на сталелитейном заводе EAF. После того, как шлак перемешан, используется ковш-печь для выполнения задачи дальнейшего восстановления и рафинирования. Обычно графитовые электроды используются для трехфазных печей переменного тока.
Основные факторы, влияющие на потребление графитового электрода в EAF Steelmaking

- Основными причинами потери и потребления графитовых электродов являются перегрузка и время ожидания.
- Низкое качество или неправильная пропорция лома приводит к плохому шлакообразующему эффекту и увеличивает время плавки.
- Увеличение времени подачи приводит к более высокой вероятности повреждения дна электрода и разрушения.
- Оборудование для электропечи не соответствует спецификациям электродов.
- Выбор кривой мощности и передачи, управление напряжением и током пусковых и стабилизирующих дуг, использование длинных, средних и коротких дуг и конфигурация системы водяного охлаждения важны для срока службы и потребления электродов.
- Качество самого графитового электрода влияет на коэффициент расхода. В настоящее время плавка и процесс электродуговых печей предъявляют более высокие требования к антиокислительным свойствам и термостойкости графитовых электродов. Кроме того, пользователи очень обеспокоены высоким потреблением, вызванным колебаниями качества. Следовательно, однородность и стабильность графитового электрода являются наиболее важными факторами, определяющими расход.
Описание
Графитовый электрод л.с. является проводящим элементом для электродуговых печей. Он изготавливается из нефтяного кокса, игольчатого кокса, каменноугольного пека и производится в результате ряда строгих производственных процессов. Сильноточные линии вводят через порт графитового электрода внутри корпуса печи. Это высвободит электрическую энергию в дуговой печи для нагрева печи.
Спрос на электроды большего диаметра увеличивается с увеличением размеров печи ЭДП.Графитовые электроды диаметром 500 или 600 мм становятся все более популярными в последние годы.
Особенность
- Антиокислительная обработка для долголетия.
- Высокая чистота, высокая плотность, сильная химическая стабильность.
- Высокая точность обработки, хорошая обработка поверхности.
- Высокая механическая прочность, низкое электрическое сопротивление.
- Устойчив к растрескиванию и растрескиванию.
- Высокая стойкость к окислению и тепловому удару.
Приложение
Графитовые электроды широко используются для производства легированных сталей, металлов и других неметаллических материалов и т. Д.
- Электродуговая печь постоянного тока.
- AC электродуговая печь.
- Дуговая печь под флюсом.

Графитовый электрод для дуговой печи под флюсом

Графитовый электрод для дуговой печи переменного тока

Графитовый электрод для дуговой печи постоянного тока
Спецификация
Диаметр | Сопротивление (≤, мкОм · м) | Плотность (≥, г / см 3 ) | Прочность на изгиб (≥, МПа) | Модуль упругости (≤, ГПа) | Зольность (≤,%) | CTE (100–600 ° C) (≤ 10 –6 / ° C) | Текущая нагрузка (A) | Плотность тока (А / см 2 ) | |
---|---|---|---|---|---|---|---|---|---|
дюймов | мм | ||||||||
8 | 200 | 6.5 | 1,62 | 10,5 | 12 | 0,3 | 2,4 | 5500–9000 | 18–25 |
9 | 225 | 6,5 | 1,62 | 10,5 | 12 | 0,3 | 2,4 | 6500–10000 | 18–25 |
10 | 250 | 6.5 | 1,62 | 10,5 | 12 | 0,3 | 2,4 | 8000–13000 | 18–25 |
12 | 300 | 6,5 | 1,62 | 10,5 | 12 | 0,3 | 2,4 | 13000–17400 | 17–24 |
14 | 350 | 6.5 | 1,62 | 10,5 | 12 | 0,3 | 2,4 | 17400–24000 | 17–24 |
16 | 400 | 6,5 | 1,62 | 10,5 | 12 | 0,3 | 2,4 | 21000–31000 | 16–24 |
18 | 450 | 6.5 | 1,60 | 9,8 | 12 | 0,3 | 2,4 | 25000–40000 | 15–24 |
20 | 500 | 6,5 | 1,60 | 9,8 | 12 | 0,3 | 2,4 | 30000–48000 | 15–24 |
22 | 550 | 6.5 | 1,60 | 9,8 | 12 | 0,3 | 2,4 | 37000–57000 | 15–23 |
24 | 600 | 6,5 | 1,60 | 9,8 | 12 | 0,3 | 2,4 | 44000–67000 | 15–23 |
Диаметр (мм) | Длина (мм) | ||||||
---|---|---|---|---|---|---|---|
Номинальный диаметр | Фактический Диаметр | Номинальная длина | Допуск | короткая длина | |||
(дюйм) | (мм) | (макс.) | (мин.) | (грубая точка) | |||
8 | 200 | 205 | 200 | 197 | 1600 | ± 100 | -275 |
9 | 225 | 230 | 225 | 222 | 1600 | ||
10 | 250 | 256 | 251 | 248 | 1600/1800 | ||
12 | 300 | 307 | 302 | 299 | 1600/1800 | ||
14 | 350 | 357 | 352 | 349 | 1600/1800 | ||
16 | 400 | 409 | 403 | 400 | 1600/1800/2000/2200 | ||
18 | 450 | 460 | 454 | 451 | 1600/1800/2000/2200 | ||
20 | 500 | 511 | 505 | 502 | 1800/2000/2200/2400 | ||
22 | 550 | 562 | 556 | 553 | 1800/2000/2200/2400 | ||
24 | 600 | 613 | 607 | 604 | 2000/2200/2400 |
Качество поверхности
- На поверхности электрода должно быть менее двух дефектов или отверстий, максимальный размер которых указан в таблице ниже.
- На поверхности электрода не должно быть поперечной трещины. Для продольной трещины длина должна составлять менее 5% от длины электрода, а ширина должна составлять от 0,3 до 1,0 мм.
- Ширина черной области на поверхности электрода должна быть менее 1/10 от окружности электрода, а длина должна быть менее 1/3 от электрода.
Спецификация Дефект Размер | Номинальный диаметр графитового электрода (мм) | |
---|---|---|
300–400 | 450–600 | |
диаметр (мм) | 20–40 (<20 мм должно быть незначительным) | 30–50 (<30 мм должно быть незначительным) |
Глубина (мм) | 5–10 (<5 мм должно быть незначительным) | 10–15 (<10 мм должно быть незначительным) |
RP для производства стали в электродуговой печи
Описание
Графитовые электроды RP , относящиеся к литым колоннам графита, используются в качестве высокотемпературного проводящего материала для электродуговых печей. Регулярная мощность графитированных электродов указана с допустимой плотностью тока менее 17 А / см 2 . Качество графитового электрода определяет производительность и стоимость ЭДП сталеплавильного производства.
Как производитель, мы также поставляем графитовые электроды класса UHP и графитовые электроды HP для сверхмощных или мощных электродуговых печей.Помимо использования в дуговых печах, графитовые электроды также широко используются в дуговых печах с флюсом и в ковшовых печах.
Особенность
- Высокая пропускная способность по току.
- Превосходное сопротивление поломке.
- Высокая стойкость к окислению и тепловому удару.
- Хорошая стабильность размеров, не легко деформироваться.
- Высокая механическая прочность, низкое электрическое сопротивление.
- Высокая точность обработки, хорошая обработка поверхности.
Приложение
Графитовые электроды широко используются для производства легированных сталей, металлов и других неметаллических материалов и т. Д.

Дуговая печь с эксцентриковым дном

RP графитовый электрод для производства стали EAF

RP для обычной мощности EAF
Спецификация
(дюйм) | Сопротивление (≤, мкОм · м) | Плотность (≥, г / см 3 ) | Прочность на изгиб (≥, МПа) | Модуль упругости (≤, ГПа) | Зольность (≤,%) | CTE (100 ° C — 60 ° C) (≤, 10 -6 / ° C) | Текущая нагрузка (А) | Плотность тока (А / см 2 ) |
---|---|---|---|---|---|---|---|---|
8 | 8.5 | 1,53 | 8,5 | 9,3 | 0,5 | 2,9 | 5000–6900 | 15–21 |
9 | 8,5 | 1,53 | 8,5 | 9,3 | 0,5 | 2,9 | 6100–8600 | 15–21 |
10 | 8.5 | 1,53 | 8,5 | 9,3 | 0,5 | 2,9 | 7000–10000 | 14–20 |
12 | 8,5 | 1,53 | 8,5 | 9,3 | 0,5 | 2,9 | 10000–13000 | 14–18 |
14 | 8.5 | 1,52 | 7,0 | 9,3 | 0,5 | 2,9 | 13500–18000 | 14–18 |
16 | 8,5 | 1,52 | 7,0 | 9,3 | 0,5 | 2,9 | 18000–23500 | 14–18 |
18 | 8.5 | 1,52 | 7,0 | 9,3 | 0,5 | 2,9 | 22000–27000 | 13–17 |
20 | 8,5 | 1,52 | 7,0 | 9,3 | 0,5 | 2,9 | 25000–32000 | 13–16 |
22 | 8.5 | 1,52 | 7,0 | 9,3 | 0,5 | 2,9 | 32000–40000 | 13–16 |
24 | 8,5 | 1,52 | 7,0 | 9,3 | 0,5 | 2,9 | 38000–47000 | 13–16 |
Диаметр (мм) | Длина (мм) | ||||||
---|---|---|---|---|---|---|---|
Номинальный диаметр | Фактический Диаметр | Номинальная длина | Допуск | короткая длина | |||
(дюйм) | (мм) | (макс.) | (мин.) | (грубая точка) | |||
8 | 200 | 205 | 200 | 197 | 1600 | ± 100 | -275 |
9 | 225 | 230 | 225 | 222 | 1600 | ||
10 | 250 | 256 | 251 | 248 | 1600/1800 | ||
12 | 300 | 307 | 302 | 299 | 1600/1800 | ||
14 | 350 | 357 | 352 | 349 | 1600/1800 | ||
16 | 400 | 409 | 403 | 400 | 1600/1800/2000/2200 | ||
18 | 450 | 460 | 454 | 451 | 1600/1800/2000/2200 | ||
20 | 500 | 511 | 505 | 502 | 1800/2000/2200/2400 | ||
22 | 550 | 562 | 556 | 553 | 1800/2000/2200/2400 | ||
24 | 600 | 613 | 607 | 604 | 2000/2200/2400 |
Качество поверхности
- На поверхности электрода должно быть менее двух дефектов или отверстий, максимальный размер которых указан в таблице ниже.
- На поверхности электрода не должно быть поперечной трещины. Для продольной трещины длина должна составлять менее 5% от длины электрода, а ширина должна составлять от 0,3 мм до 1,0 мм.
- Ширина черной области на поверхности электрода должна быть менее 1/10 от окружности электрода, а длина должна быть менее 1/3 от электрода.
Спецификация Дефект Размер | Номинальный диаметр графитового электрода (мм) | |
---|---|---|
300–400 | 450–600 | |
Диаметр (мм) | 20–40 (<20 мм должно быть незначительным) | 30–50 (<30 мм должно быть незначительным) |
Глубина (мм) | 5–10 (<5 мм должно быть незначительным) | 10–15 (<10 мм должно быть незначительным) |