состав, сырье, оборудование для производства древесно-полимерного композита
-
1. Общее описание.
-
2. Подготовка полимера.
-
3. Подготовка наполнителя – муки из рисовой шелухи.
-
4. Закуп и доставка прочих составных компонентов ДПК.
-
5. Подготовка смеси ДПК.
-
6. Изготовление профилей ДПК способом экструзии.
-
7. Финишная обработка профилей.
-
8. Упаковка и складирование перед отправкой в продажу.
Общее описание технологии работы производства изделий из ДПК на основе HDPE, ПНД
Производство профилей (изделий) из древесно-полимерного композита на основе ПНД (HDPE) требует наличия следующих сырьевых составляющих — полимера, наполнителя (мука древесная либо мука из шелухи рисовой, подсолнечника, или бамбука), антиоксидантов, лубрикантов, минеральных наполнителей, красителей, связующего вещества.
Основные требования к сырью – низкая влажность, так как влажность напрямую влияет на качество и последующий срок службы изделий из древесно-полимерного композита.
Требования к полимеру (ПНД, HDPE) – достаточное содержание антиоксидантов и стабильный ПТР (показатель текучести расплава), который влияет на стабильность процесса экструзии профилей из древесно-полимерного композита, а следовательно на производительность и на качество ДПК. Производство ДПК на первичной грануле в принципе не рентабельно, основной задачей производителя ДПК является поиск и организация поставок вторичной гранулы стабильного качества.
Достаточное количество антиоксидантов в полимере определяет срок службы композита, его качество и долговечность через несколько лет эксплуатации. Отсутствие антиоксидантов приводит к тому, что полимер, в процессе экструзии или под воздействием ультрафиолета, в процессе эксплуатации подвергается деструкции, своего рода «выгоранию», становится хрупким, и может рассыпаться в пыль.
Основные требования к наполнителю – низкая влажность и мелкий размер частиц. Приемлемая для производства влажность должна быть не более 4%, но для получения качественного древесно-полимерного композита необходима древесная мука с нулевой влажностью. Для этого муку необходимо просушить на стадии подготовки смеси ДПК в миксере, при этом, чем выше влажность, тем больше времени и электроэнергии потребуется на сушку наполнителя, а также будет быстрее изнашиваться оборудование. От размера частиц муки зависит влагопоглощение древесно-полимерного композита, чем больше размер частиц, тем выше влагопоглощение, но если добавить больше сшивающего агента и полимера, то влагопоглощение древесно-полимерного композита можно привести к норме и с крупной мукой.
В России при производстве ДПК в основном используют связующие вещества (сшивающие агенты, аддитивы) на основе ПНД (полиэтилен низкого давления, HDPE) с привитым малеиновым ангидридом (белый порошок или крупная гранула). В Китае используют более широкий спектр сшивающих агентов, в том числе не содержащих ангидрид. Основным недостатком аддитивов содержащих ангидрид является – их нейтрализация в случае, если в сырье имеется влага, а также при использовании стеаратов металлов в качестве лубрикантов. Для того, чтобы получить качественный продукт ДПК, надо хорошо просушить сырье и не использовать в производстве стеараты металлов, хотя действуют они на порядок эффективнее стеариновых кислот. Китайские аддитивы не содержащие ангидрид могут хорошо совмещать компоненты композита, даже если в наполнителе есть небольшая влажность и в качестве лубрикантов используются стеараты металлов. Также некоторые аддитивы без ангидрида содержат в своем составе лубриканты и тем самым позволяют снизить расход лубрикантов в целом, и соответственно повысить рентабельность производства.
Подготовка полимера
Для производства ДПК идеально подходит полиэтилен низкого давления – ПНД (HDPE) с низким ПТР (показатель текучести расплава). Также хорошо подходит поливинилхлорид ПВХ (PVC), с его применением, как правило, древесно-полимерный композит можно сделать дешевле, но у него есть свои плюсы и минусы. Основные плюсы ПВХ: твердость конечного продукта, низкая цена. Минусы: плохая морозостойкость, токсичность при нагреве, при аварийной остановке можно не успеть очистить шнеки, цилиндр и фильеру, и они придут в негодность, но самое плохое – испарениями отравить рабочих, а также существенное отличие ПВХ от ПНД – ПВХ выдерживает не более пяти переплавок.
Для высокой рентабельности производства очень важно использовать полимер со стабильным ПТР, однородного состава и качества. В этом случае производство будет работать с минимумом брака и будет рентабельным. В случае, когда полимер неоднородный и ПТР постоянно меняется – работать крайне сложно, трудно увеличить скорость экструзии и удерживать ее в требуемых параметрах, с сохранением качества и геометрии.
Подготовка полимера (из отходов производств) может состоять из нескольких этапов, в зависимости от качества и состояния исходного сырья. Первое, что необходимо сделать – это измельчить крупные части на мелкие кусочки, определенного размера. Для измельчения литников, обрезков труб большого диаметра лучше всего подойдет одновальный шредер с прижимной плитой. Он «отгрызает» кусочки полимера от большого куска (литника). Затем полученные кусочки можно измельчить до нужной фракции с помощью дробилки. Для измельчения канистры или подобных элементов наиболее подходит двух (четырех) вальный шредер или большая дробилка.
Затем, если сырье изначально было чистое, можно его дополнительно измельчить или сразу использовать по назначению, а если сырье содержало включения – необходимо его переплавить с помощью гранулятора полимеров и очистить расплав с помощью фильтра-сетки.
В любом случае, состав комплекта оборудования для организации производства ДПК надо определять исходя из видов, источников сырья на котором планируется работать.
Подготовка муки (наполнителя)
В составе ДПК как правило примерно 60% от массы формируется дешевым наполнителем. В качестве наполнителя используют в основном древесную муку, которую получают из опилок, муку из шелухи рисовой, подсолнечника, а также бамбука. Наполнитель должен быть сухим, оптимальная влажность не более 4%. Древесная мука при хранении обычно подтягивает в себя до 8%-10% влажности, поэтому ее желательно использовать сразу после измельчения.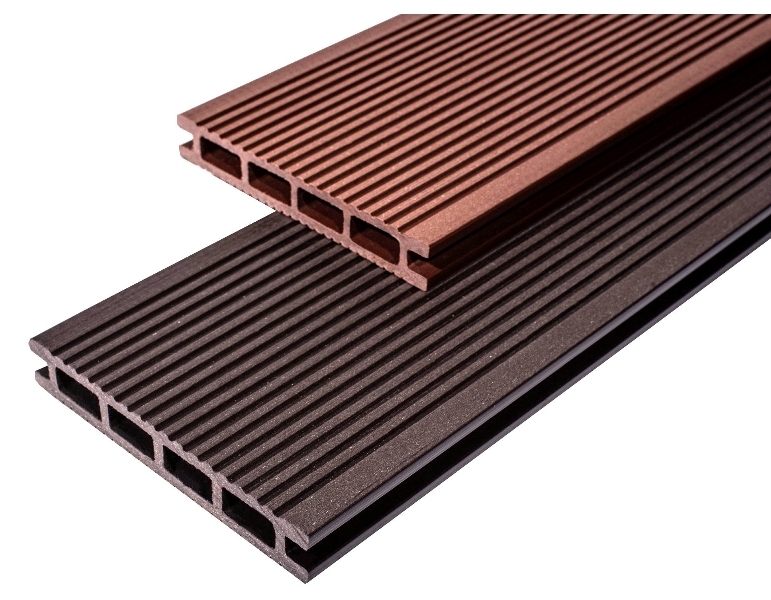
Для измельчения опилок или шелухи лучше использовать ударные или молотковые мельницы, это проверено на собственном опыте. Импеллерные мельницы для этого не подходят. Импеллер истирает частицы, при этом конечно он их подсушивает, но в процессе измельчения от нагрева с поверхности частиц выжигается лигнин и композит от этого теряет прочность.
Важные составляющие ДПК
В составе древесно-полимерного композита кроме полимера и муки, также как наполнитель используются мел и тальк. Они играют роль как песок в бетоне. С их помощью композит становится плотнее и тверже.
Также в состав ДПК входят антиоксиданты, красители, связующий агент (аддитив), лубриканты.
Антиоксиданты предохраняют от деструкции полимер как от высоких температур в процессе экструзии, так и в последующей эксплуатации от ультрафиолета. Обычно используют антиоксиданты двух типов 1010 и 168 (186), или два в одном, есть и такие.
В качестве красителя для ДПК оптимально использовать чистый пигмент – железноокисные красители. Различные мастербатчи и прочие гранулы – это тот же пигмент, только в более низкой концентрации, но дороже и добавлять его надо больше.
Связующее вещество (аддитив) – это гранула ПНД с привитым малеиновым ангидридом. Сам малеиновый ангидрид в чистом виде — это белый порошок или кусочки спрессованного порошка, он «склеивает» полимер с наполнителями. Прививают ангидрид к ПНД, переплавляя их вместе в двухшнековом экструдере со специальными параллельными длинными шнеками. На выходе получается слегка желтоватая/мутноватая гранула. Основной недостаток ангидрида – его нейтрализация влагой и стеаратами металлов.
На собственном опыте мы поняли, что лучше использовать аддитивы без содержания ангидрида – продукт получается более стабильного качества, процесс экструзии также проходит более стабильно, увеличивается скорость выхода продукта и соответственно рентабельность производства.
На крупных производствах ДПК в Китае используют аддитивы без малеинового ангидрида. Мы также используем подобные аддитивы из Китая, которые покупаем напрямую на крупных заводах в Китае, гарантирующих качество.
В качестве внешних и внутренних лубрикантов используют в основном полиэтиленовый воск и стеариновую кислоту. Некоторые производители используют добавки на основе смеси индустриального масла и силикона. Мы пробовали все возможные способы и по нашему мнению самый эффективный лубрикант для ДПК – стеарат цинка, но его желательно использовать с аддитивом без ангидрида.
Подготовка смеси ДПК
Для производства ДПК применяют два типа производственных линий. Если рассматривать мелкое производство 1-2 линии, то можно использовать одношаговую линию. Если производство от 2-х и более линий, то однозначно удобнее работать на двухшаговых линиях. Оба типа линий включают в себя подготовку смеси ДПК на одно или двухстадийном миксере. Одностадийный миксер выполняет перемешивание компонентов ДПК с нагревом до определенной температуры, при этом лубриканты расплавляются и впитываются в наполнители, затем производит выгрузку смеси. Двухстадийный дополнительно охлаждает смесь до заданной температуры, затем производит ее выгрузку. После одностадийного миксера смесь желательно перемещать в накопительный бункер с ворошителем, там она будет постепенно остывать не слеживаясь.
Очень эффективно использовать двухстадийный миксер, если в горячий (верхний бункер) подавать часть компонентов, а оставшиеся компоненты подавать в нижний бункер. Плюсы – производительность выше почти в два раза, не надо подавать воду для охлаждения в нижний бункер. При этом производительность увеличивается реально в два раза. Миксеры использовать желательно с нагревом маслом и инвертором, так как миксеры с нагревом только трением выжигают смесь в месте контакта лопастей миксера со смесью, в результате изделия теряют прочность за счет выжигания лигнина.
Технология изготовления профилей
На самом деле технологий производства ДПК существует достаточно много, но суть в целом одна. Экструдер расплавляет смесь и выдавливает профиль через фильеру с одновременным ее охлаждением и отверждением на выходе. Смесь может быть как в гранулах – для двухстадийной линии, так и в виде смеси + гранулы полимера – для одностадийной линии. Главное в процессе экструзии – подобрать оптимальный режим работы или если не получается – подкорректировать состав смеси, чтобы скорость экструзии и качество были приемлемыми. Основные параметры режима работы – температура нагрева в различных зонах экструдера и фильеры, интенсивность охлаждения, загрузка шнеков, скорость экструзии. Также важным параметром является давление расплава в фильере – оно также может меняться от температурных факторов, скорости и от вязкости (состава смеси). То есть, подбирая состав смеси и режим экструзии можно добиться высокой производительности при хорошем качестве продукта.
Технология финишной обработки
Финишная обработка террасной доски из ДПК – это 90% успеха в продажах при прочих равных условиях. На выходе из фильеры все доски имеют глянцевую поверхность, но эксплуатировать глянцевую доску крайне неудобно и не практично. Во первых – она скользкая, во вторых не практичная – она легко царапается.
Для того, чтобы доска из ДПК была более привлекательной и выгодно отличалась от других предложений на рынке, а также чтобы она была практичной используют несколько видов обработки ее рабочей поверхности.
Первый это шлифовка. Рабочую поверхность террасной доски обрабатывают на шлифовальном станке шкуркой (наждачным полотном). На выходе получается ровная гладкая поверхность. Получненную поверхность можно обработать на станке для тиснения (эмбоссинг), хотя правильнее называть такой вид обработки поверхностным обжигом. Так как тиснения как такового нет, но рисунок структуры виден, такой рисунок со временем выгорает и стирается.
Второй вид обработки – самый распространенный в России – это брашинг. Брашинг – это обработка радиальными стальными щетками. Щетки обдирают глянец и в зависимости от толщины ворса наносят структуру на поверхность доски. Брашинг предпочтительнее тиснения если геометрия профиля изделия не достаточно качественная, не точная – брашинг пропускает неровности. При таком виде обработки поверхность не выравнивается, если террасная доска имеет поверхность «вельвет», то щетки могут также удалять глянец в канавках, что делает внешний вид доски не очень привлекательным.
Третий, самый редкий вид обработки – настоящий эмбоссинг, глубокое тиснение, которое еще называют 3D тиснением. Обычно его делают на полнотелых профилях, не имеющих камер, так как пустотелая доска не выдерживает высокого давления необходимого для нанесения текстуры и ломается. Доска выглядит как натуральная, состаренная древесина. При этом не вскрывается структура композита и соответственно доска остается более защищенной от внешних воздействий.
На камерных профилях террасной доски тиснение хорошего качества получается пока только у LG WOOZEN и у нас. На разработку собственной технологии мы потратили почти 2 года.
Упаковка и складирование перед отправкой в продажу.
На процесс производства влияет организация упаковки и зоны складирования. Качество упаковки также влияет на уменьшение количества повреждений изделий в процессе доставки клиенту.
Упаковывать изделия желательно в стрейч-пленку, при этом изделие не пачкается и не скользит при складировании и перевозке.
Древесно-полимерный композит (ДПК)
Главная \ Каталог продукции \ Линии для ячеистых листов, профилей, труб и шлангов \ Древесно-полимерный композит (ДПК)
Древесно-полимерный композит представляет собой материал, содержащий большой процент натуральных волокон, связанных полимером. Наиболее часто используемый в настоящее время натуральный наполнитель — древесная или рисовая мука, произведенная из отходов — древесных опилок и рисовой шелухи. Использование такого дешевого сырья становится все более актуальным для снижения себестоимости конечного изделия, предлагаемого на рынок строительных материалов. Кроме того, ДПК профиль является отличным товаром-конкурентом для дерева, превосходя его по внешним и эксплуатационным характеристикам.
Профили из древесно-полимерных композитов (ДПК) пользуются огромной популярностью по всему миру. Наибольшей популярностью пользуются такие профили из древесно-полимерного композита как террасная доска (декинг), садовые ограждения, оконные профили, сайдинги и аксессуары, внутренние детали автомобилей, противошумные барьеры, дверные профили, парковые скамьи, столы и др. мебель. С каждым годом количество изделий, производимых на оборудовании для производства древесно-полимерного композита растет.
В 1974 году компания ICMA San Giorgio, основываясь на огромном опыте в области деревообработки, разработала технологию древесно-полимерных композитов и запатентовала ее п од маркой WOOD-STOCK. Компания продолжила развивать технологию, что привело к появлению на рынке линий ICMA для производства декинга и других профилей из ДПК. Используя огромный накопленный опыт в сфере ДПК, компания ICMA предлагает линии для производства ДПК профилей на основе полиолефинов. Применение в рецептуре полимеров полиолефиновой группы дает возможность использовать процент наполнения до 70% против 50% наполнения ПВХ. При работе на ПП или ПЭ можно использовать вторичное сырье при условии, его однородности. Переработка же вторичного ПВХ может быть очень трудной задачей. ПП и ПЭ являются не токсичными материалами и они являются безопасными для окружающей среды. По причине содержания хлора в составе ПВХ необходимо вводить больше добавок для стабилизации этого элемента для нормальных климатических условий, чтобы обеспечить защиту окружающей среды.
Базовая рецептура для производства ДПК профиля:
ПОЛИМЕР: PP гомополимер, HDPE (ПЭНД)
ДРЕВЕСНАЯ МУКА: Гомогенная мука с размером частиц от 250 µ до 1000 µ, максимальная влажность: 4 – 5%
БАЗОВЫЙ СОСТАВ КОМПОЗИТА: 25% PP/HDPE
65÷70% древесная мука
5÷10 % добавки
Компания ICMA применяет для производства изделий из ДПК технологию прямой экструзии, что дает ряд преимуществ:
1. Снижение веса погонного метра профиля при сохранении физико-механических свойств. Достижение более высокой степени однородности дает возможность производить белее легкий профиль при аналогичных физико-механических свойствах (по сравнению с профилями, произведенными по другим технологиям). Как результат – экономия материала и снижение себестоимости конечной продукции.
2. Возможность ввода большего количества древесной муки. Компания ICMA комплектует свои линии двухшнековыми экструдерами со шнеками сонаправленного вращения. В экструдерах такого типа значительно усилен эффект смешения компонентов и гомогенизации расплава. Это самая эффективная на сегодняшний день в мире технология производства ДПК. Ввод древесной муки – до 80% от веса изделия.
3. Снижение потребления электроэнергии. Технология не требует предварительного производства гранулы либо агломерации. Нет необходимости повторно нагревать ранее охлажденные гранулы. Как результат меньшая потребность в электроэнергии, а следовательно ниже и себестоимость продукции.
4. Увеличение срока эксплуатации шнековой пары. Стандартный срок эксплуатации 15 — 30 тысяч часов. Поскольку древесная мука является абразивной, использование ее в качестве наполнителя снижает срок службы шнековой пары (шнек-цилиндр). Ввод древесной муки в гомогенизированный расплав позволяет уменьшить отрицательное воздействие. Это позволяет снизить износ шнековой пары в 2-3 раза по сравнению с вводом материала в первую зону экструдера, как это делает большинство производителей. Кроме того, это снижает потребление энергии и уровень нагрузки на шнек.
5. Допустима более высокая степень влажности древесины. Конструктивные особенности экструдеров со шнеками однонаправленного вращения позволяют увеличить длину зоны дегазации в сравнении с экструдерами с противоположно направленным вращением шнеков. В результате более эффективное удаление влаги из смеси. Это позволяет использовать древесную муку с более высокой степенью влажности и избавляет от необходимости досушивания непосредственно в момент загрузки.
6. Группа шнек-цилиндр – модульная: наборный шнек и цилиндр состоят из элементов длиной 4D каждый. То есть при необходимости можно поменять шнек или цилиндр не целиком, а только отдельные элементы/модули.
Типовая компоновка оборудования для производства ДПК профиля включает следующие модули:
1 — Накопитель сырья
2 — Гравиметрические загрузчики сырья и добавок
3 — Гравиметрический загрузчик древесной муки
4 — Опорные рамы
5 — Двухшнековый экструдер сонаправленного вращения
6 — Боковое устройство подачи древесной муки
7 — Шестеренчатый насос расплава
8 — Экструзионная головка ДПК профиля
9 — Калибраторы и охлаждение
10 — Опорный каркас калибратора
11 — Тянущее устройство
12 — Система поперечной резки
13 — Накопительный стол
Если у Вас остались вопросы по процессу производства профиля из древесно-полимерного композита ДПК, ценам на предлагаемого нами оборудование, сроках изготовления и условиях поставки, Вы можете отправить запрос на info@avexx. ru и получить интересующую информацию.
Особенности обработки древесно-пластиковых композитов
Скачать в формате PDF —
Мы обсудили факторы, влияющие на дизайн древесно-пластиковых композитов, но как быть на этапе обработки при производстве пластика? Древесно-пластиковые композиты по-прежнему придерживаются темы об относительной близости к традиционным пластикам с точки зрения обработки, но опять же, есть несколько вещей, которые производители должны учитывать при использовании этих замечательных материалов.
Размер гранул
Размер гранул является важным аспектом в производстве пластика, независимо от того, какое сырье используется. Это не менее актуально при работе с пеллетами из древесно-пластикового композита. Несмотря на это, некоторые поставщики древесно-пластиковых композитов, похоже, игнорируют важность маленьких округлых гранул на этапе производства. Они просто не желают инвестировать в оборудование, необходимое для достижения однородности или прохождения трудоемких процедур сушки, необходимых для более точных методов резки гранул.
Когда гранулы слишком большие, они имеют тенденцию плавиться неравномерно, создавать дополнительное трение и оседать в конечный продукт с худшей структурой. Идеальная пеллета должна быть размером с небольшой шарик и иметь округлую форму для достижения идеального соотношения поверхности к объему. Эти размеры облегчают сушку и помогают обеспечить плавный поток на протяжении всего производственного процесса. Производители, работающие с древесно-пластиковыми композитами, должны рассчитывать на ту же форму и однородность, которые они связывают с традиционными пластиками. Наличие органического наполнителя не является оправданием для гранул хаотичного размера.
Влажность и температура
Низкое содержание влаги, опять же важный фактор в любом производстве пластика, необходим для создания высококачественных пластиков с органическими наполнителями. Правильно спроектированный производственный процесс может взять на себя большую часть нагрузки по уменьшению присутствия влаги. В операции, предназначенной в первую очередь для производства древесно-пластиковых композитных материалов, большая часть оборудования на объекте должна быть предназначена для сушки. Органические наполнители должны быть должным образом высушены перед добавлением в пластик, иначе они не будут правильно сцепляться. Композиты необходимо снова высушить перед упаковкой, чтобы избежать начала формования и возможной деградации продукта. В идеале клиентам самим не придется сушить композитные пластики по прибытии на объект. Низкое содержание влаги — это то, что производители должны просто требовать от своих поставщиков.
Температура обработки является одним из немногих этапов производственного этапа, на котором древесно-пластиковые композиты значительно отличаются от обычных пластиков. Древесно-пластиковые композиты обычно обрабатываются при температуре примерно на 50 градусов ниже, чем тот же материал без наполнителя. Большинство древесных добавок начинают гореть при температуре около 400 градусов по Фаренгейту.
Плавление древесно-пластиковых композитов при слишком высокой температуре может привести к сдвигу — протолкнуть слишком горячий материал через слишком маленькое отверстие, где повышенное трение сжигает древесину и вызывает обесцвечивание и разрушение пластика. Этой проблемы можно избежать, обрабатывая древесно-пластиковые композиты при более низкой температуре, обеспечивая адекватный размер литников и удаляя любые ненужные повороты или прямые углы на пути обработки.
Относительно низкие температуры обработки означают, что производителям редко требуется достижение более высоких температур, чем для традиционного полипропилена. Это устраняет сложную задачу по отводу тепла от производственного процесса. Нет необходимости в дополнительном механическом охлаждающем оборудовании, пресс-формах, специально предназначенных для уменьшения нагрева, или других экстраординарных мерах. Это означает дальнейшее сокращение времени цикла для производителей в дополнение к уже более быстрому времени цикла из-за присутствия органических наполнителей.
Древесно-пластиковые композиты также совместимы с пенообразователями. Добавление этих пенообразователей может создать бальзоподобный материал. Это полезное свойство, когда готовый продукт должен быть особенно легким или плавучим.
Что все это значит для производителей
По технологии обработки древесно-пластиковые композиты ведут себя так же, как и любой другой пластик. При вспенивании, экструзии и литье под давлением древесно-пластиковые композиты совместимы с существующим оборудованием. При литье под давлением следует учитывать вышеуказанные соображения относительно размера и расположения литника, но общий процесс остается прежним. При использовании стандартного экструзионного оборудования гранулы древесно-пластикового композита одинакового размера без проблем оправдают ожидания.
Все вышеперечисленные свойства в сочетании с научно обоснованным экологичным дизайном делают работу с древесно-пластиковыми композитами знакомой многим производителям пластмасс, а также с дополнительным удовлетворением от меньшего воздействия на планету. Чтобы узнать больше о том, что следует учитывать при работе с древесно-пластиковыми композитами, загрузите нашу техническую документацию, используя форму ниже.
Производство с использованием древесно-пластиковых композитов
Процесс выбора материала обычно начинается с новой идеи для продукта или идеи по улучшению существующего продукта. Затем владелец этой идеи садится с дизайнером продукта, чтобы обсудить, как превратить ее в реальность.
Они могут обсудить необходимые физические характеристики, материалы, которые теоретически могут удовлетворить эти потребности, а также преимущества и недостатки каждого потенциального материала. После того, как эти дизайнерские решения приняты, продукт может быть отправлен производителю.
Хотя многие стандартные детали, касающиеся состава древесно-пластиковых композитов, изготавливаются задолго до того, как материал поступает к производителю, эти подробности будут представлять некоторый интерес для инструментальных мастеров, формовщиков, экструдеров и других производителей, поскольку они могут иметь тонкий эффект на общее течение процесса.
Даже при использовании древесно-пластиковых композитов, в которых так много сохранилось традиционного производства пластика, производителям необходимо иметь представление о таких деталях, как процент биоматериалов, используемых в композите, размер частиц и температура обработки.
Эти знания помогут развеять любые опасения, что древесно-пластиковые композиты являются полностью иностранным сырьем, и развеять любые мифы о присущей им «технологичности».
Размер частиц и порода древесины: выбор дизайнера
Размер частиц и порода древесины — это две характеристики древесно-пластиковых композитов, которые дизайнеры могут выбирать до производства. Эти характеристики обычно выбираются на этапе проектирования и оказывают существенное влияние на внешний вид готового продукта.
Частицы древесины большего размера будут видны в готовом изделии, что сделает его более похожим на древесину. С другой стороны, продукты, изготовленные из частиц меньшего размера, будут выглядеть так, как если бы они были изготовлены из традиционного пластика. Если внешний вид изделия из дерева важен для изделия в целом, дизайнерам больше подойдет более крупный размер частиц.
Порода древесины, выбранная в качестве органического наполнителя для композитного пластика, влияет на цвет конечного продукта. Изделия, изготовленные с использованием соснового наполнителя, получатся легче, чем изделия, изготовленные, например, из кленового наполнителя. Всегда полезно обсудить вопросы выбора цвета с вашим поставщиком.
Смеси твердых пород дерева — еще один вариант для дизайнеров. Но их может быть трудно подобрать по цвету из-за естественной изменчивости, возникающей из-за уникальности каждой смеси. Если консистенция является первоочередной задачей, подумайте о том, чтобы держаться подальше от смесей лиственных пород.
Разработчикам продукта может быть полезно привлечь производителей к обсуждению размера частиц и пород древесины, почему они были выбраны, а также получить любые рекомендации от поставщика по достижению согласованных конечных характеристик. Это обеспечит плавный переход от концепции к реализации.
Соображения по рецептуре и инструментам для древесно-пластиковых композитов
Соотношение древесины и пластика в выбранной формуле древесно-пластикового композита будет иметь некоторое влияние на его поведение в процессе производства. Например, процентное содержание древесины в композите будет влиять на показатель текучести расплава (MFI). Как правило, чем больше древесины добавлено в композит, тем ниже ПТР.
Процентное содержание древесины также влияет на прочность и жесткость изделия. Вообще говоря, чем больше дерева добавлено, тем жестче становится продукт. Древесина может составлять до 70 процентов всего древесно-пластикового композита, но результирующая жесткость достигается за счет пластичности конечного продукта, вплоть до того, что он может даже стать хрупким.
Более высокие концентрации древесины также сокращают продолжительность машинного цикла за счет добавления элемента стабильности размеров древесно-пластиковому композиту при его охлаждении в форме. Это структурное усиление позволяет удалять пластик при более высокой температуре, чем обычный пластик. При температурах, когда обычные пластмассы еще слишком мягкие, чтобы их можно было извлечь из форм, можно успешно извлекать композиты, изготовленные из дерева.
Если продукт будет производиться с использованием существующих инструментов, размер литника и общая форма молдинга должны учитываться при обсуждении оптимального размера древесных частиц. Частица меньшего размера, вероятно, лучше подойдет для инструментов с небольшими воротами и узкими расширениями. Если другие факторы уже заставили конструкторов остановиться на большем размере частиц древесины, то может быть целесообразно соответствующим образом изменить существующую оснастку. Но, учитывая существующие варианты для разных размеров частиц, такого исхода следует полностью избежать.
В общем, инструменты при работе с древесно-пластиковыми композитами более или менее такие же, как и при работе с обычными пластиками. Даже когда изменения необходимы, их часто можно вносить как модификации существующих инструментов, а не как перезагрузку с нуля. Эта совместимость делает переход к работе с древесно-пластиковыми композитами относительно легким.
Особенности обработки древесно-пластиковых композитов
Размер гранул является важным аспектом в производстве пластика, независимо от используемого сырья. Не менее актуально это и при использовании пеллет из древесно-пластикового композита.
Несмотря на это, некоторые поставщики древесно-пластиковых композитов, кажется, игнорируют важность маленьких округлых гранул на этапе производства. Они просто не желают инвестировать в оборудование, необходимое для достижения однородности или прохождения трудоемких процедур сушки, необходимых для более точных методов резки гранул.
Когда гранулы слишком большие, они имеют тенденцию неравномерно плавиться, создавать дополнительное трение и оседать в конечный продукт с худшей структурой. Идеальная пеллета должна быть размером с небольшой шарик и иметь округлую форму для достижения идеального соотношения поверхности к объему. Эти размеры облегчают сушку и помогают обеспечить плавный поток на протяжении всего производственного процесса.
Производители, работающие с древесно-пластиковыми композитами, должны рассчитывать на ту же форму и однородность, которые они ассоциируют с традиционными пластиками. Наличие органического наполнителя не является оправданием для гранул хаотичного размера.
Низкое содержание влаги, опять же важное соображение в любом производстве пластика, необходимо для создания высококачественных пластиков с органическими наполнителями.
Правильно спроектированный производственный процесс может взять на себя большую часть нагрузки по уменьшению присутствия влаги. В операции, предназначенной в первую очередь для производства древесно-пластиковых композитов, большая часть оборудования на объекте должна быть предназначена для сушки. Органические наполнители должны быть должным образом высушены перед добавлением в пластик, иначе они не будут правильно сцепляться.
Композиты необходимо снова высушить перед упаковкой, чтобы избежать начала плесени и возможной деградации продукта. В идеале клиентам самим не придется сушить композитные пластики по прибытии на объект. Низкое содержание влаги — это то, что производители должны просто требовать от своих поставщиков.
Температура обработки является одним из немногих этапов производственного этапа, на котором древесно-пластиковые композиты значительно отличаются от обычных пластиков. Древесно-пластиковые композиты обычно обрабатываются при температуре примерно на 50 градусов ниже, чем тот же материал без наполнителя. Большинство древесных добавок начинают гореть при температуре около 400 градусов по Фаренгейту.
Плавление древесно-пластиковых композитов при слишком высокой температуре может привести к сдвигу — протолкнуть слишком горячий материал через слишком маленькое отверстие, где повышенное трение сжигает древесину и вызывает обесцвечивание и разрушение пластика. Этой проблемы можно избежать, обрабатывая древесно-пластиковые композиты при более низкой температуре, обеспечивая адекватный размер литников и удаляя любые ненужные повороты или прямые углы на пути обработки.
Относительно низкие температуры обработки означают, что производителям редко требуется достижение более высоких температур, чем у традиционного полипропилена. Это устраняет сложную задачу по отводу тепла от производственного процесса.
Нет необходимости в дополнительном механическом охлаждающем оборудовании, пресс-формах, специально предназначенных для уменьшения нагрева, или других чрезвычайных мерах. Это означает дальнейшее сокращение времени цикла для производителей в дополнение к уже более быстрому времени цикла из-за присутствия органических наполнителей.
Что касается методов обработки, древесно-пластиковые композиты снова ведут себя так же, как и любой другой пластик. При вспенивании, экструзии и литье под давлением древесно-пластиковые композиты совместимы с существующим оборудованием.
При литье под давлением необходимо учитывать вышеуказанные соображения относительно размера и расположения литника, но общий процесс остается прежним.
При использовании стандартного оборудования для экструзии древесно-пластиковые композитные гранулы одинакового размера без проблем оправдают ожидания.
Древесно-пластиковые композиты также совместимы с пенообразователями. Добавление этих пенообразователей может создать бальзоподобный материал. Это полезное свойство, когда готовый продукт должен быть особенно легким или плавучим.
Особенности работы с древесно-пластиковыми композитами
Особенности составов древесно-пластиковых композитов следует обсуждать и учитывать при проектировании и производстве продукта. Дизайнеры должны помнить, что выбор материала, касающийся размера и породы древесины, будет иметь значение для производителей.
У производителей наверняка возникнут вопросы по поводу выбранного материала. Будет ли это работать с моим существующим оборудованием? Потребуется ли мне перепроектировать мой инструментарий? Какого времени цикла я должен ожидать от древесно-пластиковых композитов?
Знание ответов на эти вопросы поможет производителям более комфортно работать с древесно-пластиковыми композитами. Как оказалось, древесно-композитные пластики очень похожи на обычный пластик, но обладают дополнительным преимуществом экологической устойчивости.